Warum Origin One für den 3D-Druck von Produktionsteilen verwendet wird
Der Origin One ist ein neuer harzbasierter 3D-Drucker von Stratasys. Es ist ab sofort verfügbar und die Einheiten werden weltweit ausgeliefert. Stratasys ist kein Unbekannter im Drucken mit Harzproduktionsteilen. Ihre Polyjet-Technologie druckt seit vielen Jahren hochdetaillierte Visualisierungsmodelle, genaue und spezialisierte Werkstatthilfen sowie medizinische Modelle. Dies ist jedoch das erste fassbasierte Harzsystem, das dem Stratasys-Portfolio hinzugefügt wurde, und es hat einen drastisch anderen Anwendungszweck.
P3-Technologie eignet sich hervorragend für Produktionsteile
Der Origin One wird von der programmierbaren Photopolymerisationstechnologie oder P3 angetrieben. P3 verwendet einen 4K-Projektor, um die gesamte Schicht bei jedem Zyklus teilweise auszuhärten. Anschließend werden die Teile in einer UV-Kammer vollständig ausgehärtet. Es verfügt über einen einzigartigen pneumatischen Trennmechanismus, der verhindert, dass Teile am Boden des Bottichs kleben, was ein entscheidender Grund dafür ist, warum der Origin One sowohl bei großen, blockigen Teilen als auch bei hochdetaillierten, komplizierten Teilen hervorragend ist. Stratasys hat sich mit großen Materialherstellern wie DSM und Henkel zusammengetan, um eine breite Palette von Hochleistungsharzen anzubieten. Neue Materialien werden ständig von Stratasys zertifiziert und eine Open Materials License ist verfügbar, um die Maschine für Forschung und Tests vollständig freizuschalten.
Angesichts der in allen Branchen grassierenden Lieferkettenprobleme suchen Unternehmen nach einer kostengünstigen, agilen Lösung, um den sich ständig ändernden Anforderungen ihrer Kunden gerecht zu werden. Der Origin One ist gut aufgestellt, um diese Probleme zu lösen, indem er Endverbraucherteile in Produktionsqualität aus einer Vielzahl von Materialien und eine Maschine bereitstellt, die den Benutzern die volle Kontrolle über ihre Prozesse gibt. Mehr Materialien bedeuten mehr Anwendungen. Wie nutzen Unternehmen diese leistungsstarke Technologie?
Origin One-Materialien
Derzeit werden mehr als 12 Materialien zum Start verfügbar sein, weitere werden folgen. Die Anwendungen des Origin One können fast endlos erscheinen. Benutzer finden regelmäßig neue und einzigartige Möglichkeiten, diese Maschine zu nutzen. Eines der leistungsstärksten Materialien in Bezug auf die mechanischen Eigenschaften ist 3955 der Marke Loctite von Henkel. Es hat eine sehr hohe Temperaturbeständigkeit (HDT> 300C), eine hohe Steifigkeit und erfüllt Flammen-, Rauch- und Toxizitätsstandards für anspruchsvolle Anwendungen in der Luft- und Raumfahrtindustrie. Schauen wir uns ein Unternehmen an, das dieses Material bereits für seine Endverbraucherteile verwendet:TE Connectivity.
Luft- und Raumfahrtanwendung
TE Connectivity entwickelt und fertigt Steckverbinder und Sensoren für raue Umgebungen. Sie haben sich zum Ziel gesetzt, eine sicherere, nachhaltige, produktive und vernetzte Zukunft zu schaffen, indem sie Lösungen anbieten, die Elektrofahrzeuge, Flugzeuge, digitale Fabriken und Smart Homes antreiben. Im vergangenen Jahr trat einer ihrer bestehenden Kunden aus der Luft- und Raumfahrt an sie mit einer Bitte heran, die sie nicht verpassen wollten:Stecker und Halterungen für einen Helikopter. Diese Anfrage war mit einzigartigen Herausforderungen verbunden, da die Steckverbinder noch nie zuvor entworfen oder hergestellt wurden. Die Zeit- und Volumenanforderungen an einen Halter in Produktionsqualität führten dazu, dass herkömmliche Herstellungsmethoden und Entwicklungszeitpläne sowohl für TE Connectivity als auch für seinen Kunden unzureichend waren. Die Materialwahl war eine weitere Hürde. Der FDM-3D-Druck könnte die erforderlichen mechanischen Eigenschaften wie hohe Hitze- und Flammschutzeigenschaften bereitstellen, wäre jedoch nicht in der Lage, die Genauigkeit von +/- 0,002 Zoll zu erreichen. Es gab nur eine Lösung, um den hohen Anforderungen ihrer Kunden gerecht zu werden:die Origin One.
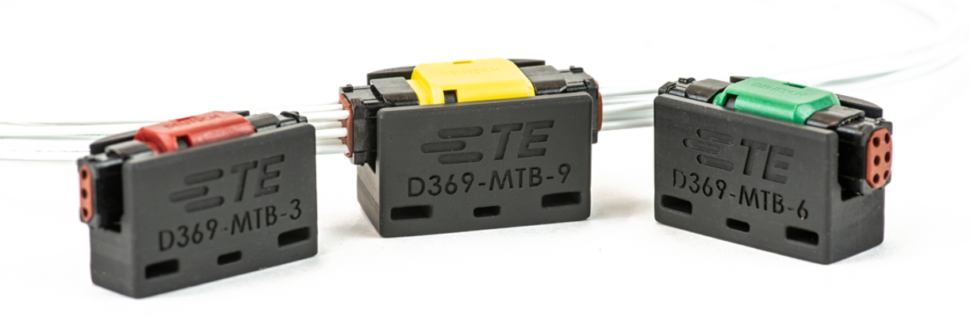
Heute sehen wir, wie Hardware, Software und Materialien von Stratasys wirklich zusammenkommen, um den Produktionsmaßstab für uns Realität werden zu lassen. Wir glauben, dass dies dazu beiträgt, TE Connectivity zu einem agileren und kostengünstigeren Partner für viele der weltweit führenden OEMs in Branchen von der Automobilindustrie über die Luft- und Raumfahrt bis hin zu Haushaltsgeräten zu machen, während wir an einer stärker vernetzten Zukunft arbeiten.
