Erhöhter Zugang zu AFP
„Unser Ziel ist es, die Hindernisse für die Herstellung von Verbundwerkstoffen zu verringern“, sagt Pravin Luthada, CEO von Addcomposites. Addcomposites hat ein Tool zur automatischen Faserplatzierung (AFP) entwickelt, das an jedem vorhandenen Roboterarm montiert werden kann.
Der AFP-XS ist zum Kauf, aber auch zum Mieten erhältlich. Es ist leicht, wiegt leer 6,5 kg und ist kompakt. „Wir versenden es in einem Karton, der ungefähr die Größe eines Computer-Desktop-Towers hat“, sagt Luthada. „Die Ersatz-Schneidmesser und Verbrauchsmaterialien sind ebenfalls im Mietpreis enthalten.“
Dies birgt für mich ein hohes Disruptionspotenzial und ist auch fast unvermeidlich, wenn sich die Branche in Richtung intelligenter Produktionslinien und Fabriken der Industrie 4.0 bewegt. Wir sehen bereits, dass solche Linien durch die Partnerschaft von Airborne mit SABIC und dem Factory 4.0 Testlab an der Swinburne University etabliert wurden. Wir beobachten auch die Konvergenz von AFP und 3D-Druck und die Kombination mehrerer Prozesse zu einzelnen automatisierten Systemen oder Zellen (z. B. AFP und Filament Winding, CNC-Bearbeitung, Laseroberflächenbehandlung und -fügen usw.), um neue Flexibilität, Multifunktionalität und Geschwindigkeit zu erreichen . Wenn es nach Addcomposites geht, könnten große, teure AFP-Zellen bald der Vergangenheit angehören.
Leidenschaft für die Herstellung zugänglicher Verbundwerkstoffe
Die Vision für den AFP-XS-Werkzeugkopf von Addcomposites entstand vor einigen Jahren, als der CEO für die Indian Space Research Organization (ISRO) arbeitete. Insbesondere Indien ist einer der am schnellsten wachsenden Märkte für Verbundwerkstoffe, doch „in Indien gibt es keine mir bekannten AFP-Systeme“, sagt Luthada. „Wir haben bei ISRO eine Ausschreibung für ein automatisiertes System zur Herstellung von Verbundwerkstoffen, hauptsächlich Laminaten und Sandwichstrukturen für Satelliten und Trägerraketen, ausgeschrieben, aber alle Antworten, die wir erhielten, waren zu teuer. ISRO war mit seinen Raumfahrtprogrammen recht erfolgreich, stellte jedoch weiterhin die meisten seiner Verbundprodukte im Handlaminierverfahren her.“
