PEEK vs. PEKK vs. PAEK und kontinuierliches Formpressen
Dies ist eine Fortsetzung der kürzlich von mir verfassten Artikelserie über thermoplastische Verbundwerkstoffe (TPCs) (siehe unten) sowie des Artikels über thermoplastische Bänder, den Jeff Sloan in der Februar-Ausgabe geschrieben hat.
- Konsolidieren thermoplastischer Verbund-Flugzeugstrukturen, Teil 1
- Konsolidieren thermoplastischer Verbund-Flugzeugstrukturen, Teil 2
- Demonstratoren für thermoplastische Verbundwerkstoffe – EU-Fahrplan für zukünftige Flugzeugzellen
- PEEK oder PEKK in zukünftigen TPC-Flugzeugstrukturen?
TPCs fliegen seit den 1990er Jahren in Flugzeugen und in Primärstruktur seit 2010 – Gulfstreams G650 verfügt über ein Seiten- und Höhenruder aus Kohlefaser/Polyphenylensulfid (PPS), das vom Fokker-Geschäft von GKN Aerospace (Redditch, Großbritannien) unter Verwendung des Cetex-Prepregs von TenCate hergestellt wird.
Ich glaube, manchmal vergessen wir, wie viel Erfahrung wir bereits mit der TPC-Technologie haben. In der Vergangenheit haben wir uns gefragt „Warum fliegen nicht mehr TPCs in Flugzeugen?“. Vielleicht können wir jetzt mit der Vorbereitung von Boeing auf das New Midmarket Airplane (NMA) und den Fortschritten der europäischen Flugzeugindustrie über Clean Sky 2 und andere Entwicklungsprogramme endlich eine neue Runde von Anwendungen in Betrieb nehmen.
Inzwischen gibt es bereits eine umfangreiche Lieferkette mit einer Reihe von Veteranen. Hier werde ich mit TenCate (vor kurzem von Toray übernommen), Teijin und Solvay Kontakt aufnehmen. Jeder hat eine andere Sichtweise, welche Polymere und Verarbeitungstechnologien Potenzial bieten.
TenCate – TPC-Veteran entwickelt die Technologie weiter
TenCate behauptet mehr als 40 Jahre Erfahrung bei der Entwicklung thermoplastischer Verbundwerkstoffe. Sein Cetex Marke ist bekannt für Prepreg und vorverfestigte Laminate (auch Organoblech genannt), erstreckt sich aber auch auf Bulk Molding Compound (BMC) sowie unidirektionale (UD) und gewebte Bänder. Das Unternehmen hat eine lange Erfolgsgeschichte mit dem kompletten Sortiment an Thermoplasten (siehe Grafik unten) und hat jetzt Low Melt Polyaryletherketone (LM PAEK) hinzugefügt ). Diese Materialien werden in Anwendungen verwendet, die von TenCates Aerospace- und Industrial-Divisionen unterstützt werden, sowie in Massenmarktprodukten wie Unterhaltungselektronik und Sportschuhen über die Performance Composites-Division des Unternehmens.
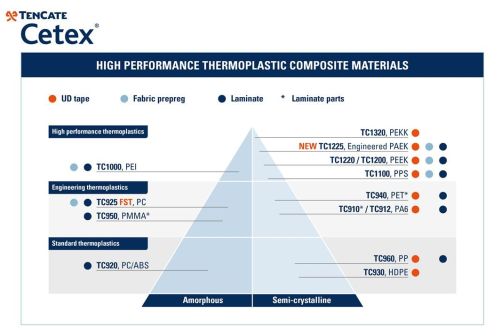

Thermoplastische Cetex-Bänder sind in einer Vielzahl von Matrixpolymeren erhältlich, die von niedrigerer Schmelztemperatur/niedrigerer Leistung bis hin zu höherer Schmelztemperatur/höherer Leistung reichen.
QUELLE:TenCate (oben), Tri-Mack Plastics Mfg. Corp . (Unterseite)
mit PEEK, PAEK von CW hinzugefügt.