Mark Savage, Senior Manager, Additive Manufacturing von TE Connectivity
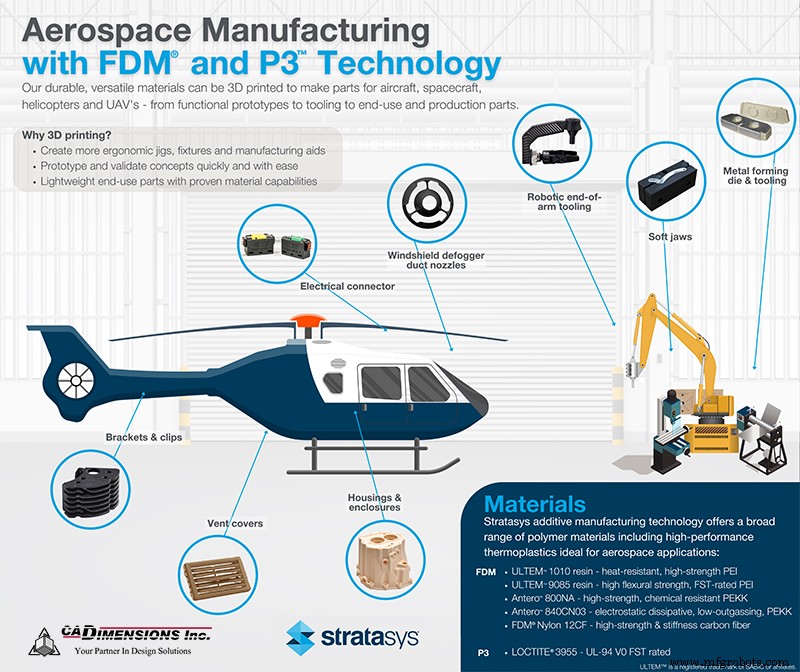
Klicken Sie hier, um die ganze Geschichte zu lesen oder das Video anzusehen!
Produktionsteile für medizinische Anwendungen
Eine weitere Branche, die strenge Anforderungen und Vorschriften hat, die der Origin One erfüllen kann, ist die medizinische Industrie. Derzeit gibt es zwei medizinische Materialien von Henkel, die die Standards ISO 10993-5 und -10 für Biokompatibilität erfüllen, wenn sie mit einem validierten Workflow verarbeitet werden:MED412 und MED413. MED412 ist mäßig flexibel, duktil, hat eine hohe Schlagzähigkeit und kann mit medizinischem Polypropylen verglichen werden. MED413 ist ein vielseitiges technisches Material, das dem medizinischen ABS am ähnlichsten ist. Diese Materialien erschließen viele Anwendungen in der Entwicklung von Medizinprodukten.
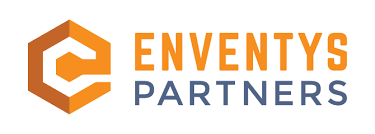
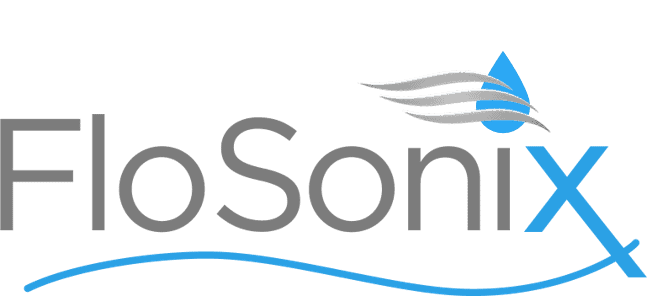
Ein Unternehmen, das bereits Medizinprodukte für den Endverbraucher unter Verwendung einer Kombination von Origin-Materialien produziert hat, ist Eventys Partners, eine Full-Service-Produkteinführungsagentur, die alle Aspekte der Produktentwicklung abwickelt. Sie haben Zugang zu einer Vielzahl von Herstellungsmethoden, daher kommt es nicht oft vor, dass ein Unternehmen mit einer Anfrage zu ihnen kommt, die ihre Fähigkeiten in Frage stellt. FloSonix, ein führendes Gerät zur Läusebekämpfung, wandte sich an Eventys mit einem neuen Design für ein Gerät zur Behandlung von Kopfläusen. Eventys war zunächst ratlos. Das Handgerät erforderte biokompatible und hitzebeständige Materialien, ein leichtes Design und strukturierte Griffe, alles mit einem ästhetisch ansprechenden Erscheinungsbild. FloSonix forderte jährlich 200 bis 300 Geräte an. Die Herausforderung bestand darin, dass die Teilegröße, Anzahl und Designkomplexität zu teuer und mit herkömmlichen Fertigungsmethoden schwer zu erreichen wären. Das bloße Entwerfen und Prototyping des Produkts selbst wäre zu teuer gewesen.
