Neu kaufen oder umbauen? Ein systematischer Ansatz für schwierige Instandhaltungsentscheidungen
In der Fertigungswelt herrscht ein Missverständnis über Zuverlässigkeit und es hat erhebliche Auswirkungen auf Fabriken, Manager, Techniker, Zuverlässigkeitsexperten und Endergebnis in Produktionsstätten weltweit. Das Missverständnis beruht auf einem risikobasierten Zuverlässigkeitsansatz, der Produktivitätsverbesserungen möglicherweise nicht richtig erkennt, was zu erhöhten Kosten führt.
Der Fehler, den einige Zuverlässigkeitsexperten machen, ist folgender:Wenn sie nach Antworten suchen, wenn eine Produktionsmaschine oder ein Prozess in der Fabrikhalle ausfällt, verfolgen sie einen risikobasierten Ansatz, um sich ausschließlich auf den Herstellungsprozess zu konzentrieren, anstatt die Ursache des Fehlers zu analysieren .
Statistiken zeigen, dass 50 Prozent der Wartungs- und Reparaturaufträge ein Teil erfordern. Die Kontrolle von Zuverlässigkeits- und Wartungskapitalausgaben und Kostenbudgets machen es schwierig, den Zuverlässigkeitsansatz zu verbessern, da bis zu 20 Prozent der Betriebskosten der Anlage wartungsbezogen sind und 73 Prozent der Wartungs-MRO-Bestände inaktiv sind.
Glücklicherweise gibt es einen anderen Ansatz. Die Analyse auf Prozessebene ist zweifellos wichtig, daher liegen Zuverlässigkeitsexperten nicht falsch, den Herstellungsprozess zu bewerten, wenn sie versuchen, die Produktivität zu verbessern und die Betriebszeit zu erhöhen. Der Fehler einiger Zuverlässigkeitsabteilungen besteht darin, nicht nach den Ursachen zu suchen. Erforderlich ist ein Ansatz, der den Prozess einige Schritte weiterführt und Datentrends analysiert, um ein Verständnis dafür zu entwickeln, wie und warum Komponenten auf Systemebene versagen.
In diesem Beitrag werden die Probleme untersucht, die einem risikobasierten Ansatz innewohnen, der sich ausschließlich auf die Analyse auf Prozessebene konzentriert. Es wird die Lösung skizzieren, die eine Erweiterung dieser Strategie um eine Analyse auf Komponentenebene darstellt, einschließlich einer Untersuchung von Faktoren, der Entwicklung und Implementierung von Korrekturmaßnahmen, die zur Beseitigung von Fehlern und zur kontinuierlichen Verbesserung beitragen. Das Papier wird dann die Ergebnisse überprüfen, die Hersteller erwarten können, wenn sie ihren Zuverlässigkeitsansatz modernisieren.
Ein risikobasierter Ansatz für Zuverlässigkeit
In Produktionsanlagen verwenden Zuverlässigkeitsingenieure normalerweise eine Strategie zur Wertstromanalyse, bei der jede Phase des Prozesses identifiziert wird, die Rohstoffe in ein fertiges Produkt umwandelt, und jeden Schritt des Arbeitsablaufs im Detail analysieren. Produktionsanlagen sind ein wichtiger Teil des Wertstroms, und Zuverlässigkeitsingenieure haben die Aufgabe, sicherzustellen, dass alle Komponenten so zuverlässig wie möglich sind, um Spitzenleistungen zu gewährleisten.
Als Teil ihrer Zuverlässigkeitsstrategie identifizieren Zuverlässigkeitsingenieure jede Komponente – elektrische Systeme, Hydraulik usw. – arbeiten methodisch durch jedes System und bewerten, wie sich der Ausfall einer Komponente auf die Produktion auswirken würde.
Der Zuverlässigkeitsingenieur könnte beispielsweise eine Hydraulikleitung als Fehlerpunkt identifizieren und mithilfe der risikobasierten Strategie einen Plan zur Schadensbegrenzung erstellen, der die Aufrechterhaltung einer Ersatzteilversorgung für die Leitung oder den Bau von Redundanzen umfassen könnte, um sicherzustellen, dass der Betrieb fortgesetzt oder erhalten wird bei einem Systemausfall schnell wieder auf Kurs.
