Additive Fertigung mit industriellem 3D-Druck:Post-Processing-Erfolgsstrategien
Additiv gefertigte (AM) Teile sind selten vollständig, wenn sie vom Druckbett kommen oder die Baukammer verlassen. Hier sind fünf Strategien, um sie funktional, ästhetisch und genauer zu machen.
Trotz aller Bemühungen der Hersteller von industriellen 3D-Druckern erfordern die Kunststoff- oder Metallteile, die aus ihren Maschinen kommen, normalerweise zusätzliche Arbeit, bevor sie als fertig betrachtet werden.
Dieser Schritt in der Produktion fertiger Teile wird als Nachbearbeitung bezeichnet und ist ein notwendiges Übel in der Welt der additiven Fertigung.
Es umfasst spanende Bearbeitung, Wärmebehandlung, Schleifen und andere abrasive Prozesse. Dazu gehören auch Veredelungsarbeiten wie Lackieren und Galvanisieren sowie esoterische Technologien, die wir ausführlicher besprechen werden.
Von Schichten, Stützen und Genauigkeit
Es gibt viele Gründe, 3D-gedruckte Teile nachzubearbeiten.
Zunächst einmal bestehen die meisten dieser Teile aus hauchdünnen Schichten aus Metall, Kunststoff oder Verbundwerkstoffen. Und ähnlich wie die Kanten eines Taschenbuchs weisen die Oberflächen eines bedruckten Teils ein deutlich treppenförmiges Aussehen auf, das je nach Anwendung und kosmetischen Anforderungen vor dem Gebrauch glatt gemacht werden muss.
Das Entfernen von rauen Oberflächen trägt auch dazu bei, Spannungserhöhungen zu beseitigen, die zu Rissen führen können, ein wichtiger Aspekt für tragende Teile.
Die meisten 3D-gedruckten Teile erfordern während des Bauprozesses temporäre Stützen. Diese gerüstähnlichen Strukturen verhindern, dass sich die Schichten und Abschnitte nach oben kräuseln oder nach unten durchhängen (je nach AM-Prozess), und sie halten wärmeinduzierte Verwerfungen auf einem Minimum. Sobald das Teil fertig ist, müssen diese Stützstrukturen entfernt werden, normalerweise durch mechanische oder abrasive Mittel – wie Sie sehen werden, reicht manchmal ein warmes Bad aus.
Last, but not least, ist die Teilegenauigkeit. Ungeachtet seiner immensen Gestaltungsfreiheit und der Möglichkeiten, die er für starke und dennoch leichte Teile bietet, ist der 3D-Druck noch nicht sehr genau, zumindest nach herkömmlichen Fertigungsstandards. Es gibt die bereits beschriebene Oberflächenrauheit, mit der man sich auseinandersetzen muss, sowie Ebenheit, Rundheit und alles andere. Dadurch müssen Löcher aufgerieben oder gebohrt, Zapfen rundgedreht, Montageflächen plan gefräst werden. Aus diesem Grund machen viele 3D-gedruckte Teile – und sicherlich solche aus Metall – nach dem Druck einen Ausflug in die Maschinenhalle.
Strategien für eine erfolgreiche Nachbearbeitung des 3D-Drucks
Glücklicherweise unternehmen eine Reihe von Geräteherstellern – sowie die 3D-Druckerhersteller selbst – Schritte, um diese AM-Mängel zu beheben.
Diese Arbeit wird noch wichtiger, wenn die Produktionsmengen steigen und sich Additive zu einem Mainstream-Prozess entwickeln. Obwohl Sekundärprozesse niemals verschwinden werden (eine Tatsache, der sich auch subtraktive Hersteller bewusst sind), werden diese Unternehmen zumindest denen das Leben erleichtern, die Teile für ihren Lebensunterhalt drucken.
