Lösungsbasierte Herstellung digitaler Verbundwerkstoffe
Die Natur baut Strukturen, die erstaunlich stark, vielseitig und anpassungsfähig sind, wachsen und als Reaktion auf ihre Umgebung funktionieren – denken Sie an Bäume, Knochen und Chitin. Letzteres bildet sowohl die harten Schalen und flexible Gelenke von Krebstieren. Die Konstruktionen der Natur produzieren wenig bis gar keinen Abfall, benötigen sehr wenig Energie und werden am Ende ihrer Lebensdauer recycelt. Im Gegensatz dazu sind von Menschenhand geschaffene Konstruktionen typischerweise vorgeschrieben, verbrauchen große Mengen an Energie, erzeugen giftige Abfälle und werden meist nicht recycelt. Laut Daten der US-Umweltschutzbehörde aus dem Jahr 2018 beträgt der Anteil der recycelten Materialien bei Kunststoffen nur 9 % (keine Veränderung seit 2010), 25 % bei Glas und 33 % bei Metallen (beide weniger als 2010). Obwohl die digitale Konstruktion und Fertigung rasant voranschreitet und die Produktion anspruchsvoller, multifunktionaler Strukturen und Komponenten ermöglicht, haben diese Technologien noch nicht die gleichen Fortschritte in Bezug auf Nachhaltigkeit gemacht.
Dies war die Inspiration und das Ziel für das Projekt Water-Based Digital Fabrication, das von der Mediated Matter Group am Media Lab des Massachusetts Institute of Technology (MIT, Cambridge, Massachusetts, USA) ab 2013 entwickelt wurde. Diese Initiative entwickelte eine neuartige digitale Fertigung Technologie, die die am häufigsten vorkommenden natürlichen Materialien der Erde mit einem robotergesteuerten Mehrkammer-Extrusionssystem kombiniert, das unterschiedliche Konzentrationen von Biokompositlösungen abscheidet – die erste war Chitin aus Krustentierschalen und Essigsäure – um Strukturen mit anisotropen Eigenschaften zu schaffen. Gradienten mechanischer, chemischer und optischer Eigenschaften werden über Längenskalen von Millimetern bis Metern erzeugt, wodurch nicht nur einzigartige Geometrien und Multifunktionalität, sondern auch das Potenzial zur strukturellen Selbstorganisation erreicht wird. Zum Beispiel können die nassen Abscheidungen so gestaltet werden, dass sie beim Trocknen als Reaktion auf gerichtete Verdampfungsspannungen innerhalb der mehrschichtigen Verbundstoffe Formen (z. B. Zylinder) bilden.
Diese lösungsbasierte digitale Fabrikation wurde als Brücke zwischen der biologischen und der gebauten Umgebung mit potenziellen Anwendungen in nachhaltigen Architekturplatten, recycelbaren Verpackungen und Konsumgütern oder leichten biologisch abbaubaren Autoteilen konzipiert. Das MIT erforschte schließlich Verbundwerkstoffe unter Verwendung von Zellulose-Mikrofasern, Pektin, Algen und keramischen Nanoplättchen. Aber was wäre, wenn Sie diese digitale Abscheidung auf Wasserbasis mit den kontinuierlichen und kurzfaserverstärkten additiven Extrusionstechnologien kombinieren könnten, die in den heutigen 3D-gedruckten Verbundwerkstoffen schnell vorankommen?
Warum Chitosan-Lösung?
Erste Experimente im Projekt Water-Based Digital Fabrication verwendeten Chitosan, das aus Chitin gewonnen wurde. Chitin ist das nach Cellulose am zweithäufigsten vorkommende natürliche Polymer auf der Erde. Es hat eine ähnliche chemische Struktur wie Cellulose und besteht nicht nur aus den hochmoduligen, hochzähen Schalen von Krebstieren und Insekten, sondern auch aus dem starken und dennoch flexiblen Gewebe ihrer Gelenke. Natürliche Materialien – insbesondere Polymere und Polysaccharide wie Chitin und Zellulose – stellen eine riesige erneuerbare Ressource dar, die in viel höheren Mengen produziert wird als künstliche synthetische Polymere, erklärt Laia Mogas-Soldevila, eine der wichtigsten MIT-Forscherinnen in diesem Projekt. Sie behauptet, dass Polysaccharid-Derivate bestehende petrochemische Polymere ersetzen könnten, neue Eigenschaftskombinationen bieten und eine nachhaltigere Herstellung ermöglichen könnten.
