Haydon Kerk steigert die Produktivität mit DATRON um über 300 %!
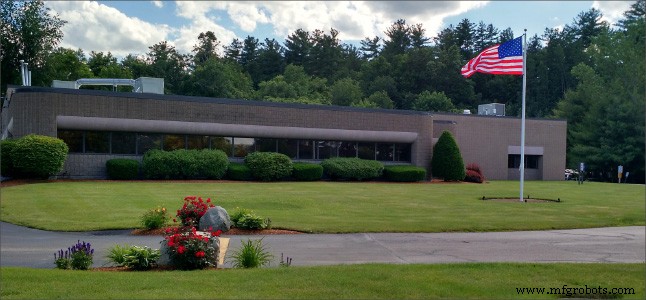
Großer Hersteller fügt Hochgeschwindigkeitsbearbeitung hinzu, um Schienen für Gleitbaugruppen herzustellen. Haydon Kerk ist ein interner Teil der Advanced Motion Solutions-Gruppe von AMETEK, die sich auf die Herstellung einer vollständigen Palette von Komponenten und Präzisions-Bewegungssteuerungssystemen konzentriert. Dazu gehören Linearantriebe, Gewindespindeln und -muttern, Linearschienen und -führungen, Antriebe, Motoren und andere Komponenten. Die Kerk Products Division in Milford, NH, wurde in den 1970er Jahren von den Brüdern Ken und Keith Erickson auf der Grundlage ihres patentierten, verbesserten spielfreien Leitspindeldesigns gegründet.
Heute werden ihre Produkte hauptsächlich in der Industrieautomation, Medizin, Luft- und Raumfahrt, Verteidigung, Petrochemie und Halbleiterindustrie eingesetzt. Werksleiter Stan Brown sagt:„Ob es sich um Leitspindeln handelt, die in Präzisionsautomatisierungssysteme mit hoher Toleranz oder Schrauben in Teile für die orthoskopische Chirurgie (als Ersatz für Herzklappen) eingesetzt werden, wir können uns fast darauf verlassen, dass es sie geben wird ein gewisses Maß an Anpassung erforderlich.“ Jim Lamson, Manufacturing Engineering Manager, stimmt zu und sagt:"Wir scherzen, dass niemand jemals etwas aus unserem Katalog bestellt, es ist eher wie ein Buch mit Vorschlägen."
Zu diesem Zweck fertigt und lagert Haydon Kerk allein für Schrauben über 475 verschiedene Kombinationen von Durchmessern und Vorschub pro Gewindetyp zur Verwendung in seinen Standardprodukten und kundenspezifischen Lösungen. Logischerweise erfordert ihr Geschäft eine Menge Ausrüstung, um mit allen von ihrem Kundenstamm geforderten Variationen Schritt halten zu können. In mehreren Gebäuden auf ihrem Campus beherbergen sie Maschinen vom Schweizer Typ, Doosan-Revolverdrehmaschinen, Gewindewalzmaschinen, Haas-VMCs, OmniTurn-CNC-Drehmaschinen, Senkerodiermaschinen und Mori-Seiki-VMCs.
Die Suche nach einer Produktionslösung führt zu einem Hochgeschwindigkeits-Bearbeitungszentrum
Im Jahr 2011 war es ihre Reihe von Gleitbaugruppen, die sie dazu veranlasste, nach einem anderen Gerät zu suchen – speziell zum Fräsen von Schienen aus eloxiertem Aluminium-Strangpressmaterial. Wie bei ihren anderen Produkten erforderten auch diese Teile ein erhebliches Maß an Anpassung, um eine Reihe von Kundenanforderungen zu erfüllen. Lamson sagt:„Die Anzahl der Befestigungslöcher, die Größe der Befestigungslöcher, ob es sich um Gewinde- oder Durchgangslöcher handelt, oder die Länge der Schienen kann unterschiedlich sein, aber bei jeder Bestellung gibt es ein gewisses Maß an kundenspezifischer Anpassung.“
Damals verwendete Haydon Kerk verschiedene Fräsmaschinen, um diese Schienen herzustellen, und Lamson sagt, dass es Probleme gab. „Der Prozess war einfach zu langsam. Wir hatten mehrere Schichten mit mehreren Bedienern pro Schicht, die versuchten, Schritt zu halten, und sie wurden begraben und fielen zurück. Wir brauchten eine andere Lösung und ich begann, nach anderen Fräsmaschinen zu suchen, die diese langen Aluminium-Strangpressprofile verarbeiten können.“
