Anpassung von Ultraschallsensoren für die Optimierung und Steuerung von Verbundwerkstoffprozessen
Dieser Blog ist eine Fortsetzung meines Berichts über das Projekt CosiMo („Verbundwerkstoffe für nachhaltige Mobilität“). Dieses Projekt wurde 2018 von Faurecia Clean Mobility (Nanterre, Frankreich) ins Leben gerufen, um die „intelligente Herstellung“ einer Batteriekastenabdeckung aus Verbundwerkstoff zu demonstrieren. Das 1.100 Millimeter lange und 530 Millimeter breite Herausforderungsteil verfügte über Glasfaservlies- und unidirektionale Kohlefaserverstärkungen sowie Metall- und Schaumstoffeinlagen, eine komplexe Geometrie mit verschiedenen Radien und Dicken von 2,5 bis 10 Millimetern. Das Teil wurde mit thermoplastischem Harzspritzpressen (T-RTM) geformt, bei dem Caprolactammonomer eingespritzt und dann während des beheizten Presszyklus in-situ polymerisiert wurde, um einen Polyamid 6 (PA6)-Verbundstoff zu bilden. Das Hauptziel des Projekts war die Untersuchung eines vollautomatisierten Prozesses mit geschlossener, sensorbasierter Prozesssteuerung.
In diesem Blog wird das Netzwerk von 74 Sensoren, das im CosiMo-Challenge-Teil verwendet wird, genauer untersucht, insbesondere die von der Universität Augsburg (UNA, Augsburg, Deutschland) entwickelten Ultraschallsensoren und wie die Daten aller Sensoren verwendet wurden, um ein digitales Modell des Prozesses (digitaler Zwilling).
Basierend auf dem Erfolg von CosiMo und dem Bedarf an einem Entwicklungszentrum für sensor- und KI-basierte Fertigungsentwicklung hat die UNA in Zusammenarbeit mit dem CosiMo-Projektpartner Deutsches Zentrum für Luft- und Raumfahrt (DLR) Zentrum für Leichtbauproduktionstechnologien ( ZLP, Augsburg) und dem Fraunhofer-Institut für Gießerei-, Verbundwerkstoff- und Verfahrenstechnik (Fraunhofer IGCV). „Wir errichten eine neue, 5.000 Quadratmeter große Anlage, die wir gemeinsam betreiben werden“, sagt Dr. Markus Sause, UNA-Professor und Direktor des Augsburg AI Production Network. „Wir werden automatisierte Produktionszellen haben, von denen viele auf Verbundwerkstofftechnologien ausgerichtet sind, die es uns ermöglichen werden zu demonstrieren, was KI leisten kann.“
CosiMo-Sensornetzwerk
Für das CosiMo-Projekt wurden 74 Sensoren in das Stahl-RTM-Werkzeug der Christian Karl Siebenwurst GmbH &Co. KG (Dietfurt, Deutschland) zum Formen des T-RTM-Batteriekastendeckels integriert. Zur Überwachung der Prozessparameter während der Harzinjektion, Infiltration (Flussfrontüberwachung) und In-situ-Polymerisation umfasst dieses Netzwerk:
- 1 Vakuumsensor
- 4 Druck-/Temperatursensoren von Kistler (Winterthur, Schweiz)
- 4 Temperatursensoren von Kistler
- 8 dielektrische Analyse (DEA)/Temperatursensoren von Netzsch (Selb, Deutschland)
- 57 Ultraschallsensoren entwickelt von der Universität Augsburg.
In meinem ersten Bericht über CosiMo habe ich diskutiert, wie dieses Sensornetzwerk für F&E und nicht für die Standardproduktion geeignet ist:
„Für eine industrielle Serienfertigung würde niemand so viele Sensoren einbauen und das würden wir auch nicht erwarten“, sagt Jan Faber, Projektleiter CosiMo-Fertigung im DLR ZLP. „Aber für diese Forschungsuntersuchung war dieses große Sensornetzwerk sehr präzise und halfen uns, vollen Einblick in den Prozess zu haben und Materialverhalten . Wir konnten die lokalen Auswirkungen des Prozesses als Reaktion darauf sehen auf Variationen in der Teiledicke oder in den integrierten Materialien, wie dem Schaumkern.“
Wie wurde dieses Netzwerk aufgebaut? „Die meisten waren die Ultraschallsensoren, weil sie die niedrigsten Kosten haben“, erklärt Faber. „Wir haben sie in einem Raster in einem definierten Abstand zueinander eingesetzt. An einigen Stellen haben wir die Ultraschallsensoren herausgenommen und Kistler Temperatur-/Drucksensoren oder Netzsch DEA-/Temperatursensoren eingebaut. Und für diese speziellen Sensoren, sowohl DEA als auch Kistler, haben wir nur versucht, einen in der Nähe des Angusses zu haben, wo das Harz eintrat, und dann einen weit entfernten. So konnten wir die Stellen überwachen, an denen das Harz ankommt, nachdem wir die Werkzeugtemperatur bereits einige Zeit gesehen hatten.“
Warum verschiedene Arten von Sensoren verwenden? „Eine Forschungsaufgabe bestand darin, die Signale zu vergleichen und zu sehen, wie sich die verschiedenen Sensoren verhalten“, sagt Faber. Dies ist wichtig, da die unterschiedlichen Sensortypen auf unterschiedlichen Messprinzipien basieren. DEA-Sensoren messen beispielsweise die Wechselstromimpedanz des Harzes, die sich in verschiedene Fraktionen aufteilen lässt, die wiederum unterschiedliche Effekte im Polymer zeigen. Kistler verwendet unterdessen piezoresistive Sensoren, die auf einer siliziumbasierten Wheatstone-Brücke – einer Art Schaltung zur Messung des dynamischen elektrischen Widerstands – basieren, die mit einer Membran verbunden ist, die das Sensorende bildet, das in der Wand des Formhohlraums installiert ist. Die Membran dehnt sich unter Druck aus, wodurch sich der elektrische Widerstand der Silizium-Wheatstone-Brücke ändert, die wiederum ein elektrisches Signal ausgibt. „Wir haben auch den neuen Sensor 4001a von Kistler verwendet, der sowohl Druck als auch Temperatur misst“, sagt Faber. „Es war sehr nützlich, beide Werte für ausgewählte lokale Punkte im Tool zu haben.“
UNA-Ultraschallsensoren
Der Großteil der im CosiMo-Teilenetzwerk eingesetzten Sensoren waren von UNA entwickelte Ultraschallsensoren. Sause merkt an, dass diese nicht nur wegen ihrer geringen Kosten (<10 Euro) bevorzugt wurden, sondern auch, weil sie eine breite Palette von Informationen liefern können.
