Stratasys, Champion Motorsport-Team testet 3D-gedruckte Kerntechnologie
Am 27. Juni belegte ein modifizierter 911 Porsche GT2 RS Clubsport von Champion Motorsport (Pompano Beach, Florida, USA) den ersten Platz in der Time Attack 1 Division des 99 . Pikes Peak International Hill Climb in Colorado Springs, Colorado, USA
Eines der Erfolgsgeheimnisse des Teams waren die aerodynamischen Strukturen des Autos – die Kotflügel, Unterbodenstreben, der Diffusor und andere Komponenten des Fahrzeugs, die die Luft beim Fahren effizienter um das Fahrzeug herum bewegen. Viele dieser Komponenten wurden vom Partner Stratasys (Rehovet, Israel und Eden Prairie, Minnesota, USA) in 3D gedruckt, einschließlich der erfolgreichen ersten Anwendung für eine neue werkzeuglose, mit Kohlefaser umwickelte Sandwichkerntechnologie.
Erprobung von 3D-gedruckten Werkzeugen und Kerntechnologien
Champion Motorsport ist seit mehreren Jahren Kunde von Stratasys, „aber die Partnerschaft hat sich zu mehr als einer typischen Lieferanten-Kunden-Beziehung entwickelt“, sagt Allen Kreemer, leitender strategischer Anwendungsingenieur bei Stratasys. Stratasys und Champion haben beispielsweise zuvor zusammengearbeitet, um eine neue Technik zu testen, die Stratasys für den 3D-Druck von löslichen Werkzeugen entwickelt hatte. Bei dieser Technologie wird ein löslicher Kunststoffkern in Form eines Kanals oder eines anderen schlauchförmigen Teils bedruckt und anschließend mit Kohlefaser-Prepreg umwickelt. Unter Verwendung eines Tanks zur Entfernung von löslichem Support löst sich das gedruckte Werkzeug auf und hinterlässt ein nahtloses, fertiges, hohles Verbundrohr.
„Das war wirklich der Beginn unserer Partnerschaft mit Champion Motorsport, bei der wir zusammengearbeitet haben, um diesen sehr komplizierten, nahtlosen Kohlefaserkanal auf unkonventionelle Weise ohne Grenzen wie bei der CNC-Bearbeitung oder beim Formen zu schaffen“, sagt Patrick Carey, Senior VP – Amerika, Produkte und Lösungen bei Stratasys.
Im Jahr 2019 beschlossen die Unternehmen, an einem Projekt zusammenzuarbeiten, um eine neue Iteration derselben Technologie zu testen:einen 3D-gedruckten, mit Kohlefasern umwickelten Kern, der nicht ist in Wasser auflösen, das ist stattdessen ein struktureller Kern für das fertige Teil oder den Prototyp.
Kreemer erklärt, dass die Bearbeitung und Formgebung von Kernmaterialien bei Sandwichbauteilen – ob flexible Aluminiumwaben, starrer Strukturschaum oder etwas anderes – schwierig und teuer sein kann. Stratasys druckt einen starren Wabenkern aus dem Hochtemperaturkunststoff SABIC (Riyadh, Saudi-Arabien) Ultem 1010. „Wir drucken die exakte Form, die auf das Auto passt, dann einfach mit Kohlefaser umwickeln, einsacken und aushärten, ohne eine Form zu verwenden“, sagt Kreemer. „Wir haben mit löslichen Kernen angefangen, die unsere Kunden immer noch verwenden, und sind jetzt auf diese Sandwich-Kerne umgestiegen, die breite Anwendungen in der Luft- und Raumfahrt und in der Automobilindustrie haben werden.“
„Wir nennen es ‚werkzeuglos‘, und das ist wirklich der Schlüssel“, fügt Carey hinzu. „Wir haben diese Anwendung erstellt, um den gesamten Prozess des Bauens der Form und des anschließenden Einlegens in die Form zu überspringen.“ Er merkt an, dass durch den Wegfall von Werkzeugen auch die Form nach Bedarf leicht geändert werden kann.
