CosiMo:Intelligenter thermoplastischer RTM-Prozess für den Herausforderungssimulator für Batteriekastendeckel demonstriert
Das Projekt „Composites for Sustainable Mobility“ (CosiMo) wurde 2018 von Faurecia Clean Mobility (Nanterre, Frankreich) ins Leben gerufen, um einen intelligenten Thermoplast-Composite-Resin Transfer Moulding (RTM)-Prozess zu entwickeln, der ein umfassendes Sensornetzwerk einschließlich Daten aus einem intelligenten Werkzeug verwendet als Maschinendaten einer Spritzgießmaschine und Heißpresse. Das Projekt wird bis Ende 2021 abgeschlossen sein und die CosiMo-Partner haben Kenntnisse und Erfahrungen mit Closed-Loop-Regelungen gesammelt, die Echtzeit-Sensordaten mit Materialparametern aus Labordaten und Simulationsdaten kombinieren. CosiMo wird vom Bayerischen Staatsministerium für Wirtschaft, Landesentwicklung und Energie im Rahmen des Campus Carbon 4.0 Programms gefördert.
Das 1.100 Millimeter lange und 530 Millimeter breite Demonstrationsteil wurde vom Forschungszentrum von Faurecia Clean Mobility in Augsburg entwickelt. Das Ziel war es, Material- und Prozessgrenzen zu erforschen, einschließlich Metall- und Schaumkern, komplexe Geometrie, verschiedene Radien und Dicken von 2,5 bis 10 Millimetern. Glasfaservliese bis 1.000 Gramm/m² lieferte das Institut für Textiltechnik (ITA) in Augsburg. Untersucht wurden auch Glasfaser-Gelege (NCF) und unidirektionale Kohlefaser-Tapes zur lokalen Verstärkung. Die Glasfasermaterialien ermöglichen die Verwendung von recycelten Fasern aus End-of-Life (EOL)-Verbundteilen.
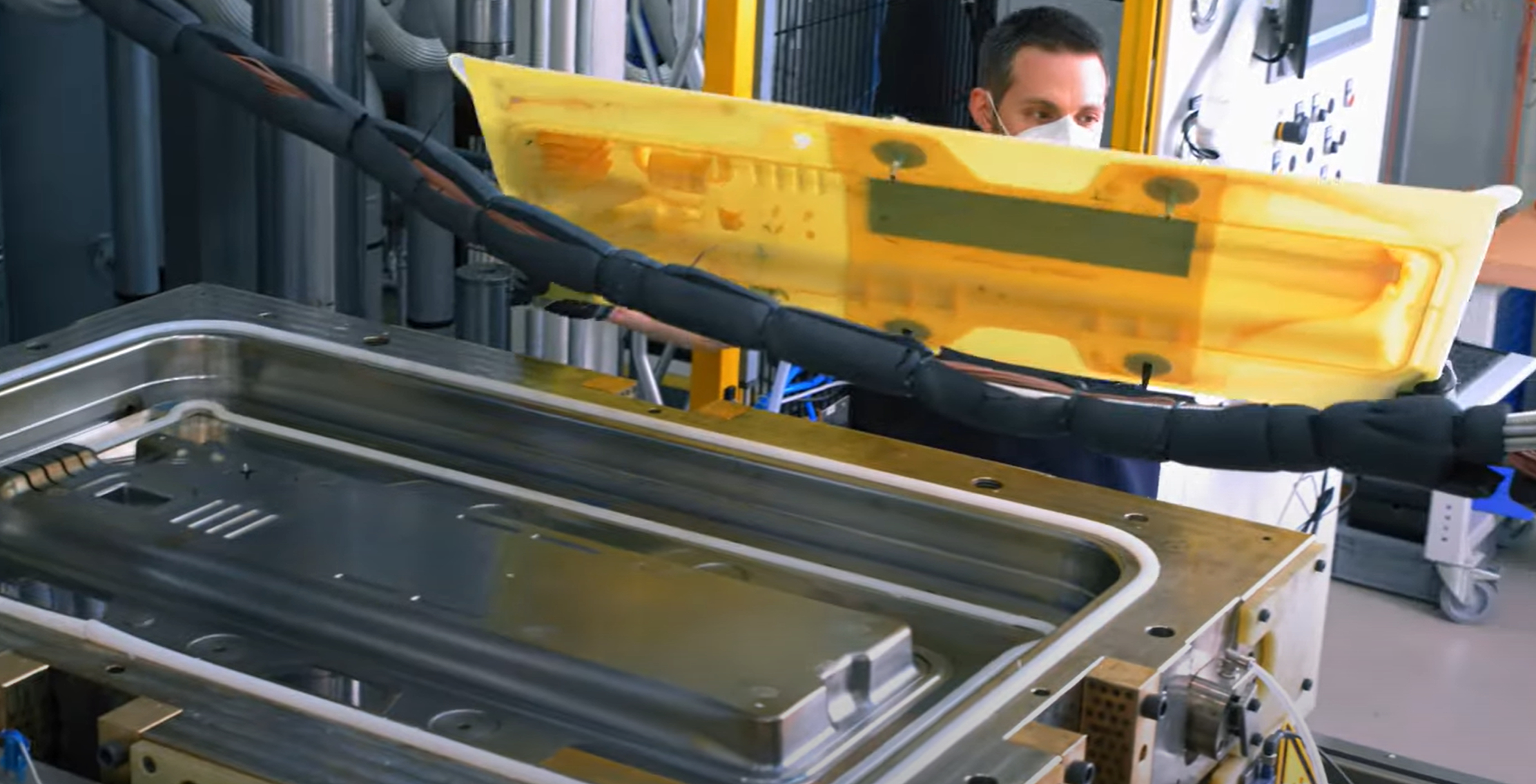
Basierend auf dem Teiledesign von Faurecia Clean Mobility und dem in Augsburg gefertigten Preforming-Werkzeug wurde für das T-RTM-Verfahren in CosiMo eine 3K (Drei-Komponenten) Spritzmaschine von KraussMaffei (München, Deutschland) verwendet. Das Verfahren ist eine Ableitung eines von Tecnalia (Donostia-San Sebastián, Spanien) patentierten 2K-Verfahrens, das von KraussMaffei auf der K-Messe 2016 in Düsseldorf demonstriert wurde. Die 3K-Spritzmaschine wurde mit einer 4.400-Kilonewton-Wickert-Heißpresse (Landau in der Pfalz, Deutschland) kombiniert, in die ein RTM-Werkzeug aus Stahl eingebaut war. Das RTM-Tool wurde von Siebenwurst in Dietfurt, Deutschland, hergestellt.
