Beschleunigung thermoplastischer Verbundwerkstoffe in der Luft- und Raumfahrt
Endlosfaserverstärkte thermoplastische Verbundwerkstoffe (TPCs) wurden als Schlüsseltechnologie für die Zukunft nachhaltiger Flugzeuge genannt und bieten erhöhte Produktionsraten von leichten, hochzähen Teilen, die ohne Löcher oder Befestigungselemente zu wirtschaftlichen Schweißbaugruppen verbunden werden können.
CW veröffentlichte 2018 eine Artikelserie zu TPC-Bändern, in-situ-Konsolidierung und Schweißen und präsentierte 2019 zwei Webinare zu TPCs in Automobilanwendungen und TPC-Entwicklungen für die Luft- und Raumfahrt. Die meisten von mein Bisherige Artikel und Präsentationen beziehen sich auf Hersteller von TPC-Teilen und Ausrüstungslieferanten in Europa sowie auf die Automated Dynamics-Abteilung von Trelleborg in den USA. Ich habe auch eine Tour durch das in den USA ansässige Tri-Mack Plastics gemacht. Aber leider habe ich hier in den USA einen anderen TPC-Teilehersteller übersehen, der seit 15 Jahren im Stillen die Technologie- und Produktionsgrenzen vorantreibt. ATC Manufacturing – mit Sitz in Post Falls, Idaho, etwas außerhalb von Spokane, Washington – produziert eine Million Teile pro Jahr, ausschließlich endlosfaserverstärkte Thermoplaste und alles für die Luft- und Raumfahrtindustrie. Da ATC ein einzigartiges Know-how in der schnellen Umformung von 3D-Teilen entwickelt hat, ist ATC auch ein wichtiger Partner im Forschungsprogramm RApid High-Performance Molding (RAPM) mit Boeing Co. (Chicago, Illinois, USA) und der Defense Advanced Research Projects Agency (DARPA , Arlington, Virginia, USA) für das US-Verteidigungsministerium (DoD).
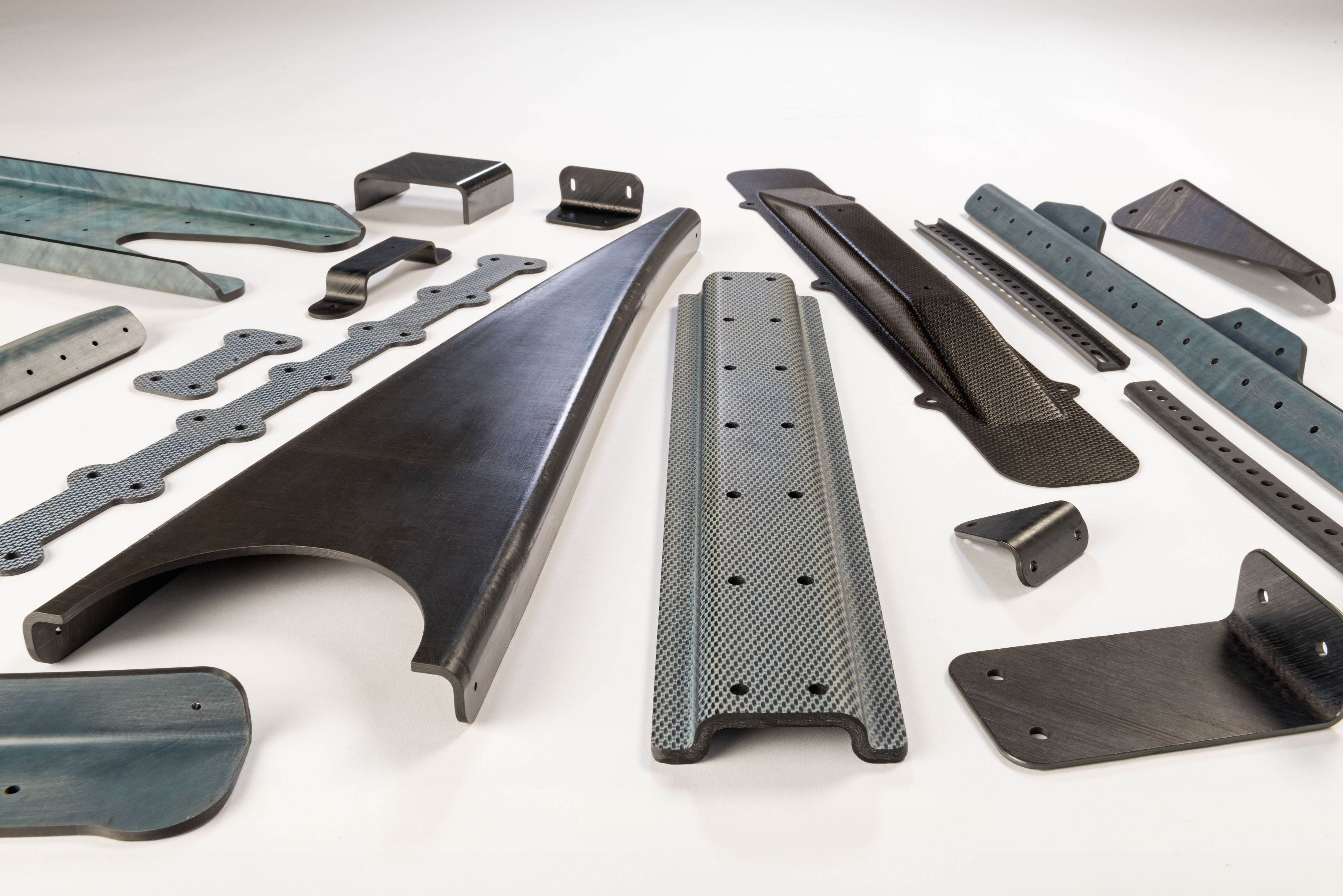
ATC Manufacturing produziert jährlich eine Million thermoplastische Verbundteile für Luft- und Raumfahrtanwendungen, einschließlich Rippen, Clips, Halterungen und Versteifungen. QUELLE | ATC-Fertigung