3D-gedruckte, preisgekrönte Aerodynamik
Für das Champion Motorsport-Projekt flossen drei verschiedene Technologien in die insgesamt 16 aerodynamischen Teile ein, die Stratasys entweder für das Prototyping oder die endgültige Installation am Rennfahrzeug gebaut hat, erklärt Carey. „Wir druckten die Ultem 1010-Kerne [mit Kohlefaser umwickelt], wir druckten einige Teile in 3D mit kohlenstofffasergefülltem Nylon 12 und wir druckten Teile mit Nylon 6, wenn Flexibilität und Schlagfestigkeit erforderlich waren.“
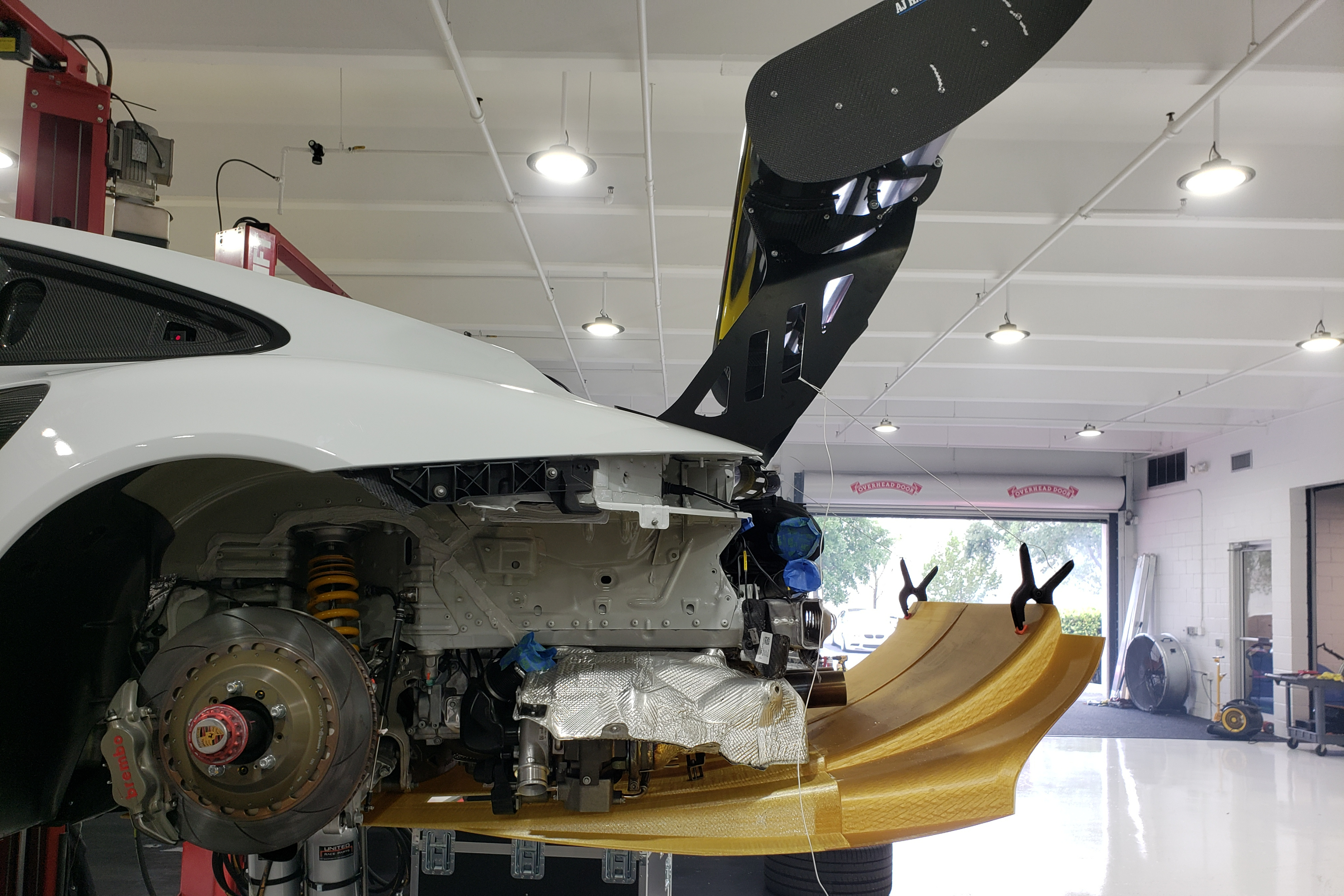
Das größte Teil war ein 7 Fuß langer, 5 Fuß breiter Heckdiffusor-Prototypteil, der zum Testen des endgültigen Teiledesigns gebaut wurde. Es wurde in sieben Teilen auf einem F900 Fused Deposition Modeling (FDM) Stratasys Drucker unter Verwendung von Ultem 1010 Polyetherimid (PEI) Polymer gedruckt, miteinander verbunden, in Kohlefaser-Prepreg gewickelt, verpackt und im Ofen gehärtet. Die Durchlaufzeit für das Teil betrug etwa fünf Tage für den Druck und etwas mehr als 24 Stunden für das Auflegen und Aushärten:„Es war extrem schnell und das, was wir damals brauchten“, sagt Chris Lyew, Maschinenbauingenieur bei Champion Motorsport.
