Teilekonsolidierung mit additiver Fertigung neu denken
Mechanische Baugruppen sind sowohl in Konsumgütern als auch in Industrieprodukten üblich. Selbst relativ preiswerte Produkte können aus Dutzenden von Einzelteilen bestehen, und in komplexen Maschinen können es leicht Hunderte oder Tausende von Komponenten sein. Die additive Fertigung (AM) ermöglicht ein hohes Maß an Teilekonsolidierung und macht manchmal sogar die Montage überflüssig.
Die Vorteile der additiven Fertigung für die Teilekonsolidierung
AM ist auf einzigartige Weise in der Lage, komplexe Geometrien herzustellen, die mit herkömmlichen Herstellungsverfahren nicht hergestellt werden können. Eine mechanische Baugruppe, die normalerweise aus vielen Teilen besteht, die als separate Komponenten hergestellt und dann zusammengefügt werden, kann als eine Einheit additiv gefertigt werden, selbst wenn die Geometrie sehr komplex ist. Neben der Konstruktionsvereinfachung bietet die Verwendung von AM für die Teilekonsolidierung weitere greifbare Vorteile:
Geringere Projektionskosten insgesamt
Der beste und offensichtlichste Vorteil der Konsolidierung Ihrer Teile mit AM besteht darin, dass weniger Teile für die Montage benötigt werden, was bedeutet, dass Sie weniger Geld für die Montagekosten ausgeben. Das Herausnehmen der Montage aus der Gleichung bedeutet auch, dass Sie potenzielle kostentreibende Faktoren wie Qualitätskontrolle oder Bestandsverwaltung reduzieren. Indem Sie die additive Fertigung verwenden, um mehrere Teile als eins herzustellen, verringern Sie das Risiko versteckter Kosten und Projektverzögerungen.
Weniger Material
In der traditionellen Fertigung steigen mit zunehmender Teilekomplexität typischerweise auch die Teilekosten. Bei AM ist dies nicht der Fall – mit zunehmender Teilekomplexität steigen die Teilekosten nicht. In vielen Fällen sinken die Teilekosten, da eine erhöhte Komplexität oft bedeutet, dass weniger Material verwendet wird. Bei der Verwendung von AM ist es möglich, den Materialverbrauch im Vergleich zur herkömmlichen Fertigung um bis zu 70 % zu senken.
Geringeres Gesamtrisiko
Durch die Teilkonsolidierung werden eine Reihe von Risiken reduziert oder ganz eliminiert. Sie können beispielsweise das Risiko umgehen, dass Ihr Lieferant das betreffende Teil nicht mehr liefern kann. Dieses Lieferantenrisiko wird mit der Anzahl der Teile in der Baugruppe multipliziert. Wenn Sie mehrere Teile als eine Einheit mit AM drucken können, sinkt die Wahrscheinlichkeit, dass dieses Problem auftritt, erheblich.
Es gibt auch andere Risiken, die ebenfalls reduziert werden. Die Fälle von Teileversagen nehmen ab, wenn das Teil als einzelne Einheit hergestellt und nicht separat montiert wurde. Ein weiteres Risiko ist die Veralterung; Wenn das Teil das Ende seiner Lebensdauer erreicht, haben Sie keinen verbleibenden Bestand, der entsorgt werden muss.
Bessere Leistung
In vielen Fällen können Sie mit AM ein Teil mit besserer Leistung herstellen, da es Geometrien ermöglicht, die wünschenswert sind, aber mit herkömmlicher Fertigung nicht hergestellt werden können. Einige der Anwendungen von AM, die aufregende Vorteile für eine verbesserte Produktleistung bieten, umfassen geringes Gewicht, ein hohes Verhältnis von Festigkeit zu Gewicht, Wärmeübertragung und Flüssigkeitsfluss sowie Energieabsorption.
Wie können Sie Teile für die Konsolidierung identifizieren?
Wenn Sie über eine Teilekonsolidierung mit AM nachdenken, besteht der erste Schritt darin, sich auf die Funktion der Baugruppe zu konzentrieren, die Sie ersetzen möchten. Dann müssen Sie die Annahmen hinterfragen, die zu Ihrem ursprünglichen Design geführt haben, das mit traditioneller Fertigung hergestellt wurde.
