Hirsh Precision vertraut dem System
Bei Hirsh Precision Products basiert die Kultur darauf, Geschäfte mit Integrität und Grundwerten wie Vertrauen, Zuversicht und Engagement zu führen
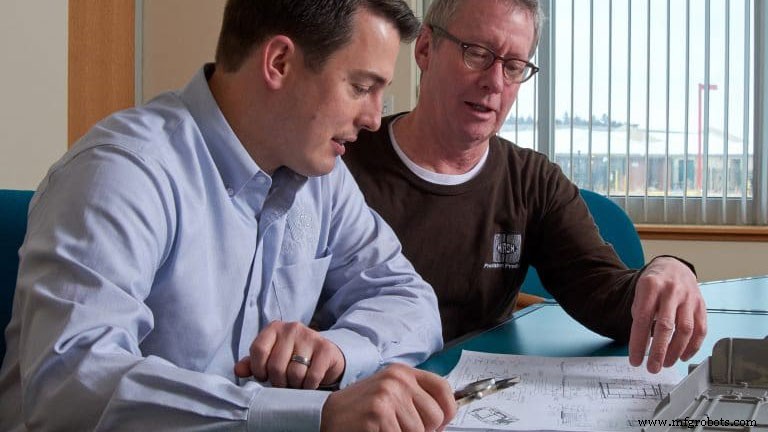
Von einem einfachen Fixierstift bis hin zu einem komplexen Flüssigkeitsverteiler beginnt jedes hergestellte Teil mit einer Idee. Ein Geschäft in Colorado verwirklicht die Konzepte seiner Kunden, indem es fortschrittliche Fertigungstechnologie und sorgfältiges Prozess- und Datenmanagement mit einer teamorientierten Unternehmenskultur und fast 40 Jahren Erfahrung verbindet.
Der Zerspanungsmechaniker Steve Hirsh gründete 1979 Hirsh Precision Products Inc. in Boulder, Colorado. Mit einer einzigen Bridgeport-Fräsmaschine bearbeitete Hirsh kleine Produktionsserien sowie Werkzeug- und Vorrichtungskomponenten für eine Vielzahl von Kunden. Sein Bruder Mike trat in das Unternehmen ein, und die Werkstatt fügte eine LC-10 Okuma-Drehmaschine und eine CNC-Wells-Index-Vertikalfräse mit manuellem Werkzeugwechsel hinzu.
Als das Geschäft wuchs, zog das Geschäft in die Einrichtung eines seiner Kunden, eines Spezialwerkzeugherstellers für die Automobilindustrie, der auch nach 38 Jahren Kunde bleibt. 1993 baute Hirsh Precision Products ein eigenes Gebäude mit einer Fläche von 24.000 ft2 (2230 m2). Heute beschäftigt das Unternehmen rund 70 Mitarbeiter, die an fünf Tagen in der Woche im Zweischichtbetrieb arbeiten. Etwa zwei Drittel der Produktion des Shops bezieht sich auf die medizinische Industrie, wobei der größte Teil Geräte wie Komponenten für Blutverarbeitungsgeräte umfasst.
Produktqualität, Teamcharakter
Im Laufe seiner Geschichte war die Leitmaxime von Hirsh Precision Products „Qualitätsarbeit pünktlich geliefert“. Der heutige technische Leiter des Unternehmens, Steve Hirsh, sagte:„Hochwertige Arbeit ist das Ergebnis einer integren Geschäftstätigkeit und die Grundlage unserer Unternehmenskultur.“
Laut Hirsh konzentriert sich das Unternehmen auf kontinuierliche Verbesserung, Lernen und Vertrauen unter den Teammitgliedern seiner Mitarbeiter. Die Beziehung von Hirsh Precision Products zu seinen Teammitgliedern kann als einzigartig bezeichnet werden.
Die Einstellungsphilosophie des Unternehmens zielt darauf ab, sicherzustellen, dass sowohl das Unternehmen als auch das Teammitglied gut zusammenpassen. Der Schwerpunkt liegt auf Persönlichkeit, Integrität und Eignung über dem anfänglichen Qualifikationsniveau. „Man kann den grundlegenden Charakter nicht lehren oder wie man pünktlich auftaucht oder Fehler eingesteht“, sagte Hirsh. Wenn ein Mitarbeiter leidenschaftlich, interessiert und neugierig ist, können technische Fähigkeiten vermittelt werden, fügte er hinzu.
