Urethanguss vs. Spritzguss – Ein DFM-Leitfaden
Design for Manufacturing (DFM) umfasst die Optimierung des Teiledesigns, damit Hersteller qualitativ hochwertige Teile mit den geringstmöglichen Kosten pro Einheit herstellen können. Durch die Berücksichtigung der Herstellungsmethode und ihrer Einschränkungen können Designer die Produktionszeit verkürzen, Kosten senken und umfangreiche Neukonstruktionen vermeiden.
Die Best Practices für DFM variieren je nach Produkt, das Sie herstellen, und Ihrer gewählten Herstellungsmethode. Während Spritzguss und Urethanguss beides Formtechnologien sind, mit denen geformte Kunststoffteile hergestellt werden können, gelten für sie unterschiedliche DFM-Richtlinien. Hier ist alles, was Sie wissen müssen.
Urethanguss vs. Spritzguss
Bevor Sie mit dem Spritzgießen von Teilen beginnen, müssen die geeigneten Werkzeuge konstruiert und per CNC-Bearbeitung hergestellt werden. Die Geometrie Ihres Teils wirkt sich direkt auf Ihre Werkzeuge aus. Wenn Sie also eine komplexe Komponente haben, benötigen Sie auch komplexe Werkzeuge. Komplexe Teile müssen möglicherweise Gleitbewegungen, Heber oder entfernbare Kerne in das Design der Form integrieren. Beim Spritzgießen kommen Kern und Kavität zusammen. Geschmolzener Kunststoff wird dann in das Werkzeug gespritzt, gekühlt, gehärtet und ausgeworfen, um ein verwendbares Teil zu erzeugen.
Urethanguss beginnt mit einem Urmuster, das durch CNC-Bearbeitung oder 3D-Druck erstellt wird. Der Bediener platziert das Originalmodell in einem Formkasten, füllt den Kasten mit flüssigem Silikon und härtet es dann aus. Nachdem der Aushärtungsprozess abgeschlossen ist, wird die Form in zwei Hälften geschnitten, um das Urmodell zu entfernen. Was zurückbleibt, ist ein Hohlraum in der Form des zu formenden Teils. Anschließend wird die Kavität mit Urethan-Gießharz gefüllt und zum Aushärten in eine beheizte Vakuumkammer gegeben.
- Während bei beiden Verfahren der Hohlraum einer Form mit einem Kunststoffmaterial gefüllt wird, gibt es einige wesentliche Unterschiede zwischen Urethanguss und Spritzguss.
- Formen für den Spritzguss bestehen oft aus Stahl oder Aluminium, wodurch sie weitaus haltbarer sind als die Silikonformen, die beim Urethanguss verwendet werden.
- Die Erstellung einer Urethan-Gussform ist kostengünstiger als die Erstellung einer Spritzgussform. Komplexe Spritzgussformen können leicht Zehntausende von Dollar kosten, aber die Herstellung einer Urethan-Gussform kostet normalerweise Hunderte oder Tausende von Dollar.
- Während es mehrere Monate dauern kann, bis eine Spritzgussform in die Produktionsphase übergeht, können Urethan-Gussformen in weniger als zwei Wochen bearbeitet werden.
- Urethanguss verzeiht mehr Wandstärke und Hinterschneidungen als Spritzguss.
Wenn Sie eine Großserienproduktion planen oder enge Toleranzen haben, ziehen Sie den Spritzguss in Betracht. Metallformen sind langlebiger und steifer als Silikonformen, und Metall liefert kontinuierlich eine gleichbleibende Teilequalität. Außerdem haben Sie beim Spritzgießen viel mehr Kontrolle als beim Urethanguss. Der Hersteller kann nicht nur den Materialfluss und die Kühlraten steuern, sondern auch die Einspritztemperatur und den Ort beim Spritzgießen. Auch wenn die Kosten für die Erstellung einer Form für den Spritzguss anfangs hoch erscheinen mögen, werden sie kosteneffektiv, wenn sie auf Tausende von Teilen aufgeteilt werden.
