Prepreg-Schneidsystem reduziert Abfall und beschleunigt die Montage des Schweizer Businessjets
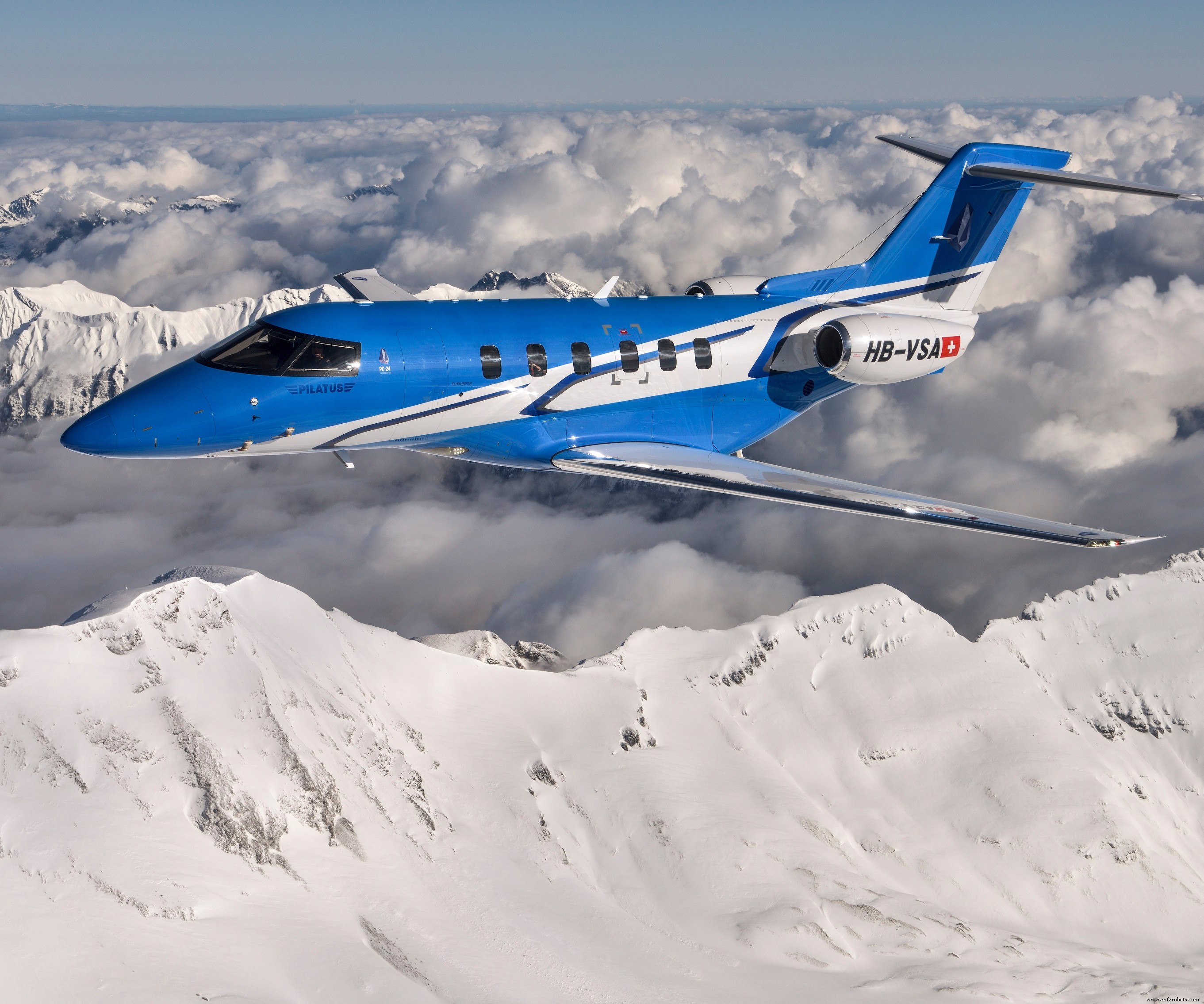
Quelle | Zünd
Dank Carbon- und Glasfaserkomponenten ist der PC-24 Business-Jet der Pilatus Aircraft AG (Stans, Schweiz) mit einem Basisgewicht von nur 5,3 Tonnen (weniger als 12.000 Pfund) ermöglicht Start und Landung auf kurzen, unbefestigten oder geschotterten Start- und Landebahnen, die normalerweise Turboprop-Flugzeugen vorbehalten sind. Tatsächlich ist der PC-24 kann auf einer Start- und Landebahn von nur 890 Metern (2.920 Fuß) starten und benötigt nur 720 Meter (2.362,2 Fuß) für die Landung.
