Deformationsmechanismus unter der Oberfläche beim Nanoschneiden von Galliumarsenid mithilfe molekulardynamischer Simulation
Zusammenfassung
Während des Nanoschneidprozesses wird monokristallines Galliumarsenid verschiedenen Oberflächen-/Untergrundverformungen und -schäden ausgesetzt, die die Leistung des Produkts erheblich beeinflussen. In diesem Artikel werden molekulardynamische Simulationen des Nanoschneidens auf Galliumarsenid durchgeführt, um den Deformationsmechanismus der Oberfläche und des Untergrunds zu untersuchen. Versetzungen finden sich im bearbeiteten Untergrund. Phasenumwandlung und Amorphisierung werden anhand von Koordinationszahlen untersucht. Die Ergebnisse zeigen die Existenz einer Zwischenphase mit einer Koordinationszahl von fünf während des Schneidprozesses. Modelle mit unterschiedlichen Schnittgeschwindigkeiten werden etabliert, um die Auswirkungen auf die Versetzung zu untersuchen. Der Einfluss der Kristallanisotropie auf den Versetzungstyp und die Dichte wird anhand von Modellen mit unterschiedlichen Schnittorientierungen untersucht. Darüber hinaus wird auch die Untergrundspannung analysiert.
Einführung
Galliumarsenid (GaAs) ist eine typische Art von III-V-Verbindung und auch eines der wichtigsten Halbleitermaterialien. Begünstigt durch seine großartigen Eigenschaften wie direkte Bandlücke, hohe Elektronenbeweglichkeit und hoher spezifischer Widerstand findet monokristallines Galliumarsenid breite Anwendung in verschiedenen Bereichen wie infrarotoptischen Geräten und Mikrowellengeräten. Mit der kontinuierlichen Weiterentwicklung seiner Produktion werden die strengen Anforderungen an Oberflächenrauheit, Oberflächenformgenauigkeit und Untergrundbeschädigung zunehmend gestellt. Die Nanoschneidtechnologie ist vorteilhaft, um die Leistung optischer Galliumarsenid-Elemente zu verbessern und ihr Anwendungsgebiet zu erweitern. Der Nanoschneidprozess von Galliumarsenid-Kristallen ist mit vielen Schwierigkeiten wie Sprödriss, Anisotropie und anderen unterirdischen Schäden konfrontiert. Daher ist die Untersuchung des Nanoschneidmechanismus von Galliumarsenid von großer Bedeutung für die Lösung der Bearbeitungsprobleme, die Verbesserung der Oberflächenqualität von Galliumarsenid und die Entwicklung einer entsprechenden nanometrischen Bearbeitungstechnologie.
Viele Studien führten nanoskalige Experimente mit Galliumarsenid durch. Fanget al. [1] verglichen die Nanoindentations- und Nanoscratch-Eigenschaften von Galliumarsenid und Silizium. Tayloret al. [2] untersuchten die Ultra-Low-Load-Nanoindentationen in Galliumarsenid (100) mit einer Würfeleckenspitze. Bradbyet al. [3] fanden die Pop-in-Ereignisse von Galliumarsenid in einer kugelförmigen Vertiefung. Fanget al. [4, 5] untersuchten die Bearbeitungseigenschaften weicher, spröder Halbleiter und erhielten erstmals durch Diamantdrehen eine Galliumarsenid-Spiegeloberfläche. Obwohl viele Studien über Eindrücke und physikalische Eigenschaften von Galliumarsenid berichtet wurden, ist wenig über seinen Nanoschneidprozess und den Mechanismus der Schadensbildung bekannt. Dies liegt vor allem an den großen Schwierigkeiten bei der Durchführung der Experimente und anschließenden Charakterisierungen. Einerseits ist es aufgrund des Nanometermaßstabs und der hohen Schnittgeschwindigkeit nahezu unmöglich, den Nanoschneidprozess zu begutachten und die nanometrischen Daten mittels Online-Messung zu messen. Andererseits ist es kostspielig, eine Reihe von nanometrischen Bearbeitungs- und Messexperimenten durchzuführen.
Die Simulation der Molekulardynamik (MD) ist eine der effizientesten Methoden, um den Mechanismus der nanometrischen Bearbeitung zu erforschen. Shimadaet al. [6, 7] bewiesen, dass die MD-Simulation ein effektiver Weg ist, den nanometrischen Bearbeitungsprozess zu beschreiben. Komanduriet al. [8] fanden das Strukturübergangsphänomen von Silizium im Nanoschneidprozess mit MD-Simulation. Pei et al. [9] untersuchten die Versetzungsbildung von Kupfer mit den großmaßstäblichen MD-Modellen der nanometrischen Bearbeitung. Lai et al. [10] untersuchten die Auswirkungen des kritischen Spanwinkels und der Materialverformung von Germanium beim nanometrischen Schneiden und untersuchten darüber hinaus den teilweise überlagerten Nanoschneidprozess [11]. Darüber hinaus hat sich der Multiskalenmodellierungsansatz im Bereich der Ultrapräzisionsbearbeitung stark entwickelt [12,13,14]. Die Multiskalensimulation kombiniert Simulationsmethoden in unterschiedlichen Skalen, wie z. B. das MD-Modell im Nanomaßstab und das FE-Modell im Nano-/Mikromaßstab [15], um den Bearbeitungsprozess umfassender und realistischer zu studieren. In diesem Beitrag werden die unter der Oberfläche liegenden Deformationsmechanismen des Nanoschneidprozesses fokussiert, daher wird die MD-Simulation als Forschungsmethode ausgewählt.
