Composites im Wettlauf um den Weltraum
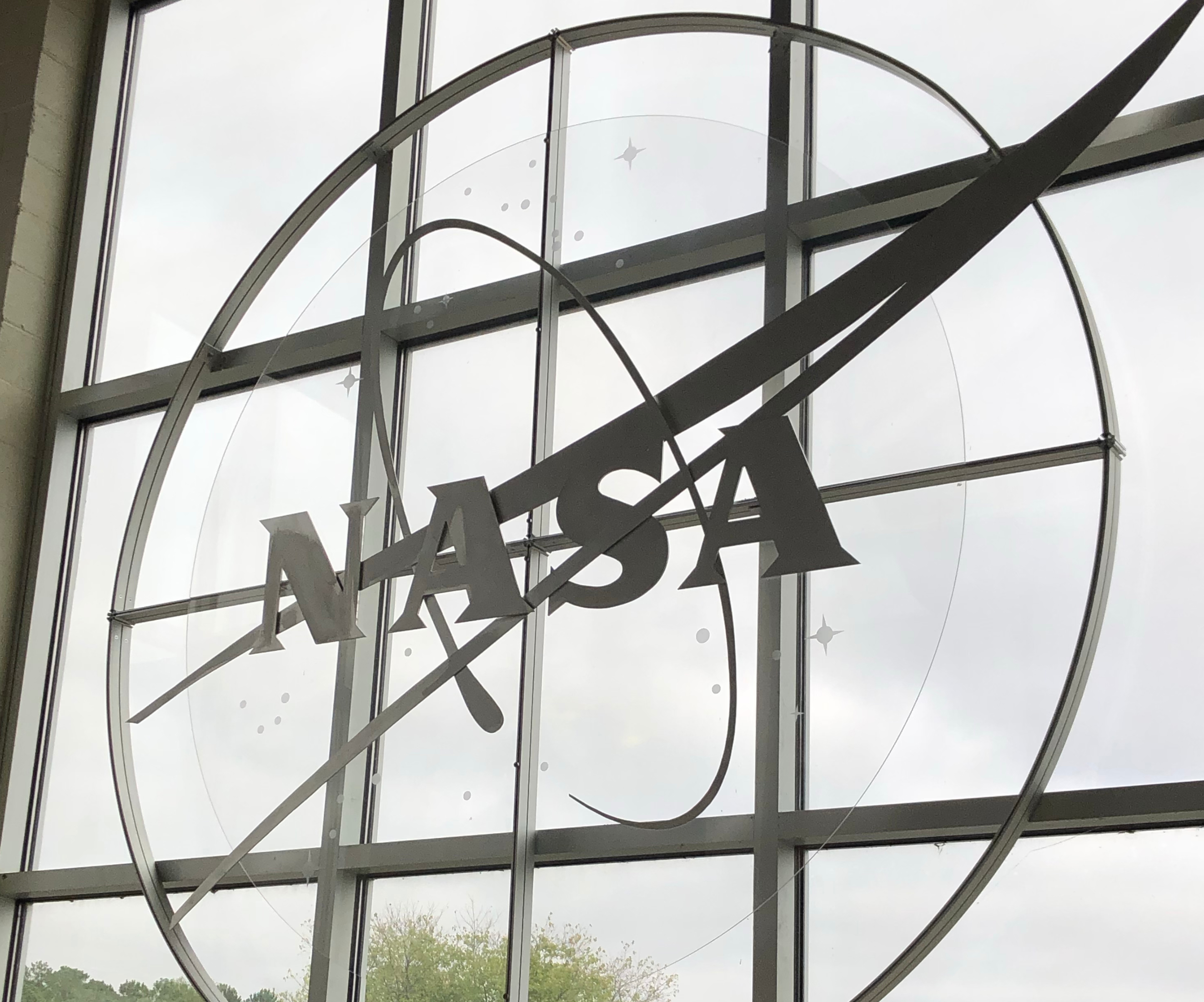
Am 20. Juli 2019 feierte der erste Apollo das 50-jährige Jubiläum Mondlandung. Obwohl zu der Zeit der Apollo Kapsel gebaut wurde, die Verbundwerkstoffindustrie noch in den Kinderschuhen steckte und die Materialien noch nicht weit verbreitet waren, der Apollo Kapsel verwendete frühe Verbundtechnologie in Form eines ablativen Hitzeschildes aus Avcoat, einem Epoxy-Novolak-Harz mit Silicafasern in einer Glasfaser-Phenol-Wabenmatrix. Auf die Primärstruktur wurde eine Glasfaserwabe aufgeklebt und das pastöse Material in jede Zelle einzeln eingespritzt. Seit Apollo , fortschrittliche Verbundwerkstoffe haben sich sprunghaft weiterentwickelt und haben eine bedeutende Rolle in Weltraumprogrammen mit dem Einsatz in Trägerraketen, Space Shuttles, Satelliten, Weltraumteleskopen und der Internationalen Raumstation gespielt.
Heute ist die Menschheit bereit für einige aufregende neue Schritte in der Weltraumforschung. Die derzeitige Regierung hat eine Rückkehr der US-Astronauten zum Mond bis 2024 gefordert und ein Budget von mehr als 25 Milliarden US-Dollar für das bemannte Weltraumforschungsprogramm der National Aeronautics and Space Administration (NASA, Washington, D.C., USA) für 2021 angekündigt. NASA-Administrator Jim Bridenstine sagt, das Budget sei "eines der stärksten Budgets in der Geschichte der NASA".
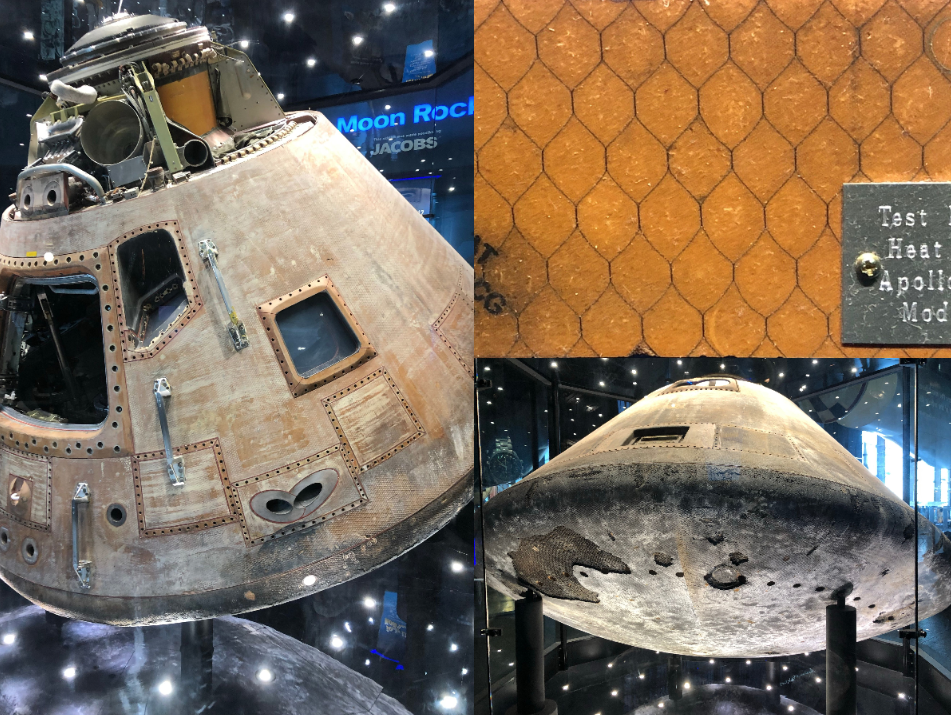
Zusätzlich zu einer weiteren Mondaufnahme hat die NASA aktuelle und bevorstehende Missionen zur Untersuchung unseres Sonnensystems von der Sonne bis zu den eisigen Monden der äußersten Planeten und darüber hinaus. Missionen zur Erforschung der Sonne sind derzeit im Gange:Zum Zeitpunkt dieses Schreibens überwacht die Parker Solar Probe derzeit die Sonnenatmosphäre und ein Solar Orbiter ist erfolgreich gestartet. Es werden auch Anstrengungen unternommen, um die Erforschung von Exoplaneten und fernen Galaxien durch die Mission Transiting Exoplanet Survey Satellite (TESS) und das James Webb-Weltraumteleskop voranzutreiben, von denen letzteres im letzten Jahr Fortschritte in Richtung Startbereitschaft gemacht hat.