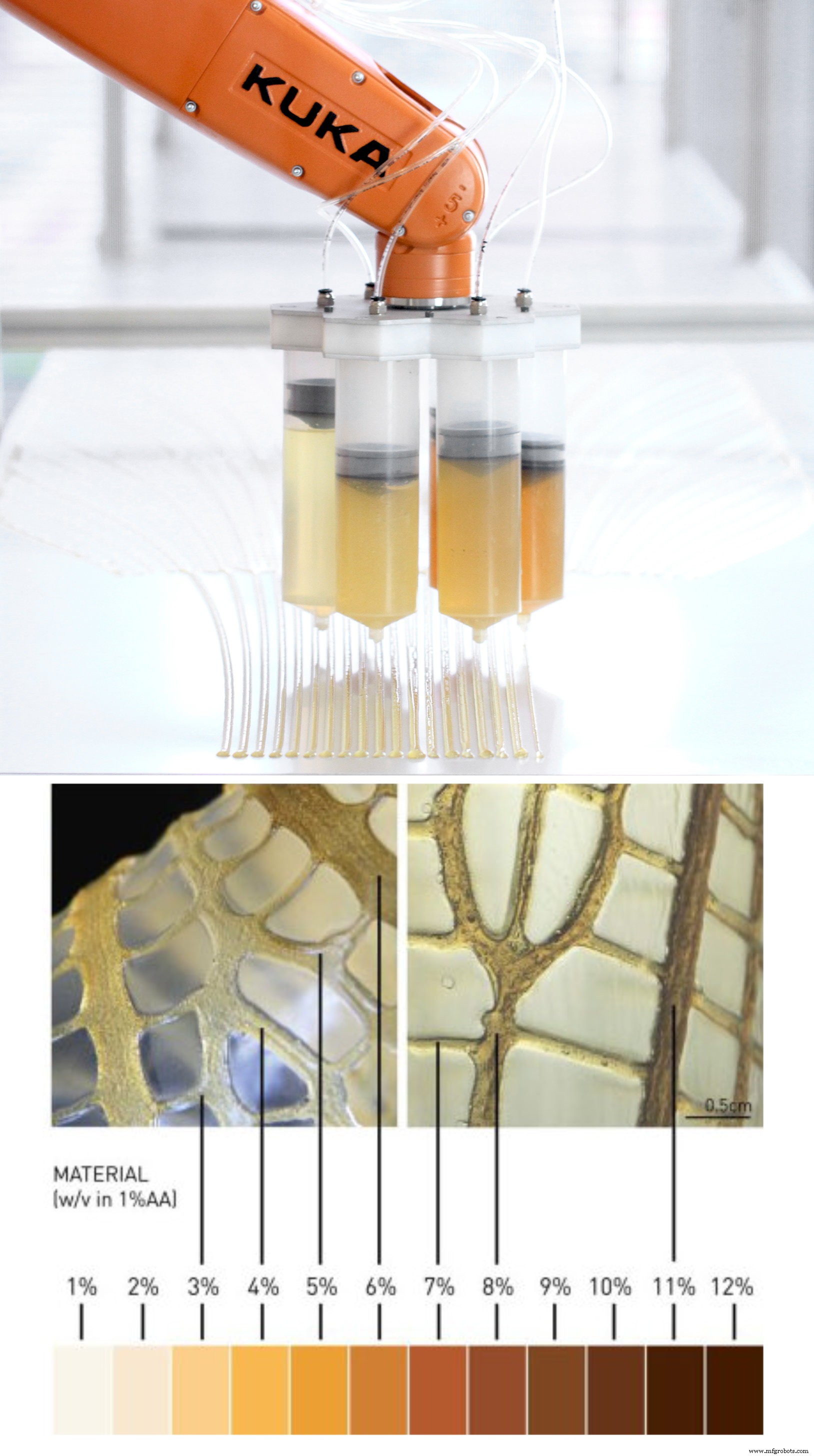
Mogas-Soldevila gibt in ihrer Dissertation aus dem Jahr 2015 „Water-based digital design and Fabrication:Material, Product, and Architecture Explorations in Printing Chitosan and its Composites“ einen hervorragenden Überblick über die Entwicklung der MIT-Technologie. Sie erklärt, dass die Idee, lösungsbasierte digitale Fabrikation zu verwenden, aus dem Studium von Inkjet- und Düsen-basierten Biofabrikationsmethoden entstand, um weiche Materialien als Gerüste für das Gewebewachstum herzustellen.