Was die untersuchten Materialien betrifft, so konzentrieren sich die meisten MD-Simulationsstudien in der nanometrischen Bearbeitung auf das Element Halbleiter wie Silizium und Germanium oder Metalle wie Kupfer und Aluminium. Über die numerische Analyse des Nano-Schneidens von Galliumarsenid wurde über weniger Studien berichtet. Fanet al. [16] untersuchten die duktile Reaktion von Galliumarsenid durch MD-Simulation und Drehexperimente. Yi et al. [17] untersuchten die Phasenumwandlung und Anisotropie von Galliumarsenid im Nanoscratch-Prozess mittels MD-Simulation. In diesem Beitrag wird eine Reihe von dreidimensionalen MD-Simulationen durchgeführt, um die duktile Verformung beim Nanoschneiden von monokristallinem Galliumarsenid zu untersuchen. Auch der Einfluss von Schnittparametern wie Schnittgeschwindigkeit und Schnittorientierung wird systematisch untersucht.
Methoden
MD-Simulationsmodelle werden etabliert, um das Verformungsverhalten von sprödem kristallinem Galliumarsenid im Nanoschneidprozess zu untersuchen. Das dreidimensionale MD-Simulationsmodell ist in Abb. 1 dargestellt. Das Werkstück ist als monokristallines Galliumarsenid aufgebaut, das im Zinkblende-Gitter kristallisiert, wobei Ga- und As-Atome die beiden FCC-Untergitter besetzen. Die Größe des Werkstücks beträgt 85 nm × 30 nm × 35 nm. Das Werkstückmodell besteht aus drei Schichten:Grenzschicht, thermostatische Schicht und Newtonsche Schicht. Durch die Grenzschicht wird das Werkstück fixiert, während die thermostatische Schicht auf eine konstante Temperatur von 293 K eingestellt wird, um die Wärmeabfuhr im realen Bearbeitungsprozess zu imitieren. Die Newtonsche Schicht ist der Schnittbereich, der den Mechanismus des Nano-Schneidprozesses aufdeckt. Die Bewegungen der Atome in der Newtonschen Schicht gehorchen dem klassischen zweiten Newtonschen Gesetz. Um das Diamantwerkzeug im realen Schneidprozess zu imitieren, wird ein Halbkugel-Diamantwerkzeugmodell mit einem Schneidenradius von 10 nm gebaut und die Schnitttiefe auf 4 nm eingestellt. Das Diamantwerkzeug wird auf bestimmte Geschwindigkeiten eingestellt, um in das Werkstück zu schneiden. Aufgrund der begrenzten Rechenressourcen wird das Modell minimiert und vereinfacht, ist aber dennoch überzeugend, um die duktile Verformung und Schadensbildung im Nanometerbereich zu erklären. Das Diamantwerkzeug ist als Halbkugel vereinfacht, um das duktile Abtragsverhalten in horizontaler Richtung wie Seitenströmung und Aufstau auf zwei Seiten des Werkzeugs zu untersuchen, was die wichtigen Eigenschaften der dreidimensionalen Simulation sind. Um den Einfluss der Prozessparameter zu untersuchen, werden Modelle mit unterschiedlichen Schnittgeschwindigkeiten und -orientierungen gebaut. Tabelle 1 listet die Parameter der Modelle auf.
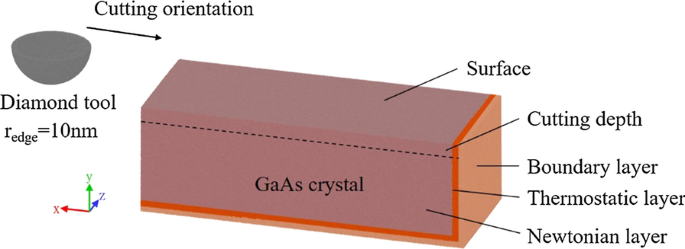
MD-Simulationsmodell
Das Potential ist die Grundlage für die Berechnung der Kraft und Energie zwischen Atomen und ist auch eine der wichtigsten Einstellungen in der MD-Simulation. In der vorangegangenen Studie wurde ein Potenzialsystem bestehend aus drei Potenzialarten für die Simulation von Galliumarsenid und Diamantwerkzeugmodell ermittelt [18]. In diesem System wird ein Tersoff-Brenner-Potential verwendet, um die Wechselwirkung zwischen Ga und As zu beschreiben, was einen guten Simulationseffekt zeigt [19]. Zur Beschreibung der Wechselwirkung zwischen Diamantwerkzeug und Galliumarsenid-Werkstück über eine quantenchemische Methode wird ein exponentielles Abstoßungspotential etabliert, das in Form eines vereinfachten Born-Mayer-Potentials vorliegt [18]. Im Diamantwerkzeug wird ein Tersoff-ZBL-Potential verwendet. Das potenzielle System ist in Abb. 2 zusammengefasst.
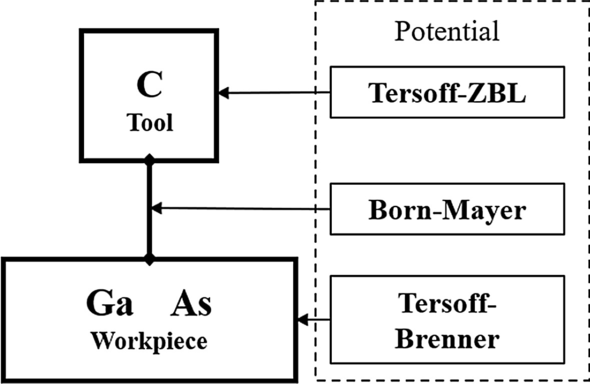
Potentielles System im Modell
Zur Durchführung der MD-Simulation wird LAMMPS verwendet, während die Visualisierung und Analyse über OVITO erfolgt, einschließlich der Dislokationsanalyse (DXA), Stressberechnung und Koordinationsanalyse. Die Relaxation des Werkstücks ist als NPT-Ensemble eingestellt, um die Energie des Systems zu minimieren und die freie Oberfläche zu stabilisieren, während der Nano-Schneidprozess als NVE-Ensemble eingestellt ist. Der Zeitschritt für die Integration in die Simulation beträgt 1,0 fs.
