Swinburne University und CSIROs Industry 4.0 Testlab for Composite Additive Manufacturing
Die Swinburne University of Technology (Melbourne, Australien) richtet in Zusammenarbeit mit der australischen National Science Agency, der Commonwealth Scientific and Industrial Research Organization (CSIRO) ein Industrie-4.0-Testlabor für die additive Fertigung von Verbundwerkstoffen ein, siehe Kohlefasern kosten“). Die Anlage befindet sich derzeit am Standort Clayton von CSIRO im Bau und wird im Oktober 2020 fertiggestellt.
Dieses von der australischen Bundesregierung unterstützte Industry 4.0 Testlab for Composites ist eines von sechs in einem australischen nationalen Netzwerk, ähnlich dem Labs Network Industrie 4.0 in Deutschland. Dieses Testlab ist die erste nationale Einrichtung im staatlichen Netzwerk, deren Ziel es ist, kleinen und mittleren Unternehmen (KMU) die Möglichkeit zu geben, neue Technologien und Geschäftsmodelle, die durch Industrie 4.0 geschaffen wurden, zu testen und Aspekte vom Design bis zur wirtschaftlichen Machbarkeit in einem vorwettbewerblichen Rahmen zu untersuchen Umgebung mit minimalem technischen und finanziellen Risiko. Jedes Testlab hat einen ausgeprägten Produktfokus. Für Swinburne ist dies die additive Fertigung von Verbundwerkstoffen.
„Das Industry 4.0 Testlab for Composites in Swinburne wird einen Prozess im Pilotmaßstab bieten, um die Fertigungskapazitäten Australiens zu verbessern“, sagt Bronwyn Fox, stellvertretender Vizekanzler für Forschung und Unternehmen an der Swinburne University. Fox kam 2015 zu Swinburne und übernahm zunächst die Rolle des Direktors der Fabrik der Zukunft und dann des Direktors des Manufacturing Futures Research Institute der Universität. Bevor sie zu Swinburne kam, war sie Forschungsdirektorin für Carbon Nexus an der Deakin University.
„Das Testlab von Swinburne wird die Funktionen der digitalen Composite-Produktion in einer immersiven Umgebung demonstrieren“, sagt Fox. „Die Prozesse im Pilotmaßstab werden von der Teilekonstruktion über die Optimierung bis hin zum fertigen Produkt digital gesteuert. Außerdem werden wir einen digitalen Zwilling des Prozesses erstellen und die Grenzen der virtuellen Inbetriebnahme verschieben.“
Dieses Composites 4.0-Hub wird in einem neuen, maßgeschneiderten Gebäude untergebracht. „Das gemeinsame CSIRO/Swinburne Testlab konzentriert sich auf ein weltweit erstes Verfahren zur additiven Fertigung von kohlenstofffaserverstärkten Verbundwerkstoffen im industriellen Maßstab“, sagt Dr. Marcus Zipper, Executive Director des Geschäftsbereichs Future Industries von CSIRO. „Damit passt der Standort im Herzen von Claytons Additive Manufacturing-Bezirk hervorragend. Bei CSIRO geht es darum, Chancen für KMU und das breitere Innovationsökosystem zu schaffen, und dieses Testlab ist ein weiteres Beispiel dafür.“
Partner und Prozess
Im Industry 4.0 Testlab for Composites gibt es viele wichtige Partner mit Siemens Australia (Bayswater, Victoria) war einer der ersten, der Swinburne 2017 einen Zuschuss von 135 Mio. offene Plattform für das Internet der Dinge (IoT), MindSphere.
