Kontrolle der sekundären Oberflächenmorphologie von elektrogesponnenen PVDF-Nanofasern durch Regulierung des Lösungsmittels und der relativen Luftfeuchtigkeit
Zusammenfassung
Diese Arbeit präsentiert eine einfache und zuverlässige Methode zur direkten Erzeugung von Polyvinylidenfluorid (PVDF)-Nanofasern mit sekundärer Oberflächenmorphologie (z. B. poröse Oberflächen, raue Oberflächen, gerillte Oberflächen und innere Porosität) unter Verwendung einzelner/binärer Lösungsmittelsysteme und relativer Luftfeuchtigkeit. Wir haben die für die Bildung dieser Morphologien verantwortlichen Mechanismen aufgeklärt, indem wir die molekularen Wechselwirkungen zwischen Polymer, Lösungsmittel(n) und Wasserdampf systematisch untersucht haben. Unsere Ergebnisse bewiesen, dass die Bildung der sekundären Oberflächenmorphologie die Anwesenheit von Wasserdampf, einem Nicht-Lösungsmittel des Polymers, bei einem angemessenen Grad an relativer Feuchtigkeit erfordert. Die Bildung der sekundären Oberflächenmorphologie war abhängig von der Verdampfungsgeschwindigkeit des/der Lösungsmittel(s) (ACE, DMF und deren Gemische) sowie der Interdiffusion und Penetration des Nichtlösungsmittels (Wasser) und Lösungsmittel(s). ). Die Ergebnisse von N2 physikalische Adsorptions-Desorptions-Isothermen zeigten, dass die makroporösen Fasern (> 300 nm) die höchste spezifische Oberfläche von 23,31 ± 4,30 m 2 . aufwiesen /g und Porenvolumen von 0,0695 ± 0,007 cm 3 /g, wodurch die hohe Ölaufnahmekapazität von 50,58 ± 5,47 g/g, 37,74 ± 4,33 g/g und 23,96 ± 2,68 g/g für Silikonöl, Motoröl bzw. Olivenöl ermöglicht wird. Wir glauben, dass diese Arbeit als Richtlinien für die Bildung verschiedener Strukturen von makroporösen, rauen und gerillten Nanofasern mit innerer Porosität durch Elektrospinnen dienen kann.
Hintergrund
Elektrospinnen ist ein Faserbildungsverfahren, das elektrostatische Kräfte zum Ausstoßen und Strecken von Polymerstrahlen in Fasern einbezieht. Das Verfahren produziert derzeit Fasern mit einem Durchmesser von wenigen Nanometern bis hin zu mehreren Mikrometern [1]. Verschiedene Morphologien von elektrogesponnenen Fasern, einschließlich Perlenfasern [2], poröse Fasern [3], gerillte Fasern [4], Mehrkanalfasern [5], Bändchenfasern [6], nebeneinander liegende Fasern [7], Hohlfasern [8 ], hierarchische Fasern [9], reiskornförmige Nanokomposite [10], Schmetterlingsflügelfasern [11], Kern-Mantel-Fasern [12] und gekräuselte Fasern [13] können durch Steuerung der Elektrospinnparameter [14] gebildet werden.
Elektrogesponnene Nanofasern haben ausgezeichnete Eigenschaften wie hohe spezifische Oberfläche, Flexibilität, einfache Funktionalität, Vielfalt der Morphologie und Struktur, überlegene Richtungsfestigkeit und hohe Porosität gezeigt, was sie zu einer bevorzugten Materialform für verschiedene Anwendungen wie Energy Harvesting macht [15], Sensoren [16], Filtration [17,18,19], biomedizinische Anwendungen [20], selbstreinigende Oberflächen [21,22,23] usw. Studien haben gezeigt, dass durch Regulierung der Sekundärmorphologien (zB poröse Oberflächen, gerillte Oberflächen, raue Oberflächen und innere Porosität) von elektrogesponnenen Fasern konnten deren Eigenschaften und Verhalten stark verbessert oder verändert werden. Zum Beispiel haben poröse Fasern aufgrund der Erhöhung ihrer spezifischen Oberflächen durch die Einführung von Intrafaserporen eine breite Anwendung in einer Vielzahl von Anwendungen wie Katalyse, Filtration und biomedizinischer Forschung gezeigt [24]. Raue Fasern wurden verwendet, um die elektrische Leistung der Spülenergiegeräte aufgrund der Vergrößerung der Reibungsflächen zu verbessern [25]. Gerillte Fasern haben ein großes Potenzial im Bereich Tissue Engineering und superhydrophobe Oberflächen gezeigt [26]. Darüber hinaus führt die Erhöhung der spezifischen Oberfläche und Porosität zu einer verbesserten Absorptionsleistung [27, 28], Katalyse [29, 30] usw.
Zuvor haben wir über die Herstellung von Polystyrolfasern mit einstellbaren Makroporenstrukturen und -verteilungen unter Verwendung einer Mikrofluidikdüse mit drei Kanälen berichtet, die eine Flüssigkeitsmischung aus zwei Eingangskanälen und ein synchronisiertes Elektrospinnen der resultierenden Mischung aus dem anderen Ausgangskanal ermöglicht [3] . Darüber hinaus haben wir über die Herstellung von Celluloseacetatbutyrat- und Polystyrolfasern mit Rillenstruktur durch Elektrospinnen unter Verwendung eines gemischten Lösungsmittelsystems aus einem Lösungsmittel mit hohem Siedepunkt und einem Lösungsmittel mit niedrigem Siedepunkt berichtet [4, 31].
In dieser Studie demonstrieren wir die Herstellung von Polyvinylidenfluorid (PVDF)-Nanofasern mit makroporösen, rauen und gerillten Oberflächenstrukturen und inneren Poren durch Elektrospinnen ohne spezielle Sammelmethode oder Nachspinnenbehandlung. Als Modell wurde hier PVDF gewählt, da es in verschiedenen Lösungsmitteln gelöst werden kann.