Dies können notwendige Schritte sein, aber wenn Zuverlässigkeitsexperten die Zuverlässigkeit auf der Prozessebene statt auf der Ebene der Systemkomponenten angreifen, können sie Entscheidungen treffen, die zu kostspieligen und unnötigen Ausgaben führen.
Unabhängig davon, ob es sich um die erheblichen Kosten im Zusammenhang mit dem Austausch komplexer Prozesssysteme handelt oder um die Kapitalbindung in einem Bestand von MRO-Komponenten, die möglicherweise nie eingesetzt werden, ist der risikobasierte Ansatz der Zuverlässigkeit ein ineffizienter und kostspieliger Ansatz, um Ausfälle von Produktionslinien zu verhindern.
Das Problem mit dem risikobasierten Ansatz besteht darin, dass er nicht weit genug geht, da er nicht die Grundursache des Ausfalls angeht, die wahrscheinlich Komponenten sind. Es gibt mehrere Fehlerquellen für eine bestimmte Komponente.
Alternde Komponenten oder veraltete Produkte, Konstruktionsfehler und falsch identifizierte Teile sind nur einige Beispiele für Faktoren, die dazu führen können, dass ein Gerät auf Komponentenebene ausfällt.
Um ihren Zuverlässigkeitsansatz wirklich zu modernisieren, müssen Zuverlässigkeitsexperten verstehen, wie und warum Komponenten auf Systemebene ausfallen. Ein Zuverlässigkeitsansatz auf Komponentenebene definiert die Ursache des Fehlers besser und reduziert Investitionen in Lagerbestände und zukünftige CAPEX-Investitionen.
Es ist wichtig, sich daran zu erinnern, dass hinter jeder Komponente, die versagt, eine Geschichte steckt. Zuverlässigkeitsexperten müssen Maßnahmen ergreifen, um sicherzustellen, dass die Geschichte nicht in den Schrott- und Mülleimern verloren geht. Zuverlässigkeit, Wartung und Ersatzteile spielen eine entscheidende Rolle, wie in Abbildung 1 dargestellt.
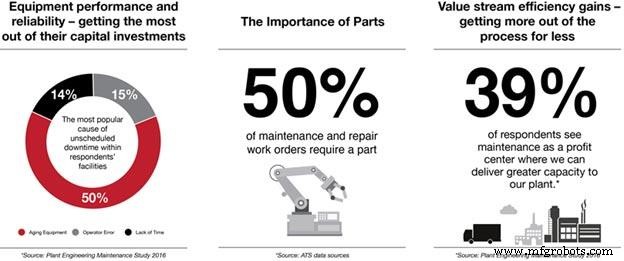
Abbildung 1. Die Bedeutung von Zuverlässigkeit, Wartung und Ersatzteilen
Betrachten Sie das reale Beispiel eines alternden Servomotorantriebs, der zufällig auch ein veraltetes Produkt ist, das mehrere Ausfälle in der Produktionslinie verursacht. Unter Verwendung des risikobasierten Ansatzes stellt der Zuverlässigkeitsingenieur fest, dass zufällige Platinenausfälle darauf hinweisen, dass das Laufwerk seine Nutzungsdauer überschritten hat, und kann einen CAPEX-Plan implementieren, um die Installationsbasis zu ersetzen, um Produktionsverzögerungen zu minimieren.
Wenn der Zuverlässigkeitsingenieur jedoch eine Strategie auf Komponentenebene verfolgt, würde die Untersuchung des Fehlerpunkts eine Ursachenanalyse beinhalten, die feststellt, dass zufällige Leiterplattenausfälle auf das Alter zurückzuführen sind.
Der Zuverlässigkeitsingenieur könnte ein Rebuild-Verfahren für die Platine entwickeln, bei dem alternde Komponenten durch neuere Premium-Komponenten ersetzt werden. In einem realen Szenario führte dieser Ansatz zu einer 54-prozentigen Reduzierung der Ausfälle.
Indem der Zuverlässigkeitsingenieur auf diese Weise die Ursache des Problems anging, anstatt sich ausschließlich auf Abhilfemaßnahmen auf Prozessebene zu konzentrieren, konnte der Zuverlässigkeitsingenieur nicht nur die Nutzungsdauer der Komponenten verlängern, sondern auch deren Ausfallraten im Laufe der Zeit senken. Das in Abbildung 2 unten dargestellte Trenddiagramm zeigt die Reduzierung von Fehlern im Zusammenhang mit sich entwickelnden Standards für Wiederaufbauverfahren.