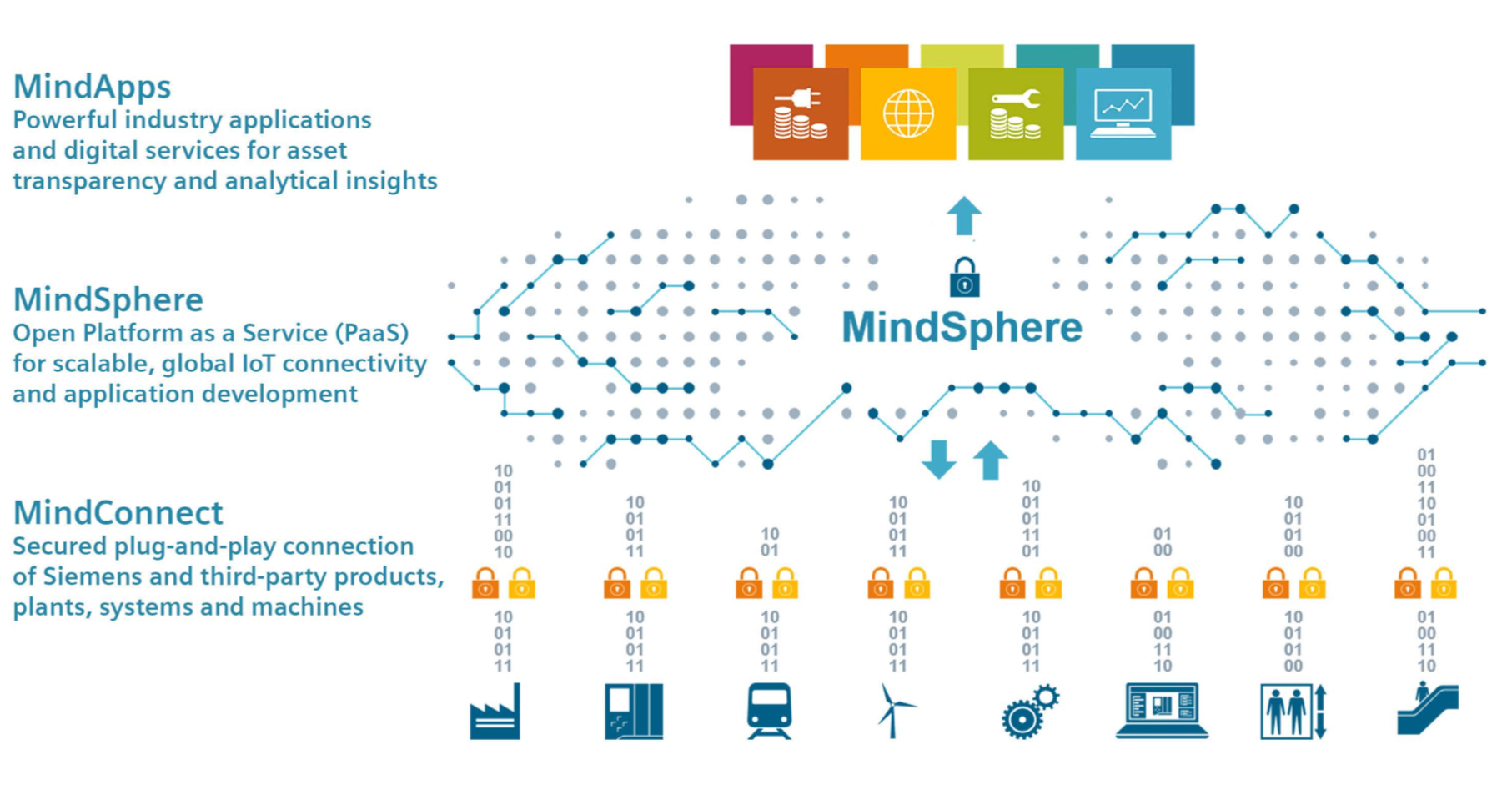
Laut einer Präsentation von Siemens Australien gab es im August 2019 rund 500 digitale Apps/Angebote innerhalb von MindSphere und 1,4 Millionen verbundene Geräte und Systeme. „MindSphere wird es Geräten verschiedenster Hersteller ermöglichen, miteinander zu kommunizieren“, erklärt Fox in ihrer ICCM22-Präsentation „An Industry 4.0 Approach to the 3D Printing of Composite Materials“. Dieses Dokument beschreibt, wie das Swinburne Industry 4.0 Testlab funktioniert:
„Sensoren … ermöglichen es jeder Stufe der Produktionslinie, eine große Menge an Prozessdaten zu sammeln. Diese Informationen werden in einer sicheren lokalen Cloud gespeichert und werden auch sofort verwendet, um Produktionsdaten an andere Maschinen in der Linie weiterzugeben und rückzumelden, wodurch ein sich selbst anpassender Produktionsprozess ermöglicht wird.
