Beseitigung von Hindernissen für den Leichtbau von Schiffen mit Verbundwerkstoffen
Glas- und kohlefaserverstärkte Polymer-Verbundwerkstoffe (GFK und CFK) werden seit Jahrzehnten zum Bau von Schiffen verwendet, darunter zahlreiche 40- bis 60-Meter-Minenjäger und noch größere Schiffe, darunter die 72 Meter lange Korvette der Visby-Klasse der schwedischen Marine und die 75 Meter lange Segelyacht Mirabella V . Die 141 Meter lange Motoryacht Swift 141 (umbenannt in Yas ) ist eine niederländische Stahlfregatte, die mit GFK/CFK in Unterdecksohlen und Dreidecker-Aufbauten (siehe „Von der Fregatte zur Luxus-Gigayacht“) umgebaut wurde, einschließlich einer Verbund-Stahl-Deckverbindung.
Dennoch werden Verbundwerkstoffe im Schiffbau selten verwendet. Dies ist hauptsächlich auf die Safety Of Life At Sea (SOLAS)-Vorschriften der International Maritime Organization (IMO, London, Großbritannien) zurückzuführen, die vorschrieben, dass Handelsschiffe bis zum MSC/Circ aus Stahl gebaut werden müssen. 1002 wurde 2002 ausgestellt und erlaubt alternative Designs.
„Die Verordnung schreibt eine Risikoanalyse vor, die zeigt, dass die alternative Konstruktion und Konstruktion Stahl gleichwertig ist“, erklärt Stéphane Paboeuf, Leiter der Abteilung Verbundwerkstoffe der Klassifikationsgesellschaft Bureau Veritas (BV, Nantes, Frankreich). „Dieser Prozess ist langwierig, teuer und die endgültige Entscheidung könnte immer noch negativ ausfallen.“ Obwohl Verbundwerkstoffe viele Vorteile für den Schiffbau bieten, haben die Herausforderungen des Brandschutzes und der Vorschriften den Einsatz jedoch erschwert.
Unterdessen suchen Reeder, Betreiber und Bauherren nach Lösungen für eine verbesserte Nachhaltigkeit, darunter geringeres Gewicht zur Reduzierung des Kraftstoffverbrauchs, der Treibhausgasemissionen und des Schiffstiefgangs – letzteres für flache Binnengewässer. Die inhärente Korrosionsbeständigkeit von Verbundwerkstoffen zur Reduzierung der Wartung ist ebenfalls attraktiv.
Im Jahr 2017 hat die IMO MSC.1/Circ. herausgegeben, eine neue Reihe von Richtlinien für die Verwendung von FRP-Verbundwerkstoffen in Handelsschiffen. Da die Bewertung dieser Richtlinien durch die IMO im Jahr 2021 näher rückt, finden erstaunlich viele Aktivitäten statt. Zwei europäische Konsortien, FIBRESHIP und RAMSSES, die vom 378-köpfigen europäischen Netzwerk für Leichtbauanwendungen auf See (E-LASS) unterstützt werden, führen diese Welle von Demonstrationsprojekten an, die Verbunddecks, Ruder, Rümpfe, modulare Kabinen und Aufbauten, Patch . umfasst Reparaturen an Stahl- und Verbund-Stahl-Schweißverbindungen. Gemeinsam wollen sie die Barrieren für den leichten Schiffsbau aus Verbundwerkstoff überwinden, indem sie nicht nur die Brand- und Tragfähigkeit großer Strukturen und ganzer Schiffe demonstrieren, sondern auch neue Wege für Zertifizierungs- und Produktionsmethoden, neue Verbindungstechnologien und Konstruktionswerkzeuge entwickeln. Sie tauschen auch Informationen über laufende Workshops, Wissensdatenbanken und Material-/Designdatenbanken aus. Für Marine-Verbundwerkstoffe mag sich ein neuer Markt öffnen, aber welche Lösungen werden dafür benötigt?
FIBRESHIP und RAMSSES
FIBRESHIP und RAMSSES wurden im Juni 2017 gestartet, finanziert durch das Horizon 2020-Programm der Europäischen Union. FIBRESHIP hat 18 Mitglieder und läuft bis Mai 2020, während RAMSSES 36 Mitglieder hat und im Mai 2021 endet. Beide umfassen Unternehmen aus der gesamten Lieferkette, darunter F&E-Zentren, Universitäten, Material- und Technologielieferanten, Teilehersteller, Schiffsarchitektur- und Ingenieurbüros, Werften, Reeder und Klassifikationsgesellschaften. Letztere sind verantwortlich für die Entwicklung spezifischer Regeln für den einzelnen Schiffsbau basierend auf den allgemeinen Richtlinien der IMO. Sie sind von Flaggenstaaten (jedes Schiff trägt die Flagge eines Landes) ermächtigt, den Schiffbau zu prüfen und sicherzustellen, dass diese Regeln befolgt werden. „Es ist wichtig, dass alle Beteiligten und Endnutzer einbezogen werden“, sagt Alfonso Jurado, Leiter F&E bei Tecnicas y Servicios de Ingeniería (TSI, Madrid, Spanien) und FIBRESHIP-Projektkoordinator.
„Das Hauptziel von FIBRESHIP ist die Entwicklung von Konstruktions- und Produktionskapazitäten für große Seeschiffe (über 50 Meter Länge) mit weniger Gewicht“, fährt Jurado fort. „Das ist auch die Hauptmotivation für mein Unternehmen.“ TSI entwickelt die Verbundstruktur eines insgesamt 85 Meter langen Fischereiforschungsschiffs (FRV), das als Demonstrator dienen wird und bisher eine Reduzierung des Strukturgewichts um fast 70 % gegenüber dem Referenzschiff aus Stahl erreicht. „Das ist erstaunlich und bietet die echte Möglichkeit, der Schifffahrtsbranche zu helfen“, sagt er. Ein 20 Tonnen schwerer Abschnitt dieses FRV, der 11 mal 11 mal 8,6 Meter misst (siehe Eröffnungsbild), wurde von der Partnerwerft iXblue in La Ciotat, Frankreich, gebaut und im Juni 2019 beim zweiten öffentlichen Workshop von FIBRESHIP ausgestellt (siehe Nachrichtenbeitrag mit Video des hergestellten Demonstrators).
