Experteninterview:Jonathan Warbrick von Graphite Additive Manufacturing über den Erfolg mit 3D-Druck
Die Landschaft für AM-Servicebüros verändert sich schnell, da der Trend zur Produktion weitergeht. Servicebüros müssen mehr denn je agil sein und sich an eine Branche anpassen können, die sich ständig verändert.
Graphite Additive Manufacturing ist ein in Großbritannien ansässiger AM-Dienstleister, der industrielle 3D-Drucklösungen anbietet. Mit starken Verbindungen zur Welt der britischen Formel 1 und des Motorsports umfassen die Lösungen von Graphite Produktionsteile, Werkzeuge, Konzeptmodelle und Prototypen.
Wir sprechen mit dem Business Development Manager von Graphite, Jonathan Warbrick, um zu besprechen, wie es gelingt, die Nase vorn zu haben, welche Möglichkeiten es in AM gibt und was es braucht, um heute als Servicebüro erfolgreich zu sein.
Was ist die Mission von Graphite?
Unser Ziel bei Graphite ist es, unseren Kunden dabei zu helfen, die besten Lösungen mit additiver Fertigung zu finden, vom Prototypen bis hin zur Produktion. Dazu gehört auch, ihnen zu helfen zu verstehen, welche Technologien und Materialien für ihre Anwendungen am besten geeignet sind. Wir unterscheiden uns von vielen anderen Servicebüros dadurch, dass wir auch unsere eigenen Materialien herstellen.
Unser Geschäftsführer Kevin Lambourne, Während seiner Arbeit bei Red Bull Racing stellte er fest, dass er nicht das technische Wissen von den britischen Servicebüros bekommen konnte, um die High-End-Top-Level-Projekte, die er leitete, wirklich zu unterstützen.
Als Ergebnis dieser Erfahrung gründete Kevin Graphite im Jahr 2012, um diese Lücke zu füllen und das Servicebüro der Wahl für Konstrukteure und Ingenieure für die additive Fertigung zu sein und unseren Kunden erstklassige technische Unterstützung zu bieten Prototypen bis zur Produktion.
Großbritannien ist weltweit führend in Bezug auf Innovationen im Motorsport, und die additive Fertigung hat dabei eine Schlüsselrolle gespielt. In der Anfangszeit lag unser Branchenfokus also auf Formel 1 und Motorsport.
Seitdem haben wir Schritte unternommen, um zu diversifizieren und unser Wissen in den breiteren Markt einzubringen.
Große Erfolge für uns in den letzten Jahren waren Anwendungen für Branchen wie Automobil, Schifffahrt, Luft- und Raumfahrt und Verteidigung. Wir arbeiten immer noch viel im Formel-1-Feld und im Motorsport – das ist unser Erbe –, aber wir beliefern auch eine Reihe von Sektoren, die kleine bis mittlere Serien produzieren.
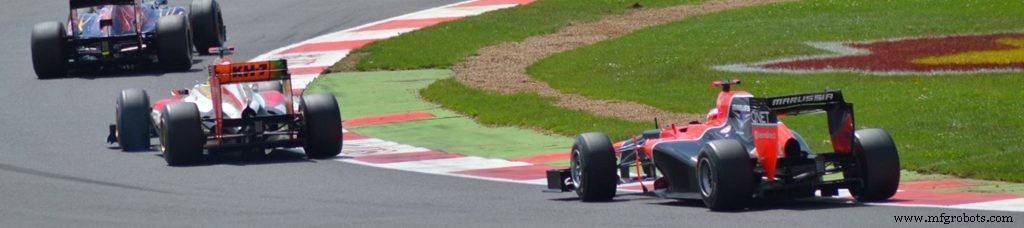
Wie ist es heute, ein Servicebüro zu führen?
Für uns ist das Geschäft wirklich positiv verlaufen und wir haben das letzte Jahr mit einem Hoch abgeschlossen. Wir hatten in den letzten drei Jahren ein nachhaltiges Wachstum von etwa 20 % und werden dieses Jahr wieder um 20-25 % wachsen.
Die Herausforderung zu dieser Jahreszeit besteht wie immer darin, einen Neustart durchzuführen, um zu verstehen, welche Märkte wir angreifen möchten, und gleichzeitig die Beziehungen zu stärken, die wir bereits mit unseren bestehenden Kunden haben.