Nach unserem besten Wissen wurden bisher keine Studien systematisch untersucht, in denen die Bildung der makroporösen (> 300 nm), rauen und gerillten elektrogesponnenen PVDF-Nanofasern mit interner Porosität durch Kontrolle der relativen Luftfeuchtigkeit gesteuert wurde. Hier berichteten wir über das Elektrospinnen von PVDF-Lösungen bei vier relativen Feuchtigkeitsniveaus (5 %, 25 %, 45 % und 65 %) unter Verwendung von sowohl einzelnen als auch binären Lösungsmittelsystemen. Das Hauptziel dieser Arbeit ist es, die Machbarkeit der Herstellung von makroporösen, rauen und gerillten Fasern mit festen und porösen Innenstrukturen unter Verwendung unterschiedlicher relativer Feuchtigkeit zu untersuchen und ihre Bildungsmechanismen aufzudecken. Durch systematische Untersuchung des Einflusses der relativen Feuchtigkeit auf die sekundäre Oberflächenmorphologie von elektrogesponnenen PVDF-Fasern kamen wir zu dem Schluss, dass die relative Feuchtigkeit eine wichtige Rolle bei der Bestimmung der Oberfläche und der inneren Morphologie von PVDF-Fasern spielt. Diese Studie kann nützliche Richtlinien für die Herstellung der sekundären Oberflächenstruktur von Nanofasern durch Elektrospinnen liefern.
Methoden
Chemikalien und Materialien
PVDF-Pellets (Mw =275.000) wurden von Sigma-Aldrich, Inc. bezogen. Aceton (ACE) und N,N-Dimethylformamid (DMF) wurden von Shanghai Chemical Reagents Co., Ltd., Shanghai, China bezogen. Alle Materialien wurden ohne weitere Reinigung verwendet.
Elektrospinnen von PVDF-Fasern mit sekundärer Oberflächenmorphologie
Um makroporöse, raue und gerillte Fasern zu erhalten, werden 18 % ACE (w /v ) PVDF-Lösung, 35 % DMF (w /v ) PVDF-Lösung und 25 % (ACE/DMF) (w /v ) PVDF-Lösungen mit den Lösungsmittelverhältnissen (4:1, 2:1, 1:1, 1:2 bzw. 1:4) wurden hergestellt, und jede Lösung wurde in eine Plastikspritze gefüllt. In dieser Arbeit war das Lösungsmittelverhältnis das Volumenverhältnis und die Lösungskonzentration Gewicht/Volumen (w /v ) (g/ml). Als Spinndüse wurde eine 21-Gauge-Spritzennadel verwendet, die an einer Spritzenpumpe (KDS 100, KD Scientific Inc., USA) befestigt war, die mit einem Hochspannungslieferanten (Tianjin Dongwen Co., Ltd., China) verbunden war. Ein geerdeter Trommelkollektor (40 cm Länge und 20 cm Durchmesser) wurde 18 cm von der Spinndüse entfernt platziert und die Rotationsgeschwindigkeit wurde auf 2 U/min eingestellt, um zufällig orientierte Fasern zu erhalten. Alle Experimente wurden bei 20 °C und unterschiedlicher relativer Luftfeuchtigkeit (5 %, 25 %, 45 % und 65 %) durchgeführt. Die Temperatur wurde durch die zentrale Laborklimaanlage eingestellt und die relative Luftfeuchtigkeit wurde durch die Umgebungsfeuchtigkeit gesteuert, die mit einem schmalen Fenster (± 2%) durch Verwendung eines Luftbefeuchters/Luftentfeuchters weiter eingestellt werden konnte. Alle Proben wurden mit einer Zufuhrgeschwindigkeit und einer angelegten Spannung von 1,5 ml/h bzw. 18 kV hergestellt. Alle vorherigen Parameter wurden angepasst, um Fasern mit unterschiedlichen Morphologien und ähnlichen Durchmessern zu erhalten.
Ternäres Phasendiagramm
Die Trübungspunktkurven wurden durch die Titrationsmethode bei einer relativen Feuchtigkeit von 65 % bestimmt. PVDF-Lösungen wurden durch Auflösen des Polymers in Einzellösungsmittelsystemen unter Verwendung von ACE und DMF und binären Lösungsmittelsystemen unter Verwendung von ACE/DMF im Lösungsmittelverhältnis von 1:1 hergestellt. Die erhaltenen homogenen Lösungen wurden mit entionisiertem Wasser als Nichtlösungsmittel titriert. Zu Beginn der permanenten Trübung wurden die Lösungszusammensetzung und die Menge des eingesetzten Nichtlösers notiert und in das ternäre Phasendiagramm eingetragen, das zur Darstellung der binodalen Kurven diente [32, 33].
Charakterisierung
Die Oberflächenmorphologie und der Querschnitt der elektrogesponnenen PVDF-Nanofasern wurden nach der Goldbeschichtung unter Feldemissions-Rasterelektronenmikroskopie (FE-SEM) (S-4800, Hitachi Ltd., Tokio, Japan) überprüft. Querschnitte der Fasern wurden hergestellt, indem sie in flüssigen Stickstoff gegeben und von Hand gebrochen wurden. Der Faserdurchmesser wurde unter Verwendung einer Bildanalysesoftware (Adobe Acrobat X Pro 10.1.2.45) gemäß den REM-Bildern gemessen. N2 physikalische Adsorptions-Desorptions-Isothermen (JW-BK132F, Beijing Science and Technology Co., China) wurden gemessen, um die spezifische Oberfläche, die Porenverteilung und das Gesamtporenvolumen zu bestimmen.
Ölaufnahme
Die Ölabsorptionskapazität wurde bei 25 °C unter Verwendung der folgenden Methode gemessen. Dann wurden 15 ml Wasser-Öl-Gemisch im Verhältnis 1:1 hergestellt und in ein Becherglas gegeben. Ferner wurden 0,3 g des Sorptionsmittels in das Becherglas gegeben, um 1 Stunde lang Öl zu absorbieren, und dann wurde das nasse Sorbens in ein Siebgewebe überführt und ~ 40 Minuten lang abgelassen, um sicherzustellen, dass keine Öltröpfchen auf dem Sorbens verblieben. Die Ölaufnahmekapazität wurde nach folgender Gleichung berechnet:
$$ Q\kern0.5em =\kern0.5em \frac{m_0-{m}_1}{m_1} $$wo Q ist die Ölaufnahmekapazität (g/g), m 0 ist die Gesamtmasse des nassen Sorptionsmittels nach der Ölaufnahme, die ~ 40 min (g) abgelassen wurde, und m 1 ist die Masse des Sorbens vor der Absorption (g).