Während der Interviews für meine Serie über in-situ-konsolidierte Thermoplaste wurde Low Melt PAEK als potenzielle Alternative genannt zu Polyetherketonketon (PEKK) und Polyetheretherketon (PEEK) auf der Suche nach einer schnelleren Verarbeitung. Als ich TenCate danach fragte, fasste Dr. Hans Luinge, Direktor der Forschung und Produktentwicklung für thermoplastische Verbundwerkstoffe bei TenCate, den Unterschied in den Schmelztemperaturen zusammen :
- TC1225 Kohlefaser (CF)/LM PAEK-Band 305 °C
- TC1320 CF/PEKK-Band 340 °C
- TC1200 CF/PEEK-Band 350°C
Beachten Sie, dass die tatsächlichen Temperaturen bei der Verarbeitung dieser Verbundbänder höher sein können, aber TC1225 LM PAEK ist aufgrund seines viel niedrigeren Schmelzpunkts immer noch attraktiv.
„Cetex TC1225 LM PAEK wurde in TAPAS1 eingeführt Entwicklungsprogramm, an dem wir maßgeblich beteiligt waren“, erinnert sich Luinge. Es verwendet das PAEK-Polymer von Victrex, und er weist darauf hin, dass bis 2013 , das Material TC1225 wurde bereits in einer Demonstrationsflugzeugstruktur verwendet . Airbus Nantes stellte einen Rumpf aus Paneel mit integrierten Versteifungen auf der Paris Air Show 2013. Es wurde mit dem von TenCate gelieferten CF/LM PAEK-Band mit pressgeformten Omega- und stumpf verbundenen T-Stringer-Elementen hergestellt, die mit der Haut verschweißt wurden und mit automatischer Faserplatzierung hergestellt wurden (AFP).
„Low-melt PAEK eignet sich gut für AFP, Stanzformen und Schweißen“, sagt Scott Unger, Global Chief Technology Officer von TenCate. Aber mit der unteren Schmelze Temperatur, sind nicht die mechanischen Eigenschaften für LM PAEK niedriger als PEKK und PEEK? Unger sagt nein, sie sind alle ungefähr gleich . „PEEK, PEKK und LM PAEK sind alles gute Konstruktionsmaterialien, und aus Kostensicht ist TC1225 preislich konkurrenzfähig mit TC1200 CF/PEEK und kostengünstiger als TC1320 PEKK.“
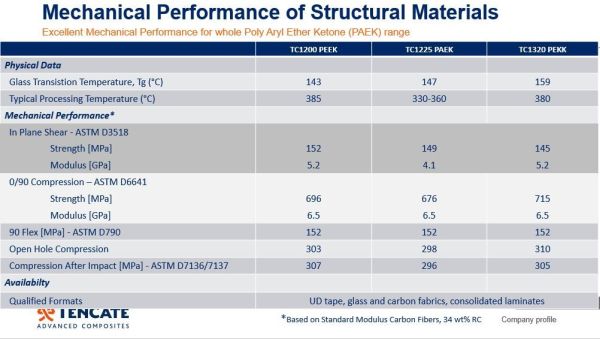
Niedrigschmelzendes PAEK beschleunigt die In-situ-Konsolidierung
Darüber hinaus verspricht TC1225 LM PAEK eine In-situ-Konsolidierung, die laut Unger „potenziell der Heilige Gral ist. In der Vergangenheit haben wir jedoch festgestellt, dass Ihre AFP-Geschwindigkeiten muss sehr langsam sein, um eine In-situ-Konsolidierung zu erreichen .“ Er erklärt:„Sie können keine in-situ-Konsolidierung erreichen, ohne ein Klebeband zu verwenden, das einen viel niedrigeren Hohlraumgehalt aufweist, als es im endgültigen Laminat oder der endgültigen Struktur akzeptabel ist. Es gibt zwei Schlüsselfaktoren :Tape-Qualität und wie gut Matrixharz und Faser im UD-Tape verteilt sind.“ Unger behauptet, dass die Herstellungsverfahren für UD-Klebebänder von TenCate darauf ausgelegt sind, extrem niedrige Hohlräume zu erzeugen, um Prozesse wie schnelles AFP gefolgt von nur außerhalb des Autoklaven/Vakuumbeutels zu ermöglichen (OOA/VBO)-Konsolidierung sowie einstufiges, in-situ-konsolidiertes AFP.