Abbildung 2. Reduzierung der Ausfallrate in Abhängigkeit von sich entwickelnden Mindeststandards
Konstruktionsprobleme können auch zu Ausfällen von Produktionsanlagen beitragen. Ein Zuverlässigkeitsingenieur analysiert beispielsweise einen wiederkehrenden Ausfall der Steuerplatine an einem Motorantrieb und stellt fest, dass dieser aufgrund einer Überhitzung der Steuerplatine ausfällt.
Wenn der Zuverlässigkeitsingenieur nur Faktoren auf Prozessebene berücksichtigt, könnte die Korrekturmaßnahme darin bestehen, einen Mindest-/Höchstwert für den Lagerbestand festzulegen, um sicherzustellen, dass ein Lagerbestand an Ersatzteilen für Motorantriebe verfügbar ist, um Produktionsverzögerungen zu minimieren.
Wenn der Zuverlässigkeitsingenieur jedoch eine Strategie auf Komponentenebene verfolgt, würde die Untersuchung des Fehlerpunkts eine Ursachenanalyse beinhalten, die einen Konstruktionsfehler entdeckt. Im realen Beispiel wurde festgestellt, dass der Motorantrieb eine Steuerplatine hatte, die sich zu nahe an einem Kühlkörper befand, was zum Ausfall der Kondensatoren führte.
Nachdem die Ursache identifiziert wurde, implementierte der Hersteller einen Korrekturplan, der einen proaktiven Rückruf anderer Installationen und eine technische Lösung umfasste, die dazu führte, dass die Steuerplatine vom Kühlkörper entfernt wurde, was zu einer Reduzierung der Ausfälle um 96 Prozent führte, da in Abbildung 3 unten dargestellt.
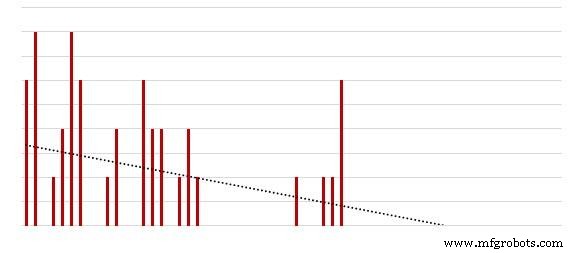
Abbildung 3. Reduzierung der Ausschussrate
Ein drittes Praxisbeispiel dafür, wie ein Ansatz auf Prozessebene zu unnötigen Ausgaben und vermehrten Fehlern führen kann, betrifft eine Fabrik, die aufgrund falscher Teileidentifikation ein Problem mit falschen Druckwandlerinstallationen hatte.
Der Hersteller hat mehrere Modelle der Aufnehmer für eine Vielzahl von Anwendungen unter einer einzigen Artikelnummer auf Lager. Beim risikobasierten Ansatz bestand die Korrekturmaßnahme darin, einen Mindest-/Höchstwert für den Lagerbestand festzulegen, um sicherzustellen, dass der Lagerbestand verfügbar war, wenn Druckwandler ausfielen.
Ein Zuverlässigkeitsingenieur führte eine Bewertung auf Komponentenebene durch und identifizierte das Problem mit den falsch installierten Druckwandlern. Der Zuverlässigkeitsingenieur implementierte einen Korrekturplan, um Wandler pro eingestellten Druckparameter zu lagern und neue SKUs für jeden Parameter festzulegen. Infolgedessen gingen die Fehler bei der Umsetzung des Plans um 37 % zurück, wie das Diagramm in Abbildung 4 unten zeigt.
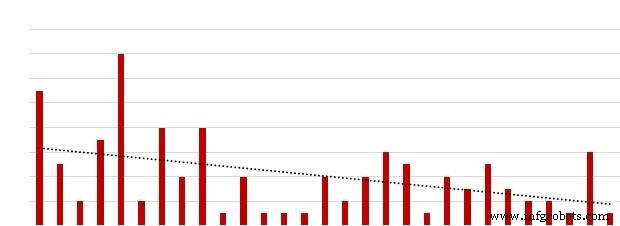
Abbildung 4. Verringerung der Wandlerausfälle
Wie diese drei Beispiele zeigen, ist das Verständnis, wie und warum diese Komponenten auf Systemebene ausfallen, der Schlüssel zum Aufbau einer echten Zuverlässigkeitsleistung. Durch einen Drilldown über die Prozessebene hinaus konnten Zuverlässigkeitsingenieure die Ursachen analysieren und Lösungen entwickeln, die die Betriebszeit verbessern, die Betriebskosten senken und die Effizienz steigern. Auch neue Technologien können eine Schlüsselrolle bei der Effizienzsteigerung spielen.