Ultraschallsensoren werden seit Jahrzehnten zur Prüfung fertiger Verbundteile eingesetzt, haben aber auch eine lange Tradition im Spritzguss. Ultraschallsensoren senden eine hochfrequente Schallwelle in ein Medium und messen deren Reflexion (Impuls-Echo) und/oder Transmission. Im Projekt CosiMo lag die Nennfrequenz bei 2.000 Kilohertz. Von den 57 im Werkzeug verbauten Ultraschallsensoren — in einem Abstand von 20 Millimetern von der Kavitätenoberfläche — arbeiteten 10 im Sendebetrieb, der Rest im Impuls-Echo-Betrieb. Ultraschallsensoren messen die Geschwindigkeit der Welle und die Abnahme der Amplitude (Dämpfung); beide sind empfindlich gegenüber den Eigenschaften des Polymers. Außerdem kann die Wellengeschwindigkeit als Funktion von Druck und Temperatur berechnet werden, aber die Ultraschalldaten müssen auf das untersuchte Polymer kalibriert werden.
„Der von uns entwickelte Ultraschallsensor unterscheidet sich eigentlich nicht wesentlich von dem, was im Handel erhältlich ist“, sagt Sause. „Es basiert auf einem piezoelektrischen Material, das eine elastische Bewegung sehr empfindlich in ein elektrisches Signal umwandelt. Aber wo typische Sensoren bei Temperaturen von bis zu 150°C arbeiten können, mussten wir die hohen Temperaturen des thermoplastischen Spritzgießens von über 200°C mithalten, was für die Sensorelektronik eine kleine Herausforderung war.“
„Wir mussten auch das mechanische System entwickeln, um den Sensor richtig in das Werkzeug zu integrieren“, erklärt er, „was eine Federspannung mit guter Abdichtung erforderte, um eine gute Kopplung zu gewährleisten. Es gab ein großes Portfolio an Anforderungen, die der Sensor erfüllen musste; Also mussten wir es so ziemlich von Grund auf neu entwerfen. Wir haben auch ein angemessenes akustisches Design des gesamten Systems durchgeführt.“
Überwachung von Polymerisation und Fließfront
„Bei der Akustik stehen die elastischen Eigenschaften der Materialien im Werkzeug im Fokus“, so Sause weiter. „Grundsätzlich ist die Steifigkeit in einer Flüssigkeit nicht dieselbe wie bei abgeschlossener Polymerisation. Wir beobachten diesen Übergang effektiv. Wir betrachten die akustische Intensität der Wellenreflexion an der Grenzfläche von der Form zum Polymermaterial an jeder Sensorposition und verfolgen so kontinuierlich die Aushärtung im Laufe der Zeit.“
Die Mechanik dieser Messung wird von Sause und Faber et. al., im SAMPE Europe 2021-Konferenzpapier „Sensorbasierte Prozessüberwachung der in-situ-Polymerisation in der T-RTM-Herstellung mit Caprolactam“. Das Verhältnis der Amplitude des akustischen Signalechos vor und nach der Preform-Imprägnierung hängt vom Reflexionsindex an der Grenzfläche Form-Teil, R, ab. Dieser nähert sich mit fortschreitender Polymerisation einem konstanten Wert an. Im Idealfall ist die Änderung von R gleich Null, sobald sich die Polymerisation dem Abschluss nähert.
Es ist auch möglich, aus dem akustischen Sendesignal die Laufzeit der Ultraschallwellen durch den imprägnierten Vorformling zu extrahieren. Dies ist hilfreich, da die Schallgeschwindigkeit durch den Vorformling mit dem Polymerisationsgrad verknüpft ist. Für die zum Zeitpunkt des SAMPE Europe 2021-Papiers abgeschlossenen Experimente betrug die Zeit zwischen der gründlichen Benetzung des Vorformlings am Ort des Sensors bis zum Abschluss der Polymerisation 240 Sekunden.
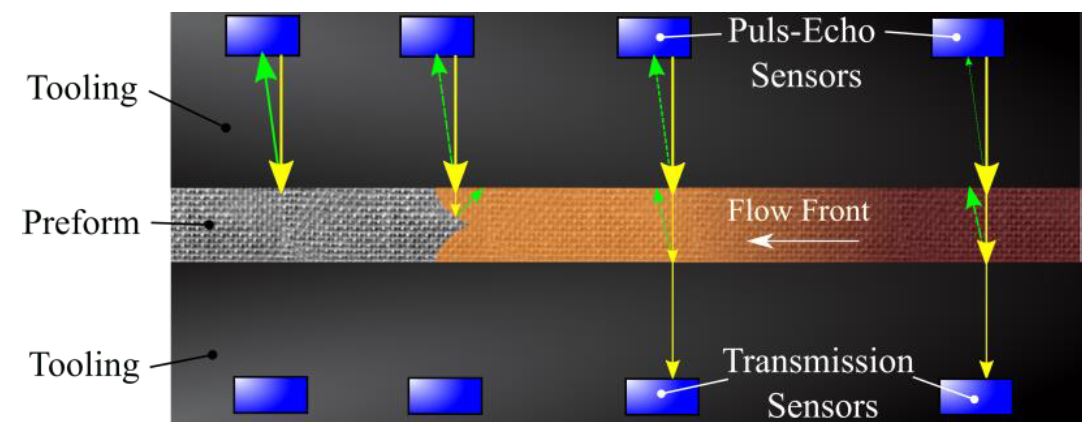
„Außerdem können wir den Fluss während der Injektion überwachen“, erklärt Sause, „weil sich die akustische Signalinformation ändert, wenn die Polymerflussfront den Sensor passiert.“ Ebenfalls im Papier von SAMPE Europe 2021 bestätigt, fiel das akustische Signal ab einem anfänglichen normalisierten Wert von 1 auf 0,85 bis 0,9 ab, als die Caprolactam-Flussfront für den ausgewählten Sensor 15 Sekunden nach Beginn der Injektion eintraf.