„Unser Klebeband ist extrem konsistent mit 0 bis 0,5 % maximaler Lücken “, sagt Winand Kok, TenCate Director of Expert Services EU. „Unsere Banddicke ist auch sehr konsequent , weshalb wir bei konsolidierten Laminaten sehr genaue Lagendicken erzielen können. Diese Beständigkeit ist auch für thermoplastische Schweißprozesse und die in-situ-Konsolidierung wichtig.“ Unger kommt auf die zweite Anforderung zurück, die er oben skizziert hat:„LM PAEK hat einen viel besseren Fluss gegenüber PEKK und PEEK. Es kann auch mit höheren Geschwindigkeiten verarbeitet werden als PEKK und PEEK.“
Dieser letzte Punkt wurde in einem Laminat-zu-Laminat-Vergleich gezeigt . „Wir haben TC1320 CF/PEKK-Laminate hergestellt mit einer Coriolis-Laser-AFP-Maschine im ThermoPlastic Composites Research Center (TPRC) in Twente, Niederlande“, sagt Unger, „mit hoher Geschwindigkeit von 600 mm/s . Wir haben dann konsolidiert dieses Laminat nur mit Staubsauger In einem Ofen." Er räumte ein, dass es aufgrund des schnellen AFP-Layups zwischen den Lagen Porosität gab, aber diese Hohlräume wurden während des zweiten Konsolidierungsschritts beseitigt, der in den Mikrophotographien des Laminats veranschaulicht ist. „Wir haben das TC1320-Material auch mit 200 mm/s faserverlegt und stellte fest, dass die Porosität zwischen den Lagen wurde nicht eliminiert mit der langsameren Geschwindigkeit. Wir haben dann ein gleichwertiges Laminat mit derselben AFP-Maschine hergestellt, diesmal jedoch mit TC1225 CF/LM PAEK Tape ohne sekundären OOA/VBO-Konsolidierungsschritt – d. h. vollständige In-situ-Konsolidierung über AFP. Wir haben die gleichen Konsolidierungseigenschaften erreicht wie beim 2-stufigen PEKK-Panel.“
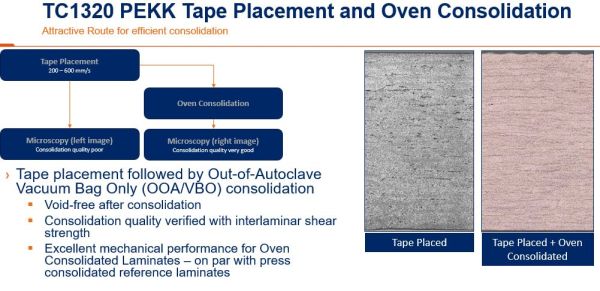

CF/PAEK, hergestellt mit AFP in-situ-Konsolidierung (kein zweiter Schritt) zeigte die gleichen Konsolidierungseigenschaften wie CF/PEKK, hergestellt mit schneller AFP + Konsolidierung im Ofen (oben). QUELLE:TenCate
Unger notiert die AFP-Geschwindigkeit von 200 mm/s für die in-situ konsolidiert CF/PAEK-Laminat ist mehr als zweimal das behauptete Henri de Vries, leitender Wissenschaftler, Verbundwerkstoffe, in der Abteilung für Strukturtechnologie des Niederländischen Zentrums für Luft- und Raumfahrt (NLR, Amsterdam), in meinem Artikel „Consolidating Thermoplast Composite aerostructures in place, Part 2“:
„Jetzt prüfen wir, wie weit wir pushen können die in-situ-Konsolidierung AFP-Geschwindigkeit unter Beibehaltung akzeptabler Porenwerte und mechanischer Eigenschaften innerhalb des Laminats“, sagt Unger. „Wir haben viel daran gearbeitet, eine versteifte TPC-Platte mit automatisierten Prozessen zu verlegen. Jetzt besteht das Ziel darin, die Technologiereife aufzubauen .“ Kok sagt, dass TenCate dies weiterhin tut und mit Industriepartnern zusammenarbeitet, darunter Kunden und F&E-Institute. Ein Beispiel war der Motormast hergestellt mit TC1320 CF/PEKK Tape auf dem TenCate-Stand auf der JEC 2018 ausgestellt. TenCate arbeitete sowohl mit dem Pylon-Schalenhersteller NLR als auch mit Dutch Thermoplastic Components (DTC) zusammen, die pressgeformte Rippen als Versteifungselemente an die Schale geschweißt haben. Obwohl dieses Teil unter Verwendung von AFP hergestellt und dann in einem Autoklaven konsolidiert wurde, stellt Kok fest:„Wir untersuchen auch, wie wir Bänder für die zweistufige Konsolidierung weiter optimieren können, indem nur Vakuumbeutel in einem Ofen anstelle eines Autoklaven verwendet werden.“

