Kundenspezifische Werkzeuge, Werkstückhalterungen helfen dabei, Rotoren in Form zu bringen
Durch die Entwicklung eines genaueren Bearbeitungsprozesses für die Paarung Spiralrotoren können die Kompressormodelle dieses Whipple-Kompressors Luft effizienter in einen Motor drücken, um höhere PS-Zuwächse zu erzielen. Kundenspezifische Spann- und Formwerkzeuge ermöglichen es dem Unternehmen, Kompressorrotoren in einer Aufspannung auf seiner B-Achsen-Dreh-Fräsmaschine präzise zu fräsen.
Whipple Superchargers aus Fresno wurde 1987 vom ehemaligen Leiter der Rennmannschaft und Autobesitzer Art Whipple gegründet und stellt Doppelschrauben-Kompressoren für Automobil- und Schiffsrennfahrer und andere her, die die Leistung ihrer Motoren verbessern möchten. Diese Arten von „Leistungsaddierern“ (Turbolader und Lachgas sind andere) führen zusätzliche Luft in einen Motor ein, die über das hinausgeht, was der Motor alleine ziehen kann. Mehr Luft bedeutet, dass mehr Kraftstoff hinzugefügt werden kann, was sowohl den Hubraum als auch die PS-Leistung eines Motors wesentlich erhöht.
Entscheidend ist hier der genaue, berührungslose Eingriff zweier schraubenförmiger Rotoren im Inneren des Kompressorgehäuses. Beim Whipple-Design hat der männliche Rotor drei spiralförmige Lappen und der weibliche vier, erklärt Supercharger-Designer Garrett Bright. Diese rotieren gegeneinander und extrem eng. Wenn sich die Flügel von jedem an den Lufteinlassöffnungen vorbeibewegen, wird die Luft zwischen den Rotoren und dem Gehäuse eingeschlossen. Die Rotation des Rotors verringert nach und nach den Raum, den die Luft einnimmt, und komprimiert sie. Die Kompression wird fortgesetzt, bis der Innenflügelraum einer Auslassöffnung ausgesetzt wird, durch die die Luft mit einem höheren als atmosphärischen Druck in den Ansaugkrümmer abgegeben wird, der oben auf dem Motor sitzt.
Der Wirkungsgrad des Kompressors hängt von der Wirksamkeit der Abdichtung zwischen den zusammenpassenden Rotoren und dem Gehäuse ab. Zuvor hatte Whipple ausschließlich Rotoren verwendet, die von einem externen Unternehmen hergestellt und geliefert wurden. Es verwendet immer noch diese mitgelieferten Rotoren für einige seiner Kompressormodelle. Seitdem hat das Unternehmen jedoch damit begonnen, seine eigenen Rotoren im eigenen Haus zu konstruieren und zu bearbeiten, und der von ihm entwickelte Bearbeitungsprozess produziert zylindrischere und genauere Rotoren als die von seinem Lieferanten gelieferten, was zu Kompressordesigns führt, die 5 % effizienter sind als diese mit den mitgelieferten Rotoren.
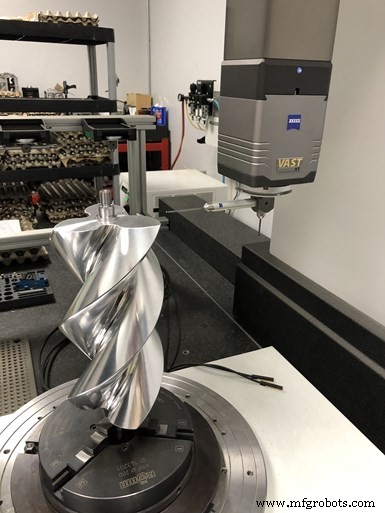
Messungen, die auf diesem KMG vorgenommen wurden, ermöglichten Whipple die Bestimmung die Genauigkeit der gelieferten Rotoren und der Rotoren in den Maschinen im eigenen Haus. Sein Ziel ist es, einen Abstand von 125 Mikron zwischen zusammenpassenden Rotoren zu erreichen, was jetzt mit seinen internen Multitasking-Bearbeitungsfähigkeiten erreicht werden kann.
Bright erklärt, dass Whipple angespornt wurde, seine eigenen Rotoren zu fertigen, nachdem es die Ergebnisse von Messungen an den Rotoren seines Lieferanten gesehen hatte, die auf seinem Zeiss Accura Koordinatenmessgerät (CMM) durchgeführt wurden. Dieses KMG verfügt über einen Drehtisch sowie die Vast-Scanning-Technologie von Zeiss und die Gear Pro-Option in seiner Calypso-Messsoftware. Laut Bright ist diese Software besonders effektiv für die Messung zusammenpassender Rotoren, da er spezifische Kontrollpunkte auf den spiralförmigen Profilen des männlichen und weiblichen Rotors zuweisen kann, wo sie sich treffen, um das Spiel zwischen den beiden an diesen Punkten zu bestimmen. Er legte fest, dass das Profil für jeden Rotor ±63 Mikrometer betragen sollte, mit dem Ziel, einen Abstand von etwa 125 Mikrometer zu erreichen. Whipple hat das nicht von seinem Rotorlieferanten bekommen.