Ergebnisse und Diskussion
Allgemeine Beschreibung
Wie in Abb. 3 gezeigt, wird das Galliumarsenid-Werkstück bei einem Schnittabstand von 60 nm mit einer Schnittgeschwindigkeit von 400 m/s entlang der [\(\overline{1}\)00]-Richtung auf der (010) bearbeitet. Flugzeug. Das Werkstück wird mit der Verschiebung des Atoms im y . gefärbt -Richtung. Die Atome vor dem Werkzeug fließen nach oben und werden durch Extrusion zu Spänen. Eine Menge Atome fließen nach unten und bilden die bearbeitete Oberfläche. Auf beiden Seiten der bearbeiteten Nut türmen sich die Atome durch Extrusion und Pflügen des Werkzeugs mit einer Höhe von 2 nm auf. Das Ergebnis zeigt, dass die Verformung und Abtragung des spröden Galliumarsenid-Kristalls ein duktiles Verhalten darstellt, wenn die Bearbeitung im Nanometerbereich erfolgt. Im Simulationsprozess sind nur wenige Arsenid-Cluster erkennbar, die sich auf der bearbeiteten Oberfläche niederschlagen. Diese Studie zeigt das Vorhandensein von Arsenid-Ausfällungen nach dem Glühen [20]. Das Tersoff-Brenner-Potenzial konnte die Ausfällung von Arsenid-Clustern simulieren [19]. Beim Schneidprozess wird das Oberflächenmaterial mit einer Schneidhitze erhitzt und anschließend geglüht, wobei sich Arsenid-Cluster bilden. Diese Ausfällung ist jedoch beim Nanoschneidprozess kein großes Problem. Daher werden diese Atome bei der nachfolgenden Analyse ausgeblendet.
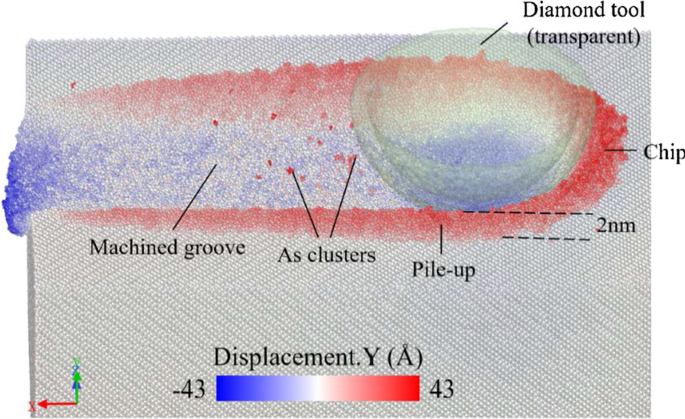
Ergebnis der Nano-Schneidsimulation, eingefärbt mit der Verschiebung des Atoms im y -Richtung
Vergleichen Sie den Schnittkraftverlauf während des Bearbeitungsprozesses in Abb. 4. Zunächst steigen Tangentialkraft und Normalkraft mit dem Einschneiden des Werkzeugs in den Werkstoff an. Die Seitenkraft schwankt um 0, da sich die Kräfte im z . aufheben -Richtung. Wenn die Kräfte stabilisiert sind, schwanken die Normalkraft und die Tangentialkraft um 1700 nN bzw. 700 nN. Es zeigt sich, dass die Kraft im y -Richtung ist aufgrund des großen effektiven negativen Spanwinkels des Diamantwerkzeugs, wie im Modell dargestellt, im Schneidprozess dominant. Der negative Spanwinkel bringt eine große Druckspannung mit sich, die beim Schneidvorgang eine hohe Normalkraft verursacht.
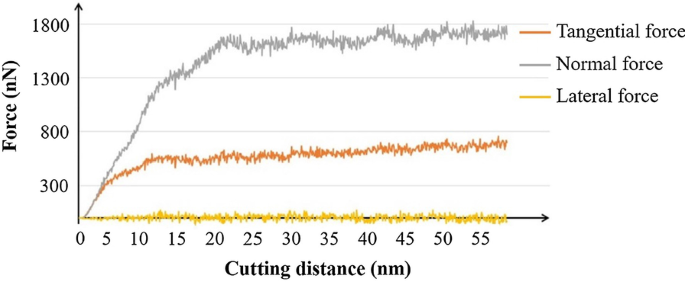
Schnittkraft im Nano-Schneidverfahren
Versetzungen und Stapelfehler
Die Schadensbildung unter der Oberfläche ist ein wichtiger Teil der Untersuchung des Nano-Schneidmechanismus. Um die Bearbeitungsparameter weiter zu optimieren, ist es notwendig, den Schadensbildungsmechanismus von Galliumarsenid während der Bearbeitung herauszufinden. Kristalle weisen eine Anisotropie der Atomstruktur auf, und dies ist eines der schwerwiegendsten Probleme im Bearbeitungsprozess, das die Prozessleistung mit unterschiedlichen Ausrichtungen beeinträchtigen würde.
Die Verteilung der Versetzungen im bearbeiteten Untergrund ist in Abb. 5 dargestellt, und die Werkzeugbewegung erfolgt entlang der Schnittrichtung (010) [\(\overline{1}\)00]. Die Versetzungen werden um die maschinell bearbeitete Rille herum beobachtet und bilden eine Versetzungsschicht von etwa 8 nm. Im bearbeiteten Untergrund gibt es zwei Haupttypen von Versetzungen. Die Versetzungen 1/2[110] gleiten hauptsächlich in den beiden Seitenwänden der bearbeiteten Nut, während sich die Versetzungen 1/6[112] unter dem Nutgrund verteilen. Die Versetzungen 1/2[110] und 1/6[112] erwiesen sich als perfekte Versetzungen (blaue Linien) bzw. partielle Versetzungen (grüne Linien). Die Bildung von Versetzungen bedeutet die transitiven Bewegungen der lokalen Atome, was bedeutet, dass die Verformung und Entfernung im duktilen Zustand erfolgen. Es ist bewiesen, dass das spröde Material auch in ausreichend kleinem Maßstab einen duktilen Zustand zeigt.
