Das Museum der Zukunft bauen
Das Museum der Zukunft, das derzeit in Dubai, Vereinigte Arabische Emirate (VAE), entsteht, ist eines der komplexesten Bauwerke, die jemals gebaut wurden. Das 78 Meter hohe Gebäude beherbergt sieben Stockwerke in einer torusförmigen Hülle, die auf einem dreistöckigen Podium sitzt. Die Außenfassade des Torus besteht aus 1.024 feuerhemmenden (FR) Verbundplatten. Jedes Paneel ist mit Edelstahl verkleidet und hat eine einzigartige 3D-Form und integrierte arabische Kalligraphie. Das fließende Drehbuch formt Gedichte, die die Vision für Dubais Zukunft von Seiner Hoheit Scheich Mohammed bin Rashid Al Maktoum, Vizepräsident und Premierminister der Vereinigten Arabischen Emirate und Herrscher des Emirats Dubai, beschreiben. Sie dienen auch als Fenster des Gebäudes, lassen Tageslicht durch den stützenfreien Innenraum und sorgen nachts durch eine 14 Kilometer integrierte LED-Beleuchtung für einen dramatischen Effekt.
Von Scheich Mohammed als Inkubator für Innovation und Erfindung konzipiert, gilt das Museum der Zukunft als eines der fortschrittlichsten Gebäude der Welt, an dem Menschen neue Technologien erleben und erforschen können. Es ist auch ein Symbol für Architektur, die durch digitales Design und den Einsatz effizienterer Materialien Grenzen überschreitet. Mit parametrischer Auslegung wurde das Stahldiagrid – ein Fachwerk aus 2.400 sich diagonal kreuzenden Stahlträgern – entwickelt, an dem Bodenplatten aus Verbundbeton und 17.000 Quadratmeter Verbundverkleidung befestigt sind, letztere aus 1 Million Quadratmeter multiaxialer glas- und kohlefaserverstärkter Epoxid-Prepreg.
Das Unternehmen Affan Innovative Structures aus Dubai lieferte das Verbunddesign für die Paneele sowie die Herstellung und Unterstützung bei der Installation. „Dies ist das erste Mal, dass ein solches Projekt durchgeführt wird“, sagt der CEO des Unternehmens, Dr. Amer Affan. „Und auch das erste Mal, dass Verbundplatten verwendet wurden, um mehrere Gebäudefunktionen über solch komplexe Formen zu integrieren.“
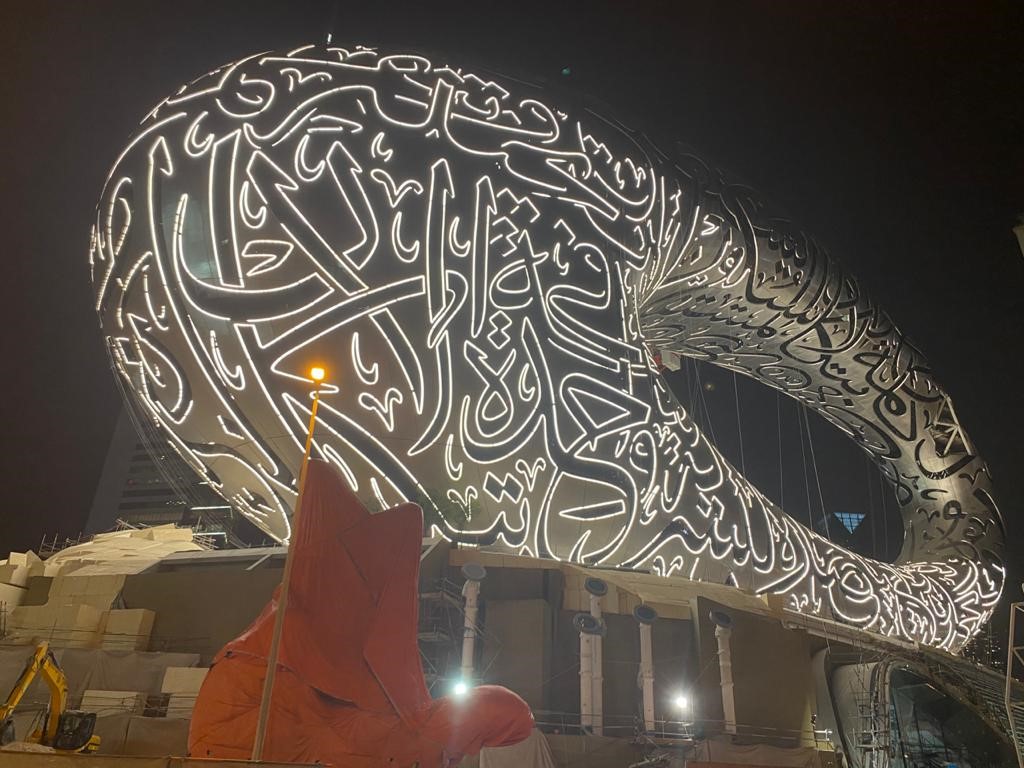
Der Hauptarchitekt Shaun Killa erklärt, dass solche komplexen Außenbereiche normalerweise Regenschirme sind, mit einem Gebäude dahinter, das das Abdichtungssystem enthält. „Das vereinfacht die Sache, weil es beim Erstellen dieser sehr dreidimensionalen Formen etwas nachsichtiger ist“, bemerkt er. „Bei diesem Gebäude übernimmt jedoch die Hülle die Abdichtung, die Luftdichtheit, die Konstruktion und die Beleuchtung.“ Affan räumt ein, dass sein Unternehmen für ein so großes Projekt klein ist, „aber wir haben unser technisches Know-how genutzt, um etwas Einzigartiges zu schaffen und gezeigt, wie Gebäude in Zukunft gebaut werden.“
Fähigkeit in komplexen, digitalen Designs
Affan Innovative Structures wurde zunächst vom Ingenieurteam des Museums der Zukunft kontaktiert. „Es gab nicht viele Unternehmen, die die erforderlichen Arbeiten für die Außenverkleidung ausführen konnten“, sagt Affan. „Der einzige andere Wettbewerber schlug eine normale Vorhangfassade mit Aluminium- oder Edelstahlpaneelen außen vor.“ Vorhangfassaden, die typischerweise zusätzlich zu einem Stahltragwerk verwendet werden, sind dünn und bestehen aus Aluminiumrahmen, die Glas-, Metall- und/oder dünne Steinfassaden tragen (siehe „Die Gebäudehülle:GFK-Elementfassaden“). Dies wurde vom Ingenieurteam als zu schwierig und nicht in der Lage, das gleiche Erscheinungsbild wie mit einer integrierten, multifunktionalen Verbundplattenfassade zu erzielen, abgelehnt. Daher wurde letzteres, vorgeschlagen von Affan Innovative Structures, für das Projekt ausgewählt. „Wir verfügen auch über eine einzigartige Technologie, die es uns ermöglicht, große Platten herzustellen“, fügt Affan hinzu, „bis zu 3 Meter breit und 9 Meter hoch, in beide Richtungen gebogen, was weniger Fugen bedeutet.“
Affan Innovative Structures war für dieses Projekt einzigartig geeignet. Das 2004 von Dr. Affan gegründete Unternehmen bietet schlüsselfertige Komplettlösungen – vom Konzeptentwurf über die Installation bis hin zur Gebäudewartung – und konzentriert sich auf sehr technische Herausforderungen. Der Lebenslauf des Unternehmens umfasst den komplexen, geometrischen Aluminiumschirm/die Verkleidung für das King Abdullah Sports City Stadium (Jeddah, Saudi-Arabien), die Eingangsüberdachung aus Verbundwerkstoff und 64 kunstvoll gemusterte Glas- und Stahloberlichter für die Yas Mall (Abu Dhabi, Vereinigte Arabische Emirate) , das äußere Verbunddach für das Sidra Hospital (Doha, Katar) und viele andere anspruchsvolle Projekte. Diese Fähigkeit in komplexen Stahl-, Glas- und Verbundbaugruppen wäre genau das, was für die multifunktionale Verbundfassade des Museums der Zukunft benötigt wird.
