So implementieren Sie einen Total Productive Maintenance Plan (TPM)
Die erfolgreiche und nachhaltige Umsetzung von Total Productive Maintenance (auch bekannt als TPM) sollte ein zentrales Anliegen jedes gewissenhaften Betriebsleiters oder Produktionsleiters sein. TPM führt zu reduzierten Ausfallzeiten, weniger Stopps und Ausfällen und einer geringeren Wahrscheinlichkeit, dass Produkte während des Herstellungsprozesses Qualitätsmängel erleiden.
Warum ist TPM ein so effektives Tool? Kurz gesagt, weil befugte Bediener, die eine aktive Rolle bei der Inspektion und Wartung ihrer eigenen Ausrüstung übernehmen, immer zu einer verbesserten Produktion und Zuverlässigkeit der Ausrüstung beitragen.
Im Laufe der Jahre haben Studien die positive Korrelation zwischen der Implementierung eines TPM-Programms und der gesamten Fertigungsleistung bestätigt. Einige Ergebnisse deuten darauf hin, dass ein Unternehmen den Produktionsausfall um ca. 20 % reduzieren kann, indem es einen umfassenden produktiven Wartungsplan durchführt. Dennoch stellt sich eine wichtige Frage:Wie kann ein Unternehmen TPM effektiv implementieren ? Die folgenden Informationen werden dieser Frage nachgehen.
Sind Sie daran interessiert, Wartungskosten zu sparen?
Sie können hier auf weitere nützliche Ressourcen und Forschungsberichte zugreifen.
Was Total Productive Maintenance ist
Zur Erinnerung:Jedes TPM-Programm umfasst mindestens 8 Kernkonzepte, die eine große Rolle bei der Bestimmung des endgültigen Erfolgs der Initiative spielen. Diese 8 Konzepte sind:
-
Autonome Wartung
Dieses grundlegende Element von TPM konzentriert sich auf die Schulung und Befähigung von Wartungspersonal wie Maschinenbedienern, routinemäßiges Wartungsmanagement selbst durchzuführen. -
Fokussierte Verbesserung
Diese Säule von TPM bezieht sich auf proaktive Wartungstechniken:einen aktuellen Prozess auf ganzheitliche Weise zu untersuchen und Möglichkeiten zu seiner Verbesserung zu identifizieren. -
Geplante Wartung
Ein geplantes Wartungsprogramm nutzt historische Ausfallzeitdaten und prädiktive Analysen, um wichtige Wartungsaufgaben um wahrscheinliche Ausfallraten oder erwartete Leerlaufzeiten herum zu planen. -
Qualitätspflege
Der Qualitätswartungsprozess soll sicherstellen, dass die tatsächlich durchgeführten Wartungsaufgaben die allgemeinen Ziele der Fehlererkennung, Fehlervermeidung und Qualitätssicherung effizient erreichen. -
Frühe Ausrüstungsverwaltung
Durch die Nutzung des Feedbacks von Bedienern mit praktischer Erfahrung stellt ein frühzeitiges Ausrüstungsmanagement sicher, dass die Konstruktion neuer Ausrüstungsteile die Lebensdauer, Zugänglichkeit und Produktivität der Maschinen optimiert. -
Schulung
Jedes TPM-Programm sollte ein Schulungs- und Schulungselement für Bediener und Manager gleichermaßen enthalten. -
Sicherheit und Gesundheit
Alle TPM-Prozesse sollten Sicherheits- und Gesundheitsaspekte berücksichtigen, um eine sichere Arbeitsumgebung für Bediener und andere Mitarbeiter zu fördern. -
TPM-orientierte Verwaltung
Abgesehen von rein mechanischen Überlegungen berücksichtigt ein gut konzipiertes TPM-Programm auch Verwaltungsfunktionen wie Auftragsabwicklung und Terminverwaltung und sucht nach Möglichkeiten, diese zur Unterstützung der Produktion zu verbessern.
