Thermoplastische Bänder verstärkt mit textilbasierter PAN-Kohlefaser
Eine seit langem bestehende Herausforderung in der fortschrittlichen Verbundwerkstoffindustrie besteht darin, Wege zu finden, um kostengünstigere Kohlefasern herzustellen, damit alle Industrien, die diese wertvolle und wirksame Verbundwerkstoffverstärkung verwenden möchten, diese nutzen können. Die Kosten für Kohlefasern sind dank jahrzehntelanger Arbeit zur Steigerung der Produktivität durch Vorläuferchemie, Maschineninnovationen, Prozessverbesserungen und mehr erheblich gesunken.
Ein vielversprechender Bereich ist die Verwendung alternativer Vorstufen zu konventionellem Polyacrylnitril (PAN) in Luft- und Raumfahrtqualität. Beispielsweise haben das US-Energieministerium (DOE, Washington, DC, USA) und das Oak Ridge National Laboratory (ORNL, Oak Ridge, Tennessee, USA) Verfahren zur Herstellung von Kohlefasern aus alternativen Vorläufern entwickelt, die von Polymeren bis hin zu Lignin reichen , zu Kohle.
Alternative Vorläufer
Einer der vielversprechendsten dieser Vorläufer und der, der der Kommerzialisierung am nächsten kommt, ist PAN auf Textilbasis, das der Faser ähnelt, die zur Herstellung von Acrylpullovern verwendet wird. Wie andere alternative Vorstufen, die ORNL untersucht hat, unterscheidet sich die textilbasierte PAN-Kohlefaser (TCF) in vielerlei Hinsicht von der speziellen PAN-Kohlefaser für die Luft- und Raumfahrt.
Einer der Unterschiede besteht darin, dass die textilbasierte PAN-Vorstufe, da sie für den Einsatz in der Textilindustrie bestimmt ist (denken Sie an Vorhänge, Kleidung, Möbelstoffe), in einem Wide-Tow-Format geliefert wird, das von Natur aus kostengünstiger ist als spezielle Luft- und Raumfahrtqualität PAN-Vorstufe. Dies hat bei der Carbonfaser-Produktion den Effekt, den Durchsatz zu erhöhen und die Umwandlungskosten im Vergleich zu herkömmlichen PAN-Fasern zu senken. Es neigt auch dazu, viel größere Schleppfasern zu produzieren – in der Größenordnung von 300.000 bis 450.000 auf der Linie in der Carbon Fiber Technology Facility von ORNL im Vergleich zu 3K bis 50.000, die für herkömmliche PAN-Kohlenstofffasern typisch sind. Obwohl die Verarbeitung der TCF-Vorstufe länger dauert, da sie keine Reaktionsbeschleuniger wie herkömmliches PAN enthält und typischerweise bei niedrigeren Temperaturen betrieben wird (eine Funktion der Notwendigkeit, Verweilzeit und Temperatur auszugleichen), ist die Tatsache, dass so viel mehr Fasern zu einem bestimmten Zeitpunkt verarbeitet werden kann und der geringere Energieverbrauch auf Gewichts- oder Volumenbasis hilft, Kosten zu senken. Tatsächlich schätzt ORNL, dass insgesamt ~60% Energieeinsparungen durch die Faserumwandlung und ~50% Kosteneinsparungen möglich sind.
Dies wiederum bietet die Möglichkeit, in ungewöhnlich großen Mengen kostengünstigere Fasern herzustellen und daraus Produkte mit einem geringeren CO2-Fußabdruck herzustellen. In Branchen wie Automobil/Landverkehr, Unterhaltungselektronik, Sportartikel, Bau/Bau und Windenergie ist TCF eine attraktive Verstärkung, da Anwendungen im Vergleich zu festigkeitsorientierten Anwendungen in der Luft- und Raumfahrt eher steifigkeitsgetrieben sind. Insbesondere Nicht-Luft- und Raumfahrtindustrien könnten potenziell viele Fasern verbrauchen.