Neue Raumfahrzeuge und Programme sind in den letzten Jahren auch aus der verstärkten Zusammenarbeit zwischen nationalen und internationalen Raumfahrtagenturen sowie kommerziellen Unternehmen entstanden. Zum Beispiel SpaceX (Hawthorne, Kalifornien, USA) mit seinem Crew Dragon Raumschiff und Boeing Space and Launch (Arlington, Virginia, USA) mit seinem Starliner Raumschiffe, rasen auf den ersten bemannten US-Raumflug seit der Einstellung des Space-Shuttle-Programms im Juli 2011 zu. Die beiden Unternehmen haben Testflüge mit der NASA in der Hoffnung auf eine bemannte Mission im Jahr 2021 durchgeführt.
Von der verstärkten Unterstützung des Raumfahrtprogramms der NASA bis hin zum explosiven Wachstum des kommerziellen Weltraums scheint die Menschheit wirklich bereit für das nächste große Raumfahrtzeitalter. Verbundwerkstoffe und fortschrittliche Materialien spielen eine immer größere Rolle bei der Herstellung von Trägerraketen, Raumfahrzeugen und Instrumenten, die all diese Erkundungen ermöglichen.
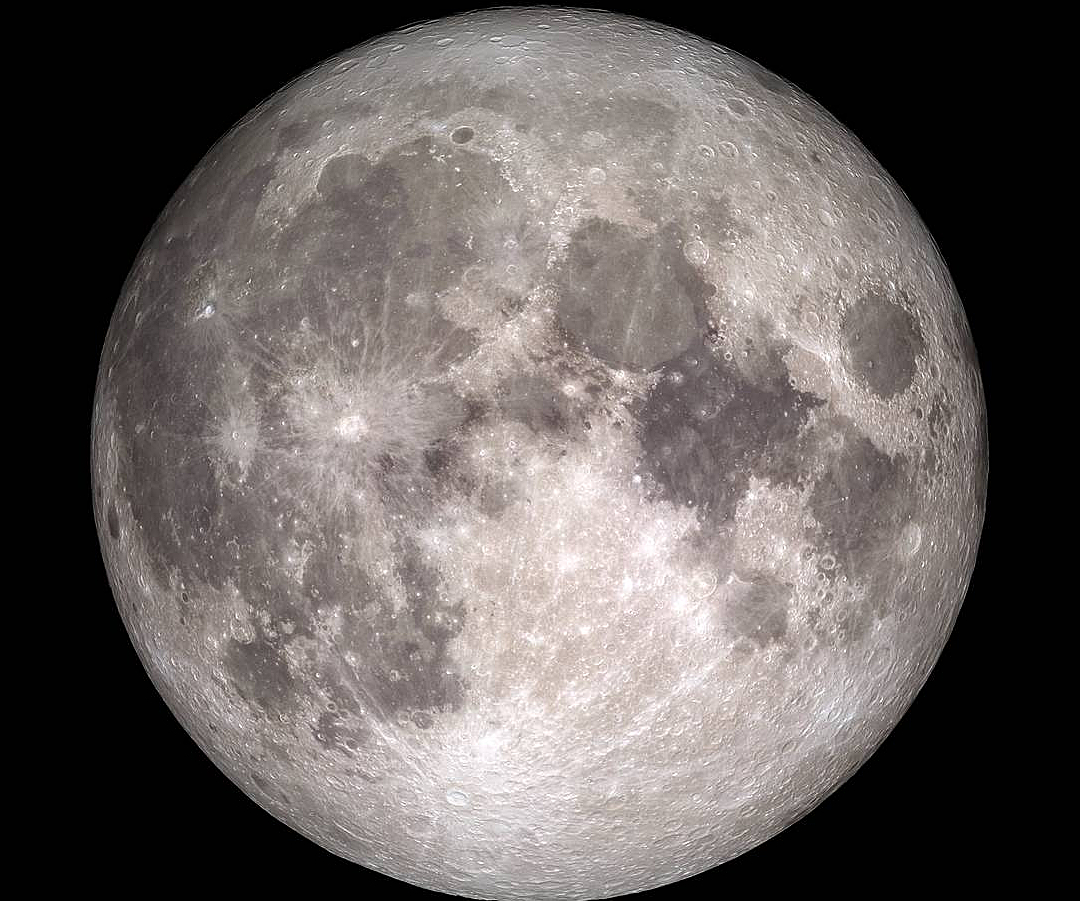
Mond
Das übergreifende Programm zur Rückkehr des Menschen zum Mond ist nach Artemis benannt, der griechischen Göttin des Mondes und der Jagd, der Zwillingsschwester von Apollo – und der Umfang des Programms ist groß. Artemis wird eine Mondbahn-Basis errichten, die es Astronauten nicht nur ermöglicht, den Mond weiter zu erforschen, sondern den Mond auch als Außenposten für eventuelle Missionen zum Mars zu nutzen. Mehrere Projekte bilden die Artemis Programm, darunter ein neues schweres Startsystem, das als Space Launch System (SLS) bekannt ist, das Orion Besatzungsschiff, eine Raumstation im Mondorbit, bekannt als Gateway und ein Mondlander. Fortschrittliche Verbundwerkstoffe berücksichtigen alle diese Komponenten auf die eine oder andere Weise.
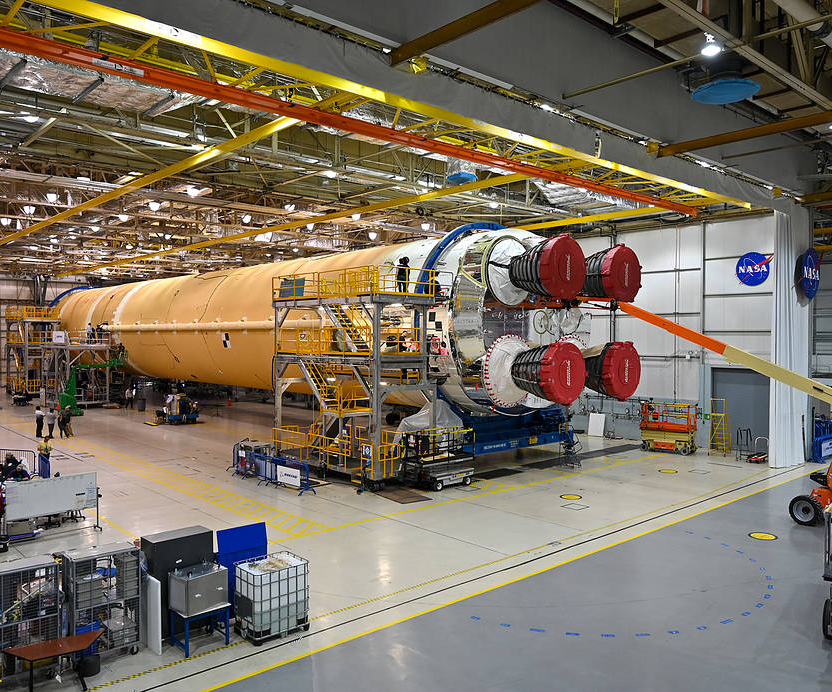
Schwerer Launcher. SLS Rocket Stage wird für den Versand vorbereitet. Quelle | NASA
Das Space Launch System (SLS)
Die neue schwere Trägerrakete der NASA soll die Erforschung jenseits der Erdumlaufbahn ermöglichen. Im Jahr 2015 investierte die NASA in eine Electroimpact (Mukilteo, Washington, USA) Maschine zur automatischen Faserplatzierung (AFP), um großformatige Raketenteile herzustellen, die Sandwichstrukturen von mehr als 8 Metern Durchmesser aus Kohlefaserhäuten mit einem Aluminiumwabenkern umfassen. Der AFP-Kopf fasst bis zu 16 Kohlefaserspulen und ist am Ende eines 21-Fuß-Roboterarms positioniert, der die Fasern in präzisen Mustern auf einer Werkzeugoberfläche platziert, um Strukturen unterschiedlicher Formen und Größen zu bilden.
Ähnliche Sandwichstrukturen werden von RUAG Space (Decatur, Ala, USA) in einem manuellen Layup-Verfahren hergestellt. Das Unternehmen arbeitet mit Dynetics (Huntsville, Ala., USA) an einem Universal Stage Adapter (USA), der die Oberstufe von SLS mit dem Orion verbinden wird Crew-Modul. RUAG Space wird die Hülle des Adapters mit einem Durchmesser von 8,4 Metern herstellen, die aus vier zusammengesetzten Wabenkern-Viertelplatten besteht, die heiß miteinander verbunden werden (Mehr erfahren).
