Arten von Formverfahren – Gesamtübersicht [mit Bildern]
In diesem Artikel besprechen wir Formverfahren, Arten von Formverfahren, die auf der Grundlage verschiedener Begriffe wie Trockensandformen, Grünsandformen, Bankformen usw. klassifiziert werden.
Formverfahren im allgemeinen Gebrauch können nach verschiedenen Formen klassifiziert werden. Sie können grob wie folgt klassifiziert werden:
- Handformen , und
- Maschinelles Formen .
In Stück- und Kleinserienfertigung werden Gießerei-Praxis-Sandformen von Hand gefertigt; Formmaschinen werden in der Großserien- und Massenfertigung eingesetzt.
Arten von Formprozessen
Formgebungsverfahren werden oft klassifiziert nach :
(A) Die Art des Materials, aus dem die Form besteht, oder
(1) Grüne Sandformen,
(2) Trockene Sandformen,
(3) Hautgetrocknete Formen,
(4) Lehmformen.
(B) Die bei der Herstellung der Form verwendeten Methoden.
(1) Bankleiste,
(2) Bodenleiste,
(3) Grubenformung,
(4) Sweep-Moulding und
(5) Plattenformen.
Formverfahren basierend auf dem verwendeten Sand
1. Formteil aus grünem Sand
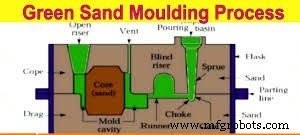
Formteil aus grünem Sand ist eine vielseitige, schnelle und kostengünstige Methode zur Herstellung von Formen für hochwertige Eisen- und Nichteisengussteile. Grüner Sand besteht aus Quarzsand, Wasser, Bentonit und anderen Zusätzen wie Kohlenstaub für Eisenanwendungen.
Grünsandformen werden mit natürlichen Formsanden oder mit Mischungen aus Quarzsand, Bindeton und Wasser hergestellt. Diese Materialien werden gründlich in Proportionen gemischt, die die gewünschten Eigenschaften für die jeweilige Arbeitsklasse ergeben.
2. Trockene Sandform
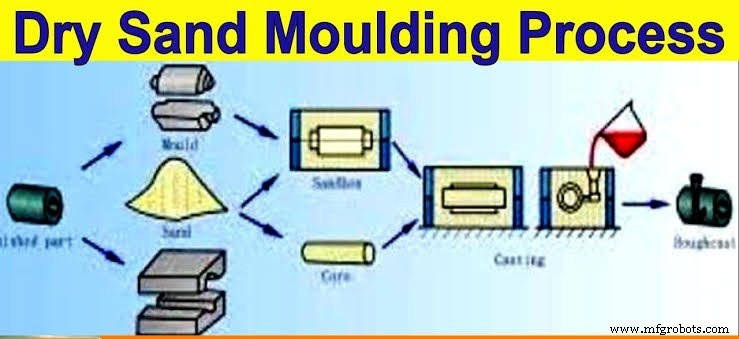
Der Formprozess bei der Herstellung von Trockensandformen ähneln denen, die beim Grünsandformen verwendet werden, außer dass eine andere Sandmischung verwendet wird und alle Teile der Form in einem Ofen getrocknet werden, bevor sie zum Gießen wieder zusammengesetzt werden.
Die grüne Sandform hängt von der Feuchtigkeit und dem natürlichen Tonbindemittel im Sand ab, um ihre Form zu behalten. Der für Trockensandformen verwendete Sand hängt jedoch von zugesetztem Bindematerial wie Mehl, Harz, Melasse oder Ton ab. Die Materialien werden mit einem dünnen Tonwasser gründlich gemischt und temperiert. Die Menge des Bindemittels wird durch die Gußgröße bestimmt gemacht.
