Composites-intensives Meisterwerk:2020 Corvette, Teil 1
Lesen Sie für Teil 2 „Composites-intensive Meisterarbeit:2020 Corvette, Teil 2“.
Die mit Spannung erwartete Chevrolet Corvette der achten Generation (C8) von General Motors Co. (GM, Detroit, Michigan, USA), die seit ihrer offiziellen Enthüllung am 18. Juli 2019 Auszeichnungen erhalten hat, hat Anfang dieses Jahres die kommerzielle Produktion aufgenommen. Die neue Corvette Stingray Cabrios und Coupés zeichnen sich nicht nur durch ihre Schönheit aus und die Tatsache, dass GM ein leistungsstarkes Mittelmotor-Raketenschiff mit Straßenzulassung ab einem Preis von weniger als 60.000 USD produziert hat – ein Drittel des Preises eines Mittelmotors mit vergleichbarer Leistung Autos – aber sie bieten auch eine beeindruckende Auswahl an neuen und wirklich innovativen Verbundwerkstoffen, die wir hier und nächsten Monat in Teil 2 beschreiben werden.
Neue Engine-Konfiguration ändert alles
GM Engineering ging in das vorläufige Design mit dem Wissen, dass sie an einem Mittelmotorfahrzeug arbeiten würden – der ersten in Serie produzierten Corvette in acht Generationen, um diese Konfiguration zu tragen. „Wir haben die Frontmotor-Architektur im Hinblick auf die Leistung so weit wie möglich weiterentwickelt, daher war der Wechsel zu einem Mittelmotor-Design der nächste logische Schritt, um ein bereits großartiges Auto zu verbessern und der Segmentführer zu sein“, erklärt Tadge Juechter, Executive Chief Engineer von GM -Globale Korvette . Ausgestattet mit dem Z51-Leistungspaket ist die 2020 Corvette Stingray kann in 2,9 Sekunden von 0-60 mph (0-97 kmh) beschleunigen und eine Höchstgeschwindigkeit von 194 mph (312 kmh) erreichen. Das Verschieben des Motors in Richtung Fahrzeugheck beeinflusste viele Dinge, darunter den Schwerpunkt des Fahrzeugs, die relative Position der Insassen, die Position des Getriebes und das Design der Unterbodenverkleidungen und des Kofferraums. Das Mittelmotordesign führte auch in neuen Bereichen des Autos zu höheren Betriebstemperaturen und höheren Geräuschen.