Eine der treibenden Kräfte hinter unserem jüngsten Wachstum ist, dass wir vom Prototyping in die Produktion übergehen – und dies möge noch lange so weitergehen.
Im Motorsport sind die Volumina eher gering und die Vorlaufzeiten sehr kurz.
In Bezug auf den Aufbau eines nachhaltigen Geschäftsplans und das zukünftige Wachstum wissen wir, dass wir großartige Lösungen für unsere Formel-1- und Motorsportkunden haben.
Der Schlüssel für uns liegt darin, eine wirklich gute Balance zwischen schnellen Turnarounds für die dringend benötigten Projekte und den stetigen Klein- bis Mittelserien zu finden. Als solche haben wir einen Express-Service und einen Economy-Service eingeführt. | von der Einstellung neuer Mitarbeiter bis zum Umzug in eine größere Einrichtung im September letzten Jahres aktiv Schritte unternommen, um dies zu beheben. Wir haben also etwas Raum, in den wir hineinwachsen können, was großartig ist.
Eine weitere Herausforderung, mit der wir in den letzten Jahren konfrontiert waren, ist die fehlende Automatisierung bei der Verwaltung einiger unserer Aufträge mit geringerem Wert. Diese nahmen viel Zeit in Bezug auf die Planung von Jobs in Anspruch. Die Software zur Workflow-Automatisierung war ein großer Vorteil für unser Unternehmen, da sie es uns ermöglicht, unseren Workflow weitaus schlanker und automatisierter zu gestalten.
Für viele Servicebüros besteht die Versuchung, zu versuchen, allen Menschen alles zu bieten. Bei so vielen verschiedenen Materialien und Technologien ist es wichtiger, sich auf bestimmte Bereiche zu spezialisieren und zu liefern.
Wir müssen sehr vorsichtig sein, um sicherzustellen, dass unser Wachstum nachhaltig ist. Das bedeutet, dass wir diese Investitionen sowohl an den aktuellen Bedürfnissen unserer Kunden als auch an den Bedürfnissen vornehmen, die sie in 6 bis 12 Monaten haben werden.
Wie wägen Sie ab, ob Sie in eine bestimmte Technologie investieren sollten oder nicht?
Es geht vor allem darum, Ihren Kunden diese neuen Technologien und Materialien vorzustellen, die Grenzen und Möglichkeiten einer bestimmten Technologie zu verstehen und darauf zu vertrauen, dass eine Nachfrage dafür besteht.
Für uns bedeutet das, wirklich datengetrieben zu sein. Wir versuchen, jede neue Technologie zu verstehen und wir drucken Testteile, um ein Gefühl dafür zu bekommen, was sie können und was nicht, bevor wir diesen Sprung wagen.
Es kommt also darauf an, nah an Ihren Kunden zu sein, Einführung neuer Technologien, sobald sie auf den Markt kommen, und sicherzustellen, dass, bevor Sie eine große Investition in eine Maschine tätigen, ob SLS, SLA, MJF oder FDM, tatsächlich Bedarf besteht.
Wir haben unseren Kunden beispielsweise die Multi Jet Fusion-Technologie von HP in den letzten zwei Jahren vorgestellt, um sicherzustellen, dass sie die Einschränkungen und Fähigkeiten dieser Technologie vollständig verstehen.
Wie würden Sie den aktuellen Stand der additiven Fertigungsindustrie beschreiben?
Die Branche hat noch einen langen Weg vor sich, bis sie kostengünstige Fertigungslösungen anbieten kann. Aber das ändert sich schnell.
Es gibt einen großen Spielraum für weitere Produktionslösungen, insbesondere im Bereich Metalle und Hochleistungskunststoffe.
Ein gutes Beispiel dafür sind die britischen Supersportwagenhersteller. Viele der Teile unter der Motorhaube und im Fahrerhaus dieser Fahrzeuge werden jetzt in 3D gedruckt. Einer unserer Kunden nutzt die additive Fertigung, um Gewicht zu sparen und die Leistung zu verbessern, aber die Qualität der Drucke steht an erster Stelle.
Einfache Teile wie Lüftungsschlitze und Windschutzscheibeneinfassungen wären früher nie gedruckt worden, da die Technologie eher für den Prototypenbau gedacht war. Jetzt sind sie eine häufige Anwendung für diese wirklich High-End-Märkte.
