Unausgeglichene Wahrnehmungen
Steigern ausgewogene Werkzeuge die Produktivität? Die Auswirkung von Unwucht ist eine der einfachsten physikalischen Theorien, die sich jeder vorstellen kann. Überlegen Sie, was passiert, wenn Sie zu viele nasse Handtücher auf einer Seite Ihrer Waschmaschine haben, während sie sich dreht. Oder wie Sie fahren würden, wenn Ihr Auto keine ausgewuchteten Räder hätte.
Diese Szenarien sind leicht vorstellbar, aber die Auswirkung der Unwucht ist bei Werkzeughaltern für Fräsanwendungen aufgrund mehrerer Missverständnisse, die in der Formenbauindustrie seit Jahren bestehen, nicht so offensichtlich. Darüber hinaus werden die Vorteile des Auswuchtens von Werkzeughalterbaugruppen bei allen Geschwindigkeiten oft einfach übersehen.
Ein ausgewogener Rückblick
Es war die Formenbauindustrie, die als erste erkannte, wie wichtig es ist, wirklich ausgewuchtete Werkzeughalterbaugruppen zu verwenden. Eine Werkzeughalterbaugruppe besteht aus Werkzeughalter, Schneidwerkzeug, ggf. Spannbolzen, Mutter, Spannzange usw. Anfang bis Mitte der 90er Jahre gab es Bearbeitungszentren, die bis zu 15.000 U/min schnell laufen konnten eine Reihe von Spindelausfällen. Die weniger massiven Spindeln auf diesen Hochgeschwindigkeitsmaschinen und die extreme Unwucht der meisten verwendeten Werkzeughalter machten die Unwucht zu dem zu lösenden Problem.
In den frühen 90er Jahren gab es keine bekannte Maschine auf dem Markt, die speziell dafür ausgelegt war, die Werkzeughalterbaugruppe genau auszugleichen. Infolgedessen kauften hochmoderne Unternehmen, die versuchten, der technologischen Kurve einen Schritt voraus zu sein, Auswuchtmaschinen, die zum Auswuchten von Teilen wie Rotoren, Rädern, Kurbelwellen, Turbinen usw. entwickelt wurden – keine Werkzeughalter. Allerdings haben diese Auswuchtmaschinen die Baugruppen tatsächlich aus dem Gleichgewicht gebracht, sodass die Kunden bei der Bearbeitung mit ihren „ausgewuchteten“ Werkzeughaltern keinen merklichen Unterschied feststellen konnten.
In den späten 90er Jahren kam schließlich eine Auswuchtmaschine auf den Markt, die wirklich Werkzeughalterbaugruppen auswuchtete. Darüber hinaus umfassten weitere um diese Zeit eingeführte Auswuchtfortschritte feinere, „vorgewuchtete“ Werkzeughalter sowie Werkzeughaltersysteme, die eine konsistentere Auswuchtwiederholbarkeit beim Wechseln von Schneidwerkzeugen (d. h. Schrumpfpassungs-Werkzeughalter) bieten. Diese Kombination von Entwicklungen ermöglichte es Formenbauern, den Einsatz der neuesten Hochgeschwindigkeitstechnologien zu beschleunigen und zu optimieren und Formen mit feineren Oberflächen herzustellen, was zu einer stark reduzierten Polier- und/oder Erodierarbeit führte.
Obwohl die Werkzeugindustrie vor zwei Jahrzehnten die Notwendigkeit erkannte, ausgewuchtete Werkzeughalter für ihre Hochgeschwindigkeitsanwendungen zu verwenden, ist die Industrie immer noch etwas verwirrt darüber, wie wichtig es ist, wirklich ausgewuchtete Baugruppen zu verwenden.