Inhouse-Bearbeitung
Der unternehmensinterne Rotorbearbeitungsprozess mit Formwerkzeugen ähnelt dem seines Lieferanten, jedoch mit Werkstückhalterungsmodifikationen zur Erhöhung der Steifigkeit.
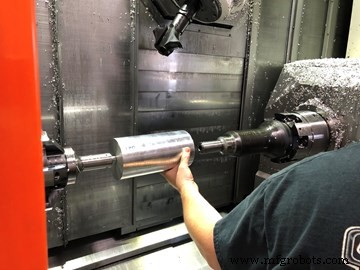
Wie ein Bediener einen 6061-Aluminium-Rotorrohling einlädt die Drehmühle, die Hauptspindel der Maschine und dann die Gegenspindelklemme auf den hervorstehenden Stahlwellenzapfen der Welle.
Die vor einigen Jahren für diese Anwendung angeschaffte Maschine ist eine Mazak Integrex e-420H-S II Dreh-Fräsmaschine mit B-Achsen-Fräskopf. Tatsächlich führt diese Drehmühle keine Drehung aus.
Zylindrische Rotorrohlinge aus Aluminium 6061 werden zunächst auf einer weiteren Maschine in Längsrichtung zentriert gebohrt, um eine Stahlwelle einpressen zu können. Während ein Bediener einen Rohling in die Integrex lädt, klemmen die Hauptspindel der Maschine und dann die Nebenspindel auf die vorstehenden Zapfen der Welle. Als nächstes wird die B-Achse der Maschine drastisch geneigt, um ein kundenspezifisches Formwerkzeug auszurichten, das in diesem Winkel dem gewünschten Rotornutprofil entspricht. Schließlich wird das Drehformwerkzeug entlang der Z-Achse bewegt, während der Rotor langsam gedreht wird, um jede Rille in mehreren Durchgängen zu erzeugen.
Anfänglich verwendete Whipple verlängerte ER-Spannzangen im Pullback-Stil, um die Wellenzapfen festzuklemmen. Die verlängerte Länge war erforderlich, um die Rohlinge von der Gegenspindel weg zu positionieren, damit die B-Achsen-Spindel genügend Freiraum hatte, um so weit über das Spannfutter der Gegenspindel zu kippen, wie es für die Aufnahme des Formwerkzeugs erforderlich war. Die Rückzugsfunktion dieser Spannzangen machte das Laden von Rotorrohlingen jedoch zeitaufwändig und herausfordernd. Das Anziehen der Spannzange (was zu einem Rückzug führte) belastete die Hauptspindel übermäßig, was bedeutete, dass die Gegenspindel der W-Achse eingefahren werden musste, um das Herauswählen der Last zu unterstützen. Andernfalls könnten Rattern oder schlechte Oberflächenbeschaffenheit die Folge sein. Infolgedessen mussten die Bediener kontinuierlich spannen und erneut spannen, bis der größte Teil der Last beseitigt war, was normalerweise 10 Minuten dauerte. Außerdem ersetzte Whipple ständig Spannzangen aufgrund der Abnutzung, die sie durch so viele Male angezogen und gelöst hatten.
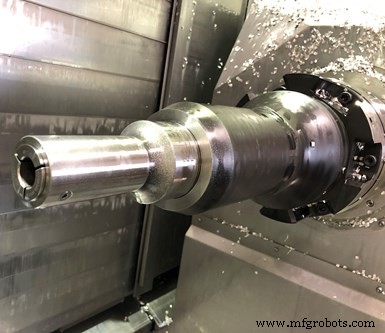
Im Gegensatz zu den bisher verwendeten ER-Spannzangen sind tote Spannzangen ziehen Werkstücke nicht zurück und belasten die Hauptspindel nicht, die beseitigt werden müssten. Dies reduzierte die Einrichtung von 10 auf zwei Minuten.
Auf Anraten von Kellen Bush, dem Anwendungstechniker von Mazak, der mit Whipple an diesem Projekt zusammengearbeitet hatte, wandte sich das Unternehmen an Hainbuch, um einen alternativen Ansatz für die Werkstückspannung zu entwickeln. Hainbuch-Verkaufsleiter Tom Chambers erklärt, dass die kundenspezifische Werkstückhaltelösung des Unternehmens nicht nur die größere Reichweite bietet, die erforderlich ist, damit die B-Achse der Maschine störungsfrei in den erforderlichen Winkel geneigt werden kann, sondern auch eine höhere Steifigkeit bietet und gleichzeitig das Umrüsten vereinfacht. Dies ist vor allem deshalb möglich, weil totlange Spannzangen anstelle von Rückzugstypen verwendet werden. Chambers sagt, Spannzangen mit toter Länge „klemmen im Raum“, was bedeutet, dass sich die Rotorrohlinge nicht bewegen, wenn die Spannzangen festgeklemmt werden. Dadurch wird keine zusätzliche Last auf die Hauptspindel aufgebracht, die herausgewählt werden müsste. Umstellungen dauern jetzt nur noch zwei Minuten.