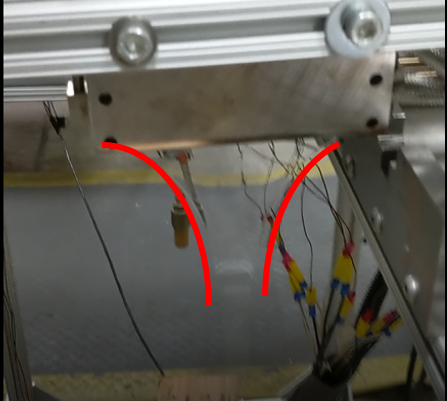
TCF ist jedoch immer noch ein anderes Produkt als herkömmliche PAN-Kohlenstofffasern, sodass nicht nur daran gearbeitet werden muss, diese Faser besser zu charakterisieren, sondern auch Möglichkeiten zu ihrer Verarbeitung und Verwendung zu finden. Da es in einem ultrabreiten Kabel verarbeitet werden kann, erfordert dieser Precursor während des gesamten Faserherstellungsprozesses Modifikationen der Prozessausrüstung. Es ändert auch die Oberflächenmodifikation und Verpackung nach der Produktion und wirkt sich natürlich auf die Verarbeitungsprozesse aus, die von der Herstellung von Bändern und Geweben bis hin zu Prepregs und Preforms reichen.
Das Institute for Advanced Composites Manufacturing Innovation (IACMI, Knoxville , Tenn., USA) hat in den letzten drei Jahren an einer Reihe von von Mitgliedern unterstützten Forschungsprojekten gearbeitet, um diese Probleme anzugehen. Ein interessantes Projekt hat Möglichkeiten untersucht, das ultrabreite Schleppband TCF in thermoplastische Verbundbänder umzuwandeln.
Kosten senken
Das Interesse an thermoplastischen Verbundbändern hat in vielen Branchen zugenommen, aber diese Produkte sind in der Regel teuer, da spezielle Ausrüstung und Know-how erforderlich sind, um jede Faser erfolgreich mit vorpolymerisierten, hochmolekularen und hochviskosen thermoplastischen Harzen zu imprägnieren ihre nicht umgesetzten, niedrigviskosen duroplastischen Gegenstücke. Es ist nur allzu einfach, Bänder mit vielen Hohlräumen und schlechter Faserbenetzung zu produzieren, die mit Endteilen enden, die nicht nur schrecklich aussehen, sondern auch die Gefahr eines vorzeitigen Ausfalls bergen.
Dr. Uday Vaidya, Professor und Direktor des Lehrstuhls für Advanced Composites Manufacturing, University of Tennessee-Knoxville (UTK, Knoxville, Tennessee, USA) und Chief Technology Officer (CTO) von IACMI, arbeitet seit Anfang der 2000er Jahre mit George . an Programmen für thermoplastische Verbundwerkstoffe Husman, Präsident von Husman Consulting Inc. (Cape Coral, Florida, USA) und pensionierter Direktor und CTO von Zoltek Co. Inc. (St. Louis, Missouri, USA). Ihre vielfältigen Wechselwirkungen führten zur Idee der Inline-Imprägnierung konventioneller Heavy-Tow-Carbonfasern (24K bis 50K) zur Herstellung von thermoplastischen Verbundbändern am Ende der Faserproduktionslinie. Die Herstellung von Tapes unmittelbar nach der Faserherstellung würde einen separaten Zwischenschritt und den damit verbundenen Versand und Umschlag eliminieren. Es ist zu hoffen, dass dies dazu beiträgt, die Kosten für Bänder und Teile, die aus diesen Bändern hergestellt werden, zu senken.
Die Verwirklichung dieses Konzepts erforderte eine Entwicklung sowohl des Verfahrens als auch der Ausrüstung, um kohlenstofffaserverstärkte thermoplastische Bänder in verschiedenen Kabelgrößen herzustellen. Vaidya und Husman haben 2018 gemeinsam mit der University of Tennessee Research Foundation (UTRF, Knoxville, Tennessee, USA) ein vorläufiges Patent für ein Verfahren zur Inline-Produktion von thermoplastischen Bändern, die mit bis zu 50.000 Tow-Carbonfasern verstärkt sind, angemeldet. Im folgenden Jahr erweiterten Vaidya und sein UTK-Team diese Arbeit um die thermoplastische Imprägnierung von Ultrabreitband-TCF (300K bis 450K Tow) mit einer zweiten Einreichung.
