Verbinden von Verbundwerkstoffen mit Stahl
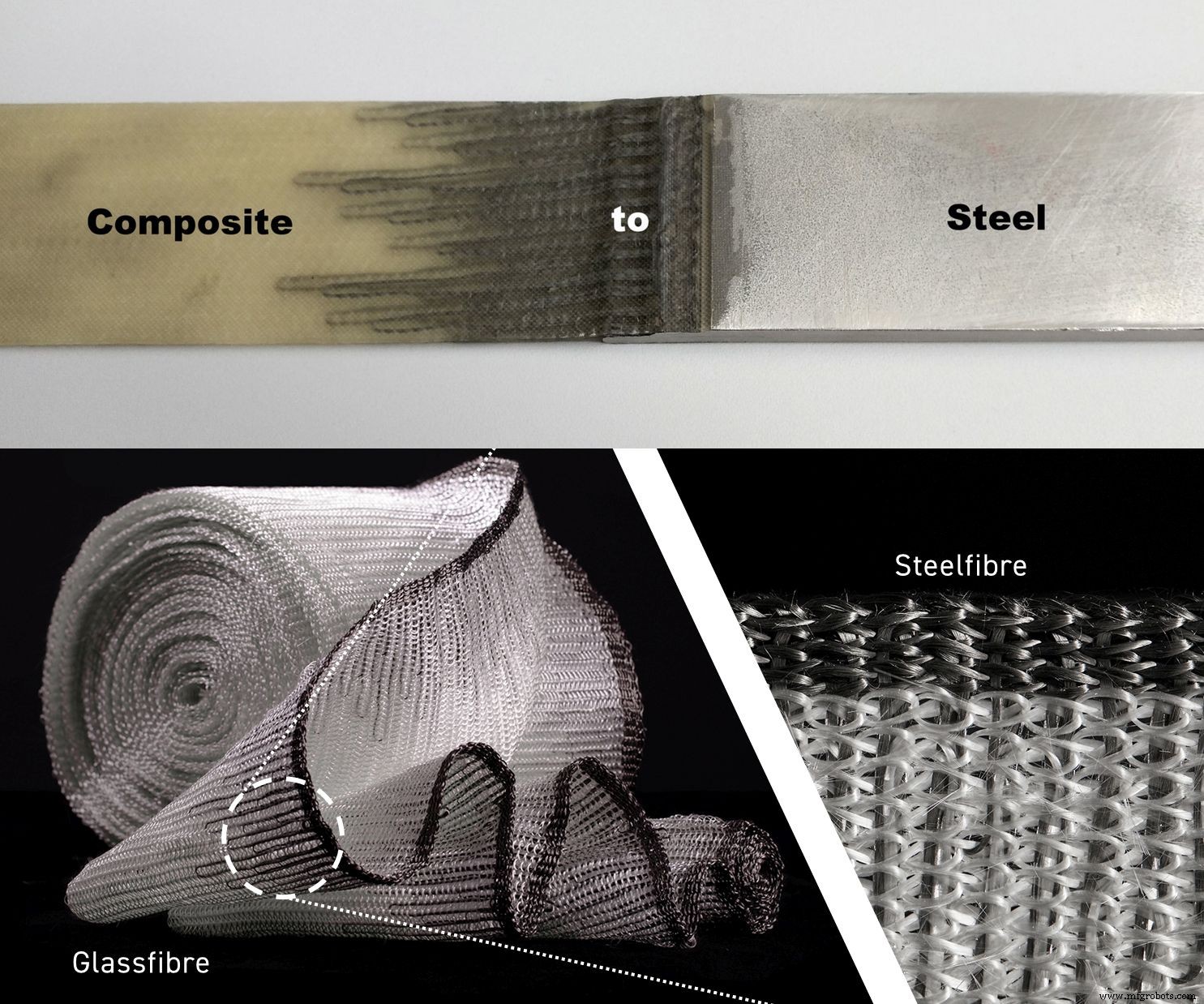
Dieser Blog ist ein Begleitartikel zu meinem Feature-Artikel vom Dezember 2019 „Beseitigung von Hindernissen beim Leichtbau von Schiffen mit Verbundwerkstoffen“, der einige weitere Details und Bilder enthält.
