Job Shops automatisieren? Wetten!
Ein einzelner Bediener kann manchmal mehrere Roboter betreuen, die jeweils mehrere Maschinen betreuen – das summiert sich!
Wenn „Automatisierung“ das ständige Dröhnen ist, das Sie heutzutage von praktisch jedem in der Metallbearbeitung hören, sind Job-Shop-Besitzer vielleicht die einzigen, die „Nein!“ Rufen. Oder zumindest „Warte!“ Wie, fragen sie, können Sie Teile mit geringem Volumen und hoher Produktvielfalt kostengünstig automatisieren? Doch es ist nicht nur machbar, sondern wahrscheinlich notwendig.
Wie Steve Alexander, Vice President of Operations bei Acieta LLC, einem Automatisierungsintegrator mit Standorten in Waukesha, Wisconsin, und Council Bluffs, Iowa, es ausdrückte:„Die USA sind weltweit führend in der Fertigung, haben aber auch eine der höchsten Produktionsstunden pro Stunde Arbeitskosten. Job Shops konkurrieren nicht nur mit anderen lokalen Geschäften um Geschäfte, sondern auch mit anderen Ländern. Die Automatisierung kann ihre Kosten senken, sodass sie besser konkurrieren können.“
Er fügte hinzu, dass die Nachfrage nach Fertigungskapazitäten das verfügbare Arbeitskräfteangebot übersteige und „Werkstätten es möglicherweise schwierig finden, mit größeren, etablierteren Werkstätten um immer teurere Talente zu konkurrieren“. Ein Roboter kann jedoch mehrere Maschinen bedienen, und in einigen Fällen kann ein einzelner Bediener mehrere Roboter bedienen, von denen jeder mehrere Maschinen bedient.
„Das gibt den Bedienern Zeit für sekundäre Vorgänge wie das Entgraten von Teilen, das Zusammenbauen oder mehr Zeit für Qualitätsprüfungen“, sagte Alexander. Um nur zwei Beispiele zu nennen:Central United in Newburg, Wisconsin, verwendet einen einzigen FANUC M-20iB-Roboter, um zwei Drehmaschinen zu bedienen. Ein anderer Acieta-Kunde in New Berlin, Wisconsin, nutzt einen einzigen FANUC R-2000iB-Roboter zur Bedienung von vier Maschinen. „In beiden Fällen gibt es nur einen einzigen Bediener, der dafür verantwortlich ist, die Rohteile auf das Förderband oder die Wartestation zu laden, damit der Roboter sie greifen kann.“
Alexander fügte noch einen weiteren zwingenden Grund für die Automatisierung hinzu:Ergonomie. „Arbeitsunfälle sind ein Problem für Geschäfte jeder Größe. Etwas so Einfaches wie das Laden eines Teils in ein Drehfutter kann schnell zu einer sich wiederholenden Stressverletzung für einen Bediener werden, wenn dieser Vorgang hunderte Male am Tag wiederholt wird. Zusammen mit Zeitverlust und Schadenersatzansprüchen kosten diese Verletzungen Unternehmen jedes Jahr Milliarden von Dollar. Richtig integrierte Roboter können dem Bediener einen sich wiederholenden Prozess abnehmen und so das Wohlbefinden der Mitarbeiter verbessern.“
