Einfach zu verwendende Kits ermöglichen die Reparatur von Verbundstrukturen im Feld
Modular einsetzbare Brücken sind ein Schlüsselfaktor für militärische taktische Operationen und Logistik sowie für die Wiederherstellung der Verkehrsinfrastruktur bei Naturkatastrophen. Um das Gewicht solcher Brücken zu reduzieren, wird eine Verbundkonstruktion untersucht, was wiederum die Belastung von Transportfahrzeugen und Start- und Rückholmechanismen verringert. Verbundwerkstoffe bieten auch das Potenzial, die Tragfähigkeit zu erhöhen und die Lebensdauer im Vergleich zu Metallbrücken zu verlängern.
Die Advanced Modular Composite Bridge (AMCB) ist ein Beispiel, die von Seemann Composites LLC (Gulfport, Miss., USA) und Materials Sciences LLC (Horsham, Pennsylvania, USA) unter Verwendung von kohlenstofffaserverstärkten Epoxidlaminaten (Abb. 1) entwickelt und gebaut wurde ). Die Fähigkeit, solche Strukturen vor Ort zu reparieren, war jedoch ein Problem, das die Einführung von Verbundwerkstoffen behindert hat.
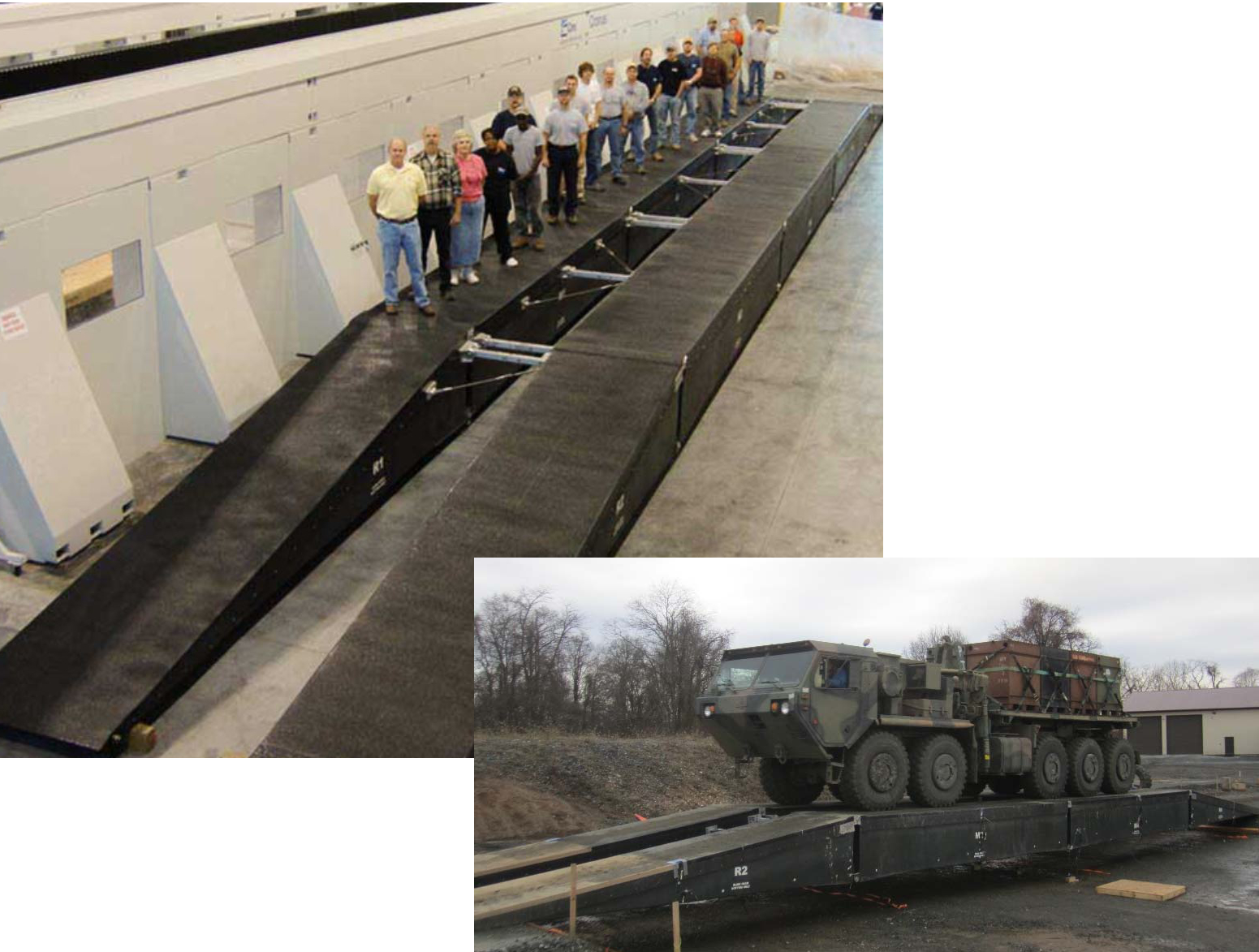
Im Jahr 2016 erhielt Custom Technologies LLC (Millersville, Md., USA) einen Phase-I-Stipendium für Small Business Innovation Research (SBIR), der von der US-Armee finanziert wurde, um eine Reparaturmethode zu entwickeln, die von Soldaten im Feld erfolgreich durchgeführt werden kann. Basierend auf dieser Methode wurde 2018 ein Phase-II-SBIR-Zuschuss gewährt, um neue Materialien und batteriebetriebene Geräte zu demonstrieren, die 90 % oder mehr der ursprünglichen Festigkeit der Struktur wiederherstellen können, selbst wenn die Reparatur des Patches von einem Anfänger ohne vorherige Schulung durchgeführt wird . Die Machbarkeit der Technologie wurde durch eine Reihe von analytischen, Materialauswahl-, Prüfkörperherstellungs- und mechanischen Prüfaufgaben sowie Klein- und Großreparaturen nachgewiesen.
Von rissigen Schiffsdecks zu Brückendecks
Der Hauptprüfer für beide SBIR-Phasen war Michael Bergen, Gründer und Präsident von Custom Technologies LLC. Bergen zog sich vom Naval Surface Warfare Center (NSWC) Carderock mit einer 27-jährigen Anstellung in der Abteilung für Strukturen und Materialien zurück, wo er die Entwicklung und Anwendung von Verbundtechnologien für die Flotte der US-Marine leitete. Dr. Roger Crane kam 2015 zu Custom Technologies, nachdem er 2011 mit 32 Dienstjahren aus der US Navy ausgeschieden war. Seine Expertise im Bereich Verbundwerkstoffe umfasst technische Veröffentlichungen und Patente zu Themen wie neue Verbundwerkstoffe, Prototypenfertigung, Fügeverfahren, multifunktionale Verbundwerkstoffe, Überwachung des strukturellen Zustands und Reparatur von Verbundwerkstoffen.