Bernie Kerschbaum ist CEO eines solchen Unternehmens:Rosler Metal Finishing USA mit Sitz in Battle Creek, Michigan. Kerschbaum empfiehlt Produktdesignern und Herstellern gleichermaßen, ihre Hausaufgaben bei der Nachbearbeitung 3D-gedruckter Teile zu machen, am besten lange vor Druckbeginn.
„Niemand bietet eine universelle Finishing-Technologie an, und oft ist es auch kein einzelner Prozess“, sagt Kerschbaum.
Er führt das Beispiel eines 3D-gedruckten Prototyps einer Shampooflasche an, bei der er vor einigen Jahren einen großen Konsumgüterkunden unterstützte, eine Flasche, die eine umfangreiche Gleitschleifbearbeitung erforderte, um das gleiche Aussehen und die gleiche Haptik wie ihr Gegenstück aus Kunststoffspritzguss zu erreichen. Andere Teile erfordern ein Nass- oder Trockenstrahlen, um raue Oberflächen zu nivellieren, während andere mehrere Endbearbeitungsvorgänge erfordern, um die gewünschte Glätte zu erreichen. Auch das Einfärben mit Farbstoffen oder Lacken ist weit verbreitet, ebenso wie das Polieren, Oberflächenschleifen und das Aufbringen von Schutzschichten.
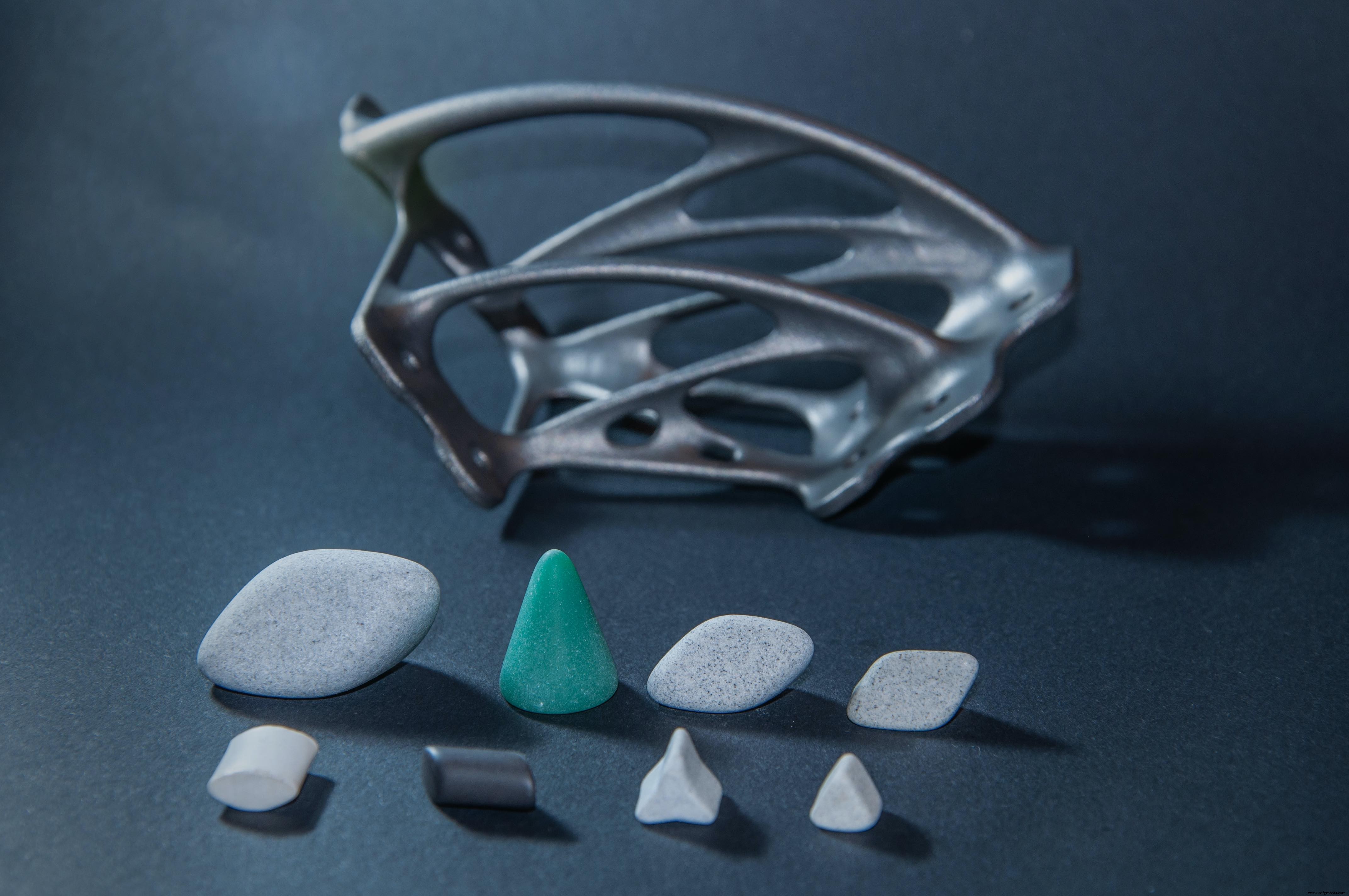
Kerschbaum listet die verschiedenen Schritte auf, die erforderlich sind, bevor diese und andere Nachbearbeitungsoperationen durchgeführt werden können.
Dazu gehört das Auspacken der Werkstücke aus dem „Kuchen“ bei Binderjet- und Pulverbettdruckern. Das Entfernen von Stützstrukturen und losem oder angesintertem Pulver von Bauteiloberflächen sowie das Glätten und Reinigen von Innengängen. Wenn es die Mengen erfordern, kann jeder dieser Arbeitsgänge automatisiert mit einem der verschiedenen Produktionssysteme der Marke AM Solutions des Unternehmens oder auf die altmodische Weise durchgeführt werden:mühsames Schleifen, Glätten und Polieren von Hand.
