Kontinuierliche Faserherstellung (CFM) mit Moi-Verbundwerkstoffen
Endlosfaser-3D-Druck und -Abscheidung gewinnt an Bedeutung. Da die Zahl der Unternehmen, die sie verwenden und weiterentwickeln, wächst, wird diese Technologie zweifellos die Verbundwerkstoffindustrie prägen.
Erstens bietet es eine Herstellung ohne Formen oder Werkzeuge. Zweitens bietet es multifunktionale Strukturen (z. B. elektrische Leitfähigkeit, Formänderung, Sensorik). Drittens öffnet es die Tür zu einer Welt der hybridisierten Fertigung – z. B. Laminieren auf 3D-Druck und Fräsen während des Druckens – sowie eine nahezu endlose Landschaft der Materialentwicklung, von Fasern aus Nitinol-Formgedächtnislegierungen (SMA) bis hin zu leitfähigen Nanokompositlösungen für Liquid Deposition Modeling (LDM). Letzteres ist eine ganze Welt für sich, auf die ich in einem zukünftigen Blog zurückkommen werde.
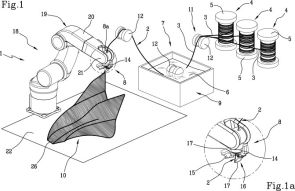
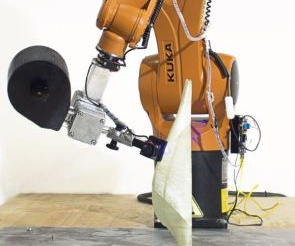
Patent WO2017085649A1 und Atropos Drucksystem. QUELLE:Moi-Composites.
Moi Composites wurde im Februar 2018 von der Materialingenieurin und Professorin Marinella Levi, dem Konstrukteur Gabriele Natale und dem Architekten Michele Tonizzo gegründet. 2013 begann Professor Levi am Politecnico di Milano (Mailand, Italien) mit dem 3D-Druck zu arbeiten. Bis 2014 gründete sie +LAB im Fachbereich Chemie, Werkstoffe und Verfahrenstechnik der Universität „Giulio Natta“. Ihre Vision war es, Forschung und Entwicklung, Lehre und Materialinnovation zu verschmelzen, indem sie Ingenieure, Designer, Forscher und Hersteller zu einem multidisziplinären, kollaborativen 3D-Druckzentrum zusammenführt.
2014 Erstes Werkzeug für den 3D-Druck von duroplastischen Endlosfaserverbundwerkstoffen 2015 Patent WO2017085649A1 2016 Partnerschaften mit Owens Corning und KUKA Robotics,Atropos Projekt- und Drucksystem 2017 JEC Innovation Award, Partnerschaft mit Autodesk,
Vizemeister des James Dyson-Preises,
Partnerschaft mit COMAU Automation
(Vollständige Zeitleiste)
„Wir haben mit moi composites angefangen, weil wir kommerzielle Teile produzieren und an internationalen Projekten beteiligt sein wollten“, erklärt Michele Tonizzo. „Wir haben festgestellt, dass es viel Markt gibt. Wir stellen biomedizinische Komponenten sowie Teile für Marine-, Öl- und Gas- sowie Luft- und Raumfahrtanwendungen her, hauptsächlich unter Verwendung von Glasfasern. Die CFM-Technologie ist in der Lage, einzigartige Lösungen herzustellen, die mit herkömmlichen Methoden unmöglich wären."