Ein Missverständnis beim Auswuchten von Werkzeughaltern ist die Annahme, dass nur die Verwendung eines vorgewuchteten Werkzeughalters ausreicht. Die Verwendung dieser vorgewuchteten Werkzeughalter wird zwar dringend empfohlen, garantiert jedoch nicht die vollständige Nutzung der Werkzeugmaschine. Nach dem Wechseln von Schneidwerkzeugen ist das Messen der Unwucht einer Werkzeughalterbaugruppe unerlässlich, um das maximale Potenzial aller Werkzeugmaschinen in einer Werkstatt voll auszuschöpfen. Sogar Maschinen mit niedrigerer Drehzahl (mit 8.000 U/min) können ihr volles Potenzial ausschöpfen, wenn sie ausgewuchtete Werkzeughalterbaugruppen verwenden. Fein ausbalancierte Werkzeughalterbaugruppen bieten viele Vorteile, einschließlich erhöhter Produktivität, Sicherheit und langer Lebensdauer von Schneidwerkzeug und Spindel. Nur wenn die Werkzeughalteranordnung einen präzisen Rundlauf und Gleichgewicht aufweist, können die optimalen Schnittbedingungen genutzt werden. In diesem Fall gilt die Faustregel:Zu viel Balance ist besser als zu wenig.
Was passiert mit den bereits im Werk befindlichen unausgeglichenen Haltern? Obwohl es in der Praxis unvermeidlich ist, unwuchtige und unwuchtige Halter zu mischen, bedenken Sie, dass ein einziger Bearbeitungsvorgang mit einem unwuchtigen Halter bei hoher Drehzahl die erforderliche Bearbeitungsgenauigkeit zunichte machen und die Spindel beschädigen kann. Aus diesem Grund sollten Werkzeugaufnahmen vorzugsweise im Werk selbst ausgewuchtet werden. Ist dies nicht der Fall, empfiehlt es sich, das Auswuchten von Werkzeughaltern zu einem Bestandteil der Warenannahme und Qualitätskontrolle zu machen. Seien wir ehrlich, woher wissen Sie, in welchem Zustand sich Ihre Werkzeughalterbaugruppen befinden, es sei denn, Sie haben eine Maschine, um sie zu überprüfen?
Ursachen und Folgen von Unwucht
Unwucht entsteht durch eine ungleichmäßige Gewichtsverteilung während der Rotation, wodurch Fliehkräfte entstehen, die mit der Drehzahl quadratisch ansteigen. Das heißt, bei gleicher Unwucht erzeugt die Spindel bei einer Drehzahl von 10.000 U/min eine 25-mal höhere Fliehkraft als bei einer Drehzahl von 2.000 U/min. Daher wirkt sich eine Unwucht in Werkzeughalterbaugruppen besonders negativ auf die Hochgeschwindigkeitsbearbeitung, schwere Werkzeuge oder Schneidwerkzeuge mit komplexen Geometrien aus.
Eine Hauptfolge der Unwucht ist diese Zentrifugalkraft, die die Spindellager belastet, was die Lebensdauer der Spindel halbieren kann. Daher empfiehlt sich immer der Einsatz von ausbalancierten Werkzeugen; Andernfalls sind Spindelgarantien nicht vorhanden oder eingeschränkt.
Eine weitere Folge sind die Schwingungen, die entstehen, wenn sich die Wirkrichtung der Fliehkraft bei rotierender Spindel ändert. Diese Vibrationen werden auf die gesamte Maschine und das Schneidwerkzeug übertragen, wodurch die Lebensdauer des Schneidwerkzeugs verkürzt wird. Es wurde berichtet, dass die Werkzeuglebensdauer einer unausgeglichenen Werkzeughalteranordnung um durchschnittlich 10 Prozent verringert wird, was zu einem Anstieg der Schneidwerkzeugkosten führt. Diese Vibrationen sind nicht nur schädlich für die Spindel und das Schneidwerkzeug; sie beeinträchtigen auch die Zuverlässigkeit des gesamten Prozesses und übertragen sich auf das Ergebnis der Bearbeitung. Vibrationen erzeugen Rattermarken, die durch zusätzliche Feinbearbeitung oder Handarbeit entfernt werden müssen.