Jurado erklärt, dass der FRV der erste von drei allgemeinen Schiffskoffern aus Verbundwerkstoffen ist, die FIBRESHIP entwickelt. Die nächsten beiden sind 260-Meter-LOA-Containerschiffe und 204-Meter-ROPAX, wobei letzteres die Ladekapazität eines Roll-on/Roll-off-Schiffes mit den Passagiereinrichtungen einer Fähre kombiniert. „Das FRV wurde als Demonstrator ausgewählt, weil es mit einer konventionelleren Schiffsstruktur kleiner und damit in naher Zukunft am besten zu bauen ist“, sagt er. „Auch Schiffseigner haben ein echtes Interesse an einem solchen Schiff gezeigt.“ Inzwischen hat RAMSSES 13 Demonstratoren im Gange, von denen 10 Verbundwerkstoffe beinhalten, und verfolgt auch ein reines Verbundschiff.
Jurado stellt fest, dass die an diesen Projekten teilnehmenden Unternehmen das Potenzial solcher neuartigen Designs und neuer Leichtbauprodukte sehen, um ihren Unternehmen sowie der Schifffahrtsindustrie jedes Landes einen Wettbewerbsvorteil zu verschaffen. Aber der Fortschritt wird nicht allein durch große Demonstranten gesichert. „Wir brauchen auch Unterstützung von den Regulierungsbehörden“, fügt er hinzu. „Ein erster Schritt besteht darin, die IMO zu engagieren und die aktuelle SOLAS-Verordnung an die neuen Anforderungen und Anforderungen der Schifffahrtsindustrie anzupassen. Ohne dies können wir nicht vorankommen, weil Versicherungsunternehmen die Faserverbundschiffe nicht zeichnen, wenn sie beispielsweise die Mindestanforderungen und die Sicherheitszertifizierung nicht erfüllen.“
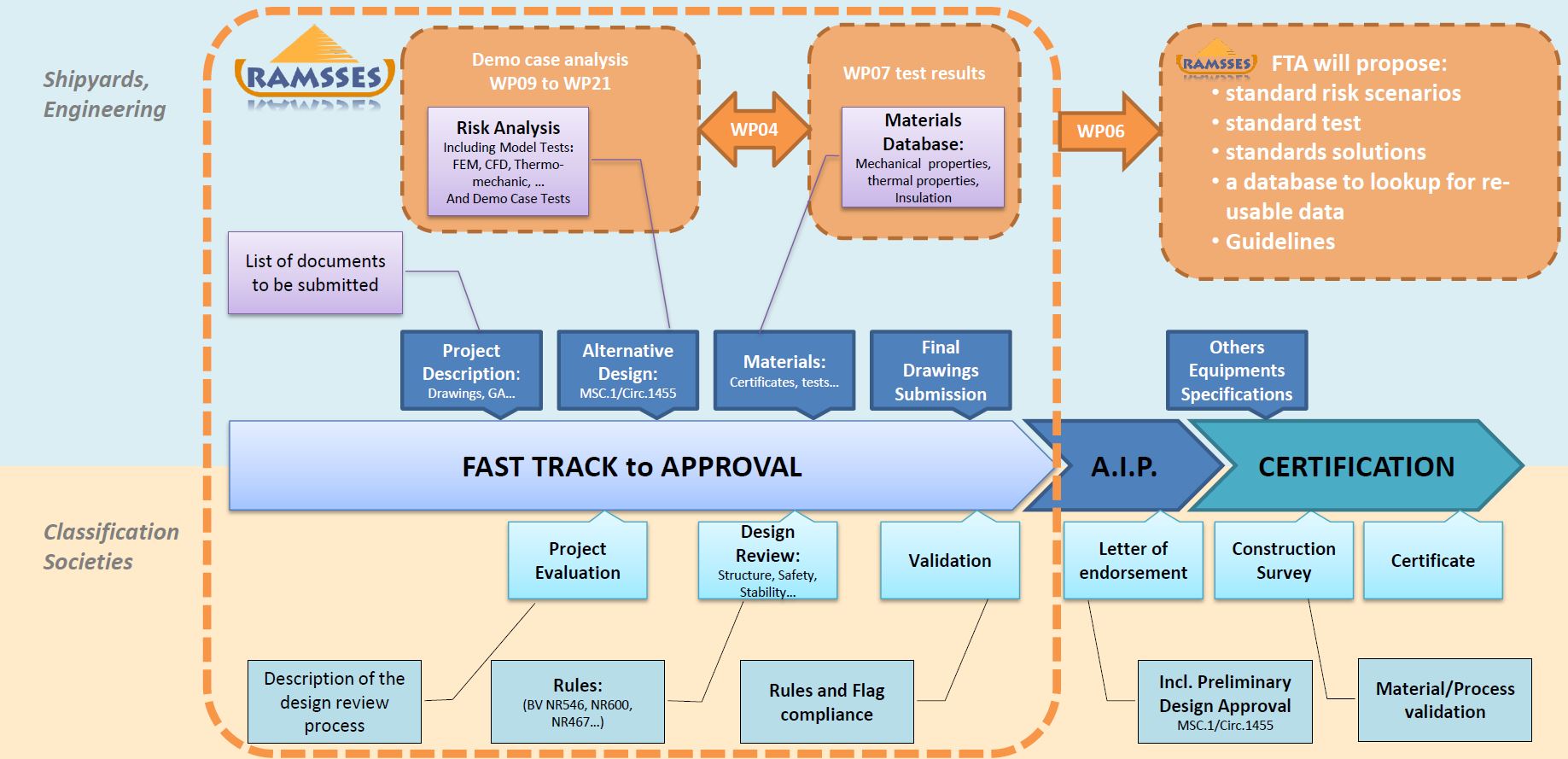
Vorgeschlagener Fast Track to Approval (FTA)-Ansatz für die Zertifizierung von Verbundwerkstoffen in Handelsschiffen, der im Rahmen des RAMSSES-Projekts entwickelt wird, wie während des E-LASS-Seminars im Juni 2019 (Vigo, Spanien) vorgestellt. Quelle | RAMSSES und Stephane Paboeuf, Bureau Veritas
„FIBRESHIP verfolgt einen langfristigen Ansatz durch die Entwicklung neuer Regeln, während RAMSSES einen kurzfristigen Ansatz durch die Verwendung bestehender Regeln und Methoden entwickelt“, erklärt Paboeuf von BV, die der einzige Klassifikationsgesellschaftspartner von RAMSSES ist, und einer von drei in FIBRESHIP neben Lloyd's Register (London, UK) und RINA (Genua, Italien). „Bei RAMSSES entwickeln wir ein Fast Track to Approval (FTA)-Verfahren, das auf der Wiederverwendung von Projektdaten basiert, um Tests zu standardisieren und Anleitungen für Design und Genehmigung bereitzustellen.“ Dieses Verfahren soll für Werften, Schiffsarchitekten und Zulieferer einfach und gut lesbar sein. Die Beschleunigung gegenüber dem aktuellen Prozess wird durch die Entwicklung von Unterstützungen in RAMSSES-Demonstrationsprojekten erreicht, darunter:
- eine Datenbank mit vorab genehmigten Lösungen und Materialprüfungsergebnissen, um Wiederholungsprüfungen zu vermeiden,
- Brandrisikoszenarien, die eine Reihe ähnlicher Anwendungen abdecken, um die Anzahl und den Umfang von Risikobewertungen zu begrenzen, und
- Analyse- und Modellierungstools, einschließlich numerischer oder statistischer Modelle, die in Zukunft physische Tests ersetzen können.