Ein Beweis für die positive Kultur des Unternehmens ist die Anzahl der Familien mit mehreren Mitgliedern am Arbeitsplatz. Hirsh sagte:„Ich zähle ungefähr 13 verschiedene Familien mit mehr als einem Mitglied, das hier arbeitet. In einigen Fällen sind es drei oder vier aus derselben Familie.“ Tatsächlich umfasst das Team drei Mitglieder der Familie Hirsh:Steve, CEO Mike und CFO Kent.
Schulungsakademie
Der Schwerpunkt des Unternehmens auf kontinuierliches Lernen ist im Laufe der Zeit gewachsen. In den Anfängen bestand das Training aus Echtzeit-Coaching an der Maschine. Die Dokumentation von Prozessschritten und Rüstvorgängen wurde hinzugefügt, um die Rüstzeiten zu reduzieren und die Wiederholbarkeit sicherzustellen. Im Laufe der Jahre wurden weitere Schulungsinitiativen durchgeführt, darunter die Einstellung eines lokalen Ausbilders für Maschinenberufe, um die Mitarbeiter vor Ort zu schulen. Im vergangenen Jahr stellte das Unternehmen einen Schulungs- und Entwicklungsmanager ein, um die Schulungen formell zu dokumentieren und zu verfolgen.
Alle Schulungsbemühungen sind jetzt unter einem Dach zusammengefasst, der Hirsh Training Academy. Das Programm bietet einen standardisierten, skalierbaren Lehrplan, in den sich die Mitarbeiter bei der Arbeit oder zu Hause einloggen können. Zu den Grundelementen gehören Orientierungsmaterialien, Sicherheit und Messtechniken.
Es werden ständig neue Kurse hinzugefügt und das System hilft auch bei der Verfolgung externer Schulungen, wie sie beispielsweise von der NTMA (National Tooling and Machining Association) angeboten werden. Jedes Teammitglied ist Mitglied der Hirsh Training Academy und kann eine auf seinen Karriereweg abgestimmte Lernrichtung bestimmen. Teammitglieder treffen sich jährlich mit Vorgesetzten, um ihre eigenen Interessengebiete zu erkunden, Schulungsthemen zu identifizieren, Ziele zu setzen und die Fortschritte des vergangenen Jahres zu überprüfen.
In Technologie investieren
Seit seiner Gründung hat Hirsh Precision Products kontinuierlich in fortschrittliche Fertigungstechnologie investiert. „Wir versuchen zu verstehen, wie sich bestimmte neue Funktionen oder Merkmale auszahlen, und stellen sicher, dass wir diese Innovationen auf intelligente Weise nutzen“, sagte COO Peter Doyle.
Heute verfügt das Unternehmen über 22 CNC-Werkzeugmaschinen, die nahezu gleichmäßig auf Fräs- und Drehmaschinen verteilt sind. Es gibt sechs Produktionszellen mit drei oder vier Maschinen pro Zelle. Fünf-Achsen-Maschinen sind weit verbreitet und werden zum Positionieren verwendet, was eine One-and-Done-Bearbeitung ermöglicht.
Die Positioniergenauigkeit ist in der medizinischen Fertigung entscheidend, um die Teileregistrierung, Toleranzen und Wechselbeziehungen von Merkmalen aufrechtzuerhalten. Die Werkstatt fertigt Teile in Größen von 1-mm-Drehteilen bis hin zu Artikeln mit einer Größe von 3 Fuß, aber „80 % unserer Arbeit passen in Ihre Handfläche“, sagte Hirsh. Sekundäre Operationen, mit Ausnahme des Galvanisierens, werden im eigenen Haus durchgeführt. Die Werkstückmaterialien reichen von medizinischen Kunststoffen bis hin zu wärmebehandelbaren Edelstählen.
Die Produktionsmengen sind im Allgemeinen nicht groß. „Jährlich stellen wir vielleicht 100 von etwas oder bis zu 10.000 von etwas anderem her. Eine typische Losgröße liegt bei etwa 200 Stück“, sagte Hirsh.
