20 Lektion 3:Vertikale Fräszentrum-Maschinenbewegung
ZIEL
Nach Abschluss dieser Einheit sollten Sie in der Lage sein:
- Die Maschinenbewegung des vertikalen Fräszentrums verstehen.
- Verstehen Sie die Ausgangsposition der Maschine.
- Verstehen Sie die CNC-Maschinenkoordinaten.
- Das Arbeitskoordinatensystem verstehen.
- Verstehen Sie die Maschinen- und Werkzeugversätze.
- Stellen Sie den Werkzeuglängenversatz für jedes Werkzeug ein.
VMC-Maschinenbewegung
CNC-Maschinen verwenden ein kartesisches 3D-Koordinatensystem. Abbildung 10. zeigt ein typisches vertikales Fräszentrum (VMC). Zu bearbeitende Teile werden auf dem Maschinentisch befestigt. Dieser Tisch bewegt sich in der XY-Ebene. Wenn der Bediener der Maschine zugewandt ist, bewegt die X-Achse den Tisch von links nach rechts. Die Y-Achse bewegt den Tisch vorwärts-rückwärts. Der Maschinenständer greift und dreht das Werkzeug. Die Säule steuert die Z-Achse und bewegt sich von oben nach unten.
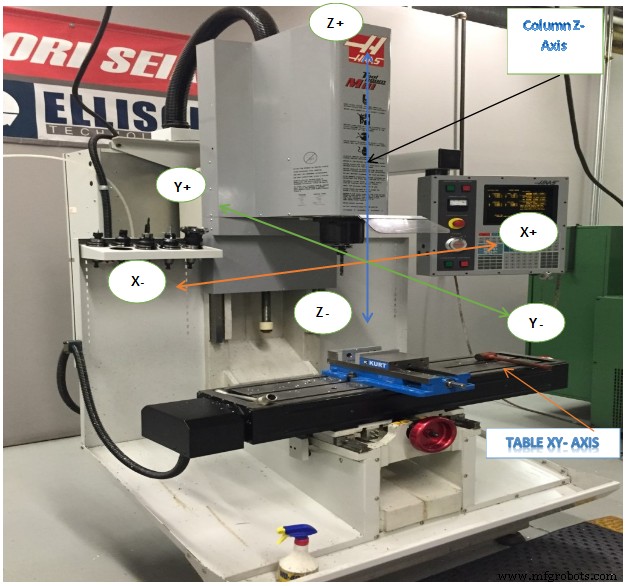
Abbildung 1. VMC-Maschinenbewegung
CNC-Maschinenkoordinaten
Das CNC-Maschinenkoordinatensystem ist in Abbildung 11 dargestellt. Der Kontrollpunkt für das Maschinenkoordinatensystem ist als Mittelfläche der Maschinenspindel definiert. Der Ursprungspunkt für das Maschinenkoordinatensystem heißt Maschinen-Home. Dies ist die Position der Mittelfläche der Maschinenspindel, wenn die Z-Achse vollständig zurückgezogen ist und der Tisch an seine Grenzen in der Nähe der hinteren linken Ecke bewegt wird.
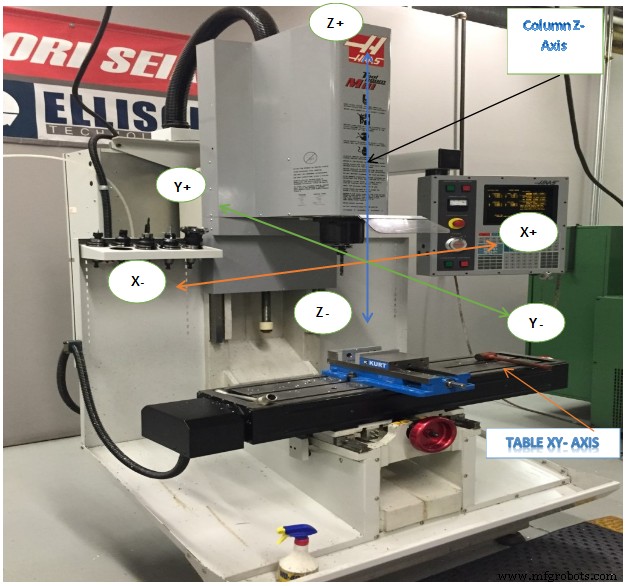
Abbildung 2. VMC-Maschinenkoordinatensystem (An der Ausgangsposition )
Wie in Abbildung 12 gezeigt, denken, arbeiten und schreiben Sie CNC-Programme bei der Arbeit mit einer CNC immer in Bezug auf die Werkzeugbewegung und nicht auf die Tischbewegung. Zum Beispiel bewegen steigende +X-Koordinatenwerte das Werkzeug relativ zum Tisch nach rechts (obwohl sich der Tisch tatsächlich nach links bewegt). Ebenso bewegen steigende +Y-Koordinatenwerte das Werkzeug zur Rückseite der Maschine (der Tisch bewegt sich zum Bediener hin). Erhöhende +Z-Befehle bewegen das Werkzeug nach oben (vom Tisch weg).