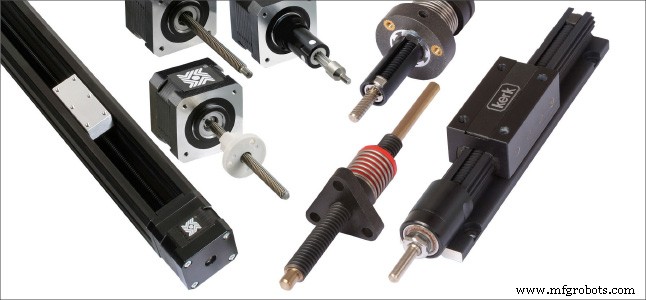
Letztlich führte Lamsons Suche nicht sehr weit, denn er fand DATRON Dynamics, den nordamerikanischen Distributor von DATRON Hochgeschwindigkeits-Fräsmaschinen, gleich um die Ecke in Milford, NH. Also packte er eine Testschiene, einige Extrusionen, eine fertige Schiene und einige Zeichnungen zusammen und machte sich auf den Weg zum DATRON Technologiezentrum, um einen Testschnitt durchführen zu lassen. Lamson erinnert sich:„Eine durchschnittliche Schiene dieser Größe brauchte über 15 Minuten, um sie herzustellen, und es gab mehrere verschiedene Setups, um sie herzustellen. DATRON fertigte die gleiche Schiene in einem Bruchteil der Zeit mit einem einzigen Setup.“
Die für den Testschnitt verwendete Maschine war die DATRON M85, die einen großen Arbeitsraum von 30″ x 40″ bietet, aber eine vergleichsweise kleine Standfläche hat. Haydon Kerk, Manufacturing Supervisor, Scott Ladue, sagt, dass diese Kombination die Augen geöffnet hat „Wenn Sie sich unsere Schneckenschienenfräsung ansehen, wo wir einen großen VMC verwenden, ist die Maschine da draußen so groß wie eine Seekiste – aber das liegt daran, dass wir die 60 Zoll Federweg brauchen. Mit der DATRON können wir immer noch eine 60-Zoll-Schiene herstellen, aber ihre Stellfläche beträgt nur 69 Zoll x 55 Zoll
Hochgeschwindigkeitsbearbeitung führt zu einer Produktionssteigerung von 300 %!
Also kaufte Haydon Kerk die DATRON M85 zum Fräsen dieser Schienen und degradierte die herkömmlichen Fräsmaschinen für andere Arbeiten. Sechs Jahre später denkt Ladue über die Auswirkungen dieser Entscheidung in Bezug auf Zeit und Arbeitskraft nach:„Wir waren in mehreren Schichten voll ausgelastet und jetzt betreiben wir die DATRON in einer Schicht und können damit Schritt halten Nachfrage. Außerdem ist das Volumen gestiegen, seit wir den DATRON im Jahr 2011 bekommen haben, also haben wir unsere Produktivität im Grunde um über 300 % gesteigert. „
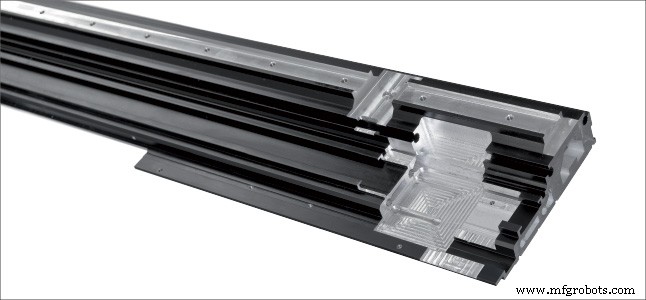
In Bezug auf die Einrichtung hat Haydon Kerk vier Kurt-Schraubstöcke mit Doppelverriegelung in den M85 integriert, damit sie zwei Schienen gleichzeitig einlegen können oder, wenn sie kurze Schienen fahren, zwei Reihen einzelner Schienen laden können. Ladue sagt: „Unabhängig von der Schienengröße ist es also nur eine Frage des Ladens des Schraubstocks und des Ausführens des Programms für diese Schienenserie, nachdem DATRONs integrierter Messtaster für die Teilelokalisierung verwendet wurde.“
Das Messen in der Hochgeschwindigkeitsbearbeitung reduziert die Rüstzeit und gewährleistet Genauigkeit
Der integrierte Messtaster von DATRON ist auf der Z-Achse montiert und die Messung wird durchgeführt, wenn der Messtaster von seiner Grundposition in die Messposition geschwenkt wird. Das patentierte kapazitive Messprinzip von DATRON gewährleistet eine hohe Wiederholgenauigkeit sowie Messgenauigkeit. Die Sonde wird einfach über eine menügesteuerte Software bedient. Nach der Messung erfolgt die Verrechnung direkt in der Steuerungssoftware, wobei das Fräsprogramm automatisch angepasst wird, um Oberflächen- oder Positionierungsabweichungen auszugleichen. Dadurch werden Bedienerfehler minimiert und Verschwendung praktisch eliminiert.