„Bei FIBRESHIP arbeiten wir mit Lloyd’s Register und RINA zusammen, um eine Reihe von Vorschriften speziell für große Schiffe aus Verbundwerkstoffen zu entwickeln“, fährt Paboeuf fort. „Für die strukturelle Leistung definieren wir neue Sicherheitsbeiwerte für lokale und globale Lasten.“ RAMSSES und FIBRESHIP schlagen außerdem vor, die aktuellen Brandklassen wie A60, B30 und B15 durch eine neue Konvention REIxx zu ersetzen, wobei R Feuerwiderstand (Tragfähigkeit im Brandfall) angibt, E Integrität (Verhinderung von Rauch- und Flammenausbreitung) bezeichnet ) und I definiert Brandschutz. „Ziel ist es, die baulichen Brandschutzklassen besser auf die verwendeten Verbundwerkstoffe abzustimmen“, erklärt Paboeuf.
Darüber hinaus befassen sich die beiden Projekte auch mit Risikobewertungen aufgrund von Flammenausbreitung, Rauchentwicklung und Brandgefahr im Entstehungsraum, aber auch auf schiffsglobaler Sicherheitsebene. „Für das Brandverhalten entwickeln wir einen lokalen Äquivalenzansatz, der sich mit dem Brandschutz auf lokaler Ebene befasst, basierend auf den Feuerklassen der Schotten und anderer struktureller Unterteilungen in jedem Raum des Schiffes“, sagt Paboeuf. „Der zweite Ansatz, die globale Äquivalenz, befasst sich mit Feuer auf Schiffsebene und berücksichtigt alle Systeme (aktiver und passiver Brandschutz, Detektion, Evakuierung usw.), die sich auf die Brandsicherheit des gesamten Schiffes auswirken, nicht nur jedes geteilter Raum.“
„Die Verbreitung von Verbundwerkstoffen im Schiffbau wird Schritt für Schritt erfolgen“, sagt er. „Es beginnt mit kleinen Teilen wie Decks und Aufbauten oder Ausrüstung wie Wellenleitungen und Propellern, bevor es zum Bau ganzer Schiffe übergeht, bei denen es sich zunächst hauptsächlich um Spezialschiffe wie Forschungs- und seismische Testschiffe und Hochgeschwindigkeitsschiffe handelt Patrouillenboot.“

Abb. 1 RAMSSES 80-Meter-Verbundschiff
Damen Shipyard (DSNS) entwickelt im Rahmen des RAMSSES-Projekts ein Offshore-Patrouillenschiff aus Verbundwerkstoffen. Sein 6 mal 6 mal 3 Meter großer Demonstrator für den Rumpfabschnitt in Originalgröße wird 2020 mit Harzinfusion in Zusammenarbeit mit InfraCore Company (ICC) und Airborne International (AIR) gebaut. Quelle | Damen Werft und RAMSSES
Demonstratoren für vollständig zusammengesetzte Schiffe
Neben dem 85 Meter langen FRV, das von FIBRESHIP demonstriert wird, wird bei RAMSSES ein 80 Meter langes Offshore-Patrouillenschiff als erstes SOLAS-Schiff komplett aus Verbundwerkstoff entwickelt. Unter der Leitung der Damen Shipyard Group (Gorinchem, Niederlande) führt diese Arbeit die Ergebnisse des 2014 begonnenen Bluenose-Projekts fort. Innerhalb des RAMSSES-Arbeitspakets 17 leitet Damen die Demonstration eines 6 x 6 x 3 Meter großen Full- maßstabsgetreuer zusammengesetzter Rumpfabschnitt dieses Schiffes, das mittels Vakuuminfusion hergestellt wurde, erklärt Matthias Krause, F&E-Ingenieur am Center of Maritime Technologies (CMT, Hamburg, Deutschland) und Koordinator des RAMSSES-Projekts zusammen mit CETENA (Genua, Italien). „Evonik hat ein neuartiges Harz für diesen Demonstrator-Rumpfabschnitt entwickelt und 6 Meter hohe Werkzeuge hergestellt. Damen arbeitet auch mit Airborne International (Den Haag, Niederlande), einem Zulieferer der Flugzeugindustrie, der auch große infundierte Strukturen gebaut hat.“ Evonik (Essen, Deutschland) hat seine Rolle bei der Verbesserung der Schlagzähigkeit und des Ermüdungsverhaltens des mit Glasfaser/Vinylester infundierten Rumpfes erläutert.