Diese beiden Experten hatten bereits ein einzigartiges Verfahren entwickelt, bei dem Verbundwerkstoffe verwendet wurden, um Risse in 5456 Aluminiumaufbauten des Lenkflugkörperkreuzers der USS Ticonderoga CG-47-Klasse zu reparieren. „Dieses Verfahren wurde entwickelt, um das Risswachstum zu reduzieren und als kostengünstige Alternative zu einem Austausch der Deckplatten im Wert von 2-4 Millionen US-Dollar zu dienen“, sagt Bergen. „Damit haben wir bewiesen, dass wir wissen, wie man Reparaturen außerhalb des Labors und in einer echten Serviceumgebung durchführt. Die Herausforderung bestand jedoch darin, dass die derzeitigen Methoden für militärische Vermögenswerte nicht sehr erfolgreich sind. Die Optionen sind eine geklebte Doppler-Reparatur [im Wesentlichen das Aufkleben einer Platte auf den beschädigten Bereich] oder die Außerbetriebnahme der Anlage für Reparaturen auf Depotebene (D-Ebene). Es gibt so viele Assets abseits, weil eine D-Level-Reparatur erforderlich ist.“
Was benötigt wird, so fährt er fort, „ist eine Methode, die von einem Soldaten ohne Erfahrung mit Verbundwerkstoffen nur mit einem Bausatz und einer Reparaturanleitung ausgeführt werden kann. Unser Ziel war es, den Prozess einfach zu machen:Handbuch lesen, Schaden begutachten und reparieren. Wir wollten kein Mischen von Flüssigharzen, da dies eine genaue Messung erfordert, um eine vollständige Aushärtung zu gewährleisten. Wir brauchten auch ein System ohne HAZMAT-Abfall, das nach Abschluss der Reparatur behandelt werden muss. Und es musste in Kits verpackt werden, die von den bereits vorhandenen Netzwerken bereitgestellt werden können.“
Neuartige geklebte Patchmaterialien
Eine Lösung, die Custom Technologies erfolgreich demonstriert hat, ist ein tragbares Kit, das einen geklebten Verbundpflaster ermöglicht, der auf die Größe des Schadens zugeschnitten ist – bis zu 12 Quadratzoll – unter Verwendung eines gehärteten Epoxidklebers. Demonstrationen wurden an Verbundwerkstoffen durchgeführt, die für das 3 Zoll dicke AMCB-Deck repräsentativ sind, das einen 3 Zoll dicken Balsakern (15 Pfund pro Kubikfuß Dichte) mit Deckschichten aufweist, die zwei Lagen von Vectorply Corp. (Phenix City, Ala., USA) C-LT 1100 Carbon 0°/90° biaxial genähtes Gewebe, eine Lage C-TLX 1900 Carbonfaser 0°/+45°/-45° triaxial und zwei weitere Lagen C-LT 1100 für insgesamt fünf Lagen. „Wir haben uns entschieden, dass das Kit vorgefertigte Patches in einem quasi-isotropen Layup ähnlicher Multiaxials verwendet, damit die Stofforientierung kein Problem darstellt“, sagt Crane.
Die nächste Ausgabe war die Harzmatrix für Laminierreparaturen. Um das Mischen flüssiger Harze zu vermeiden, würde das Pflaster Prepregs verwenden. „Die Herausforderung dabei ist jedoch die Lagerung“, erklärt Bergen. Um eine lagerfähige Patch-Lösung zu entwickeln, hat sich Custom Technologies mit Sunrez Corp. (El Cajon, Kalifornien, USA) zusammengetan, um ein Glasfaser-/Vinylester-Prepreg zu entwickeln, das mit ultraviolettem (UV) Licht in sechs Minuten aushärtet. Es funktionierte auch mit Gougeon Brothers (Bay City, Michigan, USA), die die Verwendung einer neuartigen flexiblen Epoxidharzfolie vorschlugen.