Entwicklung eines digitalen Zwillings des Prozesses
Sause sagt, dass die Entwicklung des Ultraschallsensors eigentlich nur ein sehr kleiner Teil dessen war, was UNA im CosiMo-Projekt getan hat, „und nicht einmal der faszinierendste Teil“. Die eigentliche Errungenschaft liege in der Datenanalyse und Entwicklung eines digitalen Modells des Prozesses, um eine Closed-Loop-Steuerung während der Teilefertigung zu ermöglichen.
„Wir versuchen, Informationen darüber bereitzustellen, was tatsächlich in der Form passiert“, fügt er hinzu. „Wir hatten etablierte Wege, um den Prozess mehr oder weniger an Temperatur und Druck anzupassen, aber was wir jetzt tun, ist die akustische Signalinformation auszunutzen, indem wir an jeder Sensorposition aktives Pulsen durchführen. Und so können wir verschiedene Dinge wie die Form der Fließfront, die Zeit, die sie benötigt, um jeden Teil des Vorformlings zu erreichen, und den Polymerisationsgrad an jeder Sensorposition bestimmen.“
„Idealerweise kann man Einstellungen vornehmen, um eine Regelung zu ermöglichen und während des Prozesses anzupassen“, sagt Sause. „Dazu gehören Parameter wie Spritzdruck sowie Werkzeugdruck und -temperatur. Sie können diese Informationen auch verwenden, um Ihre Materialien zu optimieren.“
Die Entwicklung des digitalen Zwillings war eine mehrstufige und partnerschaftliche Anstrengung. Es begann mit einem der dem DLR ZLP zugeordneten Arbeitspakete. „Wir haben eine Simulation auf Basis einer 2D-Platte aufgebaut, bei der wir die Füllung und Polymerisation mit der Simulationssoftware PAM-RTM der ESI Group (Rungis, Frankreich) simulieren wollten“, sagt Faber. „Wir haben die Preform-Permeabilitätsdaten von den Projektpartnern ITA (Institut für Textiltechnik, RWTH Aachen, Deutschland) und SGL Carbon (Wiesbaden, Deutschland) sowie ein reaktives Modell der thermoplastischen Polymerreaktion von der Universität Augsburg erhalten. Wir haben dann alles in die Simulation integriert und versucht zu sehen, wie nah wir den realen Sensordaten tatsächlich kommen.“
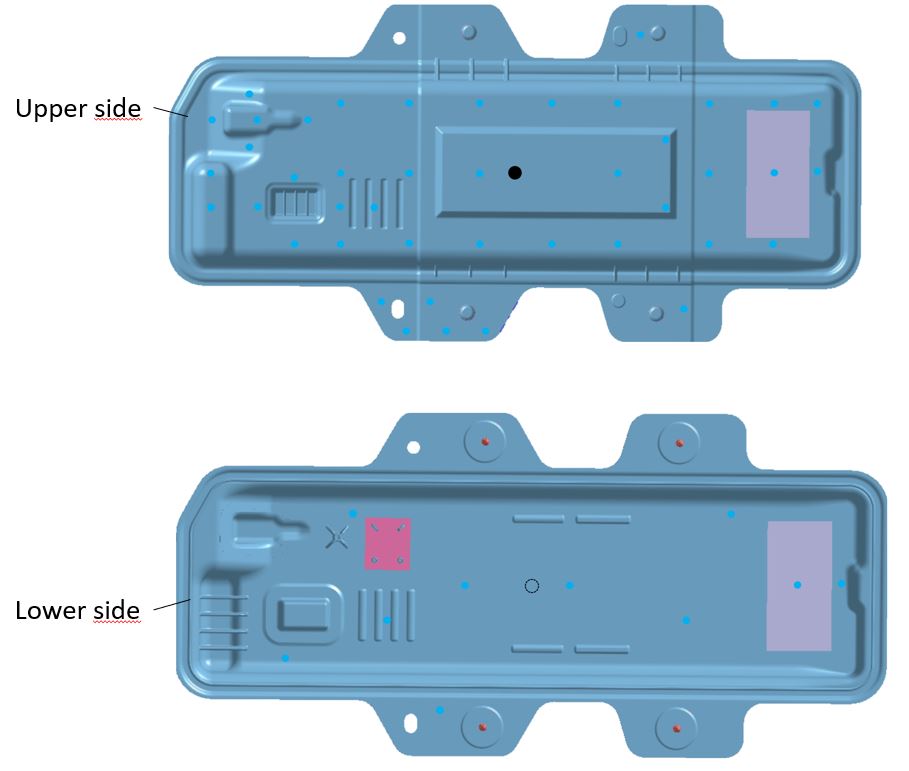
Die hellblauen Punkte in der oberen und unteren Form des CosiMo-Projektdemonstrators lieferten Daten an bestimmten Stellen des Prozesses. Dies wurde dann in der digitalen Zwillingssimulation verwendet, um zwischen den Sensorpositionen zu interpolieren und den Prozess über das Teil zu modellieren. Bildnachweis:CosiMo-Projekt, DLR ZLP Augsburg, Universität Augsburg
„Wir haben anhand des 2D-Plattenmodells festgestellt, dass wir bei der Füllung tatsächlich sehr nah dran sind“, so Faber weiter. „Aber wir hatten während der Polymerisation einige Temperatureffekte, die wir in der Simulation nicht beschreiben konnten. Zum Beispiel ist diese Polymerisationsreaktion exotherm, und man sieht in den realen Daten einen leichten Anstieg an den Temperatursensoren, aber der Anstieg in der Simulation war viel höher. Dies ist also ein Bereich, in dem wir weitergearbeitet haben.“
Unter anderem wollte das Team aus der Simulation herausfinden, wie lange es dauert, bis die Polymerisation abgeschlossen ist. „Was wir wirklich wollten, war die minimale Zeit, die wir in der Form brauchten“, sagt Faber. Diese Informationen wurden aus dem Simulationsmodell abgeleitet und stützten sich, wie die gesamte Simulation, auf mehrere Arten von Sensoren und KI-Algorithmen. Netzsch lieferte beispielsweise die dielektrischen Sensoren für die dielektrische Analyse, half aber auch bei Teilen des digitalen Zwillings des Prozesses. „Sie erstellten prädiktive KI-Modelle, um die Mechanismen innerhalb der Injektion zu untersuchen und vorherzusagen, wann die Polymerisation abgeschlossen sein sollte und wie der Polymerisationszustand sein würde“, sagt Faber.