Ein weiterer Partner dieses Demonstrators ist InfraCore Co. (Rotterdam, Niederlande), die neue Anwendungen für die InfraCore-Technologie entwickelt, die von der Schwesterfirma FiberCore Europe (Rotterdam) in mehr als 1.000 Verbundbrücken und Schleusentoren weltweit verwendet wird. „Wir haben uns ursprünglich bei diesem Projekt mit Damen zusammengetan, um einen 12 bis 14 Tonnen schweren Hubschrauberlandeplatz zu bauen“, erklärt Laurent Morel, Betriebsleiter von InfraCore. „Wir arbeiten jetzt mit ihnen zusammen, um die Decks, Schotten und die Rumpfstruktur zu bauen. Wir werden sowohl horizontale als auch vertikale Infusion verwenden, um den Rumpfabschnitt in einem Schuss herzustellen. Bisher haben wir bis zu einer Höhe von 9,8 Metern infundiert.“ Nach Fertigstellung wird dieser Demonstrator auf strukturelles und brandtechnisches Verhalten getestet, wobei die Ergebnisse und gewonnenen Erkenntnisse in die neuen FTA-Module von RAMSSES eingespeist werden.
Leichte Decks
Verbundwerkstoffe wurden bereits im ersten Roll-on/Roll-off-Autotransporter mit Verbundfrachtdeck demonstriert, der von der Uljanik Group (Pula, Kroatien) im Rahmen des RAMSSES-Arbeitspakets 14 entwickelt und gebaut wurde (siehe „Geringes Gewicht in der Höhe“ Meere“) sowie ein Leichtbau-Sonnendeck für ein 110 Meter langes Flusskreuzfahrtschiff (siehe „Verbunddeck reduziert den Tiefgang von Flussschiffen“) und ein Verbund-Zwischendeck für einen 200 Meter langen Stückgutfrachter. „Ein Zwischendeck ist ein abnehmbares Deck, das Sie installieren können, um den Laderaum zu unterteilen, um verschiedene Arten von Ladung zu erleichtern“, erklärt Arnt Frode Brevik, Manager bei Compocean (Sandvika, Norwegen), einem Anbieter von Verbundlösungen, die aus der Öl- und Gasindustrie hervorgegangen sind Industrie.
„Wir arbeiten seit mehreren Jahren mit Oshima Shipbuilding (Nagasaki, Japan) und DNV GL an der Entwicklung eines leichten Zwischendecks mit dem Ziel, das Gewicht gegenüber Stahl um 50 % zu reduzieren“, sagt Brevik. Daraus entstand ein 9 x 2 Meter großer GFK-Prototyp, der auf Stoß und maximale Belastungen getestet und dann auf der NOR-Shipping 2017 ausgestellt wurde.
Compocean hat diese Entwicklung nun auf ein neues Projekt mit Oshima, DNV GL und dem Reeder Masterbulk Pte Ltd. (Singapur) ausgeweitet, um ein 27 mal 12 Meter großes Prototyp-Zwischendeck aus Verbundwerkstoff in Originalgröße zu bauen, das im nächsten Jahr installiert wird und getestet bis Ende 2021.
„Oshima wollte Artikel optimieren, um Kraftstoff- und Handlingkosten zu senken“, sagt Brevik. „Obwohl es nicht viele Zwischendecks pro Schiff gibt, ist es ein einfacher Teil, wenn man neue Materialien einführt, da er nicht Teil der Primärstruktur des Schiffes ist.“ Das Design basiert auf einer mit Polyesterharz infundierten Glasfaserplatte mit darunterliegenden Hutversteifungen. „Wir verwenden eine Mischung aus ±45-Grad-, 0-Grad- und 0-Grad/90-Grad-Layup für alle Teile, jedoch in unterschiedlichen Verhältnissen. Außerdem muss die Decksstruktur viele Zurrpunkte integrieren, um die Ladung zu sichern.“ Die Platte wird mit einem Strukturkleber an die Hutversteifungen geklebt, während die Verschraubung in Kombination mit dem Zurrsystem verwendet wird. Eine verschraubte Stahlendhalterung verbindet den Verbundwerkstoff mit der Stahlschiffsstruktur. „Wir werden auch zukünftig eine Konstruktion mit reinen Klebeverbindungen verfolgen“, ergänzt Brevik.