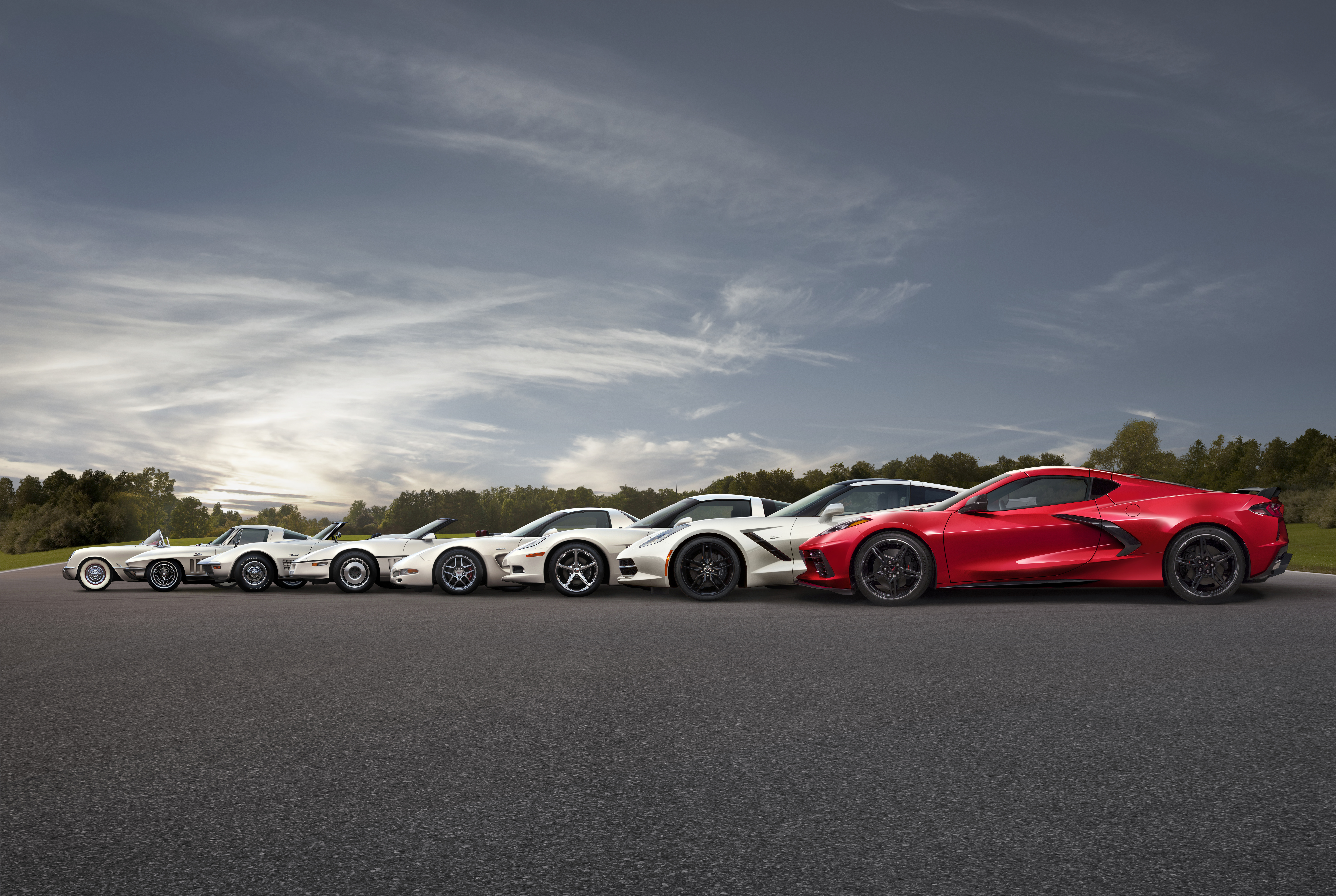
„Wegen des Mittelmotors mussten wir die Dinge anders machen“, erklärt Ed Moss, Corvette Gruppenleiter Karosseriebau. „Wir hatten von Anfang an so viele Diskussionen über die Auslegung der Karosseriestruktur. Irgendwann lag alles auf dem Tisch, als wir den besten Weg besprachen, jedes System zu entwerfen und zu bauen. Zum Beispiel haben wir bei Radhäusern Metallic versus Composite diskutiert. Hätten wir die zusammengesetzten Radhäuser des C7 beibehalten, müssten wir die Scharniersäule [A-Säule] kleben, die bei einem Mittelmotorfahrzeug direkt neben dem Vorderrad liegt, wodurch nur sehr wenig Platz übrig bleibt. Wir sind dort mit Metall gefahren. Wir haben sogar kurz über Metall- und Verbundkörperbleche gesprochen. Es wäre jedoch wirtschaftlich nicht machbar gewesen, die Styling-Linien des C8 in Metallic-Farben zu gestalten.“
„Eine echte Herausforderung, vor der wir standen, war der Umgang mit Luftansaugung“, erinnert sich Chris Basela, Corvette Der leitende Ingenieur der Karosseriestruktur erklärt die Notwendigkeit einer anderen Methode, um Kühlluft in und durch den 495 PS starken 6,2-Liter-V8-Saugmotor zu leiten, der ein Drehmoment von 470 Fuß-Pfund (637 Newtonmeter) erzeugt. „Wir haben alle möglichen Designs ausprobiert, die die Luft dazu zwangen, wirklich quälende Wege zu nehmen und Wirbel und Strömungen zu erzeugen, die wir nicht wollten. Es bedurfte vieler iterativer Arbeit mit dem Powertrain-Team, um den besten Weg für den Luftstrom zu entwickeln, da das Auto ohne Einschränkung frei atmen muss. Wir brauchten auch Zugang zur Airbox und mussten um den hinteren Kofferraum herum arbeiten. Ein weiteres Thema waren Hitze und Motorgeräusche im Fahrgastraum, denn die Insassen sitzen nicht mehr hinter dem Motor, sondern direkt davor. Und wir waren uns der Kabinenluftqualität besonders bewusst, da sich die Gesetze in Europa und anderswo seit der C7 geändert haben, also haben wir wirklich hart daran gearbeitet, VOCs [flüchtige organische Verbindungen] zu reduzieren.“