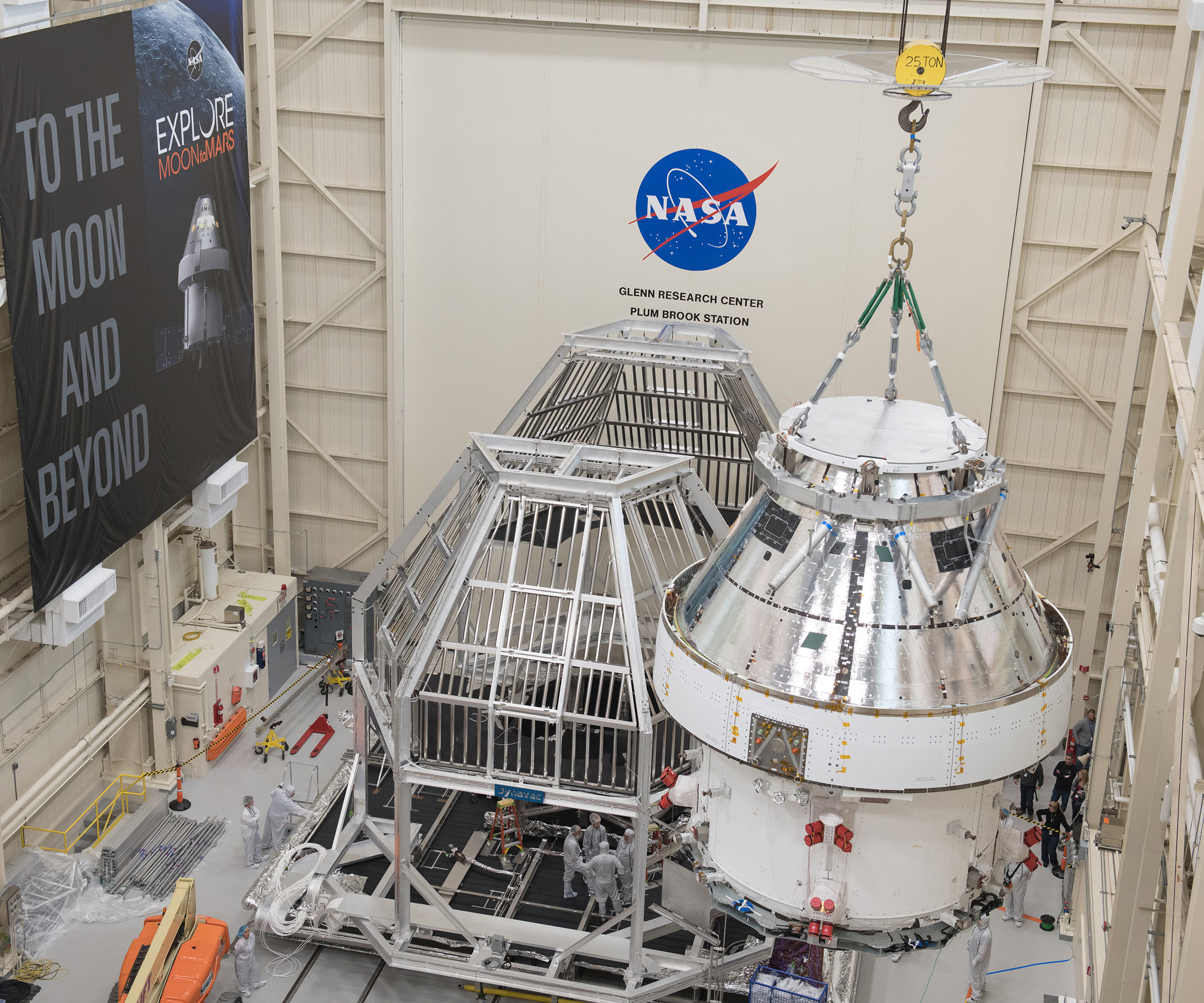
Das Orion-Mehrzweck-Besatzungsfahrzeug
Bestehend aus einem Kommandomodul von Lockheed Martin (Bethesda, Md., USA) und einem Servicemodul der European Space Agency (ESA, Paris, Frankreich) von Airbus Defence and Space (Ottobrunn, Deutschland), Orion ist das Herz der Artemis Programm und wird Astronauten ins All befördern, während der Raumfahrt als Erkundungsfahrzeug dienen und die Besatzung zur Erde zurückbringen.
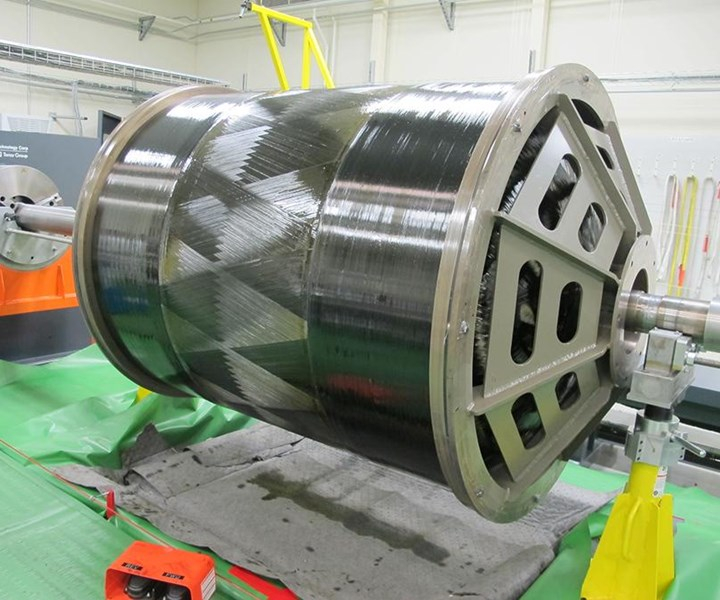
Orion Das Antriebssystem von Aerojet Rocketdyne umfasst zahlreiche Komponenten, die von Aerojet Rocketdyne (Sacramento, Kalifornien, USA) hergestellt werden, darunter acht 110-Pfund-Biotreibstoff-Hilfstriebwerke, die auf der R-4D-Triebwerksfamilie von Aerojet Rocketdyne basieren. Aerojet Rocketdyne liefert auch den Abwurfmotor Launch Abort System (LAS) und mit Verbundstoff umhüllte Druckbehälter für das Raumfahrzeug. Anfang 2020 installierte Aerojet Rocketdyne eine Kohlefaser-Wickelmaschine zur Herstellung seiner festen Raketenmotorgehäuse (Weitere Informationen).
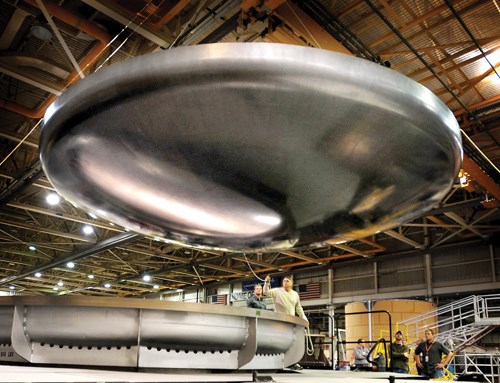
Für den Wiedereintritt Orion verwendet einen Kohlefaser-Hitzeschild mit einem Durchmesser von 5 Metern, hergestellt von Lockheed Martin die als Sandwich-Struktur mit Kohlefaser-Häuten und einem Titan-Wabenkern hergestellt wird. Der Hitzeschild wird dann mit Avcoat-Platten bedeckt – dem gleichen ablativen Material, das für den Apollo . verwendet wird Missionen (Erfahren Sie mehr).
Vier Kompressionspolster aus ablativem Material sind mit Titanschrauben am Hitzeschild an den Stellen befestigt, an denen das Befehlsmodul am Servicemodul befestigt ist. Die Kompressionspolster müssen strukturellen Belastungen während des Starts und Aufstiegs sowie Pyroschocks (von explosiven Bolzen) während der Trennung der beiden Module standhalten. Sie müssen auch die Wiedereintrittsanforderungen an Hochtemperaturbeständigkeit und Ablation erfüllen. Beim Erstflug wurden Kohlefaser/Phenol-Pads verwendet Orion Testfahrzeug, zeigten jedoch nach dem Flug Anzeichen von interlaminaren Rissen und wurden durch eine 3D-gewebte Lösung namens 3D Multifunctional Ablative TPS (3D-MAT) ersetzt, die ein 3D-gewebtes Quarzmaterial von Bally Ribbon Mills (Bally, Pennsylvania, USA) verwendet ) und ein Cyanatester-Harzsystem von Toray Advanced Composites (Weitere Informationen).