Die vorgeschlagene Linie ... ist so konzipiert, dass sie eine Produktinspektion nach jeder Phase des Herstellungsprozesses ermöglicht. Die Inspektionsdaten werden auch in der lokalen Cloud gespeichert. Die Analyse der großen, in der Cloud gespeicherten Datensätze kann zur Entdeckung neuer und unerwarteter Korrelationen zwischen dem Zustand des Endprodukts und den Parametern verschiedener Phasen des Herstellungsprozesses führen, die wiederum zur Optimierung des Produkts genutzt werden können.“
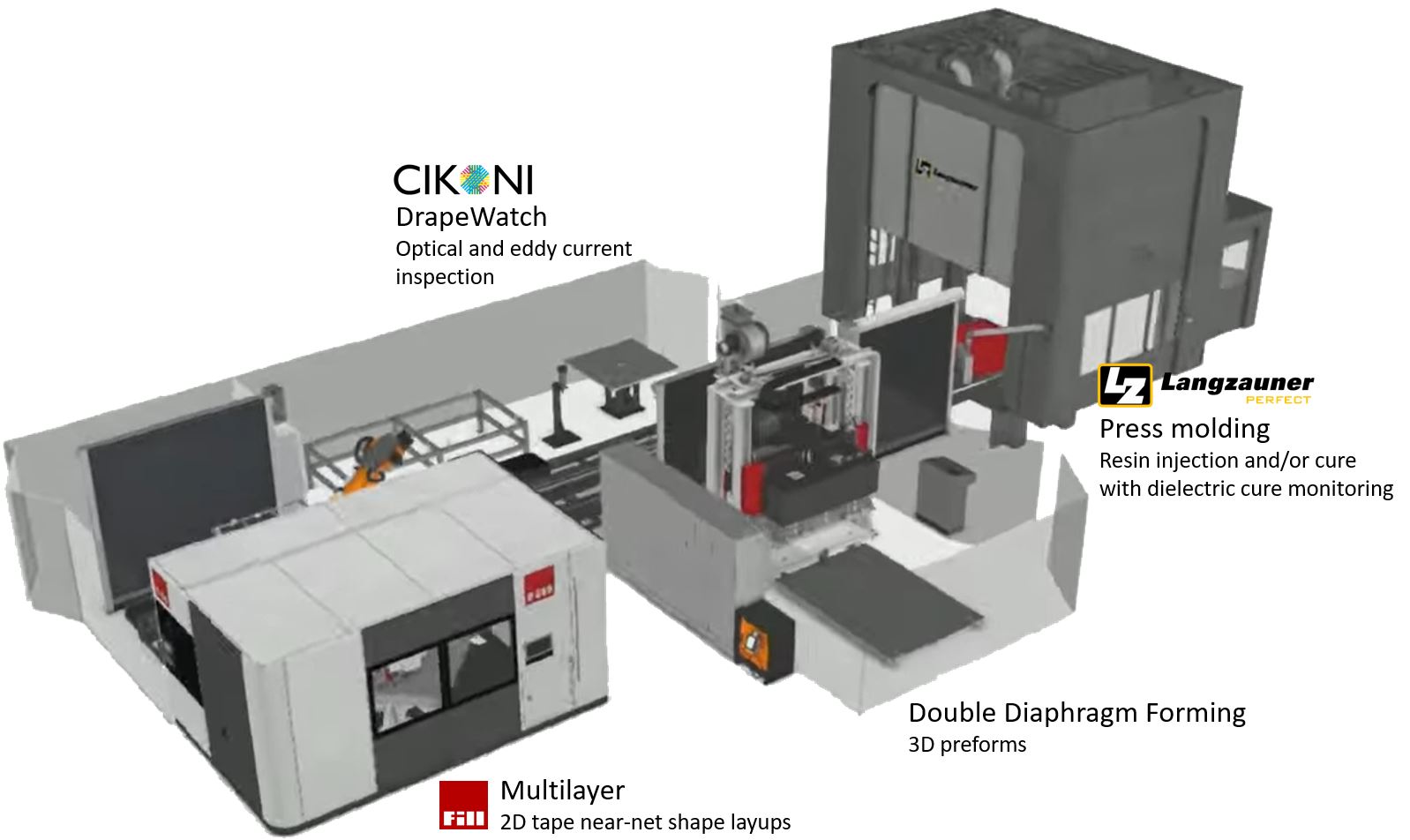
Fox weist auch darauf hin, dass Fertigungslinien für Industrie 4.0-Verbundwerkstoffe nicht von der Stange gekauft werden können. Daher hat Swinburne ein Netzwerk von Lieferanten und Endbenutzern aufgebaut, um das Design und die Entwicklung seiner Composites 4.0 Testlab-Ausrüstung und -Einrichtung zu informieren. Zu den Partnern, die Schlüsselkomponenten liefern, gehören:
FÜLLEN (Gurten, Österreich) hat das Multilayer-System geliefert, das präzise geschnittene und ausgerichtete, unidirektionale Faserbänder in endkonturnahe Formen bis zu einer Größe von 1,6 x 1,6 Metern stapelt. Near Net Shapes mit Klebeband reduzieren den Ausschuss von mehr als 60 % auf weniger als 10 %. Die Bänder werden von Spulen auf einen Drehtisch abgelegt, wobei alle 15 Sekunden eine Schicht fertiggestellt wird. Fox weist darauf hin, dass die Multilayer-Maschine von Fill Bänder aus duroplastischem Prepreg und Towpreg sowie Trockenfasern und niedrig schmelzenden Thermoplasten wie Polyamid (PA) verlegen kann. Es gibt laufende Forschung und Entwicklung für hochschmelzende Thermoplaste wie Polyetheretherketon (PEEK) und Polyetherketonketon (PEKK). „Die Multilayer-Maschine ermöglicht auch Hybridmaterialien, wie das Mischen von Glas- und Carbonfasern und Mischungen mit Naturfasern usw.“, fügt sie hinzu.