Wer ist ATC?
ATC Manufacturing wurde 2004 vom ehemaligen Boeing-Ingenieur Dan Jorgenson gegründet, der weiterhin Co-Vorsitzender des Unternehmens ist. „Wir hatten schon immer einen starken technischen und technischen Fokus“, sagt David Leach, Director of Business Development bei ATC Manufacturing. Das Unternehmen hat auch eine lange Geschichte bei Boeing, wurde in den letzten fünf aufeinanderfolgenden Jahren als Silver-Level-Lieferant ausgezeichnet und 2016 und 2017 als Boeing-Lieferant des Jahres nominiert. Halterungen und kleinere Stanzteile“, sagt Leach. „Aber in den letzten Jahren haben wir komplexere Baugruppen sowie viel dickere, größere Teile – bis zu 60 Zoll Länge – und Teile für Primärstrukturen entwickelt.“ Letztere umfassen strukturelle Flügelspitzenkomponenten, Langträger mit maßgeschneiderten Layups in verschiedenen Querschnitten sowie Rumpf- und Leitwerksstrukturen.
Das Unternehmen beschäftigt 150 Mitarbeiter mit mehr als 20 Ingenieuren. Die Herstellung konzentriert sich auf eine einzige 67.000 Quadratmeter große Anlage, die 2015 speziell gebaut wurde und für optimierte Arbeitsabläufe mit Raum für Erweiterungen ausgelegt ist. (Beachten Sie, dass eine Fläche von 52.500 Quadratfuß bereits für zukünftiges Wachstum geplant ist.) „Alles ist unter einem Dach“, bemerkt Leach, „was den Betrieb vereinfacht.“ Dazu gehören neun Stanzpressen mit Kapazitäten von 30 bis 150 Tonnen und Aufspannflächen bis 60 x 30 Zoll. „Wir installieren eine zusätzliche 200-Tonnen-Presse, die bis Ende 2019 voll betriebsbereit sein wird“, fügt er hinzu. ATC verfügt über 10 CNC-Bearbeitungsstationen, die Teile bis zu einer Länge von 3,6 m bearbeiten und Teile bis zu einer Länge von 9 m mit Wasserstrahl schneiden können.