So wurde Luthadas Leidenschaft für die Entwicklung zugänglicher Verbundwerkstoffe geboren. „Auf dem Weg zur Gründung von Addcomposites habe ich Faserwickelmaschinen und 3D-Drucksysteme für Kunststoffe und Keramik gebaut und eingesetzt.“ Als er nach Finnland zog, um seinen Master-Abschluss an der Aalto-Universität in der Nähe von Helsinki zu absolvieren, konnte Luthada ein Forschungsprojekt starten, um die Automatisierung in Verbundwerkstoffen leichter zugänglich zu machen. „Aalto ist bei Verbundwerkstoffen nicht so stark, aber dank des offenen Innovationsökosystems in Finnland sehr stark in der digitalen Fertigung“, erklärt er. „Wir konnten neu anfangen und das gesamte Design des AFP-Werkzeugkopfes überdenken, um die Kosten so gering wie möglich zu halten.“
„Wir sind das Problem einfach anders angegangen als die heutigen Anbieter“, sagt Luthada. „Wo große, teure, eigenständige Zellen gebaut werden, haben wir ein Tool entwickelt, das sich in bestehende Infrastrukturen – also jeden Roboterarm – einstecken und spielen lässt. Somit müssen unsere Kunden nicht in eine weitere Zelle investieren.“ Dennoch war das Team nicht bereit, auf die Qualität der Luft- und Raumfahrt zu verzichten. Luthada weist darauf hin, dass das AFP-XS-Tool robust und mit hochwertigen Teilen gebaut ist. „Unser Hauptaugenmerk lag auf Software und Kontrolle.“
Offenes und anpassungsfähiges Ökosystem für Composites 4.0
„Wir haben angefangen, uns zu überlegen, wie man Offline-Programmiersoftware entwickelt“, fährt er fort. „Wir haben unter anderem mit Dassault Systèmes und Autodesk gesprochen, aber für unsere Kunden würden die Systeme zu teuer. Also haben wir uns angeschaut, welche offenen Softwaresysteme es gibt.“ Der Gewinner? Nashorn 3D. „Es ist gegen eine lebenslange Lizenzgebühr von rund 1.000 Euro erhältlich“, sagt Luthada. „Es ermöglicht auch eine visuelle Programmierung, die es einfacher macht, benutzerdefinierte Änderungen innerhalb des Programms zu skripten, beispielsweise das Erstellen eines Bewegungsplans basierend auf der domänenspezifischen Sprache jeder Maschine.“