Ergebnisse und Diskussion
Um den Einfluss der relativen Luftfeuchtigkeit auf die sekundäre Morphologie von elektrogesponnenen PVDF-Fasern zu untersuchen, wurden 18 % (w /v ) PVDF-Lösung mit ACE, 35% (w /v ) PVDF-Lösung mit DMF und 25 % (w /v ) PVDF-Lösungen mit unterschiedlichen ACE/DMF-Verhältnissen wurden elektrogesponnen.
Elektrogesponnene Fasern von ACE
Aus PVDF/ACE-Lösung bei unterschiedlicher relativer Luftfeuchtigkeit gewonnene Fasern wurden ausgestellt und verglichen (Abb. 1 und 2). Glatte Fasern wurden unter Verwendung einer PVDF/ACE-Lösung bei einer relativen Luftfeuchtigkeit von 5 % gebildet (Abb. 1a und zusätzliche Datei 1:Abbildung S1A), während makroporöse Fasern bei einer relativen Feuchtigkeit von 25 %, 45 % und 65 % hergestellt wurden. (Abb. 1b–d und zusätzliche Datei 1:Abbildung S1B-D). Die Bildung von Oberflächenporen sollte der thermisch induzierten Phasentrennung (TIPS) zugeschrieben werden [24].
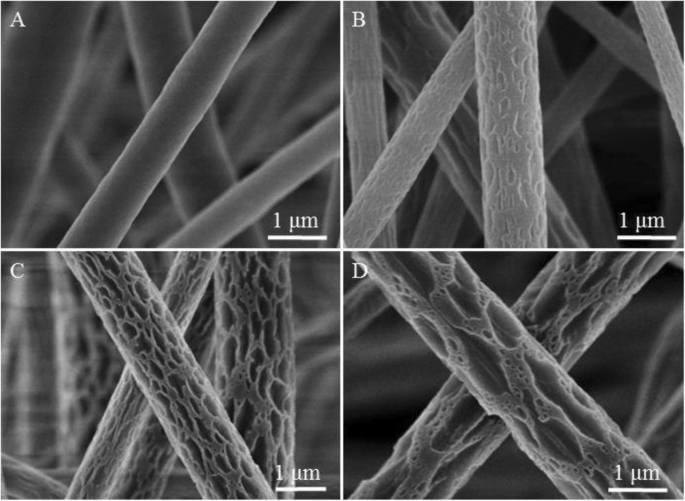
Repräsentative SEM-Bilder von Proben, die durch Elektrospinnen hergestellt wurden 18 % (w /v ) PVDF-Lösung von ACE bei unterschiedlicher relativer Luftfeuchtigkeit. a 5 %, b 25 %, c 45 % und d 65 %
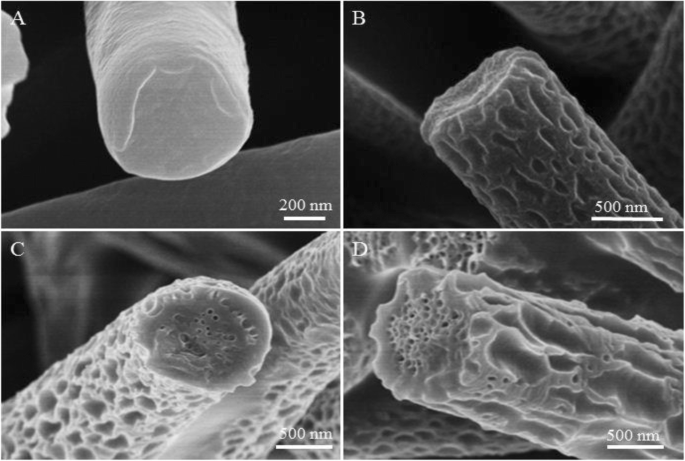
SEM-Querschnittsbilder von Proben, die durch Elektrospinnen hergestellt wurden 15 % (w /v ) PVDF-Lösung von ACE bei unterschiedlicher relativer Luftfeuchtigkeit. a 5 %, b 25 %, c 45 % und d 65 %
Um den Bildungsmechanismus von makroporösen PVDF-Fasern zu bestätigen, die aus PVDF/ACE-Lösung gebildet wurden, überprüften wir den Querschnitt der Fasern, die bei verschiedenen untersuchten relativen Feuchtigkeitsniveaus gebildet wurden. Wir fanden, dass bei einer relativen Luftfeuchtigkeit von 5 % und 25 % die gebildeten Fasern ein festes Inneres aufwiesen (Abb. 2a, b), während Fasern mit inneren Poren bei einer relativen Feuchtigkeit von 45 % und 65 % gebildet wurden (Abb. 2c, D). Somit können wir schlussfolgern, dass Fasern mit einer glatten Oberfläche und einem festen Inneren bei einer relativen Feuchtigkeit von 5% aufgrund der fehlenden Phasentrennung gebildet wurden. Während durch TIPS makroporöse Fasern mit festem Inneren gebildet wurden. Dagegen wurden makroporöse Fasern mit Innenporen bei einer relativen Luftfeuchtigkeit von 45% und 65% aufgrund der Koexistenz von TIPS und dampfinduzierter Phasentrennung (VIPS) gebildet. Mit anderen Worten, wenn die hochflüchtigen Lösungsmittel verdampften, absorbierten sie eine große Menge an Wärme und kühlten somit die Oberfläche der Fasern, was dazu führte, dass sie kondensierten und Wassertröpfchen auf der Faseroberfläche anzogen. Mit zunehmender relativer Luftfeuchtigkeit nahm die Verdunstungsrate der Wassertröpfchen ab, was zu einer Koaleszenz zwischen den Tröpfchen führte, die Makrotröpfchen bildeten, deren Mechanismus als Nukleationswachstum (NG) bekannt ist [34]. Nachdem die kondensierten Makrowassertröpfchen getrocknet waren, bildeten sie Makroporen auf der Oberfläche der Fasern. Wohingegen der Teil der Wassertröpfchen, der die Faser durchdrang, schließlich trocknete, um innere Poren zu bilden. Der Bildungsmechanismus der makroporösen Fasern bei hoher relativer Luftfeuchtigkeit ist in Abb. 3a dargestellt. Bei hoher relativer Luftfeuchtigkeit nahm die Verdampfungsrate der auf der Faseroberfläche kondensierten Wassertröpfchen ab, wodurch diese Tröpfchen aufgrund von NG mehr Zeit zum Verschmelzen hatten. Daher stieg die Größe der Makroporen auf der Oberfläche von Fasern von ~ 50 nm bei einer relativen Luftfeuchtigkeit von 25 % auf ~ 100 nm bei einer relativen Luftfeuchtigkeit von 45 % und auf ~ 400 nm bei einer relativen Luftfeuchtigkeit von 65 %. . Alle Oberflächen und inneren Morphologien, die aus PVDF/ACE-Lösung bei unterschiedlichen relativen Feuchtigkeitswerten erhalten wurden, sind in Tabelle 1 zusammengefasst. Wichtig ist, dass eine Erhöhung der relativen Feuchtigkeit von 5 auf 65 % zu einer Erhöhung des Faserdurchmessers von ~ 0,77 auf ~ 1,81 μm führt (Zusätzlich Datei 1:Abbildung S2A).