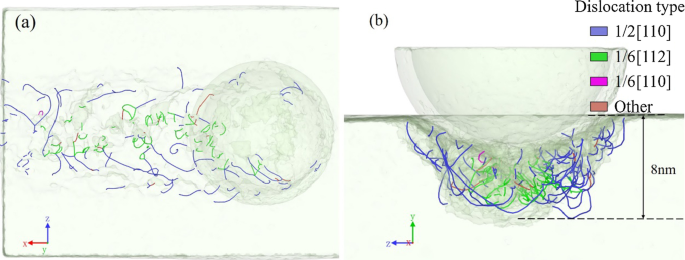
Perspektivische Ansichten der Versetzungsverteilung im bearbeiteten Untergrund, in a y -Richtung und b x -Richtung
Zur Bestimmung der Versetzungsbildung wird in der Regel die von Mises-Spannung verwendet, die unter Einbeziehung der Schubspannungskomponenten berechnet wird. Abbildung 6 ist die Querschnittsansicht der Versetzung und der von Mises-Spannungsverteilung. Durch die Extrusion konzentriert sich der hochbelastete Bereich unter dem Werkzeug. Wenn die vom Werkzeug ausgeübte Spannung die Streckgrenze des Werkstückmaterials überschreitet, gleitet das Material entlang der Gleitfläche, und die Relativbewegung des Gleitmaterials führt zu Versetzungen. Daher bilden sich Versetzungen und erstrecken sich aufgrund der hohen Spannungen im Bearbeitungsbereich in den Einkristall hinein. Die lokale Energie wird durch die atomare Bewegung freigesetzt.
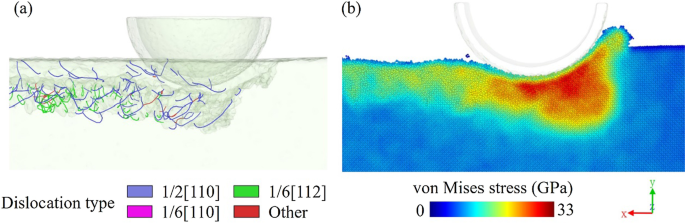
a Dislokationsverteilung und b von Mises Spannungsverteilung im Untergrund des Nano-Schneidmodells
Versetzungen in den spröden und duktilen Werkstoffen sind sehr unterschiedlich. Galliumarsenid ist ein typischer spröder Kristall, und die Versetzungen konzentrieren sich in der Nähe der bearbeiteten Oberfläche. Versetzungen in duktilen Materialien wie Kupfer dehnen sich jedoch aus und rutschen tief in das Werkstück hinein und bilden während des Schneidprozesses einen Versetzungscluster hoher Dichte [21], wie in Abb. 7a gezeigt. Versetzungen resultieren aus der duktilen Verformung von Materialien. Die Ausdehnung von Versetzungsclustern für duktile Materialien führt zu einem breiten Spektrum duktiler Verformungen und einer diffusen Spannung. Die Lokalisation von Versetzungen in spröden Materialien wie Galliumarsenid weist jedoch darauf hin, dass die duktile Verformung nur in Oberflächennähe ohne vollständigen Spannungsabbau erfolgt. Wenn die Spannung auf einen Schwellenwert konzentriert wird, können andere Arten von Schäden wie Phasenumwandlungen oder Risse auftreten. In unserer vorherigen Studie [18] wurde die Rissbildung von Galliumarsenid untersucht und es wurde festgestellt, dass sich der Abtragsmodus von duktilem Modus mit Versetzungsbildung zu spröder Modus mit Rissen ändert, wenn die Schnittgeschwindigkeit erhöht wird. Die Versetzungsbildung wird die Spannung freisetzen, die eine Rissbildung verursachen kann, und der Verformungsmodus wird in diesem Fall eher duktil als spröde.
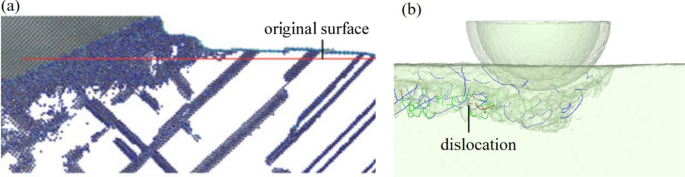
Versetzung beim Nanoschneiden verschiedener Einkristallmaterialien:a Kupfer [21] und b Galliumarsenid
Abbildung 8 zeigt die im bearbeiteten Untergrund gefundenen Stapelfehler. Atome im Werkstück werden anhand der Koordinationszahl eingefärbt. Zur bequemen Inspektion sind vierfach koordinierte Atome mit einer ursprünglichen Zinkblende-Struktur verborgen. Es kann beobachtet werden, dass im bearbeiteten Untergrund periodisch angeordnete Atome mit dreifacher Koordination existieren. In Kombination mit den Teilversetzungen unter dem Rillengrund können die Teilversetzungen, die hauptsächlich von den Korngrenzen oder freien Oberflächen emittiert werden, zur Bildung von Stapelfehlern oder Zwillingen führen [22, 23]. Die Stapelfehler im Modell sind keine vollständig versetzten Atomebenen, sondern mehrere kleine Bereiche an der Grenze von Einkristall und amorpher Schicht, daher existieren die Teilversetzungen an den Grenzen von Stapelfehlern. Daraus kann auch geschlossen werden, dass Stapelfehler im tatsächlich bearbeiteten Untergrund vorliegen können.
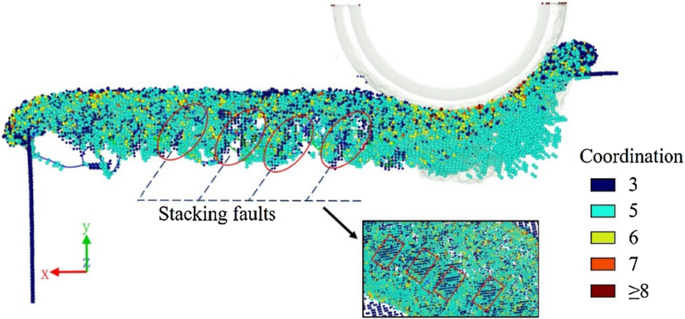
Stapelfehler im bearbeiteten Untergrund
Phasentransformation und Amorphisierung
Die Gitterstruktur des Materials kann sich aufgrund hoher Spannungen beim Nanoschneiden ändern. Durch das Studium des Phasenumwandlungsprozesses kann ein besseres Verständnis des Schneidens von Galliumarsenid erreicht werden, was für die Optimierung der Prozessparameter oder die Gestaltung des Vorbehandlungsexperiments vor dem Nanoschneiden nützlich ist.