Die HYCONNECT GmbH (Hamburg, Deutschland) ist ein Startup, das von Dr. Lars Molter, einem Schiffsarchitekten und 10-jährigen Veteran des Center of Maritime Technologies (CMT, Hamburg, Deutschland), gegründet wurde, einem Forschungs- und Entwicklungszentrum der deutschen maritimen Industrie. „Die deutschen Firmen, die Megayachten und Kreuzfahrtschiffe bauen, haben alle das gleiche Problem“, sagt Molter. „Ihre Kunden möchten mehr Ausstattung, ein weiteres Deck, mehr Schall- und Temperaturisolierung oder neue Designmerkmale wie geschwungene Formen und integrierte Beleuchtung hinzufügen. Auch wenn diese Konstruktionen mit Aluminium oder Stahl möglich sind, ist dies sehr zeit- und kostenintensiv.“
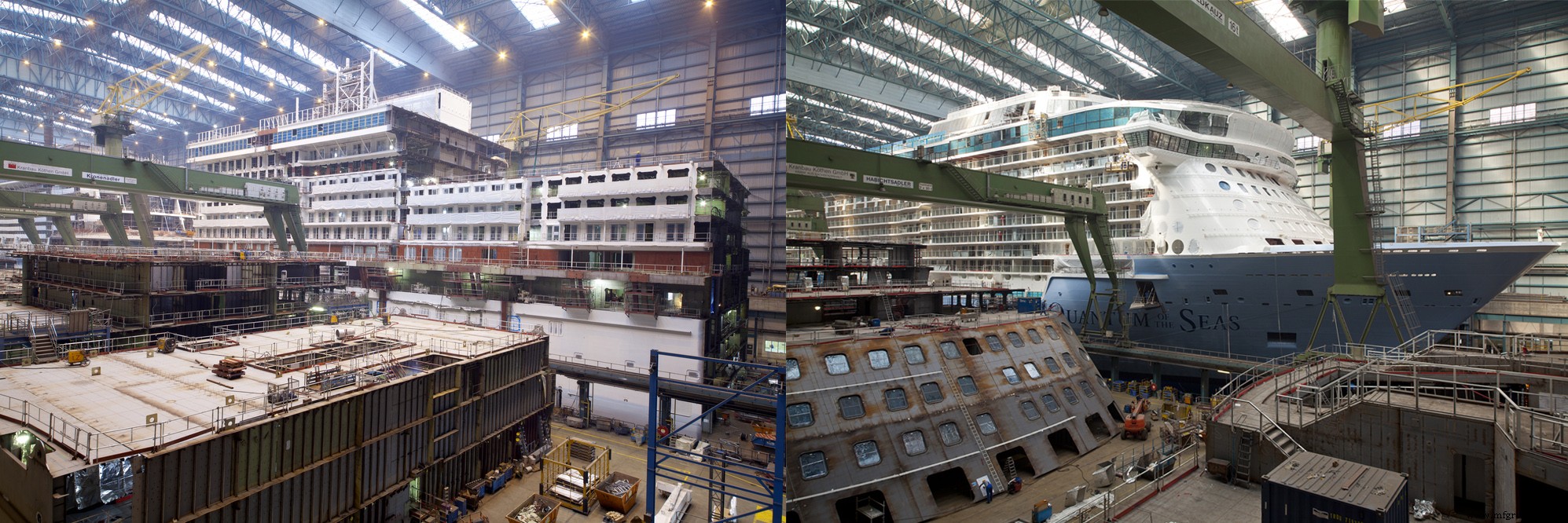
Schiffe werden normalerweise in Blöcken aus geschweißten Stahlkomponenten gebaut, um eine schnellere Montage zu ermöglichen, wie hier gezeigt. Das FAUSST-Verbindungssystem ermöglicht das Einschweißen großer Verbundwandpaneele oder anderer Konstruktionen in diese Stahlskelettbauweise und bietet so Leichtbauweise nach gängigen Schiffsbaumethoden. QUELLE | Meyer Werft
Probleme beim Kleben in Hybridstrukturen
Molter und viele andere können die Vorteile erkennen, die Verbundwerkstoffe für Schiffe bieten können, aber derzeit werden Schiffe aus Stahl gebaut. Es gibt viele, die an der Entwicklung von Schiffen aus reinem Verbundwerkstoff arbeiten, aber inzwischen besteht eine große Chance, Schiffsgewicht und Emissionen mit einer Vielzahl von Verbundkomponenten zu reduzieren. Ein Problem ist jedoch, wie sie mit dem Stahlgerüst des