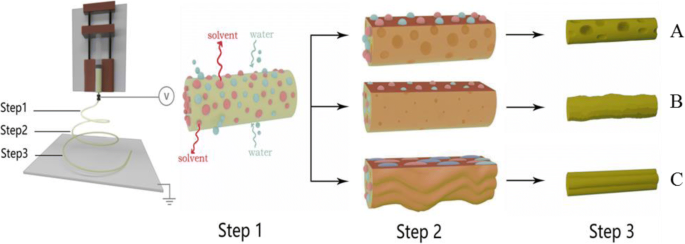
Prozessdiagramme des Lösungsstrahls beim Elektrospinnen bei hoher relativer Luftfeuchtigkeit. Schritt 1:Verdampfung des Lösungsmittels und Wasserkondensation, Schritt 2:Eindringen von Wassertröpfchen und Porenbildung und Schritt 3:Dehnung und Verfestigung der Fasern. a Makroporöse Fasern, b grobe Fasern und c gerillte Fasern
Elektrogesponnene Fasern aus DMF
35 % (w /v ) PVDF-Lösung wurde bei unterschiedlicher relativer Luftfeuchtigkeit (5%, 25%, 45% und 65 %) elektrogesponnen.
Glatte Fasern wurden unter Verwendung einer PVDF/DMF-Lösung bei einer relativen Luftfeuchtigkeit von 5 % hergestellt (Abb. 4a und zusätzliche Datei 1:Abbildung S3A), während raue Fasern bei einer relativen Feuchtigkeit von 25 %, 45 % und 65 % gebildet wurden (Abb . 4b–d und Zusatzdatei 1:Abbildung S3B-D) aufgrund von Knickinstabilität [35] und Dehnung durch elektrische Kraft [26]. Gemäß dem Querschnitt der Fasern, die bei der vorherigen untersuchten relativen Luftfeuchtigkeit gebildet wurden, stellten wir fest, dass Fasern mit festem Inneren nur bei einer relativen Luftfeuchtigkeit von 5 % erhalten wurden (Abb. 5a), während Fasern mit inneren Poren bei einer relativen Luftfeuchtigkeit von . gebildet wurden 25 %, 45 % und 65 % (Abb. 5b–d). In diesem Fall können wir sagen, dass die Fasern ohne Phasentrennung eine glatte Oberfläche und ein festes Inneres bildeten, während Fasern mit einer rauen Oberfläche und inneren Poren aufgrund von VIPS erhalten wurden [24]. Mit anderen Worten, die gemeinsame Diffusion und Penetration von DMF und Wasserdämpfen spielte eine wesentliche Rolle bei der Bildung von Fasern mit Innenporen; Da der Dampfdruck von Wasser (2,34 kPa) höher ist als der von DMF (0,36 kPa) bei einer Temperatur von 20 °C, ist es vernünftig anzunehmen, dass der Wasserdampf den nahegelegenen Bereich der Grenzfläche zwischen der Luft gesättigt hat und der Strahl zuerst, gefolgt von seiner Wirkung als Nichtlösungsmittel, um eine PVDF-Hülle auf der Oberfläche des Flüssigkeitsstrahls auszufällen. Die verfestigte PVDF-Schicht trug dazu bei, das DMF im Inneren zu umgarnen und seine Verdampfungsrate zu verringern, was möglicherweise verhinderte, dass der Wasserdampf schnell kondensiert oder sich auf der Oberfläche zu großen Tröpfchen ansammelt. Der Wasserdampf durchdrang die Hülle und trat ständig in die PVDF-DMF-Phase ein, was zu einer schnellen Phasentrennung führte. Abbildung 3d beleuchtet den Bildungsmechanismus rauer Fasern bei hoher relativer Luftfeuchtigkeit. Alle Oberflächen und inneren Morphologien, die aus PVDF/DMF-Lösung bei unterschiedlichen relativen Feuchtigkeitsniveaus erhalten wurden, sind in Tabelle 1 zusammengefasst. Interessanterweise führt die Erhöhung der relativen Feuchtigkeit von 5 auf 65 % zu einer Erhöhung des Faserdurchmessers von ~ 0,8 auf ~ 1,79 μm (Zusätzliche Datei 1:Abbildung S2B).