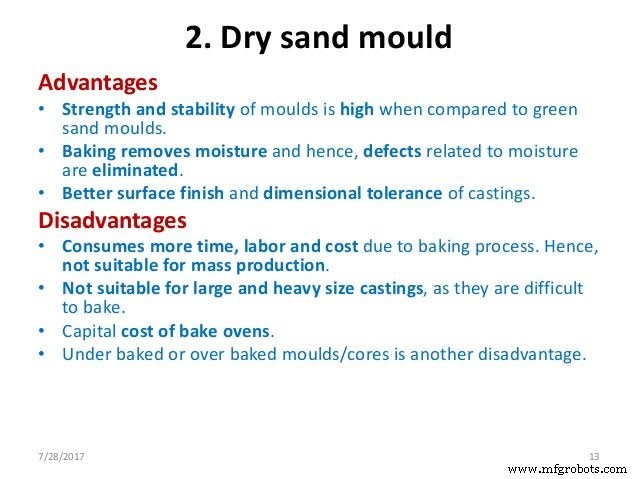
3. Hautgetrockneter Formkörper
Der hautgetrocknete Formprozess ist ein Prozess, bei dem die Feuchtigkeit aus der Oberflächenschicht des gestampften Sandes bis zu einer Tiefe von etwa 25 mm oder mehr unter Verwendung von Gasbrennern oder Heizgeräten getrocknet wird. Es hat bis zu einem gewissen Grad die Vorteile sowohl des Grünsand- als auch des Trockensandformens. Da die zum Trocknen benötigte Zeit geringer ist als bei trockenem Sand, ist das Verfahren kostengünstiger. Die Hauttrocknung eignet sich besonders für sehr große Formen oder für Arbeiten, die genaue Details erfordern.
4. Lehmform
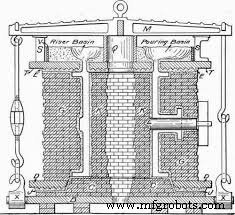
Lehm ist Ton und Sand, der mit Wasser zu einer dünnen plastischen Mischung vermischt wird, aus der Formen hergestellt werden. Lehmsand enthält auch Schamotte oder Ganister. Der Lehm muss ausreichend haftfähig sein, damit er an den senkrechten Flächen haften kann. Lehmformen bedürfen immer einer besonderen Vorkehrung, um eine ausreichende Belüftung zu gewährleisten. Ziel ist es, Poren in der ansonsten kompakten, engmaschigen Masse künstlich zu öffnen. Also verschiedene Arten von organischem Material wie gehäckseltes Stroh und insbesondere Pferdemist , wird mit dem Sand vermischt. Eine typische Lehm-Sand-Mischung ist unten angegeben:
Dieser wird als Gips auf die raue Struktur der Form aufgebracht, die normalerweise aus Mauerwerk besteht, und die genaue Form wird durch eine rotierende Bewegung um eine zentrale Spindel gegeben, wie in der Abbildung gezeigt. Gusseisenplatten und -stäbe werden verwendet, um das Mauerwerk zu verstärken, das den Formstoff zurückhält. Lehmformen können auch durch die Verwendung eines Skelettmusters aus Holz hergestellt werden. Die Oberflächen von Lehm werden geschwärzt und vor dem Zusammenbau getrocknet.
Lehmformen werden hauptsächlich zur Herstellung großer Gussstücke verwendet, für die es zu teuer wäre, vollständige Muster und gewöhnliche Kolbenausrüstung zu verwenden. In Lehmformen werden Gegenstände wie große Zylinder, Rundkessel, chemische Töpfe, große Zahnräder und andere Maschinenteile hergestellt.
Arten von Formprozessen basierend auf den verwendeten Methoden
1. Bank- und Bodenleiste
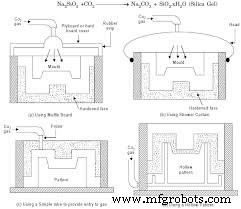
Bankleiste gilt hauptsächlich für Formen, die klein genug sind, um auf einer Werkbank mit einer für den Former bequemen Höhe hergestellt zu werden.
Sehr schwere Gußstücke oder Gußstücke mit beträchtlicher Tiefe oder Fläche können im Sand des Gießereibodens ähnlich wie Grünsand- oder Trockensandformung geformt werden. In solchen Fällen fungiert der Boden selbst als Widerstand, und dieser kann mit einem Oberkasten abgedeckt oder die Form offen gegossen werden.