Geschlitztes CF/LM PEKK-Band, Laminat hergestellt mit automatisiertem Tapelegen (ATL) und einer pressgeformten Rippe, hergestellt von DTC. QUELLE:www.composites.nl
Unger weist darauf hin, dass die CF/LM PAEK-Produkte von TenCate, die bei der Entwicklung und Demonstration von primären Flugzeugstrukturen verwendet werden, tatsächlich sowohl Kohlenstofffasern ohne Größe verwenden sowie Kohlefaser mit Schlichte . Er sagt, dass es vor fünf Jahren ungewöhnlich gewesen sein mag, LM PAEK-, PEKK- und PEEK-Prepreg-Bänder zu sehen, die Kohlefasern mit verwendeten Schlichten aufgrund nachteiliger Auswirkungen auf die mechanischen Eigenschaften, die mit den Schlichten verbunden sind, ist dies sicherlich nicht mehr der Fall heute.
Ein letzter Punkt, der das Potenzial von LM PAEK unterstreicht, ist, dass NIAR und die FAA dabei sind, die erste öffentliche Datenbank für einen thermoplastischen Verbundwerkstoff zu erstellen , unter Verwendung des TC1225 CF/LM PAEK von TenCate. Die Datenbank soll Anfang nächsten Jahres veröffentlicht werden und dieses Material wurde aufgrund seiner mechanischen Eigenschaften und seiner einfachen Verarbeitung ausgewählt.
Teijin – Langjähriger CF-Produzent steigt in TPCs ein
Der Kohlefaserhersteller (CF) Toho Tenax Co. Ltd. (Tokio, Japan) wird jetzt weltweit in Teijin Carbon umbenannt, mit drei großen Tochtergesellschaften:
- Teijin Carbon Europe
- Teijin Carbon America
- Teijin Carbon Singapur.
Der Produktname bleibt Tenax.
„Wir haben vor 15 bis 20 Jahren viel Zeit in die Entwicklung von Thermoplasten investiert“, sagt Jean-Philippe Canart, zuvor Produktmanager für Thermoplasthalbzeuge bei Toho Tenax Europe und jetzt Marktingenieur für Luft- und Raumfahrt bei Teijin Carbon America. „Eine unserer Strategien war die Entwicklung eines unidirektionalen (UD) thermoplastischen Klebebands , die wir 2013 eingeführt haben .“
Canart erklärt die Bausteine für diese Entwicklung:„Eine unserer Kerntechnologien ist die thermoplastische Schlichte für CF . , die bei der Bandverarbeitung hilft. Aufgrund der hohen Verarbeitungstemperaturen für Thermoplaste muss die übliche CF-Leimung entfernt werden. Neben der Temperaturbeständigkeit bietet die thermoplastische Schlichte auch eine zusätzliche Leistung mit Faser-zu-Matrix-Adhäsion im fertigen Verbundwerkstoff. Eine unserer größten Linien in Europa produziert 1.700 Tonnen CF pro Jahr, die mit TP-Schlichtung ausgestattet sind. Daraus entwickelten wir UD-Tape mit PEEK, PEKK und PPS thermoplastische Matrizen für den Einsatz hauptsächlich in Luft- und Raumfahrtanwendungen, aber wir arbeiten auch an Öl- und Gas- und Industrieanwendungen.“
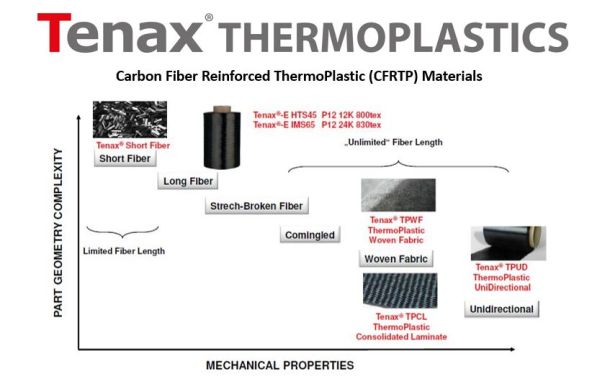
QUELLE:Teijin .