Schiffes verbunden werden. „Wir haben uns das Kleben angeschaut“, erklärt er, „aber es gibt kein standardisiertes Fugendesign, das auf allen Schiffen verwendet werden kann, und es gibt keine allgemeinen Regeln für die Anwendung von Kleben in SOLAS.“
Die von der International Maritime Organization (IMO, London, Großbritannien) herausgegebenen Vorschriften zur Sicherheit des Lebens auf See (SOLAS) verlangten, dass Handelsschiffe bis 2002 aus Stahl gebaut werden, als MSC/Circ. 1002 wurde ausgestellt und erlaubte alternative Designs. Diese Alternativen erfordern jedoch die Durchführung einer Risikoanalyse, die zeigt, dass die alternative Konstruktion und Konstruktion Stahl gleichwertig ist – ein Prozess, der langwierig, teuer und für jedes gebaute Schiff maßgeschneidert ist.
„Wir haben DNV GL gefragt, was sie für Verbindungen aus unterschiedlichen Materialien genehmigen würden“, sagt Molter. „Sie sagten, dass die Primärstruktur normalerweise eine mechanische Befestigung erfordern würde; reine Verklebung wäre ohne überflüssige Befestigungsmittel nicht ohne weiteres zu bescheinigen.“ Diese Probleme mit maßgeschneiderten Zertifizierungs- und Regulierungsbehördenanforderungen für redundante Befestigungselemente im Vergleich zu rein geklebten Primärstrukturen sind in Verkehrsflugzeugen identisch vorhanden. „Außerdem müssen Sie beim Kleben die Umgebung und den Prozess kontrollieren“, sagt er und stellt fest, dass dies inmitten des Schweißens und Schneidens, das typischerweise den Werftbau dominiert, schwierig ist.
FAUSST-Gelenke
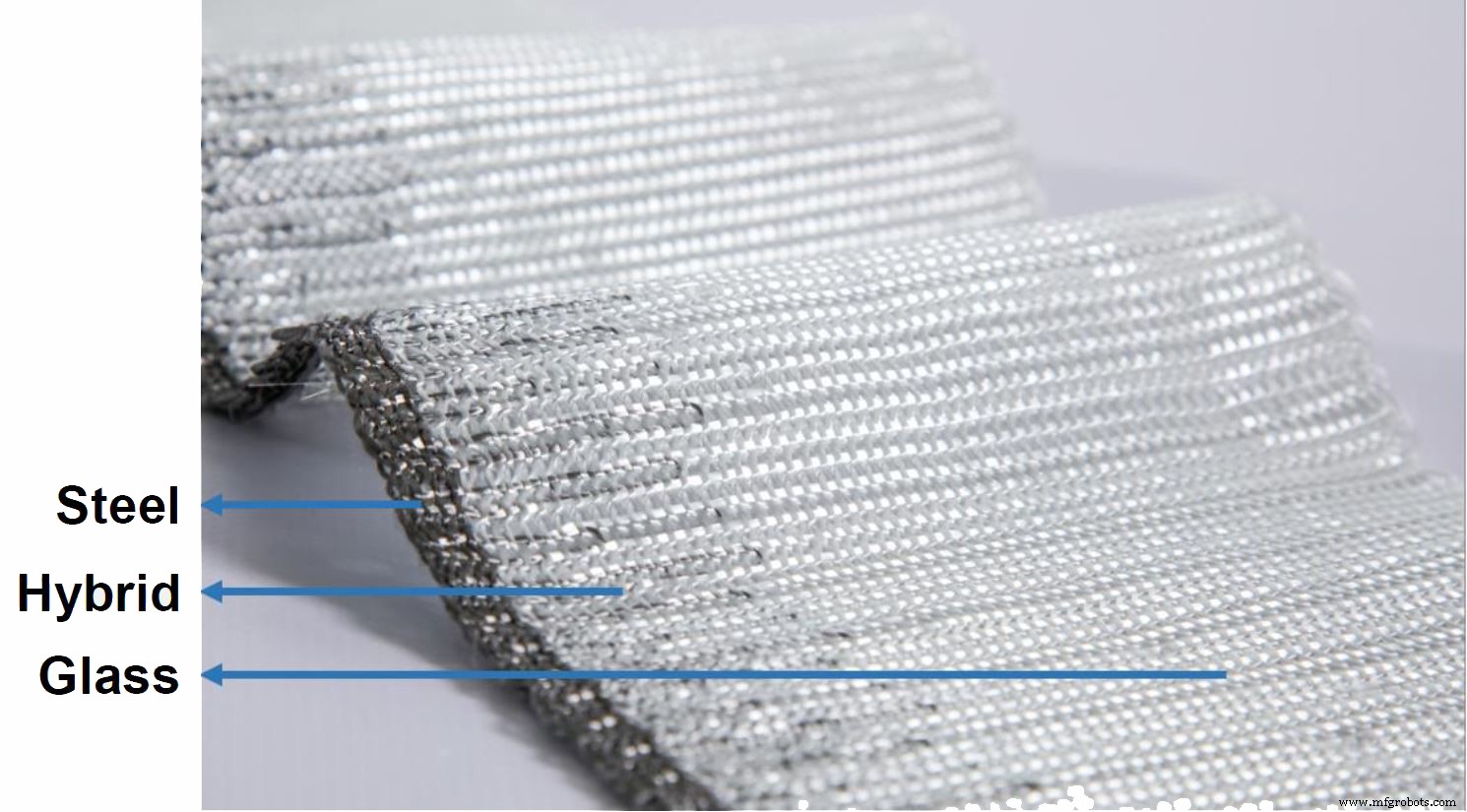