Optionen &Integratoren
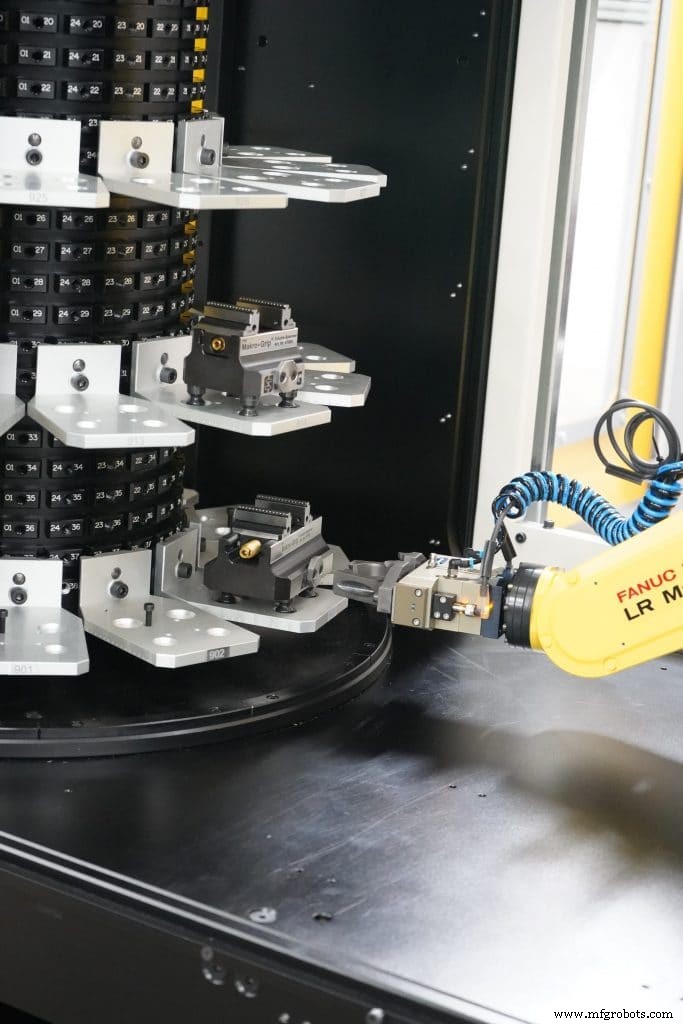
So weit, ist es gut. Aber wie John Lucier, Automatisierungsmanager bei Methods Machine Tools Inc., Sudbury, Massachusetts, erklärte, kann das einfache Ziel, „mehr Teile effizienter zu fertigen“, zu sehr unterschiedlichen Ansätzen führen, je nach Art der zu produzierenden Arbeit und den beteiligten Volumina .
Nehmen wir zum Beispiel an, ein Lohnfertiger mit mittlerem Volumen muss mehrmals pro Woche umrüsten. „Bei richtiger Planung könnte eine Zelle in der bemannten Schicht umgestellt werden, was eine schöne unbeaufsichtigte Produktion in der folgenden Schicht ermöglicht.“ Und in diesem Zusammenhang würde die erforderliche Geschwindigkeit des Roboters zu einem großen Teil von der Bearbeitungszykluszeit der produzierten Teile abhängen. Je kürzer die Zykluszeit, desto schneller muss der Roboter sein und desto unwahrscheinlicher kann ein Roboter mehrere Maschinen unterstützen.
Aber auch Geschäfte mit noch geringeren Volumina – sogar Losgrößen von einem – können gute Kandidaten für die Automatisierung sein, erklärte Lucier. Abgesehen davon, dass „die wichtigste Überlegung darin besteht, die Umrüstzeit zu verkürzen oder sogar die Rüstzeit vollständig zu eliminieren. Die Leute werden von Zykluszeit und Lade-/Entladezeit eingeholt, aber wenn Ihr Volumen so gering ist, dass die Hälfte Ihrer Zeit mit Umrüsten verbracht wird, dann kann es sinnvoll sein, die Umrüstzeit anzugreifen, selbst auf Kosten der Zykluszeit.“
Eine Möglichkeit, die Einrichtung zu „eliminieren“, besteht darin, sie zu automatisieren, und die heutigen Roboter können so programmiert werden, dass sie sowohl ihre eigene Werkzeugbestückung am Ende des Arms als auch die Werkstückhalterung in der Maschine ändern. Ein anderer Ansatz besteht darin, gemeinsame Paletten von einem Karussell (oder einer anderen Art von Stapler) zu laden, unabhängig davon, welches Teil hergestellt wird. Dadurch entfällt die Notwendigkeit, Roboterwerkzeuge zu wechseln oder unterschiedliche Lade-/Entladebewegungen für verschiedene Teile zu programmieren.
Das Methods PlusK-System geht noch einen Schritt weiter und belädt auch Werkzeughalter aus dem Karussell. Das Karussell des PlusK wurde für die Unterstützung der Maschinen der RoboDrill-Serie von FANUC entwickelt und verfügt über fünf Ringe mit jeweils 12 Stationen, also insgesamt 60 Stationen. Jede Station kann entweder eine Teilepalette oder einen Werkzeughalter aufnehmen und der Roboter kann beide Teile auf den Arbeitstisch des RoboDrill und Werkzeuge in den integrierten Werkzeugrevolver der Maschine mit 21 Werkzeugen laden.