Es wurde beschlossen, eine düsenbasierte 3D-Abscheidung unter Verwendung von Chitosanpulver zu versuchen, das zu einem Gel bei Gewichts-zu-Volumen-Konzentrationen (w/v) von 1-12 % unter Verwendung von 4% w/v Essigsäure in wässriger Lösung verarbeitet wurde. Diese Hydrogele reichten von einer durchscheinenden Flüssigkeit mit einer Viskosität wie wässriger Honig bei einer Konzentration von 3% bis zu einem undurchsichtigen Material mit der Konsistenz von Naturkautschuk bei einer Konzentration von 12% (Abb. 1). Erste Ergebnisse von abgeschiedenem und getrocknetem Chitosanfolien zeigten eine Zugfestigkeit von 40 Megapascal, die Mogas-Soldevila in Faserrichtung als vergleichbar mit Nylonpolymer oder Holz bezeichnete. Die Strukturen wurden bei Raumtemperatur hergestellt und ausgehärtet.
Neuartige digitale Fertigungsplattform
Die maßgeschneiderte robotische additive Fertigungsplattform, die das MIT zum Auftragen der Chitosan-Gele entwickelt hat, kombiniert einen sechsachsigen Agilus KR1100-Roboterarm von KUKA (Augsburg, Deutschland) (eine 54-Kilogramm-Plattform mit 10 Kilogramm Nutzlast und ±0,03-Millimeter Wiederholgenauigkeit/Genauigkeit) mit ein auf Extrusion basierender Endeffektor. Der neuartige Endeffektor enthielt sechs Fässer für die Chitosan-Hydrogele, die mit einem computergesteuerten Luftdrucksystem verbunden waren, das positiven (Drucklufttank) und negativen (Vakuumpumpe) Luftdruck mit einem digitalen PSI-Regler und zwei Schrittmotoren zur Steuerung der Extrusion umfasste.
Dieser Endeffektor wog 4 Kilogramm einschließlich geladener Spritzen und Ablagerungsmaterial. Typische Durchflussraten reichten von 8 bis 4000 Kubikmillimeter pro Sekunde unter Verwendung von Düsen mit einem Innendurchmesser von 0,5 bis 8 Millimeter. Die lineare Bewegung des Systems variierte von 10-50 Millimeter pro Sekunde. Der Auftragbereich war 1.000 Millimeter lang und 500 Millimeter breit, jedoch wurden die Längenbeschränkungen später über ein verschiebbares Druckbett beseitigt.
Die Schrittmotoren, das pneumatische System und der Roboterarm wurden digital gesteuert, um die Vorschub-/Geschwindigkeitsverhältnisse zu koordinieren, variable Mischungsverhältnisse und Extrusionsraten zu ermöglichen und den Auftragsdruck und die Geschwindigkeit im laufenden Betrieb basierend auf den gewünschten Extrusionsgeometrien und Materialeigenschaften abzustimmen. Roboterbewegung und Extrusion waren nicht explizit verknüpft – d. h. beide Funktionen waren unabhängig voneinander – was eine unabhängige Steuerung jeder motorbetriebenen Spritze sowie die Verschiebung des Roboterarm-Endeffektors ermöglichte. Das System produzierte erfolgreich großformatige 3D-Formen ohne Formen und erreichte eine breite Palette von geometrischen Formen mit unterschiedlichen strukturellen Eigenschaften.
Digitales Design bis zur Deposition
Erste Herstellungsversuche basierten auf biologischen Strukturen wie Blättern und Libellenflügeln. Eine hauptsächliche Längsstruktur lieferte eine globale Form, die mit dickeren Durchmesserablagerungen und höheren Materialkonzentrationen für die Steifigkeit hergestellt wurde. Sekundärstrukturen wurden dann durch abgeschiedene Netzwerke aus Materialien mit dünnerem Durchmesser und geringerer Konzentration gebildet. Das Herstellungssystem verwendete verschiedene Techniken, um diese Strukturen aufzubauen:Aufbringen unterschiedlicher Konzentrationslösungen entlang bestimmter Pfade, digitale Drucksteuerung während der Abscheidung, um Materialbreite und -höhe zu steuern, und wiederholtes Schichten. Diese Strategien wurden in Positions-, Geschwindigkeits-, Druck- und Materialanweisungen kodiert, die in Echtzeit an den KUKA Roboter (Positionierung) und Extrusions-Endeffektor (Abscheidung) gesendet wurden.