FAUSST Hybridgewebe aus Glasfaser und Stahlfaser. QUELLE | Hyconnet
„Wir brauchten also eine No-Bond-Lösung mit mechanischer Befestigung“, sagt Molter. „Wir haben uns immer gefragt, wie wir Fasern mit Metall verbinden?“ CMT würde dies im von Deutschland geförderten Projekt FAUSST (Fiber and Steel Standard Joint) beantworten, das in Zusammenarbeit mit Fritz Moll Textilwerke (Altshausen, Deutschland) ein hybrides Kettenwirkgewebe entwickelt hat, das von 100 % Glasfasern zu 100 % Stahl übergeht Fasern.
Die Gewebearchitektur ist so ausgelegt, dass sich die Stahl- und Glasfasern mäandern und überlappen, wodurch eine Lastübertragung durch Reibung sowie eine Verzahnung an den Kreuzungspunkten erreicht wird. Diese Architektur gleicht auch gestricktes Gewebe für die mechanische Verzahnung mit unidirektionalen Fasern aus, um die Last durch die Verbindung zu tragen. Der Stoff wird mit einer elektronisch gesteuerten Strickmaschine mit Geschwindigkeiten von bis zu 100 Metern/Stunde hergestellt.
Im nächsten Schritt wird dieser an einem Metallverbinder befestigt, der eine Platte oder ein Hohlprofil sein kann. Die Stahlfasern werden mittels Widerstandsnahtschweißen (Pressschweißen) mit einem großen Kupferelektrodenrad mit dem Stecker verschweißt. Molter erklärt, dass dies wie das Punktschweißen in der Automobilindustrie ist, jedoch darauf ausgelegt ist, eine lange, kontinuierliche Naht zu erzeugen. Dieses Verfahren ermöglicht die effiziente Herstellung von FAUSST-Steckverbindern mit einer oder mehreren Gewebelagen in einem robusten und bekannten Verfahren.