Aber wie Lucier betonte, wenn Sie die Produktion von 30 oder 40 völlig unterschiedlichen Teilen automatisieren möchten, reichen 21 Werkzeuge möglicherweise nicht aus. „Normalerweise laden wir Teile in winzige fünfachsige Schraubstöcke von Lieferanten wie Lang Technovation“, erklärt Lucier. „Und normalerweise mischen und passen wir Teile und Werkzeuge im Karussell an. Nehmen wir an, ein Auftrag erfordert fünf Werkzeuge, die sich von den beim vorherigen Auftrag verwendeten Werkzeugen unterscheiden. Ich kann den Roboter verwenden, um jedes Werkzeug nach Bedarf zu laden oder alle fünf Werkzeuge auf einmal in den Revolver zu laden, ähnlich wie ein Bediener einen Job einrichten würde.“
Wenn Ihnen diese Überlegungen Kopfschmerzen bereiten, ist das verständlich. Denn obwohl es in den letzten Jahren viel einfacher geworden ist, Automatisierung zu implementieren, ist es immer noch schwierig genug, dass die meisten Job-Shops klug wären, Integratoren wie Acieta und Methods zu nutzen. Aus Luciers Sicht ist die Programmierung des Roboters der einfache Teil. Dinge wie der Umgang mit der automatischen Werkstückspannung, die Späneentsorgung in der Arbeitszone und wie man die Teile am besten dem Roboter präsentiert, sind die größeren Herausforderungen. Da zahlt sich eine kompetente Beratung aus.
Automatisierung älterer Maschinen
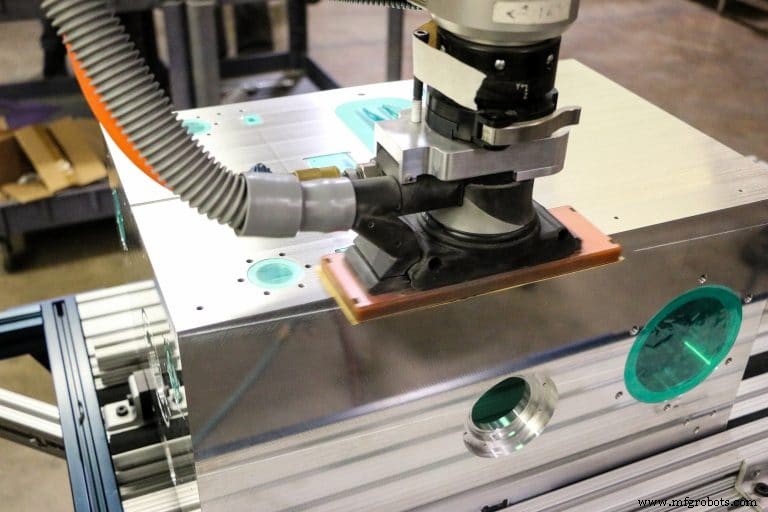
Hier ist ein Beispiel dafür, wie das passieren kann. Mitte 2017 war Gary Kuzmin, Inhaber von All Axis Machining in Dallas, Texas, ein Lehrbuchbeispiel für Frustration in der Werkstatt. Er hatte mehr potenzielle Arbeit, als die verfügbaren Arbeitskräfte unterstützen konnten, und eine Werkstatt voller deutscher High-End-5-Achsen-Bearbeitungszentren, EDMs und anderer Technologie, die die OEMs nicht wirtschaftlich mit der Art von Vielseitigkeit automatisieren konnten, die ihn aus dieser Situation herausholen könnte binden. Seine Lösung war die Investition in einen kollaborativen Roboter von Universal Robots (UR), Ann Arbor, Michigan.
Wie jeder Lohnfertiger war Kuzmins oberste Anforderung, „vollständige Flexibilität“ in seinem Betrieb zu bewahren. „Wir machen einen Teil zwei oder drei Tage lang und dann machen wir weiter mit einem anderen. In einem bestimmten Monat könnten wir 30 bis 40 verschiedene Teile auf einer Maschine herstellen.“ Also brauchte er einen Roboter, der einfach einzurichten und umzustellen war. Und er benötigte Funktionen wie kraftgesteuerte Greifer, damit sich der Roboter an unterschiedliche Teile und den Wechsel vom Rohmaterial zu einem fertigen, dünnwandigeren Teil anpassen konnte.