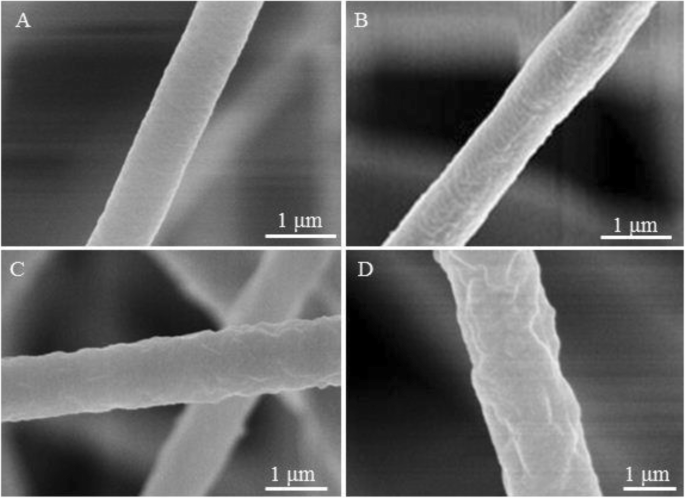
Repräsentative SEM-Bilder von durch Elektrospinnen hergestellten Proben 35 % (w /v ) PVDF-Lösung aus DMF bei unterschiedlicher relativer Luftfeuchtigkeit. a 5 %, b 25 %, c 45 % und d 65 %
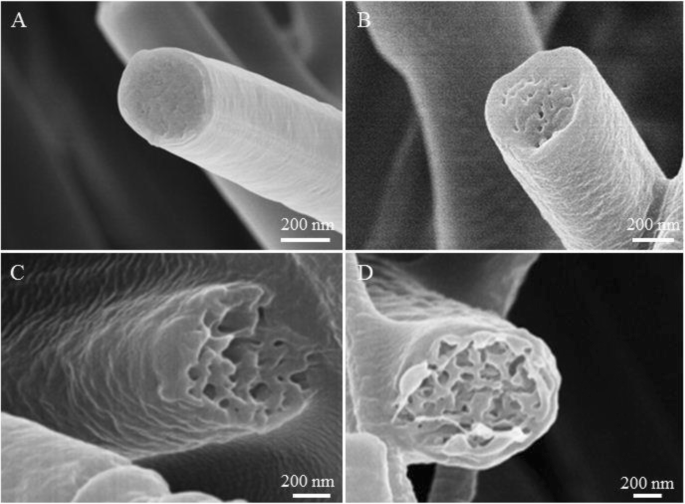
SEM-Querschnittsbilder von durch Elektrospinnen hergestellten Proben 35 % (w /v ) PVDF-Lösung aus DMF bei unterschiedlicher relativer Luftfeuchtigkeit. a 5 %, b 25 %, c 45 % und d 65 %
Fasern, die aus einer ACE/DMF-Mischlösung elektrogesponnen wurden
In diesem Fall 25 % (w /v ) PVDF-Lösungen mit unterschiedlichen ACE/DMF-Verhältnissen (4:1, 2:1, 1:1, 1:2 und 1:4) wurden bei unterschiedlicher relativer Luftfeuchtigkeit elektrogesponnen. Für 25 % (w /v ) (ACE/DMF bei einem Lösungsmittelverhältnis von 4:1), glatte Fasern wurden bei einer relativen Luftfeuchtigkeit von 5 % gebildet (Abb. 6a und zusätzliche Datei 1:Abbildung S4A), säulenflache längsgerillte Fasern wurden bei der relativen Feuchtigkeit hergestellt von 25 % (Abb. 6b und Zusatzdatei 1:Abbildung S4B) und säulenlängsgerillte Fasern wurden bei einer relativen Luftfeuchtigkeit von 45 % und 65 % hergestellt (Abb. 6c, d und Zusatzdatei 1:Abbildung S4C, D). Für 25 % (w /v ) (ACE/DMF bei einem Lösungsmittelverhältnis von 2:1), glatte Fasern wurden bei einer relativen Feuchtigkeit von 5 % gebildet (Abb. 6e und zusätzliche Datei 1:Abbildung S4E), raue Fasern wurden bei einer relativen Feuchtigkeit von 25 % hergestellt (Abb. 6f und Zusatzdatei 1:Abbildung S4F) wurden bei einer relativen Luftfeuchtigkeit von 45 % flache, längsgerichtete, gerillte Fasern erhalten (Abb. 6g und Zusatzdatei 1:Abbildung S4G), und säulenförmige, gerillte Fasern wurden bei der relativen Luftfeuchtigkeit von 65 % (Abb. 6h und Zusatzdatei 1:Abbildung S4H). Für 25 % (w /v ) (ACE/DMF bei einem Lösungsmittelverhältnis von 1:1) bei einer relativen Luftfeuchtigkeit von 5 % wurden glatte Fasern beobachtet (Abb. 6i und zusätzliche Datei 1:Abbildung S4I), raue Fasern wurden bei einer relativen Feuchtigkeit von 25 % erzeugt und 45 % (Abb. 6j, k und zusätzliche Datei 1:Abbildung S4J, K) und kleine gerillte Säulenfasern wurden bei einer relativen Luftfeuchtigkeit von 65 % hergestellt (Abb. 6l und zusätzliche Datei 1:Abbildung S4L). Für 25 % (w /v ) (ACE/DMF bei den Lösungsmittelverhältnissen 1:2 und 1:4), bei einer relativen Luftfeuchtigkeit 25% wurden glatte Fasern gesehen (Abb. 6m, n, q, r und Zusatzdatei 1:Abbildung S4M, N , Q, R), während raue Fasern bei einer relativen Luftfeuchtigkeit von 45 % und 65 % hergestellt wurden (Abb. 6o, p, s, t und zusätzliche Datei 1:Abbildung S4O, P, S, T).