(Beachten Sie, dass Netzsch seine Kompetenzen in den Bereichen Materialcharakterisierung, kinetische Simulation und Sensorik gebündelt hat, um neue Angebote für KI- und Cloud-Lösungen zu etablieren. Diese Art von integrierter Lösung wurde in CosiMo erfolgreich demonstriert, um den Polymerisationsgrad in Echtzeit zu bewerten und wird unter der Marke sensXPERT vermarktet.)
Aus dem vollständigen Netzwerk von Sensoren und Simulationen wurde festgestellt, dass 96 % der maximal erreichten Polymerisation erreicht wurden und 4,5 Minuten benötigt wurden. „Das ist also viel schneller als Infusionsverfahren, aber viel langsamer als beispielsweise eine Hochgeschwindigkeitsinjektion mit Duroplasten.“
„Die Sensordaten passen in das digitale Zwillingsmodell“, sagt Sause. „Die Idee war, parallel zum Prozess ein Modell laufen zu lassen, das durch die Sensorinformationen numerisch stabilisiert wird. Die blauen Punkte bilden ein grobes Raster von Ultraschallsensoren, und dann konnten wir zwischen diesen Punkten interpolieren. So konnten wir beispielsweise anhand der Messdaten unserer Sensoren in einem Video zeigen, wie sich die Fließfront im CosiMo-Bauteil als Funktion der Zeit entwickelt.“
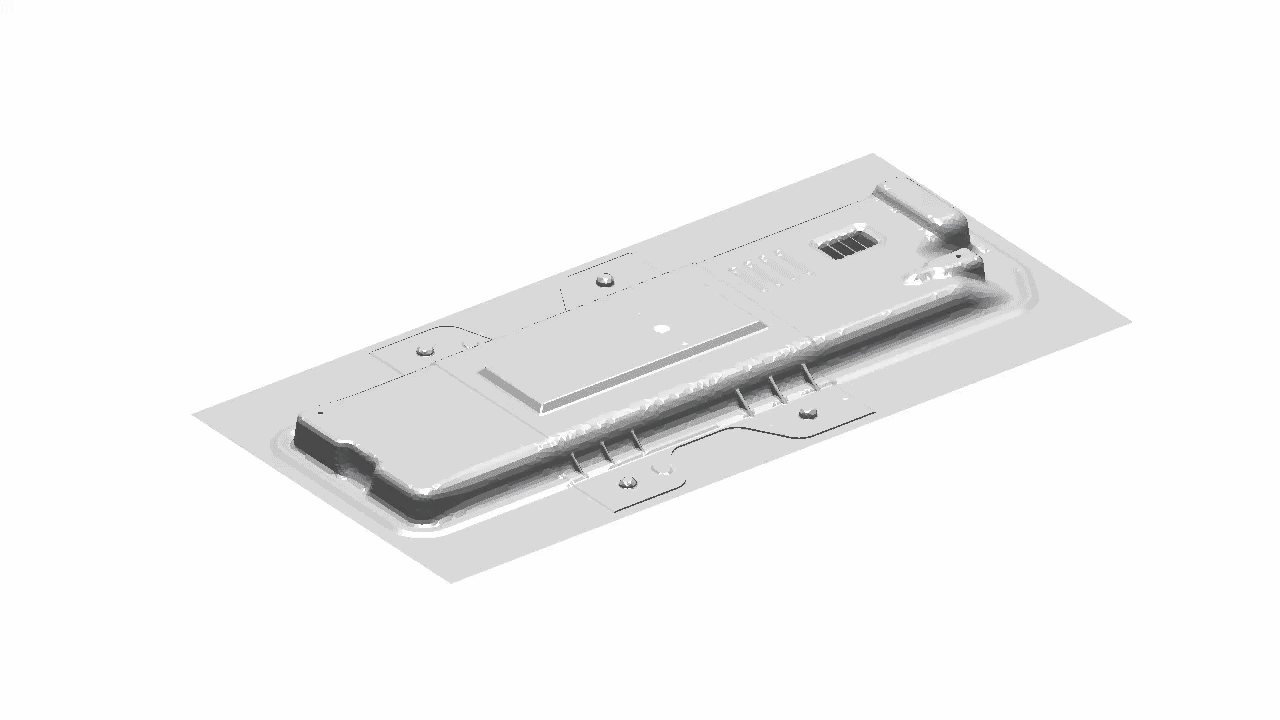
Wie wurden die Vorhersagen der Polymerisationsgeschwindigkeit validiert? „Wir hatten mehrere Ansätze“, sagt Sause. „Zuerst führte ein Doktorand hier an der UNA einen vollständigen Modellierungssatz für die Reaktionskinetik des Caprolactam-zu-PA6-Materialsystems durch. Also studierte er gleichzeitig Infrarotspektroskopie zusammen mit rheometrischen Daten und Daten von den dielektrischen Analysesensoren, um ein sehr genaues Materialmodell für die gehärtete Kinetik dieses Systems bereitzustellen und dieses Modell zu validieren. Also haben wir das gleiche Modell verwendet, um unsere Sensoren gegeneinander zu validieren.“
Architektur des digitalen Zwillings
Die Architektur der Funktionsweise des digitalen Zwillings wird von Stieber et. al. im technischen Papier von 2020 „Auf dem Weg zu Echtzeit-Prozessüberwachung und maschinellem Lernen für die Herstellung von Verbundstrukturen“:
Es besteht aus drei Teilen:der T-RTM-Maschinerie, den In-Situ-Sensoren in den Werkzeugen und dem digitalen Zwilling. Diese Struktur und insbesondere der digitale Zwilling wurden mit den folgenden Zielen O1 – O4 entwickelt:
- O1:Überwachen Sie den Herstellungsprozess jedes Verbundteils mit den In-situ-Sensoren der Werkzeuge.