Frühe Untersuchungen hatten bereits gezeigt, dass Epoxid das am besten geeignete Harz für ein Kohlefaser-Prepreg ist – UV-härtender Vinylester funktioniert hervorragend mit durchscheinenden Glasfasern, härtet jedoch nicht unter lichtblockierenden Kohlefasern aus. Basierend auf dem neuartigen Film von Gougeon Brothers zeigte das fertige Epoxid-Prepreg eine einstündige Aushärtung bei 210 °F/99 °C mit einer langen Haltbarkeit bei Raumtemperatur – eine Lagerung bei niedrigen Temperaturen ist nicht erforderlich. Das Harz härtet auch bei höheren Temperaturen aus, sagt Bergen, zum Beispiel bei 350 °F/177 °C, wenn eine höhere Glasübergangstemperatur (Tg ) Wird benötigt. Beide Prepregs werden im tragbaren Reparaturset als vorgefertigte Prepreg-Patch-Layups geliefert, die in Plastikfolienhüllen versiegelt sind.
Da Reparatursätze längere Zeit gelagert werden können, musste Custom Technologies eine Haltbarkeitsstudie durchführen. „Wir kauften vier Hartplastikkoffer – typisch für den Typ, den das Militär für den Versand von Ausrüstung verwendet – und legten Proben der Epoxidklebstoffe und des Vinylester-Prepregs in jeden“, sagt Bergen. Die Gehäuse wurden dann an vier verschiedenen Orten zum Testen platziert:auf dem Dach der Anlage von Gougeon Brothers in Michigan, auf dem Dach eines Flughafens in Maryland, im Freien in einer Anlage im Yucca Valley (Kalifornische Wüste) und in einem Korrosionsprüflabor im Freien in Südflorida. Alle Fälle hatten Datenlogger, bemerkt Bergen, „und wir haben alle drei Monate Daten- und Materialproben zur Auswertung gezogen. Eine maximale Temperatur von 140 °C wurde von den Boxen in Florida und Kalifornien gemessen, was für die meisten Reparaturharze eine echte Herausforderung ist.“ Darüber hinaus testete Gougeon Brothers das neu entwickelte unverdünnte Epoxidharz im eigenen Haus. „Proben, die monatelang bei 120 °C in einem Ofen aufbewahrt wurden, begannen zu polymerisieren“, sagt Bergen. „Bei entsprechenden Proben, die bei 110 °F gehalten wurden, hat sich die Harzchemie jedoch nur geringfügig verbessert.“
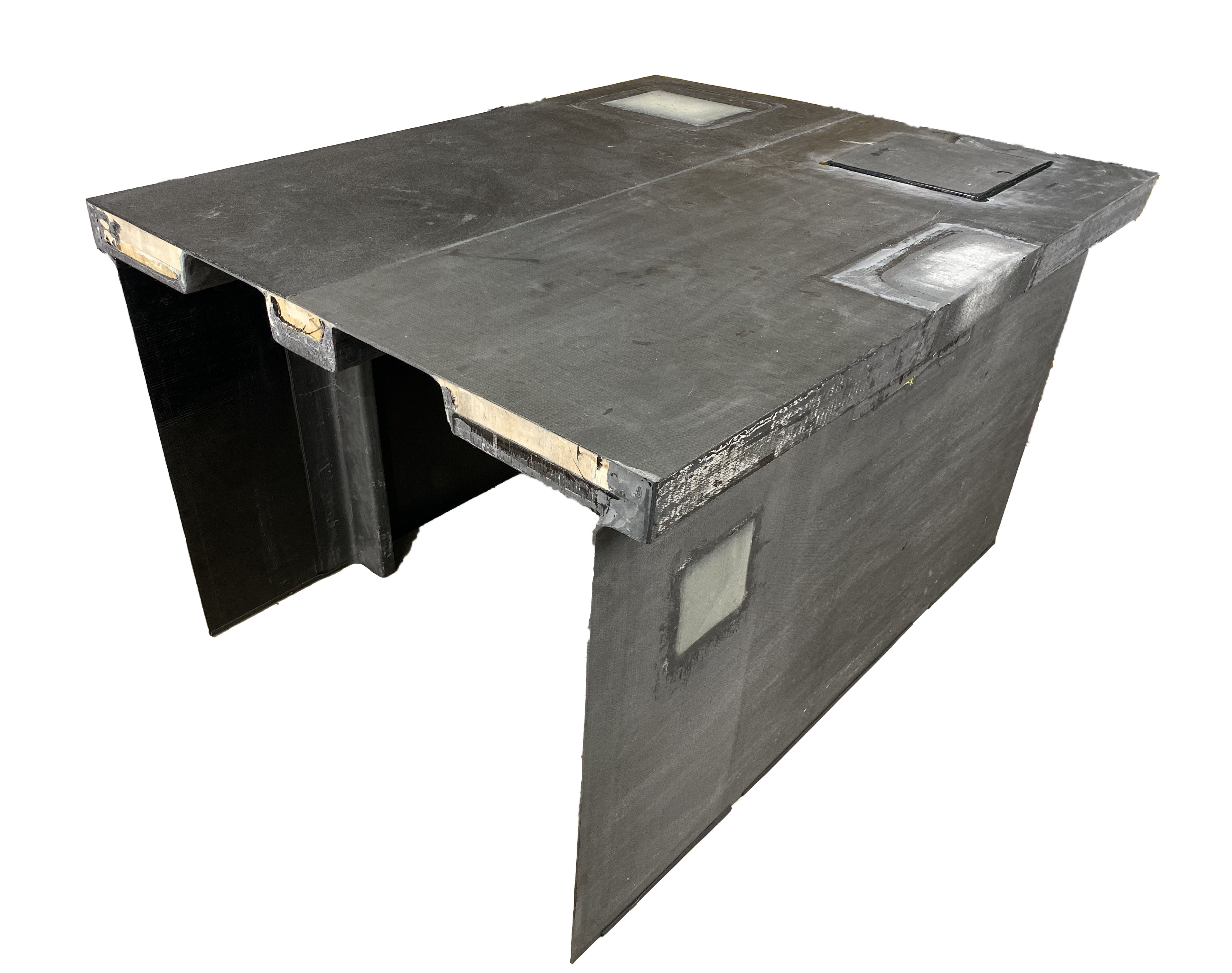
Reparaturtest
Zur Demonstration der Reparaturtechnik mussten repräsentative Laminate hergestellt, beschädigt und anschließend repariert werden. „Im Phase-I-Projekt haben wir zunächst mit kleinen 4 x 48-Zoll-Trägern und Vierpunkt-Biegetests gearbeitet, um die Durchführbarkeit unseres Reparaturprozesses zu bewerten“, sagt Crane. „Wir haben dann im Phase-II-Projekt auf 12 x 48-Zoll-Panels umgestellt, eine Last angelegt, um einen biaxialen Spannungszustand bis zum Versagen zu erzeugen, und dann die Reparaturleistung bewertet. Im Projekt der Phase II haben wir auch Reparaturen an einem von uns gebauten AMCB-Modell durchgeführt.“
Die Testplatten, mit denen die Reparaturleistung demonstriert wurde, wurden mit dem gleichen Stammbaum in Laminat und Kern wie der von Seemann Composites gebaute AMCB hergestellt, sagt Bergen, „aber wir haben die Deckschichtdicke von 0,375 Zoll auf 0,175 Zoll verkleinert, basierend auf den parallelen Achsen Satz. Dieser Ansatz wurde zusammen mit zusätzlichen Elementen der Balkentheorie und der klassischen Laminattheorie [CLT] verwendet, um das Trägheitsmoment und die effektive Steifigkeit des AMCB in Originalgröße mit handhabbareren und kosteneffizienteren verkleinerten Demonstrationsartikeln in Beziehung zu setzen. Anschließend verwendeten wir von XCraft Inc. (Boston, Massachusetts, USA) entwickelte Finite-Elemente-Analyse-Modelle (FEA), um das Design der strukturellen Reparaturen zu verfeinern.“ Kohlefasergewebe für die Testplatten und das AMCB-Modell wurden von Vectorply bezogen und der Balsakern wurde von Core Composites (Bristol, R.I., USA) geliefert.
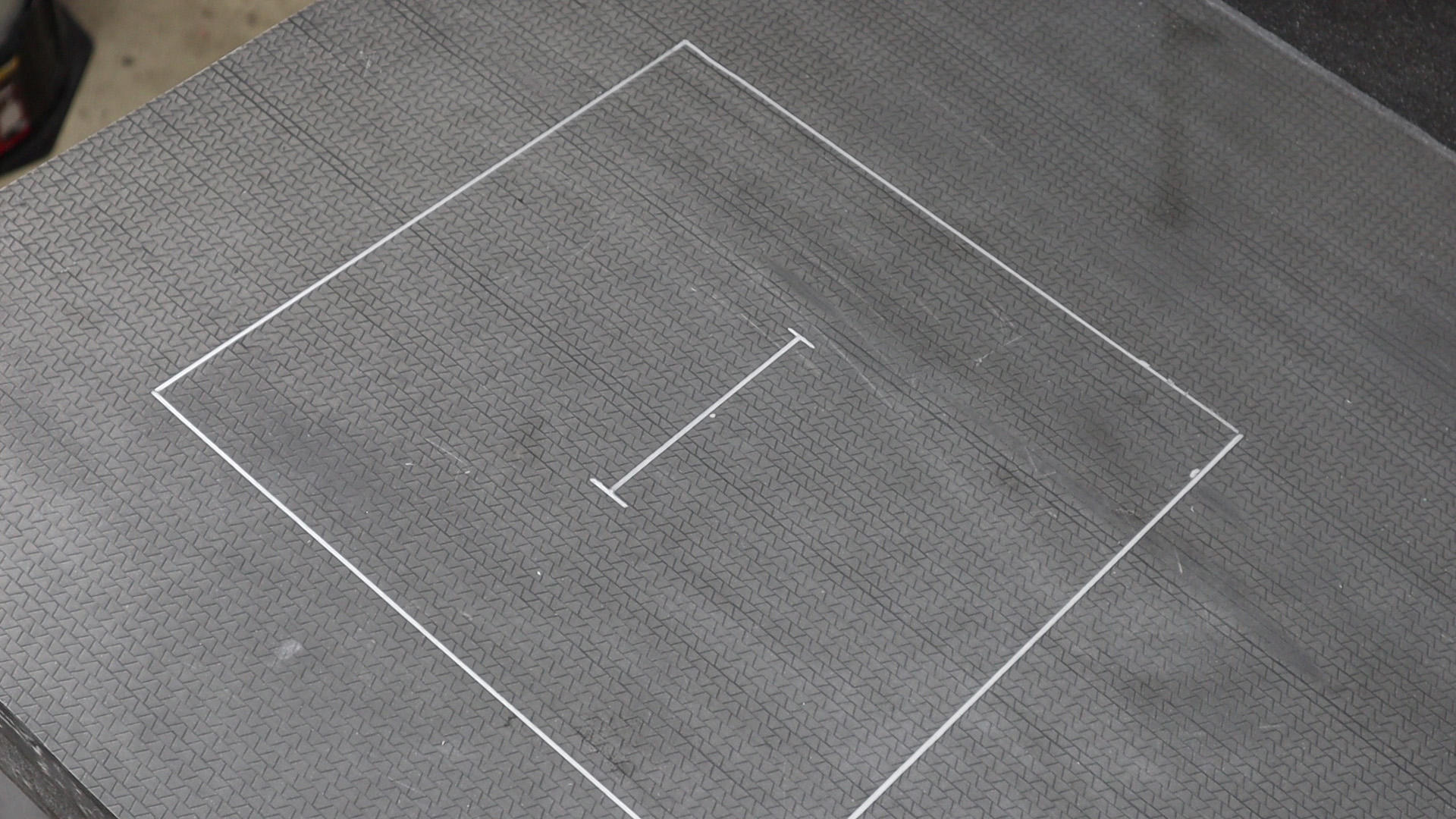
Schritt 1. Diese Testtafel zeigt den 3-Zoll-Lochdurchmesser, um den in der Mitte markierten Schaden sowie den Reparaturumfang zu simulieren. Bildnachweis für alle Schritte:Custom Technologies LLC.