Quickstep (Sydney, Australien) ist der größte unabhängige Hersteller von fortschrittlichen Verbundwerkstoffen in Luft- und Raumfahrtqualität in Australien und bietet umfassendes Know-how sowohl in autoklavgehärteten als auch in autoklavierten (OOA) Verbundwerkstoffen. Das patentierte OOA-System von Quickstep, Qure, und seine Hochleistungsversion für Luft- und Raumfahrtanwendungen, AeroQure, sind ein fortschrittlicher Herstellungsprozess für Verbundwerkstoffe, der erhebliche Vorteile gegenüber herkömmlichen Herstellungstechniken wie der Autoklavenhärtung bietet, darunter:
- Niedrige Kapitalkosten für die Einrichtung
- Erheblich kürzere Härtungszykluszeiten
- Reduzierter Energieverbrauch
- Designflexibilität, um die Materialeigenschaften des Endprodukts zu erfüllen oder zu verbessern
- Fähigkeit, komplexe integrierte Teile herzustellen.
Qure verwendet eine unter Druck stehende zirkulierende Wärmeträgerflüssigkeit (HTF), um die Form zu unterstützen und das Teil schnell zu erwärmen und abzukühlen. Niedrigere Druckverarbeitung (Vakuum plus bis zu 2,5 bar) ermöglicht kostengünstigere Werkzeuge. Schnelles Aufheizen der Form und des Materials reduziert die Prozessviskosität, verbessert die Luftabgabe und die Faserbenetzung. Eine niedrigere Viskosität verbessert die Haftung an Waben- und Schaumkernen, was zu einer höheren Schälfestigkeit und einer geringeren Kernquetschung beim Aushärten führt. Das HTF ermöglicht eine hervorragende Temperaturkontrolle, selbst bei dicken Laminaten, die anfällig für exotherme Reaktionen sind.