„Obwohl wir versuchen, das meiste von dem bereitzustellen, was der Benutzer braucht“, fährt er fort, „ist die Software so konzipiert, dass die Bediener auf die Bedienelemente zugreifen und auf die Daten zugreifen können. Die Anbindung und Steuerung der derzeit verfügbaren AFP/ATL-Tools (Automated Tape Laying) an jede vorhandene Bewegungsplattform wie einen Roboterarm oder eine CNC-Maschine ist normalerweise eine ziemliche Herausforderung. ATL/AFP-Anbieter schränken normalerweise die E/A (Eingabe/Ausgabe) des Tools ein. Wir haben uns jedoch für EtherCAT-Steuerungen entschieden, die wie ein Hochgeschwindigkeits-Informationszug ständig zwischen den IO-Ports der Roboterarmsteuerung und dem Tool laufen. Daten werden an jeder Station basierend auf vorbestimmten Befehlen gesammelt oder abgelegt, um vollen Zugriff, Feedback und Kontrolle der zwischen dem Roboter und dem AFP-XS-Tool übertragenen Informationen zu ermöglichen. Dieser Ansatz ermöglicht Echtzeitsteuerung und -kommunikation für Industrie-4.0-Anwendungen.“
Luthada merkt an, dass dieses Ökosystem der Offenheit viel Flexibilität bietet. „Wir ermöglichen eine sehr hohe Zugänglichkeit, sodass jeder, der mit CAM (Computer Aided Manufacturing) arbeitet, es in seine Roboterplattform integrieren kann. Sie können den AFP-XS beispielsweise so anpassen, dass er mit Inline-Überwachungssystemen oder mit einem robotischen Filamentwickler kommuniziert.“ Er stellt fest, dass Automatisierungsanbieter das Angebot aus der ersten Pressemitteilung des Unternehmens erkannt haben (siehe „Addcomposites führt Plug &Play AFP/ATL ein“). „Einige von ihnen haben sich an uns gewandt, um unser System in ihr Angebot an Fertigungszellen zu integrieren.“ Noch wichtiger, betont Luthada:„Unser Design macht es auch einfach, mit diesem System zu beginnen und zu arbeiten.“
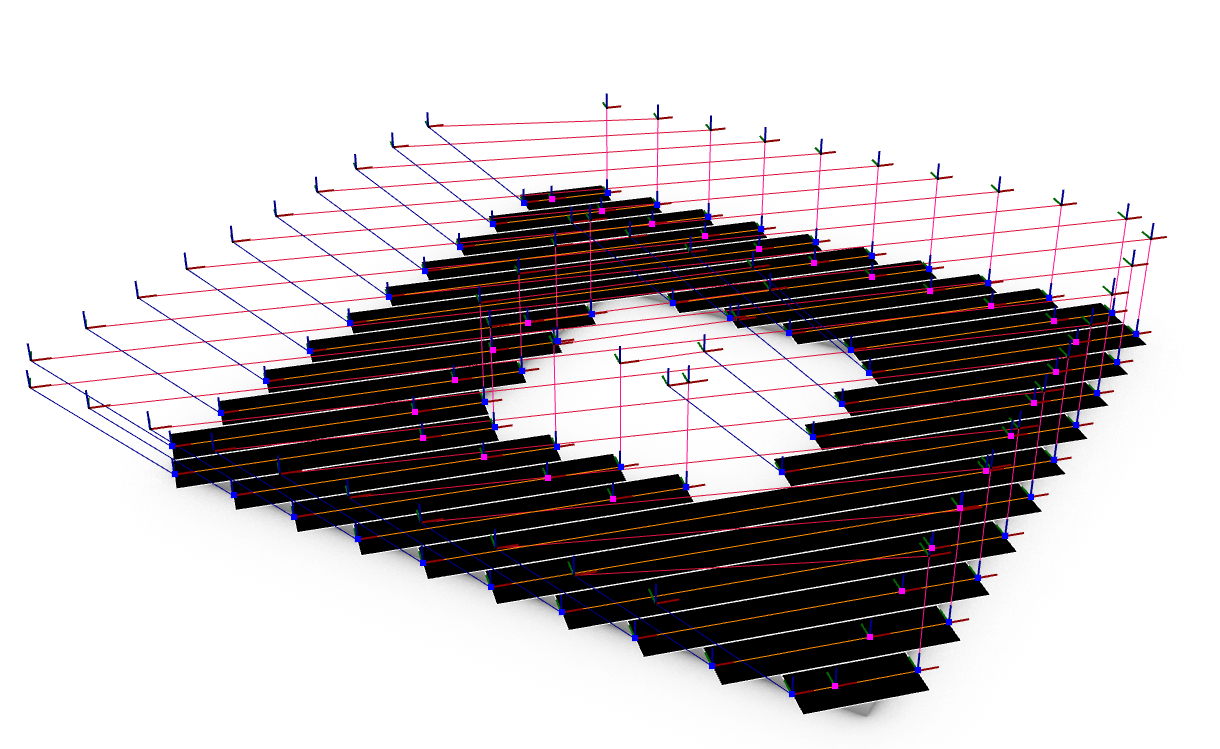
Der AFP-XS verwendet die Addpath-Software, eine offene Plattform basierend auf Rhino 3D.
QUELLE | Addcomposites
Materialien und Spezifikationen