Monokristallines Galliumarsenid hat unter Normaldruck und -temperatur eine Zinkblende-Struktur. Die Struktur ändert sich jedoch in ein sechsfach koordiniertes GaAs-II, wenn die Druckspannung 17 GPa erreicht [24]. Die Phasenumwandlung endet mit einer Wurtzit-Struktur, wenn die Spannung über 60 GPa steigt [25].
Abbildung 9a zeigt die Strukturänderung im Modell mit einer Schnittgeschwindigkeit von 400 m/s bei der Ausrichtung (010)[\(\overline{1}\)00]. Es wird beobachtet, dass eine Schicht des bearbeiteten Bereichs eine amorphe Struktur mit einer Dicke von etwa 6 nm ohne die charakteristische Struktur des Kristalls aufweist.
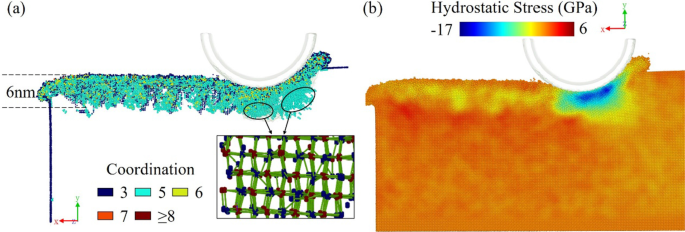
Verteilung von a hochkoordinierte Atome und fünffach koordinierte Struktur und b hydrostatische Spannungsverteilung
Es ist offensichtlich, dass einige Atome unter der Bearbeitungsposition zu einer Fünffachkoordinationsstruktur werden. Ähnlich der bct-5-Struktur von Siliziumkristallen, die sich unter Druckspannung bilden, wird diese Fünffachkoordinationsstruktur als Zwischenprodukt bei der Bildung des sechsfach koordinierten GaAs-I betrachtet. Die hydrostatische Spannung nimmt zu und verursacht die Verzerrung des Gitters beim Schneiden des Werkzeugs. Wie jedoch in der hydrostatischen Spannungsverteilung von Fig. 9b gezeigt ist, beträgt die maximale hydrostatische Spannung 17 GPa, was gerade den kritischen Wert der Umwandlung von GaAs-I zu GaAs-II erreicht. Der Untergrundbereich, in dem die hydrostatische Spannung höher als 17 GPa ist, ist sehr klein, und der größte Teil der Werkstückfläche weist eine hydrostatische Belastung unterhalb der Übergangsschwelle auf. Infolgedessen ist es schwierig, große Atomstücke mit einer sechsfach koordinierten Struktur zu finden, und die fünffach koordinierte Struktur ist eine Zwischenphase von GaAs-I bis GaAs-II.
Abbildung 10 zeigt die Kurven der radialen Verteilungsfunktion eines ausgewählten Bereichs im Schneidprozess, d. h. des Bereichs unter dem Diamantwerkzeug. Die radialen Verteilungskurven vor, während und nach der Verarbeitung werden berechnet. Das Werkstück hat zu Beginn eine geordnete Zinkblendestruktur, deren Verlauf aus regelmäßigen Spitzen besteht. Wenn das Diamantwerkzeug über den ausgewählten Bereich greift, zeigt die radiale Verteilungsfunktion einen ungeordneten Zustand sowohl im Nahbereich als auch im Fernbereich. Dies impliziert das Vorhandensein einer starken Amorphisierung mit der ungeordneten Anordnung der Atome in der Umgebung. Die Krümmung des bearbeiteten Untergrunds impliziert jedoch, dass sich die Struktur erholen kann und im Nahbereich geordnet und im Fernbereich ungeordnet wird. Mit dem Abbau von Spannung ändert das Material die Struktur in einen Zustand mit minimaler Energie. Atome mit einer Zwischenphase können in einen amorphen oder anderen Zustand übergehen. Somit zeigt die Kurve einen stabilen bearbeiteten Zustand mit amorphem Galliumarsenid. Es kann festgestellt werden, dass beim Bearbeitungsprozess eine seitliche Spitze bei 3,3 Å vorhanden ist und die Spitze verschwindet, wenn das Werkzeug verlässt. Dieses Phänomen zeigt die Bildung und das Verschwinden der Zwischenphase, die als elastische Verformung im Schneidprozess aufgefasst werden kann. Ohne die Kraft des Werkzeugs erholt sich ein Teil der Atome in die Zinkblende-Struktur und die anderen wechseln in eine andere stabile Phase oder einen amorphen Zustand, der die permanente duktile Verformung darstellt.