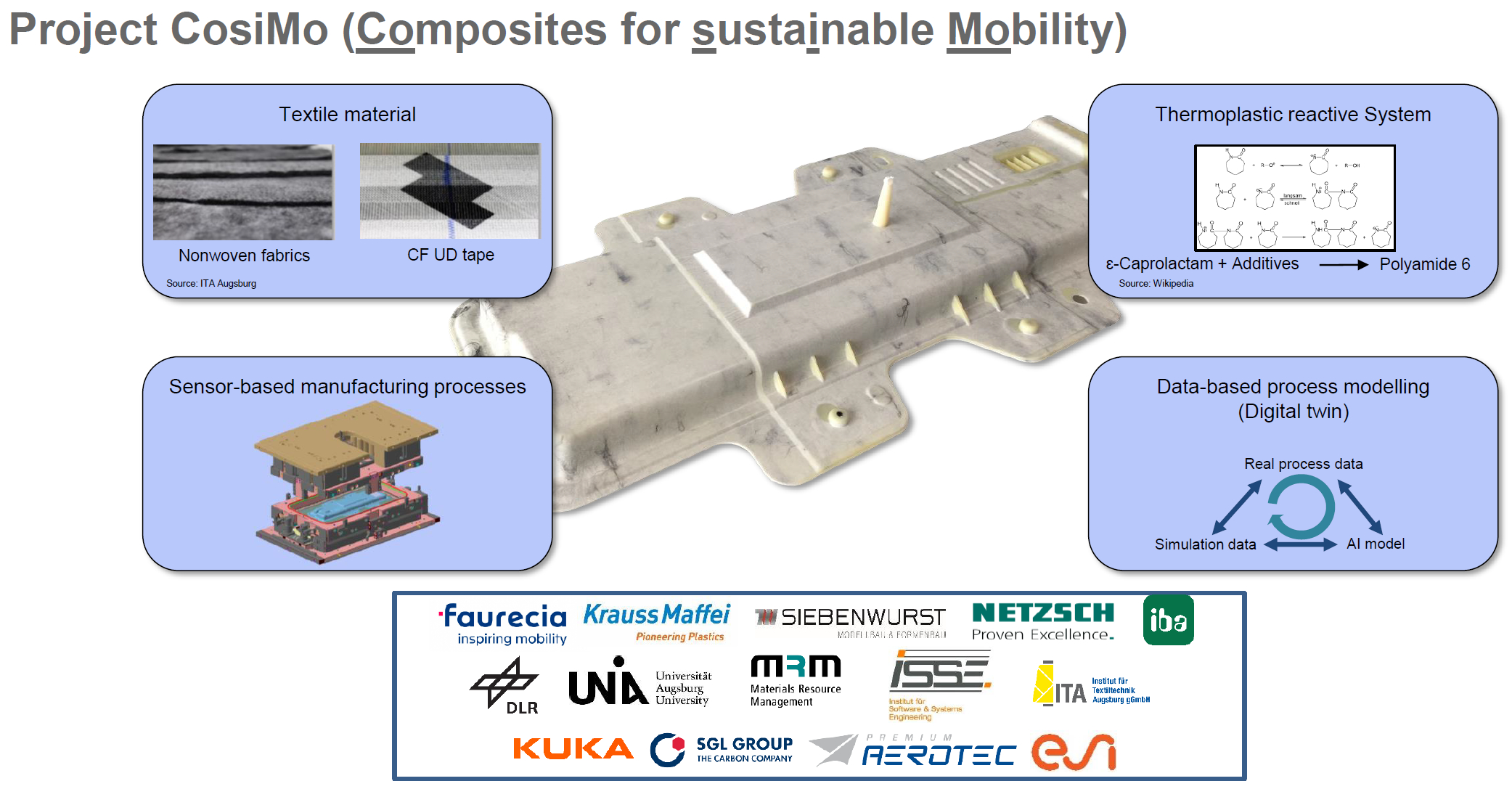
Das Hauptziel des Projekts war die Untersuchung der Vollautomatisierung und sensorbasierten Prozesssteuerung für einen einstufigen T-RTM-Prozess mit einem sensorgesteuerten RTM-Werkzeug und einer Heißpresse. Rund 100 Demonstrationsteile wurden in diesem Projekt vom Zentrum für Leichtbau-Produktionstechnologien (ZLP, Augsburg) des Deutschen Zentrums für Luft- und Raumfahrt (DLR) gefertigt. „Diese Teile mit unterschiedlichen Verstärkungen waren von hoher Qualität und wiesen eine hohe Reproduzierbarkeit auf“, sagt Jan Faber, Projektleiter CosiMo-Fertigung im DLR ZLP.
Als Projektleiter des Arbeitspakets „HAP 3 – Intelligent Tooling“ bildete das DLR ZLP zudem die zentrale Schnittstelle zwischen grundlegenden Materialcharakterisierungen in den Arbeitspaketen „HAP 1 – Tailored Nonwovens“ und „HAP 2 – Reaktive Systeme“ und dem „HAP 4“ - Datengesteuerte Prozesssteuerung”.