„Innerhalb jeder Verbundplatte befindet sich ein System aus Flachglas [Platten] in arabischer Schrift“, erklärt Affan. „Das Glas ist in den Paneelen fast versenkt, bis zu 200 Millimeter tief.“ Diese Aussparung ändert sich nicht nur von der Oberseite des Gebäudes, mit weniger Aussparung, um Wassereinschlüsse zu verhindern, nach unten, wo vertikale und hinterschnittene Platten tief zurückgesetzt werden können, ohne Wasser einzuschließen, sondern auch innerhalb jeder Platte, schräg und abnehmend, um ein allmähliches, natürliches . zu erzeugen Rand für das Skript. „Die Position und die Kanten der Aussparung variierten auch je nach Position des Glases innerhalb des Panels, da das Glas flach, aber die Panels gebogen waren“, bemerkt Affan. „Das war nur mit digitaler Konstruktion und CNC-Bearbeitung möglich.“ Diese Präzision war auch erforderlich, um sicherzustellen, dass die von einer Tafel zur nächsten variierende Schrift beim Verlegen der Tafeln genau ausgerichtet wurde, damit Buchstaben und Wörter korrekt über die Gebäudehülle fließen.
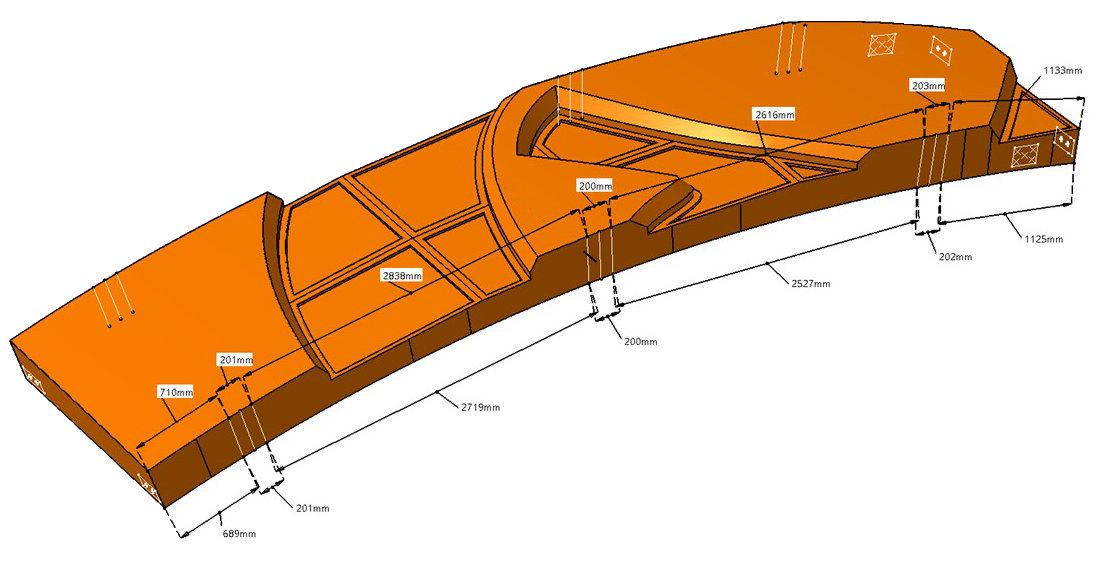
Für Affan bestand die einzige Lösung darin, die arabische Schrift und Aussparungen in jede Verbundplatte einzuformen. „Bewehrungen würden in präzise CNC-gefräste Formen eingelegt“, erklärt er. Zufällig ist die CATIA-Software (Dassault Systèmes, Vélizy-Villacoublay, Frankreich), mit der Affan Innovative Solutions seine CNC-Maschinen antreibt, auch das 3D-CAD-Programm, das von der Luft- und Raumfahrtindustrie zur Konstruktion komplexer Flugzeug- und Verbundstrukturen verwendet wird. Darüber hinaus beherrscht das 28-köpfige Team von Affan auch die BIM-Software Tekla, Rhino 3D (Robert McNeel &Assoc., Seattle, Washington, USA) und AutoCAD von Autodesk. „Wir haben alle Zeichnungen in CATIA erstellt, ebenso wie das Laminatdesign, was uns die Möglichkeit gab, solch komplexe Bearbeitungen durchzuführen“, sagt Affan.
Die Konstruktion war jedoch nicht trivial und musste einer Vielzahl von strukturellen und Windlasten standhalten. Zum Beispiel habe das Innere des Torus einen Windkanaleffekt erzeugt, erklärt Affan. Diese Platten müssen bis zu 450 kg/m 2 aushalten (92 lb/ft 2 ) der Windlast. (Beachten Sie, dass die International Building Code Windlasten von 71 lb/ft 2 auflistet für Hurrikan-Hochrisikogebiete in West Palm Beach, Florida, USA). Auch die Verbundplatten für das Museum der Zukunft sind auf Gewichtsminimierung zugeschnitten. „Die Platten verwenden 9 bis 13 Lagen, die je nach Standort und Belastung variieren“, sagt Affan. Er fügt hinzu, dass das Composite Technology Center (Stade, Deutschland), eine Airbus-Tochter und ein langjähriger Partner über die Handelsorganisation CFK Valley ev (Stade, Deutschland), „eine externe Überprüfung unserer Laminatkonstruktion, Durchbiegung und Steifigkeit durchgeführt hat“. Berechnungen.“
Eine zusätzliche Komplexität und Innovation besteht darin, dass die Paneele auch ein eigenes Befestigungssystem integriert haben. „An den Rändern bilden 24 Lagen die kassettenartige Anschlussgeometrie zum Anschluss an das Gebäude“, erklärt Affan. Ein Kassettensystem ist eine Methode zum Anbringen von Außenverkleidungen, die ursprünglich für regenschirmartige Installationen entwickelt wurde. Obwohl Typen und Geometrien variieren, ermöglichen Kassetten in der Regel eine flache, regensichere Außenfläche, die hinter dem tragenden Rahmen des Gebäudes befestigt wird. Für die Fassadenplatten des Museums der Zukunft wurden keine Einzelteile zur Bildung der Kassettenkanten benötigt, sondern in jede Form eingearbeitet und so in jede Verbundplatte integriert.