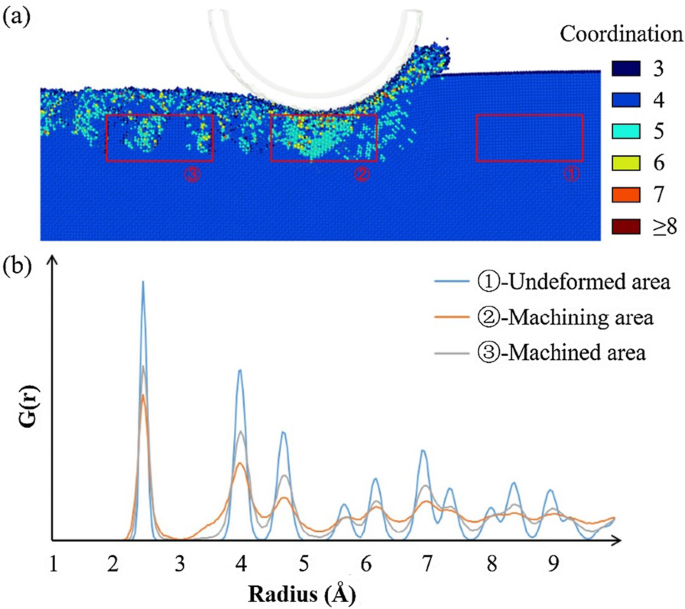
Ausgewählte Bereichsradialverteilungsfunktion:a ausgewählte Bereiche; b entsprechende radiale Verteilungsfunktionskurven
Schnittgeschwindigkeit und Ausrichtungseffekte auf die Verformung des Untergrunds
Die Bildung von Oberflächen-/Untergrundschäden wird von vielen Faktoren beeinflusst und unterschiedliche Schneidparameter beeinflussen die Bildung der Versetzung.
Die Versetzungsverteilungen bei unterschiedlichen Schnittgeschwindigkeiten sind in Abb. 11a–c gegenübergestellt. Die Versetzungsdichte nimmt mit zunehmender Schnittgeschwindigkeit allmählich ab. Besonders bei Schnittgeschwindigkeiten bis 200 m/s wird der bearbeitete Untergrund reichlich mit Versetzungen versorgt. Wenn der Schneidprozess einer hohen Dehnungsrate unterliegt, ist die Zeit für die Keimbildung und Ausbreitung der Versetzungen nicht ausreichend. Dadurch treten weniger Versetzungen auf und auch die durch Versetzungen induzierte duktile Verformung ist weniger dominant. Das Material wird schnell verformt und desorganisiert, und die Erholungszeit ist auch kurz, und amorphe Atome mit nicht regelmäßiger Struktur lassen sich leichter formen. Daher ist eine höhere Schnittgeschwindigkeit eine Möglichkeit, die Bildung von Versetzungen einzudämmen. Abbildung 11d–f sind die Querschnittsansichten der von Mises-Spannungsverteilung in den drei entsprechenden Modellen. Bei einer höheren Schnittgeschwindigkeit ist die Beanspruchung des werkzeugnahen Materials wegen der großen Schnittenergie relativ höher. Im Vergleich der drei Modelle weist das 800 m/s-Modell eine höhere Spannungskonzentration vor dem Werkzeug auf und der bearbeitete Untergrund weist einen kontinuierlicheren Spannungsbereich mit höheren Werten auf. Im Gegenteil, der Stress wird durch die Bildung von Versetzungen in den langsamen Modellen abgebaut. Die durch die Versetzungen induzierte duktile Verformung wird die lokale Dehnungsenergie und die Spannung freisetzen, die durch die Biegung und elastische Verformung des Gitters verursacht wird. Daher kann bei Werkstücken mit einer höheren Schnittgeschwindigkeit der Spannungszustand aufgrund des Fehlens von Versetzungen stark sein, was die Bildung von Rissen beim Schnittprozess erleichtert.
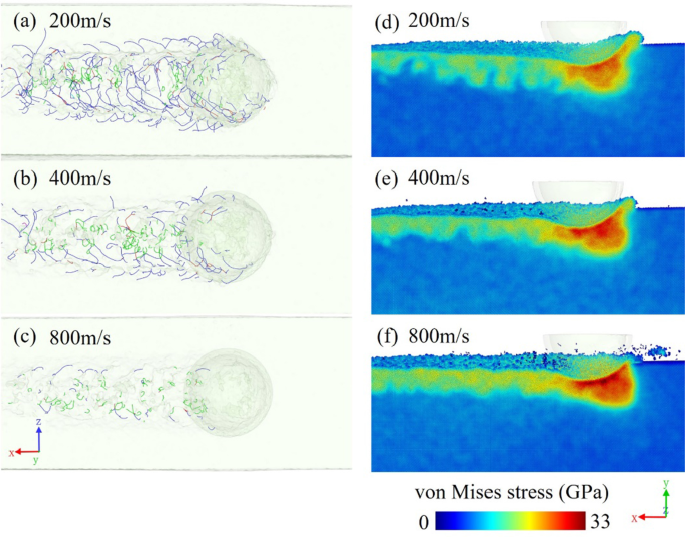
Perspektivische Ansichten der Versetzungsverteilung und der Von-Mises-Spannungsverteilungen in Modellen mit unterschiedlichen Schnittgeschwindigkeiten von a , d 200 m/s, b , e 400 m/s und c , f 800 m/s
Anisotropie ist ein ernstes Problem beim Nanoschneidprozess des Kristalls [26, 27], einschließlich des einkristallinen Galliumarsenids. Aufgrund seiner einkristallinen Struktur zeigt der Galliumarsenid-Kristall unterschiedliche Eigenschaften in verschiedenen Kristallorientierungen. Drei Modelle mit unterschiedlichen Schnittebenen und -orientierungen werden gebaut, um die Anisotropie zu untersuchen. Die Schnittorientierungen sind (010)[\(\overline{1}\)00], (\(\overline{1}\)10)[\(\overline{1}\)\(\overline{1}\ )0] und \((\overline{2}11)\,[\overline{1}\overline{1}\overline{1}]\). Abbildung 12a–f spiegeln die großen Unterschiede wider, die zwischen den Versetzungsverteilungen bestehen. Wie oben erwähnt, gibt es im (010)[\(\overline{1}\)00]-Modell zwei Arten von Versetzungen. Wenn die Schnittrichtung entlang der Richtung \((\overline{1}10)\,[\overline{1}\overline{1}0]\) liegt, befinden sich die meisten Versetzungen am Boden der bearbeiteten Nut, während einige geclusterte Versetzungen erstrecken sich bis zur Oberfläche vor dem Werkzeug. Auf beiden Seiten der Seitenwand in Abb. 12b sind nur wenige Versetzungen zu finden. Bei der Schnittrichtung \((\overline{2}11)\,[\overline{1}\overline{1}\overline{1}]\) werden baumartige Versetzungen beobachtet, die sich von der Mitte nach beiden Seiten erstrecken , die den bearbeiteten Untergrund bedeckt, wie in Abb. 12c gezeigt. Im Gegensatz zum ersten Modell gibt es jedoch nur wenige partielle Versetzungen in \((\overline{1}10)\,[\overline{1}\overline{1}0]\) und \((\overline{2} 11)\,[\overline{1}\overline{1}\overline{1}]\) Modelle, und die meisten Versetzungen sind perfekte Versetzungen entlang der [110]-Orientierung. Ebenso werden Stapelfehler im bearbeiteten Bereich von \((\overline{1}10)\,[\overline{1}\overline{1}0]\) und \((\overline{2}11) nicht gefunden. \,[\overline{1}\overline{1}\overline{1}]\) Modelle, entsprechend dem Fehlen von partiellen Versetzungen. Dies beweist auch den Effekt der Anisotropie im Material.