Entwicklung der Automatisierung
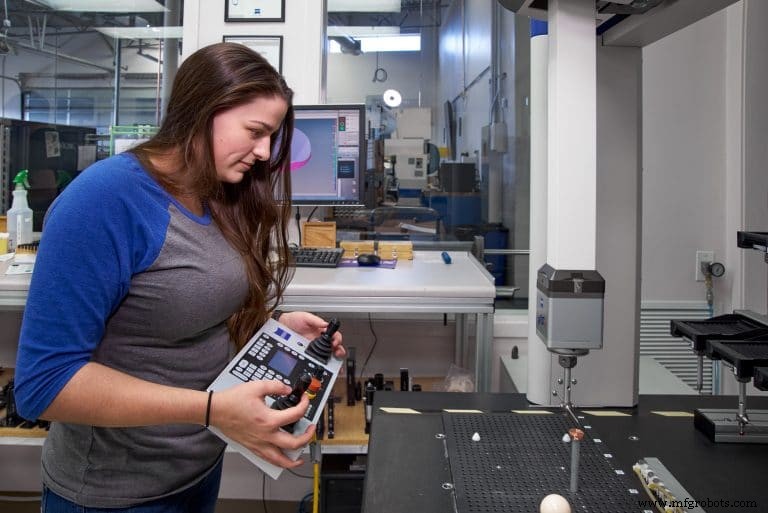
Hirsh Precision Products hat immer nach Möglichkeiten gesucht, seine Prozesse zu automatisieren. So investierte das Unternehmen bereits in den ersten fünf Jahren in pneumatische Roboter zum Beladen von Futterdrehmaschinen. Nachdem das Geschäft sein erstes Werk mit Palettenwechsel erworben hatte, erkannte das Management die Flexibilität und Produktivität, die durch den Austausch von Paletten geboten werden, und entschied, dass jedes zukünftige Werk auf diese Weise ausgestattet würde.
Der erste Ausflug der Werkstatt in die FMS-Technologie (flexible Fertigungssysteme) erfolgte mit einer Tsugami FMA mit vier Achsen und 12 Paletten, und ihre erste fünfachsige Maschine mit FMS-Konzepten war eine DMG Mori mit einem Palettenwechsler mit zehn Stationen>
Um seine FMS-Anwendungen zu erweitern, untersuchte das Unternehmen Optionen, die in FMS-Systemen mit mehreren Maschinen verfügbar sind. „Wir gehen alle zwei Jahre als Team zur IMTS, um über die für unsere Kunden und ihre Teile relevanten Technologien auf dem Laufenden zu bleiben“, sagte Hirsh. Nach gründlicher Recherche vor der Messe erwarb das Unternehmen auf der IMTS 2016 ein FMS-System bestehend aus einem Okuma MU-4000 fünfachsigen CNC-Vertikal-Bearbeitungszentrum im Zapfenstil mit einem 740 mm x 460 mm x 460 mm großen X-Y-Z-Arbeitsbereich, bedient von ein Fertigungssystem Modell MDR-750 FMS ONE des FMS-Anbieters Fastems LLC.
Seitdem hat das Geschäft eine zweite MU-4000-Fräse auf dem Fastems-System erworben und installiert, die über 36 Paletten mit 400 mm Durchmesser, drei Palettenspeicherebenen und einer LSC-Ladestation verfügt. Das System ist erweiterbar, um fünf Werkzeugmaschinen und 120 Paletten innerhalb der aktuellen Einrichtung zu handhaben.
Die Manufacturing Management Software (MMS) von Fastems ist die operative Grundlage des Systems. MMS trifft Produktionsprioritätsentscheidungen basierend auf der Verfügbarkeit von Personal, Werkzeugen, Maschinenzeit und Rohmaterial. Es erstellt einen Zeitplan, bewegt Paletten zu und von den Palettenregalen und leitet die Bearbeitung von Teilen autonom.
„Wir teilen das Fälligkeitsdatum und die benötigte Menge mit“, sagte Doyle, „dann kann MMS ‚Schach spielen‘, sich die geplante Arbeit ansehen und einen Plan erstellen, der die Liefertermine einhält, die verfügbaren Ressourcen nutzen, und maximieren Sie die Spindelzeit. Das hat zu einer hervorragenden Spindelauslastung geführt.“
Die Werkstatt gibt ihre Personalpläne ein und das System ruft fertige Teile ab, wenn Teammitglieder verfügbar sind, um sie zu entladen. „Der Betrieb des Fastems-Systems hat unserem Team gezeigt, wie wichtig es ist, die Spindeln am Laufen zu halten. Unsere Aufgabe ist es, alle erforderlichen Voraussetzungen zu organisieren, wie z. B. die Einrichtung“, sagte Doyle.
