Tugenden des Virtuellen
Wenn Passagiere in einer Boeing 787 Dreamliner ein Getränk und eine Leckerei genießen, kommt ihr Snack aus einer Kombüse des Flugzeuginnenausstatters Jamco Corporation.
Neben dem Erfolg von Jamco bei der Herstellung von Bordküchen, Toiletten und Sitzgelegenheiten für Boeing, Airbus und andere Unternehmen entstand ein integrierter Verwaltungsbedarf für 3,2 Millionen CAD-Datensätze. Trotz all dieser Daten konnte das Unternehmen einige grundlegende Fragen nicht beantworten. Warum wurde ein Produkt so gestaltet, wie es war? Warum hat es oft Designfehler in ein Teil eingebaut, obwohl es in der Vergangenheit Erfahrungen damit gemacht hat, das CAD in anderen Teilen zu ändern, um denselben Designfehler zu beseitigen? Warum wurde aus Kostengründen ein wesentliches Element gestrichen, um es später wieder hinzuzufügen? Die Lösung bestand darin, einen digitalen Thread auf der Grundlage von Aras Innovator, einer Low-Code-Produktinnovationsplattform, zu erstellen. Die Plattform ermöglicht es den Designern und Ingenieuren von Jamco in Japan, Frankreich und den Vereinigten Staaten, nach der Designhistorie zu suchen und die zugehörigen Informationen zu nutzen, um zu verstehen, warum ein Produkt so entworfen wurde, wie es war, und Fehler aus der Vergangenheit nicht mehr zu wiederholen.
„Durch die Verknüpfung von Suchergebnissen mit unseren Informationen, einschließlich Liefergegenständen und verschiedenen Vorschriften, können unsere Designer jeden Prozess jederzeit bis zum Abschluss durchsuchen und erhalten die richtigen Informationen zu Aras Innovator, ohne von der technischen Abfolge zwischen den Ingenieuren abhängig zu sein“, sagte Hiroshi Sakurai in a Fallstudie. Sakurai ist der stellvertretende General Manager der Engineering and Technology Division, Aircraft Interiors and Components Group bei Jamco.
Die Plattform und Anwendungen von Aras gehören zu den vielen Tools, mit denen Hersteller digitale Threads erstellen können, die sich idealerweise aus Daten zusammensetzen, die mit einem Produkt während seines gesamten Lebenszyklus verbunden sind. Ein digitaler Thread ist ein Protokoll oder eine Aufzeichnung, die mit den CAD-Daten beginnt und Informationen von der SPS der Maschine, daran durchgeführte Wartungsarbeiten, Sensoren, Energieverbrauch und mehr enthalten kann.
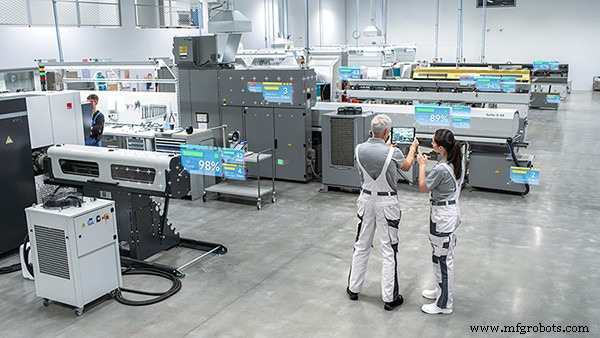
Das Unternehmen und andere verfügen auch über Tools zum Erstellen digitaler Zwillinge, bei denen es sich um virtuelle Modelle handelt, die mit physischen Assets verbunden sind, die verwendet werden, um zu verstehen, wie Änderungen vorgenommen werden können, und um die Auswirkungen dieser Änderungen abzuschätzen, ohne die reale Welt beeinflussen zu müssen. Diese Assets können Personen, Prozesse, Arbeitsabläufe und eine einzelne Maschine umfassen – oder ein System wie eine ganze Fabrik. Unter anderem können digitale Zwillinge bei der Sicherheitsplanung und bei der Fehlervermeidung eines Teils in der Konstruktionsphase helfen.
Im Allgemeinen gehören zu den Werkzeugen zum Erstellen eines digitalen Zwillings und Threads solche, die bereits aus der Fertigung bekannt sind – CAD-, PLM- und IoT-Anwendungen.