Laut Lamson ist das integrierte Messsystem besonders nützlich bei der Bearbeitung von Schienen, die länger als 30 Zoll sind. „Oft verlangt ein Kunde eine viel längere Schiene und mit dem eingebauten Messsystem von DATRON können wir das Teil fixieren, einen Teil der Schiene bearbeiten, es bewegen, ein Merkmal aufnehmen, das wir in das Teil eingebracht haben und sehr genau bis zum Ende positionieren.“
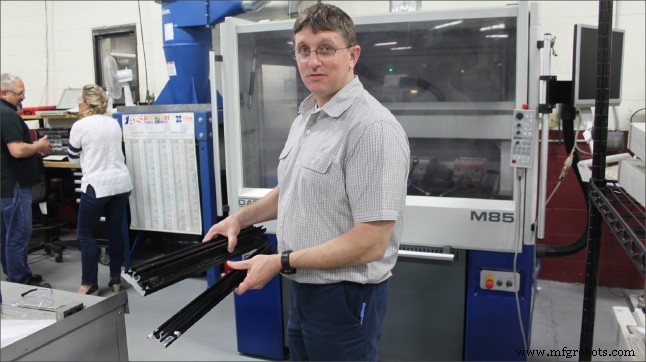
Hochgeschwindigkeitsbearbeitung mit verdunstungskühlmittel führt zu sauberen Teilen und macht sekundäre Operationen möglich Veraltet
Lamson sagt auch, dass DATRONs minimale (verdampfende) Kühlmittelmenge ein zusätzlicher Bonus war, der einen unerwarteten Vorteil hatte. „Wenn die Teile aus der Maschine kommen, müssen wir sie keinem zweiten Reinigungsprozess unterziehen, um in unseren TFE-Beschichtungsprozess zu gelangen. Die Chips, die im Chipsbehälter landen, sind saubere, trockene Chips, sie sind nicht klebrig oder ölig. Wenn Teile noch nass aus der Maschine kommen, kann man ihnen beim Trocknen buchstäblich zusehen. Außerdem ist das Kühlmittel tatsächlich ein wenig lösungsmittelhaltig, sodass die Teile wahrscheinlich sauberer aus der Maschine kommen, als sie reingekommen sind. Das war eine völlig neue und inspirierte Idee für uns, dass wir Kühlmittel haben könnten, die wir nicht brauchen aufräumen.“
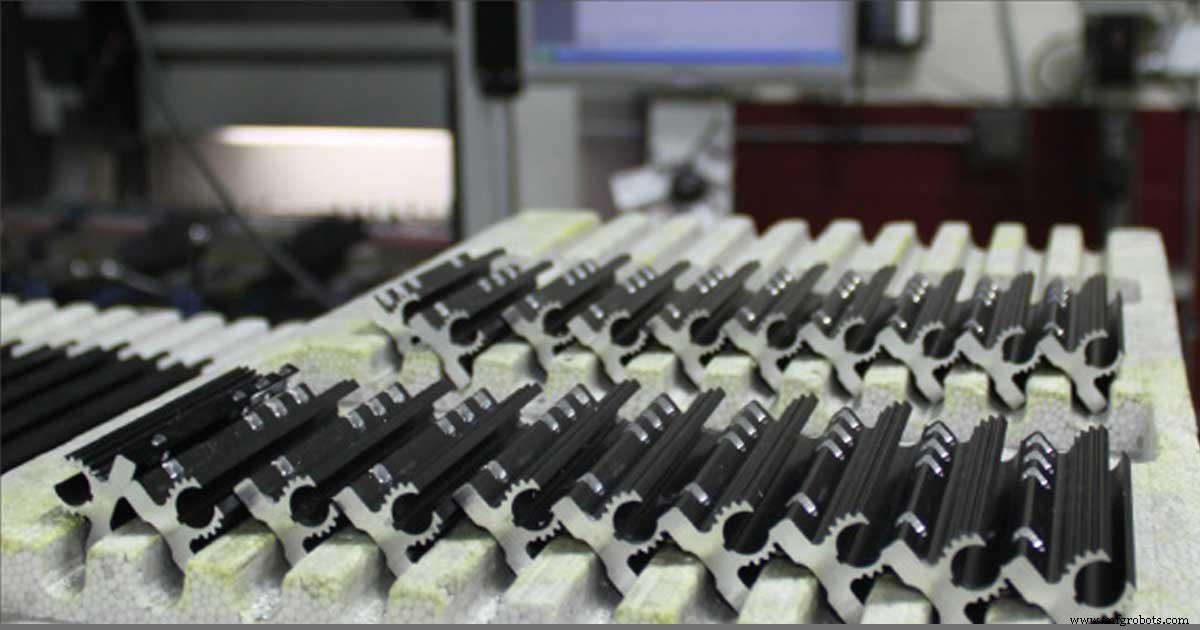
Cutting Tools for High-Speed Machining
Neben der DATRON-Maschine ist Haydon Kerk auch Kunde von DATRON-Werkzeugen geworden, und Fertigungsleiter Scott Ladue sagt:„DATRON-Werkzeuge sind ausgezeichnet. Wir kaufen nicht viel weil sie lange halten und der Bediener sie so schnell schiebt, wie die Maschine geht. Außerdem sind die Teile, die wir bearbeiten, hart eloxiert, sodass sie etwas härter als rohes Aluminium sind.