Pilatus begann schon früh in seiner Geschichte der Flugzeugherstellung mit der Verwendung von Kohlefaserteilen, beginnend mit seinen ersten Kohlefaser- (CFK) und glasfaserverstärkten Kunststoff-(GFK)-Komponenten für den PC-6 Porter Metall Universalflugzeug. Die wenigen Kompositkomponenten des PC-6 , das 1959 zum ersten Mal abhob und eine Produktionsserie von etwa 500 Maschinen durchlief, bevor es durch seinen Nachfolger PC-12 ersetzt wurde , wurden von Hand aufgelegt. PC-6 Die Montage erforderte daher erfahrene Mitarbeiter und hohe Toleranzen für die Teile.
Der neueste Flugzeugtyp des Unternehmens, die PC-24 , besteht aus vielen Teilen, viele davon mit Toleranzen im Mμ-Bereich gefräst. Der PC-24 verwendet Verbundwerkstoffe hauptsächlich für Innen- und Außenverkleidungen. Auch die Triebwerksgehäuse und Flügelspitzen bestehen aus Kohlefaser, ebenso Fahrwerkstüren, Luftkanäle, diverse Rohre, Abdeckungen und Hinterkanten an den Flügeln.
Der PC-24 enthalten mehr Verbundkomponenten als der PC-6 1959 tat, aber die Montage ist jetzt viel schneller, was Pilatus zufolge aufgrund der Fortschritte in der Produktionstechnologie möglich ist. Der Schlüssel dazu sind dauerhafte Kostensenkung, Produktivitätsoptimierung und die Möglichkeit, moderne Fertigungstechnologien einzusetzen.
Digitale Prepreg-Schneidsysteme sind Teil dieses Trends. Pilatus setzt seit Jahren auf Schneidsysteme von Zünd (Altstätten, Schweiz) und hat 2019 ein Zünd G3 L-2500 Prepreg Schneidsystem hinzugefügt. Das G3-System schneidet in einem weitgehend automatisierten Prozess Materialien für die jeweiligen Bauteile einlagig und beschriftet anschließend die Zuschnitte mit einem integrierten Inkjet-Modul.
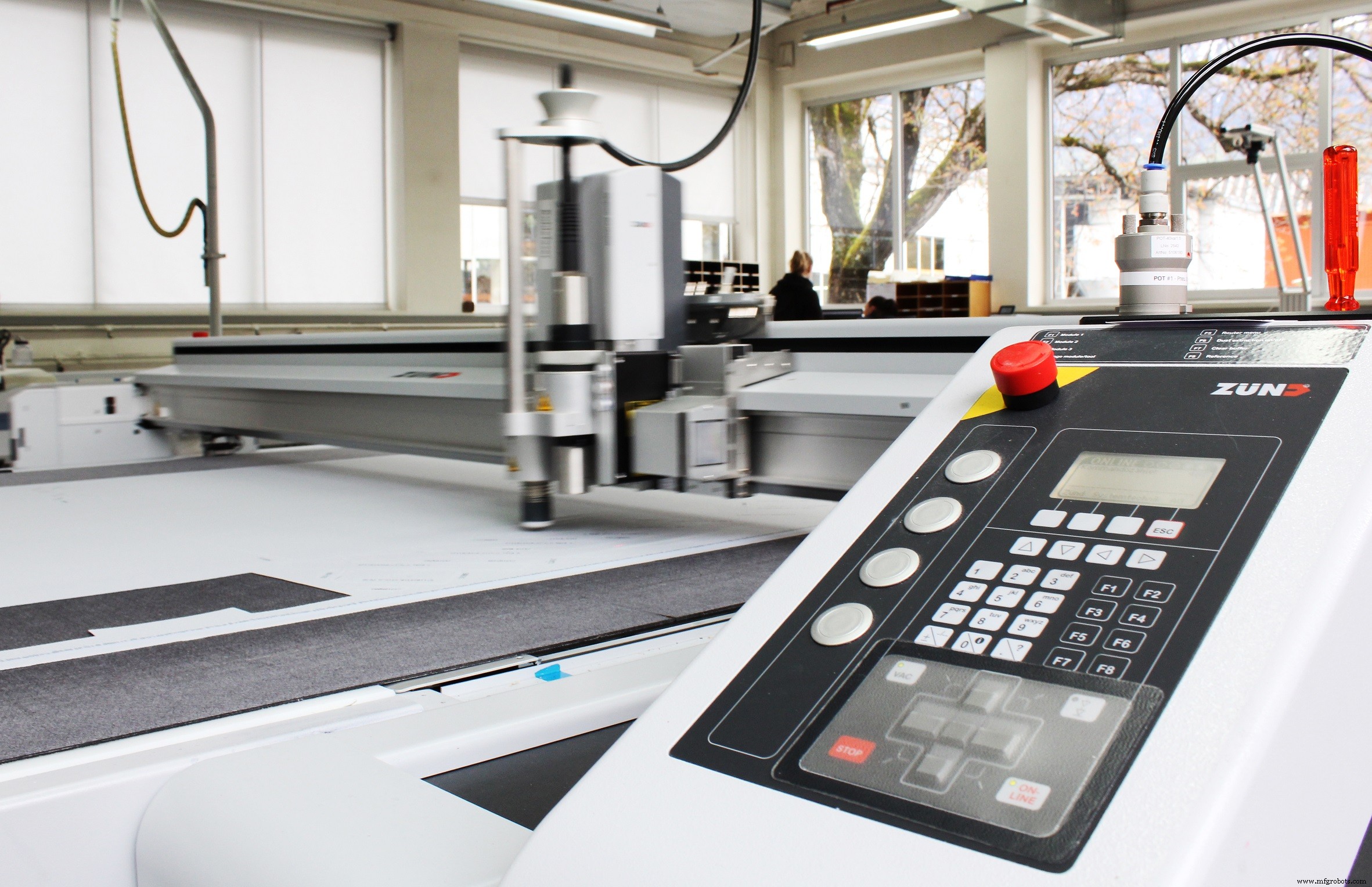
Quelle | Zünd