Innovator ist Open Source, während seine Anwendungen und die anderer Anbieter normalerweise mit einem kostenpflichtigen Abonnement in einem Software-as-a-Service-Paradigma angeboten werden. Andere Variationen unter den Tools umfassen Standard vs. benutzerdefiniert, Benutzerfreundlichkeit, Flexibilität, Unterstützung für kundenspezifische Anwendungen, Einbindung von Low-Code-Apps, Modelle zur Darstellung der Elemente in einem digitalen Zwilling, gebündelte oder à la carte-Anwendungen, und mehr.
Worin sich verschiedene Anbieter jedoch weitgehend einig sind, sind die Vorteile, die sich aus der Erstellung eines digitalen Zwillings, eines digitalen Threads oder beidem ergeben.
Digitaler Zwilling bereichert Kummerkasten
Die Erfahrung von Jamco hat gezeigt, wie nützlich es ist, einen digitalen Thread zu verwenden, um Verlauf und Kontext in der Designphase bereitzustellen und gleichzeitig wiederholte Fehler zu eliminieren, alles im Streben nach größerer Effizienz und verbesserter Qualität.
Eine weitere Verwendung wäre die Wartung, sagte Craig Melrose, Executive Vice President of Digital Transformation Solutions bei PTC.
„Ich kann ihnen das Wartungsverständnis und die Erfahrung durch Augmented Reality (AR) vermitteln, indem ich ihnen sage, dass sie dies zuerst zerlegen, dieses Element als zweites überprüfen und dieses Element als drittes inspizieren“, sagte er. „Wenn ich einen Artikel ersetzen muss, finden Sie hier die Details dazu, wie ich ihn ersetzen oder neu installieren kann. So bestätigen Sie, dass es richtig gemacht wurde. Wie man das Gerät wieder zusammenbaut und überprüft, ob alles richtig gemacht wurde und wieder eingeschaltet werden kann. Und sogar Sicherheitselemente wie das Abschalten des Stroms und das Sperren des Geräts, diese Art von Dingen, können alle über AR bereitgestellt werden.“
Ein digitaler Zwilling bietet ganz eigene Vorteile.
„Die Vorteile sind so viel größer als die Investition“, sagte Zohair Mehkri, Director of Engineering, verantwortlich für digitale Zwillinge bei Flex Ltd., einem 24-Milliarden-Dollar-Auftragshersteller. „Zum Beispiel können Sie Ihre Prozesse, Ihre Gebäude vollständig optimieren, bevor überhaupt etwas passiert. Sie können Dinge bewegen, Sie können Produkte ändern, neue Maschinen einbauen, Personal oder Material hinzufügen oder entfernen, und Sie können all das in der Software ausprobieren, bevor Sie überhaupt einen Fuß in Ihre Fabrikhalle setzen.
„Die Menge an Zeit und Mühe, die wir aufwenden, um physische Herstellungsprozesse, die uns finanziell beeinträchtigen, zurückzuverfolgen und auszuprobieren, ist enorm. Die Fähigkeit, dies in einem digitalen Zwilling zu tun, ist also enorm.“
Sobald ein digitaler Zwilling erstellt ist, können Hersteller mit der Überwachung, Optimierung und Analyse beginnen. Jeder dieser Schritte hat seine eigenen Vorteile.
„Eine Analyse eines Prozesses mithilfe eines digitalen Zwillings ist sehr aussagekräftig, da sie nicht nur Ihren Prozess beschreibt, sondern Ihnen beispielsweise Bereiche aufzeigt, die verbessert werden müssen“, sagte Mehkri. „Das muss kein Engpass sein. Es könnte sogar lauten:„Sie haben hier etwas freien Platz, den Sie wahrscheinlich nutzen könnten.“ Oder Sie können eine nicht wertschöpfende Aufgabe aus Ihrem Prozess herausnehmen.“
Das Wichtigste, was zu beachten ist, ist, dass ein digitaler Zwilling mit Hardware und Software mit dem physischen Modell verbunden ist, sagte er. Dies kann aufgrund des geschlossenen Kreislaufs zu höheren Vorteilen führen.
„Wenn im physischen System etwas passiert, sollte das digitale Modell wissen, dass eine Änderung im physischen System stattgefunden hat, das digitale Modell sollte sich selbst anpassen, um das physische System widerzuspiegeln, und sich dann basierend auf der Änderung selbst optimieren und diese Optimierung dann an die weitergeben physikalisches System“, sagte Mehkri.
Wenn es einen Engpass gibt, kann ein digitaler Zwilling Lösungen anbieten, um ihn zu beheben, sagte Ali Ahmad Malik, Assistenzprofessor für Industrie- und Systemtechnik an der Oakland University.