„Oft beginnt man mit einer ziemlich rauen Oberflächenbeschaffenheit, aber je nach Kundenwunsch können wir diese ohne allzu große Schwierigkeiten auf einen Ra-Wert im niedrigen Zehner- oder sogar einstelligen Bereich bringen“, sagt Kerschbaum. „Kugelstrahlen und Gleitschleifen haben sich als sehr effektive und wirtschaftliche Verfahren für additiv gefertigte Teile erwiesen.“
Für die Nachbearbeitung von Polymerteilen bietet Luis Folgar, Executive Vice President von Additive Manufacturing Technologies (AMT) Inc. aus Cedar Park, Texas, eine Alternative an:eines der automatisierten PostPro 3D- und PostPro SF50-Systeme seines Unternehmens.
Beide verwenden einen proprietären chemischen Dampf, der „sicher in der Anwendung, relativ kostengünstig und vor allem nachhaltig“ ist, um die Oberfläche von Teilen zu glätten, die mit Pulverbett-, Multi-Jet-Fusion- und Extrusionstechnologien gedruckt wurden.
Zu den Kandidatenpolymeren gehören Nylon, ABS (Acrylnitril-Butadien-Styrol), PC (Polycarbonat), Polypropylen, TPU (thermoplastisches Polyurethan) und TPE (thermoplastisches Elastomer), Ultem und glas- oder kohlenstoffgefüllte Materialien „mit PEEK (Polyetheretherketon) und PAEK (Polyaryletherketon) kommt bald online“, sagt Folgar.
Oberflächenbeschaffenheiten von Teilen bis zu 1 μm Ra (40 μin Ra) sind möglich, fügt er hinzu, mit einer dimensionalen Verschlechterung von nicht mehr als 0,4 Prozent, reduzierter Oberflächenporosität und Rissbildung und verbesserten Farbeigenschaften im fertigen Teil. Wie bei Rosler und anderen Anbietern bietet AMT auch automatisierte Entpulverungs- und Kugelstrahlsysteme an.