Das Mehrpalettensystem passt gut zu der sich wiederholenden Natur der meisten Hirsh-Teile. „Setups sind für uns eine der größeren Variablen“, sagte Hirsh. Der Shop kann Rüstzeiten praktisch eliminieren, indem er die Vorrichtungen auf den Paletten intakt lässt. „Mit 36 Paletten können wir Arbeitsplätze eingerichtet lassen. Durch den Palettenwechsel können wir die Vorlaufzeiten minimieren und gleichzeitig die Auslastung maximieren“, sagte Hirsh. In einer Studie, in der die Werkstatt drei typische Teileherstellungsprozesse durchführte, wurden die Einrichtungsstunden um 72, 54 und 92 % reduziert, mit einer durchschnittlichen Reduzierung von 73 %.
Hirsh betonte, wie wichtig es sei, die Fähigkeiten des Systems vollständig zu verstehen. „Fastems sagte uns, dass das System nicht einfach ein großer, schicker Palettenwechsler ist. Sie forderten uns auf, dem System zu vertrauen, unsere Aufträge einzugeben und das System die Arbeit planen und bestimmen zu lassen, wann Teile ausgeführt werden.“
Bestes Preis-Leistungs-Verhältnis
Doyle sagte:„Wenn wir uns die Mühe machen, die Technologie zu kaufen, wollen wir das Beste daraus machen!“ Dementsprechend organisierte Hirsh Precision Products ein engagiertes Fastems-Team und stellte es vor die Herausforderung, herauszufinden, was das FMS-System leisten kann.
Am wichtigsten für das Geschäft ist vielleicht, dass das FMS-System nachts, an Wochenenden und Feiertagen einen Betrieb ohne Licht ermöglicht. „Das Ziel ist es, die Spindeln 24 Stunden am Tag laufen zu lassen“, sagte Hirsh.
Palettierte Arbeitsvorrichtungen ermöglichen auch eine erhöhte Teiledichte. „Das hilft uns bei der Lights-out-Produktion“, sagte Doyle. „Bei einem Fünf-Minuten-Takt würden 36 Paletten nicht lange halten. Aber wenn Sie einstündige oder zweistündige Zyklen haben, können Sie es durch Nächte und Wochenenden schaffen. Das Fastems-System ermöglicht die volle Nutzung der unbeaufsichtigten Zeit. Anstatt alle 15 Minuten jemanden vor Ort zu haben, können wir das System über Nacht laufen lassen und die Teile am nächsten Tag austauschen.“
Er fuhr fort:„Wir können die Produktion für viele Kundenaufträge parallel sequenzieren, anstatt sie seriell zu produzieren. Für ein Teil, das 100 Stück pro Monat liefern muss, können wir 25 Stück pro Woche produzieren, was etwa fünf Stück pro Tag ausmacht. Wir können einen Job einmal am Tag an der Ladestation auftauchen lassen, anstatt 100 Stück nur dieses Artikels zu verarbeiten, bevor wir zum nächsten Teil übergehen.“ Durch die Integration der Palettenverwaltung über mehrere Maschinen kann ein Teil auch auf mehr als einer Maschine laufen.
Ein Teil, das eine fünfachsige Positionierung erforderte, um alle seine Merkmale zu bearbeiten, wurde zuvor einzeln auf einer fünfachsigen Brother-Fräsmaschine bearbeitet. Der Arbeitsraum war nur groß genug, um jeweils ein Teil zu bearbeiten. „Mit dem Fastems-System bearbeiten wir das Teil auf größeren Werkzeugmaschinen und wir können 18 der Teile gleichzeitig auf einer Palette in Bearbeitung haben“, sagte Hirsh.