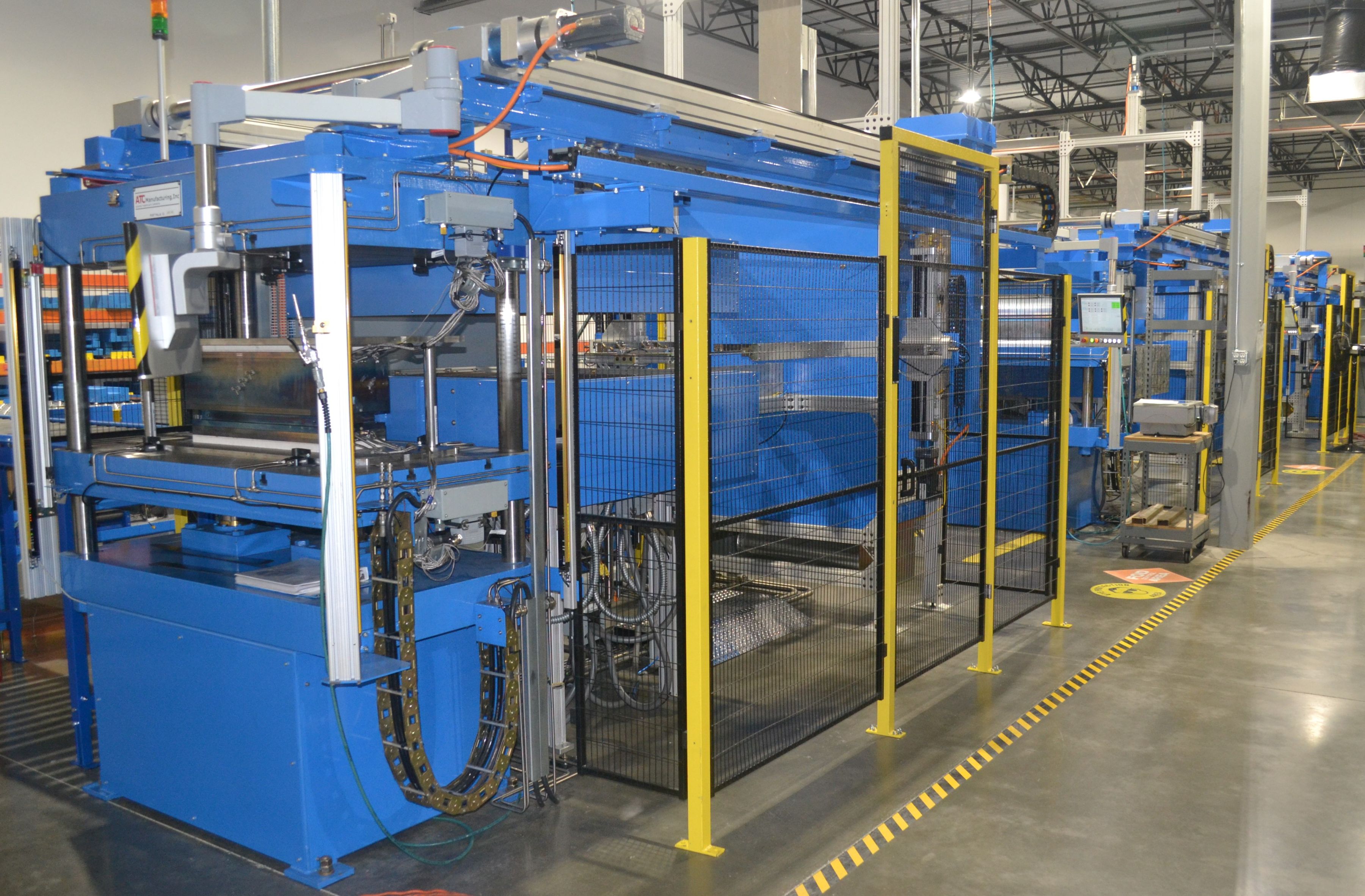
ATC Manufacturing betreibt 9 Stanzpressen, darunter die hier gezeigte 80-Tonnen-Presse, mit Kapazitäten bis 150 Tonnen und Plattenflächen bis 60 x 30 Zoll.
QUELLE | ATC-Fertigung
Die zerstörungsfreie Prüfung (NDI) ist ebenfalls in den Betrieb und das Arbeitsablaufdesign der Anlage integriert, einschließlich fünf C-Scan-Tanksysteme, die Impuls-Echo- und Durchstrahlungsprüfungen für Teile mit einer Länge von bis zu 9 m bieten. Weiteres hauseigenes Know-how umfasst die gesamte Oberflächenvorbereitung und Lackierung. „Wir haben eine sehr effiziente Oberflächenvorbereitung für thermoplastische Verbundwerkstoffe entwickelt, die schwierig zu lackieren und zu verkleben sein können“, sagt Leach und stellt fest, dass ATC auch an der Plasmabehandlung von TPC-Teilen gearbeitet hat. Das Unternehmen lackiert 200.000 Teile/Jahr und versiegelt 70.000 Teile pro Jahr.