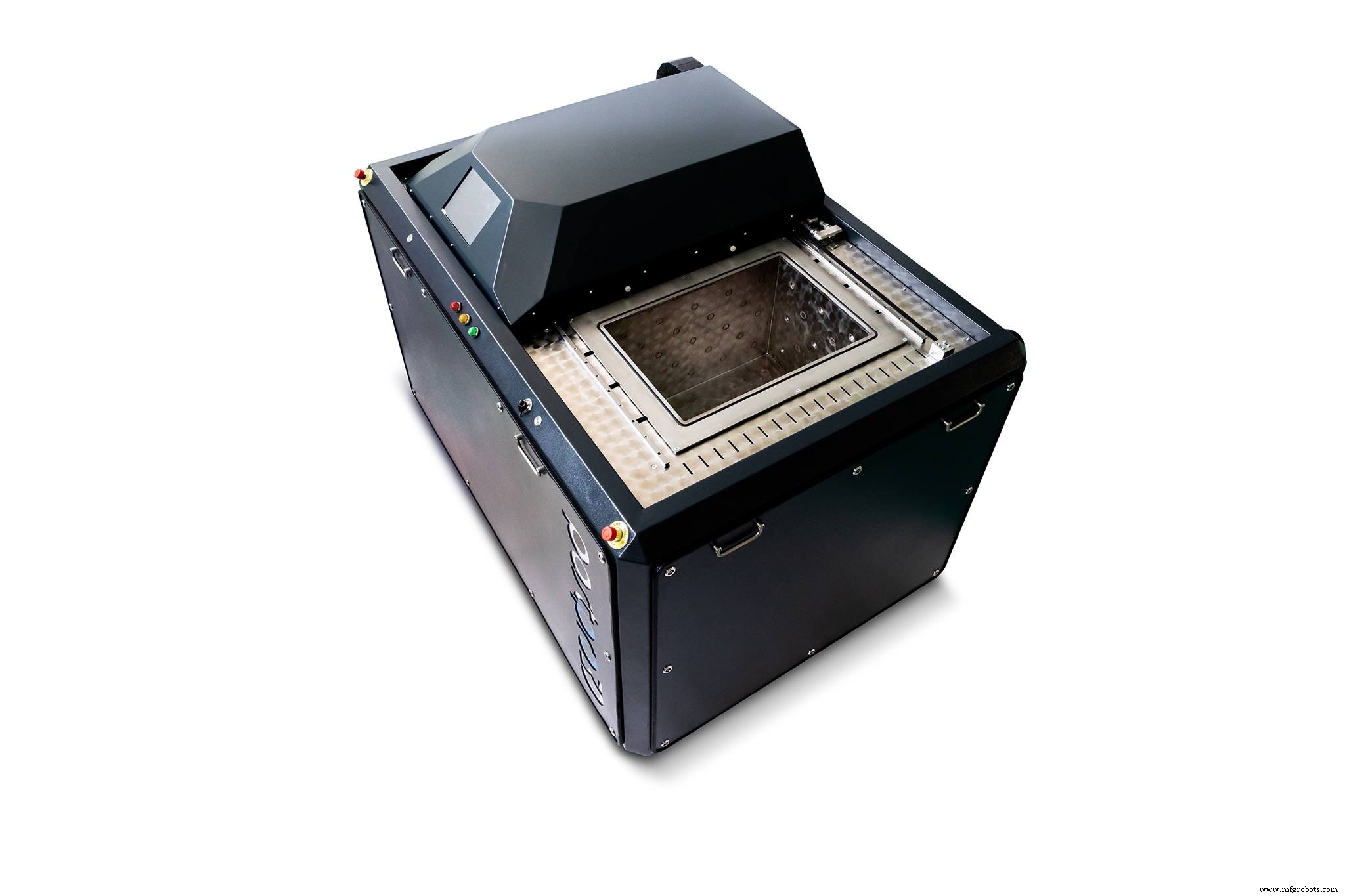
Felipe Castañeda ist Industriedesigner und Creative Director bei MakerBot in Brooklyn, New York, einer Tochtergesellschaft von Stratasys. Er stellt fest, dass bei Teilen, die mit FFF (Fused Filament Fabrication) hergestellt wurden, eine der effektivsten Methoden zum Entfernen von Stützstrukturen nach dem Drucken die Verwendung von auflösbaren Materialien ist.