Sensornetzwerk
Mehr als 70 Sensoren wurden in das RTM-Werkzeug aus Stahl integriert, um die Prozessparameter während der Harzinjektion und der In-situ-Polymerisation zu überwachen. Dieses Netzwerk umfasste eine Vielzahl von Sensoren, darunter kombinierte Druck-/Temperatursensoren von Kistler (Winterthur, Schweiz), dielektrische Sensoren von Netzsch (Selb, Deutschland) und Ultraschallsensoren der Universität Augsburg. Letztere basieren auf Konzepten weit verbreiteter kommerzieller piezoelektrischer Sensoren, wurden jedoch für die hohen Temperaturen und die Anforderungen der In-Mold-Integration bei der Verarbeitung thermoplastischer Verbundwerkstoffe modifiziert. Material-, Prozess- und Maschinendaten wurden von einem zentralen Datenerfassungssystem der iba AG (Fürth, Deutschland) gesammelt, aufbereitet und anschließend auf der Machine Learning Plattform veröffentlicht.
Prozesssimulation und -optimierung
Das Sensornetzwerk ermöglichte die Überwachung des Harzflusses und der Polymerisation sowie die Verfolgung von Teileparametern in der komplexen Werkzeuggeometrie. Prozessparameter wie Temperatur und Druck wurden verwendet, um das Harzfüll- und Polymerisationsverhalten in Echtzeit zu analysieren.
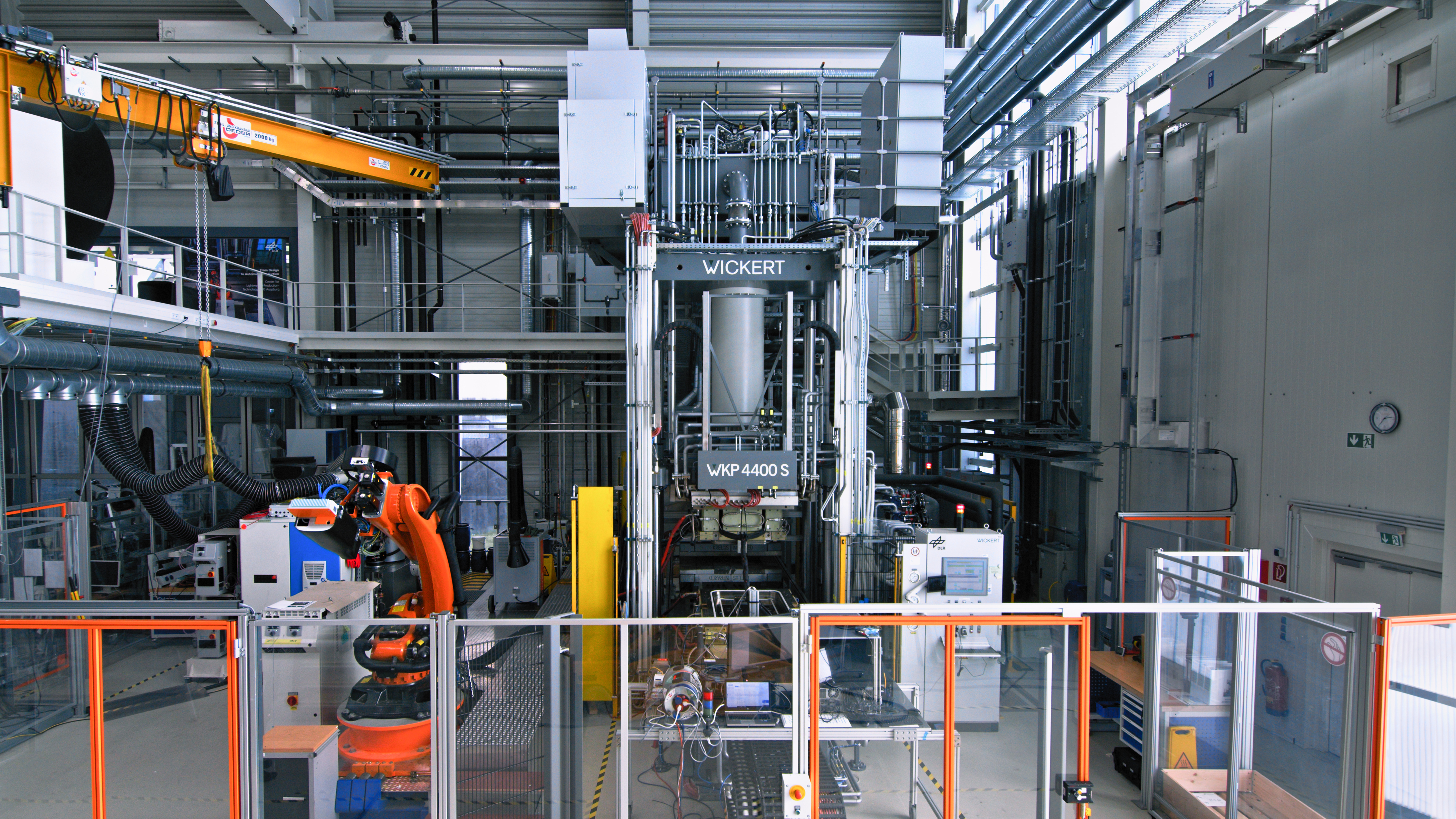
Prozessparameterdaten von Sensoren wurden auch verwendet, um Prozesssimulationsmodelle zu optimieren. Basierend auf einem zuvor definierten Fertigungsdemonstrator wurden mit der ESI PAM Composites Software (ESI Group, Rungis, Frankreich) Teilprozesse der Teilefertigung (z. B. Harzfüllsimulation) und Eigenschaften des polymerisierten Bauteils (z. B. Verformungssimulation) modelliert. Das DLR ZLP hat diese Simulationsergebnisse mit realen Prozessdaten verglichen, um den T-RTM-Prozess im Rahmen der Aktivitäten des HP3-Workpackage zu optimieren.