„In einer Montagezelle ist Ihr Ziel beispielsweise 1.000 Einheiten an einem Tag, aber zu einer bestimmten Stunde wertet der digitale Zwilling es aus und sagt Ihnen, wenn Sie im gleichen Tempo weiterarbeiten, werden Sie das Ziel nicht erreichen können.“ er sagte. „Aber es sagt mir nicht nur das potenzielle Problem, das am Ende des Tages auftreten kann, sondern gibt mir auch einige Lösungen, weil es die Möglichkeit hat, es zu simulieren, und es intelligent ist. Es enthält Informationen aus früheren Vorfällen. Vorschläge können das Hinzufügen eines Roboters oder das Erhöhen der Geschwindigkeit eines Roboters beinhalten. Das kann ich nur erreichen, wenn ich eine Datenkonnektivität habe und mein digitaler Zwilling durch vergangene Ereignisse und vergangenes Lernen immer intelligenter wird. Daher sollte eine Dimension des maschinellen Lernens darin aktiviert werden.“
Malik, der Erfahrung mit der Erstellung digitaler Zwillinge mit Robotern oder Cobots hat, sagte, dass der Zwilling auch beim Ausgleich des Montageprozesses helfen kann. In Montagezellen werden Menschen und Robotern Aufgaben zugewiesen, die zusammenarbeiten, um eine Baugruppe in einer bestimmten Zeit zu bauen, sodass kein Bediener untätig sitzt. Vor dem digitalen Zwilling wurde der Prozess immer manuell durchgeführt.
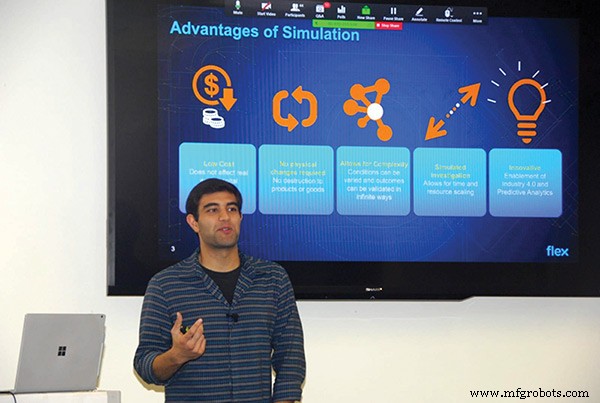
„Mit digitalen Zwillingen, die die Geschwindigkeit des Roboters kontinuierlich bewerten, balanciert er den Prozess und weist Aufgaben der richtigen Quelle zu“, sagte er. „Also gehen all diese manuellen Aktivitäten des Prozessausgleichs zu einem digitalen Zwilling. Wenn Sie eine High-Mix-, Low-Volume-Produktion haben, kann Ihnen dieser digitale Zwilling sehr helfen.“
Es hilft einer Fabrik auch, schneller auf Marktschwankungen zu reagieren, da Fertigungslinien oder -zellen schnell und virtuell hinzugefügt, gelöscht oder modifiziert werden können, um auf Marktveränderungen zu reagieren, per Simulation getestet und basierend auf den Ergebnissen akzeptiert oder abgelehnt werden können. In regulierten Branchen wird sogar davon gesprochen, eine Linie digital vorzuqualifizieren, bevor sie physisch qualifiziert wird.
Melrose sagte, dass die schnellen und virtuellen Änderungen, die mit der Simulation getestet werden, die Produktion in einem Werk am Laufen halten können.
Nehmen Sie zum Beispiel eine fiktive Fabrik mit 10 Maschinen, sagte Melrose. Arbeiter haben Schwierigkeiten, Teile in und aus einer Maschine zu wechseln, weil sie so schwer sind, also möchte der Fabrikbesitzer eine Hebehilfe hinzufügen.
„Anstatt die Produktion zu unterbrechen, kann ich all das offline in einem Computer testen, um sicherzustellen, dass es gut funktioniert“, sagte er. „Ich werde es über das Wochenende installieren und testen und am Montag einschalten, damit wir mit diesem neu hinzugefügten Element die Produktion wieder aufnehmen können.“
Was der digitale Zwilling vor allem bietet, ist ein Kontext und Rahmen für Sensordaten, die von einer intelligenten Maschine fließen, sagte Rob McAveney, CTO bei Aras.