Canart sagt, dass Teijins erster Schwerpunkt bei TPC auf dem Pressformen (Stanzen) von Clips und Halterungen für den Airbus A350 mit PEEK-beschichtetem CF-Gewebe lag :„Dies war die erste große Welle von Anwendungen in der Luft- und Raumfahrt. Wir sehen, dass sich dies jetzt auf größere, strukturellere Teile verlagert, die mit einer Mischung aus AFP-Laminaten hergestellt werden, gefolgt von einer Konsolidierung durch Stanzen.“ Canart räumt ein, dass sich die In-Situ-Konsolidierung (ISC) seit Jahrzehnten in der Entwicklung befindet, behauptet jedoch:„Wir sehen sie noch nicht als ausgereift an. Wir unterstützen F&E-Projekte und Institute bei der Weiterentwicklung.“ ISC sei möglich, sagt er, „aber die Frage ist, wie schnell können Sie Teile herstellen? Und wie robust ist der Prozess?“ Er glaubt, dass es 2025-2030 dauern wird, bis ISC-Teile für kommerzielle Flugzeuge produziert werden . In der Zwischenzeit sieht Teijin eine Expansion bei TPC-Bändern für 2-stufige AFP + Stanzproduktionslinien. „Wir haben bereits in unsere europäische Bandlinie investiert und unterstützen auch neue Prozesskapazitäten wie Continuous Compression Moulding (CCM) . Die Lieferkette wächst.“
Unterstützung der TPC-Massenproduktion – CCM
Kontinuierliches Formpressen (CCM) ist ein Verfahren, über das ich 2010 geschrieben habe:„Aerospace-grade Compression Moulding“. Es ist als X-CCM von Performance Polymer Compositesxperion (Markdorf, Deutschland) geschützt, dem Unternehmen, das das Verfahren vor über zwei Jahrzehnten ursprünglich entwickelt und vermarktet hat. X-CCM bietet hochwertige thermoplastische Verbundlaminate in einem schnellen, quasi-kontinuierlichen Verfahren. „Wir arbeiten mit xperion als Materiallieferant zusammen“, sagt Canart. „Dies ist eine ausgereifte Technologie , wird seit vielen Jahren bei Airbus und Boeing verwendet . Jetzt wächst es wirklich und wird verwendet, um geformte konsolidierte Laminate herzustellen. CCM ist günstig, aber der Querschnitt muss konstant bleiben.“
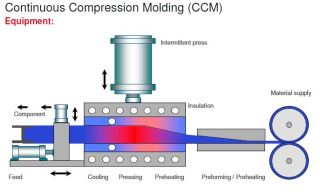
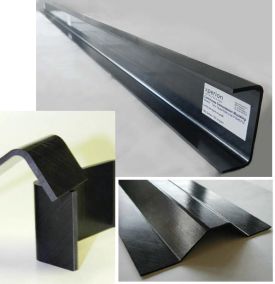
Teijin unterstützt das Wachstum bei TPC-Band- basierte Teilefertigungsprozesse wie Continuous Compression Moulding (CCM), das von xperion PPC kommerzialisiert wird.
QUELLE:Teijin, SAMPE Seattle 2014.