UR hat in allen Punkten geliefert. Seine Roboter verfügen über eine Programmierschnittstelle auf einem Handbediengerät. Sie arbeiten sicher Seite an Seite mit Menschen, da die Roboter automatisch anhalten, wenn sie einen Bediener kontaktieren (daher der Begriff kollaborativer Roboter oder „Cobot“). Sie sind leicht zu trainieren und nicht einschüchternd.
Kuzmin erklärte, dass ein Hauptgrund für die Flexibilität der Lösung von UR eine offene Architektur ist, die es Drittanbietern ermöglicht hat, Software, Bildverarbeitungssysteme, Endeffektoren und anderes Zubehör zu entwickeln, das mit UR-Robotern funktioniert. UR erleichtert den Integrationsaufwand, indem es einen One-Stop-Online-Showroom namens UR+ bereitstellt.
Trotzdem stellte Kuzmin fest, dass es keine fertige Lösung für die Programmierung des Roboters zum Schleifen oder Entgraten gab, zwei Funktionen, die er automatisieren wollte, weil sie für Menschen und insbesondere für ältere Arbeitnehmer hart sind. Daher verwendete All Axis das kostenlose Software-Entwicklungskit von UR, um eigene Routinen zu erstellen, die der Krümmung des Teils auf der Grundlage des CAD-Modells folgen.
Diese Plug-ins integrieren die Steuerung der Anwendung über das eigene Programmierhandgerät des Cobots. „Universal Robots hat fantastische Arbeit geleistet, indem es diese Lösung Geschäften wie dem unseren zur Verfügung gestellt hat“, sagte Kuzmin. „Wir sind nicht an eine proprietäre Umgebung gebunden. Stattdessen erhalten wir ein Kochbuch mit einer einfachen Möglichkeit, die Kommunikation zu erweitern“, und fügt hinzu, dass All Axis Protokolle wie TCP/IP, Ethernet, Modbus und Profinet verwendet, um Cobots und Maschinen zu verbinden.
„Ein weiterer Vorteil ist, dass wir keine speziellen Lizenzvereinbarungen bezahlen müssen – alles kommt mit dem Kauf des UR-Cobots“, sagte Kuzmin. „Wir melden uns auf der UR-Website an, um Entwickler zu werden, und laden die benötigten Elemente herunter.“
In einem anderen Beispiel entschied All Axis, dass es die Möglichkeit haben wollte, einen Cobot so schnell wie möglich von Maschine zu Maschine zu bewegen. Die Herausforderung bestand darin, ein System zu schaffen, das den Cobot sowohl zur nächsten Maschine neu ausrichtet als auch am Boden befestigt, ohne Löcher in den Beton zu bohren. Die Lösung bestand darin, einen Behälter auf den Beton zu kleben und einen Indexstift anzubringen.
„Wenn der Roboter jemals bewegt oder gewartet werden muss, entriegeln und ziehen Sie einfach die Stifte und bewegen den Roboter nach Bedarf“, sagte Kuzmin. „Wenn Sie den Roboter neu positionieren und die Stifte verriegeln, ist alles immer noch indexiert. Wir haben auch das Präsentationstablett am Roboterständer befestigt, sodass sich seine Position relativ zur Achse des Roboters nie ändert.“
Innerhalb weniger Monate waren Kuzmin und sein Team so gut in der Integration von Cobots (sie haben jetzt sieben) und so begeistert von den Vorteilen der Automatisierung, dass sie ein separates Unternehmen namens All Axis Robotics gründeten. Während Kuzmin sagte, es sei relativ einfach, eine neue Maschine zu automatisieren, indem man etwa 150.000 US-Dollar beim OEM ausgibt, sieht er ein enormes Potenzial in der Automatisierung älterer Maschinen, auf die sie sich konzentrieren.
Um ein Beispiel dafür zu nennen, wie die Automatisierung das Endergebnis bei All Axis Machining unterstützte, wurde ein Auftrag, dessen Ausführung normalerweise sechs Monate dauerte, durch den Einsatz des Roboters in zweieinhalb Monaten abgeschlossen. „Es war phänomenal. Der ROI betrug etwa sieben bis acht Monate“, sagte Kuzmin.