Es kann hilfreich sein, bei der Analyse der zu konsolidierenden Teile strukturiert vorzugehen. Eine effektive und beliebte Methode zur Analyse von Fertigung und Montage ist als Design for Manufacture and Assembly (DFMA®) bekannt. Das Modell besteht aus drei Fragen, die Ingenieuren und Herstellern dabei helfen, den Prozess der Baugruppenkonsolidierung zu beginnen:
- Muss sich das Teil relativ zu den montierten Teilen bewegen?
- Werden mehrere Materialien für die Teilfunktion benötigt?
- Muss das Teil für die Montage oder Demontage getrennt werden?
Durch das Durchdenken dieser Fragen können Konstrukteure die theoretische Mindestanzahl von Teilen bestimmen, die für die Montage erforderlich sind. Während diese Fragen als Ausgangspunkt dienen können, gibt es einige weiterführende Überlegungen, die Ihnen dabei helfen, festzustellen, ob Sie Additive für die Teilekonsolidierung in Betracht ziehen sollten:
- Sind mehrere Teile erforderlich, um diese Anforderung zu erfüllen?
- Kann ein einzelnes Teil diese Anforderung erfüllen?
Mit anderen Worten, werden wirklich mehrere Teile benötigt, damit das Teil richtig funktioniert? Gibt es andere Lösungen, wie z. B. Gitterstrukturen (oder andere komplexe Geometrien), die in ein Design integriert werden könnten, das im Wesentlichen dieselbe Funktion erfüllen und gleichzeitig die Anzahl der insgesamt erforderlichen Teile und Materialien reduzieren könnte?