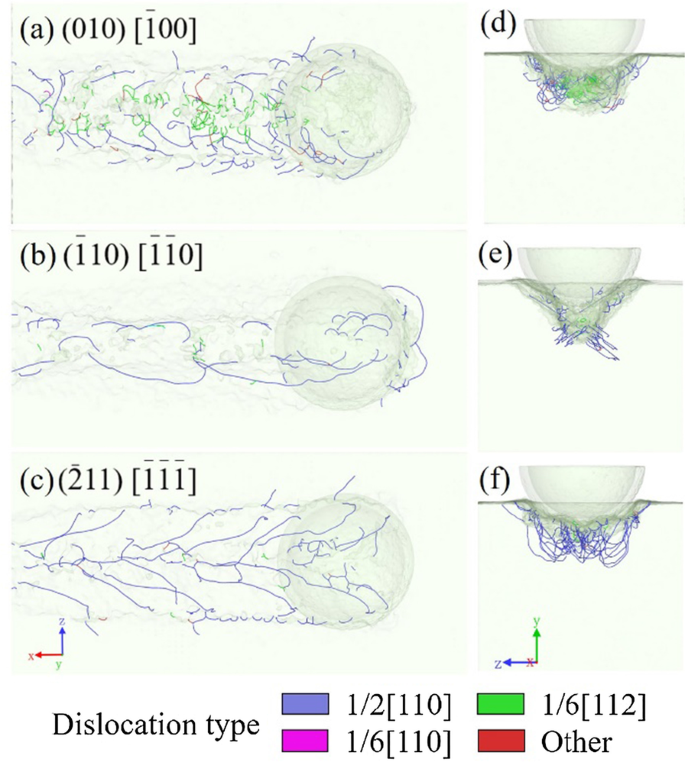
Perspektivische Ansichten der Dislokationsverteilung in den Modellen mit Schnittorientierungen entlang a , d \((010)\,[\overline{1}00]\), b , e \((\overline{1}10)\,[\overline{1}\overline{1}0]\) und c , f \((\overline{2}11)\,[\overline{1}\overline{1}\overline{1}]\)
Abbildung 13a–f vergleichen die Versetzungsverteilung und die von Mises-Spannungsverteilung der drei Modelle mit unterschiedlichen Schnittorientierungen. Die Kristallorientierung hat einen offensichtlichen Einfluss auf die Spannungsausbreitung. In den Modellen (010)[\(\overline{1}\)00] und \((\overline{2}11)\,[\overline{1}\overline{1}\overline{1}]\) , ist die Belastung vor dem Diamantwerkzeug konzentriert, aber die Erstreckungsrichtungen sind unterschiedlich. Der konzentrierte Spannungsbereich des Modells \((\overline{1}10)\,[\overline{1}\overline{1}0]\) ist jedoch breiter und der Bereich hoher Spannung vor dem Werkzeug reicht bis zur Oberfläche. Aufgrund der unterschiedlichen Kristallorientierungen sind die Spannungskomponenten entlang der Gleitrichtung unterschiedlich, was zu unterschiedlichen Erscheinungen von Versetzungen führt. Wenn der Winkel der Spannungsrichtung und der Gleitfläche klein ist, tritt die Gleitfähigkeit eher auf und das Material verformt sich im duktilen Modus. Im Gegensatz dazu neigt der Riss und Sprödbruch zur Initiierung, wenn das Verhältnis der Zugspannung senkrecht zur Spaltebene zur Schubspannung entlang der Gleitebene zunimmt.