Um die richtige Prozesssicherheit zu erreichen und die geforderten Endergebnisse zu erzielen, müssen Schwingungen reduziert werden. Eine Methode hierfür erfordert die Verringerung der Spindeldrehzahl, des Vorschubs und der Schnitttiefe. Dies kann zu einem glatteren Schnitt führen, verringert aber auch die Metallabtragsraten und die Produktivität.
Investitions-Intelligence
Das Problem mit sinkender Zerspanungsleistung und Produktivität wird nach einer einfachen Analyse deutlich:Ein Bearbeitungszentrum kostet 100 $ pro Stunde im Betrieb (Einschichtbetrieb, 1.600 Betriebsstunden pro Jahr). Mit einer 10-prozentigen Verlängerung der Metallentfernungszeit sparen Sie 10 $ pro Stunde, was 16.000 $ pro Jahr entspricht.
Ein weiterer Vorteil einer ausgewogenen Werkzeughalterbaugruppe ist die längere Lebensdauer der Spindel, die der Schlüssel zu Kosteneinsparungen und Maschinenzuverlässigkeit ist. Es ermöglicht einen planbaren Spindelwechsel und eliminiert ungeplante Maschinenstillstände. Ein wirklich ausgewogenes System kann Einsparungen von mehr als 20.000 US-Dollar pro Jahr und Maschine erzielen. Und dies beinhaltet noch nicht einmal zusätzliche Einsparungen, die durch verbesserte Oberflächenqualität der Teile, erhöhte Maßhaltigkeit und weniger Maschinenausfälle oder -stillstandszeiten realisiert werden können.
Diese Zahlen relativieren den Einwand gegen die Kosten einer Auswuchtmaschine. Man könnte argumentieren, dass eine Investition nur dann teuer ist, wenn sie sich nicht oder nicht schnell genug amortisiert. Die vorgenannten Berechnungen zeigen, dass sich eine Auswuchtmaschine tatsächlich sehr schnell amortisieren kann. Beachten Sie, dass ein einzelner Bearbeitungsvorgang mit einem unwuchtigen Halter bei hoher Drehzahl die erforderliche Bearbeitungsgenauigkeit zunichte machen und die Spindel beschädigen kann. Bedenken Sie, dass allein ein Spindeltausch mehr kosten kann als eine Auswuchtmaschine.
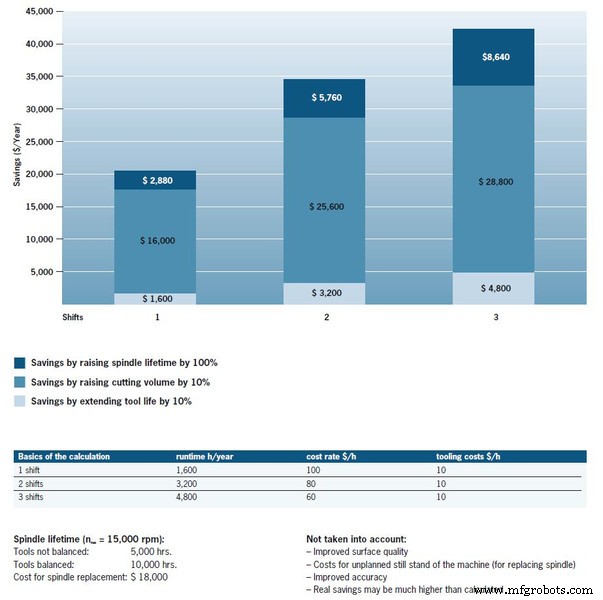
Messtests
Das Messen des Gleichgewichts einer Werkzeughalterbaugruppe ist notwendig, um einen konsistenten Bearbeitungsprozess zu gewährleisten. Wenn Sie eine wirklich ausgewuchtete Baugruppe verwenden, ist nach dem Hinzufügen eines Schneidwerkzeugs normalerweise kein weiteres Feinauswuchten erforderlich, insbesondere bei Schrumpffuttern.
