Technische Toleranzen:Typen, Grundregeln und Passungen
In der Maschinen- und Instrumentenbauindustrie bezieht sich die Austauschbarkeit von Teilen und Komponenten darauf, dass eine Charge von Teilen oder Komponenten derselben Spezifikation ohne Auswahl oder zusätzliche Reparatur (z. B. Werkbankreparatur) an der Maschine installiert werden kann, um die Spezifikation zu erfüllen Leistungsanforderungen.
Um der Austauschbarkeit von Teilen in der mechanischen Fertigung gerecht zu werden, sollten die Abmessungen von Fertigungsteilen innerhalb der gewünschten Toleranzgrenzen liegen. Diese muss einen einheitlichen Standard für Form, Größe, Genauigkeit und Leistung einer Teileart festlegen. Ähnliche Produkte müssen auch eine angemessene Sortierung haben, um die Produktserie zu reduzieren, dies ist die Produktstandardisierung. So entstand das Konzept der spezifizierten technischen Toleranzen und Passungen.
Was ist technische Toleranz?
Angenommen, ein 100-mm-Metallstab wird bearbeitet. Selbst wenn alle Stäbe in die gleiche Form bearbeitet werden sollen, kann aufgrund der Größe und Ausrichtung der Stäbe nicht die gesamte Fertigungsgenauigkeit des Stabs auf genau 100,00 mm bearbeitet werden. Obwohl die Design- und Fertigungsstandorte daran gearbeitet haben, solche Abweichungen zu reduzieren, können sie immer noch nicht auf Null kontrolliert werden.
Diese Größen- und Formabweichung schwankt grundsätzlich mit dem Zielwert als Mittelpunkt nach oben und unten. Daher werden der obere zulässige Wert und der untere zulässige Wert des oberen zulässigen Werts relativ zu der Zielgröße basierend auf der Verwendung des Metallstabs bestimmt. Die Differenz zwischen diesen beiden Werten (zulässiger Bereich) wird als „Toleranz“ bezeichnet.
Kurz gesagt, Toleranz ist die Abweichung von Teilen im Verarbeitungsprozess, Messmittelpräzision wegen der Auswirkungen der Abweichung muss vorhanden sein. Es ist die Menge an Variation, die für jede gegebene Dimension zulässig ist, um die richtige Funktion zu erreichen. Teileabmessungen innerhalb des gewünschten Toleranzbereichs werden qualifiziert. Technische Toleranzen umfassen Maßtoleranz, Formtoleranz und Positionstoleranz.
Maßtoleranz
Die Maßtoleranz ist die zulässige Abweichung einer Größe. Es sind die Grundlagen der technischen Toleranz. Der maximal zulässige Wert wird als maximale Abmessung bezeichnet. Und der Mindestwert wird als Mindestmaß bezeichnet.
Die Toleranz ist der absolute Wert der algebraischen Differenz zwischen der maximalen oberen Grenzgröße und der minimalen oberen Grenzgröße sowie der absolute Wert der algebraischen Differenz zwischen der oberen Abweichung und der unteren Abweichung.
Toleranz ist ein numerischer Wert ohne Plus- oder Minuszeichen und darf nicht Null sein. Bei konstantem Grundmaß gilt:je kleiner die Maßtoleranz, desto höher die Maßhaltigkeit. Angegebene Toleranzen geben die Anforderung an die Fertigungsgenauigkeit an und spiegeln den Schwierigkeitsgrad der Bearbeitung wider.
Formtoleranz
(1) Geradheit
Geradheit ist die Bedingung, dass die tatsächliche Form eines geraden Elements auf einem Teil eine ideale gerade Linie beibehält. Es wird auch als Grad der Geraden bezeichnet. Die Geradheitstoleranz ist die maximal zulässige Abweichung der tatsächlichen Linie von der idealen Linie. Das heißt, in der Zeichnung angegeben, um die tatsächliche Linienverarbeitungstoleranz durch den Toleranzbereich der Schwankung zu begrenzen.
(2) Ebenheit
Ebenheit ist die Darstellung der tatsächlichen Form der ebenen Elemente des Teils, um die ideale Ebene beizubehalten. Dies wird üblicherweise als Grad der Ebenheit bezeichnet. Die Ebenheitstoleranz ist die maximale Abweichung, die die tatsächliche Oberfläche gegenüber der Ebene zulässt. Das heißt, in der Zeichnung angegeben, um die tatsächliche Oberflächenbearbeitungstoleranz zu begrenzen, erlaubt der Toleranzbereich Änderungen.