2. Grubenform
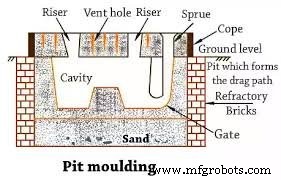
Grubenformung Prozess :Formen für große Aufträge werden im Allgemeinen in einer ausgehobenen Grube hergestellt im Gießereiboden, was das Anheben des Modells und das einfache Gießen der Form erleichtert. Da eine als Bremse fungierende Grube nicht überrollt werden kann, kann der Sand unter dem Muster durch Einstreuen gerammt werden. Das Muster kann an der richtigen Stelle aufgehängt werden, wenn der Sand darunter gerammt wird. In anderen Fällen, wenn die untere Oberfläche eines Musters flach ist, kann das Muster auf einer ebenen, dafür gerammten Oberfläche platziert werden.
Auf den Boden der Grube wird ein Koksbett gelegt, mit Stroh und dann mit einer Sandschicht bedeckt, die gerammt und eingeebnet wird. Das Koksbett ist durch vertikale Entlüftungsrohre in den Ecken der Grube mit der Atmosphäre verbunden, um einen Auslass für die erzeugten Gase bereitzustellen. Wenn der Boden leicht feucht ist, werden die Innenflächen der Grube mit Teerpappe, Ziegeln oder Holzbrettern ausgekleidet. Im Allgemeinen ist eine Box erforderlich, um den Formprozess abzuschließen. Läufer, Gießbecken, Zuführungen werden darin geschnitten.
3. Kehrleiste
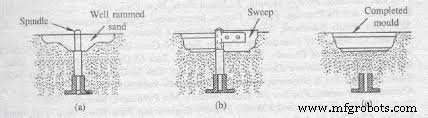
Kehrleisten werden zum Formen von Teilen verwendet, deren Form die einer Rotationsfläche ist. Im Vorprozess werden eine Basis 1 und eine Spindel 2 gut in den Gießereiboden platziert. Der Sand wird eingefüllt und gerammt, bis der Aushub ungefähr die Form und Größe des erforderlichen Gussstücks hat. Dies ist in Abbildung a dargestellt.
Dann wird ein Fegerhalter 5 in den Spindelsteg eingesetzt, der Feger 6 wird mit Schrauben und Muttern befestigt. Die Oberfläche der Form wird durch das Profil der Krümmung erzeugt, wenn sie um die Spindel gedreht wird, wie in Abbildung (b) gezeigt. Nach dem Fegen wird die Spindel entfernt und die Form in der Mitte geflickt. Der Anschnitt wird dann geschnitten und die Form ist fertig zum Gießen. Dies ist in Abb. (c) dargestellt.
4. Plattenformen
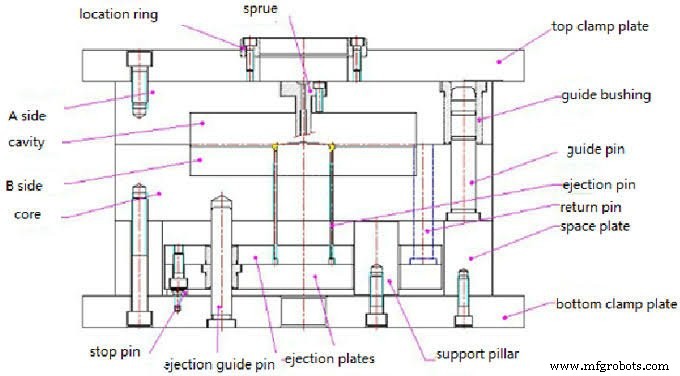
Plattenformen Prozess :Bei diesem montierten Trennverfahren wird das Muster über den Scheitel in zwei Hälften geteilt und auf Platten mit parallelen Seiten in der gleichen Form wie die Figur geteilt. Die Verwendung von Platten bietet die folgenden Vorteile :
- Die Muster lassen sich einfach handhaben und schnell.
- Die Aufgabe, die Verbindung zwischen den beiden Teilen der Form herzustellen, wird erleichtert, da die Platte ihre eigene Verbindung bereitstellt, wenn der Formkasten aufgerammt wird.
- Das Muster kann schnell gezeichnet werden , da die Platte die Seite der Schachtel überlappt und die Stifte, die sie in Position halten, während des Ziehvorgangs als Führungen dienen.