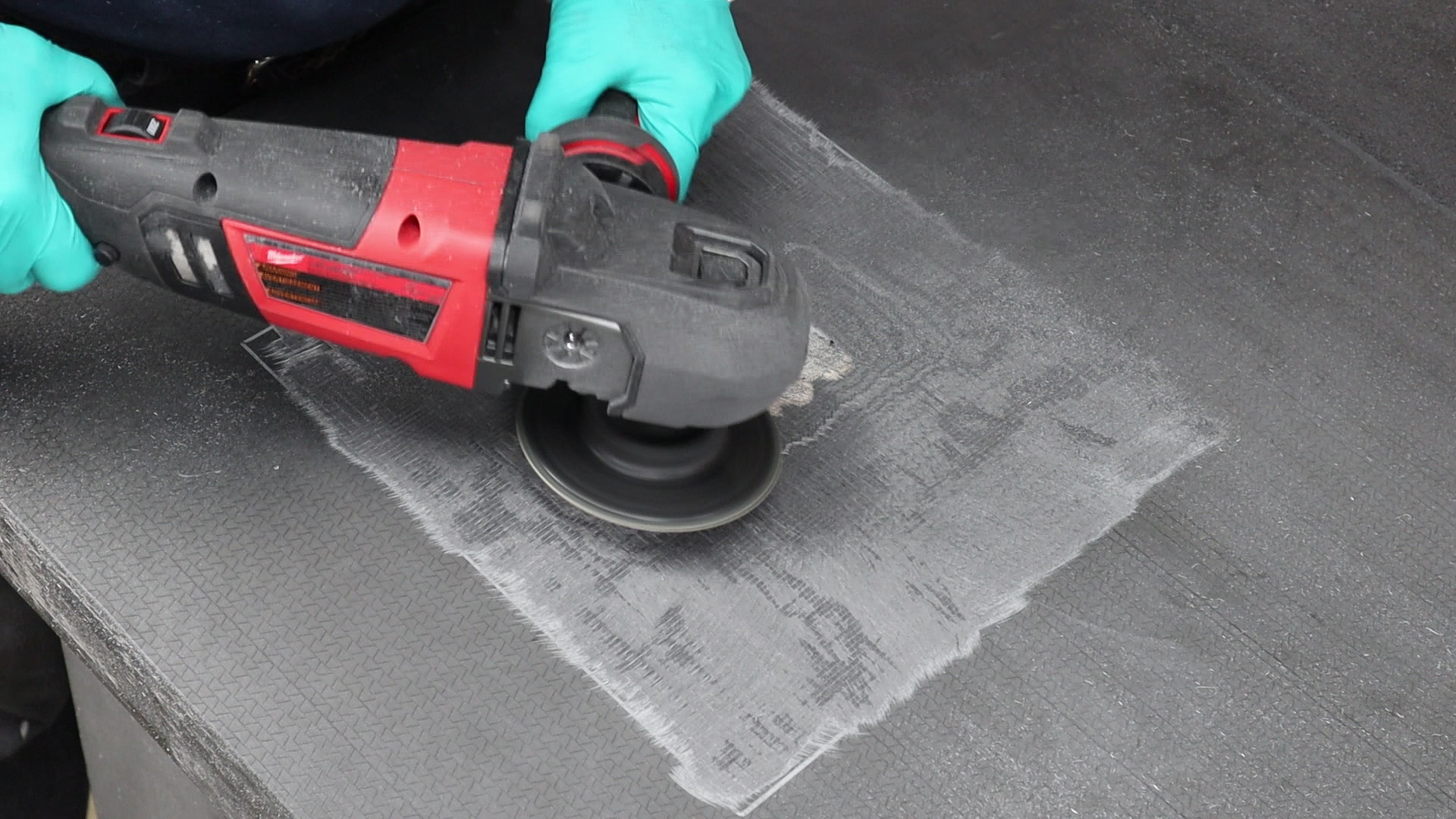
Schritt 2. Ein batteriebetriebener Handschleifer wird verwendet, um beschädigtes Material zu entfernen und einen 12:1-Kegel zu schleifen, um den Reparaturflicken zu erhalten.
„Wir wollten in den Testpaneelen einen höheren Schadensgrad simulieren, als er wahrscheinlich auf Brückendecks im Feld zu sehen ist“, erklärt Bergen. „Unser Ansatz bestand also darin, eine Lochsäge zu verwenden, um ein Loch mit einem Durchmesser von 3 Zoll zu machen. Wir haben dann den Stopfen des beschädigten Materials herausgezogen und mit einem handgehaltenen Druckluftschleifer einen 12:1-Schal durchgeführt.“
Für die Kohlefaser/Epoxid-Reparatur, erklärt Crane, wurde das Prepreg nach dem Entfernen des „beschädigten“ Obermaterials und dem Anbringen des entsprechenden Schals auf Breite und Länge zugeschnitten, um der Konizität der beschädigten Stelle zu entsprechen. „Für unsere Testpaneele waren dazu vier Lagen Prepreg erforderlich, die das Reparaturmaterial mit der Oberseite der unbeschädigten Carbon-Oberseite abgleichen. Danach wurden drei Auflagen des Kohlenstoff/Epoxid-Prepregs über diesem Reparaturabschnitt zentriert. Jede nachfolgende Lage erstreckte sich 1 Zoll auf allen Seiten der darunter liegenden Lage, was eine allmähliche Lastübertragung vom „guten“ umgebenden Material in den reparierten Bereich ermöglichte.“ Die Gesamtzeit für diese Reparatur – einschließlich Vorbereitung des Reparaturbereichs, Schneiden und Einbringen des Reparaturmaterials und Anwendung des Aushärtungsverfahrens – betrug ungefähr 2,5 Stunden.
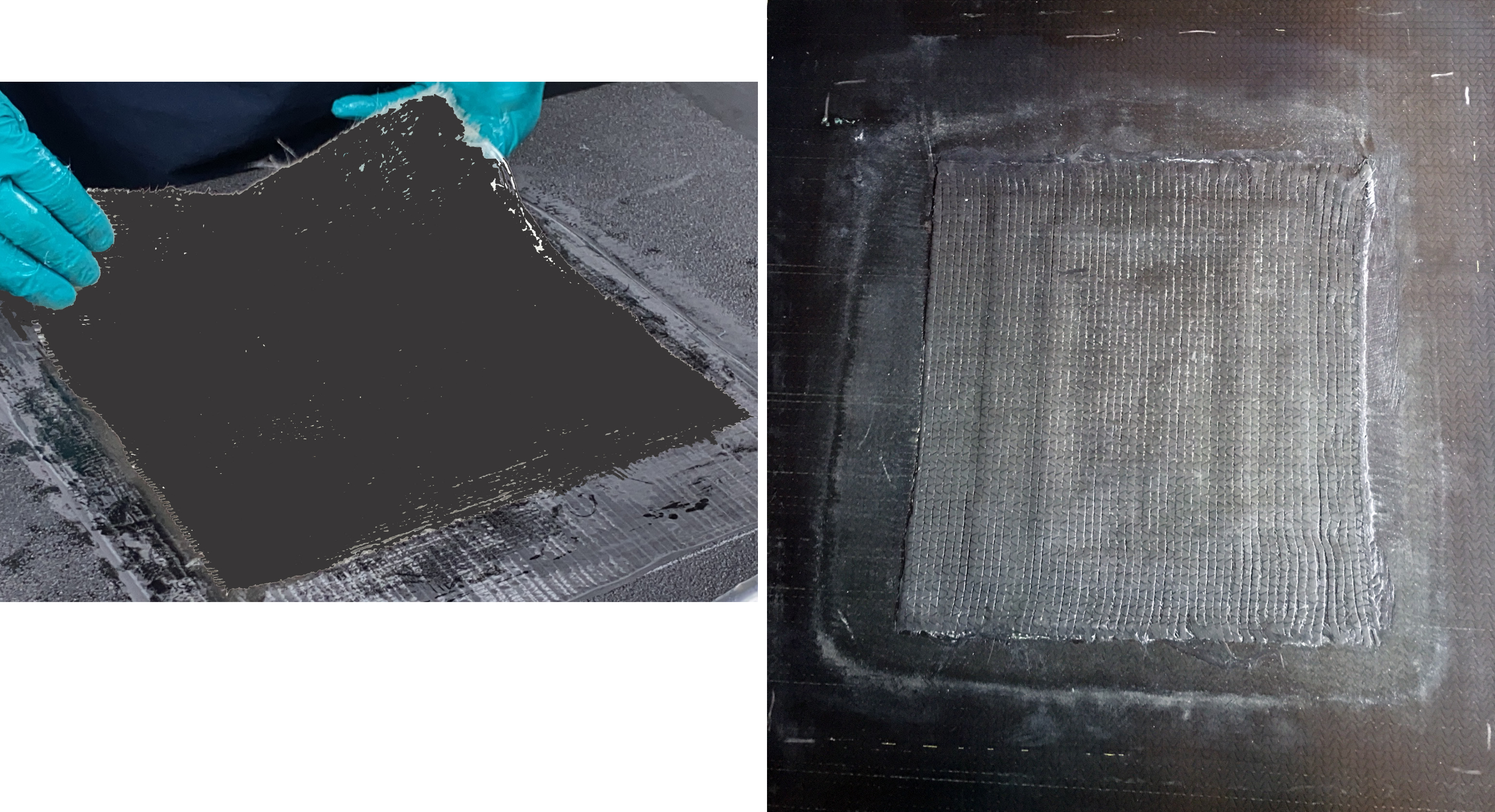
Obwohl die Carbon/Epoxid-Reparatur einfach und schnell ist, erkannte das Team die Notwendigkeit einer noch zweckmäßigeren Lösung, die die Leistung wiederherstellen könnte. Dies führte zur Erforschung des ultraviolett (UV) gehärteten Prepregs. „Das Interesse an Sunrez-Vinylesterharz basierte auf früheren Navy-Erfahrungen mit Mark Livesay, dem Gründer des Unternehmens“, erklärt Bergen. „Wir begannen damit, Sunrez ein quasi-isotropes Glasgewebe zum Prepreg mit ihrem Vinylester zur Verfügung zu stellen und das Härtungsprofil unter verschiedenen Bedingungen zu evaluieren. Da Vinylesterharz außerdem keine so geeigneten sekundären Bindungseigenschaften wie Epoxid bietet, wurden zusätzliche Anstrengungen unternommen, um verschiedene Haftvermittler zu bewerten und einen für diese Anwendung zu qualifizieren.