- O2:Visualisieren Sie jeden Herstellungsprozess in Echtzeit, um weitere Prozesseinblicke zu erhalten.
- O3:Trainieren Sie ML-Modelle mit simulierten und realen Daten, um das Ergebnis des Herstellungsprozesses vorherzusagen.
- O4:Verwenden Sie trainierte ML-Modelle, um Produktionsausschuss zu reduzieren.
Die Sensoren liefern dann Daten an die Kantenanalyse des digitalen Zwillings, die dann verwendet werden können, um die zukünftige Fließfrontdynamik vorherzusagen, den Faservolumengehalt jedes textilen Vorformlings zu bestimmen, Trockenstellen vorherzusagen und Anomalien zu erkennen, die Ausschussteile reduzieren können.
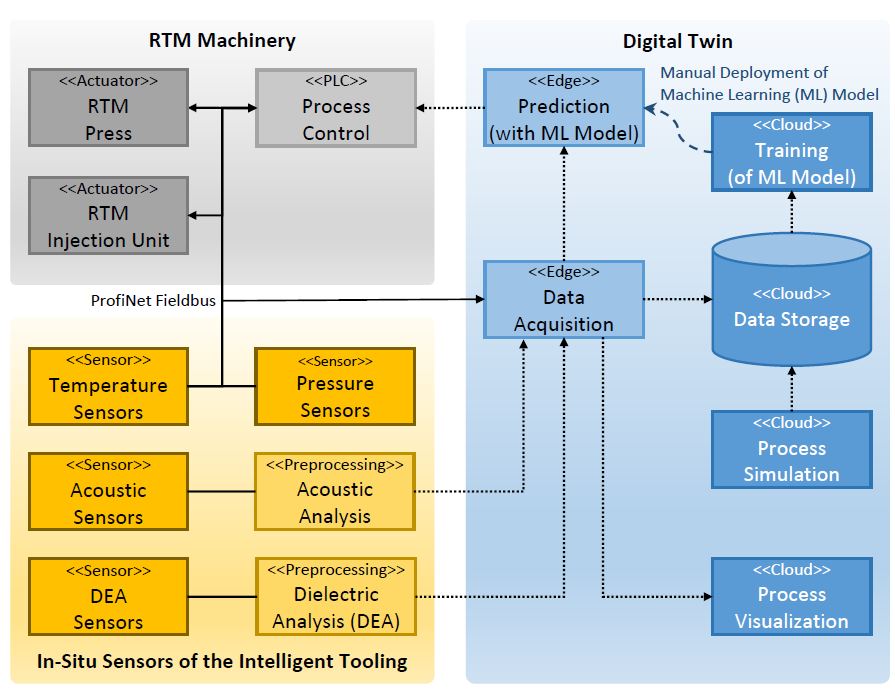
Der T-RTM-Maschinenpark besteht aus zwei serienmäßigen Komponenten:einer 440-Kilonewton-Heißpresse von Wickert (Landau in der Pfalz, Deutschland) und einer T-RTM-Spritzeinheit von KrausMaffei (München). Beide Maschinen sowie das gesamte Sensornetzwerk sind mit einer SPS (Programmed Logic Controller) verbunden, die für die Steuerung des gesamten Herstellungsprozesses verantwortlich ist.
Da die Sensoren eine Echtzeit-Vorverarbeitung benötigen, um die Rohdaten in übergeordnete Informationen über die Fließfront oder die Aushärtung des Harzes umzuwandeln, werden die vorverarbeiteten Daten direkt am Rand mit einer ibaPDA-Datenerfassungseinheit der iba AG Fürth, Deutschland). Somit werden die Sensordaten erfasst und mit einem konsistenten Zeitstempel verknüpft mit den Prozessdaten und Bauteilinformationen mit den Sensordaten pro Zielsetzung O1 und O2 zusammengeführt.
Um den Herstellungsprozess automatisch zu optimieren, werden die gespeicherten Daten verwendet, um Modelle des maschinellen Lernens (ML) zu trainieren, um das Ziel O3 zu erreichen. Diese Modelle sind beispielsweise dafür verantwortlich, die Fließfront des Harzes aus dem Sensornetzwerk zu rekonstruieren, den Verlauf der Fließfront vorherzusagen und – idealerweise – die Prozessparameter anzupassen, um das Ergebnis entweder während einer Prozessinstanz oder für nachfolgende Läufe zu optimieren . Da reale Daten in der Regel nicht ausreichen, um zuverlässige Modelle zu trainieren, nutzte das Team des digitalen Zwillings PAM-RTM-Simulationsläufe, um die gemessenen Daten zu ergänzen. Nach dem Vortraining mit simulierten Daten wurde der digitale Zwilling mit realen Daten verfeinert. Diese Strategie ist als Transfer Learning bekannt und wurde erfolgreich in Computer Vision- und Natural Language Processing-Anwendungen eingesetzt. Die mit ML möglichen erweiterten Analysen ermöglichen verbesserte Vorhersagefunktionen und Prozessvisualisierung sowie eine geschlossene Regelung.
