Korrosionsbeständige Harze ermöglichen die Ausrüstung von petrochemischen FRP-Anlagen
Verbundwerkstoffe sind für ihre Beständigkeit in stark korrosiven Umgebungen bekannt, aber für eine optimale Leistung ist es wichtig, das richtige Harz für jede Anwendung auszuwählen. Der petrochemische Komplex der SABIC-Tochtergesellschaft Petrokemya (Riyadh, Saudi-Arabien) in Jubail, Saudi-Arabien, produziert eine Vielzahl von Rohstoffchemikalien wie Ethylen, Styrol, Chlor, rohes industrielles Ethanol und mehr. Für den Produktionsprozess benötigte der Komplex eine Verbrennungseinheit mit mehreren großen Komponenten und Rohren, die Salzsäure korrosionsfrei widerstehen müssen.
Die Konstruktion und Herstellung des Abschrecktanks, des Scrubbers, des Abgastanks und der zugehörigen Behälter und Rohrleitungen wurde einem Team übertragen, zu dem der Hersteller korrosionsbeständiger Ausrüstung Ollearis (Martorelles, Spanien) und der Auftragnehmer China Tianchen Engineering Corp. (TCC, Tianjin, China) gehörten ) und das Ingenieurbüro John Zink Hamworthy Combustion (Tulsa, Oklahoma, USA). Diese Komponenten mussten dem Kontakt mit Salzsäure standhalten, mehreren Designherausforderungen gerecht werden und eine kostengünstige Lösung sein.
Glasfaserverstärkte Verbundwerkstoffe wurden als Material gewählt, das den hochkorrosiven Chemikalien standhält und gleichzeitig eine kostengünstigere Lösung als spezielle Metalllegierungen bietet. Alle Hauptkomponenten wurden aus faserverstärktem Kunststoff (FRP) hergestellt, mit einigen kleinen Ausnahmen, einschließlich Hebe- und Niederhaltelaschen (Edelstahl), Sprühdüsen (thermoplastisch oder metallisch) und Wäscherpackung.