“ Jim Lamson fügt hinzu:„Die Verwendung der DATRON hat uns dazu veranlasst, unsere anderen Maschinen etwas anders zu verwenden, weil Sie auf der DATRON nichts klopfen, Sie Gewindefräser, und wir sind daran gewöhnt, Gewindebohrer zu verwenden. Wir haben Teile auf anderen Maschinen herstellen lassen, auf denen kein Gewindebohrer verwendet werden konnte, also sind wir zu den Werkzeugmachern von DATRON gegangen und haben sie einen kundenspezifischen Gewindefräser für unsere anderen Maschinen entwickeln lassen.“
In den sechs Jahren, in denen er die DATRON-Maschine verwendet hat, hat Haydon Kerk die empfohlene vorbeugende Wartung eingehalten, und als Ergebnis bestand das stressigste „Serviceproblem“ darin, dass das Kühlmittel ausging. Werksleiter Stan Brown erinnert sich:„In Bezug auf Wartung und Zuverlässigkeit war es sehr zuverlässig und sehr beständig. Das einzige Problem, an das ich mich erinnern kann, war, dass einmal das Kühlmittel ausgegangen ist, und in diesem Fall hat DATRON hervorragenden Service und Support geleistet, indem es zusätzliches Kühlmittel bereitgestellt hat, um die Produktion am Laufen zu halten.“
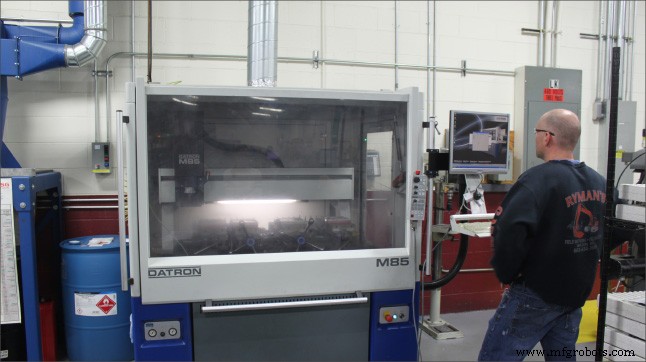
CNC-Maschine
- Herstellung von Gesundheit und Sicherheit mit autonomen Robotern
- Sensortypen mit ihren Schaltplänen
- Ihre Fertigungs-Toolbox für Produktivität der nächsten Stufe
- 3 echte Möglichkeiten zur Steigerung der Produktionsproduktivität mit Asset-Tracking
- Qualcomm steigert den Drohnennutzen mit 5G- und KI-fähiger Drohnenplattform
- Wie Saint-Gobain die Produktivität mit Markforged-Technologie steigert
- Optimierung der Fertigung mit Big Data Analytics
- Maximieren Sie die Produktivität mit der praxisorientierten Roboter-Bedienerschulung von Genesis
- 5 Minuten mit:Gavin Mee von UiPath
- Steigern Sie die Produktivität mit Benutzerberechtigungen