„Wir haben auch stark in die Forschung investiert, beispielsweise in das RAPM-Programm für DARPA, und wir sind Mitglieder des ThermoPlastic Composites Research Center (TPRC, Enschede, Niederlande)“, fährt er fort. ATC nimmt an der 10-jährigen Jubiläumskonferenz des TPRC mit dem Titel „Future of Thermoplastic Composites“ teil, die am 8. Oktober an der Universität Twente in den Niederlanden stattfindet. „Corbin Chamberlain, stellvertretender Vorsitzender von ATC, wird an einer Podiumsdiskussion teilnehmen und wir werden auch Konstruktionsteile für die Luft- und Raumfahrt demonstrieren, die wir auf einer Ausstellung in Verbindung mit der Konferenz hergestellt haben“, sagt Leach.
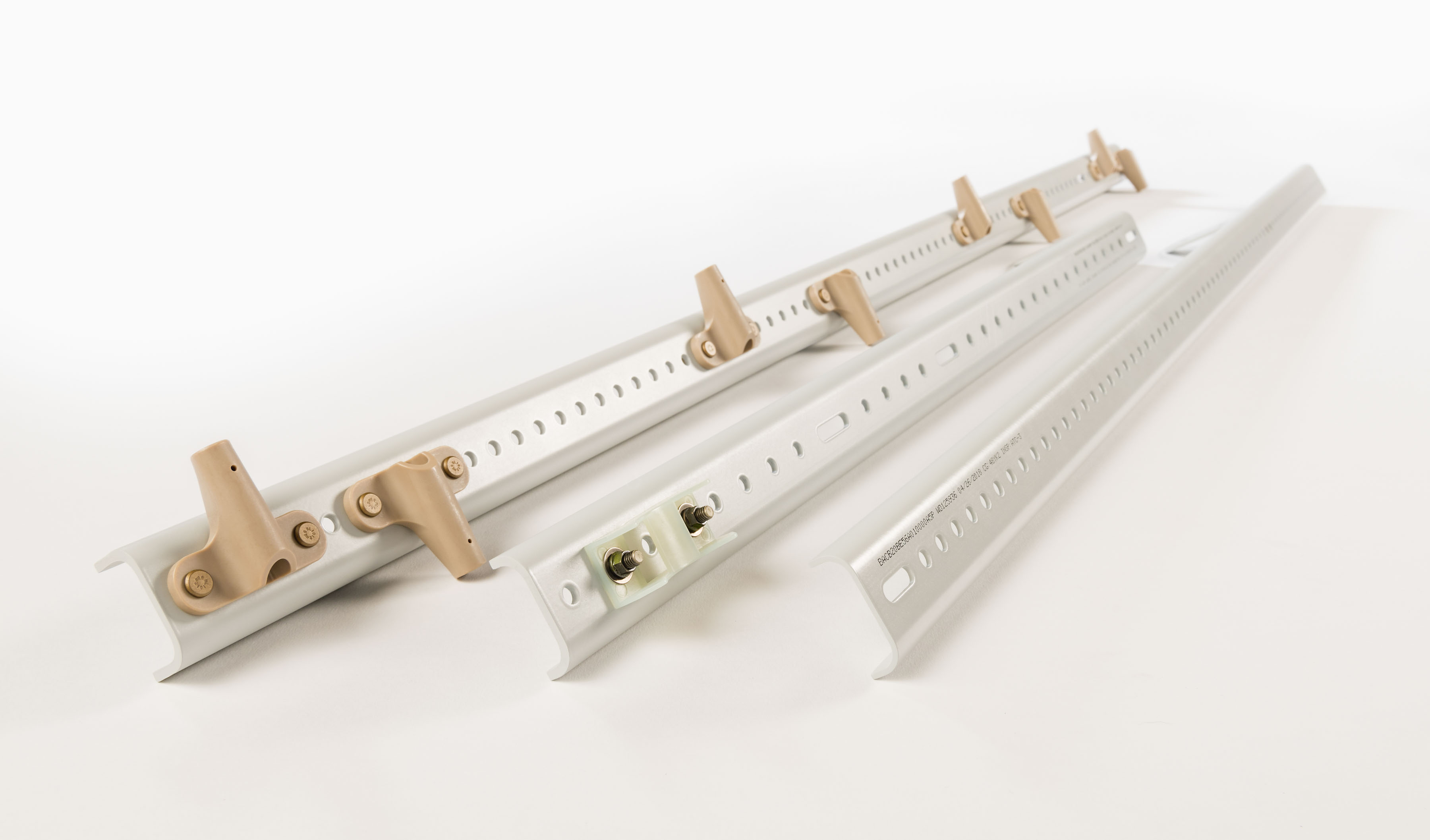
Lackierte thermoplastische Verbundkanäle mit installierten Armaturen. QUELLE | ATC-Fertigung
Stoffe auf UD-Band, Umformen und schnelle Zykluszeiten
Obwohl die Herstellung von TPC-Brackets und -Clips bei ATC mit Gewebeverstärkungen begann, sind sie jetzt auf die Verwendung von unidirektionalem (UD) Klebeband umgestiegen. „Wir haben uns dann zu größeren Strukturteilen entwickelt, weil wir bereits gute Erfahrungen mit der Formgebung von 3D-Teilen mit UD-Tape gemacht hatten“, erklärt Leach. „Diese Teile, deren Dicke von 1-2 Millimeter bis 6,5 Millimeter