Das liegt vor allem daran, dass die Mengen stimmen – wir sprechen von ein paar hundert Teilen eines bestimmten Modells. Wenn mehrere tausend Teile benötigt werden, gibt es kostengünstigere Herstellungsmethoden mit traditionellen Technologien wie dem Spritzgießen. Aber für kleine Stückzahlen wird der 3D-Druck kostengünstiger.
Erst seit kurzem bietet die additive Fertigung erstklassige Materialien, die die mechanischen Eigenschaften von Spritzguss-Alternativen nachahmen und kostengünstig sind -effektive Lösung für diese kleinen bis mittleren Produktionsserien.
Es gibt auch einen großen Spielraum, die Kosten zu senken, und das wird sicherlich mit der Zeit passieren. SLS und MJF haben sich beispielsweise als zwei Technologien erwiesen, die sicherstellen, dass Sie die richtigen Preispunkte erreichen, um mit dem traditionellen Spritzguss und anderen Fertigungsformen konkurrieren zu können.
Schließlich muss die Industrie auch die Nachbearbeitung und Veredelung von Teilen verbessern und diese automatisierter und kostengünstiger gestalten.
Viele der erforderlichen Nachbearbeitungen sind sehr manuelle Vorgänge. Wir verbringen immer noch viel Zeit in der Werkstatt, um Teile manuell zu reinigen, zu schleifen und zu strahlen. Um Zeit und Geld zu sparen, müssen wir diese Nachbearbeitung so weit wie möglich automatisieren.

Unternehmen beginnen, 3D-Drucke intern zu machen. Wie wird sich das Ihrer Meinung nach auf den Dienstleistungsmarkt auswirken?
Es wird sehr ähnlich sein wie bei Technologien wie Spritzguss und anderen Fertigungsformen, insbesondere in Branchen wie der Automobilindustrie. Im Wesentlichen stellen die Automobil-OEMs nichts her, sie montieren Teile auf großen Produktionslinien.
Mit neuen Technologien wie der additiven Fertigung werden die Unternehmen es im eigenen Haus übernehmen, um sicherzustellen, dass sie es bekommen die besten Vorteile und Kosteneinsparungen. Aber das bedeutet nicht unbedingt, dass sie alle diese Teile im eigenen Haus herstellen müssen.
Im Moment gibt es einen echten Drang, Maschinen zu kaufen und zu skalieren. Das wird sich mit der Zeit wieder verflüchtigen, genau wie bei fast jeder anderen Technologie, die im Automobil verwendet wird. Sie werden Teile auslagern und sicherstellen, dass sie pünktlich geliefert werden.
Letztendlich wird es ein Gleichgewicht geben. Nehmen Sie Volkswagen als Beispiel. Sie haben eine große Anzahl von FDM-Maschinen, die Teile in der Werkstatt drucken, um ihren Herstellungsprozess zu unterstützen. Aber sie lagern immer noch riesige Mengen gedruckter Teile an andere Servicebüros aus.
Jetzt besteht die Versuchung, die gesamte AM-Produktion ins eigene Haus zu bringen, aber das wird sich ändern, da Unternehmen erkennen, dass Sie eine große Anzahl von Maschinen benötigen, um die Produktionsanforderungen in Zukunft zu erfüllen, was sich auf Personal, Werkstattraum und Kosten auswirkt. Am Ende brauchst du immer die Unterstützung eines guten Servicebüros.
Wie hat Graphite seine eigenen Materialien entwickelt?
Es stammt wirklich aus unserer Anfangszeit, als wir hauptsächlich den britischen Formel-1-Teams dienten.
Der Wunsch, 3D-Druck zu verwenden, war die Möglichkeit, die stärksten, steifsten und leichtesten Teile für ihr Auto herzustellen, die auf der Rennstrecke einen Bruchteil einer Sekunde einsparen könnten.
Wir haben uns angeschaut, was es auf dem Markt gibt und haben unser kohlenstoffgefülltes SLS-Nylon entwickelt.