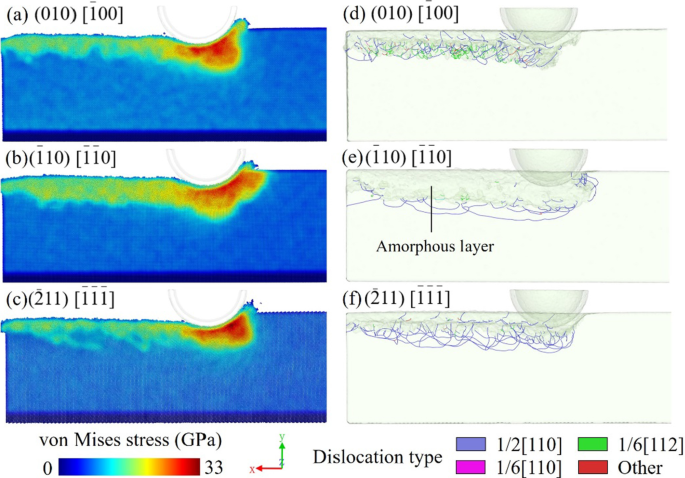
Von Mises Spannungsverteilung und Versetzungsverteilung in den Modellen mit Schnittorientierungen entlang a , d \((010)\,[\overline{1}00]\), b , e \((\overline{1}10)\,[\overline{1}\overline{1}0]\) und c , f \((\overline{2}11)\,[\overline{1}\overline{1}\overline{1}]\)
Vergleicht man die Spannungs- und Versetzungsverteilungen, können die Modelle mit einer höheren Versetzungsdichte eine geringere Spannung im bearbeiteten Untergrund aufweisen. Abbildung 13e zeigt eine dickere amorphe Schadensschicht im Untergrund des \((\overline{1}10)\,[\overline{1}\overline{1}0]\)-Modells, die den dichten Versetzungsregionen in . entspricht die anderen Modelle. Dieses Phänomen zeigt, dass sich Anisotropie auf die Schadensarten auswirken kann. Im Modell \((\overline{1}10)\,[\overline{1}\overline{1}0]\) kann die konzentrierte Spannung wegen der geringeren Versetzungsbildung nur schwer abgebaut werden. Als Ergebnis wird die Anordnung der Atome unter einem starken Spannungszustand gestört. Im bearbeiteten Untergrund ist der Spannungsbereich größer und die Eigenspannung höher. Im Gegensatz dazu hat das Modell \((\overline{2}11)\,[\overline{1}\overline{1}\overline{1}]\) eine dünnere Spannungsschicht im bearbeiteten Untergrund aufgrund des größeren Versetzungsdichte. Durch die Versetzungsbildung wird ein Teil der Spannung während des Schneidvorgangs freigesetzt. In der vorherigen Studie [18] zeigt der bearbeitete Untergrund einen starken Spannungszustand und amorphe Schäden, wenn der duktile Schadensmodus von Versetzung zu Amorphisierung wechselt. Die Risse unter der Oberfläche bilden sich leichter an der Grenze des amorphen und des Einkristalls. Daraus lässt sich ableiten, dass die Wahrscheinlichkeit von Rissen höher ist, wenn die Schnittorientierung entlang der Richtung \((\overline{1}10)\,[\overline{1}\overline{1}0]\) liegt. Die Bildung von Versetzungen kann die Bildung von Sprödschäden verringern. Neben dem Spaltungsmechanismus ist dies auch ein Grund, warum die Rissbildung durch Anisotropie beeinflusst wird.
Beim Schneidprozess wird das Material in der Nähe des Schneidwerkzeugs hohen Belastungen und starken Kompressionen ausgesetzt, was zu strukturellen Veränderungen des Materials wie Phasenumwandlung und Amorphisierung führt. Unter der amorphen Schicht tritt in einem größeren Bereich ein Gleiten auf und es bilden sich aufgrund der weit verbreiteten Spannungseffekte Versetzungen im Einkristall. Dies sind die wichtigsten duktilen Verformungen beim Nanoschneiden von Galliumarsenid. Unterschiedliche Schneidbedingungen beeinflussen den lokalen Spannungszustand und die Leichtigkeit der Versetzungsbildung. Wenn die Versetzungen aufgrund der hohen Verarbeitungsgeschwindigkeit oder Anisotropie schwierig zu erzeugen sind, wird der Modus der duktilen Verformung aufgrund der durch nicht gelöste Spannungen verursachten Amorphisierung dazu neigen, amorph dominiert zu werden. Der Riss wird sich auch in dieser Situation leicht bilden. Im Gegenteil, Versetzungen sind die Hauptkomponente der duktilen Verformung, wenn die Bedingungen für den Materialschlupf geeignet sind.
Schlussfolgerung
Die MD-Simulation wird verwendet, um den Mechanismus der Schadensbildung beim Nanoschneidprozess von Galliumarsenid-Kristallen zu untersuchen. The atomic motion and cutting force of the process are also analyzed. The dislocation, stacking fault, and phase transformation are mainly studied as the surface/subsurface damages. The conclusions can be summarized as follows:
- 1.
In the nano-cutting of gallium arsenide, the dislocation and structural transformation are found as the main deformation mechanism in the machined subsurface.
- 2.
Dislocations and stacking faults are observed in the machined subsurface groove, and the formations of stacking faults and partial dislocations are consistent.
- 3.
An intermediate phase with five-coordination is found in front of the tool because hydrostatic stress is close to but not higher than the transition threshold (17 GPa). An amorphous layer forms in the machined subsurface.
- 4.
With increasing cutting speed, the dislocation density decreases because of the high strain rate. Anisotropy has a great effect on the dislocation type and density. Partial dislocations are easier to form in the (010) [\(\overline{1}\)00] model. Moreover, the \((\overline{1}10)\,[\overline{1}\overline{1}0]\) model has a lower dislocation density and a more severe amorphization.
Verfügbarkeit von Daten und Materialien
The datasets generated or analysed during the current study are not publicly available due the data also forms part of an ongoing study, but are available from the corresponding author on reasonable request.
Abkürzungen
- MD:
-
Molekulardynamik
- GaAs:
-
Gallium arsenide
- FE:
-
Finite element
- FCC:
-
Face centered cubic
- Tersoff-ZBL:
-
Tersoff-Ziegler–Biersack–Littmark
- LAMMPS:
-
Großskaliger atomarer/molekularer massiv-paralleler Simulator
- OVITO:
-
Visualisierungstool öffnen
- NPT:
-
Number-pressure–temperature, isothermal-isobaric ensemble
- NVE:
-
Number-volume-energy, microcanonical ensemble
Nanomaterialien
- C# verwenden
- Aufstieg in Richtung 7-nm
- Einsatz von Winkeln zur Verbesserung der Zukunft der Elektronik
- Intelligenter Beton mit Nanopartikeln
- Oberflächeneffekt auf den Öltransport in Nanokanälen:eine molekulardynamische Studie
- Molekulardynamische Modellierung und Simulation des Diamantschneidens von Cer
- Studie zum Effekt der Aufprallrichtung auf den nanometrischen Schleifprozess mit Molekulardynamik
- Herstellung und optische Eigenschaften von GeBi-Filmen unter Verwendung der Molekularstrahl-Epitaxie-Methode
- Untersuchung des nanoskaligen Reibungsverhaltens von Graphen auf Goldsubstraten mittels Molekulardynamik
- Wie Indium-Gallium-Arsenid (InGaAs) die SWIR-Erkennung verbessert