Sensorintegration für die industrielle Verbundstoffproduktion
Wie also wenden Hersteller von Verbundwerkstoffteilen diese Technologie an, um eine geschlossene Regelung in ihren eigenen Produktionsprozessen zu entwickeln? Sause sagt, dass es sinnvoll ist, verschiedene Arten von Sensoren zu verwenden, um die Überwachung des Flusses und der Härtung/Polymerisation zu validieren und ergänzende Informationen bereitzustellen. Und dann geht es darum, die Sensorplatzierung zu definieren, einschließlich der Typen, die an jedem Ort platziert werden. „Zum Beispiel“, bemerkt er, „brauchen Sie Druck- und Temperatursensoren nicht überall, sondern genau dort, wo Sie diese wichtigen Datenpunkte benötigen, wie z. B. Harzeintritt, komplexe Geometriepunkte usw.“
Wie viele Sensoren? „Für CosiMo haben wir 74 Sensoren verwendet, aber für einen halben Meter benötigt man weniger, vielleicht 35 bis 40, je nach Geometrie und wichtigen Punkten“, sagt Sause. „Das hängt auch vom Produktionsprozess ab. Es gibt beispielsweise Verfahren in der Luft- und Raumfahrt, die seit Jahrzehnten eingesetzt und gut etabliert sind. Für diese benötigen Sie möglicherweise nicht sehr viele Sensoren und können möglicherweise ohne großen Entwicklungsaufwand am Anfang integriert werden. Andere Prozesse sind jedoch unbekannter und erfordern mehr Vorarbeit. Für CosiMo haben wir die Verwendung von T-RTM mit In-situ-Polymerisation zu PA6 in Betracht gezogen, und dies war beispielsweise nicht so gut dokumentiert wie RTM mit Epoxid.“
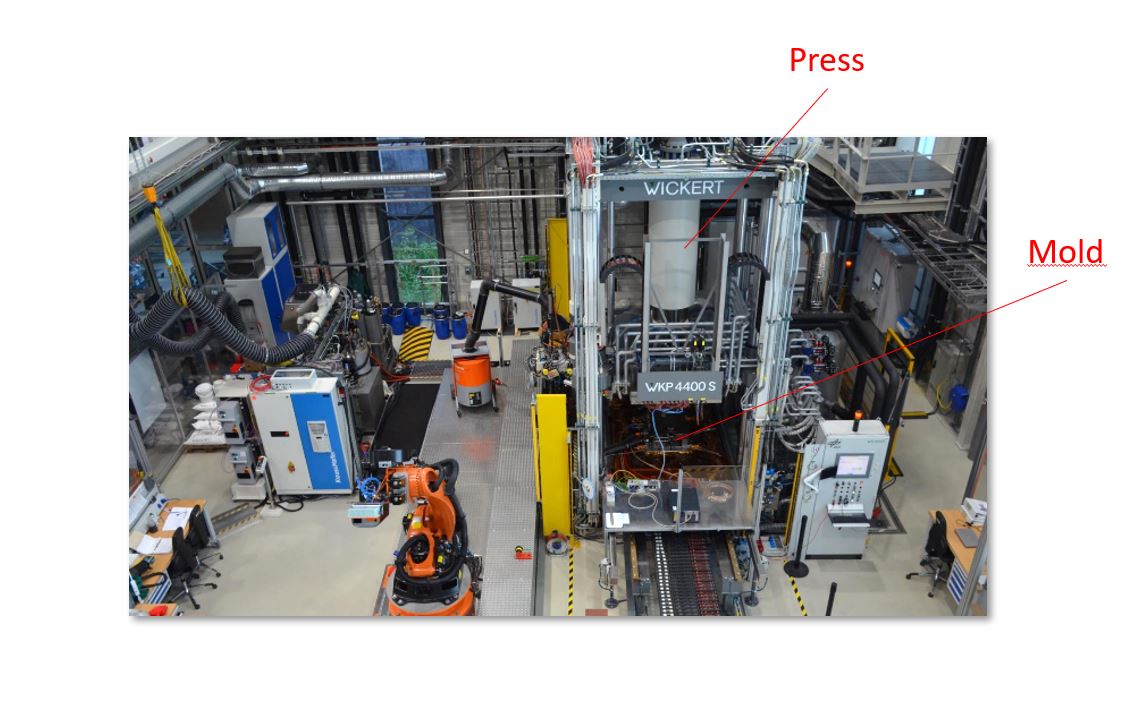
Die Fertigungsausrüstung im CosiMo-Projekt umfasste eine Wickert 440-kN-Presse und eine KraussMaffei Spritzmaschine. Bildnachweis für diese Serie:CosiMo-Projekt, DLR ZLP Augsburg, Universität Augsburg
Wie zeitintensiv ist der Aufbau eines digitalen Modells? Und ist das immer erforderlich, um eine Regelung zu erreichen? „Auch hier kommt es auf Ihren Prozess an und welches Niveau Sie erreichen wollen“, sagt Sause. „Zuallererst können Sie durch die Integration der Sensorinformationen visualisieren, was in Ihrer Blackbox der Verarbeitung passiert und welche Parameter zu verwenden sind.