Feingewuchtete Werkzeugaufnahmen sind ein Schritt in die richtige Richtung. Doch welche Auswirkungen haben die Schneidwerkzeuge bzw. Planfräser auf die Gesamtunwucht der Baugruppe? Um diese Frage zu beantworten, sehen wir uns diesen einfachen Messtest an:
Die Messungen wurden auf einer werkzeugdynamischen Auswuchtmaschine mit einem Weldonfutter, einer Spannzange und einem Schrumpffutter sowie einem Planfräser durchgeführt. Alle sind feingewuchtete Produkte mit einem Wellendurchmesser von 20 mm in der kurzen Ausführung. Die Messanforderungen waren Wuchtgüte G =2,5 bei Betriebsdrehzahl 25.000 U/min/Messvorgang eine Ebene (statisch). Zunächst wurde die Unwucht an vier verschiedenen Meißelhaltertypen gemessen (d. h. ohne Schneidwerkzeuge). Die Unwucht der Halter lag erwartungsgemäß stets innerhalb der Toleranzgrenzen. Nachfolgende Messungen mit Schneidwerkzeugen in diesen feingewuchteten Haltern zeigten deutliche Unwuchten, insbesondere bei den heute weit verbreiteten Werkzeugen mit Spannfläche.
Bei Baugruppen mit Werkzeugen mit zylindrischem Schaft und bei symmetrischer Werkzeuggeometrie in Schrumpf- und Spannfuttern wurde keine nennenswerte Unwucht festgestellt. Die gemessenen Werte lagen bei 0,8 bzw. 1,3 Gramm Millimeter (gmm). Werkzeuge mit zylindrischem Schaft und symmetrischen Schneidkanten weisen nur eine geringe Unwucht auf. Die Schrumpffutter haben keine beweglichen Teile und spannen das Werkzeug zentrisch, auch hier entsteht kaum zusätzliche Unwucht. Beim Spannzangenhalter könnte die Spannmutter ein Problem darstellen, da sie unsymmetrisch aufgebaut ist, aber aus diesem Grund sind die Muttern selbst speziell gewuchtet.
Werkzeuge mit Spannfläche hingegen konnten die Wuchtanforderungen überhaupt nicht erfüllen. Selbst mit der Weldon-Werkzeugaufnahme wurde eine echte Unwucht von 5,5 gmm gemessen, was einer Wuchtklasse von G8 entspricht. Diese erlaubt rein rechnerisch nur eine maximale Drehzahl von 7.600 U/min. Bei Spannzangenfuttern wurde für dieses Schneidwerkzeug mit Spannfläche sogar eine Wuchtgüte von G29 ermittelt, bei Schrumpffuttern sogar G38. Dies entspricht maximalen Drehzahlen von 2.700 U/min bzw. 1.600 U/min.
Auch feingewuchtete Schrumpf- und Spannzangenfutter geraten durch die Paarung mit unsymmetrischen Werkzeugen oder Werkzeugen mit Weldon-Spannfläche erheblich in Unwucht. Um bei der Bearbeitung effizient und genau zu arbeiten, müssen diese Werkzeuge nach jedem Werkzeugwechsel neu ausgewuchtet werden.
Messungen am Stirnfräser ergaben ähnliche Ergebnisse. Bei im Einsatz befindlichen Einsteckwerkzeugen wurde eine Unwucht von 20,3 gmm festgestellt, was einer Wuchtklasse von G23 entspricht. Dies liegt daran, dass Planfräser-Wendeschneidplatten Teile haben, die aufgespannt sind und sich nicht unbedingt immer an der gleichen Stelle befinden. Der Fräskopf hat bauartbedingt eine große Toleranz (Stifte mit Bohrungen und Spielpassung), sodass die Position des Werkzeugs nicht 100-prozentig definiert ist.
Diese Tests zeigen, dass ein gegenseitiges Auswuchten oder Schneiden von Werkzeug und Halter unerlässlich ist. Auch bei hochwertigen Werkzeugen ist eine Feinwuchtung für den Gesamtwerkzeugaufbau wichtig.