Einige spezielle Formverfahren
In den letzten Jahren spezielle Formverfahren wurden entwickelt, um Zeit und Kosten zu sparen, Formen und Kerne von besserer Qualität herzustellen und die Produktivität mit weniger Aufwand und Können zu steigern. Im Allgemeinen erfordern diese Verfahren nicht in allen Fällen ein Trocknen oder Backen von Formen oder Kernen, und aufgrund chemischer Reaktionen in ihnen findet eine schnelle Härtungswirkung statt. Der Einsatz folgender spezieller Formgebungsverfahren hat in den letzten Jahren stark zugenommen.
1. Kohlendioxidformen
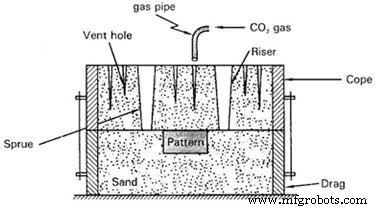
Kohlendioxid-Formteil Prozess: Das Verfahren ist im Grunde ein Härteverfahren für Formen und Kerne. Das Arbeitsprinzip des CO2-Prozesses basiert darauf, dass CO2-Gas entsteht durchgereicht wird eine Sandmischung mit Natriumsilikat (Wasserglas) wird der Sand sofort extrem fest gebunden, da das Natriumsilikat zu einem steifen Gel wird. Dieses Gel ist dafür verantwortlich, der Form die nötige Festigkeit zu verleihen.
2. Ferro-Silizium-Formteil
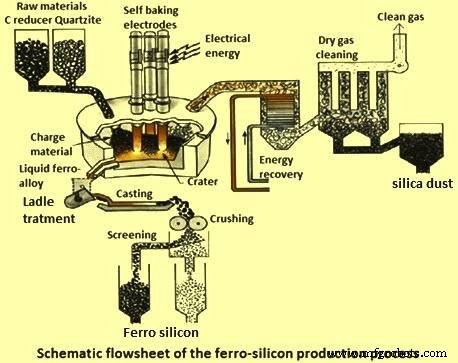
Ferro-Silizium-Formteil :Dieses Formverfahren basiert auf dem Prinzip dass wenn Natriumsilikat und pulverisiertes Ferrosilizium sind gemischt im Verhältnis 2,25 :1 auf das Gewicht, findet eine Schaumbildung statt und die Temperatur steigt durch eine exotherme Reaktion zwischen ihnen. Bei Raumtemperatur findet diese Reaktion langsam statt, aber sobald die Temperatur erhöht wird, beschleunigt sich die Reaktion. Schließlich bildet der Quarzsand eine harte Schwammmasse. Es ist kein Einbrennen der Form oder des Kerns wie beim CO2-Verfahren notwendig.
Normalerweise für Eisenguss sauberer,trockener Sand von 65 Mesh , während für Nichteisenguss , Sand von 100 mesh ist geeignet. Die Formen sind vor dem Verschließen mit einer geeigneten Schlichte einzustreichen.
3. Dicalciumsilikat-Formteil
Dicalciumsilikat-Formteil :Dieses Formverfahren basiert auf dem Prinzip das sind etwa 2-3 Prozent Dikalziumsilikat , bekannt als sehr effektives Härtemittel, und 5 Prozent Natriumsilikat sind gemischt mit Sand Zusammen mit geeigneten Schaumchemikalien erhöht sich die Fließfähigkeit der Sandmasse. Dadurch kann die Sandmischung problemlos in die Form fließen und das Stampfen, wie es bei herkömmlichen Formverfahren erforderlich ist, entfällt. Schließlich bildet der Sand eine harte Masse mit ausreichender Kollabierbarkeit
Der wichtigste Vorteil dieses Formverfahrens ist die große Einsparung an Arbeitsaufwand und Formanlagen da kein Trocknen oder Stützen erforderlich ist. Andererseits werden qualitativ hochwertige fehlerfreie Gussteile hergestellt. Dies findet breite Anwendung in mittleren und schweren Gussteilen, sowohl in Grauguss als auch in Stahlguss.