„Sogar herauszufinden, wie man zusammenbaut das Auto war eine Herausforderung“, fügt Moss hinzu. „Bei einem Frontmotor-Design haben Sie eine lange Motorhaube und einen großen Motorraum, der dem Fahrer viel Platz bietet, um das Auto vom Innenraum aus aufzubauen, selbst wenn der vordere Stoßfängerträger bereits angeschweißt ist. Auf der Mittelmotor Corvette , mit seinem sehr kurzen Frontclip halten wir die Front des Autos offen, wenn das Fahrzeug ausgebaut wird, und schrauben dann die vordere Stoßstange fest.“
„Es war ein ziemlicher Balanceakt, die richtigen Formen zu bekommen und gleichzeitig sicherzustellen, dass unsere Lieferanten die Teile und unser Team in Bowling Green [GMs in Kentucky ansässige Corvette herstellen konnten Montagewerk] könnte sie montieren“, fährt Basela fort. „Am Ende gab es nur einen Übertragsverbund von der Karosserie des C7 auf den C8.“ Dies war eine zähe Sheet Moulding Compound (SMC) der Klasse A, 1,2, spezifisches Gewicht (SG), entwickelt für die 2016 Corvette und in einer Vielzahl von Außenverschlüssen des neuen Fahrzeugs verwendet.
Fahrzeugarchitektur
Seit vier Generationen (C5-C8), Korvetten haben eine dreischichtige, aus mehreren Materialien bestehende Karosseriestruktur:den Rahmen , normalerweise eine Mischung aus Aluminium oder Stahl – diesmal mit einem kohlenstofffaserverstärkten Verbund (CFK)-Teil; die Körperstruktur , das größtenteils aus Verbundwerkstoff besteht, um von der Design- und Fertigungsflexibilität zu profitieren; plus angeschraubte Abschlüsse (Karosserieteile), die seit Covette aus Verbundwerkstoffen bestehen Debüt im Juni 1953. Diese geschichtete