Andererseits ist Urethanguss ideal für die Entwicklung von Prototypen oder die Ausführung von Kleinserien, da Soft-Tooling Geschwindigkeit, Flexibilität und Erschwinglichkeit bietet. Wenn Sie eine hohe Nachfrage nach Ihrem Produkt haben, aber Ihre dauerhafte Werkzeugbestückung noch nicht fertig ist, können Sie die Produktion mit Urethanguss beginnen.
Die wichtigsten DFM-Probleme beim Urethanguss und -spritzguss
Wenn es um DFM für Urethanguss oder Spritzguss geht, sollten Sie Toleranzen, Wandstärken und Hinterschnitte im Auge behalten.
Toleranzen
Kein Herstellungsprozess ist perfekt, daher berücksichtigen Designer und Ingenieure diese Abweichungen, indem sie akzeptable Toleranzen festlegen. Teile werden mit diesen akzeptablen Messabweichungen von Basismessungen verglichen, sodass diejenigen, deren Abmessungen diesen Einschränkungen entsprechen, als akzeptabel angesehen werden. Diejenigen mit Maßabweichungen über dem in der Toleranz definierten Betrag funktionieren nicht wie beabsichtigt. Diese Toleranzen werden während des Designprozesses festgelegt und bestimmen, welche Herstellungsverfahren verwendet werden können.
Das Erreichen enger Toleranzen mit gegossenem Urethan ist sehr schwierig – wenn nicht sogar unmöglich – da die Formen aus flexiblem Silikon bestehen, das durch die Vakuumlast bewegt werden kann. Sie sollten kein gegossenes Urethan zur Herstellung Ihrer Teile verwenden, wenn Sie unglaublich genaue Komponenten benötigen.
Andererseits bieten Metallspritzgussformen weniger Abweichungen bei den endgültig gemessenen Abmessungen, da sie sich nicht so stark bewegen können. Geschmolzener Kunststoff zieht sich jedoch beim Abkühlen zusammen, was geringfügige Abweichungen in den endgültig gemessenen Abmessungen des Teils verursacht. Sie müssen Spritzgusstoleranzen festlegen, die dies widerspiegeln.
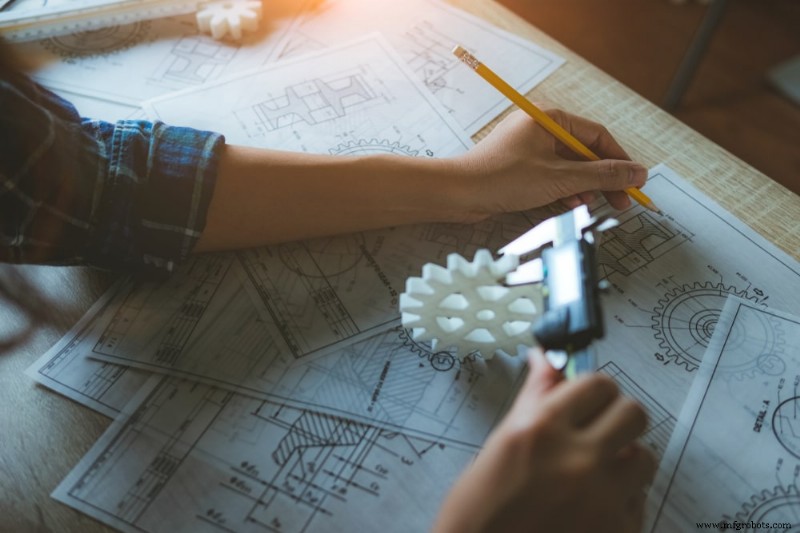
Eine Untertoleranz kann günstiger sein, kann jedoch die Benutzerfreundlichkeit beeinträchtigen, und eine Übertoleranz ist teurer und zeitaufwändiger. Indem Sie sich die Zeit nehmen, die perfekte Balance zwischen den beiden zu finden, können Sie sicherstellen, dass Ihre Teile zuverlässig und funktional sind und wie vorgesehen zu anderen Teilen passen. Berücksichtigen Sie die Funktion Ihres Teils, Toleranzstapelung und die Fertigungs- und Montageprozesse. Wenn Ihre gewählte Fertigungsmethode Ihre Toleranzanforderungen nicht erfüllen kann, müssen Sie möglicherweise eine andere Fertigungstechnologie verwenden. Sie können Ihr Teil auch so umgestalten, dass es mit weiten Toleranzen funktioniert.