Schauen Sie sich die folgende Tabelle an, um festzustellen, ob die Teilekonsolidierung mithilfe von Additiven für Sie geeignet ist.
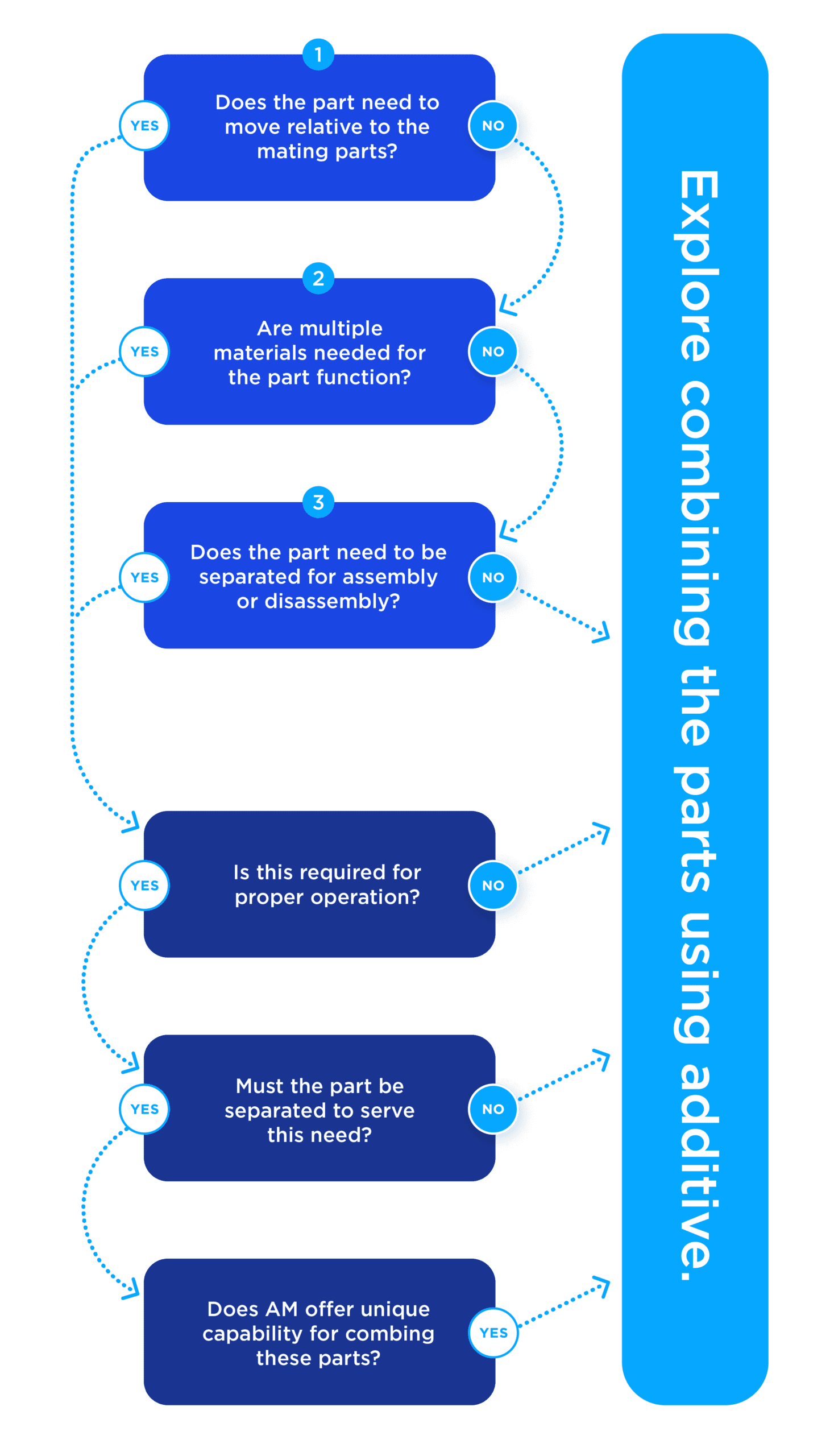
Teilekonsolidierung und additive Prozesse
Die Reduzierung der Anzahl separater Komponenten ist nur ein Faktor bei der Teilekonsolidierung. Eine weitere Möglichkeit, die Anzahl der montierten Teile in Ihrem Produkt zu minimieren, ist der Einsatz von Technologien, die eine Konsolidierung ermöglichen. Mit additiven Technologien wie HP Multi Jet Fusion (MJF) können separate Komponenten nicht nur als Ganzes gedruckt werden, sondern sind direkt aus dem Drucker in der Lage, sich in vollem Umfang zu bewegen.
Die Entscheidung, welche additive Technologie verwendet werden soll, hängt von Ihren Designanforderungen ab. Mit HP MJF benötigen Teile beispielsweise keine Stützen, wodurch Ingenieure komplexere Konstruktionen und bewegliche Teile erstellen konnten. Die Carbon®-Technologie erfordert zwar Stützen, ist jedoch in der Lage, langlebige Komponenten mit unterschiedlichen Wandstärken in einem Stück zu drucken. Ein großartiges Beispiel für die Konsolidierung von Teilen mit