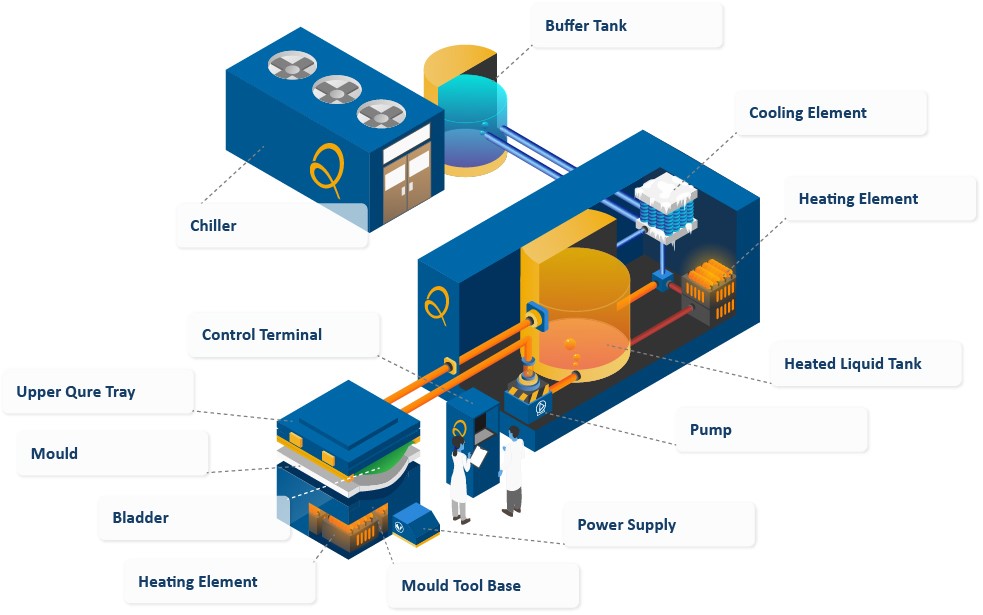
Langzauner (Lambrechten, Österreich) liefert eine Hochtemperatur-Automatenpresse mit bis zu 300 Tonnen Schließkraft, die multiprozessfähig ist – von Varianten des Resin Transfer Moulding (RTM) bis hin zum Thermoformen. Es ermöglicht das Einspritzen von Harz in trockene Preforms, gefolgt vom Härten oder Formpressen von duroplastischen und thermoplastischen Prepregs.
Energieeffizienz/Einsparung erreicht die Presse über Servohydraulik und höchste Genauigkeit auch bei asymmetrischer Belastung durch eine Einkolbensteuerung. Ein leistungsstarker Infrarot (IR)-Ofen erhitzt Materialien schnell auf die gewünschte Verarbeitungstemperatur und gleicht unterschiedliche Dicken durch eine individuelle Heizkörpersteuerung aus. Die schnelle Übergabe des vorgewärmten Materials an die Pressstation wird durch eine Linearachse gewährleistet. Das Hochtemperatur-Plattenheizsystem kann Teile bei Temperaturen von mindestens 400°C formen und ermöglicht die Verarbeitung von fortschrittlichen Thermoplasten wie Polyetheretherketon (PEEK).
Die Presse ist auch doppelmembranrahmenfähig (siehe Blog 2020 zur Doppelmembranumformung). Ein Höchstmaß an Digitalisierung und Überwachung wird durch eine flexible, robuste und benutzerfreundliche Software garantiert.
NETZSCH (Selb, Deutschland) wird eine In-Mold-Cure-Monitoring-Technologie bereitstellen, die eine Kontrolle der Composite-Herstellung basierend auf dem Materialverhalten ermöglicht.
Plataine (Israel) bietet Digitalisierungs-, Optimierungs- und Digital-Twin-Software für die Herstellung von Verbundwerkstoffen, die die Verfolgung von Werkzeugen, Teilen und Rohstoffen, die Erstellung digitaler Zwillinge und die Analyse von Maschinensensordaten zur Optimierung der Teileproduktion ermöglicht. Plataine hat eine breite Palette von Partnerschaften mit Branchenführern und Zulieferern von Verbundwerkstoffen, darunter Siemens.