Das Teil, etwa 60 mm im Quadrat, wird in drei Sequenzen bearbeitet, mit sechs Teilen in jeder Sequenz auf derselben Palette. Die erste Sequenz umfasst die Bearbeitung eines Schwalbenschwanzes auf einem Rohling. Sequenz zwei umfasst die Bearbeitung von fünf Seiten des Teils. In Folge drei wird der Schwalbenschwanz abgearbeitet und das Teil fertig gestellt. Pro Zyklus entstehen sechs fertige Teile. Hirsh sagte:„Anstatt den Auftrag zu stapeln, können wir die Teile durchsickern lassen, wenn sie unseren Bauplan einhalten.“
Zwei große Herausforderungen bei der Anwendung der FMS-Technologie von Fastems durch Hirsh Precision Products betreffen die Kompatibilität des Werkzeugmanagements und des ERP-Systems (Enterprise Resource Planning).
Die Merkmale der Werkstattarbeit mit geringem Volumen, hohem Mix und engen Toleranzen erfordern den Einsatz einer großen Auswahl an Schneidwerkzeugen. Als Hirsh Precision Products ursprünglich das Fastems-System mit den beiden Okuma-VMCs installierte, war es für die Werkstatt finanziell nicht tragbar, die Werkzeugverwaltungsfunktion des Systems einzubinden. Derzeit speichert jede Okuma-Maschine 166 Werkzeuge und die Werkzeugkapazität ist noch keine Einschränkung.
Da das Werk jedoch beabsichtigt, das System auf insgesamt fünf Bearbeitungszentren zu erweitern, entwickelt es ein eigenes System, um Werkzeuge in die und aus den Maschinen zu bewegen, wenn 166 Werkzeuge für den auf jeder Maschine produzierten Teilemix nicht ausreichen. „Wenn das FMS mehr Jobs hat, als von den verfügbaren Werkzeugtöpfen aufgenommen werden können, verschieben wir die Werkzeuge automatisiert in die Werkzeugmatrix und aus ihr heraus. Fehlersicher zu machen, dass Werkzeugbewegungen an unserem Horizont stehen“, sagte Doyle.
Ein weiteres Thema ist die ERP-Integration. Hirsh verwaltet alle seine Kundenbindungsinformationen über sein seit langem etabliertes ERP-System, das nicht darauf ausgelegt war, die Mehrpalettenplanung zu unterstützen. Der Grund dafür ist, dass das ERP-System den gesamten Teileweg vom Rohstoffeingang bis zum Versand bewertet, einschließlich externer Vorgänge wie Galvanisieren oder Wärmebehandeln. Es ist so konstruiert, dass es Engpässe erkennen kann, die für ein FMS-System, das sich auf Arbeitszellenaktivitäten konzentriert, nicht offensichtlich sind. Das ERP-System priorisiert die Just-in-Time-Fertigung, während ein FMS die Spindelauslastung priorisiert.
Folglich, so Doyle, „finden wir eine Möglichkeit, die Anforderungen beider Systeme zu vereinen, indem wir beispielsweise große Teileaufträge in Segmenten freigeben und selektiver mit den Informationen umgehen, die wir dem Fastems-System anzeigen lassen.“
Es ist keine leichte Aufgabe. „ERP-Systeme sind wie eine Hochzeit“, sagte Hirsh, „es gibt eine Verpflichtung und Investition. Sie möchten Ihr ERP-System nicht ändern, wenn Sie nicht müssen.“
Doyle sagte:„Was mir am FMS von Fastems gefällt, ist, dass es unserem Team ermöglicht, sich auf die Lösung von Problemen zu konzentrieren, die die Technologie nicht lösen kann, während es das Team von Aufgaben befreit, bei denen sich die Technologie als sehr gut erwiesen hat. Das Fastems-System eignet sich beispielsweise hervorragend für sich wiederholende Aktionen und seine Fähigkeit, Arbeit zu priorisieren und die Spindel am Laufen zu halten, ist fantastisch. Aber es wird uns nicht sagen können, wie man eine Vorrichtung entwirft, wie man über Materialeigenschaften nachdenkt oder wie man am besten einen Produktionsprozess entwirft. So können wir uns auf die Bereiche konzentrieren, die für unser Unternehmen von Vorteil sind.“
Produktions-Scorecards
Hirsh möchte, dass sich jeder Einzelne im Unternehmen bewusst ist, wie er oder sie dem Unternehmen hilft, seine Leitmaxime „Qualitätsarbeit, pünktlich geliefert“ umzusetzen. Hirsh sagte jedoch:„Wir haben festgestellt, dass wir das nicht jeden Tag überwachen konnten. Also haben wir eine Scorecard entwickelt, die von Maschinisten für Maschinisten entworfen wurde. Es nimmt unsere Prioritäten Sicherheit, Qualität und Produktivität auf und liefert zu jeder beliebigen Minute im Laufe des Tages ein Update in unserem gesamten Unternehmen darüber, wie wir in jedem dieser Prioritätsbereiche abschneiden.“
Jede Fertigungszelle verfügt über einen Computerbildschirm mit einer benutzerdefinierten Scorecard, die mit Hilfe der Teammitglieder entwickelt wurde. Dies ermöglicht eine schnelle Diagnose und Reaktion auf Produktionsanomalien.