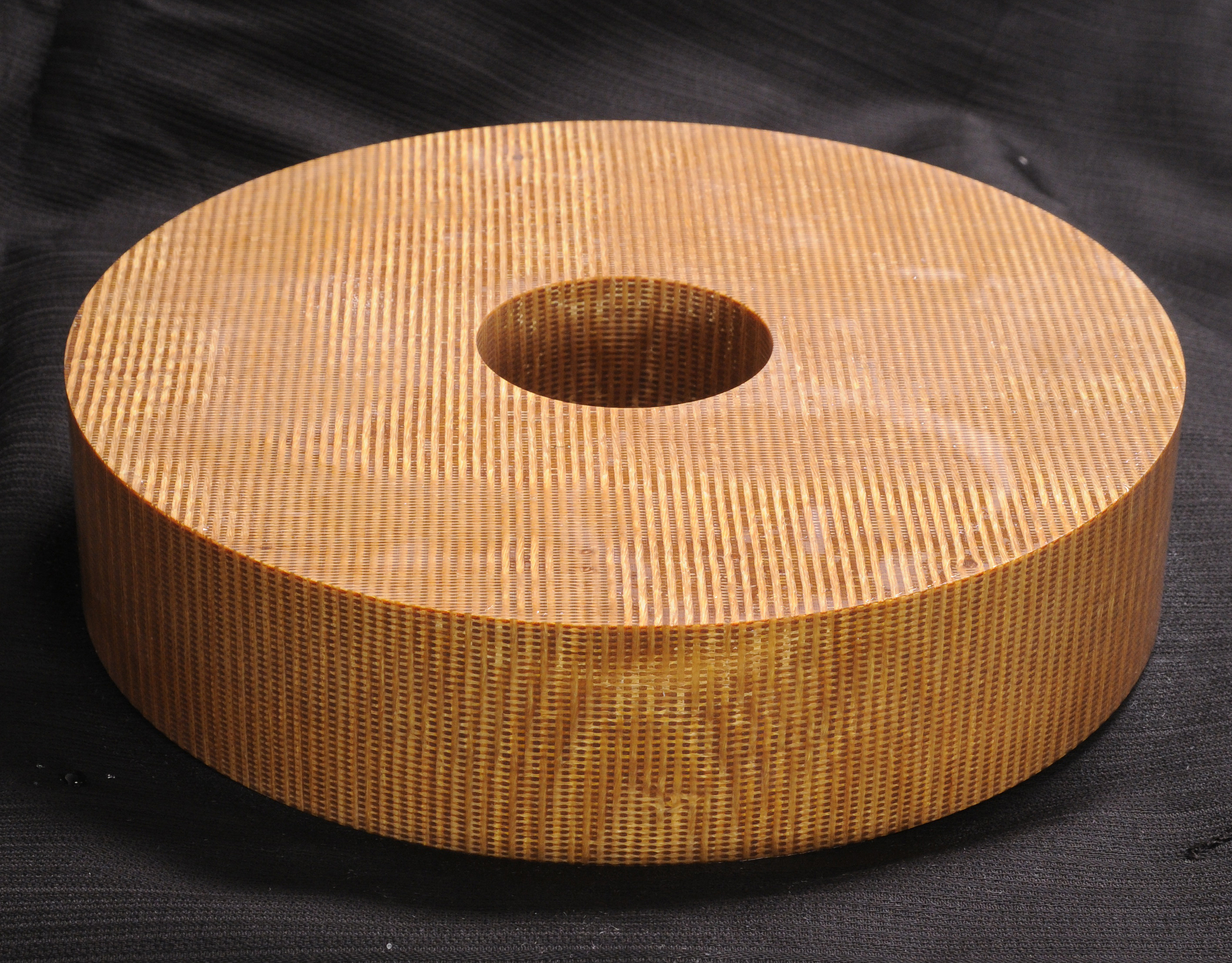
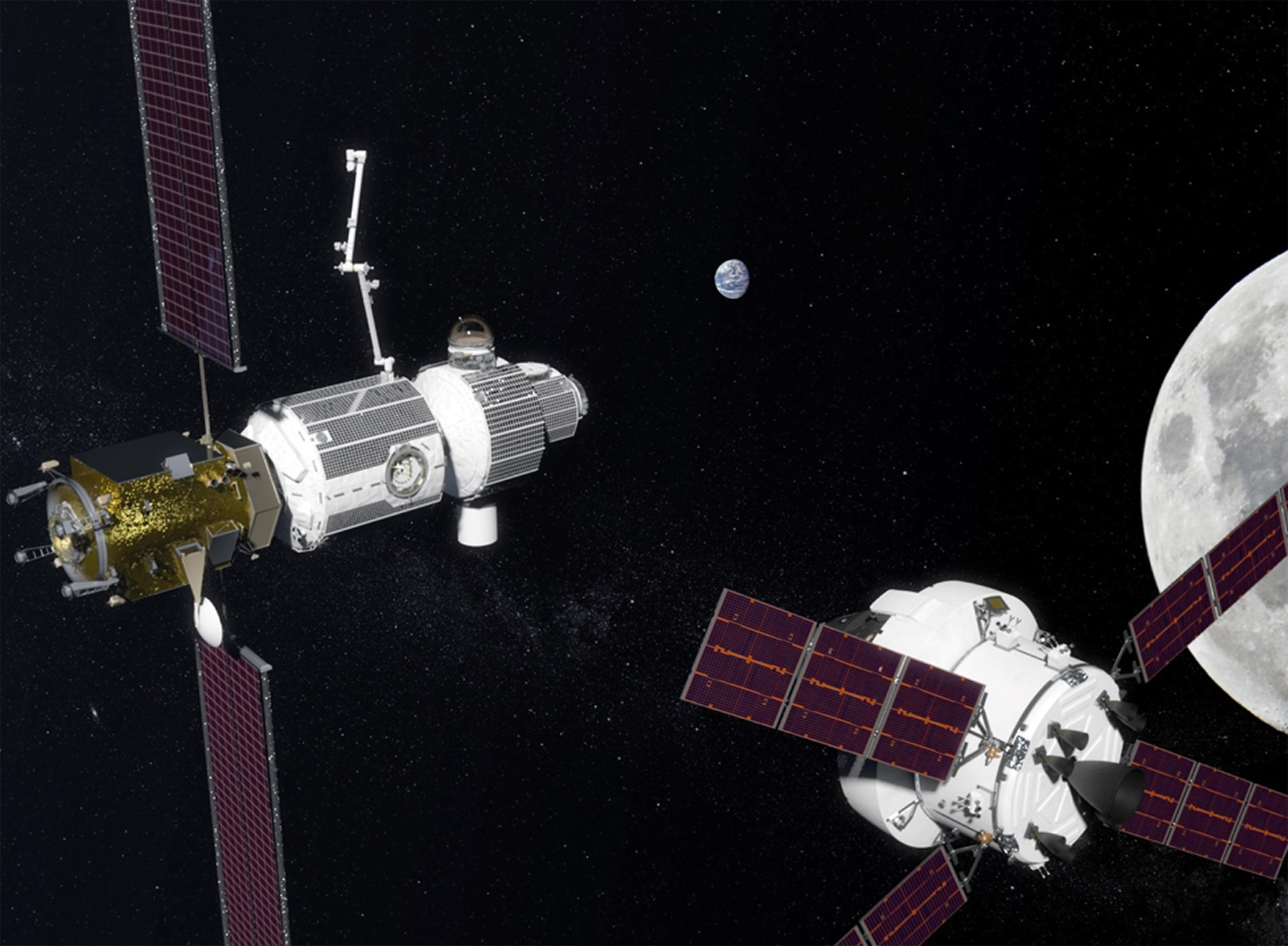
Das Lunar Orbital Platform-Gateway (LOP-G)
Gateway ist eine Raumstation im Mondorbit, die von der NASA zusammen mit internationalen Partnern, darunter russischen, kanadischen, japanischen und europäischen Weltraumbehörden, entwickelt wird. Gateways Die Rolle besteht darin, die Erforschung des Mondes zu unterstützen und als Außenposten für eventuelle Missionen zum Mars zu dienen. Die verschiedenen Module für die Station befinden sich in der Entwicklung und werden wahrscheinlich in irgendeiner Weise Verbundmaterialien verwenden.
Im Gateway-Programm kommt ein Roll-Out Solar Array (ROSA) zum Einsatz, das vom Air Force Research Laboratory (AFRL; Dayton, Ohio, USA) und Deployable Space Systems unter Verwendung von High-Strain-Composites (HSC) entwickelt wurde. HSCs sind dünne, leichte Verbundmaterialien, die so konstruiert sind, dass sie in kleine Pakete passen und sich durch Entfalten entfalten. Das ROSA-System verwendet zwei HSC-Ausleger aus Kohlefaser, um eine große Solarfelddecke auszurollen und zu spannen. (Erfahren Sie mehr über HSCs).