(3) Zirkularität
Kreisförmigkeit ist der Zustand, in dem die tatsächliche Form der Elemente eines Teils gleich weit von seinem Mittelpunkt entfernt ist. Der Grad der Rundheit, wie er oft genannt wird. Die Rundheitstoleranz ist die maximal zulässige Abweichung des Ist-Kreises gegenüber dem Ideal-Kreis im gleichen Schnitt. Das heißt, der in der Zeichnung angegebene Variationsbereich begrenzt die Bearbeitungstoleranz des tatsächlichen Kreises.
(4) Zylindrizität
Die Zylindrizität bezieht sich auf den Punkt auf dem Umriss der zylindrischen Oberfläche des Teils und hält seine Achse im gleichen Abstand. Die Zylindrizitätstoleranz ist die maximale Variation, die der tatsächliche Zylinder zulässt, um der idealen Zylinderoberfläche gegenüberzustehen. Das heißt, wie in der Zeichnung angegeben, verwendet, um den zulässigen Bereich der tatsächlichen zylindrischen Bearbeitungstoleranz zu begrenzen.
(5) Profil einer Linie
Das Profil einer Linie soll die Kurve beliebiger Form auf der gegebenen Ebene des Teils darstellen und ihre ideale Form beibehalten. Profil einer Linientoleranz ist die zulässige Abweichung der tatsächlichen Kontur einer nicht kreisförmigen Kurve. Das heißt, wie in der Zeichnung angegeben, um den Variationsbereich zu begrenzen, der durch die tatsächliche Kurvenverarbeitungstoleranz zulässig ist.
(6) Profil einer Oberfläche
Das Profil einer Oberfläche ist eine Oberfläche mit beliebiger Form auf dem Teil, um seine ideale Form beizubehalten. Profil einer Oberflächentoleranz ist die zulässige Abweichung der tatsächlichen Kontur einer unrunden Oberfläche von der idealen Kontur. Das heißt, auf der Zeichnung angegeben, wird verwendet, um den tatsächlichen Oberflächenbearbeitungsbereich einzuschränken.
Positionstoleranz
Positionstoleranz bezieht sich auf die Gesamtmenge an Änderungen, die durch die Position des bestimmten Elements relativ zum Bezugspunkt zugelassen werden. Dies ist ein weiterer wichtiger Parameter der technischen Toleranz.
(1) Richtungstoleranz
Die Richtungstoleranz bezieht sich auf den Gesamtbetrag der Variation in der Richtung, die von der Referenz in Bezug auf die bestimmten Elemente zugelassen wird. Eine solche Toleranz verkörpert Parallelität, Rechtwinkligkeit und Winkligkeit.
(2) Standorttoleranz
Die Positionstoleranz ist der gesamte Bereich der Abweichungen in einer Position, die zulässig sind, um die tatsächlichen Elemente mit der Referenz zu korrelieren. Diese Art von Toleranz umfasst Konzentrizität, Symmetrie und Position.
(3) Rundlauftoleranz
Eine Rundlauftoleranz ist ein Toleranzwert, der aufgrund eines bestimmten Prüfverfahrens angegeben wird. Die Rundlauftoleranz kann in Kreisrundlauf und Gesamtrundlauf unterteilt werden. Die Toleranz der oben genannten Formen und Positionen wird kollektiv als geometrische Bemaßung und Tolerierung (GD&T) bezeichnet.
Allgemeine Verträglichkeit
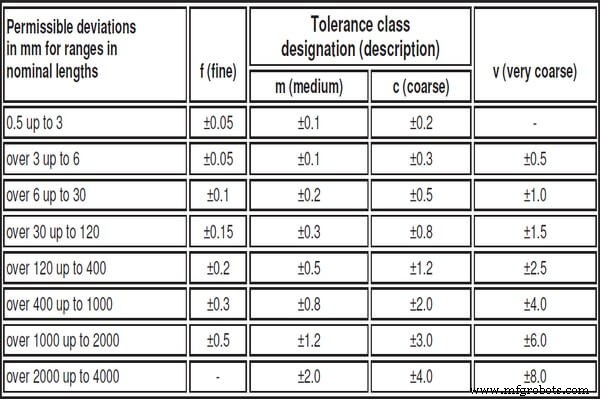
Abgesehen von der Toleranz für bestimmte Abmessungen und Eigenschaften müssen diese nicht spezifizierten Abmessungen in mechanischen Zeichnungen im Allgemeinen bestimmten Standards entsprechen. Am Beispiel unserer allgemein gebräuchlichen internationalen Ingenieurtoleranznorm DIN ISO 2768 ist die allgemeine Maßtoleranz m, die Formtoleranz K und die Kennzeichnungsmethode ISO 2768-mK. Im Folgenden finden Sie eine Tabelle mit Toleranzwerten für lineare Bemaßungen als Referenz.