Werkstoff-, Formen- und Plattenherstellung
Obwohl Affan Innovative Structures auf 10.000 Quadratmetern Composite-Fertigungsfläche über 16 Harzinfusionsmaschinen und acht glasbeschichtete Harzinfusionstische auf Stahlbasis mit einer Größe von 3 x 20 Metern verfügt, entschied man sich für Prepreg. Wieso den? „Um die erforderliche FR-Leistung zu erreichen, sind viele Additive erforderlich, sodass das Harz dick wird und beim Aufguss nicht fließt“, erklärt Affan. In diesem Fall war das Additiv Aluminiumtrihydrat (ATH, siehe „Feuer ohne Gewicht standhalten“). Er fährt fort:„Daher haben wir mit Notus Composites [Ras Al Khaimah, VAE] zusammengearbeitet, um ein FR-Epoxid-Prepreg zu entwickeln. Wir haben hauptsächlich Glasfasern verwendet, aber in bestimmten Abschnitten, in denen es Probleme mit der Durchbiegung gab, auch Kohlefasern.“ Zugelassen von der Dubai Civil Defense, hat Notus Composites EPFR-609 Prepreg in Kombination mit NE11-FR Oberflächenfolie NFPA 285, EN13051-1 und ASTM E1098 und E84 Class A Brandschutzanforderungen erfüllt (siehe „Feuerhemmende Prepregs ermöglichen .. .“ und „Besseres, billigeres Screening von GFK-Baustoffen“).
Da äußere Metalloberflächen in Dubai im Sommer Temperaturen von 80 °C (176 °F) erreichen können, erklärt Affan:„Wir haben das Prepreg bei 120 °C ausgehärtet, um eine ausreichende Tg . zu gewährleisten (Glasübergangstemperatur), um einer Kopfdurchbiegung zu widerstehen. Daher wurden die Formen aus einem Polyurethanschaum hergestellt, der dieser hohen Temperatur standhalten konnte, was teurer ist. Wir haben drei oder vier verschiedene Schäume ausprobiert, aber nur einen konnte der Temperatur plus Vakuumdruck standhalten und war dennoch weich genug, um leicht und schnell CNC-bearbeitet zu werden.