reicht, müssen zu anderen Strukturen passen. Wir müssen enge Maßtoleranzen für Stoßflächen einhalten, zum Beispiel ± 0,010 Zoll (0,25 Millimeter) Profiltoleranz und ± 0,5 Grad Winkeltoleranz.“
Anschließend begann das Unternehmen mit der Entwicklung langer TPC-Profile. „Wir stellen unser eigenes flaches Laminatmaterial mittels Continuous Compression Moulding (CCM) her“, sagt Leach. „Wir haben zwei CCM-Maschinen für flache Laminate und eine, die TPC-Prepregs zu einem kontinuierlichen 3D-Profil formt, wodurch Kanäle mit einer Länge von bis zu 25 Fuß hergestellt werden.“
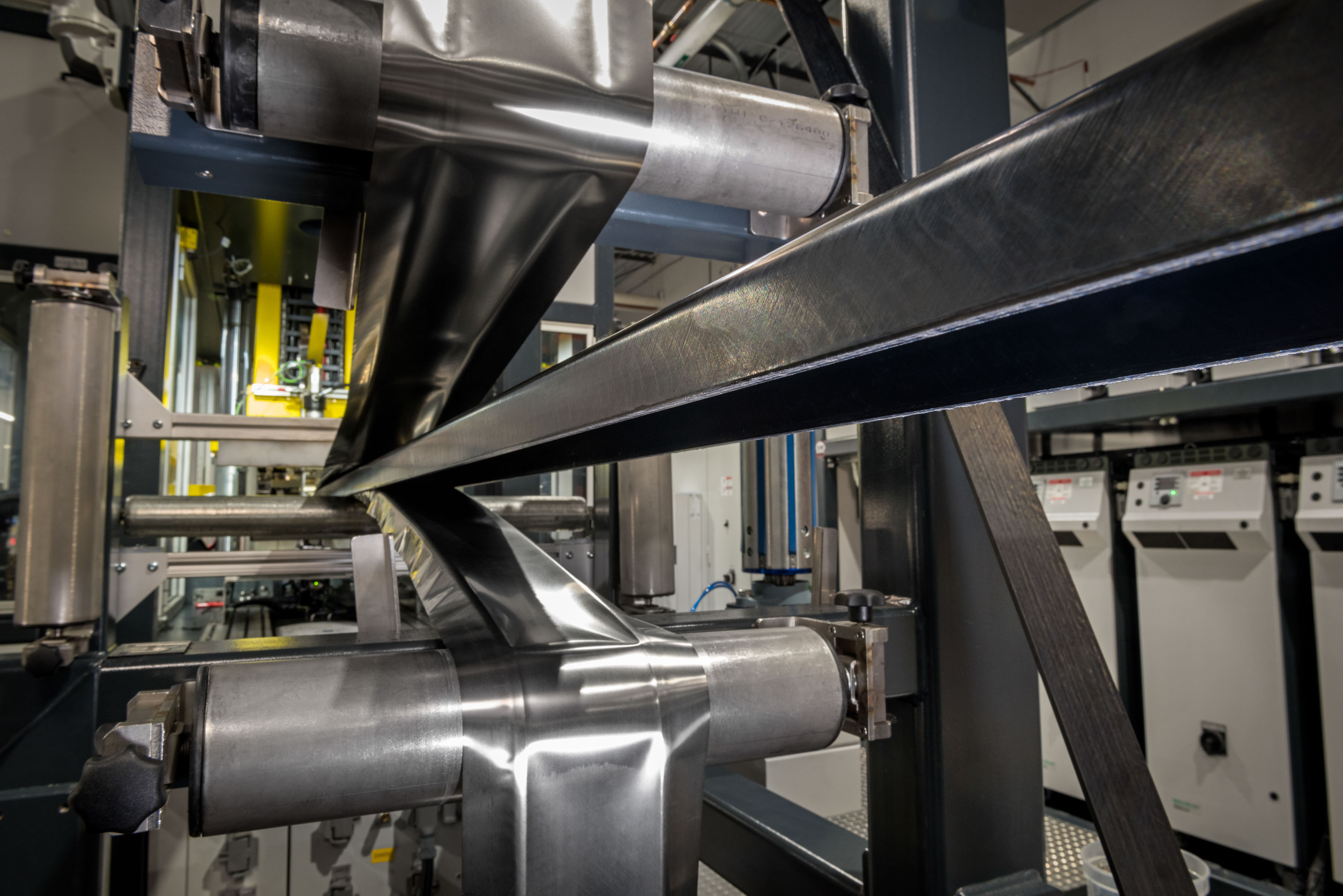
Thermoplastisches Verbundprofil, das durch kontinuierliches Kompressionsformen (CCM) geformt wird. QUELLE | ATC-Fertigung
Auf die Frage nach den Herausforderungen bei der Bildung von 3D-Profilen und -Formen erklärt Trevor McCrea, Direktor für Forschung und Entwicklung bei ATC Manufacturing, dass bei Stoffen „das Gewebe selbst einen Großteil der stattfindenden Verformung kontrolliert. Bei UD gibt es unterschiedliche Dynamiken. 90° zum Radius möchte zum Beispiel ausdünnen oder verdicken, aber das kann man in einem Strukturteil nicht haben. Diese Probleme werden bei komplexeren Formen noch schlimmer. Sie haben auch eine größere Herausforderung darin, den Prozess beim Umformen zu verwalten.“