Zunächst wurden Strukturen in einem CAD-Programm modelliert und dann mit einer eigenen Slicing-Software in gedruckte Schichten umgewandelt. Die digitale Steuerung hat die Abscheidungswege getestet und optimiert. Geometrische Werkzeugwege, die die Steuerung und den Betrieb des Extrusionssystems ermöglichen, wurden mit der Rhino3D-Modellierungssoftware (Robert McNeel and Associates, USA) und dem Skript-Plugin Grasshopper entworfen.
Das System kodierte dann eine Reihe unabhängiger Parameter, die dem digitalen Design zugeordnet sind, sowie grundlegende mechanische und chemische Materialeigenschaften. Es moderierte auch plattformabhängige Einschränkungen, die durch das Herstellungssystem gegeben sind, wie z. B. Viskositäten, Scherraten, Zylindertypen, Hardware-Reaktionszeiten und/oder Hüllgröße. Alle diese Parameter wurden dann mit designspezifischen . kombiniert Variationen wie Düsentyp, Materialzusammensetzung und zeitabhängige Druckkennfelder. Die resultierenden Berechnungen geben dann die erforderlichen Durchflussmengen, Fassnachfüllmuster und Positioniergeschwindigkeiten aus. Schließlich wurden kundenspezifische Fertigungsanweisungen generiert, die Bewegungs- und Extrusionsbefehle an die Positionierungs- bzw. Ablagerungssysteme kodieren.
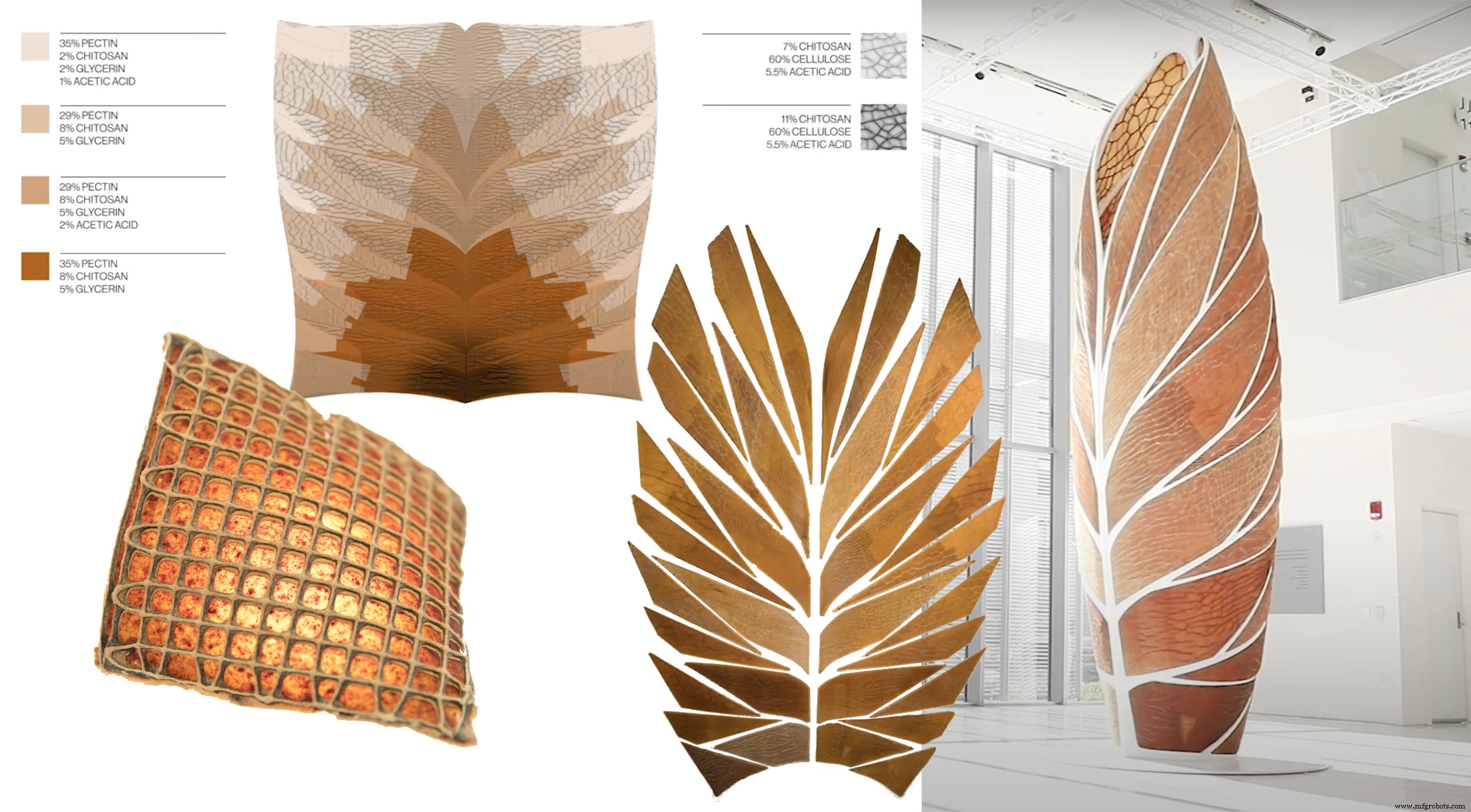
Erforschung neuartiger Strukturen