Die CNC-Bearbeitung jeder Form dauerte 12 bis 72 Stunden und jede der 1.024 Verbundplatten erforderte eine eigene Form . Alle vier CMS von Affan Innovative Structures (Zogno, Italien) 5-Achs-CNC-Maschinen – die größten mit einer Länge von 33 Metern, einer Höhe von 13 Metern und einer Höhe von 2,5 Metern – wurden benötigt, um die anspruchsvolle Produktionsrate des Museums zu erfüllen. „Wenn eine [Maschine] wegen Wartungsarbeiten ausfiel, ließen wir die anderen parallel laufen“, erklärt Affan.
Prepreg-Lagen wurden geschnitten und mit einem (Bulmer, Mehrstetten, Deutschland) Schneideautomat. „Wir haben in den Platten keinen Kern verwendet, weil es damals, anders als heute, keine Schaumkerne gab, die die FR-Anforderungen erfüllen konnten“, sagt Affan. Trotz einer solchen Automatisierung waren die 250 Mitarbeiter des Unternehmens, die es bis 2015 erreicht hatte, auch für die Produktion erforderlich, durchschnittlich vier Platten pro Tag. Teams von sechs Arbeitern, jeder mit einem Vorgesetzten und ausgewogenen Fähigkeiten, um effizient zu sein, stellten die Platten zusammen. „Normalerweise arbeiten zwei oder drei Teams an einem Projekt“, sagt Affan, „aber um diesen Produktionsplan einzuhalten, arbeiteten zu jeder Zeit 20 Teams.“
Fertigungsschritte
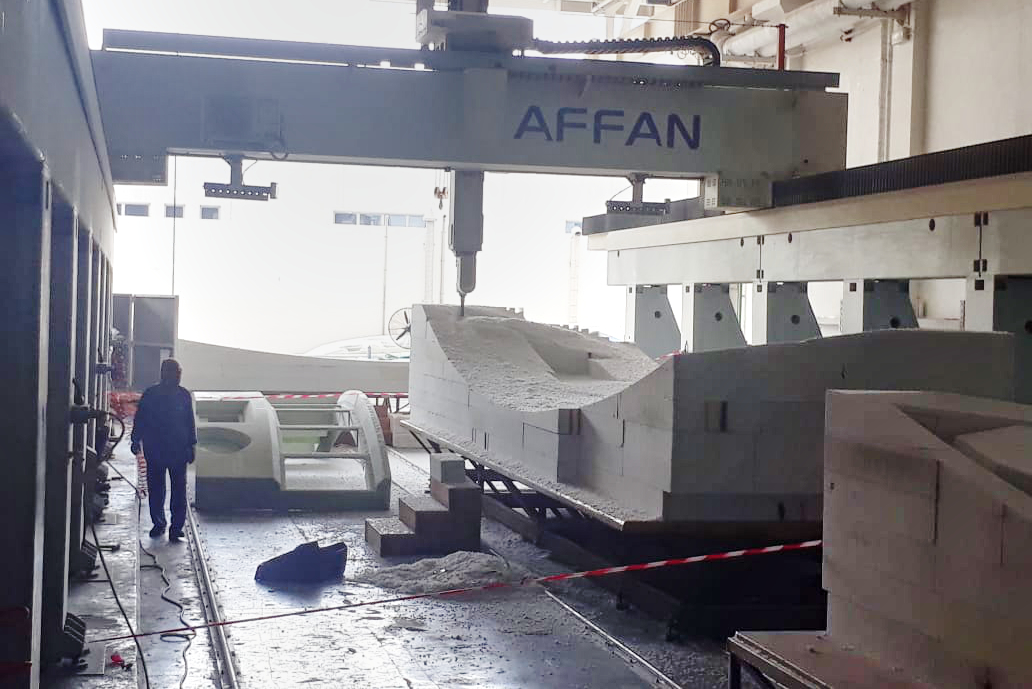
Schritt 1Polyurethanschaum wird in Präzisionsformen gefräst. Quelle für alle Bilder der Herstellungsschritte | Affan Innovative Lösungen
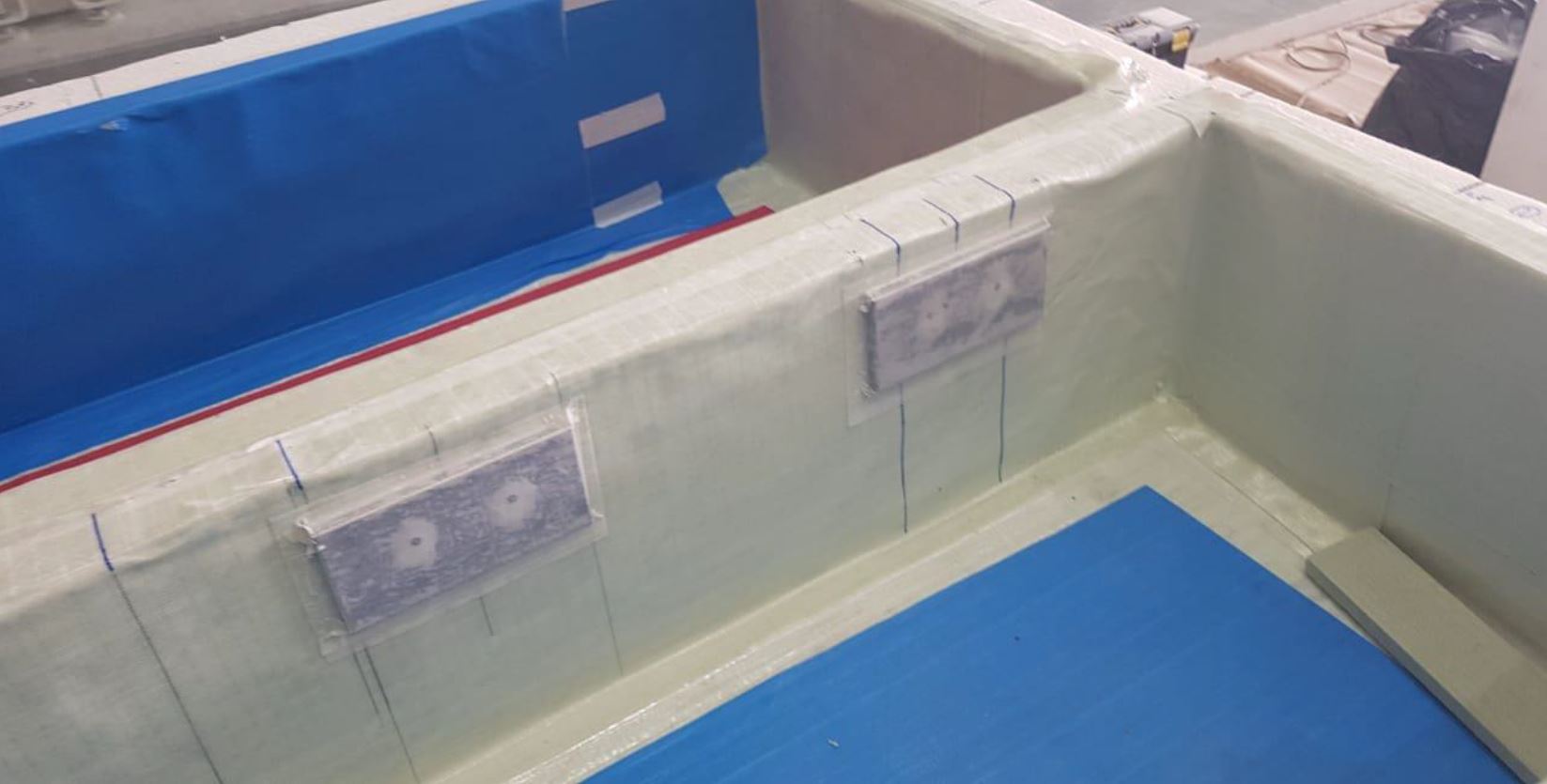
Schritt 2Glasfaser/Epoxid-Prepreg wird von Hand in die Formen gelegt.
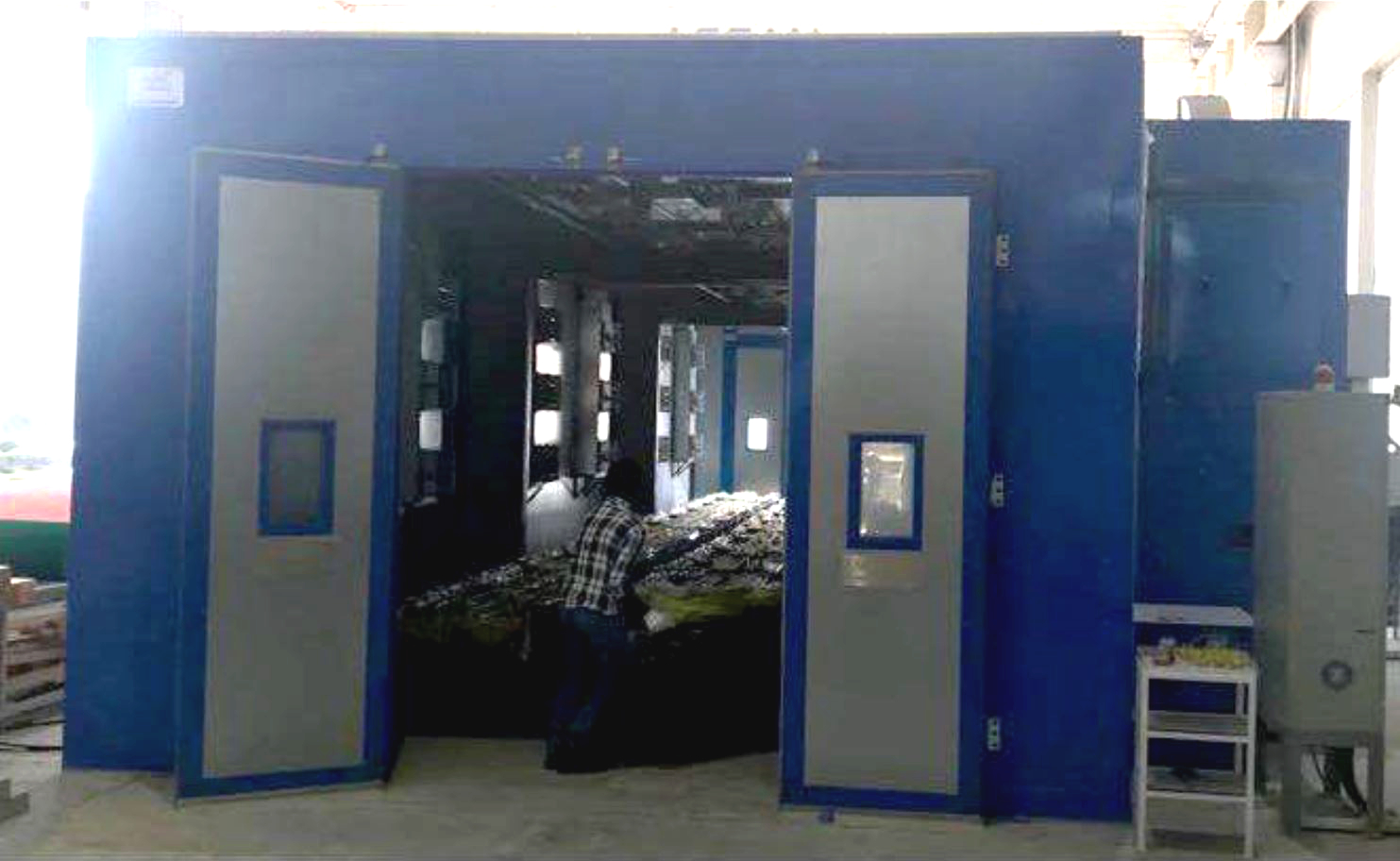
Schritt 3Prepreg-Layups werden vakuumiert und in einem Ofen 6 Stunden lang bei 120°C ausgehärtet.