Den Prozess managen? „Für uns ist das ganz anders als das Umformen in Duroplasten, da wir nur 2 Sekunden Zeit haben, um zu formen“, sagt McCrea. „In einem Autoklavenzyklus kann man viele Sünden abdecken“, fügt er hinzu. „Aber ohne diesen Spielraum nutzen wir sehr schnelle Umform- und Stanzprozesse. Wir müssen auch die Kristallinität managen.“ Denn hochbelastete Flugzeugstrukturen verwenden teilkristalline thermoplastische Matrixpolymere – wie Polyetheretherketon (PEEK), Polyetherketonketon (PEKK) und niedrig schmelzendes Polyaryletherketon (LM PAEK) – die ihre bemerkenswerten mechanischen Eigenschaften und chemische Beständigkeit aus der sich entwickelnden kristallinen Struktur beziehen wie sie abkühlen. „Man kann isotherm kristallisieren, was für flache Platten nicht allzu schwierig ist, aber bei 3D-Formen viel schwieriger wird“, sagt McCrea. „Die Materialien müssen ausreichend erhitzt werden, um sich zu formen [beachten Sie, dass die Schmelztemperaturen für diese Materialien zwischen 300–400°C liegen], aber dann schnell genug abgekühlt werden, um eine heiße Entformung zu ermöglichen, um thermische Zyklen der Werkzeuge zu vermeiden und gleichzeitig Form, Toleranz, Kristallinität und Oberflächengüte zu kontrollieren .”