In seiner vielleicht beeindruckendsten Innovation kombinierte All Axis einen UR-Roboter mit einem handelsüblichen Mikroskop und einer Kamera sowie künstlicher Intelligenz (KI) und Deep Learning, um ein System zu schaffen, das Grate, Rollkanten oder Anomalien (wie z fehlende Hardware) auf einem Teil.
Das ist wichtig, denn wie Kuzmin erklärte, können viele Grate nur unter Vergrößerung identifiziert werden und die Augen eines Menschen werden nach nur 20 bis 30 Minuten einer solchen Inspektion ermüden. Aber es ist auch schwierig zu automatisieren.
„Grate sind wie Schneeflocken – keine zwei sind gleich“, sagte Kuzmin. „Unser System, das wir Aurora nennen, nutzt KI, um sich selbst beizubringen, wie ein Grat aussieht. Je mehr Grate es sieht, desto besser kann es sie erkennen. Das System identifiziert den Grat, klassifiziert ihn und sortiert das Teil, nachdem es es aufgrund des Grats aussortiert hat. Es zeichnet auch die Inspektion und die Position des Grats auf, sodass die Bediener zurückgehen können, um das Teil effizient zu korrigieren und weiterzubewegen.“
All Axis führte Aurora im Jahr 2018 ein und Kuzmin sagt, die größte Reaktion sei gewesen:„Wir haben jahrelang nach so etwas gesucht!“ Eine kommende Version des Systems wird auch die Möglichkeit beinhalten, spiralförmige Einsätze (allgemein als Heli-Coils bezeichnet) und Hardware in Teile einzusetzen.
Industrieroboter schlagen zurück!
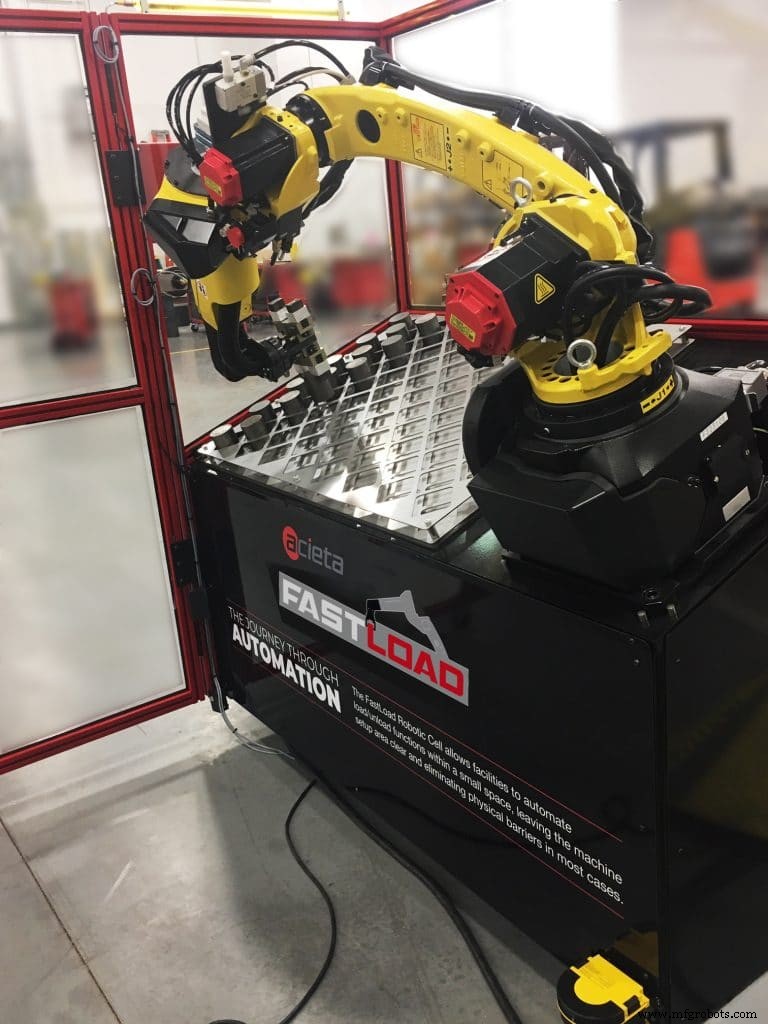
Wie bereits erwähnt, sind UR-Cobots einfach einzurichten und in eine Vielzahl von Maschinen und Zubehör zu integrieren. Aber Anbieter von Industrierobotern wie FANUC und KUKA Robotics wurden auf Funktionen wie das intuitive Handbediengerät aufmerksam und stellten ihre eigenen Versionen vor.
