Die Zugangsplatte für Drehflügler aus recyceltem thermoplastischem Verbundmaterial nimmt Fahrt auf
GKN Aerospace (Redditch, Großbritannien) berichtete im Juni 2020, dass mit dem erfolgreichen Flugtest von Bell Flights (Fort Worth, Texas, USA) V-280 Valor militärische Drehflügler, mehrere seiner thermoplastischen Verbundkomponenten (TPC) waren in die Luft geflogen. Zu diesen Komponenten gehörten zwei integral versteifte, formgepresste, thermoplastische Composite-Zugangstüren, die aus recyceltem Abfallmaterial im Rahmen des TPC-Cycle-Programms unter der Leitung des ThermoPlastic Composites Application Center (TPAC, Enschede, Niederlande) und der Saxion University (Enschede, Niederlande) hergestellt wurden ) (lesen Sie CW vorherige Berichterstattung über das vierjährige TPC-Zyklus-Programm).
Die neue Tür aus recycelten Paneelen wurde entwickelt, um ein von Hand hergestelltes Kohlefaser-/Epoxid-Teil zu ersetzen, mit dem Ziel, das Teilegewicht sowie die Herstellungskosten und die Zykluszeit zu reduzieren. Das neue Bauteil wurde von GKN Aerospace entwickelt und getestet und vom TPAC in Zusammenarbeit mit dem ThermoPlastic Composites Research Center (TPRC, Enschede, Niederlande) hergestellt. Die Zugangsplattentüren bestehen aus kohlenstofffaserverstärktem Polyphenylensulfid (PPS) von Toray Advanced Composites (Nijverdal, Niederlande), das aus konsolidiertem Abfall gewonnen wird, der bei der Produktion der TPC-V-Leitwerkskomponenten des Drehflüglers anfällt, die ebenfalls von . entwickelt und hergestellt werden GKN Aerospace.
Der proprietäre Wiederaufbereitungsprozess von TPAC umfasst drei Hauptschritte:Zerkleinern des Abfalls in zentimeterlange Flocken, gleichzeitiges Erhitzen und scherarmes Mischen und Formpressen des Teils in einer isothermen Form.
Das Demonstratorbauteil bietet nach Angaben der Projektpartner eine Gewichtseinsparung von 9 % gegenüber dem Originalteil, vor allem aufgrund der Verarbeitbarkeit des thermoplastischen Materials, das die Integration von Stringern zur geometrischen Versteifung ermöglicht. Die Ausrichtung der Stringer wurde gewählt, um die Belastungen gleichmäßiger über das Produkt zu verteilen, was zu Materialeinsparungen und Gewichtseinsparungen führt. Eine Materialoptimierung wurde auch durch die Verwendung von recycelten Materialien erreicht, wodurch der Gesamtabfall reduziert wurde.
Durch den Einsatz von wiedergewonnenen Materialien wurden erhebliche Produktionskosteneinsparungen erzielt, wodurch die Kosten für neue Materialien eliminiert wurden. Darüber hinaus erforderte das ursprüngliche Verfahren das Auflegen von Hand und die Verwendung eines Autoklaven; Der Formpressprozess außerhalb des Autoklaven (OOA) umfasst eine isotherme Form, eine schnelle Entformung und eine endkonturnahe Fertigung, um die Kosteneffizienz und die gesamte Fertigungszykluszeit zu maximieren.
„Das aktuelle Projekt unterstreicht die Rolle der angewandten Forschung, die die gesamte Wertschöpfungskette umfasst, um Innovationen von der ersten Idee bis zu einem industriell tragfähigen und getesteten Produkt in Rekordzeit voranzutreiben“, sagt Ferrie van Hattum, wissenschaftlicher Direktor von TPAC.