Ausgleich leicht gemacht
Beim Auswuchten gibt es noch Vorbehalte, doch mit der richtigen Auswuchtmaschine und einer praxisgerechten Software sollte es schnell und einfach zu bewerkstelligen sein. Kurz gesagt, der Bediener setzt den Halter in die Maschine ein und wählt die entsprechenden Anforderungen aus dem Menü aus, und die Maschine führt den Benutzer dann durch die verbleibenden Schritte.
Jeder Arbeiter, der mit Werkzeughaltern vertraut ist, sollte in der Lage sein, eine richtig konstruierte Auswuchtmaschine ohne umfangreiche Schulung zu bedienen. Das Fachwissen sollte in der Maschine liegen, in der die notwendigen Daten zu jedem Werkzeug bereits eingepflegt und gespeichert sind, was Zeit spart und Fehler vermeidet. Über die Benutzerverwaltung können zusätzliche Sicherheitsvorkehrungen getroffen werden. Beispielsweise können Sie die Rechte zum Erstellen oder Ändern von Werkzeugdaten auf bestimmte Personen beschränken. Andere Benutzer dürfen nur auf gespeicherte Werkzeuge zugreifen und können dann mit dem Auswuchten gemäß den festgelegten Anforderungen fortfahren.
Der Auswuchtvorgang ist ein weitgehend automatisierter Prozess, bei dem der Werkzeughalter in die Auswuchtspindel eingespannt und in Rotation versetzt wird, dann wird gemessen. Kraftsensoren an der Ausgleichsspindel messen die durch Unwuchten verursachten Fliehkräfte. Anschließend wertet die Software die Messwerte aus und zeigt dem Bediener an, wie viel Material ab- oder zugefügt werden muss oder wo er Gewicht verlagern muss, um die Unwucht auszugleichen.
Darüber hinaus bieten Auswuchtmaschinen verschiedene weitere Möglichkeiten, mit denen der Anwender die Unwucht beseitigen kann. Als Alternative zum Abbohren von Material können zum Beispiel Auswuchtschrauben oder -ringe Gewicht hinzufügen. Bei dieser Taktik werden zum Unwuchtausgleich zwei zusammengehörige Ringe mit definierter Unwucht auf einen zylindrischen Teil des Werkzeughalters gespannt. Die Software liefert dann den genauen Winkel, in dem die Ringe gedreht werden sollen. Ein vorhandener Linienlaser zeigt die Drehposition direkt an der Maschine an.
Das Messen dauert höchstens eine Minute, und wenn Sie mit Auswuchtringen oder Schrauben arbeiten, ist der gesamte Vorgang in zwei Minuten abgeschlossen. Wenn Sie zum Ausgleichen der Masse auf einen Bohrer an der Werkzeugaufnahme zurückgreifen müssen, kann es etwas länger dauern.
Eine klarere Wahrnehmung
Fortschritte in der Auswuchttechnologie haben das Auswuchten einer Werkzeughalterbaugruppe schnell, einfach und genau gemacht, sodass Sie wirklich das Maximum aus Ihren Werkzeugmaschinen herausholen können. Sie müssen sich nur an die grundlegende Physik des Gleichgewichts erinnern und diese dann auf den Gleichgewichtsprozess anwenden. Dann sollten alle Missverständnisse verschwinden.
Zuvor auf Haimer-USA.com vorgestellt.
Kaufen Sie Auswuchtmaschinen für Werkzeughalter von Haimer-USA auf MSCDirect.com.
Industrietechnik
- Was ist ein Stanzwerkzeug?
- Auf Erfolgskurs
- Werkzeugstahlsorten
- Wann Sie Ihre Wasserhähne aktualisieren sollten
- Drehen neu erfunden mit PrimeTurning
- Werkzeughalter für CNC-Drehmaschinen:Alles, was Sie wissen müssen
- Ein Überblick über CNC-Werkzeughaltertypen
- CNC-Werkzeughalterwagen bietet große Mobilität
- CNC-Werkzeughalterregal speichert verschiedene Werkzeughalter
- Klick-Wechsel-Werkzeughalter für schnellen Einsatzwechsel