Lucier von Method räumte ein, dass „früher kollaborative Roboter absolut einfacher zu programmieren waren. Aber die Einrichtung eines Industrieroboters unterscheidet sich nicht mehr wirklich von der Einrichtung eines kollaborativen Roboters.“ Sogar die Einrichtungsfunktion „Greifen und ziehen“ ist bei herkömmlichen Robotern verfügbar, obwohl Lucier sagte, dass dies am besten für Fälle verwendet wird, in denen Sie das Teil einfach auf einen Tisch oder gegen einen Block stellen möchten.
„Es ist perfekt, um beispielsweise dem Roboter beizubringen, ein KMG zu laden, da die Maschine nur ungefähr wissen muss, wo sich das Teil befindet, um die Kante zu finden und dann die Messungen durchzuführen“, sagte er. „Aber wenn ich in ein Spannfutter oder einen Schraubstock lade, habe ich mehr Kontrolle, wenn ich es mit dem Programmiergerät einlerne.“
Auch für Industrieroboter gibt es vielfältiges Zubehör. Zum Beispiel, sagte Lucier, sind Schnellwechsel- und Kraftsteuerungsgreifer nicht nur bei Cobots zu finden. „Schunk hat eine Reihe von kraftmessenden Greifern, die Servomotoren verwenden und von der Pneumatik wegkommen, die schwieriger zu wechseln ist. Die Elektrik kann man wirklich einwählen.“
Die Industrieroboter-Leute haben auch Lösungen, mit denen Sie den Roboter schnell von Maschine zu Maschine umpositionieren können. Im Fall von FANUC scannt eine Kamera am Roboter drei Aufkleber auf der „neuen“ Maschine, um sich automatisch neu auszurichten.
Aber nach monatelangen Versuchen sagte Lucier, dass sie keine Situation finden können, in der eine solche Fähigkeit nützlich ist. „Einen Roboter von Maschine zu Maschine zu bewegen, bedeutet mehr als nur den Roboter zu bewegen. Denken Sie an all die Dinge, die Sie ändern müssen:Vielleicht die End-of-Arm-Werkzeuge, die Zuführung, die Abführung …“ Die bessere Lösung ist eine, bei der jede Maschine ihren eigenen Roboter hat oder ein Roboter mehrere Maschinen bedient, vielleicht mit zwei Endeffektoren, damit es ohne Eingriff zwischen den Teiletypen wechseln kann.
Es ist auch so, dass Integratoren wie Acieta und Methods traditionelle Roboter zu älteren Maschinen hinzufügen können, und Roboter kosten ungefähr so viel wie Cobots. In Anbetracht der aktuellen Angebote ist der größte Vorteil von Cobots also ihre Fähigkeit, in der Nähe von Menschen zu funktionieren, ohne den Platz und die Kosten einer Einzäunung.
Der Nachteil ist, dass sie langsamer sind als herkömmliche Industrieroboter und auf leichtere Teile beschränkt sind. Das größte Modell von UR verarbeitet Teile bis zu 10 kg (24 lb). Langsamere Lade-/Entladezeiten sind bei Teilen mit langen Zykluszeiten nicht von Bedeutung, können aber die Leistung bei Aufträgen mit mittlerem bis hohem Volumen und kürzeren Zykluszeiten verringern.