TCF TP-Bänder
An technischen Herausforderungen hat es dabei erwartungsgemäß nicht gemangelt. Die Faserzufuhr und -handhabung erforderten eine erhebliche Modifikation der Ausrüstung, da TCF dazu neigt, breiter zu sein und mehr Filamente als herkömmliche Kohlefasern zu umfassen. Es ist auch anfällig für Kettenfahrverhalten während des Faserimprägnierungsschritts bei der Bandherstellung. Das bedeutet, dass sich beim Zuführen der Kabel in die Imprägnierdüse eine sinusförmige Welle bildet, die dazu führt, dass die Kabel ungleichmäßig gespalten werden und unter unterschiedlichen Spannungen in die Düse eintreten, was zu Bändern führt, die sich verdrehen, verformen und eine schlechte Faserbenetzung erzielen.
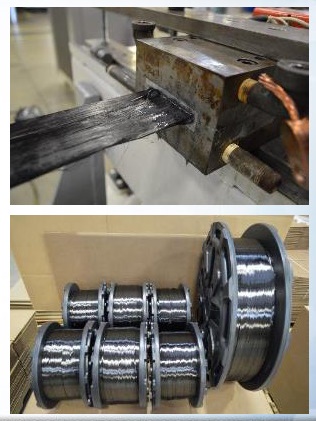
„Einen Weg zu finden, ein Gleichgewicht zwischen Faserspannung und Flexibilität zu finden, erwies sich als wirklich herausfordernd und erforderte viel Arbeit“, erklärt Vaidya. „Unser Team hat erkannt, wie wichtig es ist, die Kabelintegrität zu wahren, um die Filamente zu verteilen und ein hohes Maß an Benetzung zu erreichen, was natürlich entscheidend für die Herstellung von Qualitätsbändern ist.“
Dann war da noch das Größenproblem. TCF-Tow-Bänder sind stark beleimt, damit die Fasern reibungslos vom Spulengatter zur Imprägnierdüse gelangen, wo sie mit Harz benetzt werden, um Band herzustellen. An der Düse angekommen, hatten jedoch frühere Untersuchungen gezeigt, dass zur Erzielung einer guten Benetzung mit thermoplastischen Kunststoffen mit höherer Viskosität das Vorhandensein von Schlichte tatsächlich die Imprägnierung behinderte, was es sehr wünschenswert macht, die Schlichte zu entfernen. Versuch und Irrtum führten schließlich dazu, dass das Team eine Technik zum Abbrennen des Schlichtens entwickelte, kurz bevor die Kabel in die Imprägnierdüse gelangten.
Um die Harzrheologie und die Polymerzufuhr durch die Imprägnierdüse genau vorherzusagen und ein gutes Klebeband herzustellen, waren neue Simulations- und Validierungsarbeiten erforderlich. Das Team konzentrierte sich auf die Herstellung von TCF-Bändern mit Polypropylen (PP) sowie Polyamid 6 (PA6) – zwei Thermoplasten, die aufgrund ihrer Zähigkeit und Erschwinglichkeit in der Automobilindustrie weit verbreitet sind. Das Team verwendete die PolyXtrue-Extrusionsdüsendesign-Software von Plastic Flow LLC (Hancock, Michigan, USA), die auf dem Williams-Landel-Ferry (WLF)-Modell basiert und eine ausgezeichnete Korrelation mit gemessenen Rheologie- und Scherratenergebnissen lieferte.
Das Design selbst war ein weiterer wichtiger Forschungsbereich, insbesondere als das Team von standardmäßigen 12K- auf 50.000-Tows und dann auf Ultrabreitband-TCF-Tows umstieg. Damals musste das Werkzeug komplett neu konstruiert und ein zweistufiger Prozess angepasst werden. In der ersten Stufe wird die Faser imprägniert; in der zweiten Stufe werden optimierte Bruchwinkel für die Spann-/Imprägnierstifte – die die Zugspannung der Kohlefaser, den Fasergewichtsanteil (FWF) sowie die Qualitätskontrolle steuern – eingestellt, um die gewünschten Eigenschaften zu erreichen die fertigen Bänder. Derzeit hat das Team 30-50% FWF-Bänder sowohl aus PP als auch aus PA6 hergestellt, selbst bei den schwereren Kabeln.
