Kordsa arbeitet mit Ford Otosan an der Entwicklung von Verbundblattfedern für schwere Lkw
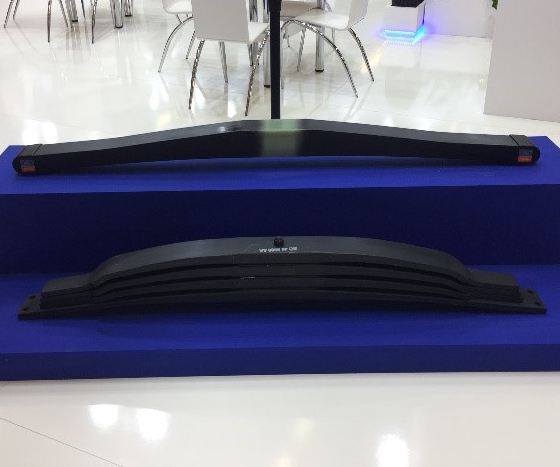
Kordsa (Istanbul, Türkei) ist ein globaler Anbieter von Reifen- und Konstruktionsverstärkungen und -technologie für Verbundwerkstoffe, der kürzlich seine Luft- und Raumfahrtkapazitäten durch den Erwerb mehrerer US-amerikanischer Unternehmen erweitert hat (siehe Jeff Sloan's Blog „The Kordsa Strategy“). Das Unternehmen erweitert auch sein Angebot im Automobil- und Schwerlastverkehr, wie seine Präsentation auf dem Composite Summit von Turk Kompozit 2019 (10.-12. Oktober, Istanbul) mit dem Titel „Kordsa’s Material Development for Composite Leaf Spring Production for Heavy Commercial Vehicles“ zeigt. In dieser Präsentation wurde eine von Kordsa und Ford Otosan gemeinsam entwickelte Technologie diskutiert, die die Chassissysteme schwerer Lkw für Ford Trucks leichter macht und Systeme zur strukturellen Zustandsüberwachung zur Prozessoptimierung, Teilequalifizierung und Online-Zustandsüberwachung umfasst.
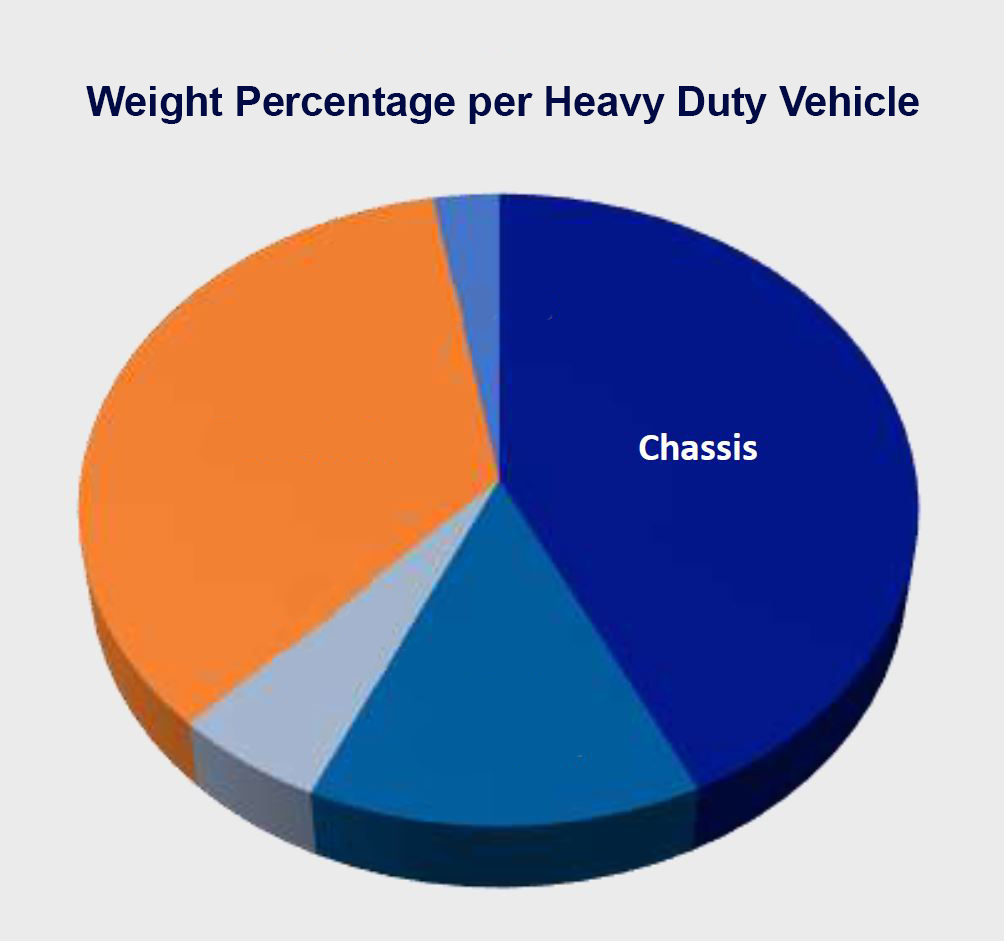
Kordsa erklärt, dass Chassiskomponenten eine einzigartige Chance für Verbundwerkstoffe darstellen, da sie den größten Einzelprozentsatz des Fahrzeuggewichts ausmachen, aber dennoch Strukturteile sind, die sich wiederholenden dynamischen Belastungen ausgesetzt sind.