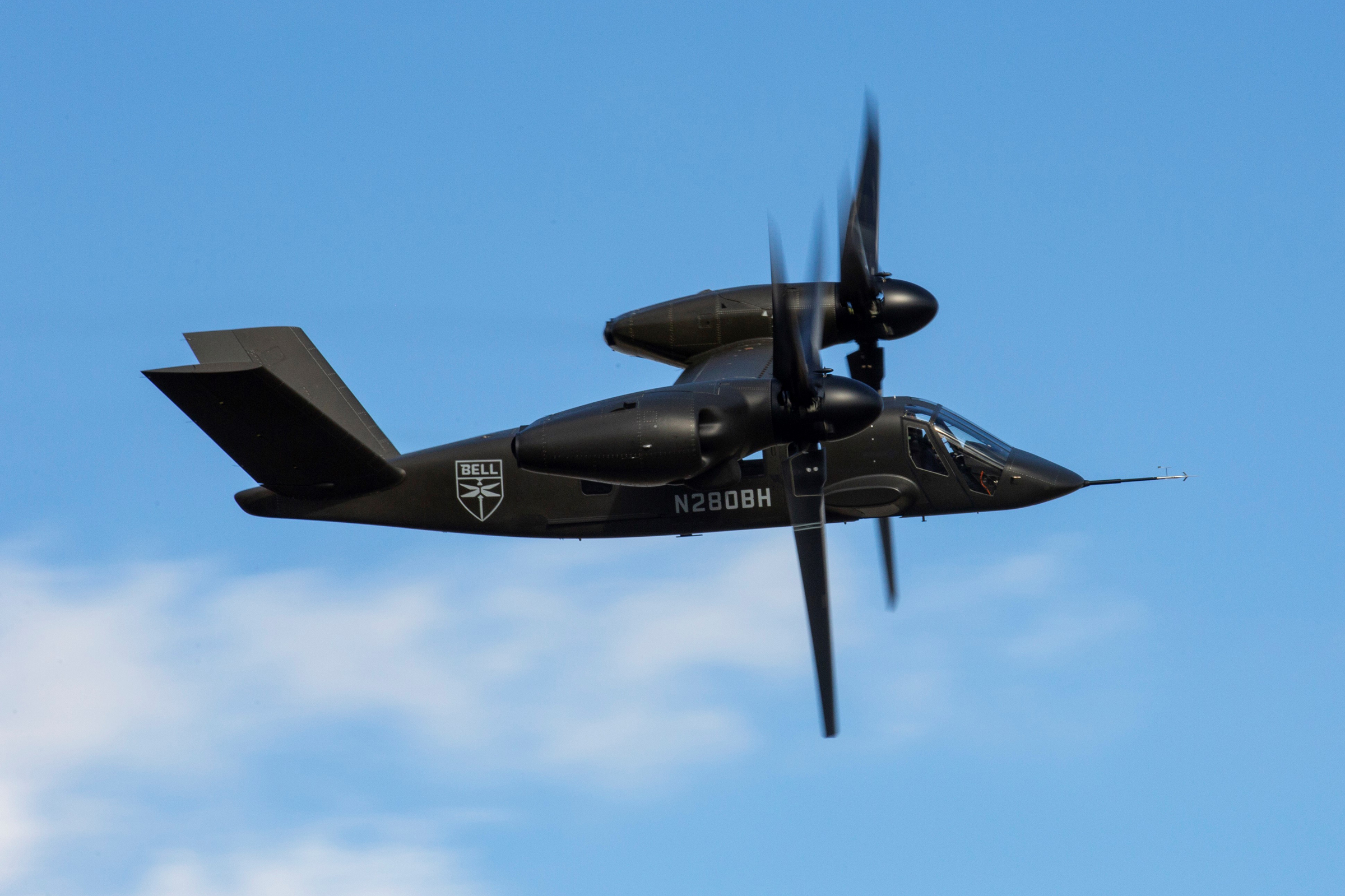
Neben der Erreichung der Gewichts- und Kosteneinsparungsziele demonstrieren die Anwendung und das Verfahren auch einen Schritt in Richtung einer nachhaltigeren Fertigung. Vorläufige Ergebnisse einer laufenden Lebenszyklusanalyse (LCA) von Saxion und TPAC zeigen signifikante CO2 Einsparungen bei der Verwendung dieses Materials, dem Herstellungsprozess – hauptsächlich aufgrund des geringeren Gewichts des Teils – der Verwendung von recyceltem Material und der Verwendung einer isothermen Form in einem OOA-Prozess. Nach Angaben der Projektpartner reduzierte die Anwendung von recycelten Fasern die CO2 Output aus der Produktion neuer Materialien und steigerte die Buy-to-Fly-Ratio des Teils deutlich. Die Schritte des Zerkleinerns, Mischens und Formpressens des Prozesses sollen auch den Energieverbrauch senken, indem der Autoklav aus dem vorherigen Herstellungsprozess von duroplastischen Verbundwerkstoffen eliminiert wird. Thermoplastische Verbundwerkstoffe produzieren während der Verarbeitung auch vernachlässigbare Mengen an schädlichen flüchtigen organischen Verbindungen (VOCs) im Vergleich zu Verbundwerkstoffen auf Duroplastbasis.
Laut TPAC sieht der für diese Anwendung verwendete Herstellungsprozess wie eine vielversprechende Lösung für andere nicht-strukturelle Luft- und Raumfahrtprodukte aus, und seine kurze Zykluszeit könnte ihn für Endmärkte, die einen höheren Volumendurchsatz erfordern, rentabel machen. Es wird daran gearbeitet, den Produktionsprozess für die Serienproduktion sowie detaillierte Kosten- und Umweltauswirkungen sowie Auswirkungen auf Qualitätskontrolle und Inspektion zu bewerten. Es wird auch eine Machbarkeitsstudie durchgeführt, um zu sehen, ob der angewandte Ansatz und die Recyclingroute auf andere Luft- und Raumfahrtanwendungen wie nicht tragende Verkleidungen, Abdeckungen und Systemhalterungen angewendet werden können.
Weitere Projektpartner von TPC-Cycle sind Nido Recyclingtechnologie (Nijverdal, Niederlande); Cato Composites (Rheden, Niederlande); Dutch Thermoplastic Components (Almere, Niederlande) und das ThermoPlastic Composites Research Center (TPRC); Regieorgaan SIA, Teil der Niederländischen Organisation für wissenschaftliche Forschung (NWO, Den Haag, Niederlande).
Harz
- Recycling:Endlosfaserverstärkte thermoplastische Verbundwerkstoffe mit recyceltem Polycarbonat
- Solvay erweitert die Kapazität von thermoplastischen Verbundwerkstoffen
- Thermoplastisches Rad nimmt die raue Straße
- EconCore Produktionstechnologie für thermoplastische Wabenplatten
- INEOS Styrolution baut Produktionsstätte für thermoplastischen Verbundwerkstoff StyLight
- Xenia führt thermoplastische CF/PP-Composite-Compounds ein
- Thermoplastische Verbundrohre auf dem Vormarsch in der Tiefsee
- NIARs NCAMP-qualifizierender TenCate thermoplastischer Verbundwerkstoff
- TenCate feiert den Zusammenschluss des Konsortiums für thermoplastische Verbundwerkstoffe in Brasilien
- SABIC bringt Verbundplatten für Bau und Konstruktion auf den Markt