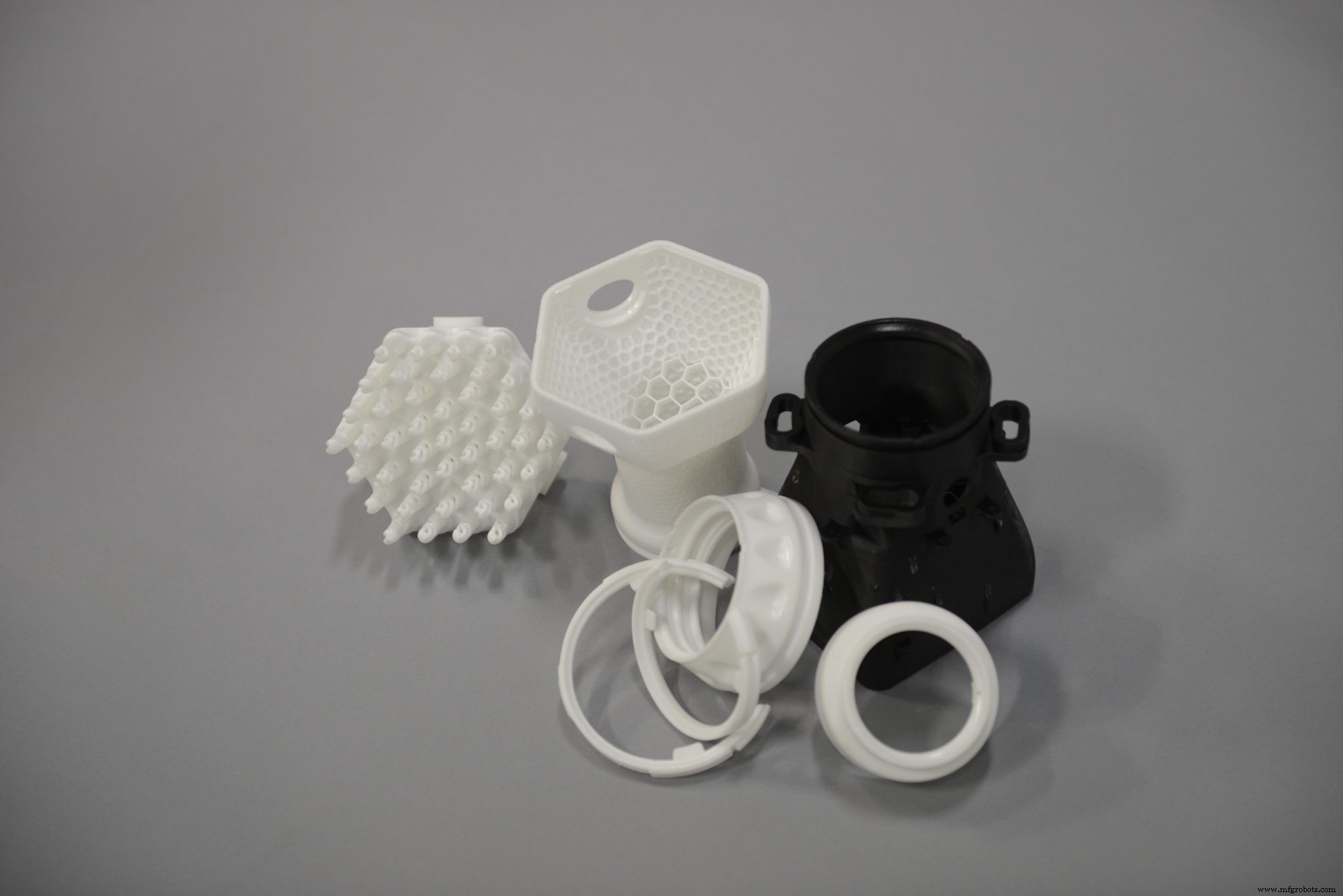
Daher suchte Eventys nach einer Lösung, die ihre Anforderungen an Prototyping und Endverbraucherproduktion erfüllt. Das Team konnte das Handheld-Gerät von FloSonix mit nur einem einzigen Origin One-Drucker von der Idee bis zur Produktion führen und benötigte nur einen zusätzlichen Drucker, um den jährlich erforderlichen Bestand von FloSonix zu decken.
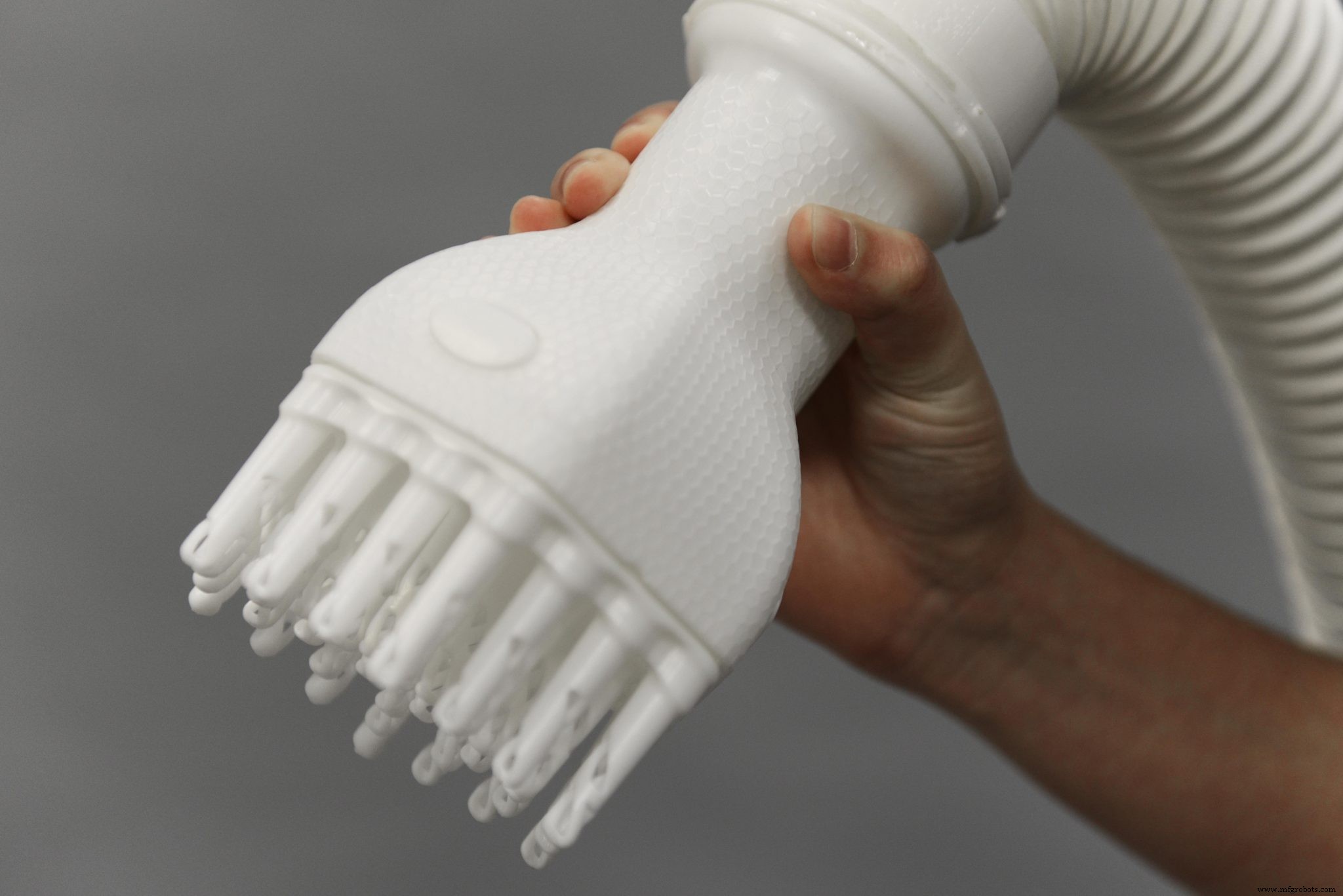
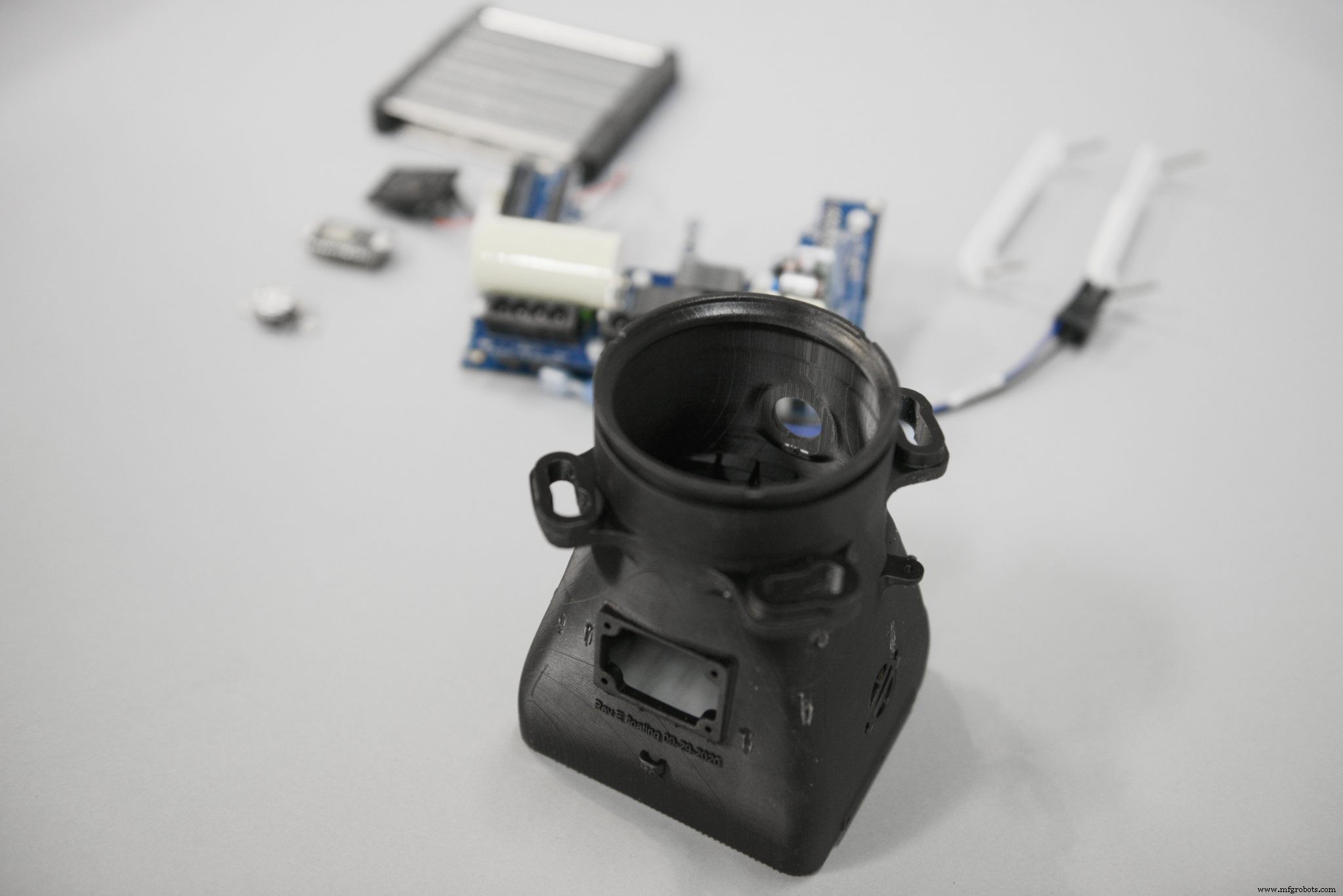
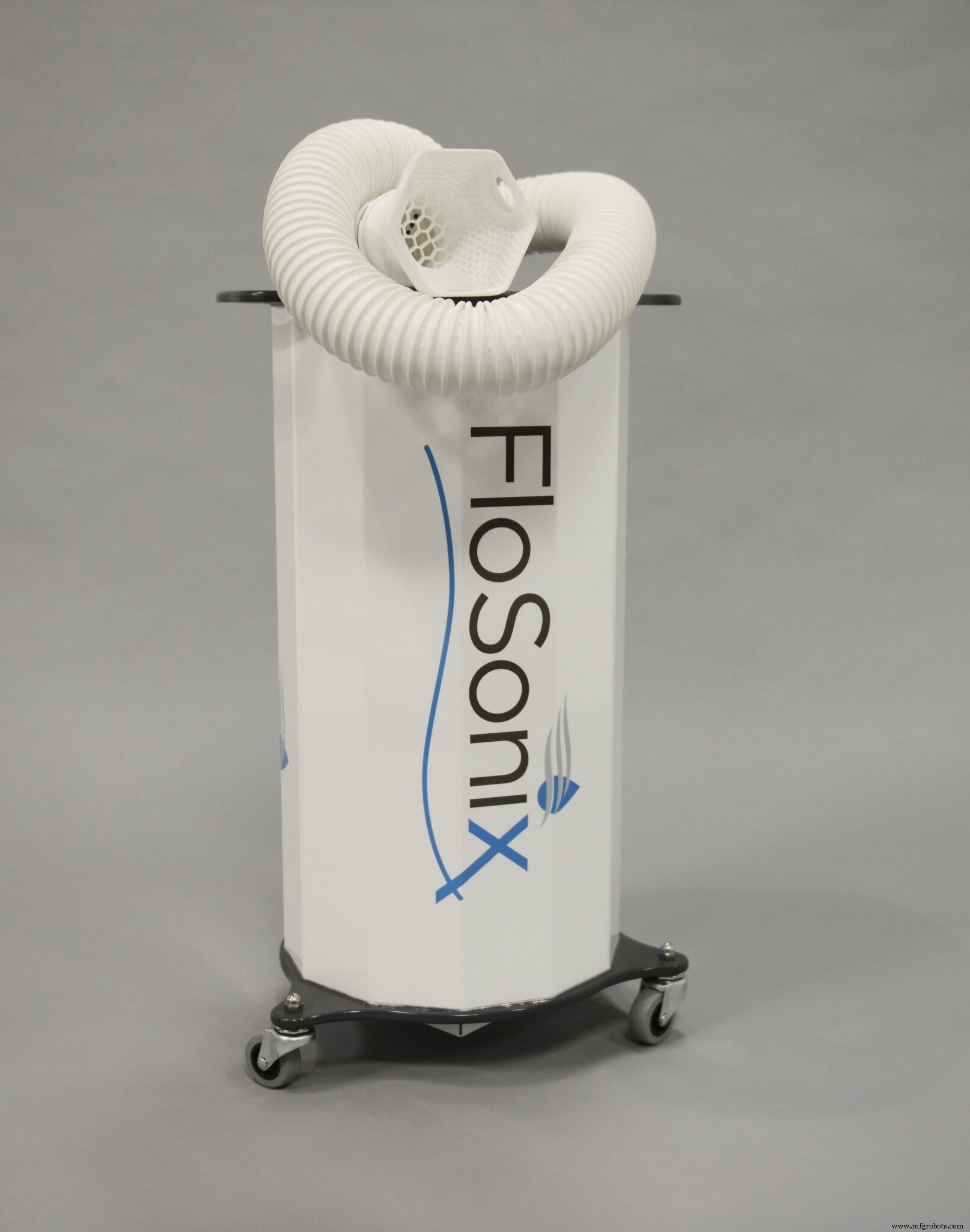
Der Origin One hat es uns ermöglicht, uns nicht nur an sich ändernde Lieferketten anzupassen, sondern unsere Entwicklung in Etappen zu planen; zum Beispiel veredeln wir das Produkt oft gerne in der Zukunft, aber nicht sofort. Die additive Fertigung ermöglicht es uns, inkrementell