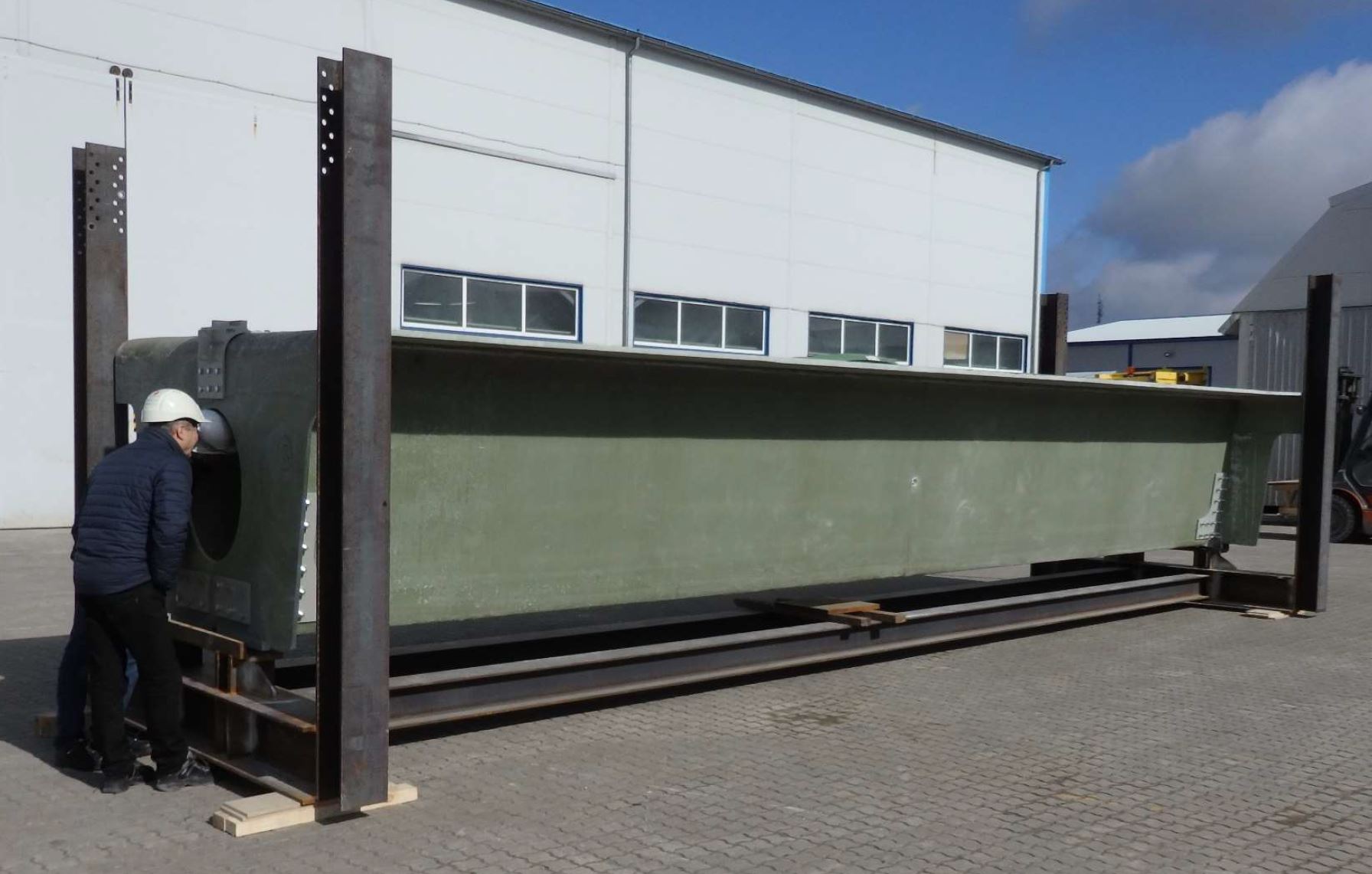
Abb. 2 Composite-Tween-Deck
Oshima Shipbuildings neues 65k-Stückgutfrachter-Design mit offener Luke wird das Prototyp-Zwischendeck aus Verbundwerkstoff von Compocean verwenden, das 50 % Gewicht gegenüber Stahl spart und aus mehreren infundierten GFK-Hutversteifungen (Einsatz) besteht, die mit einer FRP-Oberplatte mit Schraubverbindungen von verbunden sind den Verbund zur Stahlschiffskonstruktion. Quelle | Compocean und DNV GL
Nachdem Compocean die endgültige Genehmigung von DNV GL für das großmaßstäbliche Tween-Deck-Design erhalten hat, hat Compocean die Formen hergestellt und mit den Fertigungstests begonnen. „Das Verbunddeck in Originalgröße wird von einem Partner in Malaysia gebaut, der es per Lastkahn zum Schiff transportiert“, sagt Brevik. Der nächste Schritt besteht darin, eine deutliche Gewichtsreduzierung anzustreben, zum Beispiel durch Verbundluken über den Ladeöffnungen (flache Platten über den grünen „Kisten“ in der Schiffsdarstellung oben). „Bei dieser Art von Gepäckträger gibt es sieben große Lukendeckel“, bemerkt er. „Diese von DNV GL genehmigt zu bekommen, wird einige neue Herausforderungen mit sich bringen, aber der Erfolg mit dem Tween-Deck wird helfen.“
Leichter Aufbau, modulare Kabinen
RAMSSES hat sechs Arbeitspakete mit Schwerpunkt auf Verbundaufbauten und -komponenten, die über dem Hauptdeck verwendet werden, die meisten mit Demonstratoren und Testergebnissen, die 2020 präsentiert werden sollen. Das Arbeitspaket 16 unter der Leitung von Naval Group (Paris, Frankreich) demonstriert ein leichtes Verbundaufbaumodul mit einem Stahldeck verbunden. Der landgestützte Demonstrator stellt einen Standardblock für ein Offshore-Patrouillenschiff dar. „Der Schiffbau aus metallischen Werkstoffen basiert auf einer Blockbauweise, um Zeit und Kosten zu sparen“, erklärt Jurado. „Der Bau solcher Blöcke aus Verbundwerkstoffen wirft Probleme mit dem Bedarf an großen Formen sowie den Fügetechniken und den Sicherheitsanforderungen an die Verbindung auf. Fibreship hat dies untersucht und einige Empfehlungen zum Fügen von Blöcken auf Verbundbasis entwickelt, einschließlich der Montagereihenfolge.“ In RAMSSES hat die Naval Group drei Arten von Sandwichstrukturen untersucht, darunter GF/Polyester/Balsa-Kern, FR-Epoxid/PET-Schaumkern und GF/Polyester/3D faserverstärkter Schaumkern. Es entwickelt auch ein System zur Überwachung des strukturellen Zustands (SHM) innerhalb der Fugen- und Verbundplatten.
Das Arbeitspaket 18 unter der Leitung von Chantiers de l’Atlantique (Saint Nazaire, Frankreich) entwickelt eine modularisierte Lösung für Passagierkabinen. „Diese kommen in der Regel ohne Boden, weil sie auf die Stahldecks des Schiffes geschweißt sind“, sagt Krause. „Die Idee ist, sie aus Verbundwerkstoffen herzustellen, die mit allen Hilfssystemen wie Heizung und Luft, Elektrik usw solides Stahldeck, wodurch viel Gewicht gespart wird.“ Obwohl das Projekt Verbundwerkstoffe bewertet, um die Produktions- und Montagezeit für Wände, Decken und Badezimmer zu reduzieren, da der Austausch des Stahldecks schätzungsweise 125 Kilogramm pro Quadratmeter einsparen würde, liegt ein Hauptaugenmerk auf Verbundböden. Hutchinson (Paris, Frankreich) hat vorgeschlagen, seinen mineralfaserverstärkten Verbundschaumstoff ZALTEX zu verwenden, der Temperaturen von -190 °C bis 1.000 °C widersteht.