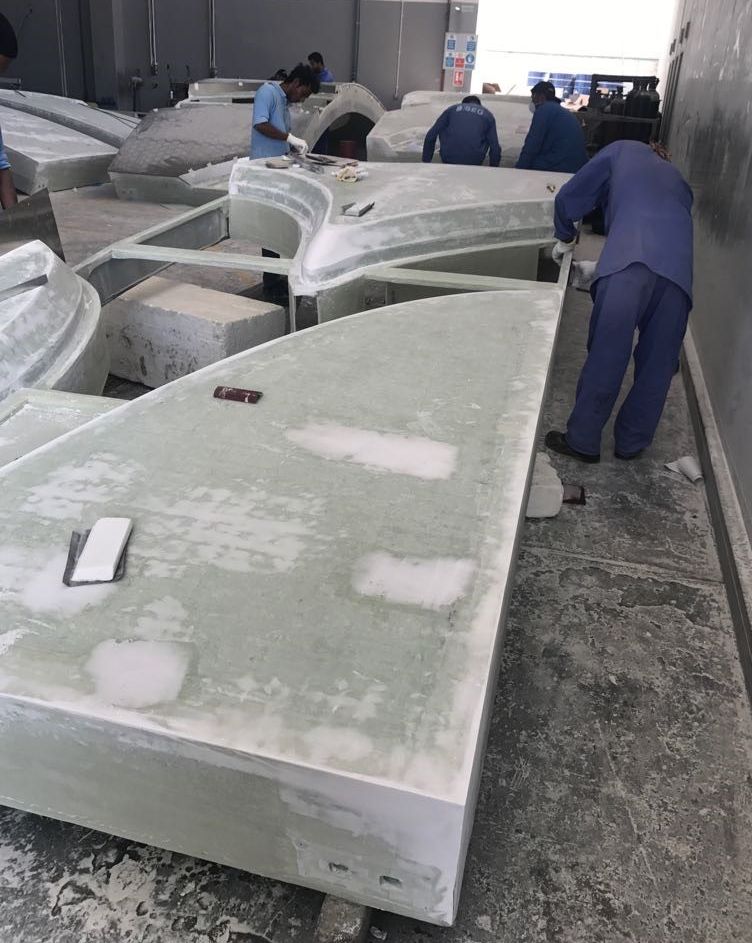
Schritt 4Entformte Platten werden für die Verklebung von Edelstahl-Finish vorbereitet.
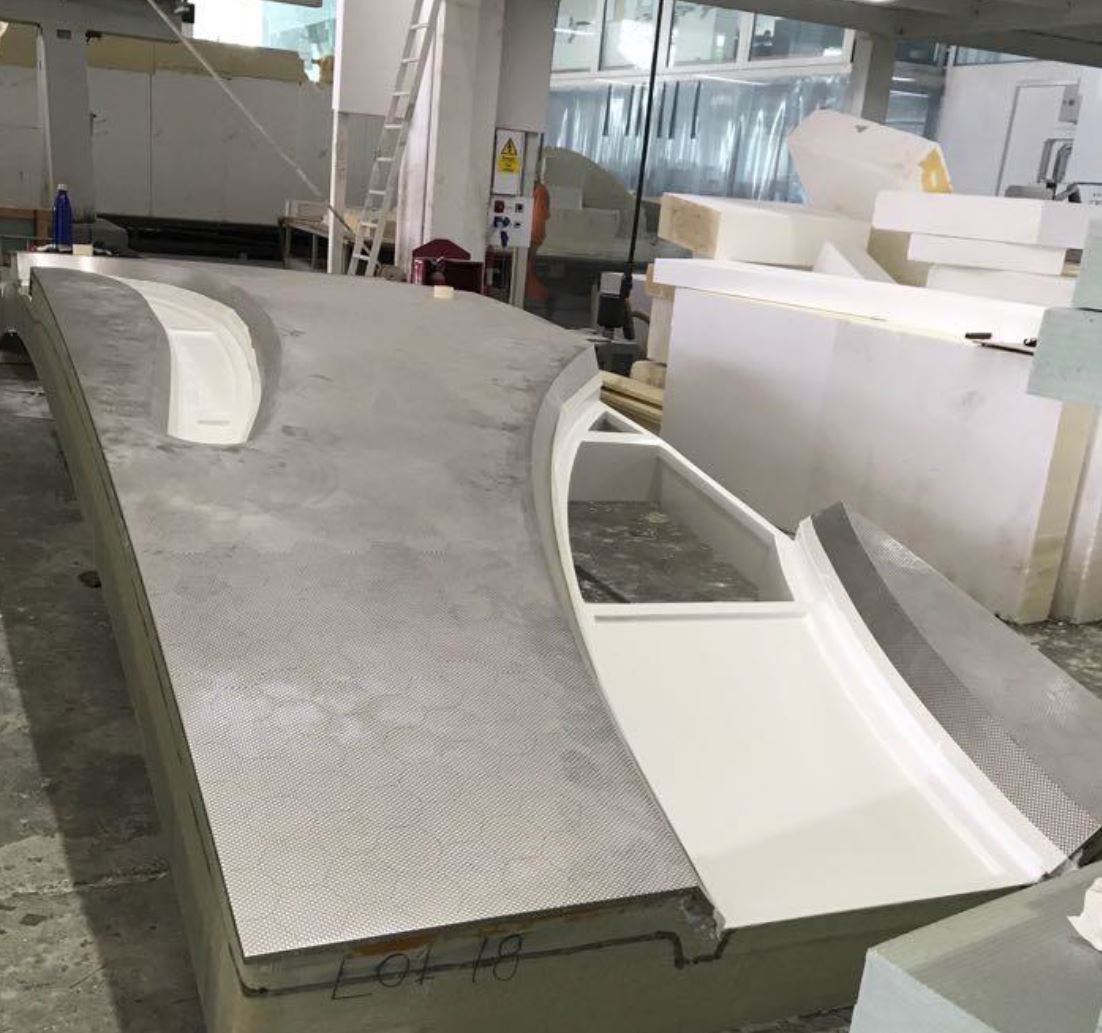
Schritt 5Edelstahl-Sechskantkanten werden auf GFK-Platten geklebt und mechanisch befestigt.
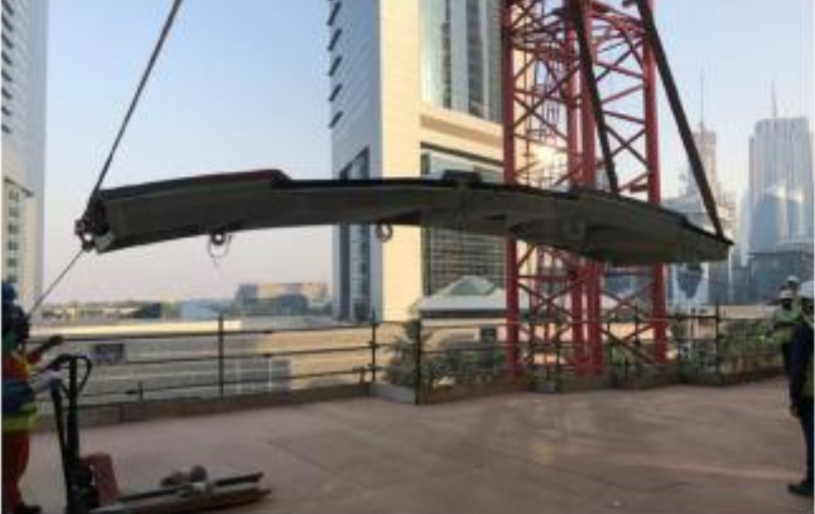
Schritt 6Fertige Paneele werden zur Installation angehoben.