Einer der Gründe für das Wachstum von TPC-Teilen in den letzten Jahren ist ihre Fähigkeit, sehr schnelle Zykluszeiten zu bieten. „Wir haben Rippen für Demonstratoren von Militärflugzeugen mit einer Zykluszeit von 5 Minuten hergestellt, und unsere durchschnittliche Zykluszeit beträgt etwa 10 Minuten“, bemerkt Leach. „Wir können die hohen Produktionsraten ermöglichen, die derzeit von Flugzeug-OEMs angestrebt werden.“ Diese sehr schnelle durchschnittliche Zykluszeit führt tatsächlich zu einem sich ständig ändernden Teilemix. „Wir würden gerne monatelang nur ein Teil produzieren, aber unsere Leistungsfähigkeit übertrifft die der Flugzeugfertigung“, sagt McCrea. „Wir radeln also immer durch verschiedene Teile.“ Der Großteil der Produktion von ATC läuft in einer Schicht pro Tag, 5 Tage pro Woche. „Wir haben genügend Kapazitäten, um der gestiegenen Produktion gerecht zu werden“, bemerkt Leach.
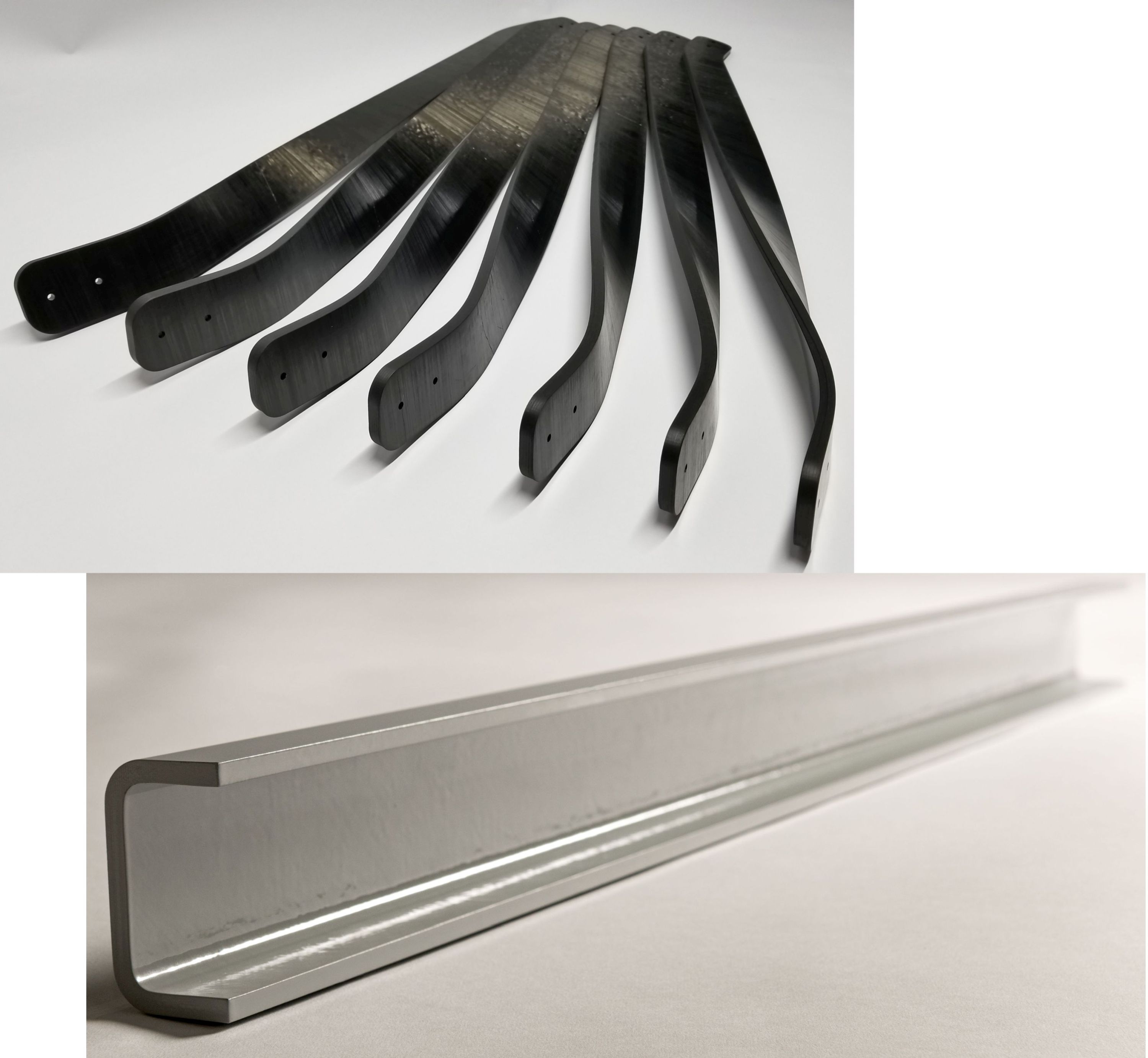
Strukturbänder aus thermoplastischen Verbundwerkstoffen und lackiertes Profil. QUELLE | ATC-Fertigung
Vision für die Zukunft
ATC bietet durch seine mehr als jahrzehntelange Erfahrung in der TPC-Produktion einen erheblichen Mehrwert. „Wir helfen unseren Kunden häufig dabei, Teile für die Fertigung zu entwickeln“, sagt Leach. „Wir verarbeiten oft Teile aus duroplastischem Verbundmaterial, zum Beispiel eine Rumpfprimärstruktur, die so hergestellt wird, dass sie die ursprüngliche Dicke beibehält. Aber es könnte ein viel leichteres Teil sein, wenn es ursprünglich für TPC entwickelt wurde.“ Wieso den? „Weil diese teilkristallinen TP-Matrix-Materialien eine höhere Leistung haben“, erklärt er. „Sie müssen nicht wie bei einer duroplastischen Matrix für Mikrorisse und Schadenstoleranz konstruieren, und es gibt auch viel weniger Hot/Wet-Knockdown. Tatsächlich gibt es bei PEEK, PEEK oder PAEK überhaupt keinen nassen Knockdown. Es gibt auch keinen heißen Knockdown, es sei denn, Sie befinden sich in der Nähe der Tg, die typischerweise ≈150°C beträgt. Beim standardmäßigen Open Hole Compression (OHC)-Test auf Schadenstoleranz beispielsweise, bei dem Sie die Festigkeit beim Übergang der Probe von RT auf 120°C beurteilen, gibt es kaum einen Knockdown.“