Das erste davon ist PVA (Polyvinylalkohol), ein weiches, biologisch abbaubares Polymer, das schmilzt, wenn es warmem Leitungswasser ausgesetzt wird. Lassen Sie die fertigen Teile einfach hinein, schwenken Sie sie einige Minuten lang herum und heraus kommt ein Teil ohne Stützen. Dies funktioniert gut für weichere Materialien wie PLA (Polymilchsäure) und PETG (Polyethylenterephthalatglykol), aber für „komplexere Polymere“ wie ABS unterstützt MakerBot die Verwendung von SR-30 von Stratasys.
Wie PVA löst es sich in Wasser auf, erfordert jedoch eine kleine Menge NaOH (Ätznatron oder Lauge) und etwas höhere Temperaturen. Diese werden jeweils während des Druckprozesses aufgebracht, wobei der Auftragskopf je nach Bedarf automatisch zwischen Werkstück und Trägermaterial umschaltet.
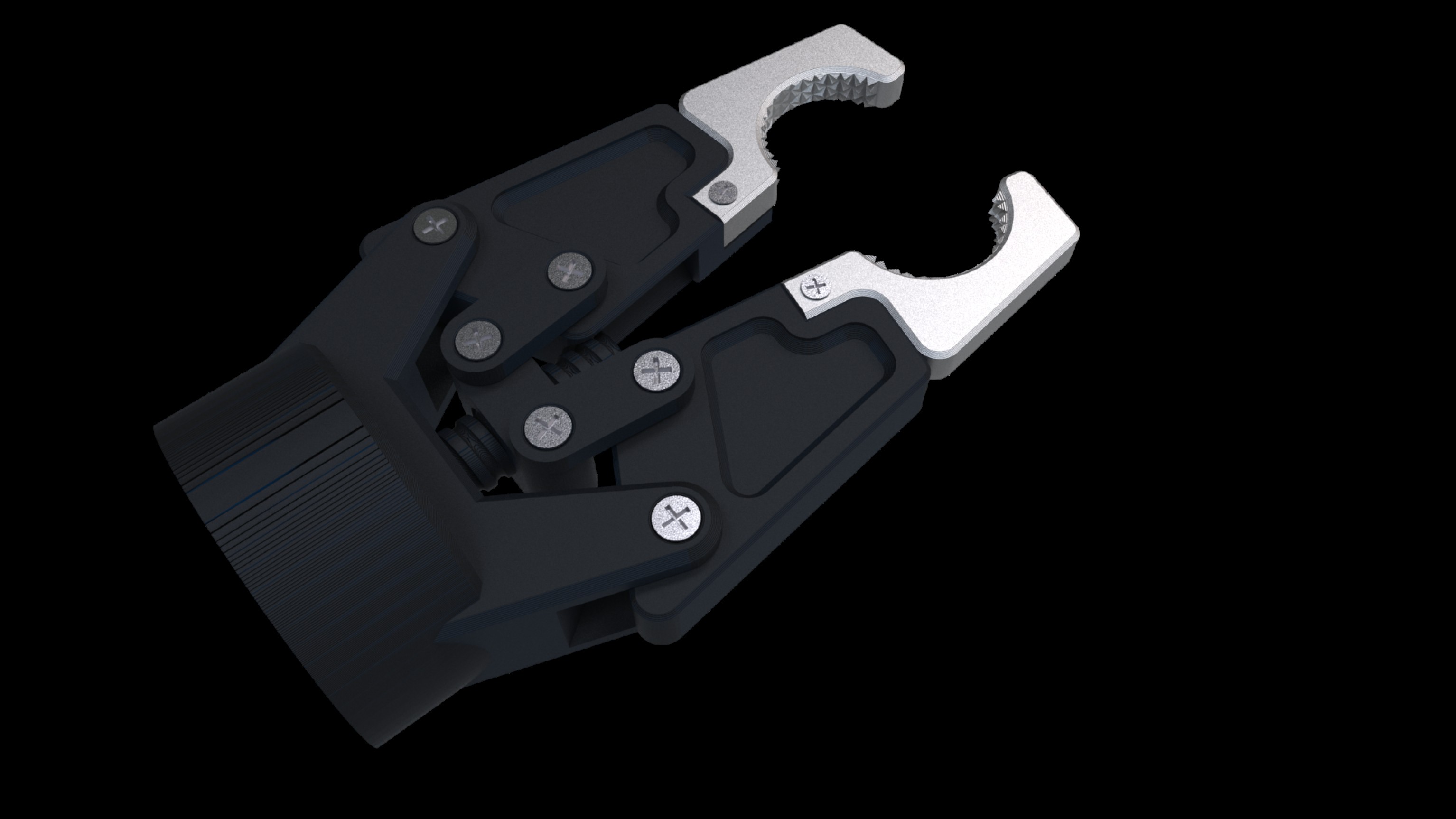
Das Schöne an diesen und anderen löslichen Materialien ist die Fähigkeit, Stützstrukturen für komplexe Teile und insbesondere Innengeometrien zu schaffen, die sonst mit mechanischen Mitteln nur schwer zu entfernen wären.
Eine weitere Möglichkeit ist das Bedrucken sogenannter Breakaway Supports. Hier wird der Löwenanteil der Stütze aus dem gleichen Material wie das Werkstück gedruckt, wobei PVA oder SR-30 nur dort aufgetragen wird, wo sich das Teil und seine Stützen verbinden. Der Entfernungsprozess ist derselbe, aber da der Druckkopf nicht so oft zwischen den Materialien wechseln muss, beschleunigt er den Bauprozess.