Der Werkzeugkopf AFP-XS verarbeitet trockene Faser- und Prepreg-Bänder in Breiten von 5 mm bis 20 mm. „Bei der Entwicklung des Werkzeugkopfes haben wir ihn für jedes Material optimiert“, erklärt Luthada. „Wir haben zuerst mit Trockenfasern angefangen, arbeiten aber jetzt mit Duroplast-Prepreg und Niedertemperatur-Thermoplast-Prepreg, also Materialien mit einer Tg unter 200 °C, wie PLA und Polyamid. Bei der Verarbeitung von thermoplastischem Klebeband verbessern wir das System, um eine in-situ-Konsolidierung (ISC) durchzuführen.“ Er sagt, dass das Unternehmen bald über eine gute Datenmenge verfügen wird, die auf einem ISC-Projekt mit thermoplastischen Klebebändern basiert, das es seit einiger Zeit durchführt. „Außerdem gehen uns Ende dieses Monats die Autoklaven (OOA) Duroplast-Prepregs aus.“
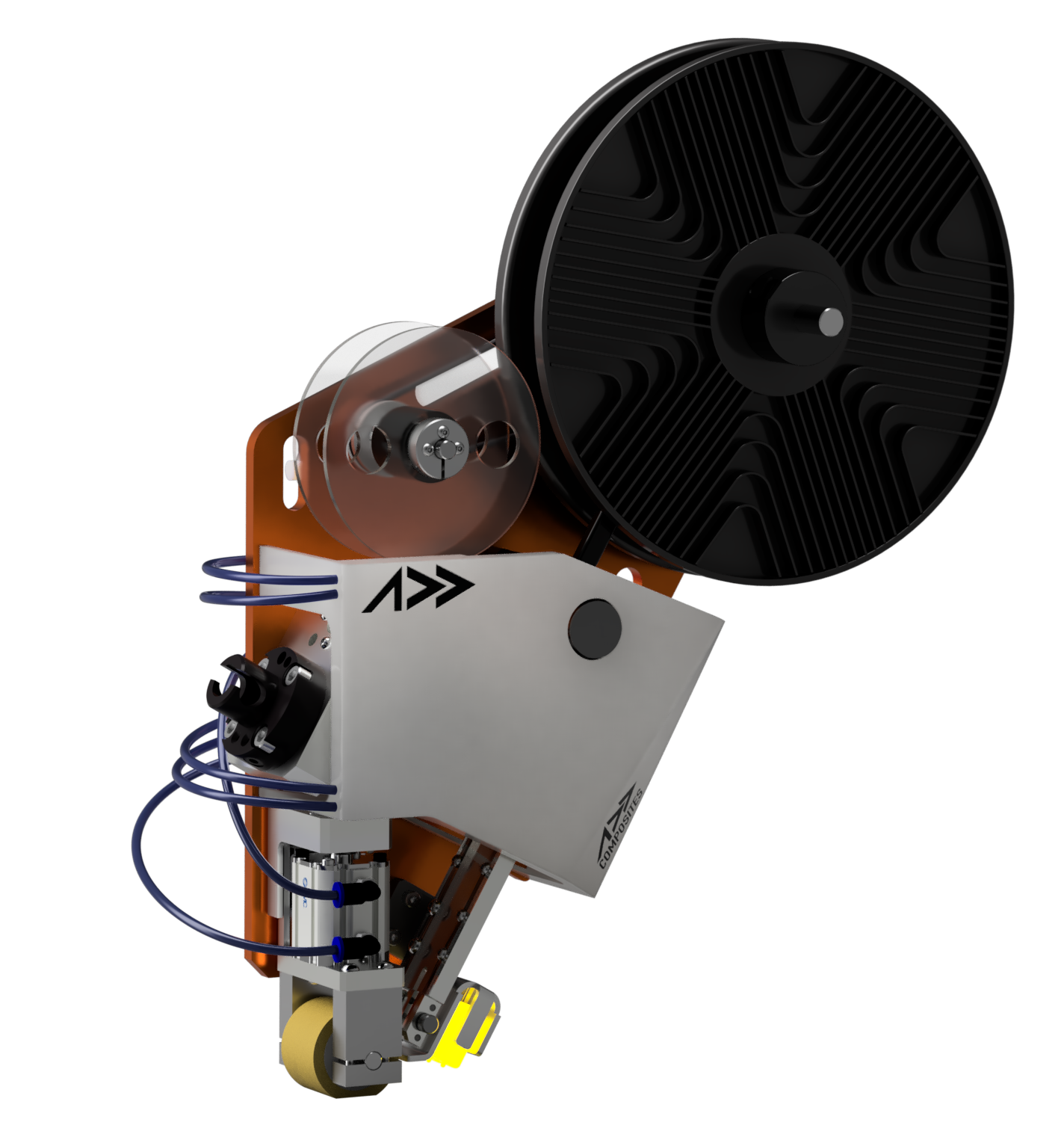
Beim Werkzeugkopf hat Addcomposites jede Komponente mit dem Ziel entwickelt, die Kosten niedrig zu halten und dennoch Luft- und Raumfahrtqualität zu erreichen. „Wir haben unseren eigenen Cutter entwickelt“, sagt Luthada. „Es brauchte viele Iterationen, aber es ist extrem leicht, wirklich kompakt und robust. Wir erreichen derzeit eine Genauigkeit von -0/+2 mm, arbeiten jedoch daran, noch engere Toleranzen zu setzen.“
Das geringe Gewicht aller Komponenten ist entscheidend. „Das Gewicht des Werkzeugkopfs beträgt weniger als 10 kg und hängt nur davon ab, wie viele Fasern der Benutzer auf die Spule laden möchte“, sagt James Kuligoski, Business Development Manager von Addcomposites. Er war zuvor Qualitätsingenieur bei Hexcel und fügt hinzu:„Dies trägt dazu bei, die Größe des benötigten Roboters zu minimieren und somit die Ausrüstungs- und Betriebskosten zu senken.“
Zum Heizen nutzt der AFP-XS derzeit Infrarot und Heißluft. „Wir verwenden keine Laser, weil sie zu teuer sind und zudem höhere Betriebs- und Wartungskosten verursachen“, bemerkt Kuligoski. Dies ist ein Grund, warum Thermoplaste mit höheren Temperaturen immer noch in Forschung und Entwicklung sind. Addcomposites erforscht jedoch auch andere Heiztechnologien, die Leistung bieten und dennoch erschwinglich sind.