Auch das Arbeitspaket 13 unter der Leitung des Kreuzfahrtschiffbauers Meyer Werft (Papenburg, Deutschland) zielt auf effiziente Prozesse bei der Montage ab, zielt jedoch auf Schotten ab. . Das Ziel besteht darin, zwei Demonstratoren zu bauen – einen onshore, einen offshore (Erprobung) – wo Verbundwände mit Stahlrahmenkonstruktionen verbunden und dann 80 mechanischen Tests unterzogen werden. Der Projektpartner InfraCore hat Analysen durchgeführt, um die Anforderungen an Wärme- und Schalldämmung, Eigenfrequenz (Vibration), Verformung und maximale Breite und Höhe für Verbundwände zu definieren. „Wir wurden gebeten, multifunktionale Innen- und Außenwände zu entwickeln“, erklärt Morel von InfraCore. „Um Zeit, Kosten und Gewicht zu sparen, müssen wir Dämmung und einen guten Innenausbau in die Leichtbauplatte integrieren. Bis zu 6800 Quadratmeter dieser Wände gibt es auf jedem Kreuzfahrtschiff. Wir haben die Möglichkeit, diese Mitte 2020 an Bord eines Kreuzfahrtschiffes zu bringen, was die ersten SOLAS-zugelassenen Verbundwände auf einem Kreuzfahrtschiff weltweit sein könnten.“
In Arbeitspaket 10 entwickelt Podcomp (Öjebyn, Schweden) ein alternatives Indoor-/Outdoor-Paneel mit biobasiertem Verbundwerkstoffe, die feuerhemmend und preislich konkurrenzfähig sein müssen. Untersucht wurden drei Sandwichkonzepte auf Basis von GF/Polyfurfurylalkohol (PFA) Prepreg von Composites Evolution (Chesterfield, UK) und unterschiedlichen Kernmaterialien. Nur ein Konzept bestand die Konuskalorimeter- und andere Brandtests, die von den RISE Research Institutes of Sweden (Borås) durchgeführt wurden. Es wird jetzt gewichts- und kostenoptimiert.
Nach Versuchen mit Aluminium- und Rührreibschweißen geht Baltic Workboats (Nasva, Estland) nun mit Verbundwerkstoffen weiter, um vormontierte, versteifte Platten für das Deckhaus/den Aufbau von Aluminium-Arbeitsbooten zu entwickeln (Arbeitspaket 15). Das Paneeldesign, die Verbindung mit anderen Paneelen und mit dem Rest der Deckshausstruktur, Statikverfahren und Isolierungslösungen werden demonstriert, sowie Einbautechniken an Bord.
Eine weitere Lösung für leichte Aufbauten wird von BaltiCo (Hohen Luckow, Deutschland), einem Hersteller von Schiffsausrüstung, entwickelt, der ein neues Start-up hat, um komplette Boote mit robotergestützten Kohlefasern zu bauen, die um eine Fachwerkstruktur drapiert werden. „Man baut das Skelett der Struktur, die man herstellen möchte, setzt etwa jeden halben Meter GFK-Kreuzstrukturen oder -Rippen, um die dann ein Roboter Kohlefaser wickelt“, erklärt Krause. Das Ziel ist ein ultraleichtes Baukastensystem mit einem hochautomatisierten Prozess. Die Demonstration umfasst die Produktion und Montage von zwei selbsttragenden Rumpf- und Deckmodulen in einem leichten, solarbetriebenen Katamaran, der nicht von SOLAS stammt.
Geschweißte GFK-Stahlverbindungen
„Wir glauben, dass die Zukunft des Schiffbaus in der Kombination von FRP-Verbundwerkstoffen, Stahl und anderen Materialien zu Hybridstrukturen liegt“, sagt Dr. Lars Molter, ein 10-jähriger Veteran bei CMT. „Wir haben uns das Kleben angesehen, aber es gibt kein standardisiertes Fugendesign, das Sie auf allen Schiffen verwenden können, und es gibt keine allgemeinen Regeln für die Anwendung von Kleben in SOLAS-Schiffen. Außerdem müssen Sie die Umgebung und den Klebeprozess kontrollieren.“ Er stellt fest, dass dies inmitten des Schweißens und Schneidens, das typischerweise den Werftbau dominiert, schwierig ist. „Wir haben DNV GL gefragt, was sie für Verbindungen aus unterschiedlichen Materialien genehmigen würden“, sagt Molter. „Sie sagten, dass die Primärstruktur normalerweise eine mechanische Befestigung erfordern würde; reine Verklebung wäre ohne überflüssige Befestigungsmittel nicht leicht zu zertifizieren.“
Molter und CMT reagierten mit dem von Deutschland geförderten Projekt FAUSST (Fiber and Steel Standard Joint), das ein Hybridgestrick entwickelt hat, das von 100 % Glasfasern auf 100 % Stahlfasern übergeht. Letzteres wird mit einem Stahlverbinder (z. B. Flachblech, Rechteckprofil etc.) verschweißt, der dann einfach in eine Schiffsstahlkonstruktion eingeschweißt werden kann (Abb. 3). Das Glasfaserende wird mittels Harzinfusion mit der Verbundstruktur verbunden. „Dieses Verbindungsdesign bietet eine 100-prozentige NDT-Inspektion, da Sie UT (Ultraschall) oder Röntgen an der Schweißnaht verwenden können“, sagt Molter. FAUSST führte mechanische, Umwelt- und Ermüdungsprüfungen an diesem Verbindungstyp durch und erhielt auch die grundsätzliche Zulassung von den Klassifikationsgesellschaften, aber es war noch viel zu tun, um die Technologie in ein kommerzielles Produkt zu überführen. Daher verließ Molter CMT und gründete 2018 die HYCONNECT GmbH (Hamburg, Deutschland).