Die von Mogas-Soldevila beschriebenen Herstellungsversuche umfassen eine 50 Zentimeter lange Struktur, die von Libellenflügeln inspiriert ist. Seine strukturellen „Adern“ bestanden aus Chitosan-Gel, das mit natürlichem Natriumalginat-Pulver verdickt wurde, auf das eine klare zugfeste Membran aus 3% Chitosan-Gel gelegt wurde. Aufgrund der selbstreparierenden Eigenschaften der Materialien wurde die Membran während der Abscheidung mit den Adern verbunden. Dieses Konzept wurde in einer Vielzahl von blattartigen Strukturen von bis zu 3 Metern Länge weiter untersucht. In einem anderen Beispiel wurde ein 5 × 15-Millimeter-Gitter flach unter Verwendung einer Lösung von Cellulose-Mikrofaser in 2% Chitosan-Gel aufgebracht. Beim Trocknen bildete es einen 50 Zentimeter langen Zylinder und nutzte die Fähigkeit, interne Verdampfungsspannungen wie oben beschrieben zu entwerfen.
Diese Technologie wurde von Jorge Duro-Royo, Architekt und Ingenieur und leitender Forscher an der MIT Mediated Matter Group unter Prof. Neri Oxman entwickelt und in den Aguahoja-Projekten weiterentwickelt, bei denen hautähnliche Strukturen („Hojas“) geschaffen und geformt wurden wasserbasierte Lösungen ("Agua"). Aquahoja I umfasste einen 5 Meter hohen Architekturpavillon (Abb. 2) und eine Bibliothek mit Materialexperimenten, die 2018 ausgestellt und dann vom San Francisco Museum of Modern Art (SFMOMA, Kalifornien, USA) für seine Dauerausstellung erworben wurden . Aguahoja II war Teil einer Ausstellung im Jahr 2019, die vom Cube Design Museum (Kerkrade, Niederlande) und dem Cooper Hewitt, Smithsonian Design Museum (New York, N.Y., USA) gemeinsam organisiert wurde.