AFP über Hardware-as-a-Service (HaaS)
Addcomposites bietet das AFP-XS zum Kauf, aber auch zur Miete zu Raten von 2.000 bis 3.000 Euro pro Monat je nach Mietdauer an. „Unsere Idee war, dass man das Tool auch als kleines Start-up oder Forschungsgruppe mieten kann, um bei der Produktionsgestaltung zu helfen“, erklärt Luthada. „Sie haben Ihre FEA und das Teiledesign fertig, müssen aber jetzt die Herstellbarkeit optimieren. Der Konstrukteur kann über unsere Website eine Simulation der Teilefertigung anfordern. Das Unternehmen kann das Werkzeug dann so lange mieten, wie es benötigt wird, und es an einen verfügbaren Roboter anschließen. Bei Bedarf können wir auch Unterstützung mit lokalen Roboterlieferanten bieten. Wenn sie fertig sind, können sie die Ausrüstung entweder zurückgeben oder zu einem reduzierten Preis kaufen.“
Bis Anfang 2020 will Addcomposites dieses Programm in allen Ländern der EU ausrollen, zunächst in Frankreich, Deutschland, Polen und Großbritannien. „Nächstes Jahr wollen wir 20 Werkzeuge in Europa und den USA bekommen“, sagt Luthada.
Addcomposites hat das AFP-XS bereits für Entwicklungsarbeiten in der Raumfahrtindustrie in Finnland eingesetzt und mit einem anderen finnischen Unternehmen zusammengearbeitet, das thermoplastische Klebebänder entwickelt. Außerdem hat es gerade ein Fertigungsautomatisierungsprojekt mit dem größten Verbundwerkstoffhersteller in Finnland abgeschlossen und führt erste Pilotarbeiten für ein Unternehmen in den USA durch.
„Unser Markt umfasst Universitäten und Forschungszentren, aber auch kleine bis mittelständische Unternehmen, die derzeit Verbundwerkstoffe im Handlaminierverfahren herstellen und Erfahrungen mit AFP und Automatisierung sammeln möchten“, sagt Kuligoski. „Wir können Tests durchführen und die Maschine filmen, während sie die Teile herstellt. Sie können das Werkzeug dann leasen und/oder kaufen, nachdem sie es auf ihren Produkten gesehen haben.“
Wie stapelt es sich?
Luthada räumt ein, dass die Leistung des AFP-XS-Werkzeugkopfs noch nicht so hoch ist wie die der derzeit von AFP-Systemlieferanten verkauften Großzellen. „Aber wir verlieren nicht an Legegeschwindigkeit“, kontert er. „Die Materialien, die wir verarbeiten, sind die gleichen. Wir sehen viel bessere Ergebnisse mit Bändern, die eine geringe Variation aufweisen, genau wie alle anderen. Aber was die Qualität der fertigen Laminate angeht, gibt es keinen Unterschied.“ Da das Unternehmen diese fertigen Laminate nicht selbst aufgießt oder aushärtet, sondern die Ausrüstung für die Hersteller liefert, ist es noch dabei, Laminatdaten zu sammeln. Da mehrere Programme jetzt fertig sind, stellt er fest, dass diese Daten bald auf der Addcomposites-Website veröffentlicht werden.
„Wir haben 2017 das Forschungsprojekt an der Aalto University gestartet und 2018 Addcomposites etabliert“, sagt Luthada. „Wir haben durch die Zusammenarbeit mit verschiedenen Herstellern so viel gelernt und entwickeln das AFP-XS-System ständig weiter. Diese Verbesserungen werden für alle Benutzer bereitgestellt, sobald sie getestet und nachgewiesen wurden. Derzeit arbeitet das System mit Kuka-Robotern und wird derzeit mit ABB und Universal Robots erprobt.“
„Wir glauben, dass Verbundwerkstoffe die Zukunft der fortschrittlichen Fertigung sind“, sagt Kuligoski, „und wir sind leidenschaftlich daran interessiert, allen Verbundwerkstoffherstellern eine intelligente, automatisierte Produktion auf erschwingliche Weise anzubieten.“
Besuchen Sie Addcomposites auf der Composites Europe vom 9. bis 12. September (Stuttgart, Deutschland) und bleiben Sie auf dem Laufenden für weitere Updates von CW .
Harz
- C# - Kapselung
- CompositesWorld SourceBook 2022
- Fehlerbehebung beim Thermoformen von thermoplastischen Verbundwerkstoffen
- Die Entwicklung additiver Verbundwerkstoffe
- Thermoplastische Verbundwerkstoffe:Strukturelle Stoßstangenhalterung
- Menschen in Verbundwerkstoffen – Januar 2019
- CAMX 2018:Ausstellungsvorschau
- Schweißen von thermoplastischen Verbundwerkstoffen
- SPE ACCE 2018 Vorschau
- Hochleistungsverbundwerkstoffe in Israel