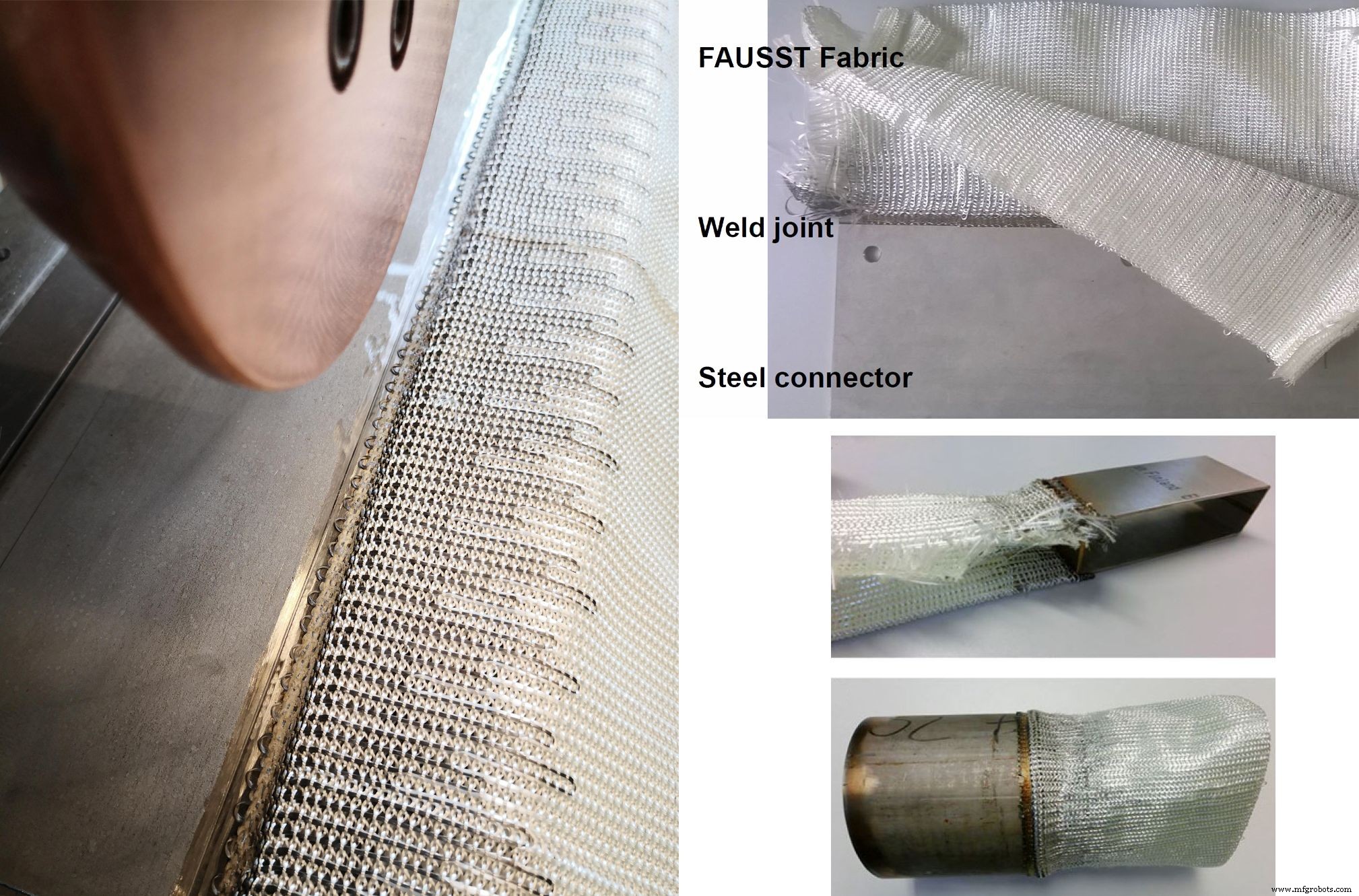
Hyconnect verwendet Nahtschweißen, um FAUSST-Gewebe mit Stahlverbindern zu verbinden. QUELLE | Hyconnect.