Die additive Fertigung (3-D-Druck) ist beispielsweise eine neue Technologie, die auch zur Verbesserung der Zuverlässigkeit auf Komponentenebene verwendet werden kann. Während sich die additive Fertigungstechnologie schnell ändert, ist sie eine effektive Methode, um Lösungen zu entwickeln, um vorzeitigen Verschleiß und Ausfälle zu verhindern.
Prototypen können sehr kostengünstig hergestellt werden, um sicherzustellen, dass das Design die Pass-, Form- und Funktionsanforderungen der ursprünglichen Designanwendung erfüllt. Im additiven Fertigungsprozess können verschiedene Materialien wie Titan verwendet werden, um Komponenten in ihrer Betriebsumgebung viel haltbarer zu machen.
Es gibt viele Beispiele, die die Wirksamkeit eines Ansatzes auf Komponentenebene veranschaulichen. Durch die Erfassung von Informationen über Komponentenausfälle können Zuverlässigkeitsingenieure einfache „Quick-Win“-Verbesserungen identifizieren und Standardarbeitsanweisungen und Technikerschulungsprogramme erstellen, die zu erheblichen Einsparungen führen.
Ein komponentenbasierter Ansatz zur Zuverlässigkeit
Zuverlässigkeitsabteilungen, die über eine Analyse auf Prozessebene hinausgehen und sich auf Probleme auf Komponentenebene innerhalb von Subsystemen konzentrieren, können die Ergebnisse erheblich verbessern, dies erfordert jedoch eine andere Denkweise über Fehlerpunkte und Minderungsstrategien.
Zuverlässigkeitsexperten, die sich mit dem Übergang zu einer Strategie auf Komponentenebene befassen, können von Außenperspektiven profitieren, z. B. von den von Originalgeräteherstellern (OEMs) verwendeten Methoden und dem Fachwissen Dritter
Grundlegende Verbesserungen können zusätzliche Möglichkeiten für zuverlässigkeitsbasierte Verbesserungen sein und können die Implementierung von Lagerraumprozessen umfassen, einschließlich 5-S, Teileidentifikation und Best Practices für die Lagerung, Testen von Zertifizierungsverfahren für Komponenten, die für die Fehlersuche verwendet werden, und Kernverfolgung, um sicherzustellen, dass die Geschichte nicht in den Papierkorb geworfen werden.
Die Entwicklung von Wartungsstandards kann ebenfalls eine Schlüsselkomponente sein, wie z. B. die Einbeziehung technischer Ressourcen in den RCA-Prozess und Einzelunterrichtseinheiten, die Stammeswissen auf Komponentenebene dokumentieren.
Um das neue Paradigma der Zuverlässigkeit vollständig zu akzeptieren, müssen Sie über abstrakte Theorien hinausblicken und praktische Erfahrungen nutzen, um neue Lösungen zu entwickeln. Ein breiterer Zugriff auf Teamexpertise kann zu besseren Ergebnissen und einem starken Engagement für die Wertschöpfung führen.
Echte Zuverlässigkeitsleistung
Der risikobasierte Zuverlässigkeitsansatz kann leider zu erhöhten Kosten für die Hersteller führen. Es ist jedoch immer noch eine wertvolle Analyse und sollte eine Kernfunktion des Zuverlässigkeitsprofis bleiben.
Zu einem modernen Verständnis von Zuverlässigkeit gehört jedoch die Erkenntnis, dass die eigentliche Fehlerursache eher Komponenten als der Produktionsprozess selbst sind. Darüber hinaus beinhaltet es den Einsatz neuer Technologien, modernster Analysen und Best Practices, um eine zuverlässigere und profitablere Ausgabe zu erzielen.
Ein Beispiel für echte Zuverlässigkeitsleistung in der Praxis ist die Erfahrung eines anerkannten Marktführers bei Ersatzreifen für Pkw und Nutzfahrzeuge, der einen neuen Ansatz zur Verwaltung seines Bestands an reparierbaren Teilen einführte.