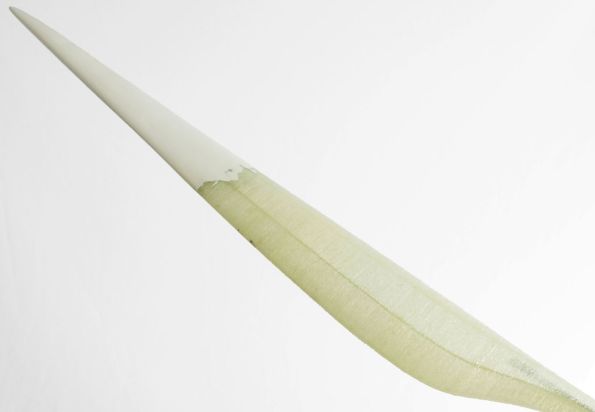
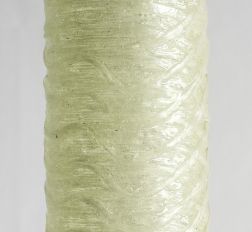
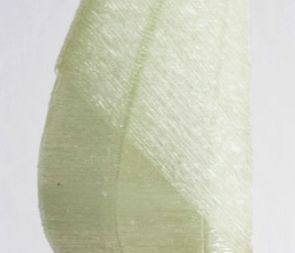
3D-gedrucktes Propellerblatt mit internem Strukturfachwerk aus Endlosglasfaser (oben). Dieses Projekt demonstrierte auch die Faserplatzierung entlang nichtlinearer Kurven (unten links) und ein kontinuierliches Faserlaminat mit traditionellen Faserorientierungen (z. B. 0°,+45 °, -45°, 90°, unten rechts). QUELLE:Moi-Composites
Sortiment an Harzen und Fasern
Atropos demonstrierte die Fähigkeit, diskontinuierliche und kontinuierlich faserverstärkte, duroplastische Polymere nicht nur Schicht für Schicht, sondern auch entlang nichtlinearer Kurven zu drucken. Es verwendete ultraviolettes (UV) Licht zum Aushärten der Polymere an Ort und Stelle. „Wir können derzeit mit UV-Härtung in Epoxid, Acryl und Vinylester drucken“, sagt Tonizzo. Er stellt fest, dass Acryl gut für Architekturteile geeignet ist, da es klar ist und keine Temperatur zum Aushärten/Nachhärten benötigt. Vinylester wird für Schiffsteile und Epoxid für Öl- und Gas- und Luft- und Raumfahrtteile verwendet.
„Bei einigen Anwendungen ist die UV-Härtung nur der Anfangsschritt und wir härten dann mit konventioneller Erwärmung nach“, beobachtet Tonizzo. „Wir sind nicht an die UV-Härtung gebunden. Wir haben mit nicht UV-härtenden Polymeren gedruckt und wissen, dass wir für Anwendungen mit höheren Eigenschaften andere Matrixoptionen benötigen.“ Als Referenz:Die Glasübergangstemperatur (Tg) ihres am häufigsten verwendeten Harzes, eines Vinylesters, liegt bei etwa 140 °C.
„Wir arbeiten auch mit Kohlefaser, aber nicht mit UV-härtenden Harzen“, sagt Tonizzo. Er weist darauf hin, dass sowohl Fasertransparenz und Farbe beeinflusst UV-Härtung. „Das Problem mit Kohlenstoff ist, dass es undurchsichtig ist und Schwarz. Dies ist die schlechteste Kombination. Wir wollen die beste Lösung für den Werkstoff Kohlefaser entwickeln, nicht nur die einfachste Technologie, die funktioniert. Es gibt viele andere Optionen für Härtungsmaterialien, die wir verwenden können, also untersuchen wir diese.“
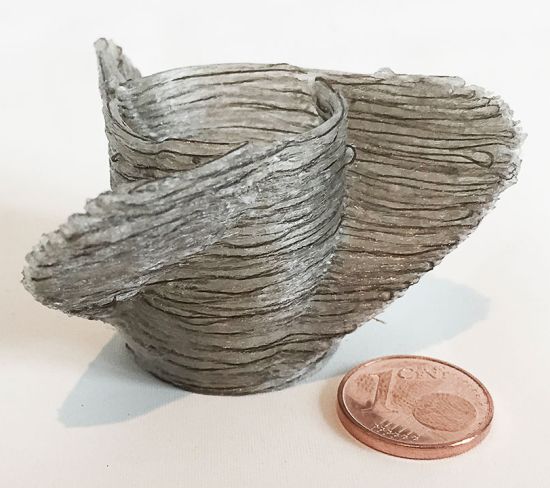
Moi-Verbundwerkstoffe können Drucken Sie kontinuierliche leitfähige Fasern für elektrische/thermische Funktionalität, Sensorik, Formänderung usw. QUELLE:Moi-Verbundwerkstoffe.
Moi Composites hat Endlosglasfasern bis zu 2400 tex (207 yd/lb mit einem maximalen Durchmesser von 24 μm gemäß einem Owens Corning-Datenblatt) gedruckt und testet Naturfasern. Es ist auch mit Basaltfasern bedruckt. „Wir können mit UV-Härtung und Basaltfaser sehr gut drucken, weil sie eigentlich etwas transparenter und brauner als schwarz ist“, erklärt Tonizzo.