zu iterieren, ohne Formen nachschneiden, umrüsten oder übermäßigen Altbestand entsorgen zu müssen; Dies sparte uns sowohl Zeit als auch Kapital, das normalerweise bei Neukonstruktionen auf dem Spiel stehen würde.
TJ Root, Senior Design Engineer bei Eventys Partners
Klicken Sie hier, um die ganze Geschichte zu lesen!
Produktionsteile gedeihen in eisigen Umgebungen bei Sportausrüstungsanwendungen
Mit dem Origin One hört es nicht nur bei Luft- und Raumfahrt und Medizin auf. Eine weitere Branche, die den Wert kundenspezifischer 3D-gedruckter Teile in Produktionsqualität erkannt hat, sind Sportgeräte. Technologische Verbesserungen sind der Schlüssel zur Aufrechterhaltung der Wettbewerbsfähigkeit in der Welt der Sportgeräte, aber die Hersteller haben Schwierigkeiten, mit den sich ändernden Kundenanforderungen Schritt zu halten.
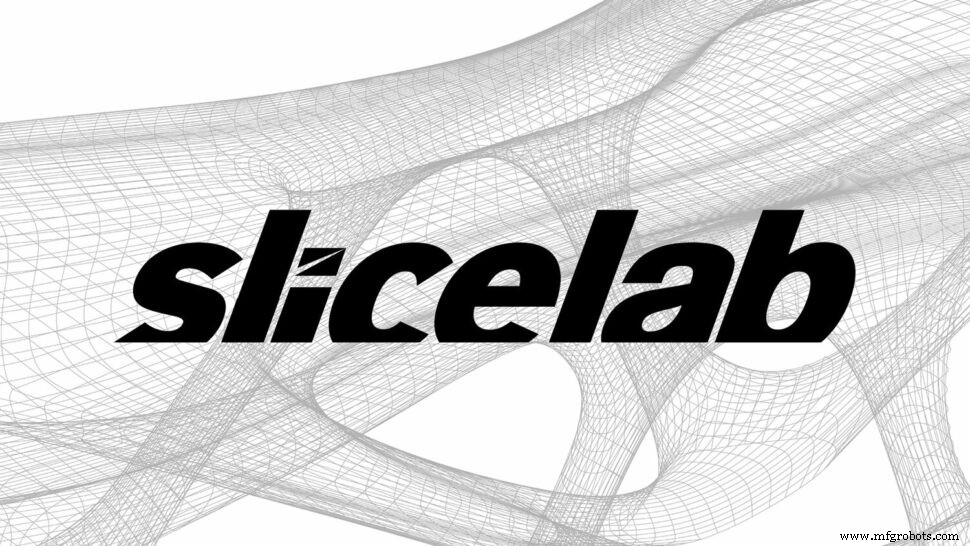
Die Designstudios Slicelab und f=f haben sich in Zusammenarbeit mit den Teams Stratasys Origin One und Henkel Loctite der Herausforderung gestellt, einen integralen Bestandteil von Snowboardbindungen neu zu erfinden:den hohen Rücken. Der hohe Rücken ist ein Teil einer Snowboardbindung, der die untere Wade des Fahrers unterstützt und ihm hilft, das Snowboard zu steuern. Je besser das Design des Teils, desto mehr Kontrolle hat der Fahrer. Der Origin One war eine klare Wahl für seine Fähigkeit, ausgedehnte Brücken und steile Überhänge ohne Qualitätseinbußen zu drucken. Eine interne Gitterträgerstruktur ermöglichte eine variable Flexibilität im gesamten Teil, die mit Spritzguss unmöglich zu erreichen wäre.