Ein externer Zuverlässigkeitsexperte bewertete die einzigartige Situation des Unternehmens und entwickelte einen Plan zur Verwaltung seines Teileprogramms durch ein Vor-Ort-Programm zur Verwaltung von reparierbaren Teilen. Mit einem proaktiveren Teilemanagement-Programm konnte der Hersteller einen Rückgang der Teileausfälle um 53 Prozent verzeichnen. Das Managementprogramm für reparierbare Teile konnte außerdem den Teilebestand um 15 % reduzieren, was zu erheblichen Einsparungen führte.
Mit erhöhter Betriebszeit und Maschinenverfügbarkeit konnte der Hersteller die wachsende Nachfrage nach seinen Produkten effizienter bedienen. Ein leitender Manager der Unternehmenswartungsabteilung des Unternehmens stellte fest, dass der Hersteller durch den Zugriff auf das Fachwissen von Drittanbietern und die Konzentration auf die Verbesserung der Zuverlässigkeit der reparierbaren Anlagen des Unternehmens seine Gesamtkosten senken und gleichzeitig die Produktionseffizienz verbessern konnte.
In einem anderen Beispiel, das den Wert echter Zuverlässigkeitsleistung veranschaulicht, arbeitete ein Tier-1-Automobilzulieferer mit einem Zuverlässigkeitsexperten zusammen, um Probleme auf Komponentenebene zu beheben, und identifizierte ein Problem mit der Lebensdauer von Kugelgewindetrieben. Zuverlässigkeit war ein Problem, da die Kugelgewindetriebe auf mehreren Maschinen eingesetzt wurden und aus Deutschland kundenspezifisch bestellt werden mussten. Dadurch hatte der Automobilzulieferer mit langen und/oder sporadischen Vorlaufzeiten zu kämpfen.
Ein intelligenterer Ansatz für Zuverlässigkeit
Fertigungsunternehmen weltweit verpassen eine einmalige Gelegenheit, indem sie sich ausschließlich auf Verbesserungen auf Prozessebene konzentrieren, die ein wichtiger Teil einer Gesamtzuverlässigkeitsstrategie sind, aber nicht tief genug gehen, um alle verfügbaren Produktivitätsgewinne und Kosteneinsparungen auszuschöpfen.
Indem es vernachlässigt wird, die Ursache von Fehlern auf Komponenten- und Subsystemebene zu analysieren, kosten Zuverlässigkeitsabteilungen, die einen risikobasierten Ansatz verfolgen, ihre Unternehmen Zeit und Geld.
Wie die in diesem Papier behandelten Beispiele veranschaulichen, gibt es einen besseren Weg. Fehlerstellen treten häufig auf Komponentenebene auf. Zuverlässigkeitsexperten, die ihren Ansatz über eine Überprüfung auf Prozessebene hinaus um eine Ursachenanalyse erweitern, können Probleme erkennen und abschwächen, die durch Faktoren wie Konstruktionsfehler, Komponentenalter und falsche Installation verursacht werden.
Durch ein besseres Verständnis dafür, wie und warum Komponenten auf Systemebene versagen, und durch ein Umdenken, um neue Perspektiven einzubeziehen, können Zuverlässigkeitsexperten die Ergebnisse auf allen Ebenen verbessern. Unterstützt durch neue Technologien wie IoT-fähige Teile und die Nutzung von Datenanalysen, um das Verhalten effektiver einzuschätzen und Strategien wie vorbeugende Wartungsprogramme zu implementieren, können moderne Zuverlässigkeitsexperten die Maschine für sie arbeiten lassen, um zuverlässige Teile, zuverlässige Prozesse und zuverlässige Einsparungen zu liefern.
Gerätewartung und Reparatur
- Der Fall für die mobile Wartung:Fiix schaut beim Podcast Asset Reliability @ Work vorbei
- Was ist Zuverlässigkeitskultur?
- Beste Leistung bei Wartung und Zuverlässigkeit
- Wartungs-Outsourcing:Ein Modell für operative Exzellenz
- Standard Aero für Wartung und Zuverlässigkeit gelobt
- Details sind wichtig für Wartung und Zuverlässigkeit
- SMRP ist wertvoll für M&R-Profis
- Familienorientierte Zuverlässigkeit
- SMRPCO erhält Genehmigung zur Erstattung von Prüfungsgebühren gemäß GI-Rechnung
- 5 Schlüssel zur Aufrechterhaltung der Gerätezuverlässigkeit