Anschließend entwickelte das Projekt eine automatisierte und simulationsdatengesteuerte Prozesssteuerung basierend auf Methoden des maschinellen Lernens. Das Institut für Software &Systems Engineering (ISSE, Prof. Reif) der Universität Augsburg generierte Trainingsdaten für maschinelles Lernen und entwickelte Modelle der künstlichen Intelligenz (KI), die den Polymerisationsstatus sowie die für die Polymerisation benötigte Zeit und potenzielle Probleme während vorhersagen Teilprozesse Harzinjektion, Füllen und Polymerisation. Dies geschah in Zusammenarbeit mit Kuka (Augsburg, Deutschland), einem weiteren wichtigen Partner des Projekts.
Ein kinetisches Modell, das den Polymerisationsverlauf beschreibt, wurde vom Institut für Materialressourcenmanagement (MRM) der Universität Augsburg entwickelt. Netzsch war auch ein wichtiger Mitarbeiter, der sein Wissen über die Überwachung des Duroplast-Prozesses auf die Überwachung des thermoplastischen Prozesses übertrug, um die Fähigkeit der prädiktiven KI-Modelle zu ermitteln, vorherzusagen, wann die PA6-Polymerisation abgeschlossen sein sollte und wie der Polymerisationszustand sein würde.
Teilefertigung und -prüfung
Für die Teilefertigung wurden die Stahlwerkzeuge auf 170 °C und die reaktiven Caprolactamharzkomponenten auf 120 °C erhitzt. Der Vorformling wurde in die Form gelegt, die dann geschlossen wurde. Nach einer kurzen Verweilzeit, damit der Vorformling auf Formtemperatur kommen konnte, wurde das Caprolactammonomer eingespritzt, was 20-25 Sekunden dauerte. Die Prozesssimulation zeigte, dass die in-situ-Polymerisation 5,7 Minuten nach der Injektion für eine Umwandlung von 98,5 % benötigte. Nach dieser Zeit wurde die Presse geöffnet und das Teil bei 170°C entformt.