Grundregeln
Regel Nr. 1 Umschlagregel
Voraussetzung dafür ist, dass Maßtoleranz und GD&T zueinander in Beziehung stehen. Die tatsächliche Toleranz des Bemaßungselements mit Hüllkurvenregel muss der maximalen Entitätsgrenze entsprechen. Dh seine äußere Funktionsabmessung überschreitet nicht die maximale Entitätsabmessung. Und seine Teildimension überschreitet nicht die minimale Entitätsdimension.
Regel #2 Unabhängigkeitsregel
Das Prinzip der Unabhängigkeit besteht darin, dass jede auf der Zeichnung angegebene Größe und Form in ihrer Position unabhängig ist und ihre eigenen Anforderungen erfüllen sollte. Es ist das Grundprinzip, dass das Verhältnis zwischen Maßtoleranz und Formtoleranz folgen sollte.
Regel #3 Toleranz der Positionsregel
Für die Positionstoleranz muss, wenn Bemaßungselemente Bezugselemente sind, S, L oder M im Merkmalskontrollrahmen angegeben werden.
Regel Nr. 4 Andere als die Toleranz der Positionsregel
Für andere als eine Positionstoleranz gilt RFS in Bezug auf die Toleranz, die Bezugsreferenz oder beides, wenn kein Modifikator angegeben ist. MMC muss im Feature Control Frame angegeben werden, wenn es angebracht und erwünscht ist.
Passt
Bei mechanischen Baugruppen wird das Verhältnis zwischen einer Bohrung gleichen Grundmaßes und dem Toleranzfeld der Welle als Passung bezeichnet. Da die tatsächliche Größe des Lochs und der Welle unterschiedlich ist, kann nach dem Zusammenbau ein Spalt oder eine Interferenz entstehen. Bei der Passung von Bohrung und Welle ist die algebraische Differenz aus Bohrungsgröße minus Wellengröße eine Lücke, wenn sie positiv ist, und ein Überschuss, wenn sie negativ ist.
Die Koordination wird entsprechend den Unterschieden der Lücken oder Interferenzen in drei Kategorien eingeteilt:
Freie Passform
Das Toleranzband der Bohrung liegt über dem Toleranzband der Welle, und jedes Bohrungspaar, das mit der Welle zusammenpasst, wird zu einer Passung mit Spiel (einschließlich eines Mindestspiels von 0).
Übermaßpassung
Das Lochtoleranzband liegt unter dem Achsentoleranzband, und jedes Lochpaar, das mit der Welle zusammenpasst, wird zu einer Presspassung (einschließlich eines Mindestspalts von 0).
Überanpassung
Die Bohrungstoleranz überschneidet sich mit der Wellentoleranz, sodass ein Bohrungspaar entweder mit Spiel oder Presspassung auf die Welle passt.
Das Wesentliche bei der Auswahl des geeigneten Toleranzniveaus besteht darin, den Widerspruch zwischen den Betriebsanforderungen der Maschinenkomponenten und dem Bearbeitungsprozess und den Kosten richtig zu lösen. Das Prinzip der Auswahl des Toleranzniveaus besteht darin, unter der Prämisse, die Anwendungsanforderungen der Teile zu erfüllen, ein niedrigeres Toleranzniveau als das Maximum festzulegen.
Die Anforderungen an die Präzisionsbearbeitung sollten mit den Fertigungsmöglichkeiten abgestimmt werden. Das heißt, bezahlbare Verfahrenstechnik, Montagetechnik und vorhandenes Equipment sollen genutzt werden. Falls erforderlich, müssen jedoch Strategien entwickelt werden, um die Genauigkeit der Ausrüstung zu verbessern und die Methode zu verbessern, um die Genauigkeit der Ware sicherzustellen.
Es ist sehr wichtig, das akzeptable Toleranzniveau für die passende Größe auszuwählen. Dadurch wird in vielen Fällen die Laufleistung, Lebensdauer und Zuverlässigkeit der passenden Komponenten bestimmt. Und gleichzeitig beeinflusst es die Herstellungskosten der Teile und die Produktionseffizienz.
CNC-Maschine
- s zur Verbesserung von Bearbeitungstoleranzen und Honen von CNC-Ausrüstung
- erfahrene Typen von CNC-Kühlmittelzufuhrsystemen in CNC
- Schafttoleranzen, Spannzangenpassungen und h6-Vorteile
- Fräsmaschinen – Einführung und besprochene Typen
- Was ist technische Toleranz? - Definition und Typen
- 3 Arten von Passformen und wie wählt man die richtige aus?
- 5 Arten von Sandgussfehlern und wie man sie vermeidet
- Arten von Metalllegierungen
- Bearbeitungstoleranzen 101:Grundlagen, Arten und Bedeutung von Bearbeitungstoleranzen verstehen
- Feinmechanik und ihre Rolle in der Fertigung