Über die Ausgangsposition der Maschine
Wenn eine CNC-Maschine zum ersten Mal eingeschaltet wird, weiß sie nicht, wo sich die Achsen im Arbeitsraum befinden. Die Ausgangsposition wird durch die Power-On-Restart-Sequenz gefunden, die vom Bediener durch Drücken einer Taste auf der Maschinensteuerung nach dem Einschalten der Steuerspannung initiiert wird.
Die Power-On-Restart-Sequenz treibt einfach alle drei Achsen langsam in Richtung ihrer äußersten Grenzen (-X, +Y, +Z). Wenn jede Achse ihre mechanische Grenze erreicht, wird ein Mikroschalter aktiviert. Dies signalisiert der Steuerung, dass die Referenzposition für diese Achse erreicht ist. Wenn sich alle drei Achsen nicht mehr bewegen, wird die Maschine als „referenziert“ bezeichnet. Maschinenkoordinaten beziehen sich danach auf diese Ausgangsposition.
Arbeitskoordinatensystem
Offensichtlich wäre es schwierig, ein CNC-Programm in Bezug auf Maschinenkoordinaten zu schreiben. Die Ausgangsposition ist weit vom Tisch entfernt, daher wären die Werte im CNC-Programm groß und hätten keine leicht erkennbare Beziehung zum Teilemodell. Um das Programmieren und Einrichten der CNC zu vereinfachen, wird für jedes CNC-Programm ein Arbeitskoordinatensystem (WCS) eingerichtet.
Das WCS ist ein Punkt, der vom CNC-Programmierer auf dem Teil, Rohteil oder der Vorrichtung ausgewählt wird. Das WKS kann zwar mit dem Teileursprung im CAD übereinstimmen, muss es aber nicht. Es kann sich zwar überall im Maschinengehäuse befinden, seine Auswahl erfordert jedoch sorgfältige Überlegung.
- Die WCS-Position muss mit mechanischen Mitteln wie einem Kantensucher, einem Koaxialindikator oder einer Teilesonde gefunden werden können.
- Es muss mit hoher Genauigkeit lokalisiert werden:normalerweise plus oder minus 0,001 Zoll oder weniger.
- Es muss wiederholbar sein:Teile müssen jedes Mal an genau der gleichen Position platziert werden.
- Es sollte berücksichtigt werden, wie das Teil gedreht und bewegt wird, wenn verschiedene Seiten des Teils bearbeitet werden.
Abbildung 13 zeigt beispielsweise ein in einen Schraubstock eingespanntes Teil. Die Außenmaße des Teils wurden bereits auf einer manuellen Maschine auf Maß gefräst, bevor sie auf der CNC-Maschine eingestellt wurden.
Die CNC wird verwendet, um die Löcher, Taschen und Schlitze in diesem Teil herzustellen. Das WCS befindet sich in der oberen linken Ecke des Blocks. Diese Ecke lässt sich leicht mit einem Kantensucher oder einer Sonde finden.
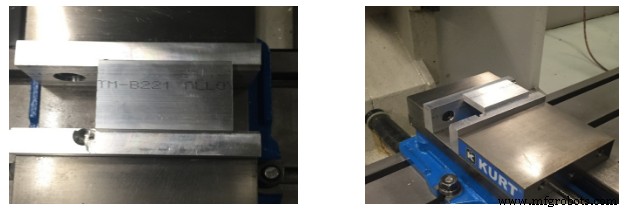
Draufsicht anzeigen
Abbildung 3. Arbeitskoordinatensystem (WKS)
Maschinen- und Werkzeugversätze
Maschinenversätze:
Da es schwierig ist, einen Schraubstock jedes Mal in genau der gleichen Position auf der Maschine zu platzieren, ist die Entfernung von Home zum WCS normalerweise nicht bekannt, bis der Schraubstock eingestellt und mit der Maschine ausgerichtet ist. Die Einrichtung der Maschine erfolgt am besten, nachdem das Programm vollständig geschrieben ist, da es teuer ist, eine CNC-Maschine im Leerlauf zu halten, während sie auf die Fertigstellung der CNC-Programmierung wartet. Außerdem kann der Programmierer während des CAM-Prozesses seine Meinung ändern, wodurch alle vorgeplanten Einstellungen obsolet werden.