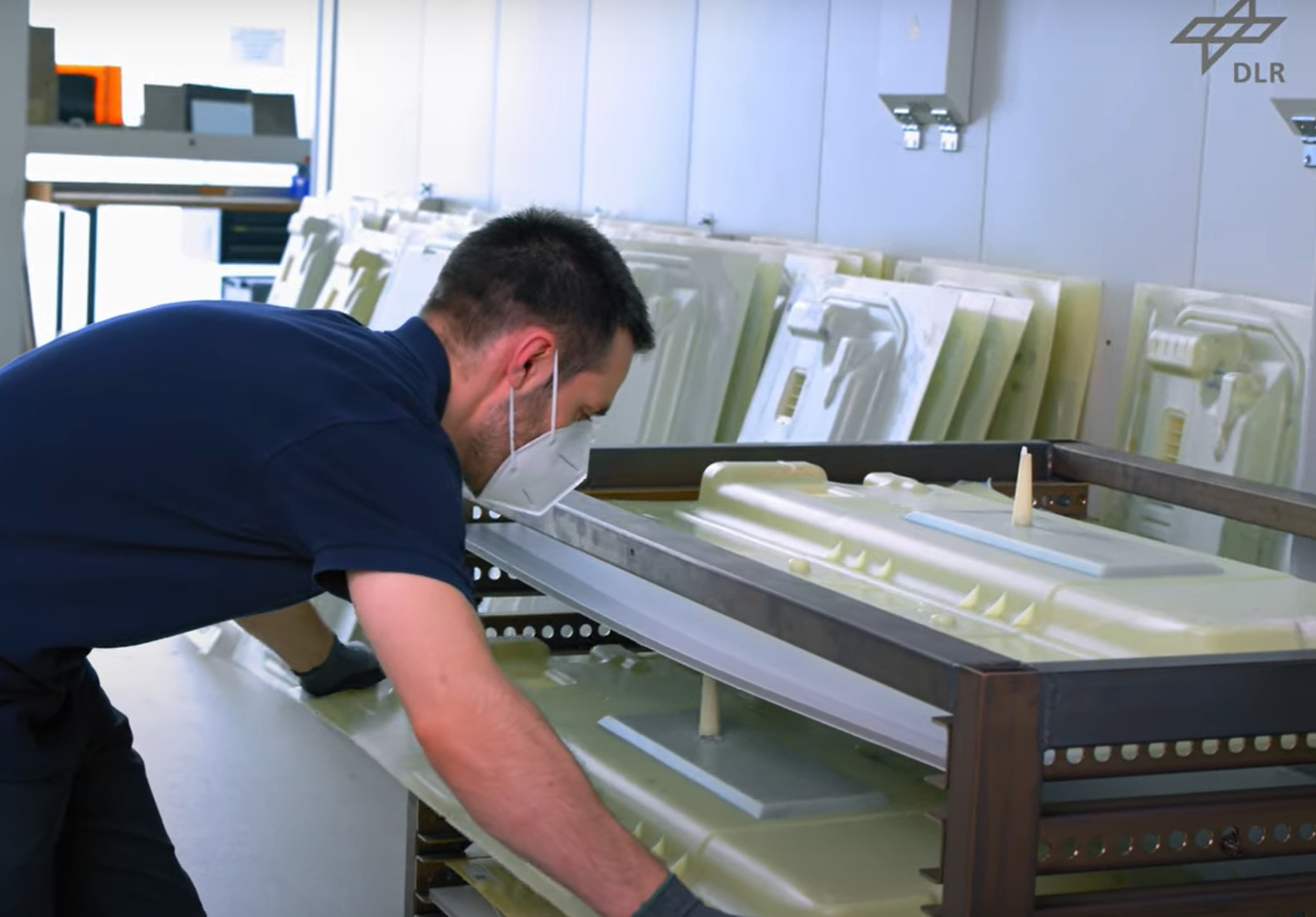
Der Polymerisationsgrad wurde durch Infrarotspektroskopie, rheometrische Daten und DEA-Sensoranalyse der Polymerisation bestätigt. Fertige Teile wurden mit zerstörungsfreien Prüfungen einschließlich Mikroskopie, Thermografie und luftgekoppeltem Ultraschall bewertet. Die Teilequalität wurde mit Prozesssensordaten korreliert und mit ähnlichen Glasfaser-/Thermoplastteilen auf dem Markt verglichen.