Ein weiterer potenzieller Beitrag zu Gateway ist Canadarm-3. Das von der Canadian Space Agency (Longueuil, Quebec, Kanada) vorgeschlagene Gerät ist ein 8,5 Meter langer Roboterarm aus Kohlefaserverbundwerkstoffen. Frühere Canadarm-Systeme wurden auf dem Space Shuttle und der Internationalen Raumstation (ISS) verwendet.
Mondlander
Zahlreiche Unternehmen arbeiten an Konzepten für Mondlandesysteme für Artemis , die alle Potenzial für Verbundwerkstoffe beinhalten. Blue Origin (Kent, Washington, USA) arbeitet beispielsweise mit Lockheed Martin, Northrop Grumman (Falls Church, Virginia, USA) und Draper (Cambridge, Massachusetts, USA) an einem vorgeschlagenen Mondlandesystem mit drei Fahrzeugen:Blue Origins Blue Moon Mondlander, ein „Transfer Element“-Fahrzeug von Northrop Grumman, das das Landesystem in der Mondumlaufbahn positioniert, und ein „Ascent Element“-Fahrzeug von Lockheed Martin, das Astronauten von der Mondoberfläche in die Mondumlaufbahn zurückbringen wird. Ein Sinkleitsystem und Flugavionik werden von Draper bereitgestellt. Mehrere andere Unternehmen, die an Konzepten für Mondlander arbeiten, sind Boeing, Dynetics, SpaceX und Sierra Nevada Corp. (Louisville, Colorado und Madison, Wis., USA).
Zusätzlich zu bemannten Mondlandern erwartet die NASA den Bedarf an kleinen und mittelgroßen Mondlandern, um eine Vielzahl von wissenschaftlichen Untersuchungen und große Technologie-Demonstrationsnutzlasten zu ermöglichen.
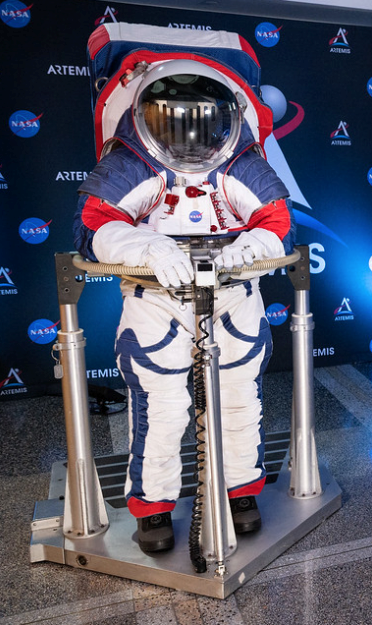
Artemis-Anzüge
Im Oktober 2019 stellte die NASA zwei neue Raumanzug-Designs vor – eine neue Exploration Extravehicular Mobility Unit (xEMU) und den Orion Crew Survival System (OCSS)-Anzug – die beide für die Artemis . verwendet werden Mondmissionen programmieren.
Es wird berichtet, dass der xEMU-Anzug gegenüber Anzügen, die derzeit für Aktivitäten außerhalb des Fahrzeugs (EVA) verwendet werden, einen erheblich verbesserten Bewegungsumfang bietet. Laut ILC Dover (Frederica, Del., USA), der seit langem mit der Herstellung von Raumanzügen der NASA zusammenarbeitet, ist der xEMU-Anzug ein Update eines fortschrittlichen Wanderanzugs, der 2016 an die NASA geliefert wurde und als Z-2 bekannt ist.
„Seit 2016 hat ILC Dover das Design von Wanderanzügen sowie von Zero-G-Anzügen und Startanzügen kontinuierlich verbessert“, sagt Dan Klopp, Produktmarketing für ILC Dover.
Der Prototyp des Z-2 Raumanzugs weist einen Karbon/Epoxy-Torso und Hüftelemente im Design auf. (Weitere Informationen zur Verwendung von Verbundstoffen in Raumanzügen finden Sie unter „Auf dem Mars reicht nicht jeder Anzug“.)