Um die wirtschaftlichste Lösung bereitzustellen und gleichzeitig die Leistungsanforderungen zu erfüllen, wandte sich Ollearis an drei AOC (Collierville, Tennessee, U.S.) Atlac-Harze. „Wir haben die Harztypen anhand des AOC-Leitfadens zur Chemikalienbeständigkeit sowie des Fachwissens des technischen Serviceteams von AOC unter Berücksichtigung der gehandhabten Flüssigkeiten und der vom Kunden angegebenen Auslegungstemperaturen ausgewählt. Es musste sichergestellt werden, dass die vorgeschlagenen Harze unter den [erforderlichen] Bedingungen gut funktionieren“, erklärt Adriano Ureña, technischer Leiter bei Ollearis.
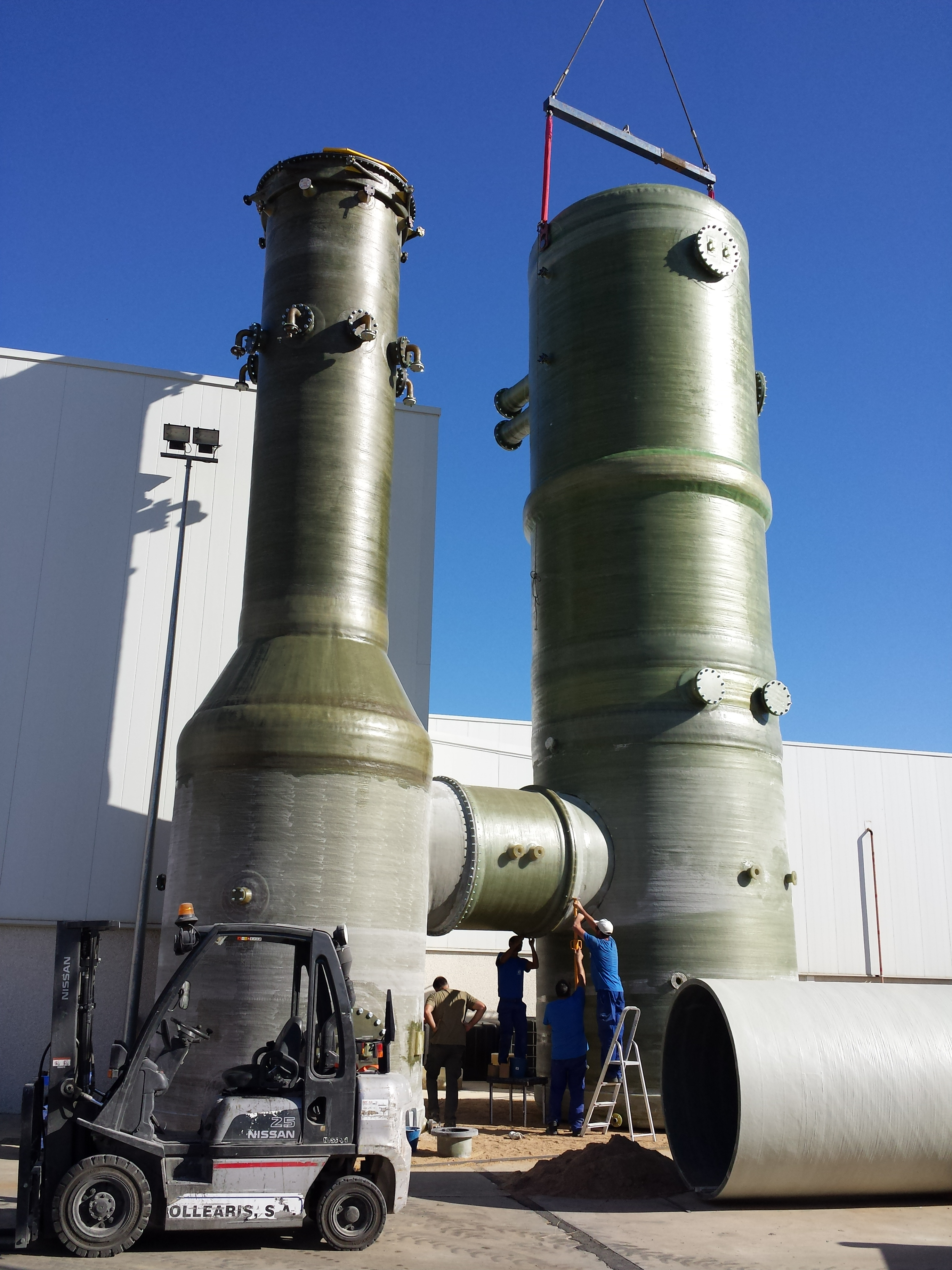
Ollearis wählte Atlac 590 Epoxid-Novolac-Harz für den Abschrecktank, der die erste Phase des Gasreinigungsprozesses darstellt. Der Tank ist 11,8 Meter hoch und hat einen Innendurchmesser (ID) von 3 Metern. Die Herausforderung besteht darin, dass im Betrieb Abgas aus der Verbrennungseinheit mit einer Temperatur von ca. Atlac 590 wurde ausgewählt, um eine Beständigkeit gegen Salzsäurelösungen und eine Beibehaltung der Festigkeit bei den erforderlichen erhöhten Temperaturen zu bieten.
Für den 14,10 Meter hohen Wäscher, den 39,7 Meter hohen Abgaskamin, aus dem das gereinigte Gas abgeführt wird, und den 1,45 Meter langen Kanal, der den Wäscher und den Quenchtank verbindet, wurde Atlac 430 Bisphenol A Epoxy-Vinylester-Harz gewählt . Dies soll ein vielseitiges Standardprodukt sein, das den vergleichsweise weniger anspruchsvollen Temperaturbedingungen für diese Komponenten entspricht – die Auslegungstemperaturen des Wäschers und des Abgaskamins erreichen bis zu 85 °C. Der Wäscher wird Salzsäurelösung ausgesetzt, die aus dem Quenchbehälter einströmt, sowie Natronlauge, die in dem Waschwasser vorhanden ist, das zur Neutralisation der Säure verwendet wird. Der Abgaskamin ist auch Luft ausgesetzt, die eine geringe Menge Salzsäure und nasses Chlor enthält.