Zukünftige Entwicklung
Für das DLR ZLP, so Faber, sei dieses Projekt ein Erfolg gewesen. „Wir haben unseren Teil abgeschlossen und viel Wissen über den Einsatz von Sensoren entwickelt, um eine vollständig digitale Regelung der Composites-Verarbeitung zu erreichen“, sagt er. „Für eine industrielle Serienfertigung würde niemand so viele Sensoren einbauen und das würden wir auch nicht erwarten. Aber für diese Forschungsuntersuchung war dieses große Sensornetzwerk sehr präzise und half uns, vollen Einblick in das Prozess- und Materialverhalten zu haben. Wir konnten die lokalen Effekte im Prozess als Reaktion auf Variationen in der Teiledicke oder in den integrierten Materialien wie dem Schaumkern sehen.“
Er stellt fest, dass dieses Projekt viel Wissen generiert hat und sieht zukünftiges Potenzial, es auf langsamere RTM- und Infusionsprozesse anzuwenden, bei denen das Risiko für Teilequalitätsprobleme in der Vergangenheit sehr hoch war. Faber wird außerdem CosiMo-Projektentwicklungen und -Ergebnisse zum Thema „Sensorbasierte Prozessüberwachung der in-situ-Polymerisation in der T-RTM-Herstellung mit Caprolactam“ am Mi., 29. September während der Live- und virtuellen Veranstaltung SAMPE Europe 21 in Session . vorstellen 1, Raum 1 – Automobil.
Das DLR ZLP ist zudem einer von drei wichtigen Partnern im im Januar 2021 gegründeten Produktionsnetzwerk Augsburg KI (Künstliche Intelligenz), das auch die Universität Augsburg und das Fraunhofer-Institut für Gießerei, Verbundwerkstoffe und Verfahrenstechnik (Fraunhofer IGCV) vereint. Wie Dr. Markus Sause, Direktor des AI Production Network und auch CosiMo-Projektforscher bei der Entwicklung von Ultraschallsensoren, erklärt:„Wir werden diese Blaupause der Zusammenarbeit, die im CosiMo-Projekt hervorgehoben wurde, auf einen viel größeren Maßstab ausdehnen und entwickeln KI-Technologien für die Produktion mit starkem Fokus auf Verbundwerkstoffe. Unser neues 5.000 Quadratmeter großes Werk in Augsburg wird 2022 eröffnet und im Laufe des nächsten Jahres mit einer Vielzahl von Maschinen ausgestattet, damit Unternehmen demonstrieren können, was KI für reale Prozesse in einer Produktionsumgebung leisten kann.“
Faurecia Clean Mobility wird unterdessen intern die Erkenntnisse aus dem CosiMo-Projekt erweitern, das vollständig auf die Nachhaltigkeitsstrategie und den ökologischen Wandel von Faurecia ausgerichtet ist. Faurecia dankt auch dem Bayerischen Bundesministerium für Wirtschaft, Landesentwicklung und Energie, das dieses Forschungsprojekt finanziell unterstützt hat.
Harz
- Batterie
- TPE-Verbindung für nachhaltige Wattestäbchen
- Thermoplastisches Biomaterial „Feinabgestimmt“ für medizinische Anwendungen
- Medizinisches TPE für preisgekrönten Therapieball
- Anpassung von Ultraschallsensoren für die Optimierung und Steuerung von Verbundwerkstoffprozessen
- Thermoplastische Bänder zeigen weiterhin Potenzial für Verbund-Flugzeugstrukturen
- Polyscope Polymers gewinnt JEC Innovation Award für Führungsschienen aus thermoplastischem Verbundwerkstoff
- Thermoplastische Tür eine Premiere für Automobilverbundwerkstoffe
- Wichtige Faktoren, die für die Auslagerung eines Montageprozesses für den Kartonbau zu berücksichtigen sind
- Dinge, die beim Box-Build-Montageprozess zu beachten sind