Beispielsweise kann ein Supervisor die Scorecard einer Zelle überprüfen und die richtige Person hinzuziehen, um zu helfen, wenn die Einrichtung lange dauert. Der einseitige Schnappschuss spiegelt jedes Kundenengagement im gesamten Unternehmen wider und zeigt, welche Teammitglieder an der Erfüllung des Engagements beteiligt sind. Um aktuelle Informationen bereitzustellen, werden die Scorecards alle zwei Minuten aktualisiert.
Bei der Recherche zu verschiedenen FMS-Systemen suchte Hirsh eher nach Langlebigkeit und zuverlässiger Leistung als nach Spitzentechnologie, die frühzeitig eingesetzt wurde. „Wir wollten die Investition in die neueste Technologie in Einklang bringen mit dem Wunsch nach etwas, das gut getestet wurde und keine Verpflichtung darstellt“, sagte Hirsh. Fastems ist die richtige Wahl für uns. Es ist eine strategische Investition für uns, von der wir erwarten, dass sie unser Geschäft für viele Jahre begleiten wird.“
Big Data verstehen
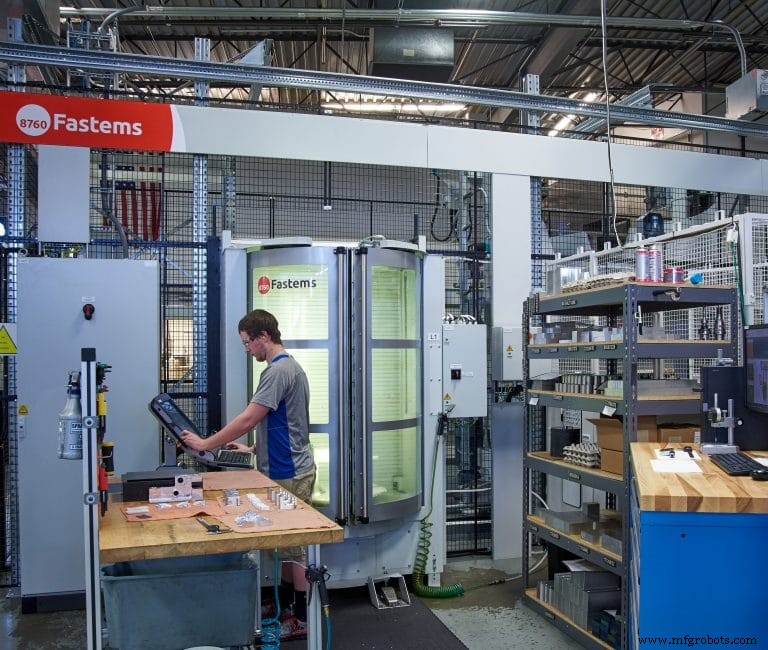
Peter Doyle von Hirsh Precision Products gibt zu:„Ich liebe Daten. Wir schauen es uns jeden Tag an. Wir haben Berichte, die sich mit jedem einzelnen Aspekt unseres Produktionsprozesses befassen. Taktzeiten, Teilenummern, Rüstzeiten, Materialkosten, Prüfdaten … alle Daten stehen zur Verfügung. Mein einziges Zögern in Bezug auf die datengesteuerte Fertigung besteht darin, sicherzustellen, dass wir sie richtig einsetzen.