Laurens de la Ossa, Senior Sales Manager bei xperion PPC, sagt:„Unser X-CCM-Verfahren ist jetzt fortschrittlicher und kann komplexere Formen herstellen, darunter asymmetrische Profile wie T- und J-Profile .“ Er fügt hinzu, dass mit dem Verfahren konsolidierte TPC-Laminate mit einer Breite von bis zu 24 Zoll hergestellt werden können. „Wir sind Teil einer ganzen Technologieinfrastruktur, die sich auf die Massenproduktion von thermoplastischen Verbundwerkstoffen zubewegt . Wir haben ein sehr schlankes Verfahren für konsolidierte TPC-Teile – es gibt keine Vakuumverpackung und wir können dicke Laminate von 60 Lagen und mehr verarbeiten , 8-10 mm dick.“
Auf welche Art von Teilen zielt X-CCM ab? „Innere Rumpfwangen, Bodenträger und andere Rahmen um den Boden oder die Decke, Strukturkomponenten und halbstrukturelle Anwendungen, die die höchste Materialleistung erfordern“, sagt de la Ossa. „Bis 2025 , wenn die neuen Flugzeugplattformen in Produktion gehen, werden wir das 6- bis 10-fache der Materialmenge erreichen jährlich nur um zu liefern, worauf wir bisher mit Angeboten geantwortet haben.“
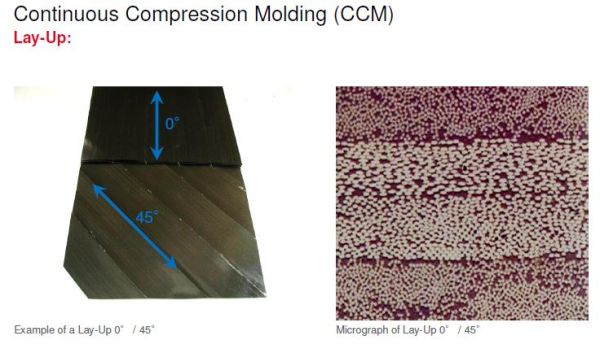
QUELLE:Teijin , SAMPE Seattle 2014
Als Teil dieses kontinuierlichen Strebens nach einer höheren Volumenproduktion konzentriert sich Teijin auf die Reduzierung der Bandmaterialkosten und die Erhöhung der Kapazität , sagt Canart. Was ist mit den Forderungen der Branche nach dickem Klebeband ? Konkret hatte de Vries vom NLR gesagt:
„Wir haben bereits Tapes mit Faserflächengewichten von 145 bis 200 g/m 2 entwickelt “, antwortet Canart. „Bei diesen Produkten ist eine Dicke von .18 mm schon ganz normal für uns. Wir haben unsere Leinen für diese Stärke und auch auf 0,20 mm angepasst, daher denke ich, dass 0,25 mm auch kein großer Sprung wären.“
Und was ist mit der Bandqualität ? „Wir glauben, dass alle Bänder für höherwertige Teile bei höheren Geschwindigkeiten modifiziert werden müssen“, sagt Canart. „Der Harzgehalt entspricht möglicherweise nicht dem, was die in-situ-Konsolidierung erfordert, und die Verteilung des Harzes innerhalb des Bands muss möglicherweise ebenfalls optimiert werden. Die Schmelzzeit und -geschwindigkeit ist für die verschiedenen Harze und Verfahren so unterschiedlich. Wir unterstützen die weitere Entwicklung in einer Vielzahl von Bereichen, einschließlich der Polymersysteme und der Architektur des Bandes , einschließlich der Oberfläche.“
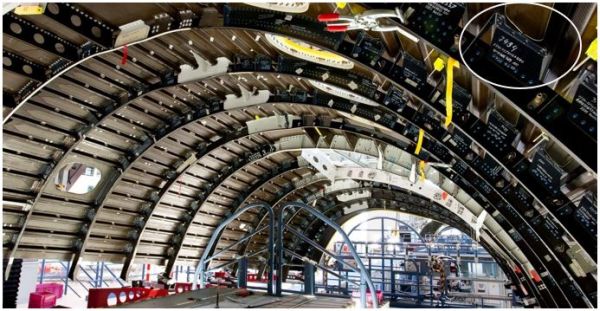
Airbus A350 Rumpf Clip aus TenCate Cetex C/PPS thermoplastischen Laminaten mit Tenax ThermoPlastic Woven Fabric (TPWF). QUELLE:Teijin, Premium Aerotec Group.