Kuzmin von Axis Machining sieht keine Notwendigkeit für Geschwindigkeit, „nur Konsistenz und Zuverlässigkeit – insbesondere bei Teilen mit langer Zykluszeit. Es ist besser, wenn ein Cobot Teile mit einer zuverlässigen Geschwindigkeit lädt und damit andere Teile entgratet, während die Maschine läuft. Und wenn Sie die Geschwindigkeit nicht brauchen, warum sollten Sie sie riskieren?“
Lucier und Alexander warnen davor, den Vorteil zu übertreiben, direkt neben dem Roboter arbeiten zu können. Zum einen, betonte Lucier, müsse man den Bediener bereits vom Bearbeitungsbereich abschirmen. Alexander fügte hinzu, dass, wenn ein Cobot ein Teil mit scharfen Kanten handhabt (wie es normalerweise bei der Bearbeitung der Fall ist), „es für einen Bediener sowieso nicht kooperativ oder sicher ist, in seiner Nähe zu arbeiten.“
Sowohl Lucier als auch Alexander sagten, die Kombination von „kollaborativen Techniken“ mit Industrierobotern biete einen nützlichen Kompromiss. „Für die Hersteller, die einen offenen Boden mit minimaler Einzäunung suchen, haben Industrieroboter die Möglichkeit, in einer zaunlosen Umgebung zu arbeiten, indem sie Bereichssicherheitsscanner verwenden“, erklärte Alexander. „Und sie können in dieser zaunlosen Umgebung ohne Geschwindigkeitseinbußen arbeiten. Wenn ein Bediener die erste Sicherheitszone betritt, wird der Roboter langsamer. Wenn der Bediener die zweite Sicherheitszone betritt, stoppt der Roboter vollständig.“
Andererseits, sagte Lucier, würde der Roboter, da die Sicherheitszone für diese Annäherung 3-4′ ist, oft langsamer werden, wenn Gabelstapler oder anderer Verkehr häufig vorbeifahren.
Wie bereits angedeutet, ist ein Bereich, der sich perfekt für Cobots eignet, die Wartung eines KMG. „KMGs sind von vornherein eigensicher“, wie Lucier es ausdrückte. „Es gibt keine Bewachung, außer um sich bewegende Komponenten herum. Sie sind nicht schnell. Sie können direkt neben ihnen stehen. Und im Allgemeinen stecken Sie das Teil nicht in eine Vorrichtung, sondern halten es vielleicht nur gegen einen V-Block oder ähnliches. Da habe ich einen kollaborativen Roboter glänzen sehen.“
Beide Experten sind sich einig, wie Alexander zusammenfasst, dass „Industrieroboter in den meisten Job-Shop- und Fertigungsanwendungen viel besser geeignet sind als Cobots.“
Überlegungen zur Software
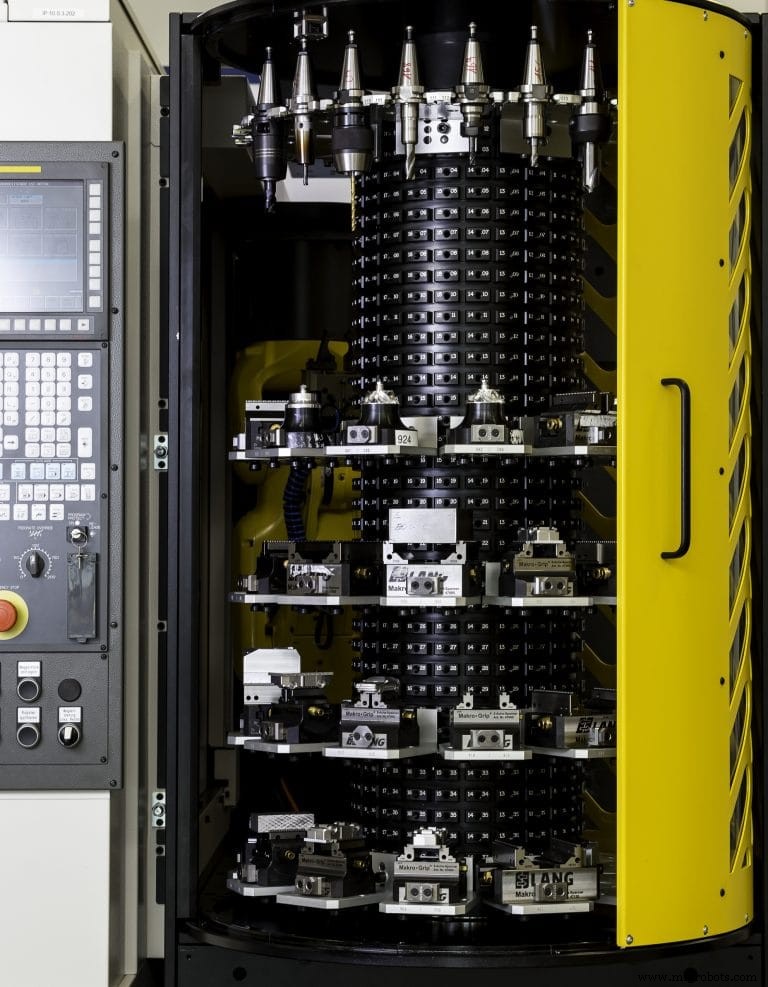
Laut Greg Mercurio, Präsident von Shop Floor Automations, La Mesa, Kalifornien, „ist Software die wichtigste Komponente in der Job-Shop-Automatisierung.“ Er sagte, Direct Numerical Control (DNC)-Software (auch als Distributed Numerical Control-Software oder „Drip Feed“-Software bekannt) „ermöglicht eine optimierte Maschinenkommunikation sowie eine Versionskontrolle für die Verwaltung von Qualität/Ausschuss und ein Mittel zur Organisation Tausender von Programmen .“
Die Hauptfunktion der DNC-Software besteht darin, Bearbeitungsprogramme direkt an die Maschine zu senden, wodurch eine Maschine mit einer relativ einfachen Steuerung in die Lage versetzt wird, eine komplexe Oberfläche zu bearbeiten.