„Wenn Sie darüber nachdenken, da ich zwei verschiedene Flugzeuge mit zwei verschiedenen Triebwerken habe, die Rückmeldungen darüber geben, wie ein Triebwerk arbeitet und wie das andere Triebwerk arbeitet“, sagte er. „Dieses Feedback ist wertvoll, aber es ist viel wertvoller, wenn ich weiß, in welchem Flugzeug sie installiert sind, wo dieses Flugzeug fliegt und wie die Wartungshistorie dieses Flugzeugs ist. All diese Dinge sind wichtig, um die Daten zu analysieren, die von diesen Sensoren zurückkommen. Also bietet der digitale Zwilling für mich den größten Mehrwert.“
Thread, Zwillings-Apps könnten CAD-ähnlicher sein
McAveney sieht die größte Herausforderung in getrennten Daten aus unterschiedlichen Systemen.
„Sie haben Daten in verschiedenen Formaten, die von verschiedenen Personen in verschiedenen Abteilungen verwendet werden, die nie miteinander sprechen“, sagte er. „Wenn sie ihre Daten angeben müssen, müssen sie sie manuell anpassen, um sie für die Bedürfnisse anderer Personen nutzbar zu machen.“
Unterschiedliche Systeme an und für sich zu haben ist nicht schlecht, es ist die Tatsache, dass es sich um unterschiedliche Systeme ohne Verbindung handelt.
„Und ich meine [nicht reden] aus einer technologischen Perspektive, ich meine [nicht reden] aus einer semantischen Perspektive“, sagte McAveney. „Das heißt, ich habe eine Stückliste in PLM, ich habe eine Stückliste in ERP, und es gibt kein Mapping, da sitzt niemand in der Mitte und sagt:‚Oh, dieses Feld in diesem System ist dasselbe wie dieses Feld in diesem System.“ Wir müssen sicherstellen, dass sie synchronisiert sind. Jetzt gibt es nicht einmal eine konzeptionelle Verbindung zwischen ihnen, geschweige denn eine physische Verbindung.“
Malik verglich die von McAveney beschriebene Situation von getrennten Daten mit der von Daten verschiedener CAD-Softwareanbieter.
„Beispielsweise konnten AutoCAD-Daten [früher] nicht in SolidWorks exportiert oder importiert werden, aber jetzt ist es eine ganz normale Sache, Daten von einem CAD in ein anderes CAD zu exportieren und zu importieren, und es gibt Standardformate“, sagte Malik. „Das Gleiche muss in dieser Dimension gemacht werden und nicht nur CAD-Daten, sondern auch dynamische Daten und die Informationen, die wir von physischen Systemen erhalten. Im Moment sind wir auf die Plattform eines Unternehmens beschränkt.“
Anbieter und Benutzer sind sich einig, dass der erste und wichtigste Schritt bei der Verwendung eines digitalen Zwillings darin besteht, Ihr Ziel und die Teile Ihres physischen Systems zu bestimmen, die Sie modellieren möchten.
Ein Fabrikbesitzer möchte vielleicht einfach seine Anlage visualisieren, sagte Mehkri, und Fragen beantworten wie:Wo sind meine Materialien? Wo verbringen die Menschen ihre Zeit? Was sind stark frequentierte Bereiche? Wo gibt es Probleme bezüglich der Leitung?
„Wenn Sie anfangen, diese Art von Herausforderungen zu visualisieren, können Sie sich mit diesem zweiten Faktor befassen, nämlich wie löse ich diese Probleme, wie optimiere ich diese Probleme oder wie werde ich diese Probleme los?“ sagte er.
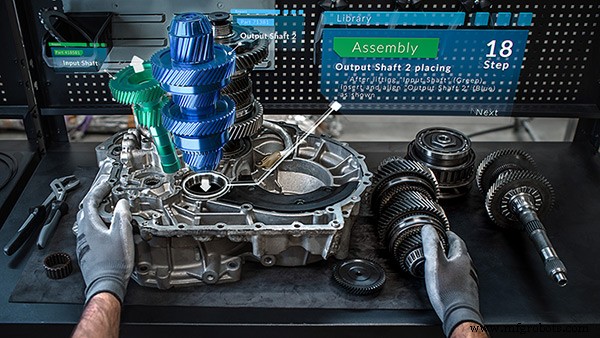
Melrose stimmt zu, dass die Wahl des richtigen Ziels entscheidend ist.
„Unternehmen sind zu Recht risikoscheu, aber wenn sie risikoscheu sind, wählen sie möglicherweise den falschen Anwendungsfall, der von geringem Wert ist, und wählen möglicherweise die falsche Technologie basierend auf dem Preis und nicht auf der Grundlage der Auswirkungen, weil sie sich des Werts nicht sicher sind“, sagte PTC Melrose. „Sie können in das Pilot-Fegefeuer gelangen.“
Während einige Anbieter von Anpassungen abraten, erlaubt mindestens ein Unternehmen Anpassungen nicht nur, sondern fördert sie auch.