Hybridstruktur ermöglicht nicht nur bezahlbaren Leichtbau in hohen Stückzahlen – insbesondere für Autos dieser Leistungsklasse –, sondern ermöglicht auch die Herstellung mehrerer Fahrzeugvarianten mit geringem Werkzeugaufwand. Tatsächlich ist es GM für den aktuellen C8 gelungen, mit nur 20 Werkzeugen alle Karosserieteile der Klasse A (verklebte Innen- und Außenteile) sowohl beim Basismodell Coupé als auch beim Cabrio zu produzieren.
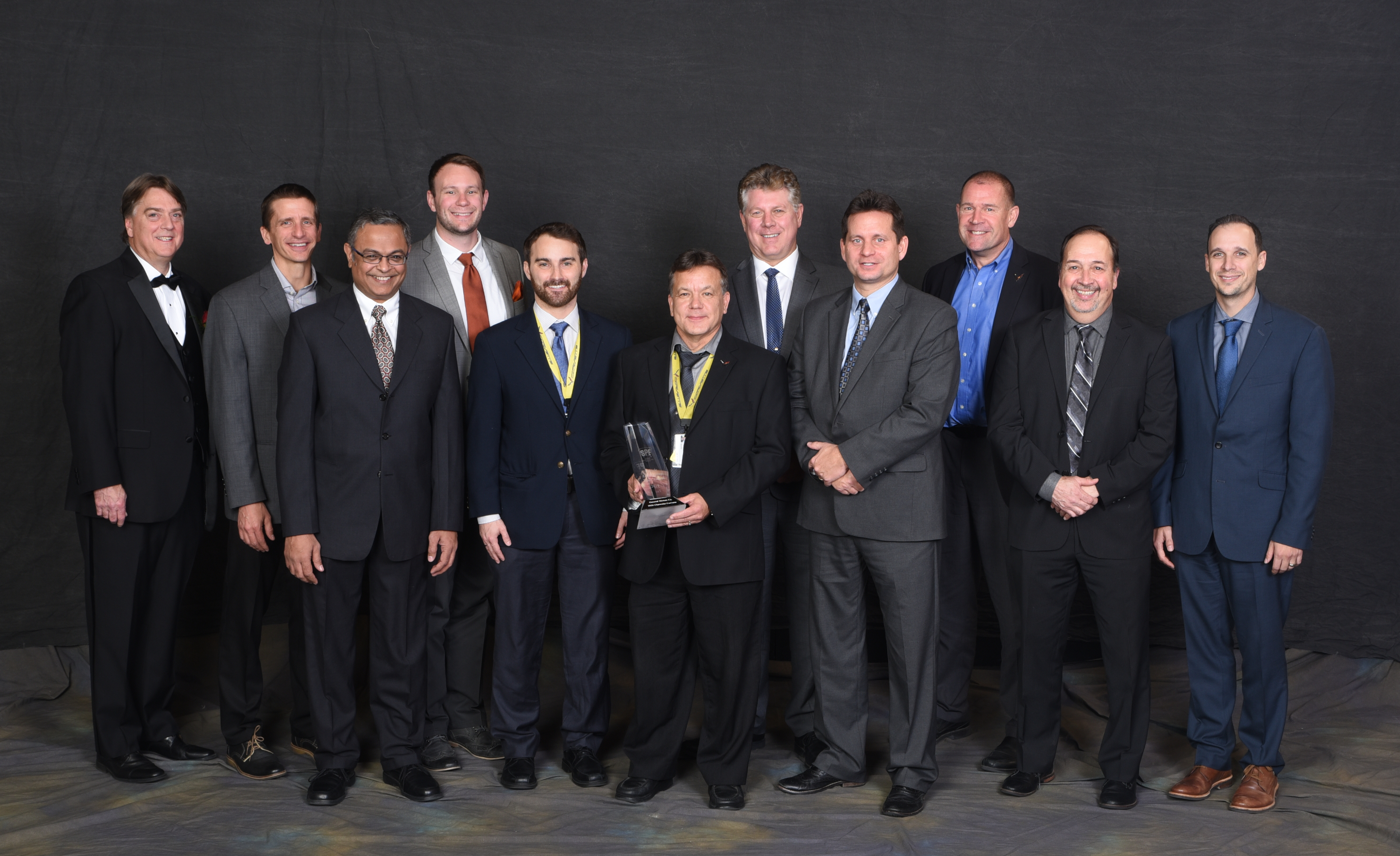
Außerdem Korvetten werden seit jeher in Offendach-Architektur konstruiert, egal ob es sich tatsächlich um Cabrios oder Coupés mit feststehenden oder abnehmbaren Dachteilen handelt. Da Fahrzeuge mit offenem Dach im Allgemeinen weniger steif sind als solche mit festem Dach, ein wichtiger Schwerpunkt für jede Corvette’ s Engineering besteht immer darin, ein möglichst steifes Fundament zu schaffen, um Federung und Lenkung zu verbessern. Historisch gesehen, Tunnel (Gehäuse Getriebe und Antriebswellen bei Frontmotorfahrzeugen) haben die Corvette dominiert Karosseriestrukturen und waren Schlüsselfaktoren für die Erzielung einer hohen Torsionssteifigkeit. Bei der neuen Corvette , erreicht GM eine noch höhere Steifigkeit. Ohne Dach ist die C8-Karosserie 53,78 % steifer als ein Benchmark-Konkurrent mit Hochleistungs-Mittelmotor, 29,27 % steifer als ein zweiter Wettbewerber mit Hochleistungs-Mittelmotor und 13,79 % steifer als der C7. Zwei Verbundteile leisteten einen wichtigen Beitrag zur Fahrzeugsteifigkeit – eines direkt an der Rahmenstruktur (hinterer Stoßfängerträger) und eines am Unterboden (unterer Tunnelabschluss).
Rahmenstruktur
Der Rahmen des C8 besteht größtenteils aus einer Aluminiumlegierung mit einem CFK-Teil, das entwickelt wurde, um die strengen Dollar-pro-Kilogramm-Ziele von GM zu erfüllen. Im Gegensatz dazu bestand der C7-Rahmen komplett aus Aluminium und der C6 bestand hauptsächlich aus Stahl.