4. Zement-Sand-Formen
Zement-Sand-Formen :Portlandzement kann als Bindematerial verwendet werden, um Sandkörner zusammenzubinden. Es hat sich herausgestellt, dass eine gute Kombination aus Festigkeit, Durchlässigkeit und Fließfähigkeit durch die Verwendung von Zement zusammen mit Natriumsilikat erreicht wird. Mit Schaumchemikalien in der Sandmischung kann auch fließfähiger Zementschlamm hergestellt werden. Das Stampfen von Sand wird somit erheblich reduziert. Eine gute Bindung kann jedoch in Sand mit der Zugabe von etwa 2 Prozent 2 Zement, 4-5 Prozent Natriumsilikat und 1 Prozent Pech oder Melasse entwickelt werden.
Diese Formen erzeugen eine glatte und genaue Oberfläche, aber der Hauptnachteil von zementgebundenen Sandformen ist, dass sie schwer aus der Form zu schlagen sind.
5. Schalenformung
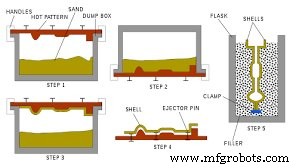
Schalenformen :Nach dem Namen seines Erfinders wird das Maskenformen auch als Croning-Verfahren bezeichnet oder C-Prozess . Dies ist eine Variante der harzgebundenen Sandtechnik zum Gießen von Stahl, Eisen oder NE-Legierungen.
Die Form wird aus einer Mischung aus feinem Sand (100-150 Mesh) und einem wärmehärtbaren Harzbindemittel gebildet, das gegen ein erhitztes Metallmodell, vorzugsweise aus Grauguss, platziert wird. Wenn die Mischung auf diese Weise erhitzt wird, härtet das Harz aus, wodurch die Sandkörner aneinander haften und eine stabile Schale bilden, die genau den Abmessungen und der Form des Musters entspricht und die Hälfte einer Form darstellt.
Nachdem die Schale ausgehärtet und von dem Muster abgezogen worden ist, werden alle erforderlichen Kerne eingesetzt, die zwei Hälften der Form werden aneinander befestigt, in eine Form gegeben und Sicherungsmaterial hinzugefügt; dann ist die Form fertig zum Gießen.
6. Heiß- und Kaltboxformen
Der Hot-Box-Prozess , besonders geeignet für die Kernherstellung, verwendet im Grunde die gleichen Materialien wie beim Schalenformen, aber hier wird das Harz zum Beschichten der Sandkörner aufgetragen. Die Harz-Sand-Mischung wird dann über das auf 200° bis 300°C erhitzte Metallmodell oder den Kernkasten geblasen und es wurde ihm ermöglicht, eine feste Masse zu bilden, anstatt eine Schalenbildung zuzulassen.
Es sind jetzt spezielle Hot-Box-Maschinen erhältlich, bei denen die Sandmischung über das erhitzte Modell geblasen wird, der geblasene Sand gehärtet wird und die Form oder der Kern dann von dem Modell oder Kernkasten abgestreift wird.
Es werden eine größere Maßgenauigkeit und höhere Produktionsgeschwindigkeiten als beim Formpressen erreicht. Dies ist ein Form- und Kernherstellungsverfahren, das im Wesentlichen für die mechanisierte Herstellung kleiner Gussstücke in großen Mengen erforderlich ist.
Das Cold-Box-Verfahren besteht aus dem Mischen von feinem trockenem Sand entweder Polyisocyanatharz Ordner und Alkydphenolharz B. Einblasen der Mischung in einen abgedichteten Kernkasten und Injizieren eines luftgetragenen Katalysatortriethylamindampfs durch den Kernkasten. Die Hydroxylgruppe des flüssigen Phenolharzes verbindet sich mit der Isocyanatgruppe, um ein steifes Urethanharz zu bilden. Die beiden Bindemittelkomponenten werden üblicherweise in einem Verhältnis von 1:1 verwendet, wobei dem Sand 1 bis 2 Gewichtsprozent der Harzmischung zugesetzt werden. a
Das Verfahren hat den Vorteil, dass keine Modellerwärmung erforderlich ist und die Aushärtung in nur 20–30 Sekunden erfolgt. Es handelt sich also um ein einfaches, hochproduktives Kernherstellungsverfahren, das sich hervorragend für kleine Gussteile eignet, die in großen Mengen benötigt werden.