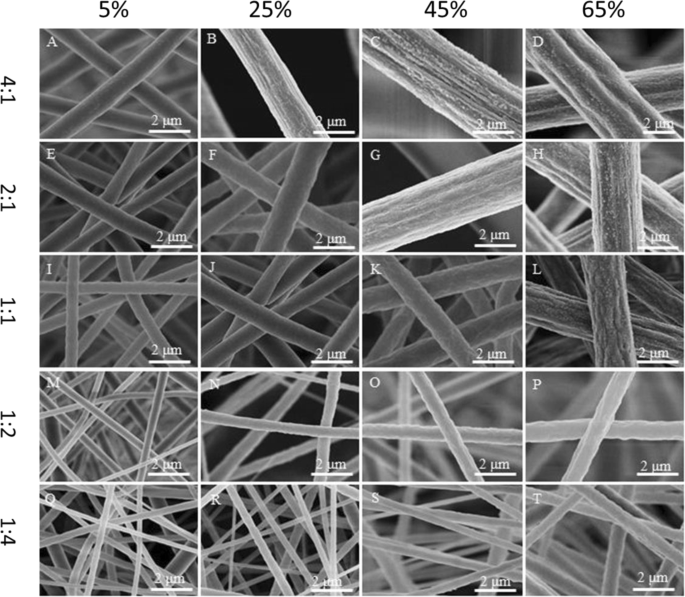
Repräsentative SEM-Bilder von Proben, die durch Elektrospinnen hergestellt wurden 25 % (w /v ) PVDF-Lösungen von ACE/DMF bei unterschiedlichen relativen Feuchtigkeitswerten (5 %, 25 %, 45 % und 65 %) und Lösungsmittelverhältnissen. a –d 4:1, e –h 2:1, ich –l 1:1, m –p 1:2 und q –t 1:4
Um den Bildungsmechanismus der aus ACE/DMF gebildeten gerillten PVDF-Fasern genauer zu bestimmen, überprüften wir den Querschnitt der Fasern, die bei allen Lösungsmittelverhältnissen und verschiedenen untersuchten relativen Feuchtigkeitswerten gebildet wurden. Wir stellten fest, dass bei einer relativen Feuchtigkeit von 5% alle gebildeten Fasern ein festes Inneres hatten. Daraus schließen wir, dass bei der Bildung von Fasern mit glatter Oberfläche und festem Inneren keine Phasentrennung auftrat (Abb. 7a, e, i, m, q). Bei einer relativen Feuchtigkeit von 25 %, 45 % und 65 % wiesen alle hergestellten Fasern Innenporen auf. Gerillte Fasern mit Innenporen wurden durch einen faltenbasierten Dehnungsmechanismus hergestellt [36]. In diesem Fall bildete sich aufgrund der schnellen Verdampfung des hochflüchtigen ACE (Dampfdruck, 24 kPa) und der Phasentrennung im frühen Stadium des Elektrospinnens eine glasige Haut, anschließend bildete sich durch die Bildung die faltige Oberfläche des Strahls der inneren Poren und anschließend zu gerillten Fasern verlängert (Abb. 7b–d, g, h, l). Abbildung 3c erläutert den Bildungsmechanismus der gerillten Fasern bei hoher relativer Luftfeuchtigkeit. Die Bildung von Nanosäulen auf der Oberfläche der gerillten Fasern könnte darauf zurückzuführen sein, dass das ACE in den Fasern durch die glasige Haut eingeschlossen wurde, was einer schnellen Verdunstung von ACE ausgesetzt war, aber es könnten noch einige Schwachstellen vorhanden sein, die zur Bildung von Nanosäulen.
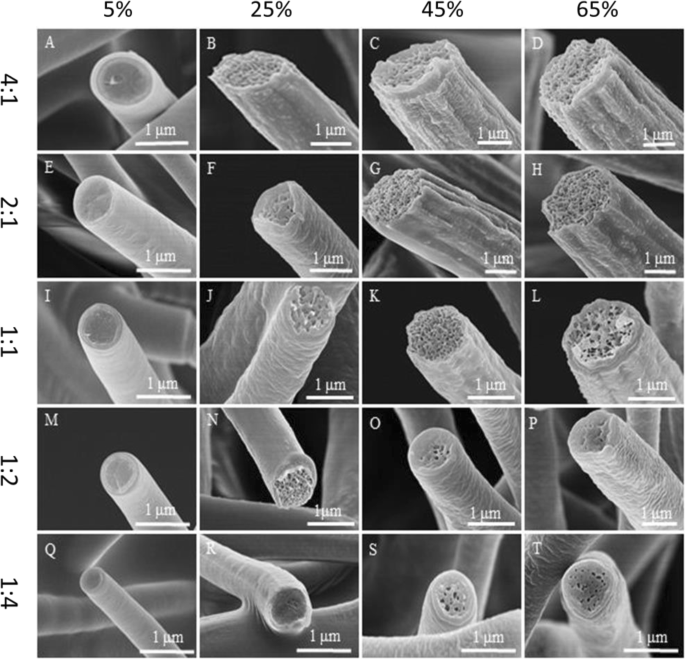
SEM-Querschnittsbilder von Proben, die durch Elektrospinnen hergestellt wurden 25 % (w /v ) PVDF-Lösungen von ACE/DMF bei unterschiedlichen relativen Feuchtigkeitswerten (5 %, 25 %, 45 % und 65 %) und Lösungsmittelverhältnissen. a –d 4:1, e –h 2:1, ich –l 1:1, m –p 1:2 und q –t 1:4
Durch VIPS wurden Fasern mit rauen Oberflächen und inneren Poren gebildet (Abb. 7f, j, k, o, p, s, t). Durch VIPS wurden auch Fasern mit glatten Oberflächen und inneren Poren gebildet (Abb. 7n, r) [24, 37]. Erwähnenswert ist, dass die Breite und Tiefe der Rillen durch die Erhöhung der relativen Luftfeuchtigkeit zunehmen. Alle Oberflächen und inneren Morphologien, die aus einer ACE/DMF-Mischlösung bei unterschiedlichen relativen Luftfeuchtigkeitswerten erhalten wurden, sind in Tabelle 1 zusammengefasst. Wir haben festgestellt, dass eine Erhöhung der relativen Luftfeuchtigkeit von 5 auf 65 % zu einer Erhöhung des Faserdurchmessers von ~ 1 auf ~ 3,75 μm . führt , ~ 0,85 bis ~ 2,9 μm, ~ 0,6 bis ~ 2 μm, ~ 0,35 bis ~ 1 μm und ~ 0,26 bis ~ 0,7 μm für die folgenden Lösungsmittelverhältnisse von 4:1, 2:1, 1:1, 1:2 , bzw. 1:4 (zusätzliche Datei 1:Abbildung S2C-G).