Aufgrund der Unsicherheit, ob in diesem Sommer aufgrund von COVID-19 persönliche Veranstaltungen durchgeführt werden können, „ging das Projekt in letzter Minute online, und viele Systeme mussten gleichzeitig angegangen werden“, erklärt Lyew. „Aerodynamik ist eine davon, und es ist normalerweise ein sehr zeitaufwändiger Prozess“, die Komponenten zu entwerfen, zu testen und zu iterieren, sagt er. Herkömmliche Verfahren würden die Herstellung von Werkzeugen, das Auflegen von Hand auf die Form und das Schneiden und Einpassen des Kerns erfordern. „Ohne diesen Prozess hätten wir unsere Terminvorgaben für den Test des Autos auf der Strecke nicht einhalten können“, sagt Lyew.
Der Frontsplitter des Autos wurde ebenfalls prototypisiert und auf ähnliche Weise getestet. Für die Prototypenteile wurden die endgültigen Produktionsteile mit herkömmlichen Werkzeugen hergestellt, aber das Prototypenteil wurde als Muster zum Testen verschiedener Iterationen verwendet. Carey bemerkt:„Mit einem werkzeuglosen Prozess können wir schneller iterieren, testen, dann schneller iterieren und testen. Mit herkömmlichen Tools könnten Sie nie iterieren, Sie erstellen einfach eins und bleiben dabei stecken. Hier können wir ein echtes Teil herstellen, testen und daraus lernen.“
Auch eine Reihe kleinerer Produktionsteile wurden von Stratasys hergestellt. Zum Beispiel wurden die Winglets auf beiden Seiten der vorderen Stoßstange des Autos aus 35 % kohlefasergefülltem Nylon 12 gedruckt, die Seitenschweller des Fahrzeugs wurden ebenfalls in Ultem 1010 mit einer Wabeninnenfüllung gedruckt und dann mit Kohlefaser umwickelt.
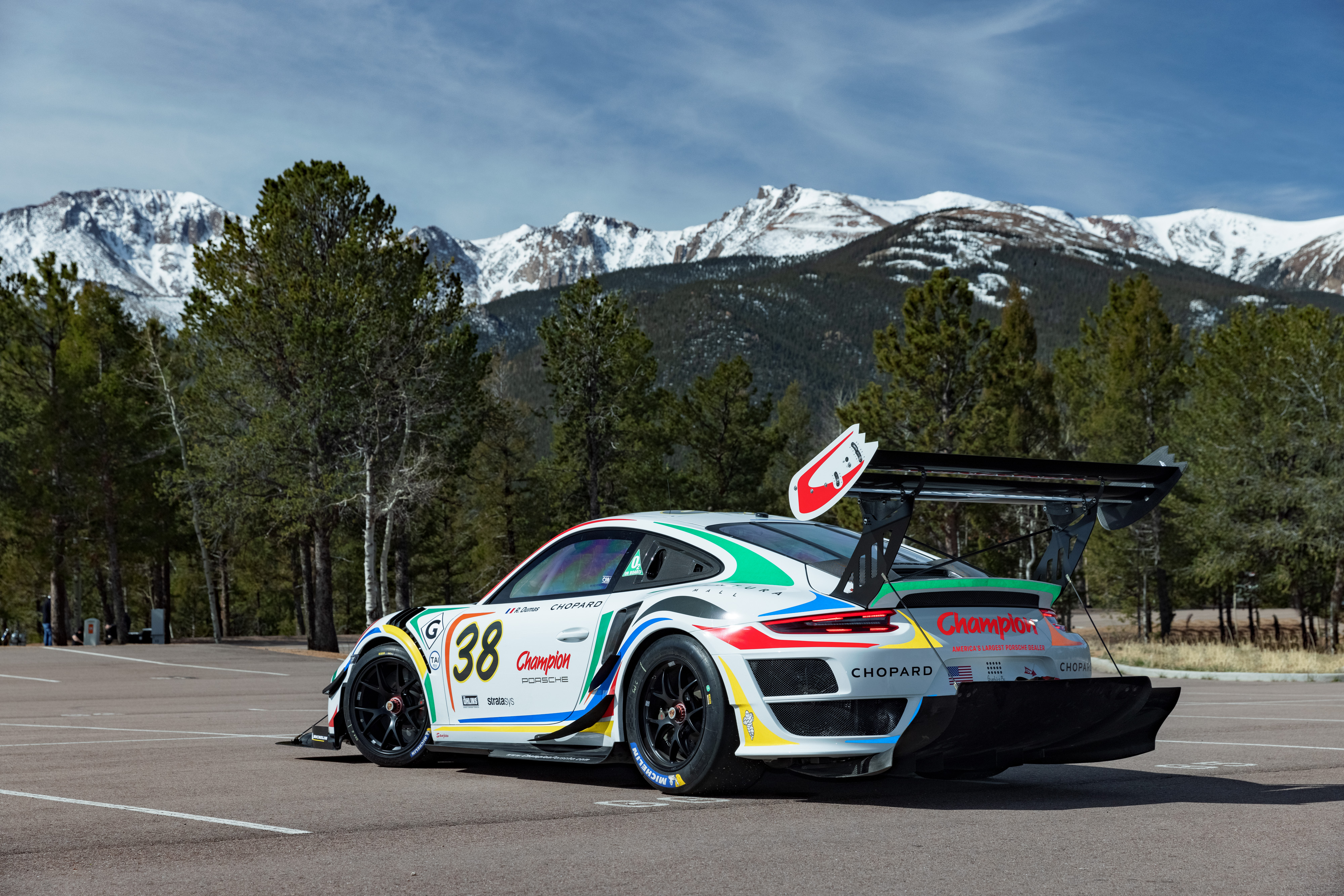
Viele der aerodynamischen „Strakes“ des Autos – kleine flossenähnliche Teile, die an strategischen Punkten an der Außenseite des Fahrzeugs angeschraubt werden, um die Luftzirkulation um das Fahrzeug herum zu kontrollieren – wurden ebenfalls entweder aus kohlefasergefülltem Nylon 12 oder unverstärktem Nylon 6 gedruckt Teile sind so konzipiert, dass sie bei Bedarf aufgrund von Beschädigung oder Verschleiß leicht neu