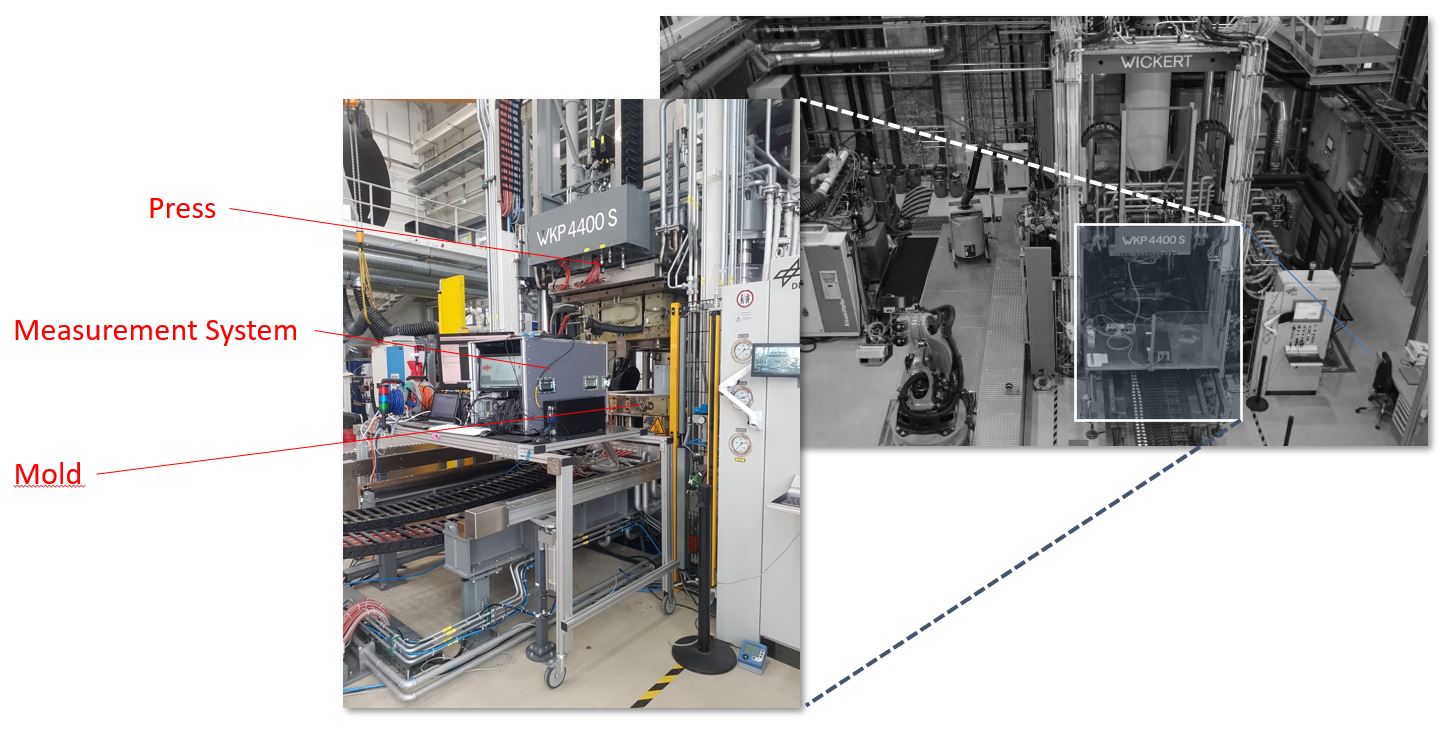
Das in CosiMo entwickelte Regelsystem integriert auch In-Mold-Sensoren und ein Datenerfassungssystem (hier Messsystem) der iba AG.
Sobald dieses erste Ziel erreicht ist, sind es noch einige Schritte, um eine geschlossene Prozesssteuerung zu erreichen. Der halbe Weg ist vielleicht, die Visualisierung zu haben und Sie können selbst auf den Stopp-Knopf drücken, um den Prozess anzupassen und Ausschussteile zu vermeiden. Auch das ist also ein Anfang. Und dann kann man den digitalen Zwilling entwickeln, der braucht aber Trainingsdaten. Sie müssen das also irgendwie bereitstellen, was bedeutet, dass Sie ein paar Teile produzieren können, die als Eingabedaten verwendet werden. Dann müssen Sie aber auch Teile von geringer Qualität herstellen. Es kommt also auf Ihre Bereitschaft an, in die Schulung Ihres maschinellen Lernansatzes zu investieren.“
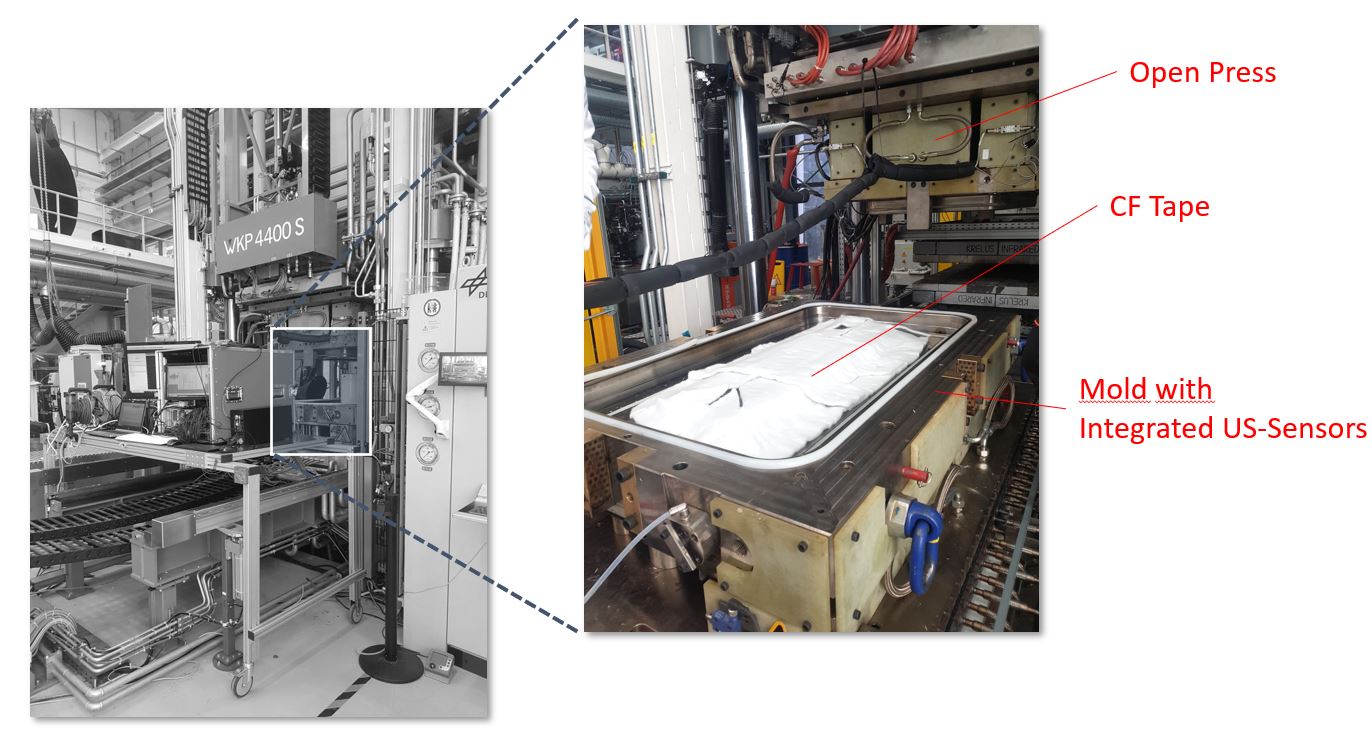
Nach dem Training kann der digitale Zwilling Prozessparameter optimieren und eine geschlossene Prozesssteuerung bieten.