Der OCSS-Raumanzug der NASA ist als Druckstart- und Einfluganzug für Orion . konzipiert Mannschaftsmitglieder. Obwohl die NASA keine Details zu den Materialien im neuen Design veröffentlicht hat, ist es eine sichere Sache, dass eine angemessene Menge Verbundwerkstoffe beteiligt ist. Start- und Einstiegsanzüge aus der Shuttle-Ära waren mit einer äußeren Schicht aus flammbeständigem Meta-Aramid Nomex von DuPont (Richmond, Virginia, USA) versehen. Frühere Extravehicular Mobility Units (EMUs) verwendeten Kombinationen aus Nomex, dem Para-Aramid-Kevlar (ebenfalls von DuPont entwickelt) und Gore-Tex, einer wasserdichten, atmungsaktiven Gewebemembran von W.L. Gore &Assoc. (Newark, Del., USA) (Weitere Informationen).
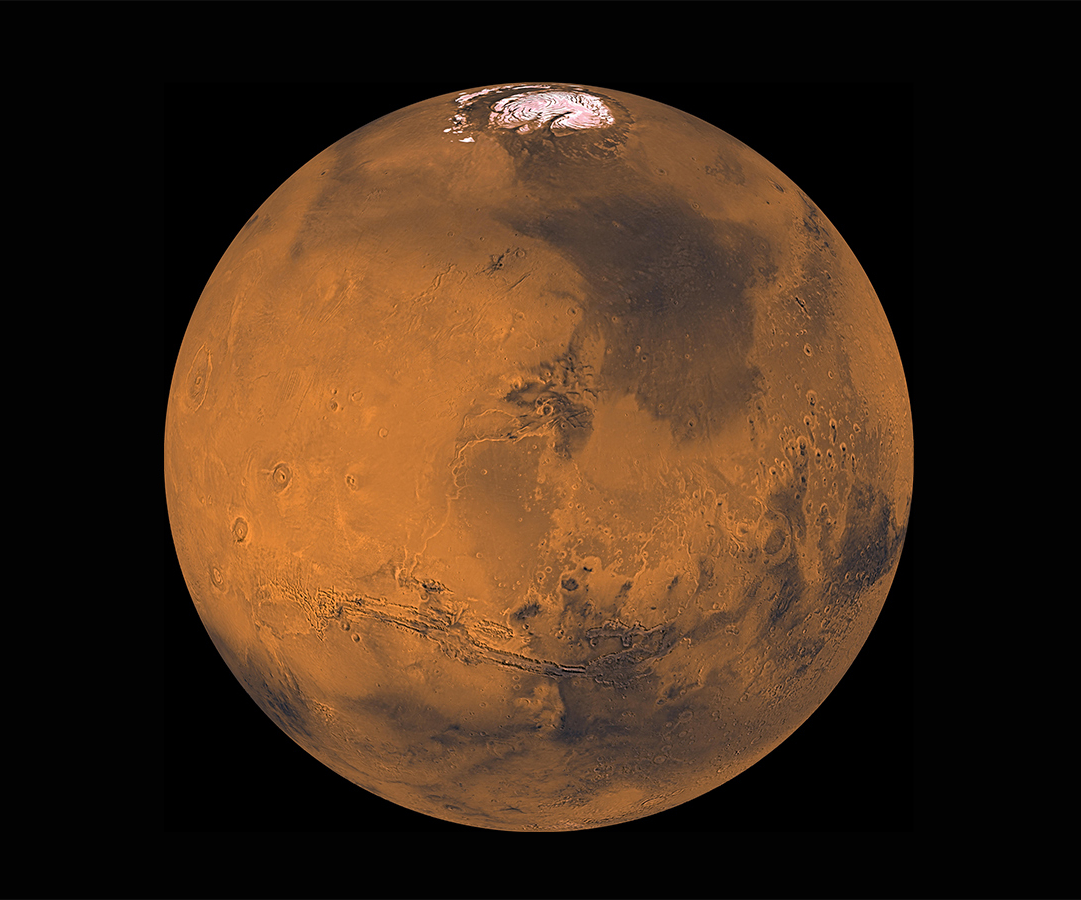
Mars
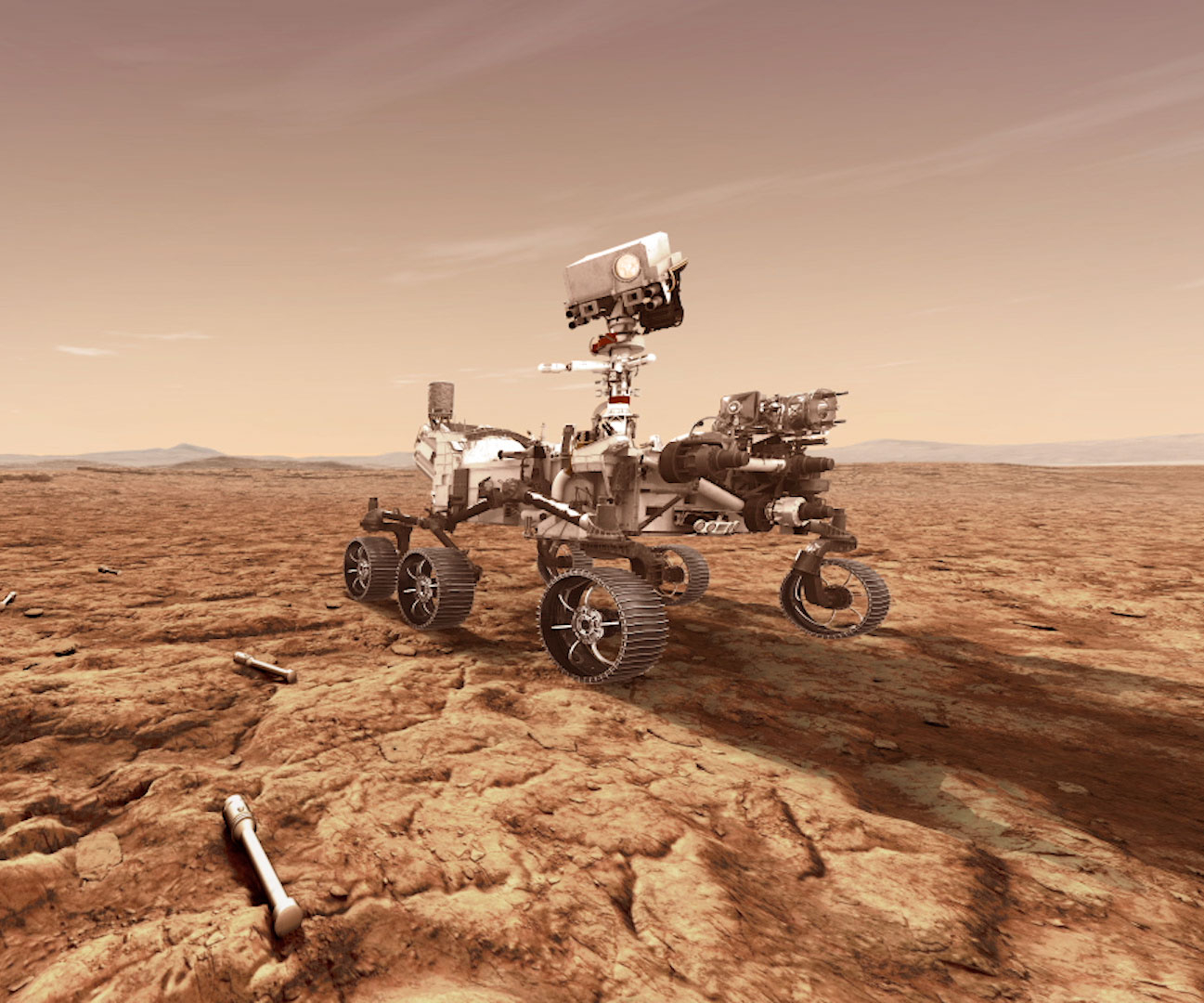
Ein Großteil der Artemis Initiative schafft die Voraussetzungen, um Menschen zum Mars zu schicken. In der Zwischenzeit arbeitet die NASA auch an einer unbemannten Mission zum Mars in diesem Sommer, die einen neuen Roboter-Rover und einen Roboter-Erkundungshubschrauber auf dem Roten Planeten etablieren wird.
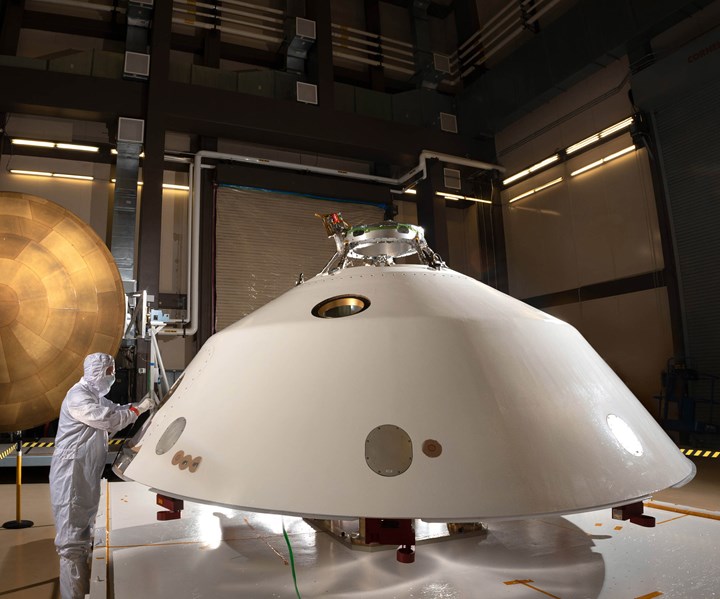
Eine kapselförmige Aeroshell wird den Rover Mars 2020 beim Eintritt in die Marsatmosphäre und bei der Landung schützen. Die Aeroshell besteht aus einer Aluminiumwabe mit Kohlefaser-Häuten. Der Hitzeschild verwendet ein gekacheltes phenolimprägniertes Kohlenstoffablator-(PICA)-Wärmeschutzsystem.
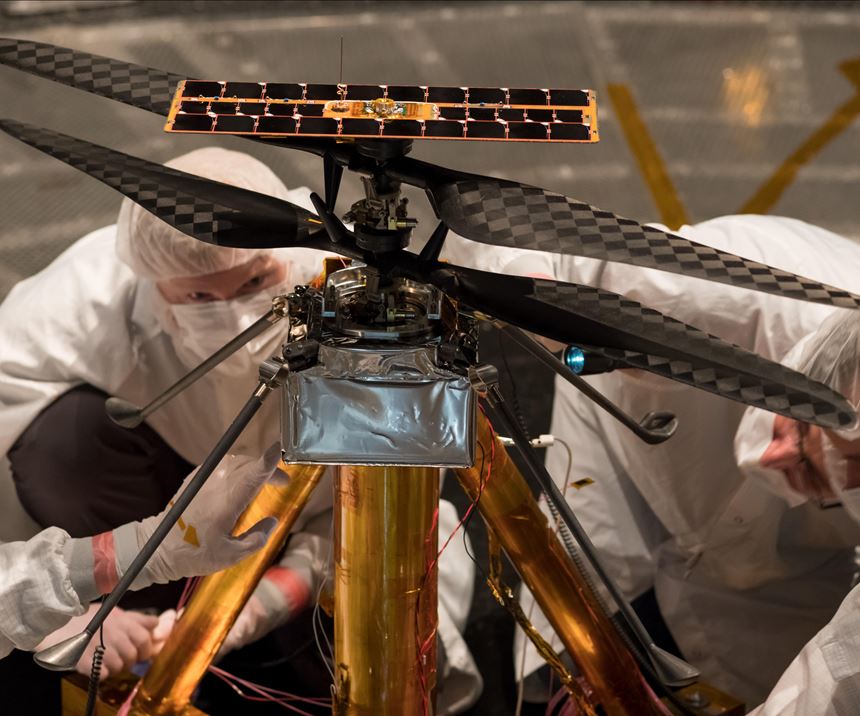
Der Mars 2020 Rover selbst ist ungefähr 3 Meter lang, 9 Fuß breit und 7 Fuß hoch (3 Meter lang, 2,7 Meter breit, 2,2 Meter hoch). Obwohl die NASA keine Details zu den Materialien veröffentlicht hat, die zum Bau des Rovers verwendet wurden, ist bekannt, dass Advanced Composites Training (ACT, London, Ontario, Kanada) als Berater für das Jet Propulsion Laboratory der NASA (JPL, Pasadena, Kalifornien, USA) diente ) zur Verwendung von Verbundwerkstoffen für den Bau des Rovers Mars 2020 (Weitere Informationen).
Mit 2.314 Pfund (1.050 Kilogramm) wiegt der Rover weniger als ein durchschnittlicher Kompaktwagen. Es muss sowohl leicht als auch langlebig für die Reise zum Roten Planeten sein und außerdem stark genug sein, um Kameras und wissenschaftliche Instrumente sowie den Mars-Hubschrauber zu tragen – ein weiteres kunststoffintensives Fahrzeug, das zur Erforschung des Planeten verwendet wird .
Der Mars-Helikopter besteht aus mehr als 1.500 einzelnen Teilen aus Kohlefaser, flugtauglichem Aluminium, Silizium, Kupfer, Folie und Schaumstoff und wiegt nicht mehr als 1,8 Kilogramm (Erfahren Sie mehr).