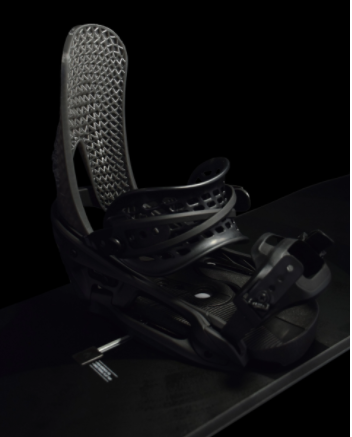
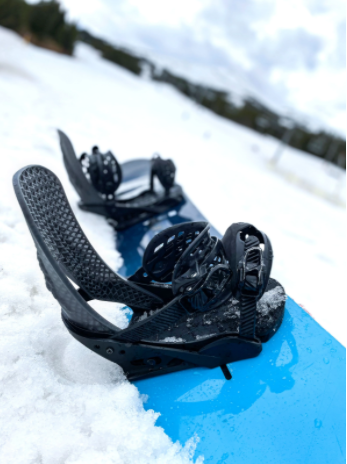
Das Materialteam von Origin One arbeitete direkt mit Slicelab und f=f zusammen, um Fehler bei Designiterationen zu beheben, einen perfekten Druck zu gewährleisten und das richtige hochwirksame, flexible und ästhetische Material auszuwählen. Sie haben sich für IND 3172 von Henkel Loctite entschieden, das über eine hervorragende Schlagzähigkeit und moderate Flexibilität verfügt. Der eigentliche Test war, als Einer der Gründer von Slicelab, Diego Taccioli, einen ihrer am Vortag gedruckten Highbacks auf seinem Snowboard installierte und auf die Pisten des Breckenridge Resort in Colorado ging. Sie haben genau wie gewünscht funktioniert.
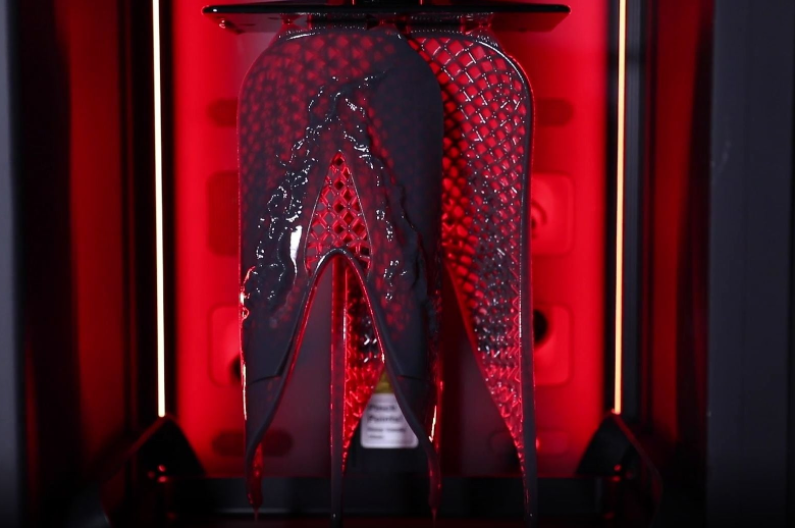
Da die additive Fertigung dort ist, wo sie heute ist, kann vorhergesagt werden, dass in Zukunft weniger Hardwarekomponenten oder Größenanpassungsfunktionen in Produkte eingebaut werden müssen. Die Möglichkeit, die mechanischen Eigenschaften des Materials in parametrische Software einzugeben, ermöglicht es uns, einfach ein paar Eingaben zu optimieren, um die Geometrie für jede Art von Leistungsunterschied zu generieren, nach der wir suchen, sei es ein ungezwungener Fahrtag oder ein intensiver Pulvertag .
Diego Taccioli, Mitbegründer von Slicelab
Klicken Sie hier, um die ganze Geschichte zu lesen oder drucken Sie sie aus!
Zusätzliche Anwendungen
Die oben genannten Fallstudien sind hervorragende Beispiele dafür, wie der Origin One heute für Endverbraucher-Produktionsteile verwendet wird, aber die Anwendungen reichen weit über diese drei hinaus. Hier sind einige Beispiele für andere Anwendungen, die alle auf dem Origin One von Stratasys gedruckt wurden.
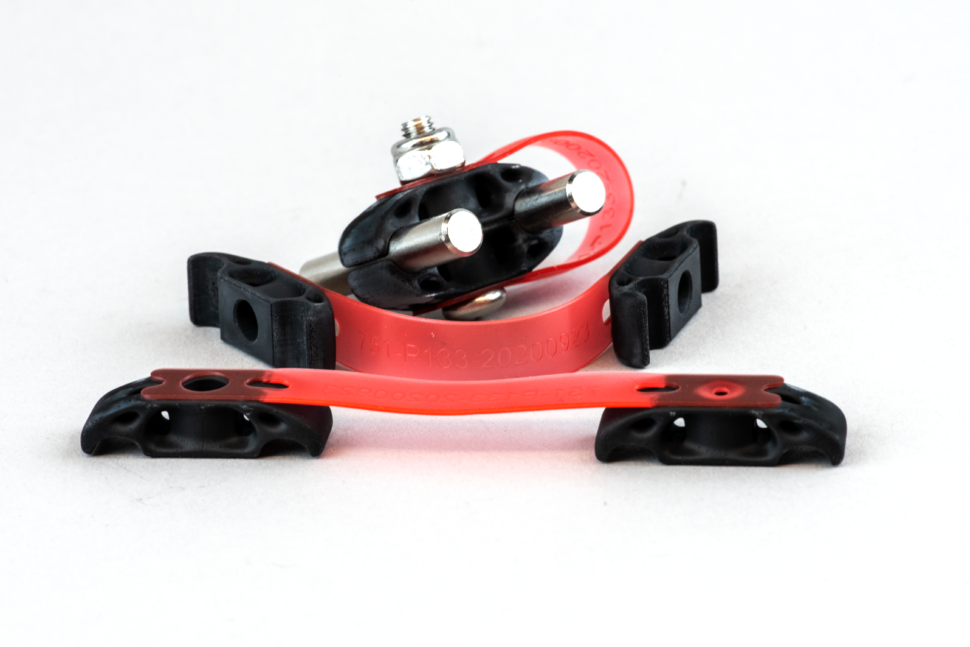
F16 Hydraulische Kabelklemme für Flugzeuge
Entworfen als Teil der Advanced Manufacturing Olympics der US Air Force RSO. Dieses Teil erforderte höchste Genauigkeit, während es heißen und kalten Temperaturen, Vibrationen, Entflammbarkeit und chemischen Belastungen standhalten konnte. Dieses auf dem Origin One gedruckte Design hat die doppelte Stärke des Originals und eine Gewichtsreduzierung von 5 %.