Solvay — Markt für PEEK und PEKK
Zu den thermoplastischen Hochleistungsprodukten von Solvay für Verbundwerkstoffe gehören Ketaspire PEEK , Novaspire PEKK , Radel Polyphenylsulfon (PPSU ) und Ryton Polyphenylensulfid (PPS ). In einer von Solvay eingereichten Erklärung behauptet das Unternehmen, dass diese Polymere im industriellen Maßstab hergestellt werden Dies ermöglicht die Berücksichtigung großvolumiger Verbundanwendungen in der Luft- und Raumfahrt und kann zur Herstellung hochwertiger Prepregs verwendet werden .
Solvay bietet derzeit APC Unitape . an Prepregs mit PEEK- und PEKK-Polymeren, mit vorwiegend differenzierter Preisgestaltung nach den Kosten der ausgewählten Faser statt Polymer wenn sie in großen Mengen produziert und verwendet werden. Daher ist es der Ansicht, dass die Auswahl der für eine bestimmte Anwendung zu verwendenden thermoplastischen Matrix durch die Kundenpräferenz gesteuert wird . Zu den Faktoren, die diese Wahl beeinflussen, gehören Temperaturleistung, mechanische Leistung, Verarbeitung der Teilefertigung, Verfügbarkeit der Materialdatenbank und Erfahrung der Mitarbeiter, um nur einige zu nennen. Solvay ist der Ansicht, dass sowohl PEKK als auch PEEK einen Bedarf decken auf dem Markt ist und in der Lage ist, faserverstärkte Prepregs in hoher Qualität zu vergleichsweise günstigen Preisen anzubieten, unabhängig davon, welches Polymer gewählt wird.
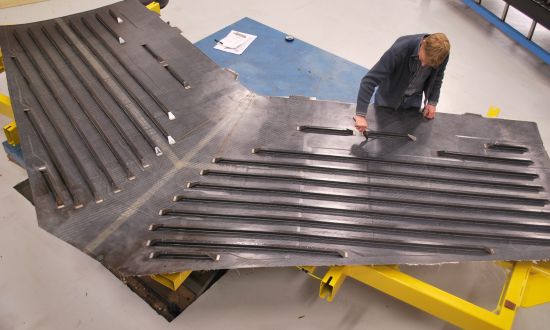
Flugzeug-Horizontalleitwerk Demonstrator hergestellt von GKN Fokker mit
Solvay APC(PEKK-FC)/AS4D. QUELLE:GKN Fokker.
Bei Thermoplasten, wie bei allen anderen Verbundwerkstoffen, ist die Auswahl an Materialien und Verfahren also nicht eingeschränkt. Tatsächlich scheinen sie sich auszudehnen. Welcher wird in der zukünftigen Flugzeugproduktion an Bedeutung gewinnen? Das wird sich noch zeigen. CW werde weiter beobachten und berichten, was wir sehen.
Harz
- Was ist Formpressen und wie funktioniert es?
- Formpressen:So funktioniert es
- Formpressen und Gießen:Vor- und Nachteile
- Hochviskoses PEEK für Spritzguss und Extrusion
- Victrex- und Bond-Partner für den 3D-Druck von PAEK-Teilen
- Thermoplastumspritzte Duroplaste, 2-Minuten-Zyklus, eine Zelle
- Kontinuierliche Bänder, D-LFT treffen in neuem Formpressverfahren zusammen
- TPAC und TPRC entwickeln Recyclingprozess für thermoplastische Verbundwerkstoffe
- EconCore arbeitet mit MEAF bei kontinuierlichen thermoplastischen Wabenkernen zusammen
- RTP Company entwickelt leichte und zähe thermoplastische Compounds