Sause räumt jedoch ein, dass der Transfer-Learning-Ansatz von CosiMo „bis zu einem gewissen Grad auf ähnliche Geometrien oder Materialsysteme und andere Variationen übertragbar ist, die die Situation nicht vollständig ändern. Auf diese Weise können Sie Ihre Datenbank aufbauen, mit der Möglichkeit, anhand der bereits erfassten Daten Effizienztrends zu erkennen. Das kannst du dann für andere Fragen verwenden, die du vielleicht nebenher hast.“
Der Anfang scheint also zu sein:Beginnen Sie mit der Verwendung von Sensoren und bauen Sie digitale Modelle zu den Sensoren, damit Sie Ihren Prozess verstehen können? „Absolut“, sagt Sause. „Und ich kann Ihnen versichern, dass die meisten Maschinen, die heute in der Produktion eingesetzt werden, immer noch sehr dumm sind. Viele Maschinen haben keine Sensoren, die Ihnen die Datenbanken liefern können, um Feedback zu den Vorgängen zu geben. Die Integration von Sensorsystemen wäre also der allererste Schritt. Aber Sie müssen eine systematische durchführen Datenerfassung und Bereitstellung einer Datenspeicherarchitektur, um mit den Daten etwas anfangen zu können . Tatsächlich sieht man viele Unternehmen, die Sensoren integriert haben, aber dann machen sie nichts mit den Daten.“
KI-Produktionsnetzwerk
Bei der Beantwortung der obigen Fragen kam Sause immer wieder auf verschiedene Gruppen innerhalb der UNA sowie auf Spin-off-Unternehmen zurück, die Sensorintegration und digitale Zwillingsdienste anbieten können. Dazu wurde im Januar 2021 das Augsburger AI Production Network von UNA, DLR ZLP und Fraunhofer IGCV ins Leben gerufen. „Der Kooperationsrahmen stammt aus Projekten, die wir in der Vergangenheit mit dem DLR und Fraunhofer hatten“, sagt Sause. „Wir nehmen die Blaupause in der KI-basierten Produktionsentwicklung von CosiMo und bauen sie jetzt sehr breit aus. So betrug das Budget für unsere Arbeit in CosiMo beispielsweise 10 Millionen Euro, für das AI Production Network sind es 92 Millionen Euro als Anschubfinanzierung. Dies wird uns die Möglichkeit geben, viele neue Forschungsprojekte wie CosiMo zur Nutzung von KI in der Fertigung zu starten. Und wir arbeiten nicht nur mit Verbundwerkstoffen, sondern haben einen starken Fokus darauf.“
Der Einsatz von Ultraschallsensoren zur Verbesserung der CNC-Bearbeitung ist ein Projekt, das bereits im Jahr 2021 gestartet wurde. „Ein Projekt zum Recycling von Keramikmatrix-Verbundwerkstoffen (CMC) steht kurz vor dem Start“, sagt Sause, „und wir werden mehrere Projekte haben, die eng miteinander verbunden sind additive Fertigung und die Wiederverwendung speziell recycelter faserverstärkter Materialien.“
Was die Rollen angeht, die jede Organisation spielen wird, erklärt Sause, dass es keinen Wettbewerb gibt, da jede Institution über ein zugewiesenes Budget verfügt. „Wir alle haben unseren Anteil und können daher wie in der Vergangenheit frei zusammenarbeiten. Außerdem kennen wir uns und unsere Kompetenzen, Stärken und Schwächen recht gut. Es macht Spaß, zusammenzuarbeiten, weil wir wissen, was wir können und was nicht. Wir sind von vielen Unternehmen angesprochen worden, die mit uns zusammenarbeiten möchten, und wir diskutieren jetzt, wie wir die ideale Ergänzung aus unserer Sicht der Kompetenzen finden können.“
Was die 5.000 Quadratmeter große Produktionshalle angeht, „das werden wir alle gemeinsam betreiben“, sagt Sause. „Wir planen, Anfang 2023 zu eröffnen und mit der Installation von Maschinen zu beginnen. Und wir sorgen für automatisierte Produktionseinstellungen, die die einzelnen Zellen miteinander verbinden. Viele von ihnen werden sich auf Technologien zur Herstellung von Verbundwerkstoffen konzentrieren. Und wir werden das tun, um auch Partnern aus der Industrie zu zeigen und zu demonstrieren, was KI in einer solchen Produktionsumgebung leisten kann. Wir möchten auch, dass Partner aus der Industrie kommen und auch Maschinen in unserem Werk platzieren, damit wir gemeinsam Projekte durchführen können, um zu sehen, wie wir neue Lösungen für ihre Standorte verknüpfen und integrieren können.“
Harz
- Ventile für schwieriges Absperren und Regeln
- Sensoren und Systeme für CBM
- Tauchbeschichtungsverfahren und Leistungsoptimierung für elektrochrome Drei-Zustands-Bauelemente
- OTOMcomposite entwickelt Software für die Composites 4.0-Produktion mit lasergestützter Bandplatzierung und -wicklung
- Wiederaufbereitbare, reparierbare und recycelbare Epoxidharze für Verbundwerkstoffe
- TPAC und TPRC entwickeln Recyclingprozess für thermoplastische Verbundwerkstoffe
- Tipps für Konfiguration und Verdrahtung von Bedienfeldgehäusen
- Was ist Ultraschallbearbeitung? - Arbeiten und Verfahren
- Anschlüsse für die Steuerung:Kommunikationsschnittstellen für Positions- und Bewegungssensoren
- Felddaten zur Prozessoptimierung sammeln