Auch Fasern, die elektrischen Strom leiten, können in der CFM-Technologie verwendet werden. Sie können nach Bedarf in der zu druckenden Struktur platziert werden. Eines der auf der +LAB-Website aufgeführten Projekte zeigt Nitinol-Fasern, eine Legierung mit Gedächtnisform. „Damit konnte man formverändernde Strukturen herstellen“, sagt Tonizzo. „Sie könnten es zum Beispiel verwenden, um Spannungen auf andere Fasern abzubauen, wie in Spannbeton.“
3D-Druck als Teil der Hybridfertigung
Atropos verwendet einen Kuka-Roboterarm mit einem Druckumschlag von 0,5 x 0,5 x 0,5 m Höhe. „Wir drucken jetzt auf einem Comau-Roboter mit einem 1,0 x 0,5 x 0,8 m hohen Umschlag, dem System der zweiten Generation“, sagt Tonizzo. „Wir haben auch größere Roboter mit Drehtischen und Bauvolumen von 1,5 x 1,5 x 1 m Höhe eingesetzt und bewiesen, dass unsere Technologie leicht skalierbar ist.“
Moi entwickelt auch einen All-in-One-Druckkopf der dritten Generation mit einem System zum Ausüben von Druck auf die Fasern, Sensoren, Schneidmechanismen und das Fräswerkzeug. Laut Tonizzo wird dies die Lücke zwischen 3D-Druck und automatisierter Faserplatzierung (AFP .) schließen ). „Der 3D-Druck erreicht nicht die Leistung von AFP, aber CFM bietet mehr Flexibilität. Wir können bereits mit Fasern mit einer Dicke von 0,25 mm drucken und haben die Möglichkeit, Kurven zu erzeugen und Endlosfasern in die ideale Position zu bringen“, fügt er hinzu.
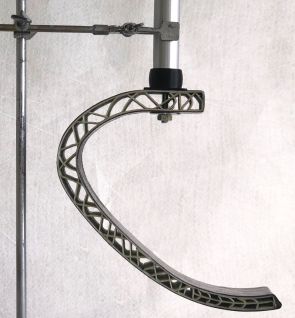
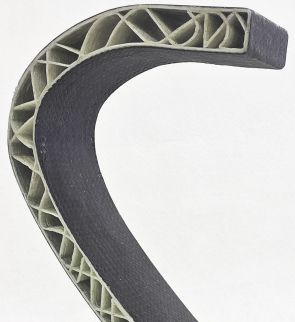
SuPeRIOR ist a Unterschenkelprothetik optimiert für minimales Gewicht, Durchbiegung und Kosten.
Der 3D-gedruckte Strukturkern wurde dann mit Kohlefaser und Epoxidharz laminiert, gefolgt von VBO-Härtung. QUELLE:Moi-Composites.
„Der 3D-Druck sollte für das eingesetzt werden, was er am besten kann“, sagt Tonizzo, „wozu auch die Optimierung des Arbeitsflusses gehört. Sie können beispielsweise einen internen Kern mit Hinterschneidungen und intelligenten Faserrichtungen in 3D drucken. Sie verwenden dann die übliche Handlaminierung und härten im Autoklaven oder nur mit Vakuumbeuteln aus.“ Er beschreibt ein Teil, das konventionell mit einer Form nicht hergestellt werden konnte. „Wir haben den inneren Kern gedruckt und dann in Laminat gewickelt und im Autoklaven mehrere Stunden bei 110 °C und 2 bar Druck ausgehärtet. Das Teil ist super geworden.“ Dieser Teil unterliegt einer Geheimhaltungsvereinbarung, daher sind keine weiteren Details bekannt, aber moi hat die SuPeRIOR-Prothetik auf ähnliche Weise hergestellt, nicht im Autoklaven, sondern nur mit Vakuumbeutel (VBO) ausgehärtet. „Alle Einbauten verwenden eine durchgehende Glasfaser“, erklärt er, „aber das äußere Laminat besteht aus handlaminiertem Kohlefasergewebe und Epoxidharz.“ Das gesamte Design reduziert die Durchbiegung und erhöht die Anpassung, während die Kosten und die Produktionszeit erheblich reduziert werden.