„Das Problem ist, dass Unternehmen oft in ihren Daten ertrinken und nicht wissen, was sie damit anfangen sollen“, so Doyle weiter. „Der Wert von Daten liegt in ihrer Fähigkeit, die Entscheidungsfindung zu unterstützen. Das Isolieren eines Problems und das Bestimmen, welche Informationen am nützlichsten sind, sollte vor dem Sammeln erfolgen.“
Doyle sagte, dass das Unternehmen in diesem Jahr Analytik und Informationsmanagement als Schlüsselkomponenten zum Erreichen seiner Strategie hinzugefügt habe. „Analysen können uns dabei helfen, herauszufinden, welche Daten für uns am aussagekräftigsten sind. Das Informationsmanagement ermöglicht es uns, die richtigen Informationen zur richtigen Zeit an die richtigen Personen weiterzugeben.“
Das Geschäft entwickelt Möglichkeiten zur Systematisierung von Daten, um Produktionsentscheidungen zu treffen. Während KMG-Daten beispielsweise einfach elektronisch erfasst werden können, implementiert die Werkstatt derzeit eine elektronische Sammlung von Werkzeug- und Teileprüfdaten, die zuvor in der Werkstatt von Hand durchgeführt und aufgezeichnet wurden. Während diese und andere Initiativen voranschreiten, so Doyle, „findet der Betrieb Möglichkeiten, die von uns entwickelte proprietäre Prozessdokumentationssoftware, unser ERP und das MMS von Fastems zusammenzubringen, damit unsere Daten selbst ein Gewinn sind. Wir wissen, dass wir die Möglichkeit haben, unsere Datennutzung zu verbessern, aber wir überlegen noch, wie.“
Ein weiterer Schritt ist die Bestimmung der Qualität der zugrunde liegenden Daten. Qualitativ hochwertigere Daten können dazu beitragen, schneller bessere Entscheidungen zu treffen. Anstatt beispielsweise ein Merkmal an jedem fünften Teil zu prüfen und die Produktion zu verlangsamen, kann die Werkstatt statistisch ermitteln, dass sie nur eines von 50 Teilen prüfen muss, wodurch die Effizienz gesteigert wird. Doyle stellt auch den wahren Wert einiger Daten in Frage. Bestimmte Daten sind zweifellos wertvoll, wie z. B. Maschinenauslastung und OEE-Zahlen, aber einige Datensätze sind nicht so nützlich.
Als Beispiel stellte er den Wert detaillierter Daten zur individuellen Leistung in Frage, wie beispielsweise nationale Benchmarking-Studien zur Produktivität pro Person. „Es gibt Aspekte der Art und Weise, wie diese Daten gesammelt werden, die bedeuten, dass die Benchmarks möglicherweise nicht vergleichbar oder für eine Entscheidung relevant sind, und ich glaube nicht, dass dies der Vorteil der datengesteuerten Fertigung ist. Der Erfolg und die Kultur von Hirsh Precision Products basieren auf unseren Grundwerten – wir sind ehrlich und vertrauenswürdig, leidenschaftlich bei dem, was wir tun, vertrauen auf unsere Fähigkeiten und Fertigkeiten, loyal und engagiert. Mit diesen Grundlagen ist es unser Ziel, Daten zu nutzen, um unsere Abläufe zu verbessern und anderen zu helfen, nicht Mikromanagement.“
Doyle sieht das Fastems-System als praktische, angewandte Möglichkeit, den Weg in die datengesteuerte Industrie 4.0-Fertigung zu beginnen. Er sagte:„Künstliche Intelligenz wird die Fertigungsindustrie verändern, wahrscheinlich mehr als alles andere. Es wird die Art und Weise ändern, wie wir unsere Teams strukturieren und schulen.“
Herausgegeben von Manufacturing Engineering Managing Editor Candace Roulo.
Automatisierungssteuerung System
- Wo befindet sich Ihr Unternehmen auf der Lean Journey?
- Der Aufstieg des Roboters:Investition in disruptive Automatisierung
- Die Bedeutung des Stromkreisschutzes beim Design elektrischer Verteilungssysteme
- Die verschiedenen Präzisionsbearbeitungstechnologien
- Präzisionsdrehmaschinensystem spart Energie
- Automatisierungssystem fördert Zugänglichkeit und Manövrierfähigkeit
- 5 Ws der tragbaren Braillezeile
- Die 5 Werkzeuge, die Lean Manufacturing zum Erfolg führen
- „Industrial IoT Company of the Year“ geht an Emerson
- Der Wissensaustausch im Unternehmen, in der Branche