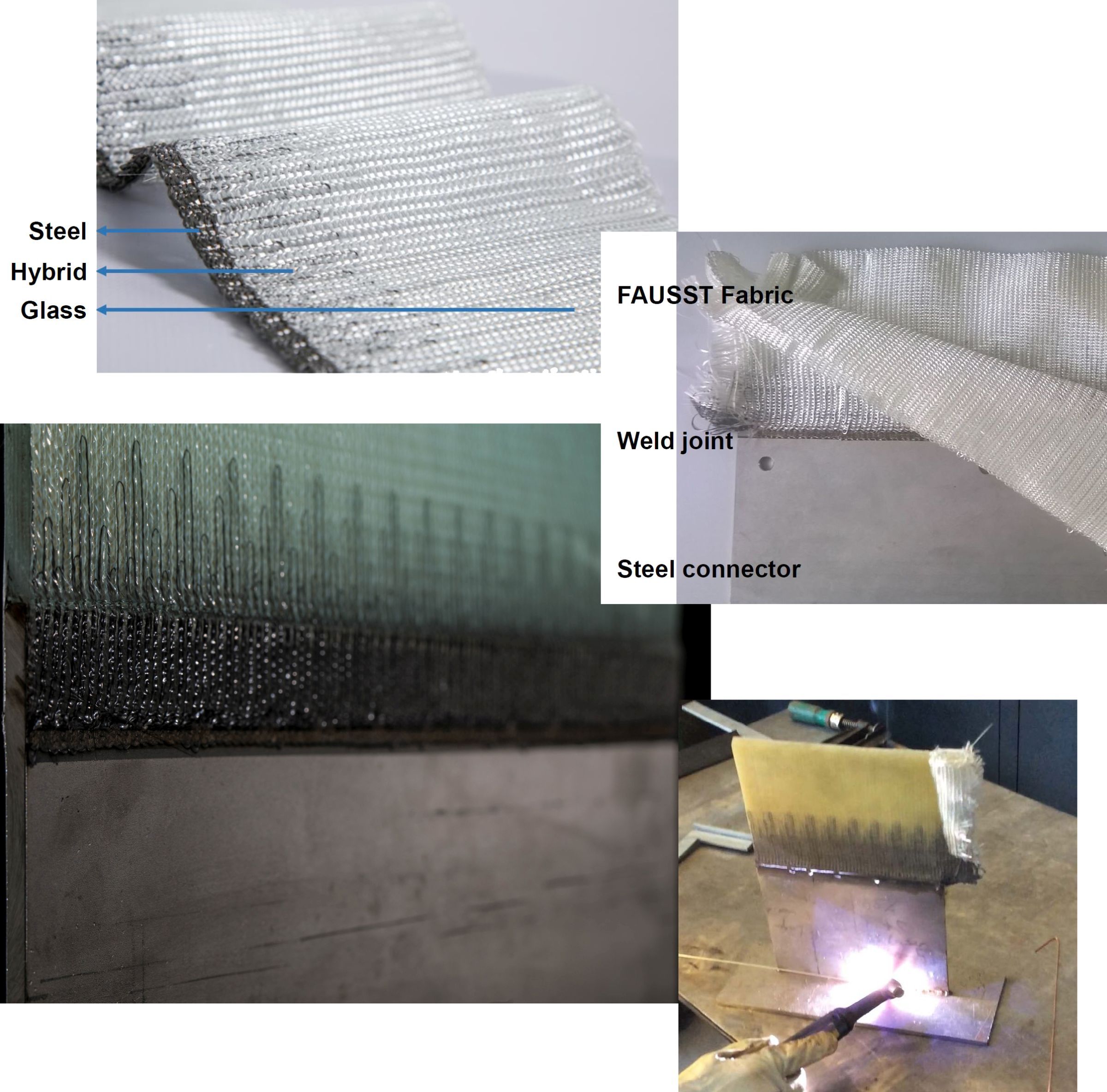
Abb. 3 HYCONNECT Stahl-GFK-Schweißverbindung
FAUSST Hybrid-Stahl-Glasfaser-Gewebe (oben links) wird an eine Stahlplatte oder einen anderen Verbinder pressgeschweißt (oben rechts) und kann dann durch Harzinfusion in eine Verbundstruktur integriert werden (unten links) . Solche hybriden Verbundstrukturen werden dann einfach in Stahlschiffsrahmen eingeschweißt (unten rechts) .
Quelle | HYCONNECT
„Wir haben uns mit Werften, DNV GL und BV getroffen und entwickeln ein zertifizierbares Produkt“, sagt Molter. „Sie bestellen einfach Ihre Verbundteile mit diesem Fügesystem und können sie dann in Ihr Schiff einschweißen. Das ist unsere Vision. Wir konstruieren die Verbund-Stahl-Verbindung und liefern dann ein Produkt, bei dem das Gewebe mit einem Stahlverbinder (Platte, Profil usw.) verschweißt ist.“
Er erklärt, dass die gemeinsame Konstruktion und das Gewebe in einem schrittweisen System zertifiziert werden:„Durch das Aufbringen von mehr Lagen FAUSST-Gewebe erhöht sich die Belastbarkeit linear.“ Als Basisprodukt könnten beispielsweise vier Lagen FAUSST mit einem daran angeschweißten 1 Meter langen Flacheisen, ausgelegt für eine bestimmte Zug- und Biegebelastung, sein. Then there would be some products available to the left (e.g., two-three layers total for a lower load rating) and right (e.g., six layers total for a higher load rating). “We are still finalizing these details, but the goal is a standardized and easy-to-use system,” notes Molter.
HYCONNECT has adapted the fabric technology to handle the difference in stiffness and coefficient of thermal expansion (CTE) between steel and composites; the use of knitted fibers for mechanical interlocking with unidirectional fibers for carrying load through the joint; and the technique required for high-quality press welding of the steel fibers to the steel connector (see "Connecting composites to steel”). “This solution is based on continuous testing,” says Molter. “Because FAUSST consists of standardized ready-made sub-products, it can be supplied quickly, within days.” Prototypes are currently being produced for selected customers, and HYCONNECT will begin full production in 2020.
Composite rudders
Ship rudders are also being developed as FRP-steel hybrids. As part of RAMSSES work package 12, Becker Marine Systems (BMS, Hamburg, Germany) is demonstrating a lightweight composite flap for a steel rudder designed for large container ships. Such rudders typically weigh more than 200 tons, says Jörg Mehldau, head of R&D at BMS. “By adding a hinged aft flap, you can significantly reduce the rudder area.” BMS pioneered this flap rudder, which dramatically reduces ship turning radius and improves course-keeping and maneuverability, enabling berthing without tugboat assistance. A composite flap not only reduces weight but also enables more functional shapes as well as more hydrodynamically- and load-optimized designs.