„Es verkürzt auch die für die Auflösung benötigte Zeit, sodass es für viele Teile einen Ansatz bietet, der das Beste aus beiden Welten bietet“, sagt Castañeda.
Dazu kommen, wie eingangs erwähnt, spanende Bearbeitung, Schleifen und bei Metallteilen auch Wärmebehandlungen, um innere Bauteilspannungen abzubauen und das Werkstück auf Wunsch zu härten.
Da die in den meisten 3D-Druckverfahren verwendeten Metalle weitgehend identisch mit ihren geschmiedeten oder gegossenen Gegenstücken sind, ist hier keine Zauberei im Spiel – sägen oder erodieren Sie einfach das Teil von der Bauplatte, klemmen Sie es fest und schneiden Sie es.
Welche Techniken verwenden Sie für die Nachbearbeitung von Teilen, die mit additiver Fertigung hergestellt wurden? Teilen Sie Ihre Gedanken und Erkenntnisse in den Kommentaren unten mit.
Industrietechnik
- 8 Wege, wie der industrielle 3D-Druck die Fertigung revolutioniert
- Nachbearbeitung für den industriellen 3D-Druck:Der Weg zur Automatisierung
- Experteninterview:Jonathan Warbrick von Graphite Additive Manufacturing über den Erfolg mit 3D-Druck
- Drucken der Sicherung 1 mit der Sicherung 1
- Additive Manufacturing Podcast Folge 3
- Die traditionelle Metallbearbeitung glänzt immer noch in der Fertigung
- Additive Fertigung beginnt, über den Desktop-3D-Druck hinaus zu reifen
- Der Fall für den 3D-Druck in der Fertigung
- Die Auswirkungen der additiven Fertigung auf die industrielle Produktion
- Stratasys:Nachhaltiger sein mit 3D-Druck