Das vertreibt HYCONNECT:das mit einem Stahlverbinder verschweißte Gewebe. „Eine Werft oder ihr Lieferant von Verbundstrukturen entscheidet sich für unser gemeinsames System“, erklärt Molter. „Sie geben die Fugenbelastung und die Art des Stahlverbinders vor und wir konstruieren und produzieren dann die FAUSST-Verbindung. Das liefern wir und sie gießen es dann in ihre Verbundstrukturen ein und die Werft schweißt diese dann in das Stahlgerüst des Schiffes ein.“
Steifigkeits- und CTE-Mismatch managen
Beim FAUSST-Hybridgewebe besteht ein Steifigkeits-Mismatch zwischen den Stahl- und Glasfasern. Molter erklärt, dass dies durch die Art und Weise, wie das Gewebe hergestellt wird, etwas abgemildert wird, „unter Verwendung von 5-7 Lagen, in denen Garne miteinander verbunden sind, und wir variieren, wie weit die Stahlfasern in das Glasfasergewebe hineinragen. Sie möchten keine großen Spitzen bei der Lastübertragung. Wir können die Steifigkeit modifizieren, indem wir diese Schichten und ihre Faserbestandteile modifizieren, zum Beispiel den Anteil und die Richtung von Glasfasern usw.“ Zusätzliche ± 45°-Fasern können hinzugefügt werden, um höhere Scherspannungen zu bewältigen und helfen auch, die unterschiedlichen Wärmeausdehnungskoeffizienten (WAK) zwischen dem Stahlverbinder und dem Glasfaserverbundstoff zu bewältigen. „Wir können auch für höhere Belastungen oder spezielle Konstruktionen konzipieren, indem wir mit getufteten Fasern durch die Dicke verstärken“, erklärt Molter.