“
Ein weiteres Problem war, dass Glasfasern nicht die gleichen mechanischen Eigenschaften wie Kohlefasern aufweisen. „Dies wurde durch die Verwendung einer zusätzlichen Schicht Glas/Vinylester im Vergleich zum Carbon/Epoxid-Patch behoben“, sagt Crane. „Der Grund, warum nur eine einzige zusätzliche Schicht erforderlich war, war, dass das Glasmaterial ein schwereres Gewebe war.“ Dies führte zu einem geeigneten Pflaster, das selbst bei sehr kalten / eisigen Außentemperaturen ohne Wärmezufuhr in sechs Minuten aufgebracht und anschließend ausgehärtet werden konnte. Crane merkt an, dass diese Reparatur in einer Stunde abgeschlossen sein könnte.
Beide Patch-Systeme wurden demonstriert und getestet. Bei jeder Reparatur wurde die zu beschädigende Stelle markiert (Schritt 1), mit der Lochsäge erstellt und anschließend mit einem Akku-Handschleifer entfernt (Schritt 2). Der Reparaturbereich wurde dann zu einer 12:1 Konizität geschärft. Die geschälte Oberfläche wurde mit Alkoholtupfern gereinigt (Schritt 3). Als nächstes wurde das Reparaturpflaster zugeschnitten, auf der gereinigten Oberfläche positioniert (Schritt 4) und mit einer Rolle verfestigt, um Luftblasen zu entfernen. Für das Glasfaser/UV-aushärtende Vinylester-Prepreg wurde dann eine Abziehschicht über den Reparaturbereich gelegt und das Pflaster wurde sechs Minuten lang mit einem kabellosen UV-Licht ausgehärtet (Schritt 5). Für das Kohlefaser/Epoxid-Prepreg wurde der Reparaturbereich vakuumiert und mit einem vorprogrammierten, batteriebetriebenen Ein-Knopf-Heißbonder eine Stunde lang bei 99 °C (210 °F) ausgehärtet.
Reparaturschritte
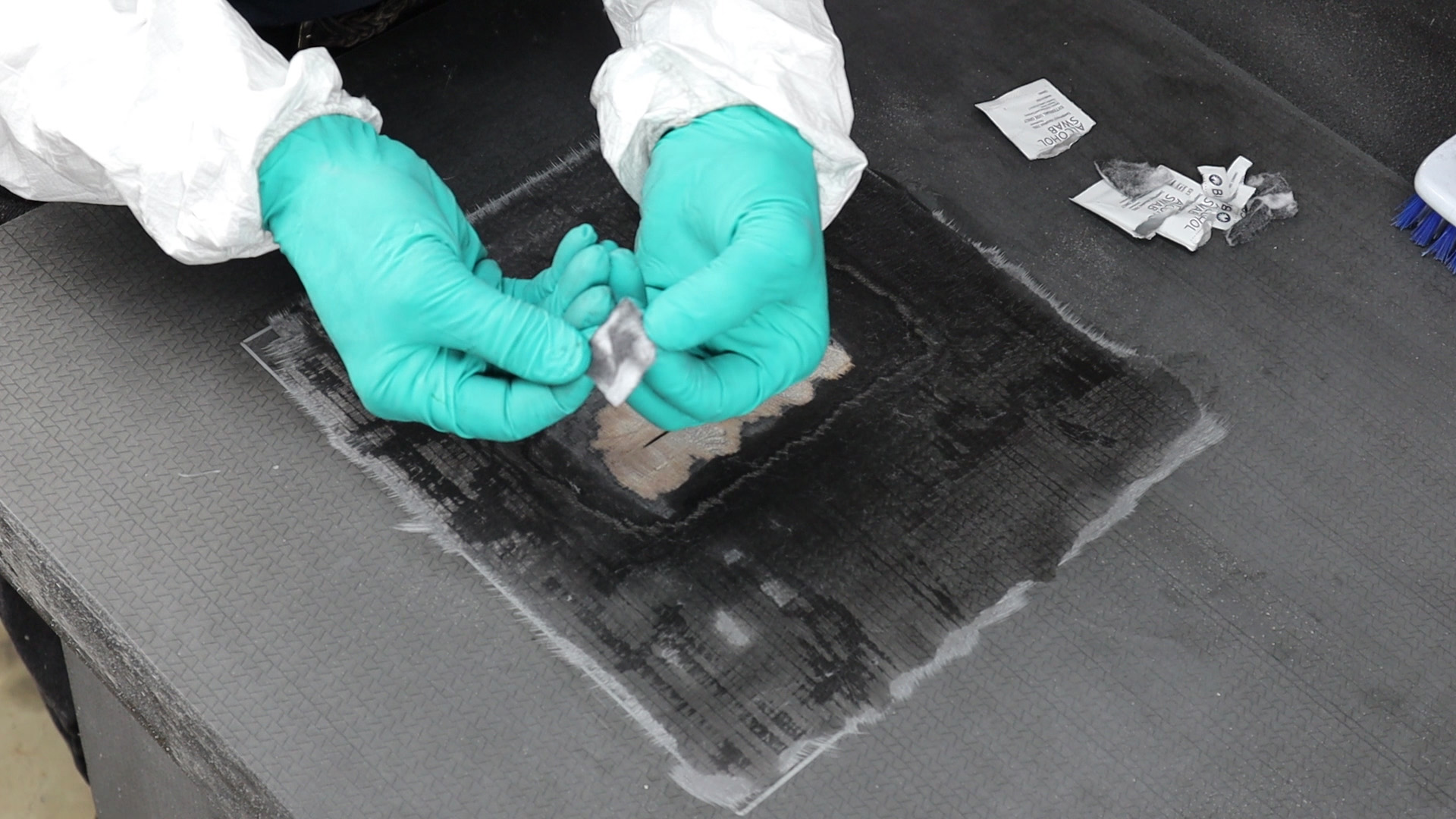
Schritt 3. Der vorbereitete Reparaturbereich wird dann mit einem Lösungsmitteltuch unter Verwendung von Einweg-Alkoholpads gereinigt.