Voxel-basierte Optimierungssoftware
Tonizzo erklärt, dass der Teilekonstruktionsprozess den Voxel-basierten Algorithmus von Autodesk mit den Algorithmen von moi zur Spannungs- und Pfadoptimierung kombiniert. Daraus ergibt sich der optimierte Faserverlauf für die Struktur. Die Software arbeitet auch, um den bestmöglichen Herstellungsweg zu wählen. „Dies ist ein iterativer Prozess“, sagt Tonizzo. „Das Design ist nicht vollständig automatisiert wie das generative Design. Es braucht immer noch Ingenieure, um Entscheidungen zu treffen. Aber ich denke, so sollte es sein – der Designer und die Software kombiniert, nicht nur KI allein.“
Multimaterial-Zukunft, starkes Marktpotenzial
In einem der Bilder vom Atropos-Druckpropellerblatt gibt es eine Nahaufnahme, die ein fast gewebtes Muster zeigt. „Das ist nicht wirklich gewebt, aber es wird bald möglich sein“, sagt Tonizzo. Er verweist mich auf das Sinuswellen-Projekt auf der +LAB-Website. „Die gezeigten Demonstratoren sind 3D-gedruckt in Kunststoff mit kurzen Fasern und dem LDM-Verfahren [Liquid Deposition Modeling], während sie am +LAB forschten. Die Algorithmen, die wir damals verwendeten, sind dieselben, die wir jetzt mit Endlosfasern vorantreiben.“
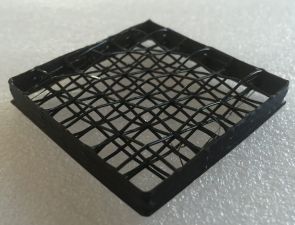
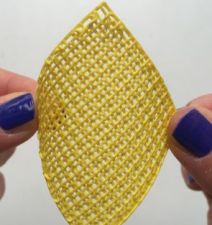
+LABs Sine Wave demonstriert 3D-gedruckte Polymer-Füllmuster mit einstellbarer elastischer Reaktion. QUELLE:+LAB.
Auf der +LAB-Website wird deutlich, dass Materialinnovationen und Möglichkeiten für diese Druckart nahezu unbegrenzt sind. Die Frage ist, was die meisten Chancen und Potenziale für stark nachgefragte Lösungen bietet. Unterdessen unterstützen Materiallieferanten die Weiterentwicklung. Owens Corning ist beispielsweise daran interessiert, Glasfaser mit mehr Matrizen wie Keramik und Beton zu demonstrieren. Dies ist natürlich für Bauanwendungen sehr interessant und könnte angesichts der aktuellen Trends zur digitalen Fertigung und energieeffizienten Bauen, Offsite-Fertigmodulen und verbesserter Nachhaltigkeit durch natürliche und recycelte Materialien, die allesamt auf Leichtbau setzen, erhebliches Potenzial haben. „Die Abteilung Giulio Natta am Politecnico di Milano ist in einem EU-Projekt zum Drucken von Geopolymeren, die sich wie Beton verhalten“, fügt Tonizzo hinzu. „Sie härten mit der Zeit von selbst aus, haben aber während des Druckens die Konsistenz wie Ton, um einen besseren Fluss zu erzielen. Wir werden auf jeden Fall in diesem Bereich weiterarbeiten, ebenso wie mit neuen Polymeren und Fasern.“
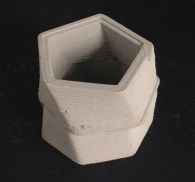
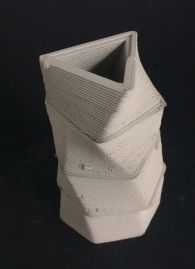
Moi-Composites is auch Drucken mit Geopolymeren, die sich wie Beton verhalten.
QUELLE:+LAB.
Werden Sie Maschinen verkaufen? „Ja, aber in Zukunft“, sagt Tonizzo. „Im Moment produzieren wir Teile und bringen die Technologie zum Kunden, wobei wir unser Know-how, unseren Druckkopf und unsere Software nutzen, um Teilelösungen nach Bedarf zu realisieren.“ Er fügt hinzu, dass moi composites im vergangenen Jahr daran gearbeitet hat, die Technologie mit CFM-Early Adopters zu verbessern und den Geschäftsszenario für viele verschiedene Teile in verschiedenen Märkten zu demonstrieren, und nun nach Investoren suchen, um CFM-Maschinen und -Prozesse für kommerzielle Marktchancen weiter zu skalieren.
Harz
- 3D-Druck-Montagevorrichtungen mit Markforged-Verbundwerkstoffen
- Additive Fertigung mit Verbundwerkstoffen in der Luft- und Raumfahrt und Verteidigung
- Bewertung einer Lieferkette für Verbundwerkstoffe im Wandel
- Vermarktung von UV-härtbaren Duroplasten für den Endlosfaser-3D-Druck
- Verbundstoffrecycling – keine Ausreden mehr
- Die kontinuierliche Faserherstellung verwischt die Grenze zwischen 3D-Druck und AFP
- Covestro bringt Maezio Endlosfaser-Thermoplaste auf den Markt
- 3D-Druckverbundwerkstoffe mit Endlosfasern
- Severstal investiert in Robotik, um die Herstellung fortschrittlicher Verbundwerkstoffe mit Airborne zu automatisieren
- GE Digital:Operational Insights with Data &Analytics