Auch der Dickenunterschied zwischen dem Stahlverbinder und dem faserverstärkten Kunststoff (FRP) muss angegangen werden. „Die neutrale Achse beider Materialien muss ausgerichtet sein“, sagt Molter. „Dies wird normalerweise erreicht, indem die Kante des Stahlverbinders auf einen 30°-Kegel bearbeitet wird, wodurch praktisch eine Kegelverbindung für eine effiziente Lastübertragung auf das FRP entsteht.“
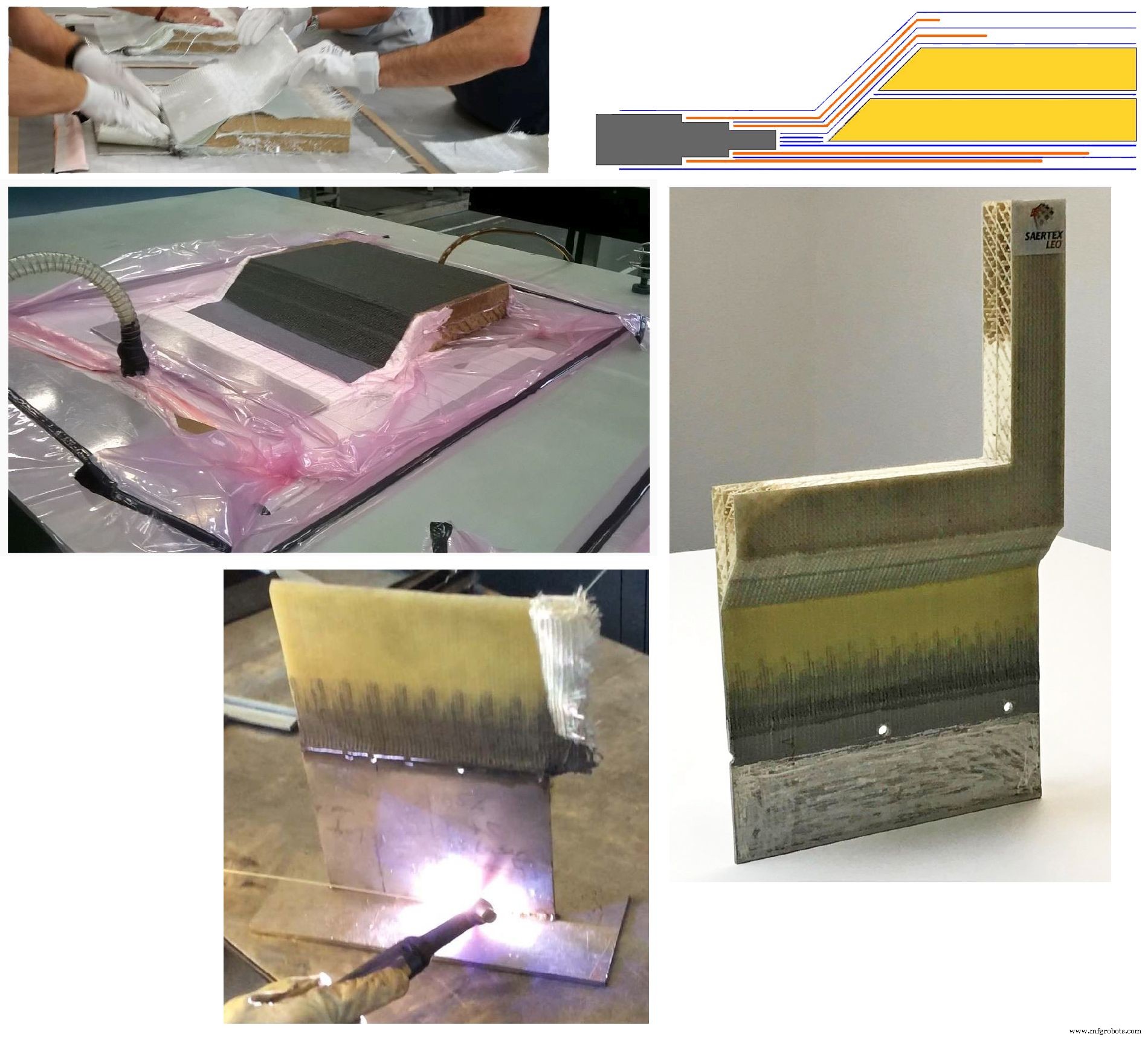
Hyconnect entwirft und produziert FAUSST-Verbindungen, die dann in Verbundstrukturen eingegossen und schließlich in einen Schiffsstahlrahmen eingeschweißt werden. QUELLE | Hyconnect.
Entwicklung eines standardisierten Gelenksystems
Molter verließ CMT und gründete 2018 HYCONNECT, um die FAUSST-Verbindungstechnologie zu kommerzialisieren. Das Unternehmen hat mit einer Vielzahl von Industriepartnern und Regulierungsbehörden zusammengearbeitet, um Tests durchzuführen und gemeinsame Designs zu wiederholen. Ziel ist es, eine „Familie“ von FAUSST-Gelenkprodukten zu entwickeln. „Durch das Aufbringen von mehr Lagen FAUSST-Gewebe erhöht sich die Tragfähigkeit linear“, erklärt Molter. „Ein Grundprodukt könnten also vier Lagen FAUSST sein, an die ein 1 Meter langer Flachstab