Wandstärke
Die Beibehaltung einer gleichmäßigen Wandstärke ist wichtig, da sie die Konsistenz von Teil zu Teil erhöht, die Spannungsverteilung verbessert und die Kosten senkt. Inkonsistente oder ungleichmäßige Wandstärken können zu Verzug, Einfallstellen, Schrumpfung, Fehlschüssen oder Hohlräumen in Spritzgussteilen führen.
Die ideale Wandstärke eines Teils hängt von seiner Größe, Geometrie und den strukturellen und ästhetischen Anforderungen ab. Für beste Ergebnisse empfehlen wir Wandstärken für Spritzgussteile zwischen 1-4 mm. Bei der Herstellung von Teilen mit Urethanguss können Wände mit unterschiedlichen Dicken vorhanden sein, obwohl beim Aushärten möglicherweise eine gewisse Schrumpfung oder Verformung auftritt. Für beide Prozesse ist es am besten, die Wandstärke unter 5 mm zu halten.
Alle Vorsprünge oder Vertiefungen, die Sie daran hindern, Ihr Teil ohne Beschädigung aus einer einteiligen Form auszuwerfen, gelten als Hinterschnitte. In einigen Fällen können vertiefte Oberflächen, Rillen und Überhänge den Entformungsprozess erschweren und Ihr Teil beschädigen. In anderen Fällen richten diese Funktionen keinen Schaden an. Es hängt davon ab, wie Sie diese Funktionen und Ihre Komponente entworfen und ausgerichtet haben.
Unterschnitte
Die Auswirkung von Hinterschneidungen hängt auch von Ihrem Herstellungsverfahren ab. Dank der Flexibilität, die Urethan-Gießsilikon bietet, können Sie das Werkzeug einfach biegen und strecken, um Ihr Teil freizugeben, wenn Sie einen Unterschnitt haben. Das Gleiche gilt nicht für die beim Spritzgießen verwendeten Metallwerkzeuge, die weitaus weniger flexibel sind. Ihr Hersteller muss möglicherweise Aktionen hinzufügen, ein Loch oder einen Schlitz in Ihrer Form erstellen oder Ihre Form mit Merkmalen neu gestalten, die parallel zur Achse verlaufen, an der sich die Form trennt, um sicherzustellen, dass Ihr Teil ausgeworfen werden kann. Dies führt zu komplexeren und teureren Werkzeugen.

Design für die Fertigung mit Fast Radius
Unabhängig davon, ob Sie sich für Urethanguss oder Spritzguss entscheiden, die Integration von DFM in den Konstruktionsprozess senkt Ihre Kosten pro Teil und spart Zeit. Indem Sie Ihre Fertigungsmethode, Toleranzen, Wandstärken und Hinterschneidungen bei der Konstruktion berücksichtigen, können Sie Fehlausrichtungen von Teilen minimieren und den Produktionsprozess optimieren.
Unabhängig davon, für welches Herstellungsverfahren Sie sich entscheiden, Fast Radius kann Ihnen dabei helfen, auf Herstellbarkeit zu konstruieren, um sicherzustellen, dass Sie mit der Qualität und den Kosten des Endprodukts zufrieden sind. Unser Expertenteam kann Sie zu geeigneten Toleranzen und Wandstärken beraten oder Ihnen dabei helfen, die für Ihr Design am besten geeignete Lösung für Hinterschneidungen zu ermitteln. Kontaktieren Sie uns noch heute, um loszulegen.
Industrietechnik
- Leitfaden zum Spritzgießen mit geringem Volumen
- Was ist Reaktionsspritzguss
- Guss vs. Spritzguss
- Thermoformen vs. Reaktionsspritzgießen (RIM)
- Spritzguss vs. Reaktionsspritzguss (RIM)
- Gießformen vs. Reaktionsspritzgießen
- Druckguss vs. Spritzguss
- Wann ist Vakuumgießen besser geeignet als Spritzgießen?
- Design von Spritzgießanschnitten:Ein ultimativer Leitfaden für die Kunststoffherstellung
- Präzisionsguss-Leitfaden