Carbon® ist die SILQ-Stuhlarmlehne von Steelcase:Früher wurde die Armlehne aus drei separaten Teilen zusammengesetzt, aber dank Gitterstrukturen und komplexen Geometrien wird sie jetzt als eine Einheit gedruckt.
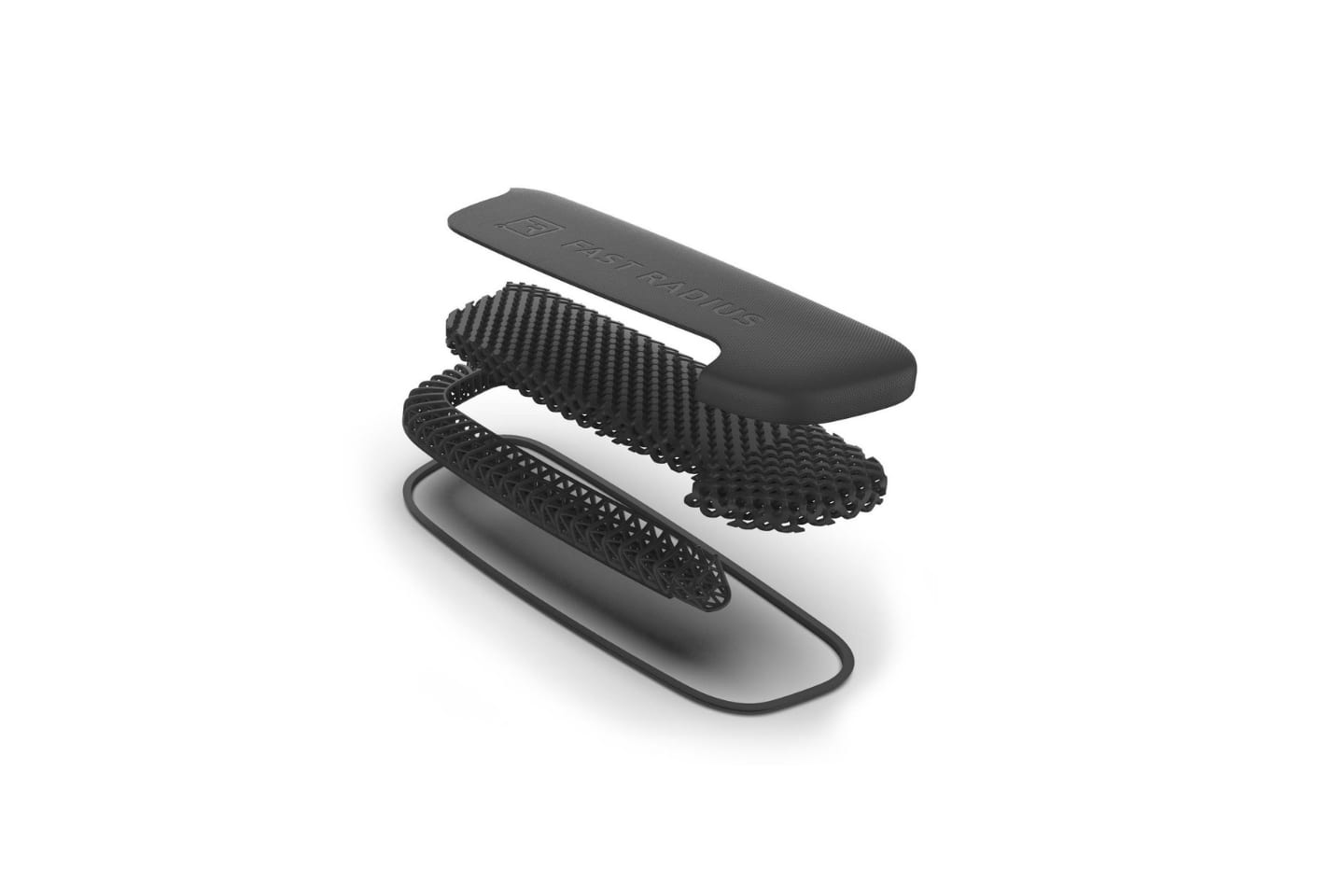
Anwendungsbeispiele zur Teilkonsolidierung
Es gibt viele Anwendungen, die von der Teilekonsolidierung mit AM profitieren könnten. Es gibt bereits Anwendungen auf dem Markt, wie z. B. mechanische Baugruppen, Fluidkomponenten, Strukturteile und mehr. Hersteller sehen eine verbesserte Leistung und Haltbarkeit dank der Konstruktion mehrerer Teile als eins. Schauen wir uns genauer an, wie sich die Teilekonsolidierung auf zwei spezifische Anwendungen auswirkt.
Pumpenlaufräder
Herkömmlich hergestellte Laufräder erfordern häufig separate Teile, die zusammengeschweißt werden. Mit AM können diese in einem Stück gedruckt werden. Wenn ein Pumpenlaufrad traditionell hergestellt wird, weist es Lücken zwischen seinen Komponenten auf. Durch die Fertigung mit Additiven kann der Spalt entfernt werden – was die Gesamtleistung des Teils verbessert. Es ist auch wichtig zu beachten, dass durch den Wegfall der Schweißnähte die Anzahl potenzieller Fehlerstellen reduziert wurde und keine Korrosion an den Schweißnähten mehr auftritt.