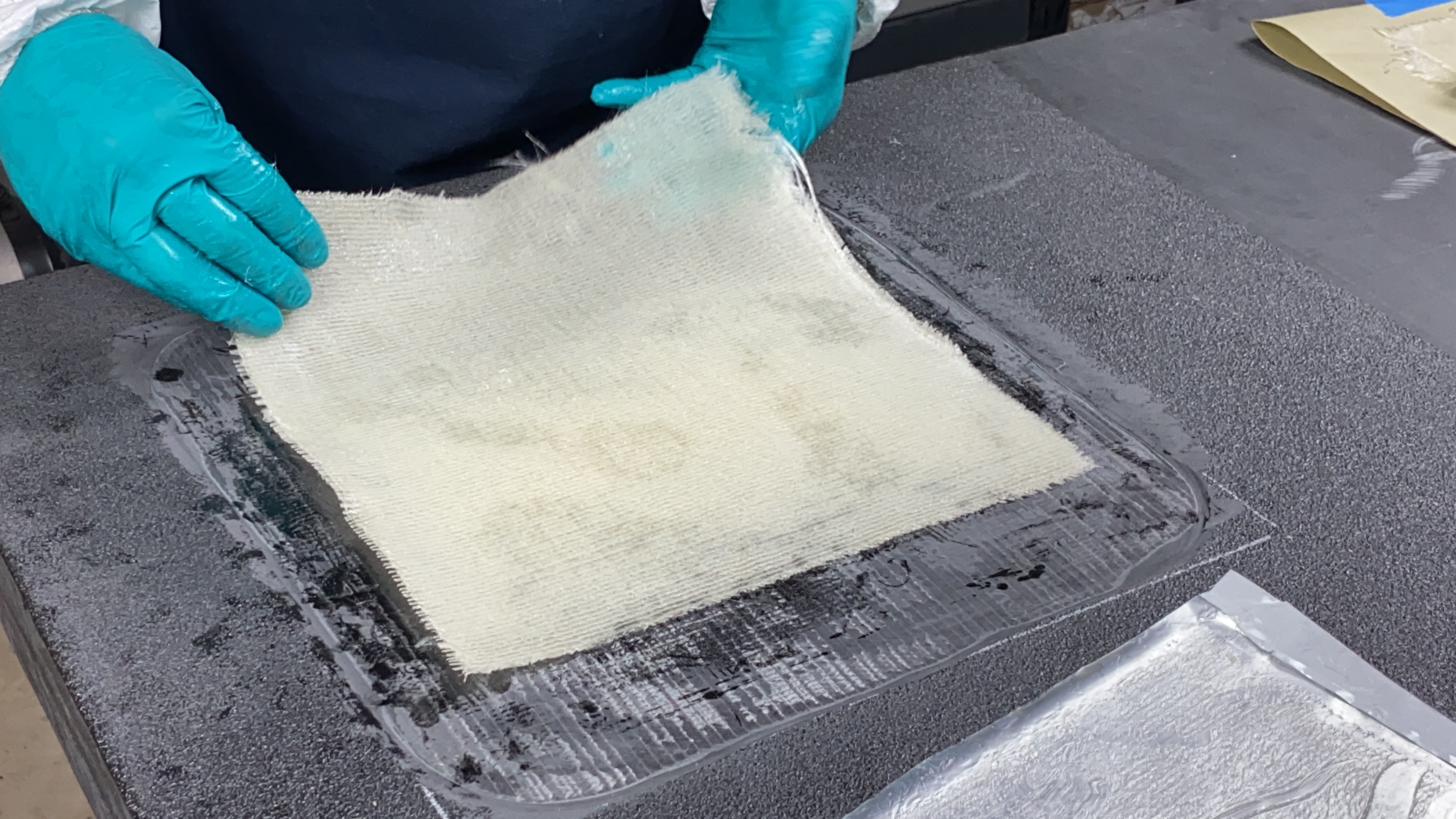
Schritt 4. Das Glasfaser-/Vinylester-Reparaturpflaster wird zugeschnitten und auf der Reparaturstelle positioniert.
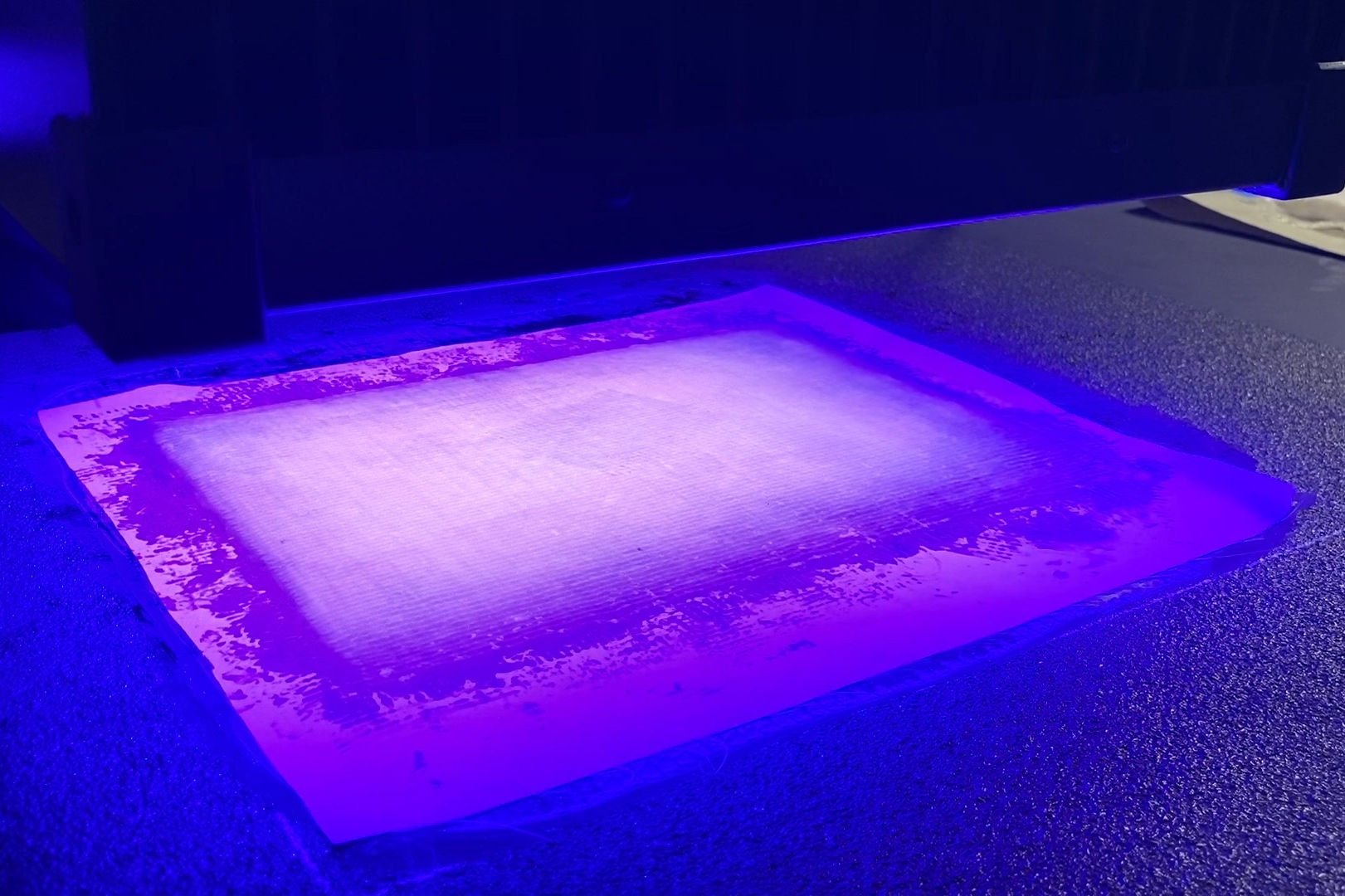
Schritt 5. Nachdem eine Abziehschicht über dem Reparaturbereich angebracht wurde, wird die Patch-Reparatur sechs Minuten lang mit einem kabellosen UV-Licht ausgehärtet.