Die Roboterfertigungsplattform in Aguahoja-Projekten wurde so weiterentwickelt, dass sie sowohl Roboter- als auch Gantry-basierte Systeme umfasst. Der Pavillon bestand aus 95 einzelnen 3D-gedruckten Segmenten. Der weiße Rücken wurde mit einem handelsüblichen F900 Fused Deposition Modeling (FDM)-System und Acrylnitril-Styrol-Acrylat (ASA)-Thermoplast gedruckt. Die mehreren Bioverbundplatten wurden mit unterschiedlichen Steifigkeits-, Flexibilitäts- und Opazitätsgraden entworfen, um Bereiche zu schaffen, die als Struktur, Fenster und Umgebungsfilter dienen. Einige der Materialien in Aguahoja I verändern sich als Reaktion auf Feuchtigkeit und Hitze, andere werden im Laufe der Jahreszeiten dunkler oder heller. Die Materialien reichen von spröde und transparent bis flexibel und lederartig, aber alle können so programmiert werden, dass sie sich in Wasser (z
Mogas-Soldevila hat seitdem am Silklab innerhalb von Tufts Biomedical Engineering (Medford, Massachusetts, USA) promoviert und untersucht, wie Seide und andere Naturfasern und Materialien verwendet werden können, einschließlich derer, mit denen sie am MIT gearbeitet hat. Heute ist sie Assistenzprofessorin für Architektur an der Stuart Weitzman School of Design der University of Pennsylvania, wo sie materialgetriebenes Design an der Schnittstelle von Nachhaltigkeit und modernsten Biowissenschaften lehrt und erforscht. Einige ihrer jüngsten Arbeiten finden Sie unter dumolab.com. „Dies sind Materialien, die aus der Natur stammen und sehr leicht zu funktionie- ren sind – wir können sie mischen, dopen und umwandeln. Wir können sie tatsächlich auf spezifische Fertigungsmöglichkeiten abstimmen. Wir schauen uns an, was morgen als nächstes kommt.“
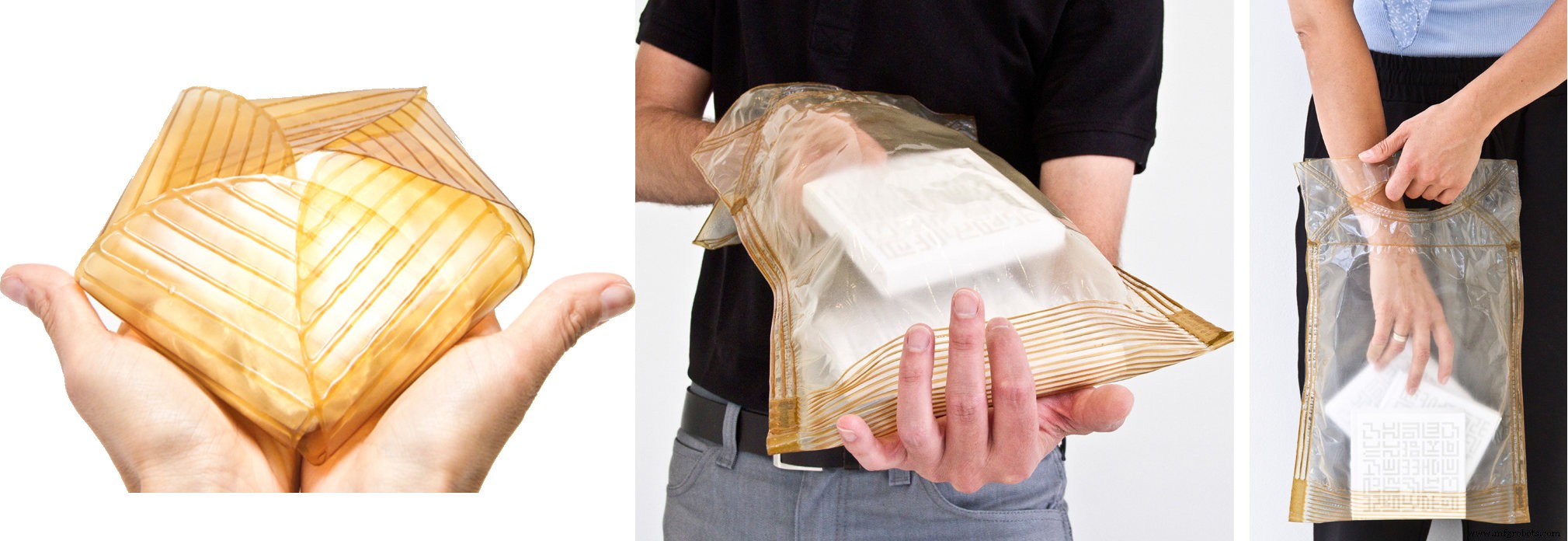
Verbundwerkstoff
- Eine Einführung in die Metallherstellung
- Voltmeternutzung
- Warum digital?
- Duroplastische Verbundwerkstoffe in HLK
- Hochwertige Werkzeuge für Duroplast-Verbundwerkstoffe
- Gründe für die Verwendung von Duroplast-Verbundwerkstoffen in Ihrem Produkt
- Kohlenstoff-Faser-Verbundwerkstoffe auf einer Rolle in Autorädern
- RS Electric Boats wählt Norco für die Herstellung von Verbundwerkstoffen
- Hochleistungsverbundwerkstoffe in Israel
- Was ist eine digitale Belegschaft?