Die Formwerkzeuge von Kyocera Unimerco, die Whipple zur Bearbeitung seiner Rotoren verwendet (ebenso wie der Rotorlieferant von Whipple), werden normalerweise nicht zum Schneiden von Metall verwendet. Laut Anders Varga, Verkaufsleiter bei Kyocera Unimerco, wird diese Art von Werkzeug typischerweise zum Schneiden von Holz, Verbundwerkstoffen und anderen Fasermaterialien verwendet. Dies ist in erster Linie auf den Druck zurückzuführen, der aufgrund der großen Kontaktfläche zwischen einem Metallwerkstück und langen Schneidkanten des Einsatzes auf das Werkzeug ausgeübt würde. Dass diese Werkzeuge in dieser Rotorbearbeitungsanwendung verwendet werden können, spricht für die Steifigkeit der Maschine mit Capto-Spindelschnittstelle und ihrer kundenspezifischen Werkstückspannung.
Durch die Verwendung von Formwerkzeugen, die dem spiralförmigen Rillenprofil der Rotoren entsprechen (Profile, die Bright verfeinert hat), entfällt das Polieren, das möglicherweise erforderlich wäre, wenn mehrere Schaftfräser zum Schnitzen der Rillen verwendet würden. Die Rotoren sind so bearbeitet, dass ihre Flügel so groß wie möglich sind, aber leicht unterdimensioniert, um eine spätere proprietäre Beschichtung zu ermöglichen. Whipple hält normalerweise zwei Schruppwerkzeuge und drei Endbearbeitungswerkzeuge für männliche und weibliche Rotoren bereit. Die Werkzeuge verwenden unbeschichtete Mikrokorn-Hartmetalleinsätze. Die Einsätze für die Schruppwerkzeuge werden über Schrauben an den Werkzeugkörpern befestigt; Endbearbeitungswerkzeuge werden daran angelötet.
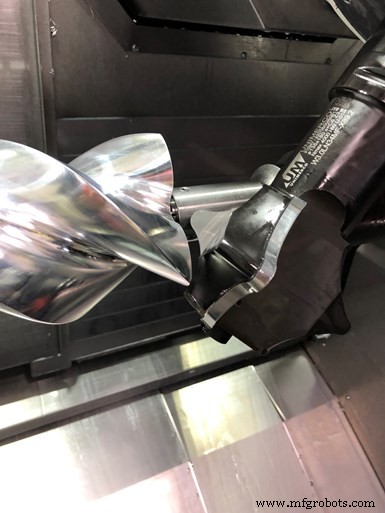
Durch die Verwendung von Formular-Tools hat Whipple keine um eine sekundäre Endbearbeitung durchzuführen, als ob Schaftfräser verwendet würden, um die Rotornuten herzustellen.
Jetzt erreicht dieser Bearbeitungsprozess nicht nur Brights 125-Mikrometer-Abstandsziel zwischen zusammenpassenden Rotoren, sondern die Zylindrizität des Rotors von Ende zu Ende ist konsistenter. Er sagt, dass der Unterschied in der Zylindrizität eines Endes eines Rotors im Vergleich zum anderen beim ursprünglichen Werkstückhalteansatz bis zu 10 Mikrometer betragen kann. Das wurde auf 1 Mikron reduziert. Die Rotorzykluszeiten sind auch etwas schneller. Die Zykluszeiten für einen männlichen Rotor betragen 14 Minuten und für einen weiblichen Rotor 20 Minuten. Aber für Whipple ist das Soße. Seine Hauptziele waren eine höhere Rotorbearbeitungspräzision und schnellere Umrüstungen, die beide verwirklicht wurden.
Industrielle Ausrüstung
- Mecademic Robotics expandiert mit seinem winzigen Roboter
- Schilling Robotics integriert Energid-Software in seinen Unterwasserroboter Gemini
- Rapid Tooling Service und seine effektiven Anwendungen
- Wie 3D-gedruckte Werkzeuge die Zukunft des Prototypings gestalten können
- Werkzeuge für Schweizer Maschinen
- Schweres Zeug drehen
- Schlanke Verbindungen herstellen
- Denken Sie darüber nach, in Live Tooling einzusteigen? Folgendes müssen Sie wissen
- 5 Hauptvorteile der kundenspezifischen Metallfertigung
- Was ist Kevlar? Eine kurze Anleitung