So implementieren Sie TPM
Während ein TPM-Programm an die spezifischen Bedürfnisse und Umstände des Unternehmens angepasst werden sollte, gibt es 7 grundlegende Schritte zur Implementierung von TPM, wie unten aufgeführt:
1. Ankündigung von Plänen für die TPM-Implementierung
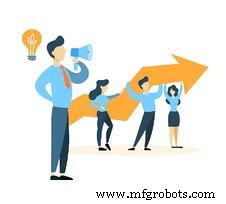
2. Identifizieren Sie einen Bereich für ein TPM-Pilotprogramm
Sie könnten sich auf ein Gerät konzentrieren, das am einfachsten zu verbessern wäre, oder auf einen Produktionsbereich, der sich als problematisch erwiesen hat und repariert werden muss, um die Rentabilität schnell zu verbessern. Identifizieren Sie in dieser Anfangsphase des TPM-Prozesses Ziele, die SMART sind:spezifisch, messbar, erreichbar, realistisch und terminiert.3. Konzentrieren Sie sich auf die Wiederherstellung des erstklassigen Betriebszustands der Zielausrüstung
Nachdem Ihr Pilotbereich identifiziert wurde, zeichnen Sie einen Basisstandard für die aktuelle Produktivität auf. Organisieren und definieren Sie Ihren Plan für die TPM-Implementierung . Verwenden Sie die 5S-Methodik (Sort, Set, Shine, Standardize, Sustain). Konzentrieren Sie sich zunächst auf die Durchführung eines autonomen Wartungsprogramms und schulen Sie die Gerätebediener nach Bedarf. So wie ein Autobesitzer durch die Durchführung grundlegender routinemäßiger Wartungsarbeiten erhebliche Reparaturkosten einsparen kann, können auch Unternehmen die Lebensdauer von Maschinen verlängern und mechanische Probleme frühzeitig erkennen, indem sie ihren Bedienern die regelmäßige Teilnahme an grundlegenden Wartungsarbeiten ermöglichen4. Beginnen Sie mit der Messung der Gesamtanlageneffektivität (OEE)
Wie auch immer Sie sich entscheiden, die OEE im Auge zu behalten, es ist zwingend erforderlich, dass ungeplante Stoppzeiten dokumentiert und für jedes Vorkommen ein Grund angegeben wird. Geben Sie eine Kategorie für „unbekannte Ursache“ oder „nicht zugewiesene Stoppzeit“ für Fälle an, in denen sich der Bediener der Stoppursache nicht sicher ist. Im Laufe der Zeit hilft Ihnen dies bei der ersten Identifizierung Hauptverlustursachen, was wiederum zu Schritt #5 führt: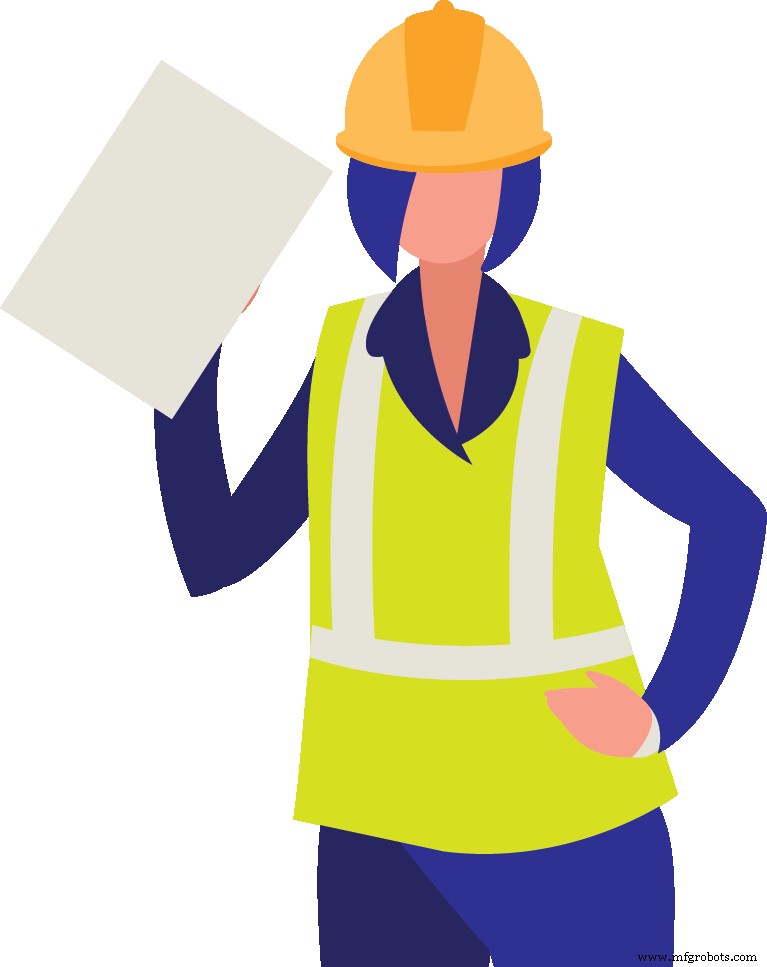
5. Hauptschadensursachen angehen
In diesem Schritt müssen Sie ein funktionsübergreifendes Team von etwa 4 bis 6 Mitarbeitern bestimmen, um eine Hauptursache für Ausfallzeiten zu untersuchen . Dieses Team erstellt einen Plan zur Beseitigung der Verlustursache und plant die geplante Stoppzeit für die Durchführung dieser Initiative. Wenn Ihre großen Verluste beispielsweise auf häufige Füllerstaus zurückzuführen sind, untersucht dieses Team die aktuellen Bedienerprozesse und Reparaturoptionen, erstellt einen Plan zur Beendigung der Staus und plant dann die Zeit für die Umsetzung des Plans ein. Sobald die festgelegte Maßnahme abgeschlossen ist, wird die OEE in Zukunft gemessen und der Prozess bei Bedarf neu gestartet.