„Als Kunde steht es Ihnen frei, diese Anwendungen mit zusätzlichen Funktionen zu erweitern, und was Aras tut, ist, Aras-Abonnenten die Möglichkeit zu geben, Anwendungen unverändert zu verwenden, Anwendungen nach eigenem Ermessen zu erweitern und neue Anwendungen nach eigenem Ermessen zu erstellen“, sagte McAveney . „Dann ist es unsere Aufgabe sicherzustellen, dass all diese Änderungen, die der Kunde vorgenommen hat, in der Lage sind, mit der Technologie voranzukommen.
„Da Aras weiterhin neue Funktionen und neue Versionen der Plattform veröffentlicht, die mit neueren Compute-Stacks funktionieren, garantieren wir im Rahmen unseres Abonnements, dass alles, was Sie heute erstellen, im nächsten Jahr funktioniert.“
Nach Mehkris Erfahrung bei der Erstellung digitaler Zwillinge verlässt er sich auf Lean-Manufacturing-Prinzipien, wenn sein Zwilling nicht mit der realen Welt übereinstimmt. Es sei unmöglich, alle Möglichkeiten aufzulisten, was einen Unterschied verursacht habe, sagte er.
„Es gibt jedoch einige Möglichkeiten, die passieren können; Ich könnte falsch modelliert haben, es könnte ein Benutzerfehler vorliegen, es könnte unterschiedliche Datenquellen geben oder die Datenquelle selbst kann ein Problem haben“, sagte Mehkri. „Normalerweise bestimmen wir das, indem wir die Power of Gemba verwenden, eine Lean-Manufacturing-Technik, die an den Ort geht, an dem die Arbeit erledigt wird. Indem wir auf die physische Ebene gehen, können wir den Prozess sehen und in ihn eintauchen und eine RCA (Ursachenanalyse) durchführen, um festzustellen, was die Diskrepanz verursacht hat, und dann dem nachgehen und das Problem herausfinden.“
Ein Bereich, mit dem Mehkri und der Rest der Branche zu kämpfen haben, ist, nicht genügend Standardinhalte zu haben, um Materialien, Maschinen und andere Elemente in einem digitalen Zwilling zu modellieren. Wenn die Software kein Modell enthält, muss der Benutzer es selbst erstellen, was zeitaufwändig ist, sagte er.
Malik sagte, dass ein Benutzer möglicherweise mehrere Produkte benötigt, um seinen digitalen Zwilling zu erstellen. „Vielleicht kann ich mit einem Tool entwerfen, welche Elemente in einem physischen System vorhanden sind“, sagte er. Ein anderes Werkzeug kann es mir ermöglichen, die Dynamik oder Kinematik des physischen Systems zu definieren, und dann kann mir eine andere Software ermöglichen, die Daten des physischen Systems in das digitale System zu integrieren. Eine Kombination aus vier oder fünf verschiedenen Softwares kann mir also helfen, einen digitalen Zwilling zu vervollständigen.“
Einige der prominenten Namen unter den Anbietern digitaler Tools verfügen über ein umfassendes Set an Tools zum Erstellen digitaler Zwillinge, aber kleine und mittlere Unternehmen können es sich oft nicht leisten oder haben keine Mitarbeiter mit den erforderlichen Fähigkeiten, um sie zu verwenden, sagte Malik. Selbst bei den größeren Anbietern übertragen verschiedene Anwendungen Daten möglicherweise nicht reibungslos und einfach.
„Aber wenn Sie eine Software finden, die mehr Funktionen in einer Umgebung bietet, bietet Visual Components beispielsweise kontinuierliche Simulation, Datenkonnektivität, diskrete Ereignissimulation oder stochastische Analyse in einer einzigen Umgebung“, sagte er. „Das ist meines Erachtens ein sehr gutes Feature, denn dann braucht man nicht drei oder vier Softwares.“
Automatisierungssteuerung System
- 5 Treiber der digitalen Lieferkette in der Fertigung
- Wartung in der digitalen Welt
- Der digitale Ansatz für den intelligenten Containerversand
- Expertenkommentar:Die Zukunft des Abfalls in einer digitalen Welt
- Der Kunde muss im Zentrum der digitalen Strategie stehen
- Censornet:Sicherung der Zukunft der Fertigungsindustrie
- Die übergroßen Auswirkungen von Industrie 4.0 auf das Backoffice
- Der Aufstieg digitaler Plattformen in der Fertigung
- Automatisierung und die Zukunft der digitalen Fertigung?
- Digitale Fertigung:Die Industrie von morgen