Aufgrund der Bedeutung der hohen relativen Luftfeuchtigkeit bei der Bildung sekundärer Oberflächenstrukturen der PVDF-Fasern haben wir das Phasenverhalten von Elektrospinnlösungen durch die Erstellung eines Phasendiagramms bei einer relativen Luftfeuchtigkeit von 65 % veranschaulicht (Abb. 8). Das Diagramm ist durch eine binodale Kurve in zwei Zonen unterteilt. Der Lösungsstrahl ist beim Extrudieren aus der Spinndüse (Zone I) wolkenlos und homogen. Mit der hohen Verflüchtigungsrate von ACE, der geringen Verflüchtigungsrate von DMF und der anschließenden Permeation von Wasser in den Lösungsstrahl wird der Anteil der Komponenten (PVDF, Lösungsmittel (s) und Wasser) im Strahl dynamisch verändert, um dem Weg zu folgen durch die Pfeile angezeigt. Der Lösungsstrahl beginnt nach dem Durchqueren der bimodalen Kurve in Zone II einzudringen, wo er trüb wird und sich aufgrund der thermodynamischen Instabilität in mehrphasig auftrennt [37, 38]. Ein höher flüchtiges Lösungsmittel (ACE) wird durch einen steileren Pfeil dargestellt, was einer schnelleren Phasentrennung entspricht.
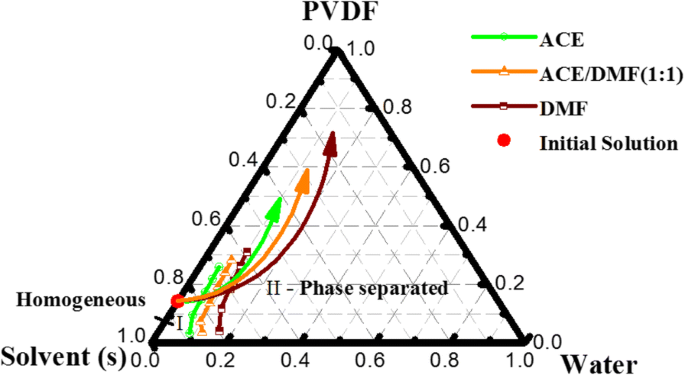
Phasendiagramm von PVDF, Lösungsmittel(n) und Wasser bei einer relativen Luftfeuchtigkeit von 65%. Der rote Punkt bezieht sich auf die Ausgangslösung
Um die Oberfläche und Porenstruktur der Fasern zu quantifizieren, wurden die Stickstoffadsorptionsisothermen der makroporösen Fasern (Abb. 1d), rauen Fasern (Abb. 4d) und gerillten Fasern (Abb. 6l) mit ähnlichen Durchmessern zum Vergleich gewählt. Die spezifischen Oberflächen der makroporösen, gerillten und rauen Fasern betrugen 23,31 ± 4,30 m 2 . /g, 10,26 ± 2,19 m 2 /g und 4,81 ± 0,58 m 2 /g und die Porenvolumina betrugen 0,0695 ± 0,007 cm 3 /g, 0,0182 ± 0,003 cm 3 /g und 0,0135 ± 0,002 cm 3 /g (Abb. 9a). Diese Ergebnisse stimmten mit der maximalen Stickstoffadsorption der makroporösen, gerillten und rauen Fasern überein, die 20,06 cm 3 . betrug /g, 12,29 cm 3 /g und 7,49 cm 3 /g bzw. (Abb. 9b). Wir bestätigten weiter, dass Mesoporen (2–50 nm) in den makroporösen, gerillten und rauen Fasern existierten (Abb. 9c), während Makroporen (> 100 nm) nur in den makroporösen Fasern auftraten, was zu ihrer hohe spezifische Oberfläche und Porenvolumen (Abb. 9d).
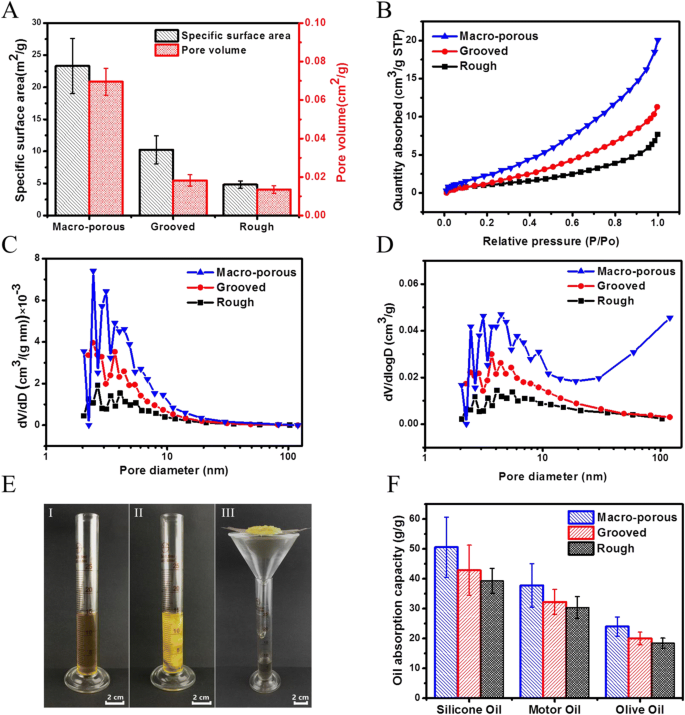
Charakterisierung der makroporösen, gerillten und rauen Fasern. a Spezifische Oberfläche und Porenvolumen. b Die Stickstoffadsorptionsisothermen. c dV/dD – Porendurchmesser-Kurve. d dV/dlogD – Porendurchmesserkurve. e Bilder der Ölaufnahme. (I) 15 ml Wasser-Öl-Gemisch (1:1) ohne Sorptionsmittel, (II) während der Absorption, (III) während der Entwässerung. f Ölaufnahmekapazitäten
Da PVDF ein hydrophobes, aber kein oleophobes Material ist, können die PVDF-Sorbentien Öl absorbieren und gleichzeitig Wasser abstoßen. Als nächstes demonstrierten wir die Anwendung der makroporösen, gerillten und rauen Fasern zur Ölabsorption (Abb. 9e). Drei typische Öle (Silikonöl, Motoröl und Olivenöl) wurden ausgewählt, um die verschiedenen Proben zu überprüfen.