6. Implementieren Sie eine proaktive Wartung
In diesem Schritt liegt Ihr Fokus auf der Vermeidung von Ausfällen oder Stillstandszeiten. Identifizieren Sie wichtige "Schmerzpunkte", die zu Geräteausfällen führen könnten , und erstellen Sie einen Zeitplan für die vorbeugende Wartung in regelmäßigen Abständen. Richten Sie schließlich einen Feedback-Prozess ein, der es Ihnen ermöglicht, die Effektivität Ihres Programms kontinuierlich zu überwachen. Dieses Feedback-System könnte Wartungsprotokolle, monatliche oder zweimonatliche Audits und Datensammlung aus Thermografie und/oder Vibrationsanalyse umfassen.
7. Implementieren Sie nach Bedarf spezifische TPM-Konzepte
Beispielsweise sollte ein frühzeitiges Ausrüstungsmanagement ins Spiel kommen, wenn neue Maschinen für die Produktionshalle entworfen und/oder installiert werden. Vielleicht sollte das Design neuer Geräte optimiert werden, um eine verbesserte Zugänglichkeit, einfachere Reinigungs- oder Schmierverfahren oder das Hinzufügen von Sicherheitsfunktionen einzubeziehen. Kommt es hingegen zu Beschaffungsproblemen oder Verzögerungen bei der Bearbeitung von Arbeitsaufträgen, sollten Sie diese administrativen Engpässe so schnell wie möglich beheben.Nutzung von TPM zur Verbesserung des Wartungsmanagements
Total Productive Maintenance ist ein Schlüsselelement zur Reduzierung von Produktionsverlusten durch Ausfallzeiten. Ein effektives TPM-Programm kann Mitarbeiter dazu befähigen, proaktive Maßnahmen zur Instandhaltung lebenswichtiger Maschinen zu ergreifen. Dies wiederum ermöglicht eine längere Lebensdauer der Produktionsanlagen. Die TPM-Implementierung trägt auch dazu bei, Qualitätsmängel und suboptimale Laufzeiten zu reduzieren.
Es gibt viele Tools auf dem Markt, wie z. B. Enterprise Asset Management-Plattformen und verwandte Programme, die Unternehmen bei der TPM-Implementierung unterstützen können. Letztendlich erfordert ein vollständig produktiver Wartungsplan zwar einige Anstrengungen für die ordnungsgemäße Gestaltung und Ausführung, aber die Belohnungen dafür sind die Investition wert!
Gerätewartung und Reparatur
- Ihren TPM-Plan in die Tat umsetzen:eine Schritt-für-Schritt-Anleitung
- So halten Sie die Wartung in einem proaktiven Modus
- So implementieren Sie eine vollständige produktive Wartung
- Vodcast:Eine Einführung in die Total Productive Maintenance
- So erstellen Sie ein elektrisches Wartungsprogramm
- Unilever erweitert das Total Productive Maintenance-Programm mit Hilfe von Informance
- Wie Betriebsleiter die regelmäßige Maschinenwartung planen können
- Total Productive Maintenance und Industrial IoT
- Implementierung der zuverlässigkeitsorientierten Wartung (RCM)
- Total Productive Maintenance:ein Leistungshebel?