Das Ziel von Kordsa und Ford Otosan ist die Reduzierung von CO2 -Emissionen und ermöglichen eine höhere Kraftstoffeffizienz und Nutzlast durch die Herstellung einer Verbundblattfeder, die das Gewicht gegenüber Stahl um 75 % reduziert. Dies würde auch die ungefederte Masse des Fahrzeugs reduzieren, um das Gewicht in anderen Systemen zu reduzieren und den Komfort durch reduzierte Geräusch-, Vibrations- und Rauheitsniveaus (NVH) zu verbessern.
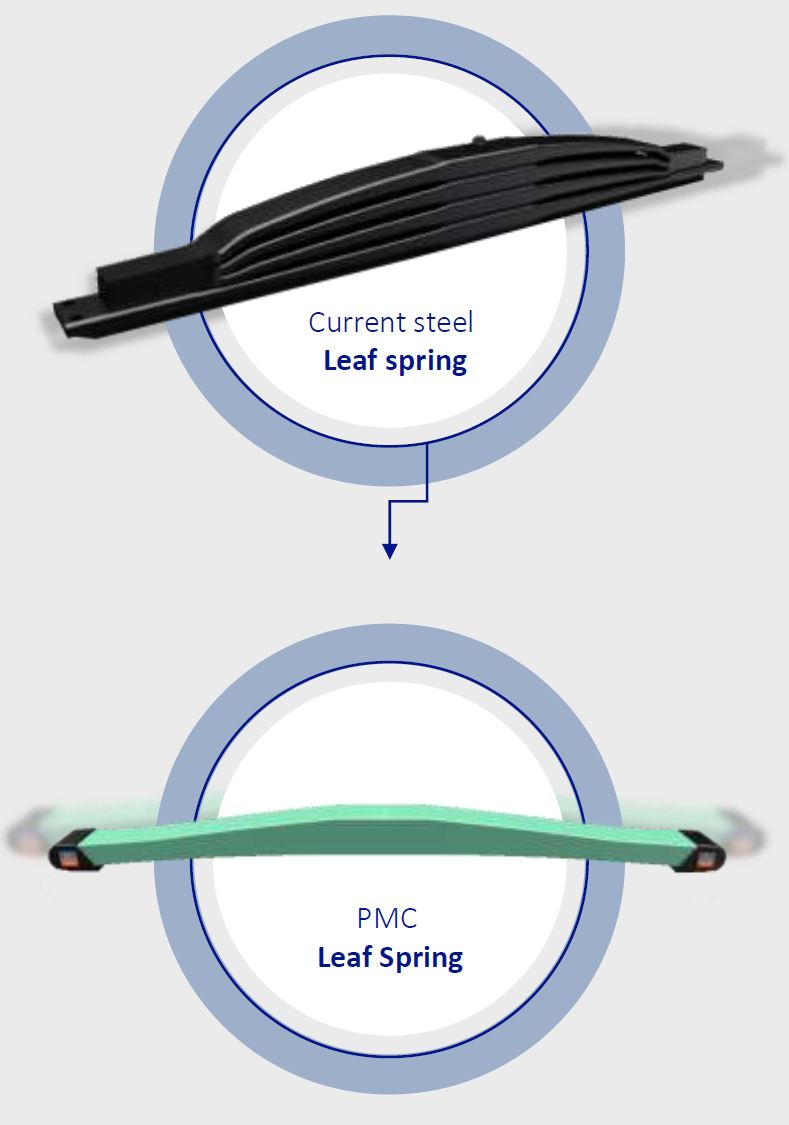
Die Ziele für diese Verbundblattfeder für schwere Lkw sind anspruchsvoll. Es muss einer Achslast von 13,4 Tonnen standhalten und einer rigorosen Betriebsumgebung standhalten und eine lange Lebensdauer von mindestens 1 Million Kilometer bieten. Dementsprechend muss dieses dicke Verbundteil – bis zu 110 Millimeter – ein ausreichend hohes Faservolumen und einen geringen Hohlraumgehalt sowie eine Glasübergangstemperatur (Tg ) zwischen 120-150°C. Die Produktionsrate muss mit der für schwere Lastkraftwagen übereinstimmen – bis zu 10.000 Teile/Jahr – was einen Aushärtungszyklus von weniger als 1 Stunde erfordert, während die Kosten wettbewerbsfähig sein müssen.