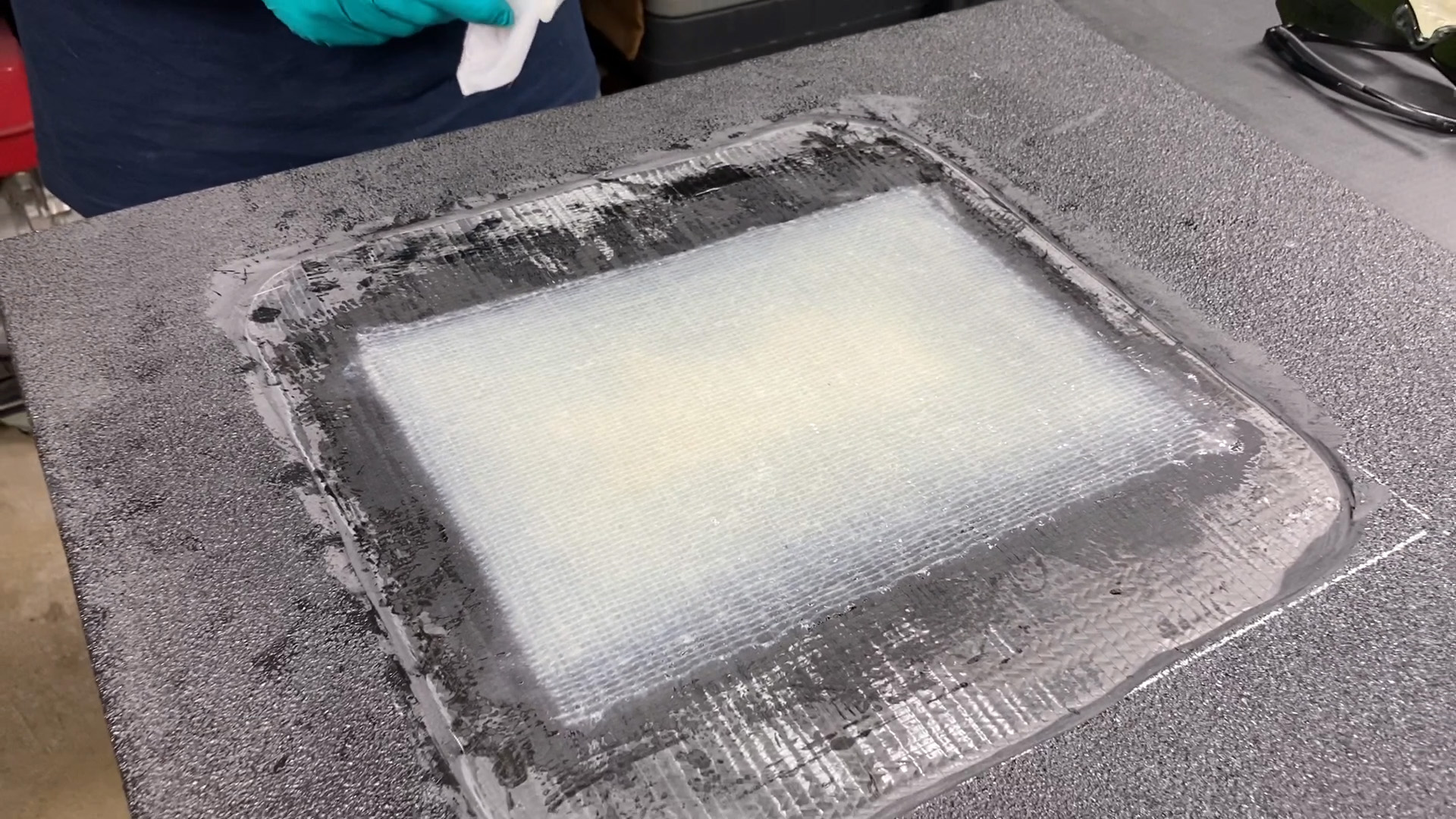
Schritt 6. Abgeschlossene UV-gehärtete Glasfaser/Vinylester-Prepreg-Flickenreparatur.
Vorherige Nächste„Wir haben dann Tests durchgeführt, um die Klebeverbindung des Pflasters und die Fähigkeit, die Tragfähigkeit der Struktur wiederherzustellen, zu bewerten“, sagt Bergen. „In Phase 1 mussten wir die einfache Anwendung und die Fähigkeit, die Festigkeit von mindestens 75 % wiederherzustellen, nachweisen. Dies wurde an den 4 x 48-Zoll-Carbonfaser/Epoxid- und Balsa-Kernträgern in Vierpunktbiegung nach der Reparatur des simulierten Schadens erreicht. Das Phase-2-Projekt verwendete 12 x 48-Zoll-Platten und musste unter komplexen Belastungsbelastungen eine Festigkeitsanforderung von mehr als 90 % aufweisen. Wir haben all diese Anforderungen erfüllt und dann die Reparaturmethoden auf dem AMCB-Modell gefilmt, um eine visuelle Referenz für die Verwendung der Infield-Techniken und -Geräte zu bieten.“
Erfolg für Anfänger, zukünftige Anwendungen
Ein wichtiger Aspekt des Projekts war der Nachweis, dass ein Anfänger die Reparatur problemlos durchführen kann. Bergen hatte dazu eine Idee:„Ich hatte unseren beiden technischen Ansprechpartnern bei der Army, Dr. Bernard Sia und Ashley Genna, eine Vorführung zugesagt. Bei der abschließenden Überprüfung des Phase-I-Projekts bat ich Ashley, die noch keine Erfahrung mit Reparaturen hatte, die Reparatur durchzuführen. Mit den Kits und dem Handbuch, die wir zur Verfügung gestellt haben, hat sie den Patch angebracht und die Reparatur ohne Probleme abgeschlossen.“
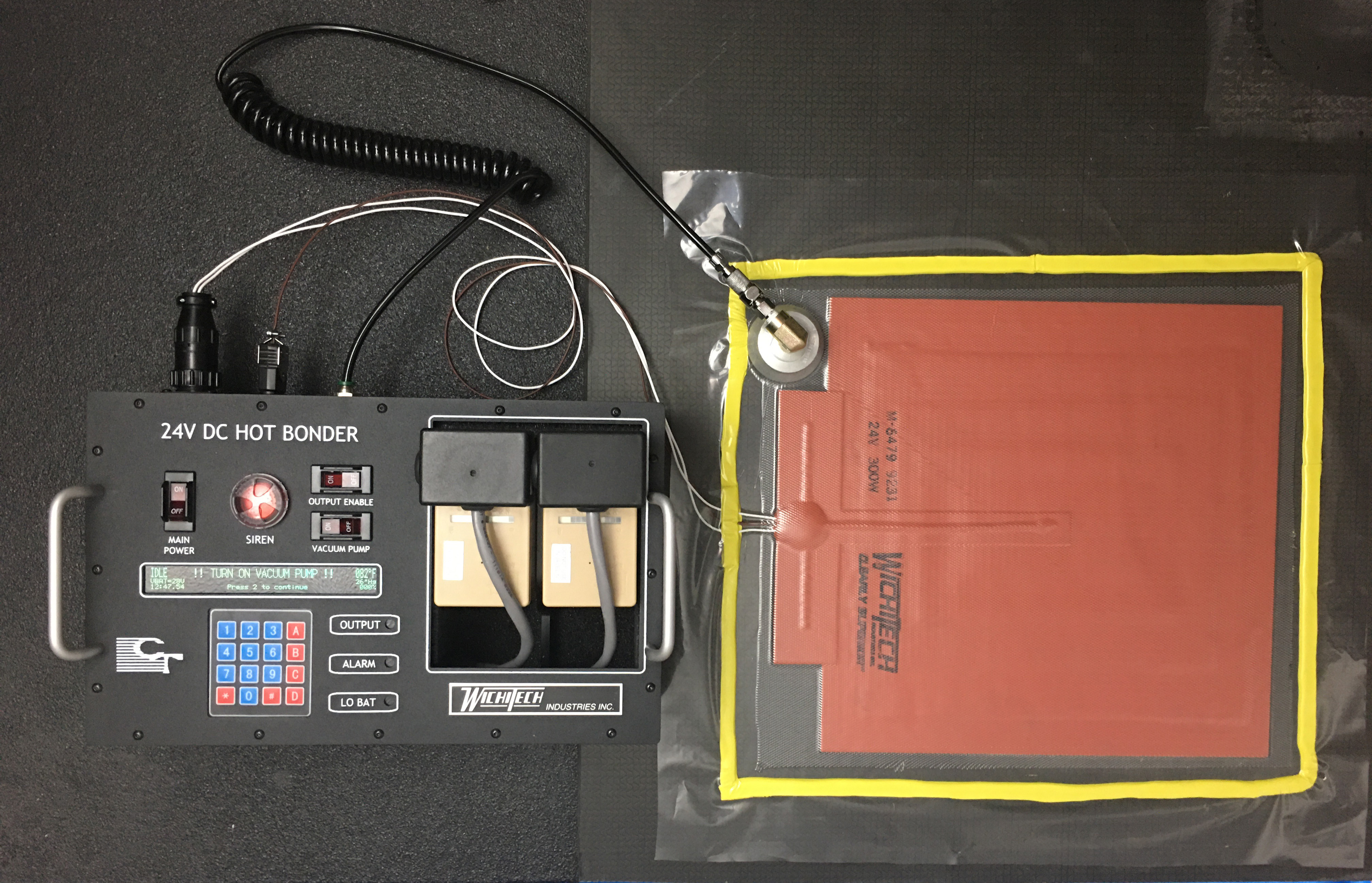