Für das um den Wäscher und den Abschrecktank herum installierte Rohrleitungssystem wurde Atlac 383 ungesättigter Bisphenol-A-Polyester aufgrund seiner chemischen Beständigkeit gegen Säuren und ätzende Flüssigkeiten zu geringeren Kosten als Standard-Vinylesterharze gewählt.
Der Abschrecktank, der Wäscher und die zylindrischen Teile des Stapels wurden in einem hybriden Herstellungsverfahren hergestellt, bei dem das nasse Filamentwickeln mit einer gleichzeitig aufgebrachten Außenschicht aus bidirektionalen Geweben kombiniert wurde. Diese Kombination erzeugte Teile mit besseren mechanischen Eigenschaften sowohl in Ringrichtung (von der Filamentwicklung) als auch in axialer Richtung (von den Geweben, die mit der Teileachse ausgerichtet sind). Die Zugabe von Gewebe reduzierte auch den Gewichtsprozentsatz an Glasfasern pro Teil, von 70 % für ein vollständig filamentgewickeltes Teil auf 55 %. Dies erhöht die Menge an korrosionsbeständigem Harz pro Teil. Andere Komponenten wurden per Handlaminierung hergestellt.
Designherausforderungen lösen
Ollearis sah sich bei der Entwicklung der Ausrüstung für dieses Projekt mehreren Herausforderungen gegenüber. Eine Herausforderung ergab sich aus der Notwendigkeit, eine harzlastige Korrosionsschutzschicht an der Innenfläche des Abschreckbehälters anzubringen, was die Gefahr von Haarrissen – oder Rissbildung – aufgrund von Temperaturschocks während des Betriebs birgt. Das Team verbesserte die Temperaturwechselbeständigkeit des Bauteils, indem es die Korrosionsbarriere mit einem Oberflächenschleier aus Kohlefaser verstärkte.
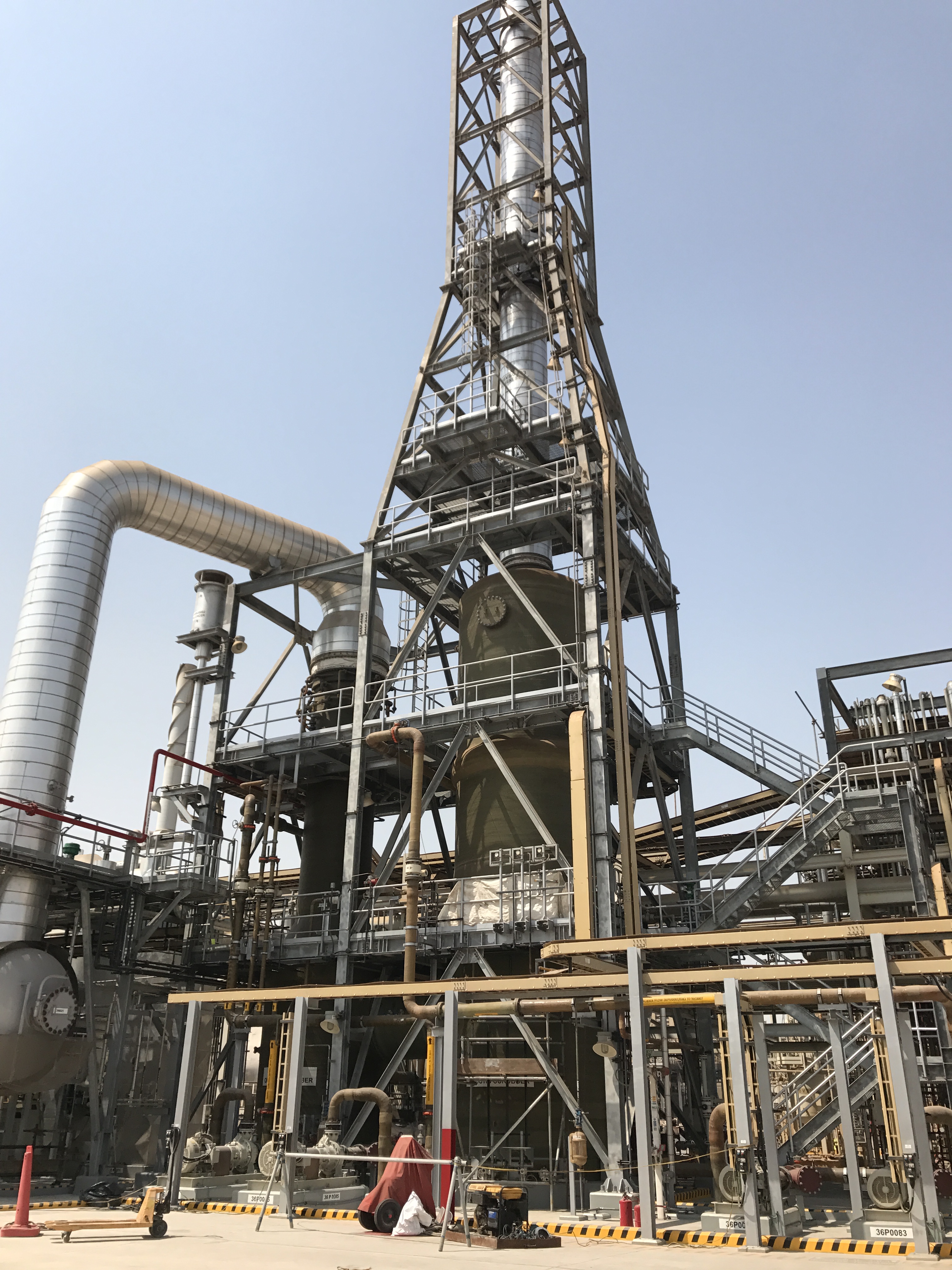
Eine zweite Herausforderung bestand darin, dass Ollearis einen Weg finden musste, das Gewicht der Packung im Inneren des Wäschers zu tragen – die Packung ist das Material, das die Gase aus der durch den Wäscher strömenden Luft entfernt. Um dies zu lösen, installierte Ollearis unter der Packung einen Verbundrost, der von