Material: Henkel 3955
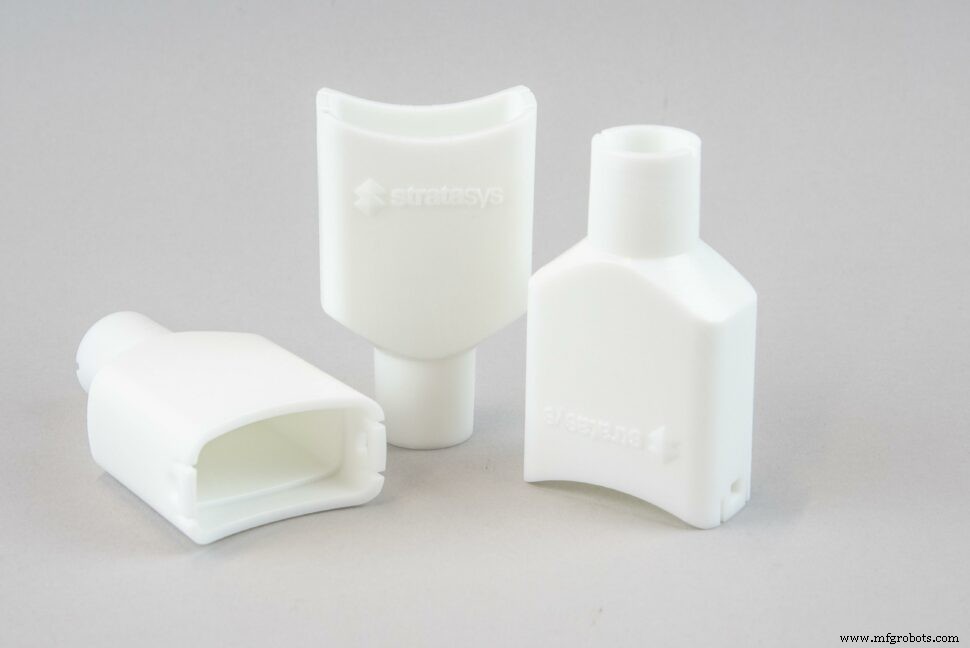
Atemschutzadapter
Wird verwendet, um den Luftstrom in einem Atemschutzgerät zu unterstützen und benötigte biokompatible Eigenschaften. Der weltweite Mangel an Atemschutzmasken aufgrund von COVID-19 führte zu einer hohen Nachfrage nach kritischen Produktionsteilen mit kurzen Vorlaufzeiten.
Material: Henkel MED413
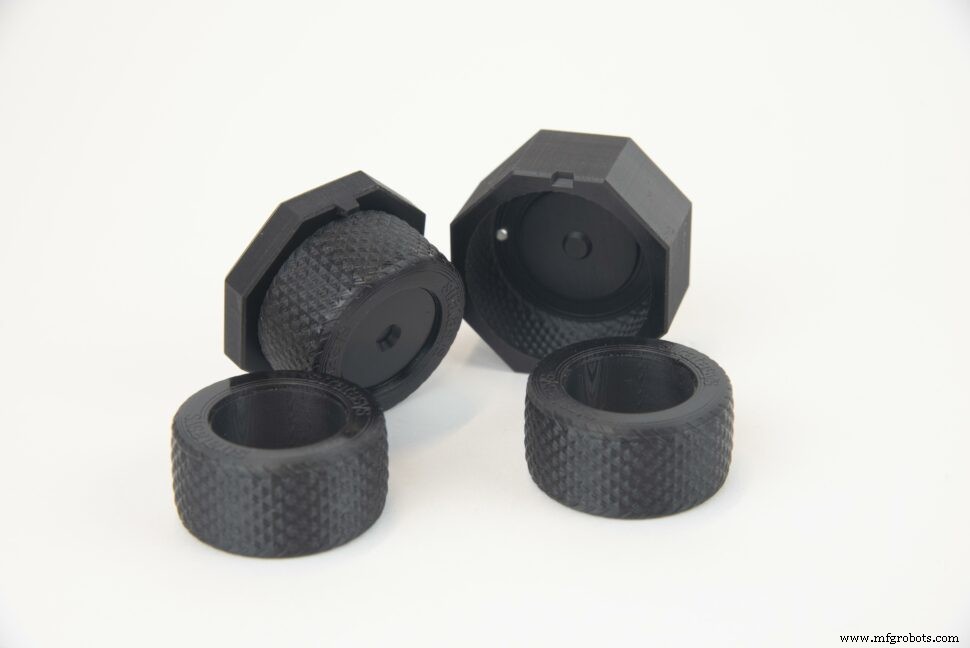
PU-Radform
Form für ein elastomeres Polyurethanrad, kompatibel mit einer Vielzahl von Formtrennmitteln und Urethan-Chemikalien, Formen haben über 1.500 Teile (und noch mehr) ohne Formverschlechterung produziert.