Pilatus verarbeitet etwa fünf Rollen Prepreg pro Tag (ca. 90 Quadratmeter) oder rund 90.000 Quadratmeter pro Jahr, wobei der Verbrauch stetig steigt, da immer mehr CFK- und GFK-Komponenten in den Maschinen des Unternehmens zum Einsatz kommen. Pilatus vertraut seit über 15 Jahren auf Zünd Digital Cutting, angefangen mit einem Cutter der PN-Serie. Die gestiegene Nachfrage nach Kohlefaserkomponenten begann die Kapazität zu überschreiten, was dazu führte, dass 2019 eine Zünd G3 L-2500 hinzugefügt wurde. Nach dem Schneiden werden die Teile montiert und bis zur Weiterverarbeitung gekühlt gelagert. Pilatus Verbundstrukturen können aus bis zu 350 Lagen Prepreg bestehen.
Ein weiterer Erfolgsfaktor von Pilatus ist die Konzentration auf die Steigerung der Produktivität. „Bei kostenintensiven Materialien wie Carbon oder Glasfaser geht es immer um Materialeffizienz und Optimierung“, sagt Patrick Rohrer, Projektleiter Systembeschaffung bei Pilatus. Wir arbeiten ständig daran, die Auslastung zu erhöhen und damit Abfall zu reduzieren – zumal wir noch wenige Recyclingmöglichkeiten haben.“
Das Unternehmen hat die Makulaturquote von 30 % auf 20 % gesenkt und nennt die effizienten Verschachtelungsfunktionen in Zünds Cut Center - ZCC-Software als wichtigen Faktor für diesen Erfolg. Die verschiedenen Lagen eines Teils sind statisch verschachtelt, d.h. die einzelnen Lagen eines Teils werden auftragsbezogen in der gewünschten Menge verschachtelt . Auch das dynamische Schachteln, bei dem die einzelnen Lagen von Teilen aus mehreren Aufträgen verschachtelt und in einer einzigen Schnittdatei zusammengefasst werden, kann, wann immer es sinnvoll ist, eingesetzt werden. Dadurch, so Zünd, erhöht sich der Nutzungsgrad des Rohstoffs weiter.
Faser
- Wie funktioniert Wasserstrahlschneiden?
- 5 Vorteile des Wasserstrahlschneidens
- Wasserstrahl vs. Laserschneiden:Was ist der Unterschied?
- Wie optimiert man eine Wasserstrahlschneidmaschine effizient?
- Was ist vor dem Kauf einer Wasserstrahlschneidmaschine zu beachten?
- Lösung reduziert Systemausbrüche für Solvay
- Zuverlässigkeit reduziert Zeit-, Talent- und Ressourcenverschwendung
- Abrasive Wasserstrahlbearbeitung und -schneiden
- Ist die Automatisierung Ihres Laserschneidsystems das Richtige für Ihre Anwendung?
- ICS wird im Hartford Business Journal vorgestellt