einer Verbundleiste und zwei Verbundträgern getragen wird. Die Leiste und Balken haben einen hohlen, rechteckigen Querschnitt und die Leiste ist mit Polyurethanschaum gefüllt. Die Leiste wurde direkt in den filamentgewickelten zylindrischen Wäscher als ein Stück hergestellt; Beim Verkleben nach der Herstellung besteht die Gefahr des Ablösens durch Belastungen durch das Verpackungsgewicht. Die Balken werden von speziell entwickelten Verbunddüsen getragen, die mit dem Scrubber-Gehäuse verbunden sind.
Eine dritte Herausforderung bei der Konstruktion ergab sich aus der Tatsache, dass der Abschrecktank und der Wäscher unter Vakuum betrieben werden, aber einen flachen Boden haben – flache Verbundplatten haben eine geringe Druck- und Vakuumbeständigkeit und müssen normalerweise sehr dick sein, um solchen Belastungen standzuhalten, was ihre Herstellung teuer macht. Um die Projektziele zu erreichen, hat Ollearis eine kostengünstigere Lösung entwickelt, indem es eine Sandwichkonstruktion verwendet, die einen Kern aus harzimprägniertem 3D-Glasfasergewebe mit Verbundhautschichten umfasst, um die Kosten und das Gewicht eines massiven Verbundteils zu reduzieren.
Für dieses Projekt wurden die Verbundkomponenten im Jahr 2016 entwickelt und geliefert, wobei die Endmontage 2017 abgeschlossen wurde.
Harz
- CRC bietet einen Leitfaden zur Vorbereitung Ihrer Anlage auf die Hurrikansaison
- So vermeiden Sie kostspielige Ausfallzeiten durch Stromausfälle in petrochemischen Anlagen
- Betriebszeit ist der Schlüssel zur Produktion im Werk von American Gypsum
- Drew Troyer:Gesamteffektivität der Ausrüstung
- Drew Troyer:Die Wertschöpfungskette der Ausrüstung, Teil 3
- Drew Troyer:Die Wertschöpfungskette der Ausrüstung, Teil 2
- Drew Troyer:Die Wertschöpfungskette der Ausrüstung, Teil 1
- Ein Leitfaden für Anfänger zu faserverstärkten Kunststoffen (FRP)
- Preise für Volumenharze meist flach oder niedriger
- Preiserhöhung für großvolumige Harze