angeschweißt ist, der für eine bestimmte Zug- und Biegebelastung ausgelegt ist. Dann wären links einige Produkte verfügbar, die zwei oder drei Schichten für eine niedrigere Tragzahl verwenden, und einige rechts, z. B. fünf oder sechs Schichten für eine höhere Tragzahl. Wir sind noch dabei, diese Details zu finalisieren, aber das Ziel ist ein standardisiertes, einfach zu bedienendes System.“
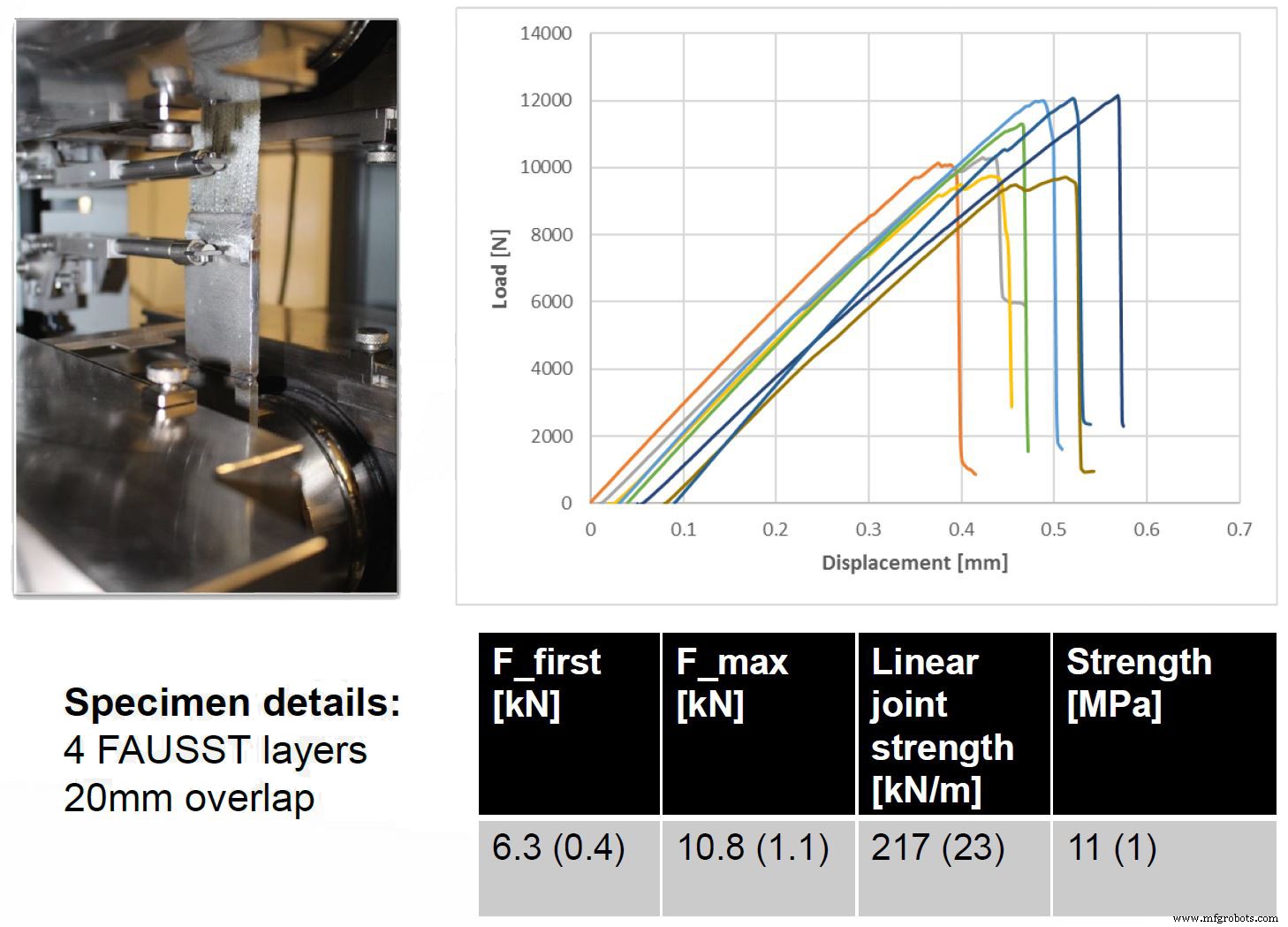
Die Hyconnect-Prüfung von Fugen aus vier Lagen FAUSST-Gewebe ergibt eine Festigkeit der Linerfuge von 217 kN/M. QUELLE | Hyconnect.
Die mechanische Charakterisierung der FAUSST-Verbindungsprodukte ist noch in Arbeit, Molter weist jedoch darauf hin, dass sie mit Klebeverbindungen konkurrenzfähig sind. „Außerdem ermöglichen sie eine 100-prozentige Prüfung der Schweißnaht mit Ultraschall oder Röntgen“, fügt er hinzu. Derzeit werden Prototypen für ausgewählte Kunden hergestellt und im Jahr 2020 skaliert.
Inzwischen hat HYCONNECT auch Interesse von Automobilunternehmen und Herstellern geweckt, die sich für Bahnanwendungen interessieren. „Bei Metalleinlegern besteht Potenzial, diese Technologie einzusetzen und auch im Hochbau sehen wir Einsatzmöglichkeiten“, sagt Molter. „Immer mehr Branchen erkennen den Wert hybrider Strukturen und die Möglichkeit kurzer Montagezeiten mit vorgefertigten Halbzeugen.“
Faser