konstruiert oder ausgetauscht werden können. „Am Pikes Peak gibt es eine ganze Reihe unwegsamer Geländemerkmale, die potenziell zu Schäden führen könnten, daher war die Möglichkeit, [die Strakes] einfach auszutauschen, für uns entscheidend“, fügt Lyew hinzu. Es wurden auch mehrere Ersatzsets gedruckt und geliefert, um sie bei Bedarf während des Rennens einfach austauschen zu können.
Jenseits des Pikes Peak
Pikes Peak war ein ideales Rennen, um diese Technologie zu testen, sagt Kreemer aufgrund der einzigartigen Umgebung, die für diese Veranstaltung spezifisch ist, die auf 14.000 Fuß Höhe am höchsten Punkt stattfindet. „Alle Rennwagen verwenden Abtrieb, um das Auto auf die Strecke zu drücken, um Traktion zu gewinnen, aber diese speziellen Autos auf dem Pikes Peak sind anders als alle anderen Motorsportarten der Welt, weil sie wirklich übertriebene aerodynamische Effekte benötigen, um die Autos auf der Strecke zu halten [ in dieser Höhe].“ Das Ergebnis sind größere Flügel und andere aerodynamische Komponenten als bei jedem anderen Rennwagentyp.
In Zukunft plant Stratasys, seine werkzeuglose Printed-Core-Technologie anderen Rennsportunternehmen für ähnliche aerodynamische Teile vorzustellen. Carey sagt, dass es in Zukunft auch viele andere potenzielle Anwendungen in Kleinserien-Automobil-, Freizeitschifffahrts- oder sogar Innenraum-Luftfahrtteilen gibt. „Wir glauben, dass wir bei jeder Anwendung, die eine Iteration oder ein benutzerdefiniertes Design erfordert, einen Mehrwert schaffen können“, sagt er.
Harz
- Materials:Lightweight Honeycomb Production Technology auf der K 2019
- Evonik gründet neues 3D-Druck-Technologiezentrum in den USA
- Neue Form von 3D-gedrucktem Material für leichtere, sicherere Fahrzeugdesigns und mehr
- So gewährleisten Sie die Sicherheit modernster ADAS-Technologie
- EconCore Produktionstechnologie für thermoplastische Wabenplatten
- Verbundwerkstoff + Metall:Hybridtechnologie mit Hohlprofil
- Ein hochspezialisierter Spieler in einem Weltklasse-Team
- Linearbewegungstechnologie
- Arno Strotgen
- Leiterplatte 101