Das einzige direkt am Rahmen montierte Verbundteil, das mit der Rohkarosserie (BIW) durch das elektrophoretische Rostbeschichtungsverfahren (das GM ELPO nennt) fährt, ist ein einzigartiger CFK-Heckstoßfängerträger. Dieser Teil trägt zur Versteifung des Rahmens und zur Aufprallleistung bei. Seine geschwungene Form – möglich dank eines neuartigen Verfahrens namens Radius-Pultrusion, das von der Thomas GmbH + Co. Technik + Innovation KG (TTI, Bremervörde, Deutschland) entwickelt wurde – ermöglicht es, sich an die Stilelemente des Hecks anzupassen und in begrenztem Raum zu passen, während die Dimensionsintegrität beibehalten wird zur Motorraumwärme. Als erstes gebogenes pultrudiertes Teil der Automobilindustrie (siehe unser ausführliches Feature zu diesem Teil in der CW-Ausgabe vom Mai 2020) wurde der hohle Zweikammerträger von Shape Corp. (Grand Haven, Michigan, USA) auf entwickelten und gebaut von TTI. Der Träger wiegt nur 1,3 Kilogramm und verfügt über eine verklebte/verschraubte Abschleppöse mit einer Auszugskraft von 25 Kilonewton.
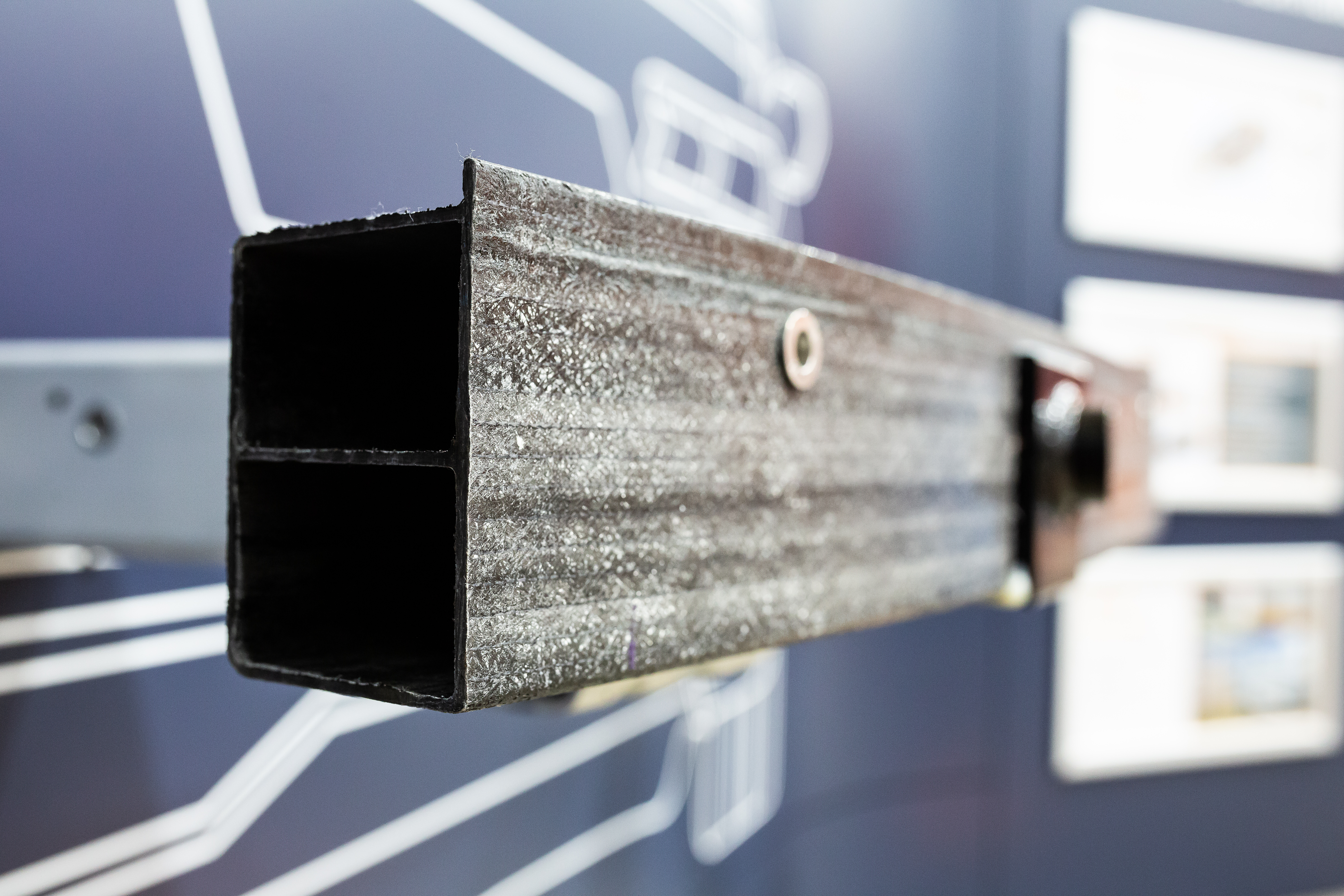
Körperstruktur:Teil A