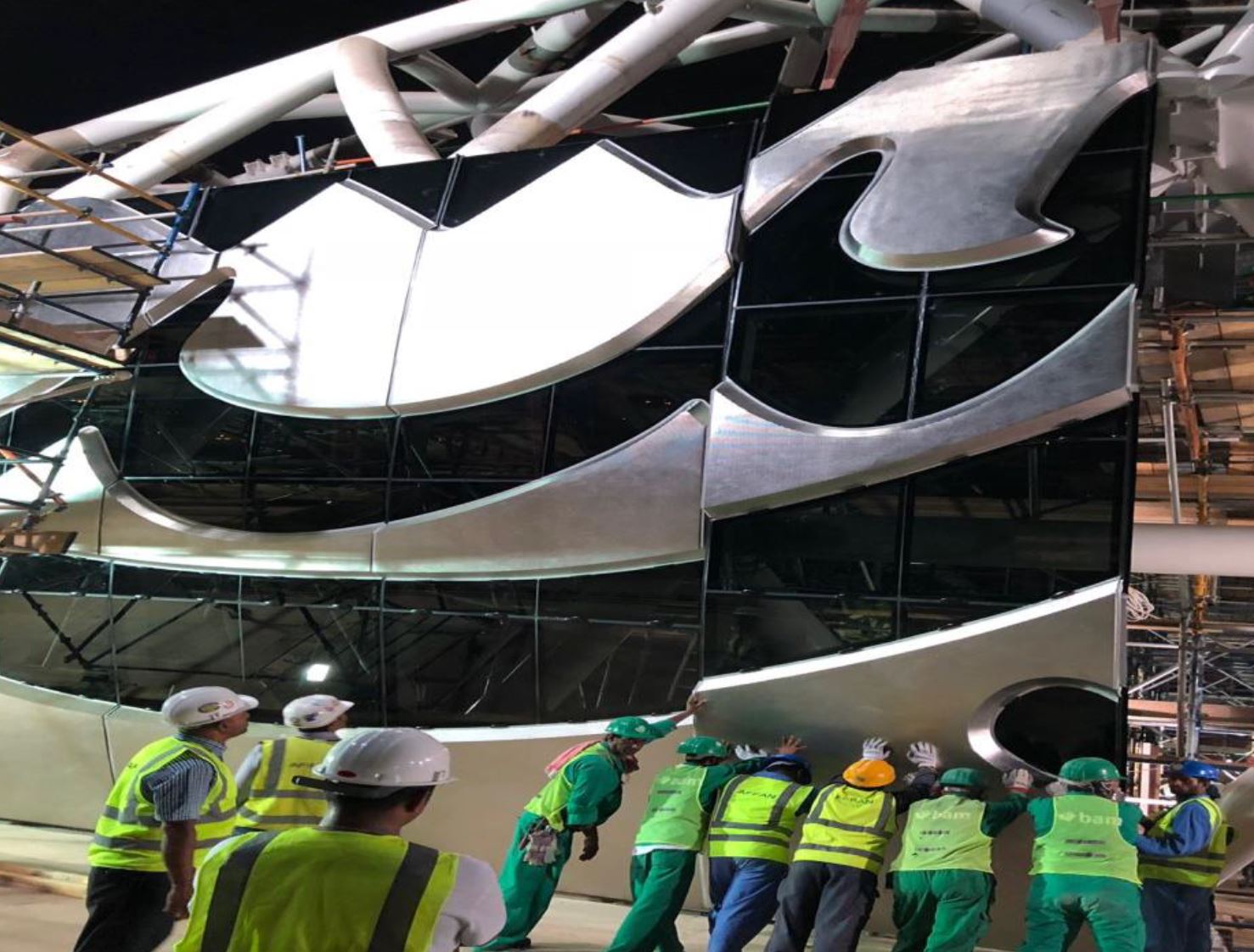
Schritt 7Jede Platte wird über ein einzigartiges 3D-„Universalgelenk“ angepasst.
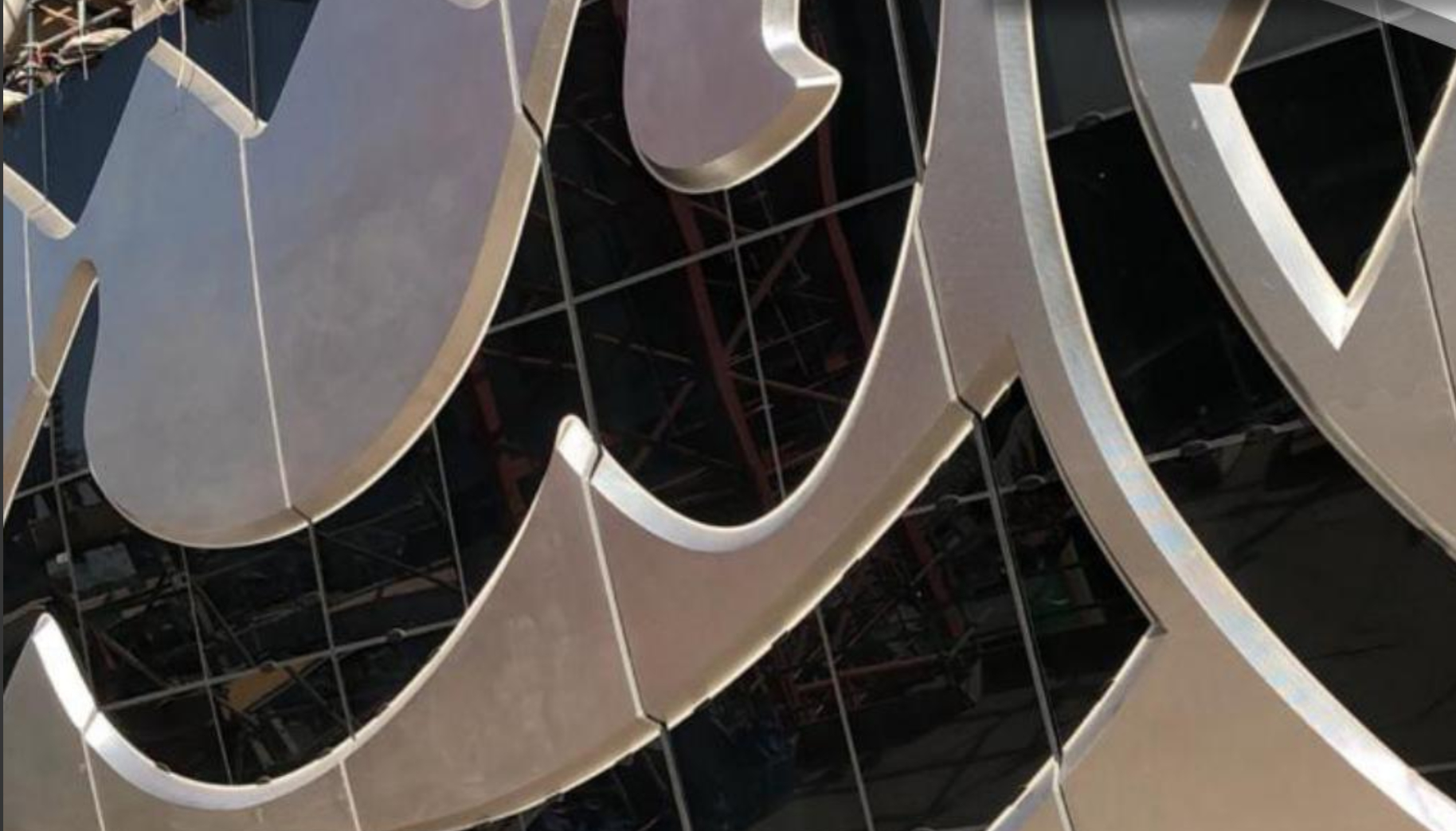
Schritt 8Jedes Paneel wird über eine einzigartige 3D-„Universalfuge“ angepasst, um eine glatt ausgerichtete Außenfassade zu erzielen.