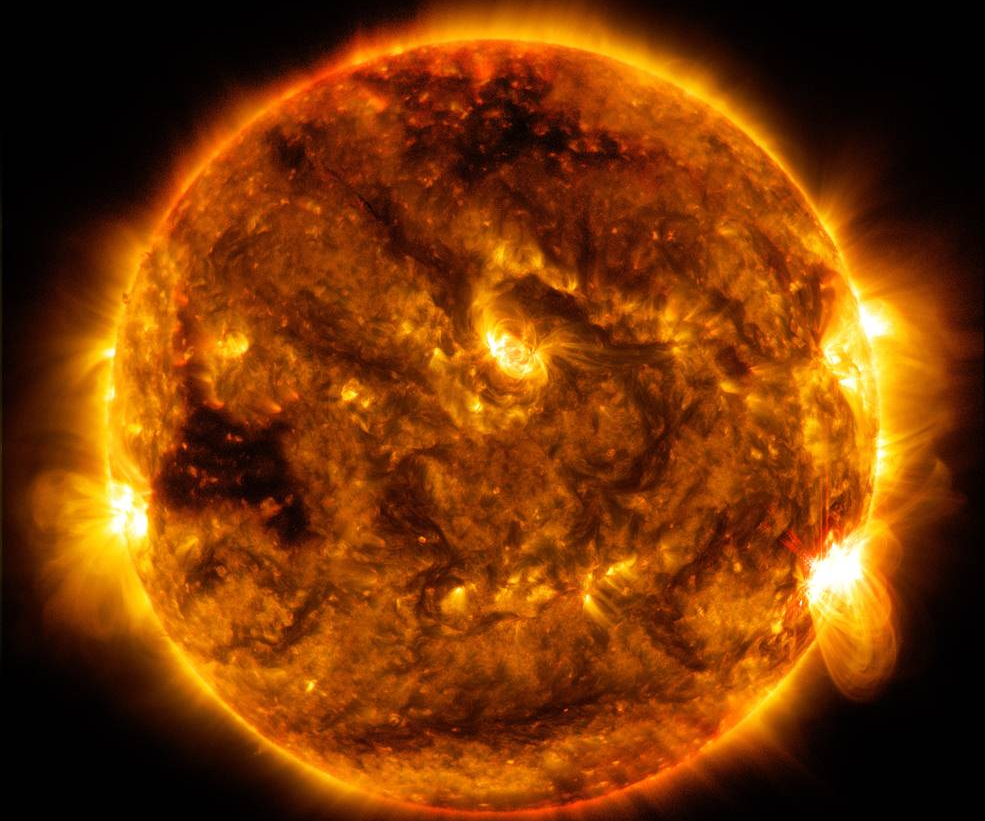
Sonne
Derzeit laufen zwei Missionen, um unser Verständnis der Sonne und ihres Verhaltens zu verbessern, beide mit dem ultimativen Ziel, Sonnenstürme vorherzusagen, die terrestrische elektrische Systeme, Satellitenkommunikation und GPS beeinträchtigen können.
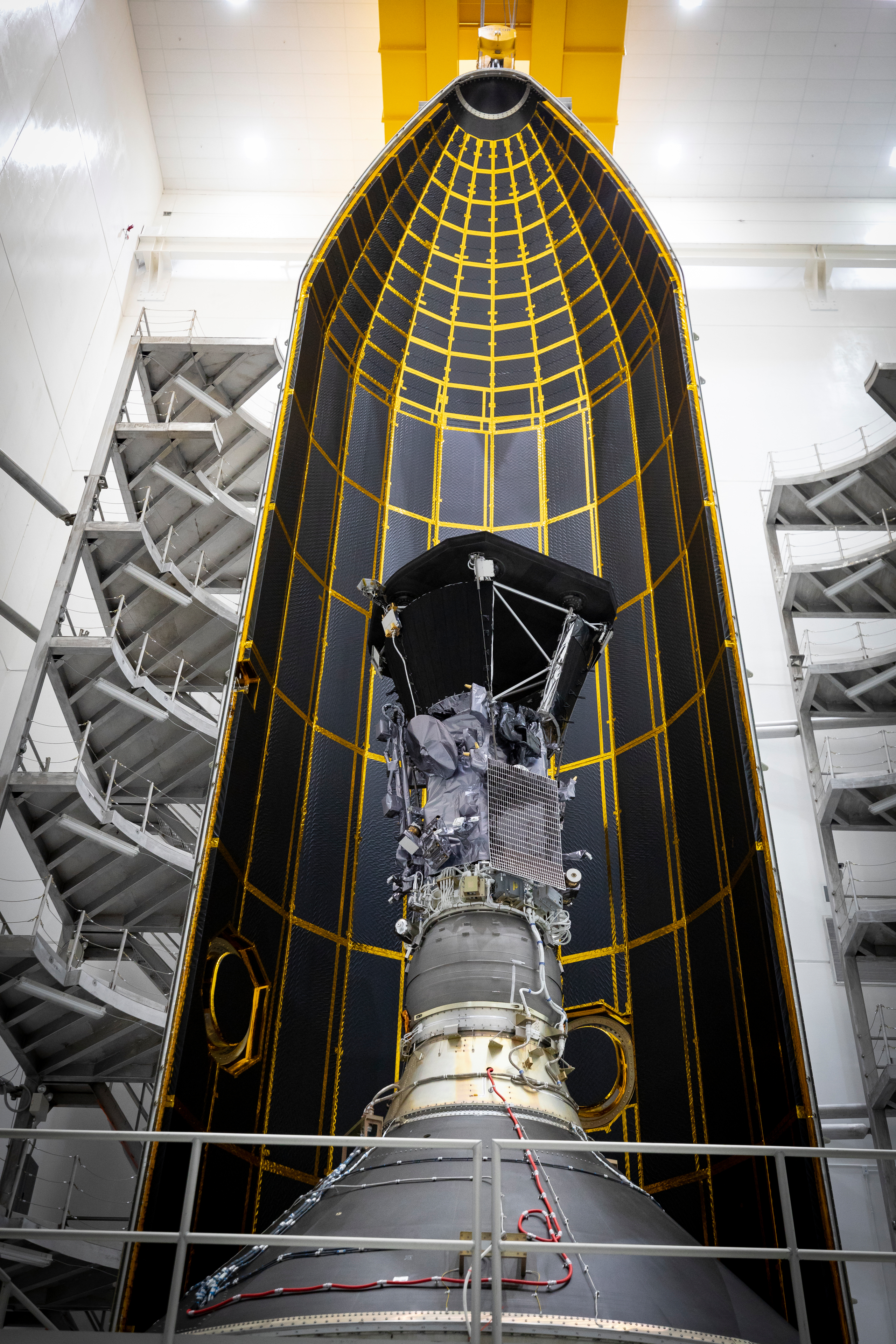
Parker Solar Probe
Die Parker Solar Probe wurde im August 2018 ins Leben gerufen und führt In-situ-Messungen und Bildgebung durch, um die Korona der Sonne und des Sonnenwinds zu untersuchen. Um den extremen Temperaturen in dieser Region standzuhalten, verwendet die Sonde eine 4,5 Zoll dicke leichte reflektierende Abschirmung. Dieses Wärmeschutzsystem (TPS) besteht aus Kohlefaser-Verbundschaum, der zwischen zwei Carbonlaminaten eingebettet und auf der der Sonne zugewandten Oberfläche mit weißer Keramikfarbe beschichtet ist. Der Schild wurde vom Johns Hopkins Applied Physics Laboratory (Laurel, Maryland, USA) entworfen und bei Carbon-Carbon Advanced Technologies (Kennedale, Texas, USA) gebaut.
Die meisten Instrumente der Sonde sind hinter dem TPS versteckt, und Sensoren entlang der Kante des Hitzeschilds halten das Raumfahrzeug in der richtigen Position. Solaranlagen, die zum Antrieb des Fahrzeugs verwendet werden, können zum Schutz in den Schatten des Hitzeschildes eingezogen werden. Ein einfaches Kühlsystem, das durch Zirkulation von einer Gallone Wasser betrieben wird, wird auch verwendet, um die Solarzellen und Instrumente kühl zu halten.
Im Januar 2019 berichtete die NASA, dass Parker Solar Probe funktionierte nach seiner vierten Annäherung an die Sonne, bekannt als Perihel, wie geplant. Das TPS des Raumfahrzeugs erreichte eine neue Rekordtemperatur von 1.134 ° F (612 ° C), obwohl das Raumfahrzeug und die Instrumente hinter diesem schützenden Hitzeschild eine Temperatur von etwa 85 ° F (30 ° C) blieben. Während der nächsten drei Perihelien der Raumsonde in den Jahren 2024-25 wird das TPS Temperaturen um 2.500 ° F (1.370 ° C) aufweisen.