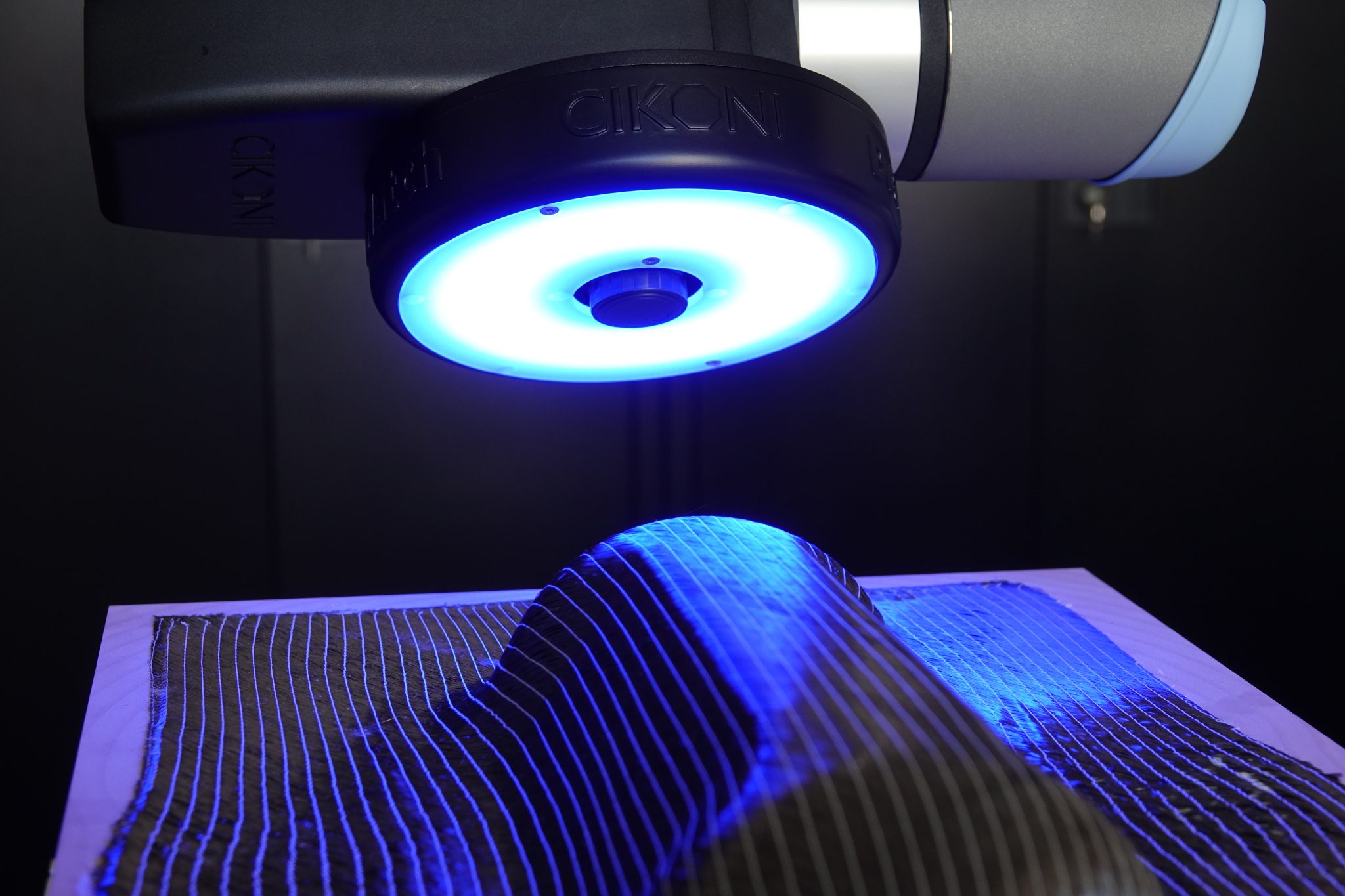
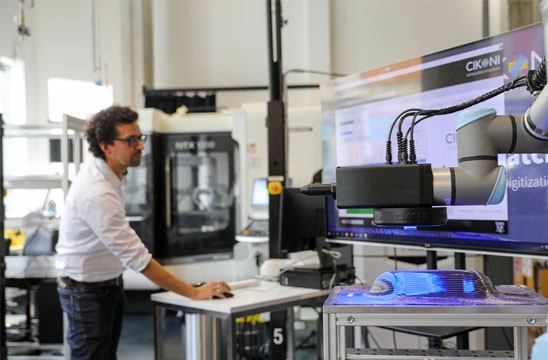
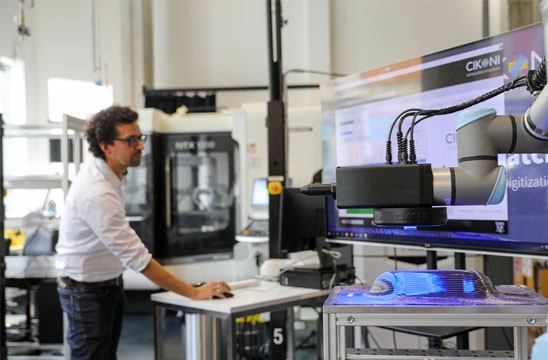
CIKONI (Stuttgart, Deutschland) hat das DrapeWatch-System zur Inline-Inspektion und Digitalisierung sowohl von Preforms als auch von konsolidierten Teilen geliefert. Dieses roboterbasierte 3D-Analysesystem kann Lücken, Fehlausrichtungen und Unregelmäßigkeiten erkennen. Es kombiniert einen visuellen Sensor zur detaillierten Oberflächeninspektion mit einem EddyCurrent-Sensor für interne Defekte und eingehende Materialanalysen. Die Daten werden von den Algorithmen der künstlichen Intelligenz des Systems analysiert, um Fehler frühzeitig zu erkennen und kostspielige Wiederholungen zu vermeiden. Eine Schnittstelle zur Finite-Elemente-Analyse (FEA) ermöglicht den Export von Faserwinkelergebnissen in Simulationsmodelle zur Bewertung der Auswirkungen von Fehlern auf die Teileleistung. Das modulare System lässt sich auch durch die Integration von Thermografie-, Ultraschall- oder Laserscanning-Geräten erweitern.