„Wir werden in der Lage sein, dünnere Teile zu konstruieren und auch einen Großteil des Aluminiums und Titans zu eliminieren, das in den aktuellen Konstruktionen der ersten Generation für Verbundwerkstoffe enthalten ist [wie die Boeing 787 und Airbus A350 Großraumflugzeuge]“, fügt McCrea hinzu. „Wir treiben die Umformung dieser Materialien weiter voran und das wird auch weiterhin neue Anwendungen eröffnen.“
Leach geht davon aus, dass dies erhebliche Auswirkungen auf zukünftige Flugzeuganwendungen haben wird. „Wir schauen uns jetzt tatsächlich Teile an, die man aufgrund der geforderten Eigenschaften und Produktionsgeschwindigkeit einfach nicht mit Duroplasten herstellen kann.“
Für weitere Informationen wird ATC Manufacturing das Fachpapier "Cost Effective Thermoplastic Composites in Aerostructures" der Autoren Corbin Chamberlain, David Leach und Trevor McCrea auf der CAMX 2019 in der Thermoplastic Materials and Applications Session am Mittwoch, den 25. September um 16:00 Uhr präsentieren in Raum 210C.
Es präsentierte auch ein gemeinsames Papier mit Boeing in einer geschlossenen Sitzung auf der SAMPE 2019 (4.-7. Mai, Charlotte, NC, USA) mit dem Titel:„Rapid High Performance Molding of Structural Thermoplastic Composite Parts“. Siehe meinen Blog:https://www.compositesworld.com/news/darpa-presents-tff-program-for-rapid-low-cost-composites-to-replace-metals-in-small-parts-for-defense- Anwendungen
Harz
- Wie der 3D-Druck die Luft- und Raumfahrt verändert hat
- Covestro verstärkt Investitionen in thermoplastische Verbundwerkstoffe
- Collins Aerospace erwirbt den Hersteller von thermoplastischen Teilen in den Niederlanden
- Thermoplastische Verbundwerkstoffe bei Oribi Composites:CW Trending, Episode 4
- Fehlerbehebung beim Thermoformen von thermoplastischen Verbundwerkstoffen
- Thermoplastische Verbundwerkstoffe:Strukturelle Stoßstangenhalterung
- ACMA veröffentlicht Programm der Konferenz für Thermoplastische Verbundwerkstoffe 2020
- Thermoplastische Verbundwerkstoffe:Malerische Aussicht
- Schweißen von thermoplastischen Verbundwerkstoffen
- Konsortium für thermoplastische Verbundwerkstoffe strebt die Massenproduktion für die Automobil- und Luftfahrtindustrie an