Im Wesentlichen füllen wir Kohlefaser mit kurzen Strängen mit einer Basis aus Nylon PA12. Wenn die Stränge zu lang sind, können Sie sehen, dass die Faser durch das Teil herausragt – Sie erhalten ausgezeichnete mechanische Eigenschaften, aber das Teil sieht schrecklich aus. Wenn Sie diese Kohlefaserstränge jedoch zu kurz machen, gehen Sie Kompromisse bei den mechanischen Eigenschaften ein.
Wir haben die unserer Meinung nach absolut optimale Faserlänge entwickelt, die mit unseren Nylonmaterialien gefüllt werden kann, um zusätzliche Steifigkeit und Festigkeit zu erzielen. Unsere Materialien haben deutlich bessere mechanische Eigenschaften, als Sie es traditionell von einem normalen PA12 oder PA11 erwarten würden. Es gibt viel bessere Steifigkeit, Festigkeit und Bruchdehnung.
In der Anfangszeit haben wir nur mit dem mit Carbon gefüllten Nylon SLS gearbeitet. Das Feedback vom Markt war fantastisch und es wurde zum bevorzugten Material in der Formel-1- und Motorsportwelt.
Neben Steifigkeit und Festigkeit schätzen die Kunden das natürlich dunkelgraue, schwarze Aussehen von das Material. Es sieht aus wie ein einsatzbereiter Kunststoff in technischer Qualität. Sie müssen das Material nicht wie bei herkömmlichen SLS-Nylons einfärben.
Aber dann hatten wir einige Kunden, die nicht unbedingt die Steifigkeit, Festigkeit und erstklassigen mechanischen Eigenschaften benötigten. Was sie wollten, war ein wirklich leichtes Nylon, also begannen wir, mit Graphit gefülltes Nylon SLS zu entwickeln. Es hat immer noch eine Dichte von Kohlefasern im Material und wir füllen es mit Graphitstaub, um einige mechanische Eigenschaften zu verleihen und das Teil direkt aus der Maschine natürlich dunkelgrau / schwarz aussehen zu lassen.
Wir verkaufen jetzt drei- oder viermal mehr Graphit-SLS als wir Carbon-SLS. Carbon SLS ist immer noch das bevorzugte Material in den Formel-1-Teams und der Rennwelt. Aber Branchen wie Marine und Automotive suchen nach kostengünstigeren Produktionslösungen. Graphit-SLS ist wahrscheinlich etwa 30 % kostengünstiger als Kohlenstoff.
Wir haben auch an einer Reihe von leichten Polymeren gearbeitet, bei denen wir versuchen, neue und innovative Materialien zu entwickeln, um der Konkurrenz einen Schritt voraus zu sein.
Wir arbeiten derzeit an einem neuen ultraleichten SLS-Material, das noch leichter ist als unser Carbon. Angesichts dieser Bemühungen, die Leistung von Hybrid- und Elektrofahrzeugen zu verbessern, ist die Gewichtseinsparung für viele Designer und Ingenieure, mit denen wir zusammenarbeiten, zu einem wichtigen Aspekt geworden. Wir wollen auch weiterhin additive Fertigungslösungen anbieten, um diese Herausforderungen zu meistern.
Was ist mit Verbundwerkstoffen?
Auf dem Markt für Verbundwerkzeuge gibt es derzeit viel zu tun. Und das geht wieder auf das zurück, was ich über das Bestreben gesagt habe, Teile leichter und effizienter zu machen.
So viele Teile, die aus Metall hergestellt wurden, gelten heute als aus Kohlefaser hergestellt. Daher setzen wir bewusst eine Reihe von Materialien und Technologien ein, um diese Verbundwerkstoffindustrie zu unterstützen.
Dazu gehören 3D-Druck-Löslichkeits- und Extraktionsdorne, keramische SLA-Formen, Hochtemperatur-FDM-Materialien sowie Vorrichtungen und Vorrichtungen. Wir sehen den Composites-Markt als ideale Ergänzung für die Additive Fertigung und haben eine Reihe von technischen Kooperationen aufgebaut.
Wie würden Sie die heutige Landschaft für AM-Servicebüros beschreiben?
Im Moment gibt es eine Vielzahl unterschiedlicher Servicebüros. Aber weil die Eintrittsbarrieren für den 3D-Druck so niedrig sind, kann man ein paar tausend Pfund für ein paar Desktop-FDM-Maschinen ausgeben und plötzlich hat man ein Servicebüro.