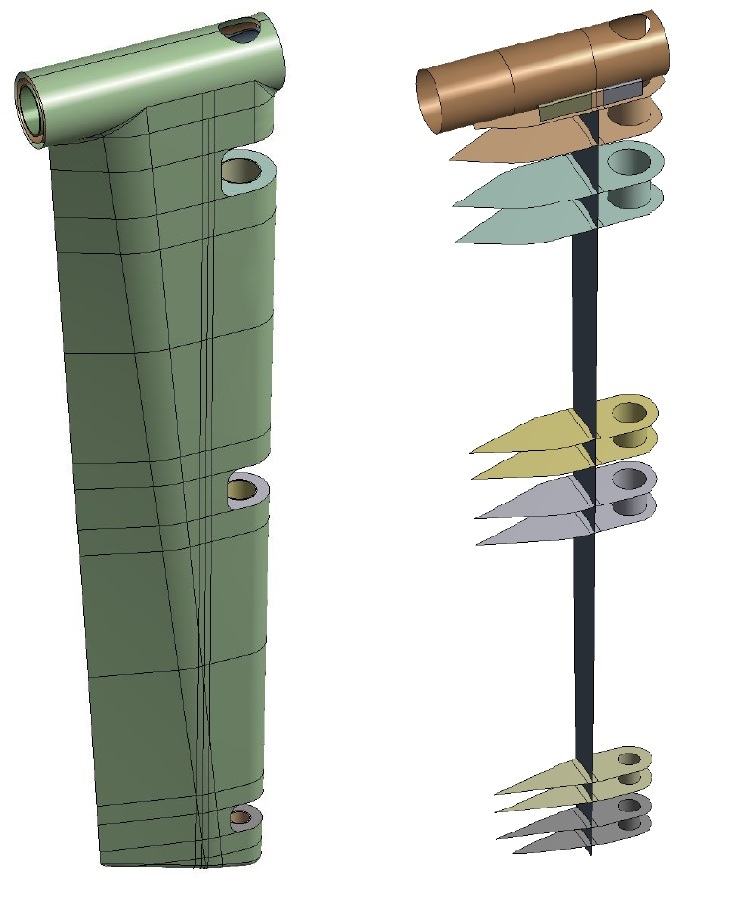
Fig. 4 Composite rudder flap
Becker Marine Systems is working with InfraCore to develop a lightweight, resin-infused rudder flap for the largest container ships. Measuring 11.8 meters long and 0.9 meter wide with a 2.9 meter chord, the full-scale flap must withstand 100 tons/m
2
of load. A 2-meter high demo will be tested 2Q 2020. Source| Becker Marine Systems
“The composite flap we are developing was inspired by the aviation industry,” notes Mehldau. For RAMSSES, the full-scale test case is aimed at one of the largest container ships (≈400 meters long), a flap measuring 11.8 longmeters and 0.9 meters wide with a chord of 2.9 meters (see Fig. 4). “We calculated the forces on this rudder and flap using formulas based on DNV GL rules for this ship’s type, weight and maximum speed,” says Mehldau. BMS then conducted preliminary design and engineering analysis, as well as trade studies for manufacturability and cost. “We first favored filament winding but it was too expensive,” he notes. “For each new ship hull, the rudder is a single design.” Thus, resin infusion was chosen, as was an alternative design from InfraCore. “It was the best for production flexibility, cost and structural performance combined,” Mehldau explains.
“To me, this was a natural fit for InfraCore because the composite lock gates we have built are very similar,” says Morel. He notes container ship rudders must withstand loads of roughly 100 tons per square meter with a surface area of 150 square meters. This matches well with InfraCore’s infusion-based technology used in bridge decks spanning up to 142 meters. Instead of bonding a high-density structural core to faceskins, InfraCore uses a low-density foam core only as a permanent formwork for multiple Z-shaped, two-flanged web structures. These are overlapped, faced with multiaxial fabrics and co-infused to form a robust construction. InfraCore will build a 1:6 scale demonstrator, using glass fiber and polyester resin materials already certified by DNV GL to keep costs low.
Morel notes that the reduced-weight InfraCore composite flap is cost-competitive, “because steel ship rudders are quite complicated to manufacture.” Mehldau agrees, “together with less maintenance and operational cost advantages, we see a successful business case.” The 2-meter -high demonstrator will be finished by 2Q 2020, followed by testing.
“We will test this using a lab test bench and air cushions, which can apply up to 8 bar of pressure equal to at least 80 Mpa of load,” says Mehldau. “We will measure strains and deflections to verify our simulations and perform a break load test.” A lab-scale demonstrator will also be tested via sea trials on a research ship in the Elbe River by CETENA (Genoa, Italy) which serves as project coordinator for RAMSSES along with CMT.
Forward momentum
“The outlook for composites in ships is good because many of the marine sector stakeholders have shown interest in FIBRESHIP, RAMSSES and other projects,” says Jurado. “The largest challenges are the need for new regulations, fire safety aspects, bonding techniques and reduction of shipbuilding costs.” For the latter, he cites automated manufacturing in shipyards as a key issue as well as mold construction and composite materials sourcing and storage. “Composites are already growing in ships,” says Krause at CMT, “but we started this work 20 years ago, so it is a slow process. However, we now have this critical mass and the industry is more connected via E-LASS.”
Jörg Bünker, head of R&D, application service for SAERTEX LEO FR products at SAERTEX (Saerbeck, Germany), agrees:“The drivers to reduce weight are strengthening. Within the next five to seven years, more composite materials will be sold into ships. This is the right time for more projects because IMO needs to see this interest and effort from the industry. Suppliers must show new solutions and shipyards must show where composites can be used, but no one can do it alone.”
Harz
- Schiff in einer Flasche
- Recycling:Endlosfaserverstärkte thermoplastische Verbundwerkstoffe mit recyceltem Polycarbonat
- Wie mobile Technologie Reisebarrieren beseitigt
- TxV Aero Composites erfüllt die AS9100-Standards
- Mikrosam automatisiert thermoplastische Verbundwerkstoffe mit einem werkzeuglosen Multi-Roboter-Bestückungssystem
- Hexcel arbeitet mit Lavoisier Composites, Arkema zusammen
- Kontinuierliche Faserherstellung (CFM) mit Moi-Verbundwerkstoffen
- Leichtbau-Gipfel:Ausrichtung auf Chancen für Automobilantriebe aus Verbundwerkstoffen
- Ashland arbeitet mit Velox für den Vertrieb von Verbundwerkstoffen in Frankreich zusammen
- 3D-Druckverbundwerkstoffe mit Endlosfasern