Die typischen Eigenschaften dieser Öle sind in Tabelle 2 aufgeführt. Wie erwartet zeigten die makroporösen Fasern unter den drei Arten von Ölabsorptionsmaterialien die höchste Ölabsorptionskapazität von 50,58 ± 5,47 g/g, 37,74 ± 4,33 g/g, und 23,96 ± 2,68 g/g für Silikonöl, Motorenöl bzw. Olivenöl (Abb. 9f). Insbesondere zeigten die makroporösen Fasern das 1,18-, 1,17- bzw. 1,19-fache Ölabsorptionsvermögen der gerillten Fasern für Silikonöl, Motoröl bzw. Olivenöl. Darüber hinaus zeigten die makroporösen Fasern das 1,29-, 1,24- bzw. 1,26-fache Ölabsorptionsvermögen der rauen Fasern für Silikonöl, Motoröl bzw. Olivenöl. Diese Ergebnisse sind darauf zurückzuführen, dass von allen Proben die makroporösen Fasern die größte Oberfläche aufweisen, während die rauen Fasern die geringste Oberfläche aufweisen. Von den drei untersuchten Ölsorten zeigten alle getesteten Proben die beste Aufnahmekapazität für Silikonöl, möglicherweise aufgrund der höheren Viskosität des Silikonöls.
Schlussfolgerungen
Wir haben eine geeignete und zuverlässige Methode zur Bildung von makroporösen, rauen und gerillten PVDF-Nanofasern mit inneren Poren demonstriert. Um den Mechanismus zu verstehen, der für die Bildung von PVDF-Fasern verantwortlich ist, haben wir drei Lösungsmittelsysteme (dh ACE, DMF und ACE-DMF-Gemisch) bei unterschiedlicher relativer Luftfeuchtigkeit (5 %, 25 %, 45 % und 65 °C) getestet %). Wir stellten fest, dass bei der relativen Luftfeuchtigkeit von 5% bei Verwendung der bisherigen Lösungsmittel keine Phasentrennung auftrat, was zur Bildung glatter Fasern mit einem festen Inneren führte. Wir fanden, dass die Bildung von Makroporen auf der Oberfläche der Fasern mit festem Inneren bei einer relativen Feuchtigkeit von 25 % aufgrund des hohen Dampfdrucks von ACE und des Keimbildungsmechanismus auf TIPS zurückgeführt werden sollte, während die Bildung von Makroporen auf die Faseroberfläche mit Innenporen bei einer relativen Luftfeuchtigkeit von 45% und 65% sollte auf die Koexistenz von TIPS- und VIPS-Mechanismen zurückgeführt werden. Darüber hinaus haben wir festgestellt, dass der niedrige Dampfdruck von DMF eine zentrale Rolle bei der Herstellung der rauen Fasern mit Poren im Inneren durch VIPS spielte. Während der faltenbasierte Dehnungsmechanismus eine Schlüsselrolle bei der Herstellung der gerillten Fasern mit einer porösen Innenstruktur spielte. Die makroporösen Fasern (> 300 nm) zeigten die höchste Ölabsorptionsleistung von 50,58 ± 5,47 g/g, 37,74 ± 4,33 g/g und 23,96 ± 2,68 g/g für Silikonöl, Motoröl und Olivenöl. bzw. Wichtig ist, dass unser Verständnis der Mechanismen, die für die Bildung der makroporösen, rauen und gerillten PVDF-Fasern mit innerer Porosität verantwortlich sind, als wichtige Referenz für die Herstellung elektrogesponnener Fasern durch Regulierung des Lösungsmittels und der relativen Luftfeuchtigkeit dienen kann.
Abkürzungen
- ACE:
-
Aceton
- DMF:
-
N,N-Dimethylformamid
- PVDF:
-
Polyvinylidenfluorid
- TIPPS:
-
Thermisch induzierte Phasentrennung
- VIPS:
-
Dampfinduzierte Phasentrennung
Nanomaterialien
- Nanofasern und Filamente für eine verbesserte Wirkstoffabgabe
- Kohlefaserproduktion und Kohlefaserteile:Was sind die Grundlagen?
- Enthüllung der atomaren und elektronischen Struktur von gestapelten Kohlenstoff-Nanofasern
- Die antibakteriellen hierarchischen Polyamid-6-ZnO-Nanofasern, hergestellt durch Atomlagenabscheidung und hydrothermales Wachstum
- Auswirkung einer In-situ-Annealing-Behandlung auf die Mobilität und Morphologie von TIPS-Pentacen-basierten organischen Feldeffekttransistoren
- Bildung und Lumineszenzeigenschaften von Al2O3:SiOC-Nanokompositen auf der Basis von durch Phenyltrimethoxysilan modifizierten Aluminiumoxid-Nanopartikeln
- Abstimmung der Oberflächenmorphologien und -eigenschaften von ZnO-Filmen durch das Design der Grenzflächenschicht
- Elektrospinnen auf isolierende Substrate durch Kontrolle der Oberflächenbenetzbarkeit und -feuchtigkeit
- Die Kopplungseffekte von Oberflächenplasmonpolaritonen und magnetischen Dipolresonanzen in Metamaterialien
- Informieren Sie sich über die Vorteile des Flach- und Rundschleifens im eigenen Haus