Aber ich denke, das ist insgesamt eine gute Sache für die Branche. Wettbewerb ist der Schlüssel, um die Branche voranzutreiben, da er Entwicklung und Innovation vorantreibt.
Es gibt einige sehr gut etablierte, ausgezeichnete Büros. Aber es gibt, wenn überhaupt, nur sehr wenige Büros, die das tun, was Graphite AM tut. In Bezug auf unser technisches Wissen und die Herstellung unserer eigenen SLS-Pulver sind wir in Großbritannien einzigartig.
Ich denke, dass es in den nächsten Jahren viele Fusionen und Übernahmen geben wird. Hauptsächlich angetrieben durch den Luft- und Raumfahrtsektor. Die Sperrung eines AM-Prozesses von der Materialbeschaffung bis zur Produktion ist der Schlüssel für flugzugelassene Teile. Dies dürfte in den nächsten Jahren zu viel Bewegung innerhalb der Branche führen.
Die Zukunft sieht für diejenigen Büros sehr rosig aus, die eine Nische erschließen und weiterhin liefern können.
Können Sie Erfolgsgeschichten mitteilen, an denen Sie glücklicherweise gearbeitet haben?
Eine aktuelle Fallstudie stammt von Nifco, einem großen Automobilzulieferer. Mit dem Streben nach Elektrifizierung und der Abkehr von traditionellen Benzin- und Diesel-Verbrennungsmotoren ist die Notwendigkeit, Gewicht zu sparen und die Effizienz der elektrischen Boost-Systeme zu verbessern, derzeit sehr vorherrschend.
So waren wir Zusammenarbeit mit Nifco an einer leichten Motorhalterung – einem Teil, das traditionell aus Aluminium gefertigt wird. Wir haben mit dem F&E-Team zusammengearbeitet, um ein kostengünstigeres, leichteres Teil herzustellen, das in Graphite SLS gedruckt werden kann. Es ist das erste 3D-gedruckte Motorlager seiner Art und das Feedback war sehr gut.
Ein weiterer ist mit FT Technologies, einem Unternehmen, das UAV- und Umweltsensoren für den Betrieb in einigen der unwirtlichsten Umgebungen der Welt herstellt. Sie wollten ein Material, das extrem leicht und langlebig sein sollte, da der Umweltsensor auf den UAV-Markt ausgerichtet war.
Der Prozess begann vor etwa einem Jahr. Wir begannen mit einigen Konzeptentwürfen und produzierten eine Reihe von Prototypen. Das Schöne am 3D-Druck ist, dass Sie ein Design optimieren, die Teile entwickeln und ein Produkt so viel schneller auf den Markt bringen können als mit herkömmlichen Methoden.
Nach einigen Design-Meetings und einigen Änderungen an der Originaldatei wurde die Komponente im September letzten Jahres auf den Markt gebracht. Dieses Teil ist jetzt in Produktion gegangen und die ersten 100 Einheiten wurden verschickt, um den Markt zu beurteilen. Das Feedback war fantastisch und ein großartiges Beispiel für den Einsatz von 3D-Druck für das Prototyping bis hin zur Produktion.
Um mehr über Graphit zu erfahren, besuchen Sie: https://graphite-am.co.uk/
3d Drucken
- Experteninterview:Pat Warner, Spezialist für additive Fertigung des Renault Formel-1-Teams
- Interview mit einem Experten:Professor Neil Hopkinson, Direktor für 3D-Druck bei Xaar
- Interview mit einem Experten:Philip Cotton, Gründer von 3Dfilemarket.com
- Interview mit einem Experten:Spencer Wright von pencerw.com und nTopology
- Interview mit einem Experten:Dr. Alvaro Goyanes von FabRx
- Interview mit einem Experten:Ibraheem Khadar von Markforged
- Wie Ford Motor Company den 3D-Druck für die Automobilindustrie innoviert:Experteninterview mit Harold Sears
- Experteninterview:CEO von PostProcess Technologies zur Lösung des Post-Processing-Engpasses für die additive Fertigung
- Experteninterview:Sintavia-Präsident Doug Hedges über die Serienproduktion mit 3D-Metalldruck
- Experteninterview:Brian Alexander von Solvay zur Entwicklung von Hochleistungspolymeren für den 3D-Druck