Um Bänder nach dem Austritt aus der Düse schnell abzukühlen, wurde ein Luftkühlungssystem nach der Imprägnierung entwickelt. Aufgrund der Breite der Produkte und der Herausforderungen bei der nachgelagerten Verwendung dieser Bänder musste das Team sogar eine Methode erarbeiten, um fertige Bänder auf Gatter/Spulen aufzunehmen.
Laut Vaidya konzentriert sich das Team derzeit auf die elektronische Integration, die den Aufbau einer formalen grafischen Benutzeroberfläche und die Entwicklung eines speicherprogrammierbaren Steuerung (SPS)-basierten Systems umfasst. Letztendlich besteht das Ziel des Teams darin, ein Produktionsmodul für thermoplastische Bänder zu entwickeln, das am hinteren Ende einer TCF- oder konventionellen Kohlefaser-Produktionslinie hinzugefügt werden kann, um die Produktion von sekundären/mittleren thermoplastischen Bändern zu erleichtern.
„Unser Team hat sich vielen technischen Herausforderungen gestellt, aber wir haben auch einiges erreicht“, erklärt Vaidya. „Der Umgang mit einem so breiten Schleppband und das erfolgreiche – und schnelle – Imprägnieren der Fasern, um hochwertige thermoplastische Bänder ohne Hohlräume zu erhalten, war schwierig. Unser Team hat jedoch eine Reihe von Prozessparametern untersucht, darunter mehrere Iterationen des Werkzeugdesigns; Simulationen des Polymerflusses durch die Düse; und verschiedene Aspekte der Faserzufuhr, des Spannens und des Vorwärmens. Wir haben nicht nur einige der Ansprüche in unserem Patent bewiesen, sondern auch Imprägnierstraßengeschwindigkeiten von 3,7 Meter/Minute erreicht, während wir 30 % FWF-Polypropylen- und PA6-Bänder herstellen.“
Nächste Schritte
Vaidya sagt, dass der Schutz des geistigen Eigentums rund um diese Bandtechnologie bei der UT Research Foundation eingereicht wurde – eine mit traditionellen 24K- und 50K-Fasern und eine mit Wide-Tow-Fasern. Die Kommerzialisierung werde sich auf die Inline-Imprägnierung innerhalb einer Kohlefaserlinie konzentrieren. „Dies wird die Nachbearbeitung erheblich reduzieren und sich leicht anpassen, wodurch die Gesamtkosten des Zwischenprodukts weiter gesenkt werden“, sagt er.
Wie können diese Bänder angebracht werden? Laut Vaidya gibt es viele Möglichkeiten:„Zum Beispiel kann das Material in Langfaserform zerkleinert, in Pultrusionsrohstoffen, Großtank-Filamentwinding, Overmolding (ähnlich Organoblech) beim Formpressen, Plattenmaterial in Hybridprozessen verwendet werden – z , mit LFT [Langfaser-Thermoplast], SMC [Sheet Moulding Compound] und anderen synergistischen Materialien.“ Dies eröffnet eine Reihe von Produkttypen, die von Steifigkeitsverbesserungen, Schlagzähigkeit und verbesserter Verarbeitbarkeit wie Formen, Ziehungen und Biegungen, Recycling und reversiblen Chemikalien profitieren würden.
Zu den Anwendungen, sagt er, gehören Automobile, Lastwagen, Windflügel, Infrastruktur (Brücken), Bau, Sportartikel, Marine- und Offshore-Produkte. „Das thermoplastische Zwischenprodukt aus Wide-Tow-Kohlefaser könnte jetzt Möglichkeiten bieten, Kohlefasern in Betracht zu ziehen, wo sie zuvor zu teuer waren“, schließt Vaidya.
Harz
- Kohlenstofffasern
- Was ist Kohlefaser?
- Faserverstärkter Kunststoff (FRP) in Aktion!
- Kohlefaserverstärkter Kunststoff (CFK)
- Klebeband aus thermoplastischem Thermoplast auf PPS-Basis
- Konsortium sucht Lösungen für thermoplastische Kohlefaser-Verbundstrukturen
- 3D-Druckverbundwerkstoffe mit Endlosfasern
- Herstellung stärkerer IM-Teile mit faserverstärkten und gefüllten Materialien
- SIGRASIC® kohlefaserverstärkter Siliziumkarbid-Filz
- SIGRASIC® Kohlefaserverstärkte Siliziumkarbid-Kurzfasern