Erschwerend kommt hinzu, dass verschiedene Werkzeuge unterschiedlich lang aus der Maschinenspindel herausragen, ebenfalls ein Wert, der im Voraus schwer zu bestimmen ist. Beispielsweise erstreckt sich ein langer Schaftfräser weiter von der Spindelfläche als ein kurzer Bohrer. Wenn das Werkzeug verschleißt oder bricht und ersetzt werden muss, ist es fast unmöglich, es jedes Mal auf die exakte Länge aus dem Werkzeughalter einzustellen.
Daher muss es eine Möglichkeit geben, das Maschinenkoordinatensystem mit dem WKS des Teils in Beziehung zu setzen und unterschiedliche Werkzeuglängen zu berücksichtigen. Dies erfolgt mithilfe von machineTool- und Fixture-Offsets. Auf CNC-Maschinen sind viele Offsets verfügbar. Für eine erfolgreiche CNC-Bearbeitung ist es unerlässlich, zu verstehen, wie sie funktionieren, und sie richtig zusammen einzusetzen.
Teileversatz XY:
Vorrichtungs-Offsets bieten der CNC-Steuerung eine Möglichkeit, den Abstand von der Maschinen-Ausgangsposition und dem WKS des Teils zu kennen. In Verbindung mit Werkzeugversätzen ermöglichen Vorrichtungsversätze das Schreiben von Programmen in Bezug auf das WKS anstelle der Maschinenkoordinaten. Sie erleichtern die Einrichtung, da die genaue Position des Teils in der Maschinenhülle nicht bekannt sein muss, bevor das CNC-Programm geschrieben wird.
Solange das Teil so positioniert ist, dass das Werkzeug alle Bearbeitungsoperationen erreichen kann, kann es sich überall im Maschinenraum befinden. Sobald die Fixture Offset-Werte gefunden, in die Steuerung eingegeben und vom CNC-Programm aktiviert wurden, arbeitet die CNC-Steuerung hinter den Kulissen, um Programmkoordinaten in WCS-Koordinaten zu übersetzen.
Beachten Sie in Abbildung 14, wie Teileversätze (+X, -Y) verwendet werden, um die Mittellinie der Maschinenspindel direkt über das WKS zu verschieben.
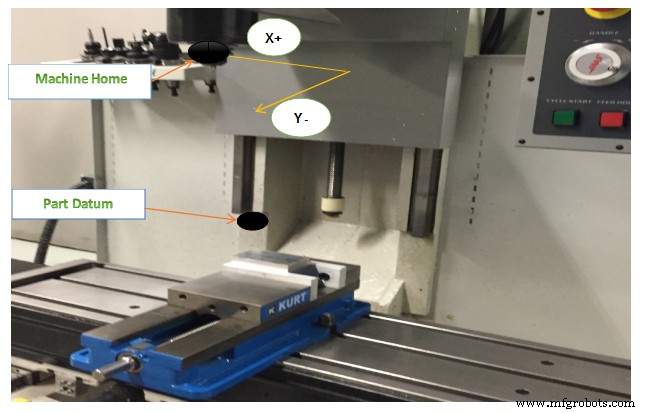
Abbildung 4:Teileversatz verschiebt Maschine auf WCS
Teilversatz Z
Der Z-Wert des Teileversatzes wird mit dem Werkzeuglängenversatz kombiniert, um der Maschine anzuzeigen, wie der Z-Bezug unter Berücksichtigung der Länge des Werkzeugs vom Nullpunkt des Teils zum Z-Nullpunkt des Teils verschoben werden soll. Abhängig davon, wie die Maschine eingerichtet und betrieben wird, kann der Vorrichtungsversatz Z verwendet werden oder nicht.
Werkzeuglängenversatz (TLO)
Jedes in die Maschine geladene Werkzeug hat eine andere Länge. Wenn ein Werkzeug aufgrund von Verschleiß oder Bruch ersetzt wird, ändert sich wahrscheinlich die Länge seines Ersatzes, da es fast unmöglich ist, ein neues Werkzeug genau an der gleichen Stelle wie das alte in den Halter einzusetzen. Die CNC-Maschine muss wissen, wie weit sich jedes Werkzeug von der Spindel bis zur Spitze erstreckt. Dies wird mit einem Tool Length Offset (TLO) erreicht.