7. Einbettformung
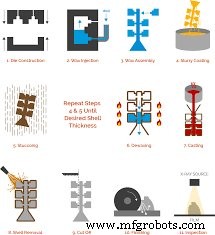
Investieren :Dieser Prozess der Gussherstellung wird oft als „Wachsausschmelzverfahren“ bezeichnet “ und „Feingussverfahren “. Der Guss kann bei diesem Verfahren mit sehr engen Toleranzen hergestellt werden und erfordert keine nachträgliche Bearbeitung.
Es besteht hauptsächlich aus zwei Phasen die in der Abbildung dargestellt sind. Zunächst wird ein Urmuster aus Holz oder Metall hergestellt, um das herum eine Form geformt wird. Er besteht nicht aus Formsand, sondern aus Gelatine oder einer niedrigschmelzenden Legierung, die über das Urmodell gegossen wird. Diese Urform besteht wie üblich aus zwei Teilen und kann geöffnet werden. Es wird zur Herstellung des „verlorenen Musters“ verwendet “.
8. Gipsformen
Gipsformen :Bei dieser Methode wird die Form vorbereitet in Gips oder Gips. In der Praxis wird der Gips mit Talkum, Asbest, Fasern, Quarzmehl und einer kontrollierten Menge Wasser gemischt, um eine Aufschlämmung zu bilden. Diese Gipsaufschlämmung wird über das in einem Kolben eingeschlossene Metallmuster gegossen.
Die Form wird vibriert und die Aufschlämmung abbinden gelassen. Das Muster wird nach etwa 30 Minuten entfernt, wenn das Abbinden abgeschlossen ist, und die Form wird getrocknet und durch langsames Erhitzen auf etwa 200°C in einem Durchlaufofen gesichert. Einsätze und Kerne werden durch Führungsstifte platziert, zurechtkommen und schleppen. Geschmolzenes Metall wird dann in die Form gegossen. Abschließend wird der Guss in der Form abgekühlt, ausgeschüttelt und die Form zerstört. Die Gussteile werden dann von Anschnitten, Angüssen und Graten befreit.
9. Keramikformteil
Im Keramikguss Bei diesem Verfahren wird eine dicke Aufschlämmung, bestehend aus speziell entwickelten Keramikaggregaten und einem flüssigen chemischen Bindemittel (Silikonester auf Alkoholbasis), über das wiederverwendbare gespaltene und angegossene Metallmuster gegossen, das normalerweise auf einer Matchplatte montiert ist. Der Schlicker füllt alle Hohlräume und Vertiefungen von selbst aus und es ist kein Stampfen oder Rütteln der Form erforderlich. Das Muster wird zurückgezogen, nachdem es sich in etwa 3 bis 5 Minuten gesetzt hat. Die Keramikmasse wird dann aus dem Kolben entfernt, mit einem Härter behandelt, um die chemische Stabilisierung zu fördern, und in einem Ofen auf etwa 980°C erhitzt, um das flüssige Bindemittel zu entfernen. Die Form ist dann bereit zum Gießen von geschmolzenem Metall.
10. Saugformen
Saugformen Prozess: Bei diesem Verfahren wird ein Vakuum erzeugt, indem Luft aus dem Formraum abgezogen wird. Anschließend wird Formsand eingesaugt und der Hohlraum verfüllt. Der Sand kann danach in das Muster gerammt werden. Das Verfahren wird zum Gießen von Eisen, Stahl und Aluminium verwendet.
Wir haben versucht, alle wichtigen Punkte in Bezug auf den Formprozess und seine Arten und Klassifizierungen abzudecken. Ich hoffe, Ihnen hat dieser Artikel gefallen. Bitte geben Sie Ihr Feedback im Kommentar unten ab.
Industrietechnik
- MTBF:Ein vollständiger Überblick
- 5 verschiedene Arten von Rechenzentren [mit Beispielen]
- Formsand:Arten und Bestandteile | Gießen | Metallurgie
- Eigenschaften von Formsand | Materialien | Gießen | Metallurgie
- Was ist Formsand? - Arten und Eigenschaften
- Arten von Sand, die im Formprozess verwendet werden
- Kolben – Vollständige Übersicht
- Definition, Prozess und Typen von Fräsmaschinen
- Bedeutung und Typen des Herstellungsprozesses
- Arten von Sandgussgeräten