Eine weitere wichtige Entwicklung ist das batteriebetriebene Härtungssystem (Abb. 2). „Bei der Reparatur vor Ort haben Sie nur Batteriestrom“, sagt Bergen. „Alle Prozessgeräte in unserem entwickelten Reparaturset sind kabellos.“ Dazu gehört der batteriebetriebene Hot Bonder, den Custom Technologies mit dem Hot Bonder-Lieferanten WichiTech Industries Inc. (Randallstown, Md., USA) entwickelt hat. „Dieser batteriebetriebene Heat Bonder ist vorprogrammiert, um die Aushärtung abzuschließen, sodass der Anfänger den Aushärtungszyklus nicht programmieren muss“, sagt Crane. „Sie drücken einfach den Knopf und es schließt die entsprechende Rampe und das Einweichen ab.“ Die derzeit verwendeten Batterien halten ein Jahr, bevor sie wieder aufgeladen werden müssen.
Nachdem das Phase-II-Projekt nun abgeschlossen ist, bereitet Custom Technologies einen Vorschlag zur weiteren Verbesserung vor und sammelt Interessenbekundungen und Unterstützungsschreiben. „Unser Ziel ist es, diese Technologie auf TRL 8 auszureifen und ins Feld zu bringen“, sagt Bergen. „Wir sehen auch Potenzial für nicht-militärische Anwendungen.“
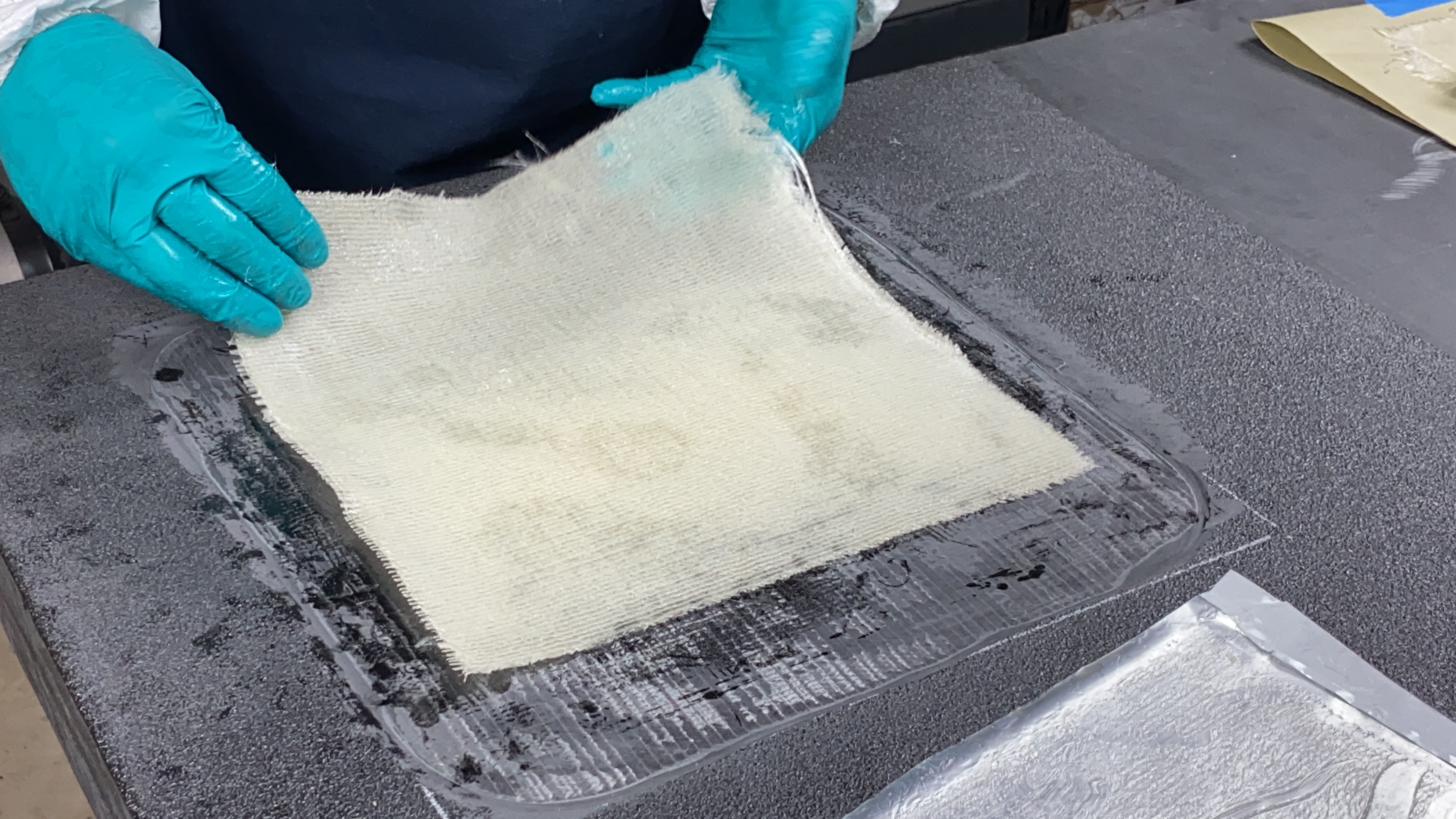
Harz
- 3 gängigste technische Anwendungen für Duroplast-Verbundwerkstoffe
- Verbundwerkstoffherstellung:Die Herstellung von Verbundwerkstoffen
- Thermoplastische Strukturen im Fokus der China Composites Expo-Präsenz von Engel
- Entwicklung von zusammengesetzten Isogitterstrukturen mit innovativer Abscheidungstechnologie
- Alveus vermarktet Compa Repairs Schiffsreparaturservice für Verbundwerkstoffe
- AFRL-Forschung bringt 3D-druckbare CF/Epoxid-Verbundwerkstoffe voran
- Hexcel arbeitet mit Lavoisier Composites, Arkema zusammen
- AMRC und Prodrive arbeiten zusammen, um die Herstellung recycelbarer Verbundkomponenten voranzutreiben
- TenCate feiert den Zusammenschluss des Konsortiums für thermoplastische Verbundwerkstoffe in Brasilien
- Verbundmaterialien:Wo sie auf der NPE2018 zu finden sind