Vorherige NächsteLayups wurden von Hand gelegt, vakuumiert und 6 Stunden lang in Öfen mit einer Länge von 20 Metern, einer Breite von 8 Metern und einer Höhe von 3 Metern ausgehärtet. „Jede CNC-Maschine hatte einen eigenen Ofen“, sagt Affan. „Wir haben nicht viele Platten pro Aushärtungszyklus zusammengefügt. Stattdessen haben wir jedes Paneel, wenn es fertig war, sofort gehärtet, um einen möglichst hohen Produktionsfluss aufrechtzuerhalten. Anschließend entformten wir die Platten und verwendeten einen 3D-Scanner, um sicherzustellen, dass die Platte im fertigen Zustand mit der CATIA-Datei übereinstimmte. Gemäß unserem umfassenden Qualitätskontrollsystem mussten wir bei jedem einzelnen Schritt des Prozesses die digitalen Dateien abgleichen.“
Fertige Paneele erhielten dann die Edelstahl-Außenbeschichtung. „Der Edelstahl wird auf jedes Paneel geklebt und dann mit mechanischen Befestigungselementen befestigt, was eine Kunst für sich ist“, sagt Affan. „Das Metall wurde in kleine Sechsecke geschnitten, um über die 3D-Platten zu drapieren. Das sechseckige Gitter variierte von Teil zu Teil, abhängig von der Krümmung. Auch wenn wir Erfahrung und Vertrauen in das Kleben haben, konnte während der Lebensdauer des Gebäudes kein einziges Sechseck auseinanderbrechen. Daher musste jedes einzelne Sechseck befestigt werden – was 200 bis 300 Befestigungen für ein einzelnes Paneel erforderte.“ Fertige Paneele wurden dann zur Installation an die Baustelle geschickt.
NASA-gestützte, problemlose Installation
Die Installation wurde tatsächlich von der Baufirma BAM International (Gouda, Niederlande) durchgeführt. „Wir haben nur Supervisoren für die Installation gestellt, die beim Umgang mit den Panels helfen“, bemerkt Affan. „Die Art und Weise, wie jeder angehoben wird, ist der Schlüssel. Die Paneele wurden so konzipiert, dass sie für die jeweilige Position im Gebäude stark genug sind. Sie müssen jedoch auf eine bestimmte Art und Weise über mindestens zwei Hebepunkte angehoben werden, genau wie Hängekassetten in traditionelleren Bauweisen.“
Es gab ein zusätzliches Problem, das Affan in einzigartiger Weise lösen konnte. „Damit jedes Paneel auf der Stahlkonstruktion sitzt und dennoch die glatte Oberfläche bildet, brauchten wir die Möglichkeit, das Paneel in Tiefe, Ausrichtung und Krümmung in 3D zu verstellen – also eine Art Kreuzgelenk mit drei Freiheitsgraden . 1985 arbeitete ich als Student bei der NASA in Kalifornien an der Dämpfung von Raumstationsstrukturen. Der Schlüssel war, jede Struktur bewegen und justieren zu können, wenn das Shuttle andockt, damit Vibrationen schnell gedämpft werden, ein bisschen wie eine Geräuschunterdrückung. Ich habe die gleiche Technologie für die Paneelbefestigung und Anpassung während der Installation verwendet.“
Da die Platten auch die wasserdichte Abdichtung des Gebäudes darstellten, durften keine Lücken zwischen ihnen bestehen. „Die Platten könnten nicht direkt aneinanderstoßen oder sie könnten reißen“, erklärt Affan aufgrund der hohen Nutzlast von 1,5 Tonnen auf dem freitragenden 6. ten Ausstellungsfläche bewegt sich die Stahlkonstruktion tatsächlich. „Wir haben einen genau beabstandeten Spalt zwischen den Platten beibehalten und dieser wurde mit einer speziellen Dichtung gefüllt.“ Diese Dichtung, die weich genug ist, um sich auszudehnen, aber dennoch steif genug, um Belastungen standzuhalten, bietet Dichtungsfunktionalität und ermöglicht gleichzeitig das ästhetische Erscheinungsbild des Gebäudes.
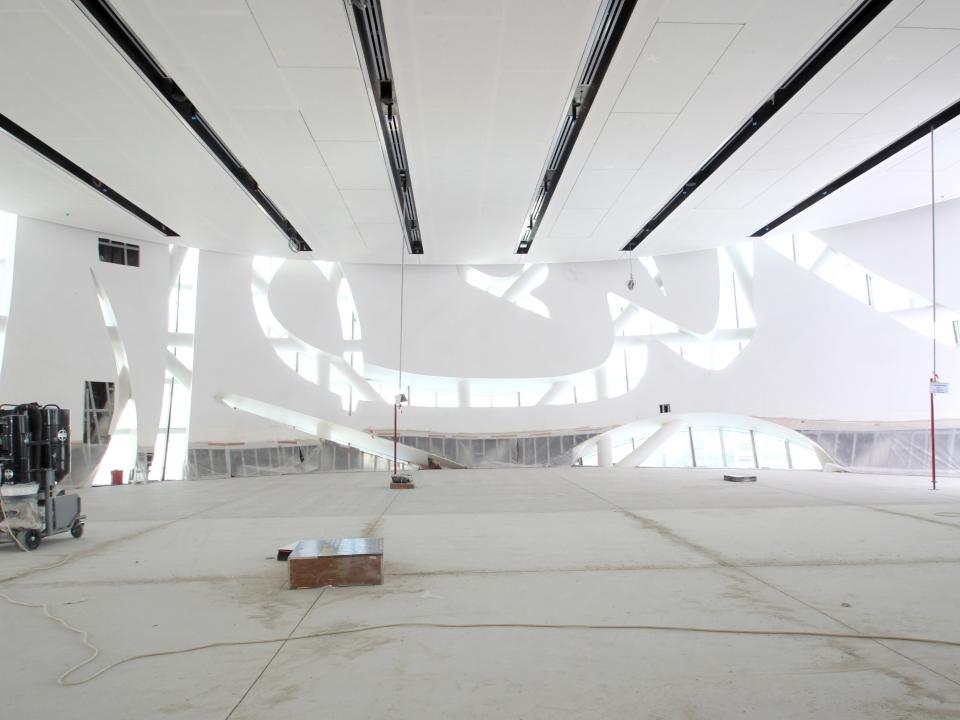
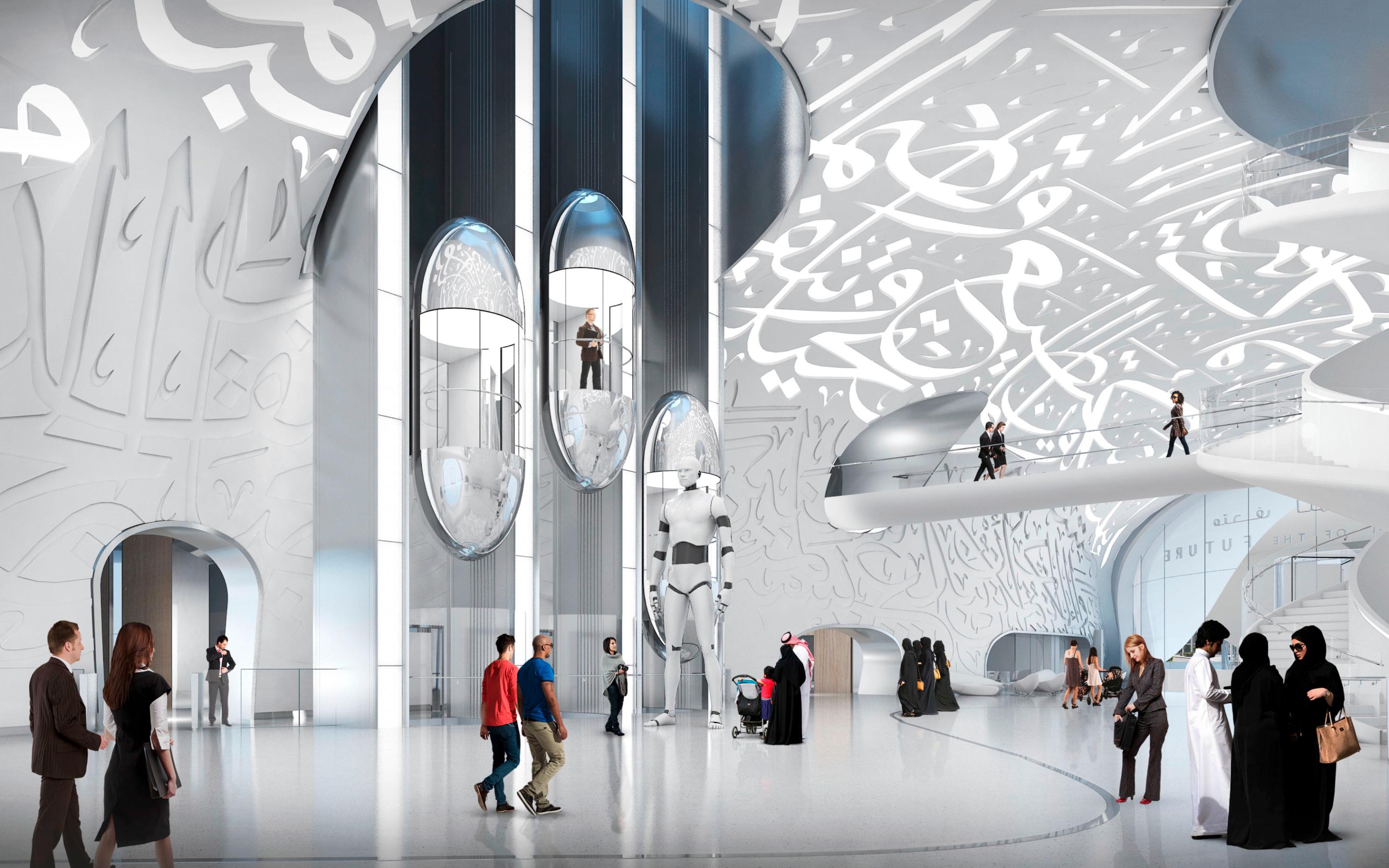