In seiner einfachsten Verwendung wird der TLO gefunden, indem die Spindel mit dem Werkzeug von der Z-Ausgangsposition der Maschine zur Z-Nullposition des Teils bewegt wird, wie ganz links in Abbildung 17 unten gezeigt. Das Werkzeug wird zum Teilebezugspunkt Z getippt und der zurückgelegte Weg wird gemessen. Dieser Wert wird in das TLO-Register für dieses Werkzeug eingegeben. Zu den Problemen bei diesem Verfahren gehört die Notwendigkeit, das Teil vor dem Einstellen der Werkzeuge auf die richtige Tiefe zu planfräsen. Auch wenn der Z-Bezug weggeschnitten ist (typisch für Teile mit 3D-Oberfläche), ist es unmöglich, den Bezugspunkt festzulegen, wenn ein Werkzeug bricht oder abgenutzt ist und ersetzt werden muss. Alle Werkzeuge müssen zurückgesetzt werden, wenn ein neuer Job eingerichtet wird. Bei dieser Methode wird Fixture Offset Z nicht verwendet, sondern auf Null gesetzt.
Die in der Mitte gezeigte Methode ist viel besser und wird in diesem Buch verwendet. Alle Werkzeuge werden auf eine bekannte Z-Position eingestellt, wie z. B. die Oberseite eines Präzisions-1-2-3-Blocks, der auf dem Maschinentisch ruht. Dies macht es sehr einfach, abgenutzte oder kaputte Werkzeuge zurückzusetzen.
Ein Werkzeugmesstaster ist der 1-2-3-Blockmethode sehr ähnlich, außer dass die Maschine einen speziellen Zyklus verwendet, um den TLO automatisch zu finden. Dies geschieht durch langsames Absenken des Werkzeugs, bis die Spitze die Sonde berührt, und aktualisiert dann das TLO-Register. Diese Methode ist schnell, sicher und genau, erfordert jedoch, dass die Maschine mit einem Werkzeugmesstaster ausgestattet ist. Außerdem sind Werkzeugsonden teuer, daher muss darauf geachtet werden, dass das Werkzeug niemals gegen die Sonde stößt.
Sowohl die 2. als auch die 3. Methode erfordern außerdem, dass der Abstand von der Werkzeugeinstellposition (der Oberseite des 1-2-3-Blocks oder der Werkzeugsonde) zum Teilebezug gefunden und in den Fixture Offset Z eingegeben wird. Die Maschine addiert die beiden Werte zusammen, um den gesamten Werkzeuglängenversatz zu bestimmen. Eine Methode dafür ist in enthalten.
3-Wege zum Einstellen des Werkzeuglängenversatzes
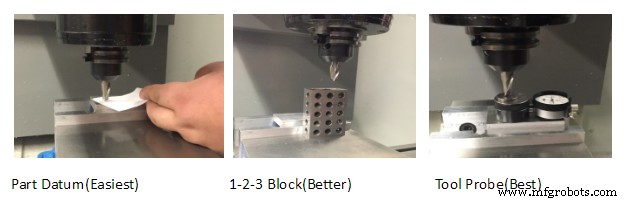
Abbildung 5. Möglichkeiten zum Festlegen von TLO
EINHEITENTEST
1. Erklären Sie die Ausgangsposition der Maschine.
2. Auf dem Vertical Milling Center (VMC) bewegt die X-Achse den Tisch in welche Richtung.
3. Auf dem Vertical Milling Center (VMC) bewegt die Y-Achse den Tisch in welche Richtung.
4. Auf dem Vertical Milling Center (VMC) bewegt die Z-Achse den Tisch in welche Richtung.
5. Please lists 3-ways to set Tool length offsets.
Industrietechnik
- Funktionen des vertikalen Bearbeitungszentrums zur Verbesserung der Produktivität
- Die wichtigsten Gründe für den Kauf eines vertikalen Bearbeitungszentrums
- Definition, Prozess und Typen von Fräsmaschinen
- Vertikaldrehzentrum mit beweglicher, umgekehrter Spindel
- Vertikaldrehzentrum fügt Verzahnungsfunktion hinzu
- Vierachsiges vertikales Drehzentrum für die Wellenfertigung
- 1 Fräsmaschinen
- 22 Lektion 5:CNC-Betrieb
- CNC-Vertikalfräser
- Was ist vertikale Bearbeitung?