Kordsa und Ford Otosan entschieden sich für Prepreg-Kompressionsformen wegen seiner Fähigkeit, eine homogene Harzverteilung und optimierte Steifigkeit durch verbesserte Faserausrichtung mit weniger Verzerrungen und reduzierten Dickenschwankungen in einem Prozess mit hoher Zuverlässigkeit und Wiederholbarkeit zu liefern. Kordsa produzierte eine Vielzahl von unidirektionalen Kohlefaser- und Glasfaser-/Epoxid-Prepreg-Chargen und führte eine vollständige Materialcharakterisierung für jede durch, wobei die von Ford Otsan benötigten Materialdaten für die Eingabe in computergestützte Konstruktionswerkzeuge (CAE) entwickelt wurden. Es arbeitete dann daran, den Lastfall für einen Prototyp einer Blattfeder für schwere Lastkraftwagen vollständig zu detaillieren und verwendete Faser-Bragg-Gitter-(FBG)-Sensoren, um Lasten zu überprüfen und Produktionsparameter sowie Ermüdungseigenschaften zu untersuchen.
Der endgültige Prototyp erzielte 75 % Gewichtseinsparungen gegenüber Stahl bei gleichzeitiger Erhöhung der Zugfestigkeit, Druckfestigkeit und Ermüdungsbeständigkeit. Kordsa wird die Entwicklung mit Ford Otosan und anderen Transportherstellern fortsetzen und sich als wertvoller Verbündeter in der Kampagne zur Reduzierung von CO2 . erweisen -Emissionen weltweit durch leichtere Autos, Lastwagen, Flugzeuge und Schiffe durch leichtere Verbundstrukturen im Vergleich zu schwereren Stahl-, Aluminium- und Magnesiumalternativen.