Material: Henkel IND403
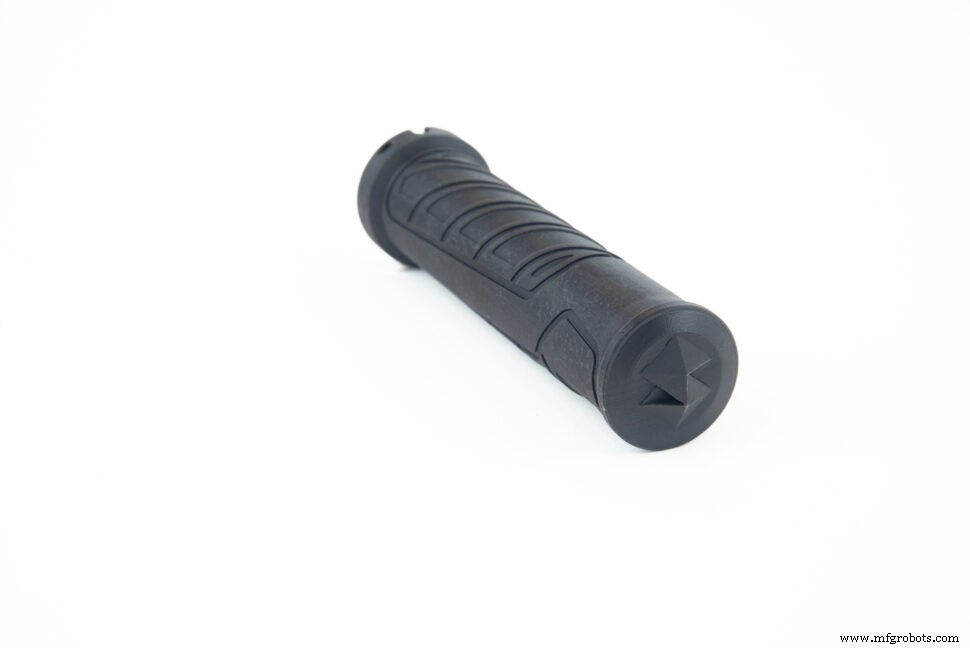
Fahrradlenkergriff
Lenkergriff erfordert Stoßdämpfung, Flexibilität und Dämpfungseigenschaften, um die beim Radfahren auftretenden mechanischen Stöße und Vibrationen in einem haltbaren, UV-stabilen Material zu absorbieren.
Material: Henkel IND402
The Bull Rider:90% der Produktionsteile werden auf dem Origin One 3D gedruckt
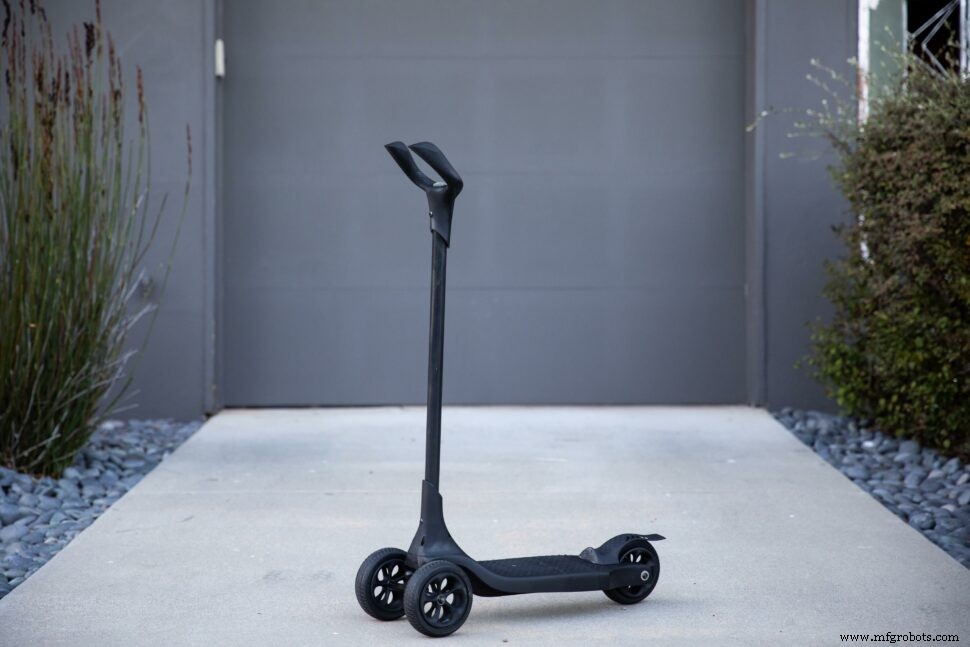
Und schließlich eines meiner persönlichen Lieblingsprojekte, das bisher vom Origin One stammt, der Bull Rider. Das neue Stratasys Dura56-Material von Loctite wurde auf die Probe gestellt, um einen funktionalen, langlebigen Tretroller zu schaffen, bei dem über 90% der Masse des Rollers aus 3D-gedruckten Teilen besteht. Das Origin One-Team hat sich mit Slicelab zusammengetan und in nur 81 Tagen vom ersten Brainstorming, drei Iterationen und dann erfolgreich ein fertiges Produkt erstellt. Alle Teile wurden in weniger als 48 Stunden mit 3 Druckern gedruckt.
Sehen Sie sich diese Infografik an, um mehr zu erfahren, oder sehen Sie sich das Video an, um es in Aktion zu sehen!
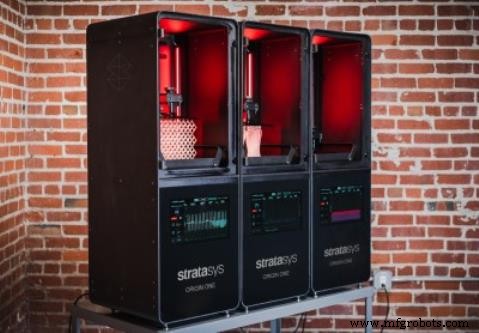
Erzielen Sie außergewöhnliche Genauigkeit.
Erfahren Sie mehr über diese erstaunliche Technologie und erzielen Sie eine außergewöhnliche Druckqualität
Origin One3d Drucken
- Warum CT-Scannen ein wichtiger Bestandteil des erfolgreichen 3D-Drucks wird
- Emirate übernehmen 3D-Drucktechnologie für Flugzeugteile
- Ist der 3D-Druck bereit für die Endfertigung?
- Nachbearbeitung für den industriellen 3D-Druck:Der Weg zur Automatisierung
- Warum ist 3D-Druck für Investoren so attraktiv?
- Anwendungs-Spotlight:3D-Druck für Turbinenteile
- Warum 3D-Druck und Software für die digitale Transformation entscheidend sind
- Warum Glasfasergewebe für die Surfbrettherstellung verwendet wird
- 10 wasserfeste Optionen für Ihre 3D-gedruckten Teile:Materialien und Nachbearbeitung
- Rückverfolgbarkeitspraktiken für die Fertigung von Präzisionsteilen