Nahezu alle Karosseriekomponenten des C8 bestehen aus Verbundwerkstoffen und werden nach dem ELPO-Verfahren mit dem Rahmen verklebt und/oder verschraubt. Zu den bemerkenswerten Verbundteilen auf dieser Ebene gehören strukturelle Unterbodenabschlüsse und der Boden – auf die wir in dieser Ausgabe eingehen werden – sowie vordere und hintere Kofferräume, Ansaugkanäle und die hintere Einfassung und Trennwand – die wir zusammen mit Karosserieteilen und Verkleidungen behandeln , nächsten Monat.
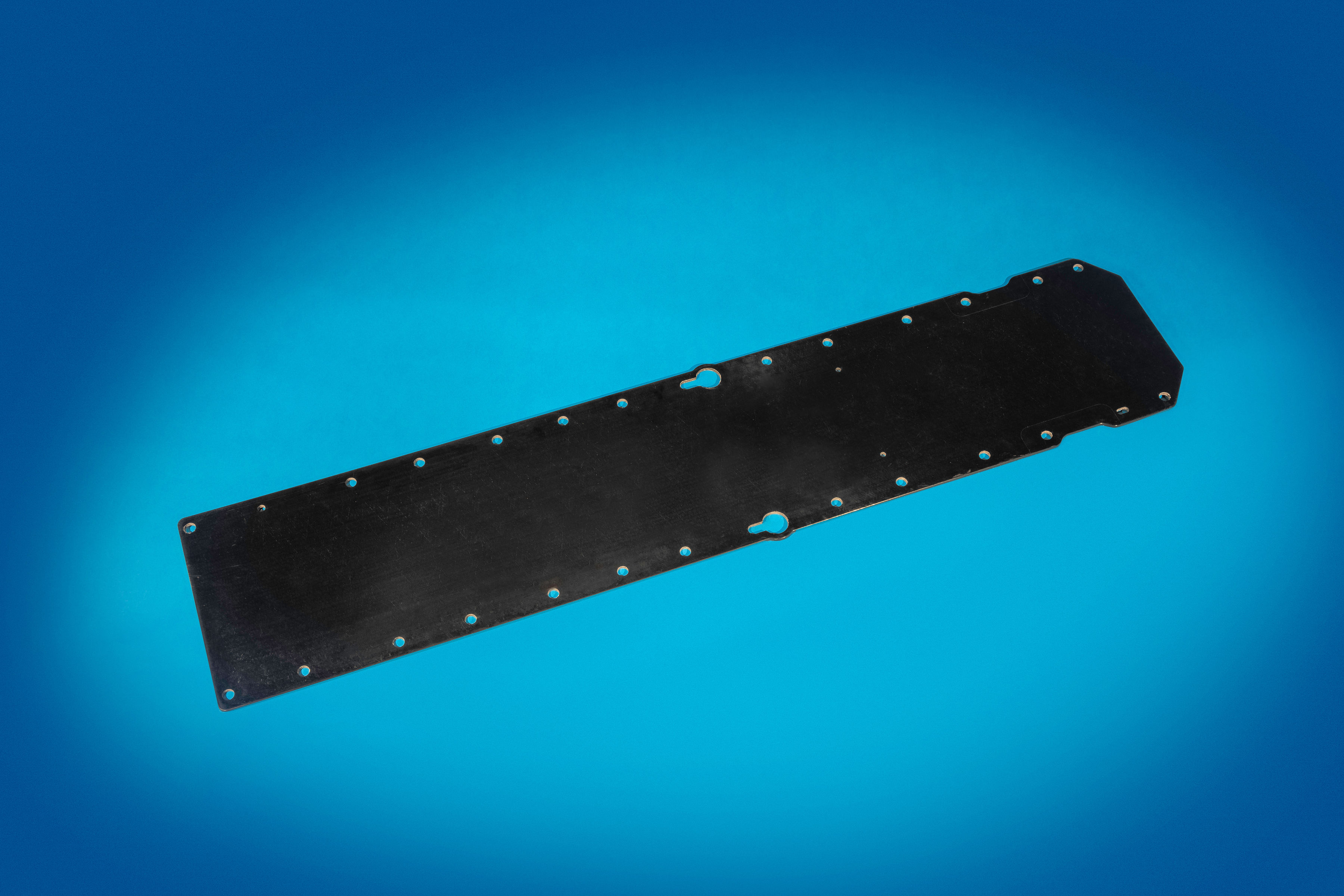
Der abnehmbare strukturelle Abschluss des unteren Tunnels des C8, der als Zugangstür dient, trägt mehr als 10 % der Torsionssteifigkeit des Fahrzeugs bei und fungiert bei einem Crash als primärer Lastpfad. Diese Hybrid-Verbundplatte besteht aus drei Lagen Glasfaser-Preform. Diese bestehen aus Endlosfasern/gewebten und geschnittenen/zufälligen Fasern mit einem Faservolumenanteil von 38 % (FVF), wobei Schleier an den oberen und unteren Deckschichten jedes Stapels angebracht sind, um die Oberflächengüte zu verbessern. Glasvorformlinge werden mit zwei Schichten von Vorformlingen verschachtelt, die unter Verwendung von Toray (Tokyo, Japan) T700 12K-Standardmodul-Kohlenstofffasern in Form eines biaxialen NCF-Gewebes mit 21% FVF und einer Vinylester (VE)-Matrix hergestellt