Mercurio und alle Experten sind sich einig, dass ein gewisses Maß an Maschinenüberwachung hilfreich ist, „um die Betriebszeit und die Maschinenkapazität zu erhöhen“. Mercurio fügte hinzu, dass Produktionsdatenmanagement-Software es Unternehmen ermöglicht, papierlos zu arbeiten, und dass „Werkzeuglagerverwaltung ebenfalls eine Notwendigkeit ist. Das Beste daran ist, dass diese Lösungen alle mit CAD/CAM, ERP, MES, CMMS und mehr integriert werden können.“
Andererseits wies er darauf hin, dass kleinere Geschäfte von einer einfachen Hardware-Ergänzung stark profitieren können, bevor sie Tausende für Software ausgeben. Wenn Sie beispielsweise älteren Geräten eine RS232-zu-USB-Schnittstelle hinzufügen, werden Tropffütterungsprogramme einfacher.
„Die Hardware ist einfach zu verwenden, einzurichten und zu warten, daher ist sie die am wenigsten zeitaufwändige Automatisierungsoption
für einen kleineren Laden. Ältere RS232-Maschinen können ein USB-Laufwerk verwenden, wie neuere CNC-Maschinen, die diese Funktion ab Werk eingebaut haben. Es ist auch eine kostengünstigere Möglichkeit für sie, ihre Produktionsstätte zu modernisieren, ohne die Ausrüstung komplett auszutauschen. Es ermöglicht auch erschwingliche Speicher-Upgrades“, fügte Mercurio hinzu.
Um auf die Roboter zurückzukommen, sagte Alexander, dass es zahlreiche Softwarepakete gibt, die von Roboter-OEMs und Drittanbietern angeboten werden, die die Roboterprogrammierung offline auf einem PC ermöglichen, während der Roboter weiterarbeitet. „Mit diesen Softwarepaketen können Sie eine CAD-Datei laden und haben dann die Freiheit, Ihren Roboterpfad mit einem Stift oder einer Maus zu ‚zeichnen‘“, erklärte Alexander. „Die Software wandelt dann Ihren gezeichneten Pfad in Robotercode um, der direkt in den Roboter geladen werden kann.“
Passenderweise hat Lohnfertiger Kuzmin das letzte Wort:„Ich wollte die Produktivität verbessern. Ich tat es, indem ich Roboter hinzufügte. Und ich bin sehr zufrieden mit dem, was wir erreicht haben. Dabei sagte ich, wir sollten das allen da draußen zur Verfügung stellen, denn das wird die Fertigung in unserem Land viel wettbewerbsfähiger machen.“
Automatisierungssteuerung System
- Wetten Sie auf die richtige Cloud
- Wie detailliert für Stellenpläne?
- Sie haben keine Zeit, die Arbeitssicherheit zu vernachlässigen
- Endbearbeitungsrevolver reduziert Zykluszeit
- Wenn Sie etwas verbessern wollen, messen Sie es
- Die Automatisierung kleiner NC-Programmieraufgaben zahlt sich im Laufe der Zeit aus
- 5 Anzeichen dafür, dass Sie Kranreparaturen benötigen
- Woran Sie erkennen, dass Sie neue Kranteile benötigen
- Benötigen Sie neue Hardware für Industriebremsen?
- Gründe, warum Sie eine kundenspezifische Bearbeitung benötigen