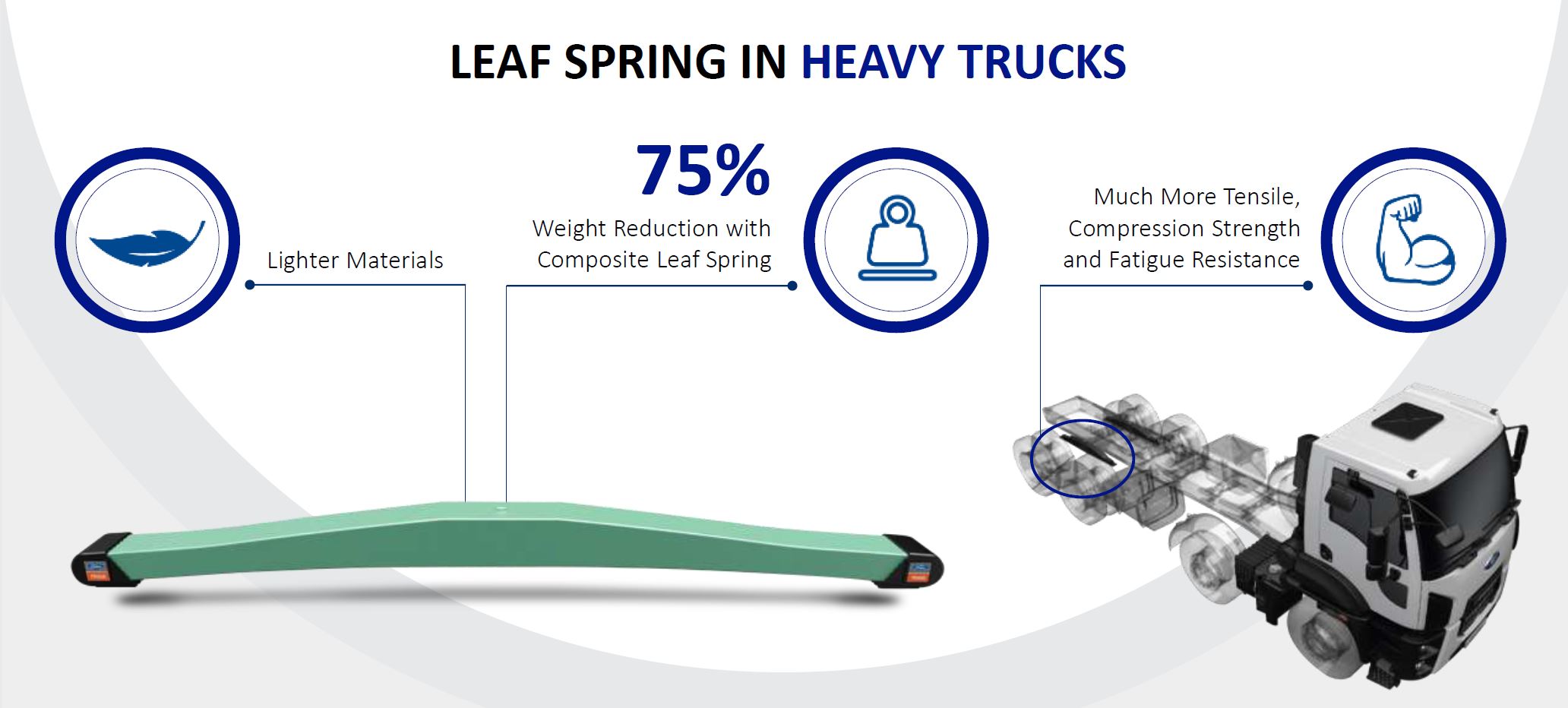
QUELLE | Kordsa und Ford Otosan
Harz
- Covestro versorgt Signify mit Materialien für 3D-gedruckte Leuchten
- Solvay arbeitet mit Boeing für Coronavirus-Gesichtsschutz zusammen
- TPE mit recyceltem Inhalt für die Fahrzeuginnenausstattung
- Hexion kooperiert mit Rassini für die Anwendung von Verbundstoff-Blattfedern im neuen Ford F-150-Modell
- Impossible Objects arbeitet mit BASF für den 3D-Verbunddruck zusammen
- Hexcel arbeitet mit Lavoisier Composites, Arkema zusammen
- Techsil bringt durchsichtigen Epoxidklebstoff für Verbundsubstrate auf den Markt
- Rhodes Interform fertigt Verbundpresse für AMRC
- Ashland arbeitet mit Velox für den Vertrieb von Verbundwerkstoffen in Frankreich zusammen
- Die Volvo Group arbeitet mit Nvidia an einer KI-Plattform für autonome Lkw zusammen