wurden. Der Abschluss wird von Moulded Fiber Glass Co. (MFG, Ashtabula, Ohio, USA) unter Verwendung seines proprietären PRiME-Prozesses (Prepositioned Reinforcement Warranty Manufacturing Excellence) hergestellt, einer Art Flüssigkompressionsformen (LCM).
Abgesehen von einem einzigen Aluminiumabschluss in der Nähe der Hinterräder, der Teil der Motorhalterung ist, bestehen die restlichen Unterbodenverkleidungen entweder aus formgepresstem SMC oder spritzgegossenem Thermoplast. Neben anderen Vorteilen reduzieren diese Paneele Unterbodenturbulenzen und -widerstand, verbessern die Kraftstoffeffizienz und halten Feuchtigkeit, Staub und Steine vom Motor und Antriebsstrang des Fahrzeugs fern. Darüber hinaus bilden sie die dimensionale Grundlage für mehrere äußere und innere Schnittstellen.
Die geringe Dichte, aber strukturell SMC-Platten verfügen über neue, von MFG entwickelte Rezepturen (in diesem Fall 40% FVF geschnittenes Fiberglas/ungesättigtes Polyester (UP)-Harz). Das Material wird als „schwimmendes“ SMC bezeichnet, da die Dichte jeder Platte weniger als 1,0 beträgt (durchschnittlicher SG =0,97) und somit in Wasser schwimmen kann. MFG produzierte alle strukturellen SMC- und LCM-Teile am Auto.