Solche Lösungen seien von Vorteil, stellt Affan fest. „Weil wir aus einem Strukturhintergrund kommen, können wir viele Materialien kombinieren. Dies ist sehr wichtig. Verbundwerkstoffe sind nur ein Material, das wir verwenden. Dies war nicht nur ein Verbundprojekt.“ Die Ergebnisse sprechen für sich. „Die Installation verlief gut; Es gab überhaupt keine Probleme“, sagt Affan, der anmerkt, dass es keine Möglichkeit gab, zu überprüfen, ob das Panel passt, außer um sicherzustellen, dass es mit der digitalen Datei übereinstimmt. „Wir hatten noch kein Panel, das nicht passte oder die falsche Form hatte oder das Wort falsch geschrieben war“, sagte Bauly, Projektmanager von Buro Happold, in einem BBC-Artikel von Elizabeth Bains.
Zukünftige modulare Bauweise
„Wir haben den gesamten Prozess gemeinsam gemanagt“, fügt Affan hinzu. „Auch die Teamarbeit innerhalb unseres Unternehmens selbst war wichtig; Design- und Layup-Gruppen mussten sich aufeinander abstimmen. Wir haben noch nie einen so großen Job gemacht und es war eine Herausforderung, aber wir mögen Herausforderungen.“
Leider hat COVID-19 seinen Tribut gefordert. „Wir haben diesen Job kurz vor der Sperrung der Pandemie beendet“, sagt er. „Jetzt sind wir auf weniger als 30 Leute gesunken. Es ist verheerend. Aber das hat alle getroffen, nicht nur uns.“ Dennoch sieht Affan Hoffnung für die Zukunft und für die Rolle, die Verbundwerkstoffe dabei spielen werden, die Nachhaltigkeit und Innovation zu erreichen, die die Welt im Bauwesen braucht. „Gerade in Dubai und im GCC (Gulf Cooperation Council) wollen die Leute neue Ideen ausprobieren. Es zeigt die Zukunft der Architektur und des Bauens.“
Diese Zukunft, betont er, werde für diejenigen sein, die modulare Konstruktionssysteme verwenden können, „und COVID-19 beschleunigt dies tatsächlich. Unternehmen bauen Module ein und senden diese an die Site. Dies wird sich entwickeln, weil es Ineffizienzen außerhalb des Standorts und in eine Fabrik verlagert, was die Kontrolle und Qualität erhöht. Vor Ort muss man alle Leute koordinieren. Es verschwendet Zeit, auf andere Subunternehmer zu warten. Außerdem sind Sie auf das Wetter und Arbeitsunterbrechungen angewiesen. Die Fertigung in einer Fabrik eliminiert all dies. Da sie stark, leicht und langlebig genug sind, um sie leicht zu transportieren und zu installieren, ermöglichen Verbundwerkstoffe diese Art der modularen Konstruktion und Sie können jede gewünschte Form herstellen.“
Affan stellt fest, dass auf Kreuzfahrtschiffen seit Jahren modulare Konstruktionen verwendet werden, bei denen jede Kabine vorgefertigt wird, komplett mit Heizung/Klimaanlage, Elektro- und Sanitärsystemen, und dann wie LEGO-Blöcke in das Stahlgerüst des Schiffes eingebaut wird. „Stellen Sie sich vor, wie viel Zeit Sie sparen, wenn jedes Modul bereits ausgestattet ist. Wir prüfen jetzt ein Projekt, um ein Hochhaus auf diese Weise aus Verbundwerkstoffen zu bauen“, sagt er. „Wenn Sie FR-Harze haben, brauchen Sie die Teile, die vorher aus Metall waren, nicht.“ Unter Berufung auf ein Marriott-Hotel, das auf diese Weise gebaut und letztes Jahr in New York City fertiggestellt wurde, fügt Affan hinzu:„Dieses Gebäude bestand aus Stahl und Holz, aber wir können es aus Verbundwerkstoffen bauen.“
Harz
- Cloud-Sicherheit ist die Zukunft der Cybersicherheit
- Die Zukunft der Slicing-Software
- Edge Computing:Die Architektur der Zukunft
- Visualisierung der Zukunft der Anlagenwartung
- Die Zukunft der Rechenzentren
- Aufbau besserer Lieferketten für die Zukunft
- Smarte Gebäudeautomation und die Zukunft der Immobilienentwicklung in Städten
- Aufbau der Mitarbeitererfahrung der Zukunft mit intelligenter Automatisierung
- Wie Tech Mahindra die Fabrik der Zukunft baut
- Die Zukunft des 3D-Drucks in der Fertigung