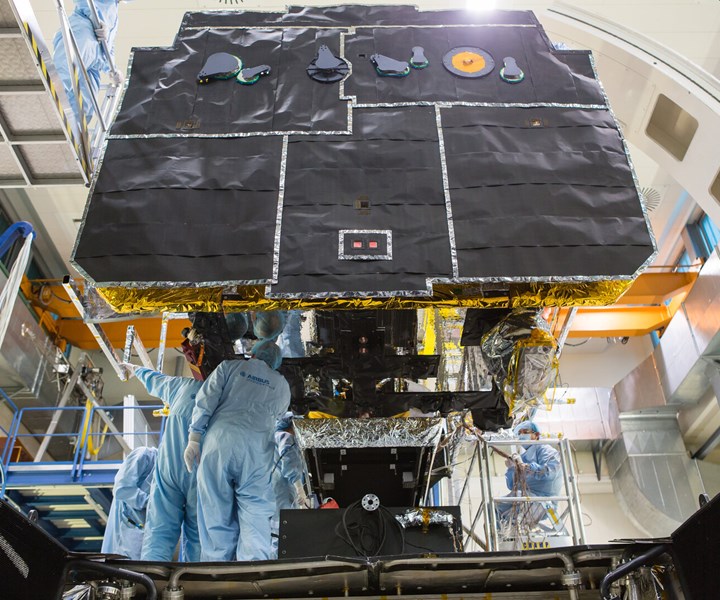
Solar Orbiter
Solar Orbiter , eine gemeinsame Mission zwischen der Europäischen Weltraumorganisation (ESA) und der NASA, die im Februar 2020 gestartet wurde. Der Orbiter befindet sich auf einer einzigartigen Flugbahn, die es seinem umfassenden Instrumentarium ermöglichen wird, die ersten Bilder der Sonnenpole zu liefern.
Das Raumfahrzeug wird durch einen geschichteten Sonnenschild aus Kohlefaserverbundstoff/Titan mit Öffnungen für verschiedene Instrumente geschützt. Der 324 Pfund schwere Hitzeschild hält bis zu 970 ° F (521 ° C) stand und verwendet eine 0,05 Millimeter dicke Schicht Titanfolie, um die Hitze zu reflektieren. Der Schild wird von einer 2,94 mal 2,56 Meter großen Trägerplatte getragen, die etwa 5 Zentimeter dick ist und aus leichten Aluminiumwaben mit zwei Karbonfaserhäuten mit hoher Wärmeleitfähigkeit besteht. Weiterer Schutz wird durch eine mehrschichtige Isolierung geboten, die 572º F (300 °C) aushält. Der Hitzeschild des Solar Orbiter ist mit einer dünnen, schwarzen Schicht aus Kalziumphosphat beschichtet.

Jenseits des Sonnensystems
Im August 2019 verbanden Ingenieure der Northrop Grumman-Einrichtungen in Redondo Beach, Kalifornien, USA, das Optical Telescope Element des James Webb Space Telescope (JWST), das Spiegel und wissenschaftliche Instrumente umfasst, und das Space Craft Element, das die Funktionen von JWST vereintSonnenblende und Raumfahrzeug, zum ersten Mal. Obwohl beide Komponenten des Teleskops einzeln getestet wurden, wurden die beiden Hälften erstmals zu einem einzigen Observatorium kombiniert. Der Meilenstein war für Webb ein wichtiger Meilenstein, da das Teleskop seiner geplanten Markteinführung im Jahr 2021 näher kommt.
JWST ist das leistungsstärkste und komplexeste Weltraumteleskop, das je gebaut wurde – 100-mal leistungsstärker als das Hubble-Teleskop. Das Teleskop wurde entwickelt, um den Kosmos mit Infrarotlicht zu erforschen, und wird es Astronomen ermöglichen, die am weitesten entfernten Objekte im Universum zu beobachten und Bilder von fernen Sternen, Exoplaneten und den ersten gebildeten Galaxien zu liefern. Das Teleskop ist auch ein spannendes Beispiel dafür, wie Verbundwerkstoffe Satelliten und Raumfahrzeuge ermöglichen.
Die Teleskopplattform besteht aus drei Hauptkomponenten – dem Optical Telescope Element (OTE), dem Integrated Science Instrument Module (ISIM) und dem Space Craft Element (SCE), das den Raumfahrzeugbus und die tennisplatzgroße Sonnenblende umfasst.
JWST verwendet eine Kohlefaser-Backplane, um die Spiegel, Instrumente und andere Elemente des Teleskops zu tragen – insgesamt mehr als 2.400 Kilogramm (2,5 Tonnen) Hardware. Die Struktur ist auch dafür verantwortlich, das Teleskop während langer Lichtsammelperioden stabil zu halten. Die Rückwandplatine kann trotz extremer Temperaturen von -243 °C bis -208 °C (-406 °F bis -343 °F) nicht mehr als 38 Nanometer variieren.
Die Rückwand wird aus Prepreg hergestellt, das Kohlefaser von Toray Advanced Composites und Cyanatesterharz von Hexcel (Stamford, Connecticut, USA) umfasst. Die Struktur umfasst mehr als 10.000 leichte Kohlefaser-Verbundteile. Die gesamte Backplane-Struktur umfasst den Mittelabschnitt, die Flügelbaugruppen und die Backplane Support Fixture (BSF) und misst im vollständig ausgefahrenen Zustand etwa 24 Fuß hoch, 3,50 Fuß breit und mehr als 11 Fuß tief (7,3 x 5,9 x 3,4 Meter). Es wiegt nur 2.180 Pfund (989 Kilogramm), kann aber Instrumente mit einem Gewicht von mehr als 7.300 Pfund (3.311 Kilogramm) tragen – eine Nutzlast von mehr als 300 % seines Eigengewichts.
Neben dem Primärspiegel und der Backplane-Struktur umfasst die OTE von JWST seine Deployable Tower Assembly (DTA), die Sekundärspiegel-Stützstruktur und das ISIM-Framework, das die wissenschaftlichen Instrumente und Kühlsysteme des Teleskops beherbergt. Diese Strukturen werden aus einem Prepreg aus ultrahochmoduliger Kohlefaser und Cyanatesterharz von Toray Advanced Composites hergestellt.
„Diese Materialien sind sehr gute Materialien für die optische Bank“, sagt Sean Johnson, Produktmanager Duroplaste bei Toray. „Die hohe Steifigkeit der UHM-Faser sorgt für eine sehr stabile Struktur [und] bietet eine gewisse Dämpfung. Es ist sehr gut bei den niedrigen Temperaturen, die [JWST] sehen wird.“
Der SCE oder Raumfahrzeugbus besteht ebenfalls aus Torays Kohlefaserverbundwerkstoffen und beherbergt den Antrieb des Raumfahrzeugs, Observatoriumsunterstützungssysteme, Solarenergie, aktive Kühlsysteme und Kommunikation. Der Bus muss gleichzeitig leicht sein und gleichzeitig einer Kraft von 45 Tonnen standhalten können, während er das Observatorium während des Starts unterstützt.
Im Oktober 2019 hat JWST die Tests zum Einsatz von Sonnenblenden erfolgreich bestanden und soll derzeit 2021 auf den Markt kommen. (Weitere Informationen).
Ein riesiger Sprung
Die nächsten Jahre werden die Bühne für ein völlig neues Zeitalter der Weltraumforschung bereiten. Da sich die Raumfahrzeuge und Systeme, die für dieses neue goldene Zeitalter benötigt werden, ständig weiterentwickeln, werden Zulieferer und Hersteller von Verbundwerkstoffen ständig herausgefordert, die Materialien und Technologien an neue Grenzen zu bringen.
Harz
- Ein Leitfaden zum Verständnis des Herstellungsprozesses von Verbundwerkstoffen
- Wie sieht die Zukunft von Verbundwerkstoffen in der Sportartikelindustrie aus?
- Die greifbaren Vorteile von VR im Engineering-Bereich
- Wie Composites Tarnung auf dem Schlachtfeld unterstützen
- Die Vorteile nutzen:Der Einsatz von Verbundwerkstoffen in landwirtschaftlichen Geräten nimmt zu
- Im Dienste der Composites-Welt in Israel und den USA
- SAMPE 2018-Keynote blickt in die Zukunft der Verbundwerkstoffe
- Nèos International gründet neues Hauptquartier für Verbundwerkstoffe in Großbritannien
- Das James-Webb-Weltraumteleskop startet erfolgreich
- 20 Jahre Wissenschaft auf der Internationalen Raumstation