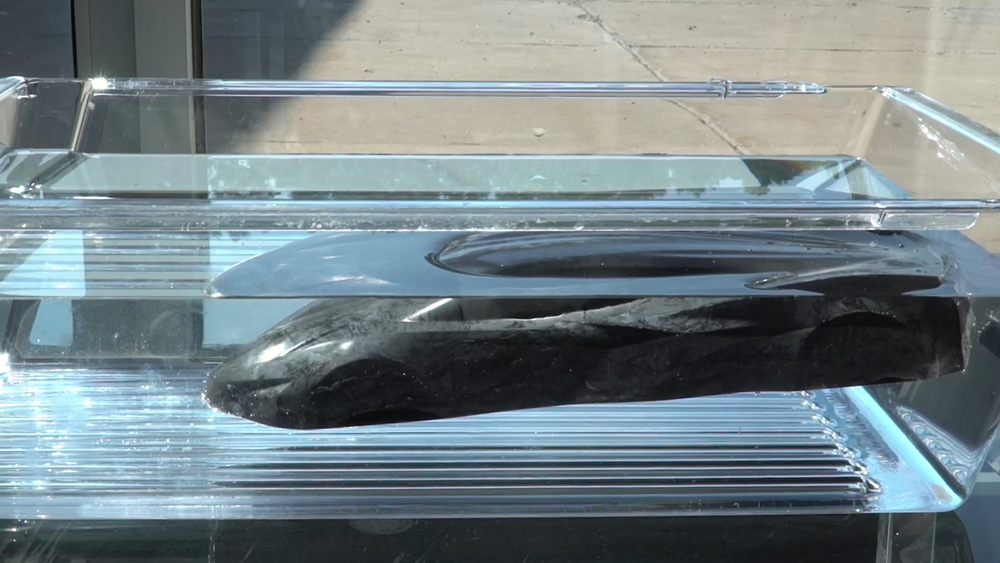
Das Fahrzeug verfügt außerdem über einen Hybridboden, der für Torsionsbiege- und Seitenpfostenaufprallschutz optimiert ist (in Eingriff mit den Schwellern und dem Tunnel, mit dem es verbunden ist). Die Bodenplatten bestehen aus gestanztem Aluminium zur Kabine, das mit Platten aus straßenseitigem 1,5-SG-Verbundmaterial (60 Gew.-% kontinuierliche und gewebte Glasfaser/VE) verbunden ist, das im PRiME-Verfahren hergestellt wird. Vor dem Heißkleben beider Schichten mit Pliogrip 9100 Polyurethan-Strukturklebstoff von Ashland Global Holdings Inc. (Wilmington, Del., USA) reinigt und bereitet MFG die Materialien vor.
Alle direkt mit dem C8-Rahmen verbundenen Verbundteile werden zunächst einer Laserablation unterzogen, einem Verfahren, das von GM, MFG und Adapt Laser Systems LLC (Kansas City, Missouri, USA) für die Corvette 2016 . entwickelt wurde und adaptiert von einem Verfahren der Verbundstoffindustrie zum Reinigen von Formen. Die Laserablation ersetzt das Schleifen von Hand und reduziert Arbeit, Zeit und Kosten, beseitigt Staub und verbessert die Wiederholbarkeit. Laserweg, Anstellwinkel und Energieniveau sind für jedes Material und jede Geometrie jedes Teils anpassbar. Um die Fertigungsflexibilität zu maximieren, wird der gesamte Unterboden einschließlich des Bodens über Kleben und Schrauben mit dem Rahmen und sich selbst verbunden.
In der August-Ausgabe von CW werden wir weiterhin über Innovationen bei Verbundwerkstoffen auf der neuen Corvette berichten , die mit zusätzlichen Komponenten auf Ebene der Karosseriestrukturen fortgesetzt und mit Außenabschlüssen (Bodypanels) sowie zusätzlichen Verkleidungen und Upgrades abgeschlossen wird. Siehe Teil 2.
Harz
- 10 Vorteile von Cloud Computing im Jahr 2020
- Die Zukunft des 3D-Drucks:12 wichtige Erkenntnisse der AMFG-Digitalkonferenz AM Landscape 2020 (Teil 1)
- Instandhaltungsleitung, Teil 3
- Einführung in Harmonische:Teil 1
- Nachhaltigkeit in der Fertigung – Teil 3
- 2020 Trends und Herausforderungen, die von Covid-19 beeinflusst werden:Teil I
- Drehen ist optional
- Was ist eine Teilenummer?
- Kleinteilbearbeitung
- Zylindrizität in GD&T