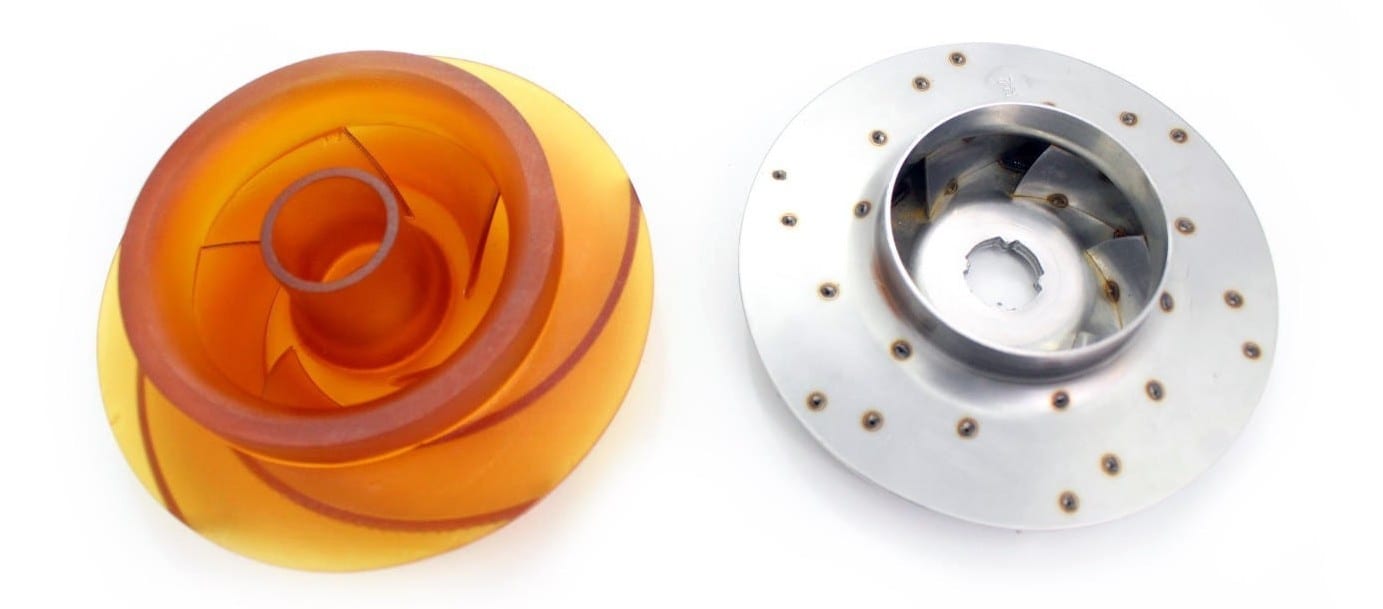
Luftführung
Luftkanäle sind auch großartige Kandidaten für die Teilekonsolidierung. Durch die Verwendung komplexer Geometrien, die durch Additive ermöglicht werden, können die Teilegeometrie und der Luftstrom optimiert werden. Ein Fallbeispiel hierfür ist ein Kühlkanal in der HP 500/300-Druckerserie, die HP MJF verwendet. Durch die Konsolidierung von acht Teilen in einem konnte HP seine Lieferkette vereinfachen und die Komponentenkosten um 30 % senken.
Hersteller streben danach, die Kosten und das Lieferkettenrisiko zu senken und die Leistung durch Teilekonsolidierung zu verbessern. AM bietet eine einzigartige Möglichkeit, Baugruppen aufgrund der jetzt möglichen komplexen Geometrien weiter zu reduzieren. Wenn Sie mehr darüber erfahren möchten, wie Ihre Anwendung konsolidiert werden kann, wenden Sie sich noch heute an unser Expertenteam.
Sind Sie bereit, Ihre Teile mit Fast Radius herzustellen?
Starten Sie Ihr AngebotIndustrietechnik
- Flüssige additive Fertigung:Erstellen von 3D-Objekten mit Flüssigkeit
- Vorteile der additiven Fertigung
- Sechs versteckte Vorteile bei der Erforschung der additiven Fertigung
- Verbesserung der additiven Fertigung durch Reverse Engineering
- Beschriften Ihrer Teile mit Gravierfüller
- Die traditionelle Metallbearbeitung glänzt immer noch in der Fertigung
- Additive Fertigung beginnt, über den Desktop-3D-Druck hinaus zu reifen
- Die sieben Arten der additiven Fertigung verstehen
- Additive Fertigung mit Ultraschall erklärt
- GD&T-Toleranzen in der Teilefertigung