Die Geräte von Fill und Langzauner werden Mitte 2020 installiert. „Fill hat für uns Experimente gemacht“, sagt Fox, „und wir haben Personal nach Österreich geschickt, um an bestimmten Teilen sowie in der Digitalisierung zu trainieren. Sobald die gesamte Prozessausrüstung in Betrieb genommen ist, werden wir die RFID-Technologie (Radio Frequency Identification) von Plataine verwenden und in seine neueste Edge-Computing-Plattform PlataineEdge skalieren, die eine Echtzeitanalyse und Kommunikation zwischen Maschinen ermöglicht.“
Ein weiterer Teil der Vision für das Composites 4.0 Testlab von Swinburne besteht darin, eine flexible Fertigung zu ermöglichen, die sich sehr schnell an sich ändernde Branchenanforderungen anpassen kann:
"In einer typischen Produktionslinie erfordert eine Produktänderung oder -modifikation erhebliche Gerätemodifikationen und manuelle Eingriffe. Damit ein solcher Produktwechsel rentabel ist, ist daher eine Mindestchargengröße des neuen Produkts erforderlich. Im Gegensatz dazu ermöglichen Smart Factories in der Vision Industrie 4.0 individuelle Kundenwünsche und sogar Einzelstücke gewinnbringend herzustellen. Eine solche Fabrik kann im Namen der Kunden und Lieferanten problemlos auf kurzfristige Änderungen reagieren. Folglich besteht eines der Hauptziele der vorgeschlagenen Fertigungslinie darin, verschiedene Produkte mit minimalem oder keinem manuellen Eingriff herstellen zu können.“ — Fox und Subic, "Ein Industrie 4.0-Ansatz für den 3D-Druck von Verbundwerkstoffen"
ARENA2036 und Links zu globalen Wertschöpfungsketten
Neben der Bereitstellung einer digitalisierten Fabrik für physische Verbundwerkstoffe 4.0 wird Swinburne auch die Arbeitskräfte der nächsten Generation ausbilden. Letzteres wird durch einen Zuschuss in Höhe von 1 Million US-Dollar/vier Jahre des australischen Global Innovation Linkages Program ermöglicht. Ein wichtiger Partner dieser Initiative ist ARENA2036, das industriegetriebene Campus-F&E-Programm der Universität Stuttgart, das sich selbst als „Die hochflexible Forschungsplattform für Mobilität und Produktion der Zukunft“ bezeichnet. Gefördert vom Bundesministerium für Bildung und Forschung (BMBF, Bonn, Deutschland) und geführt als eingetragener Verein mit 38 Mitgliedern aus Wissenschaft und Wirtschaft, verfügt die ARENA2036 über eine „STARTUP AUTOBAHN“ und ein 10.000 Quadratmeter großes Gebäude, davon 4.700 Quadratmeter ist eine offene Produktionshalle mit einer 16 Meter hohen Decke und einem 10-Tonnen-Industriekran. Swinburne trat ARENA2036 2018 als Mitglied bei.
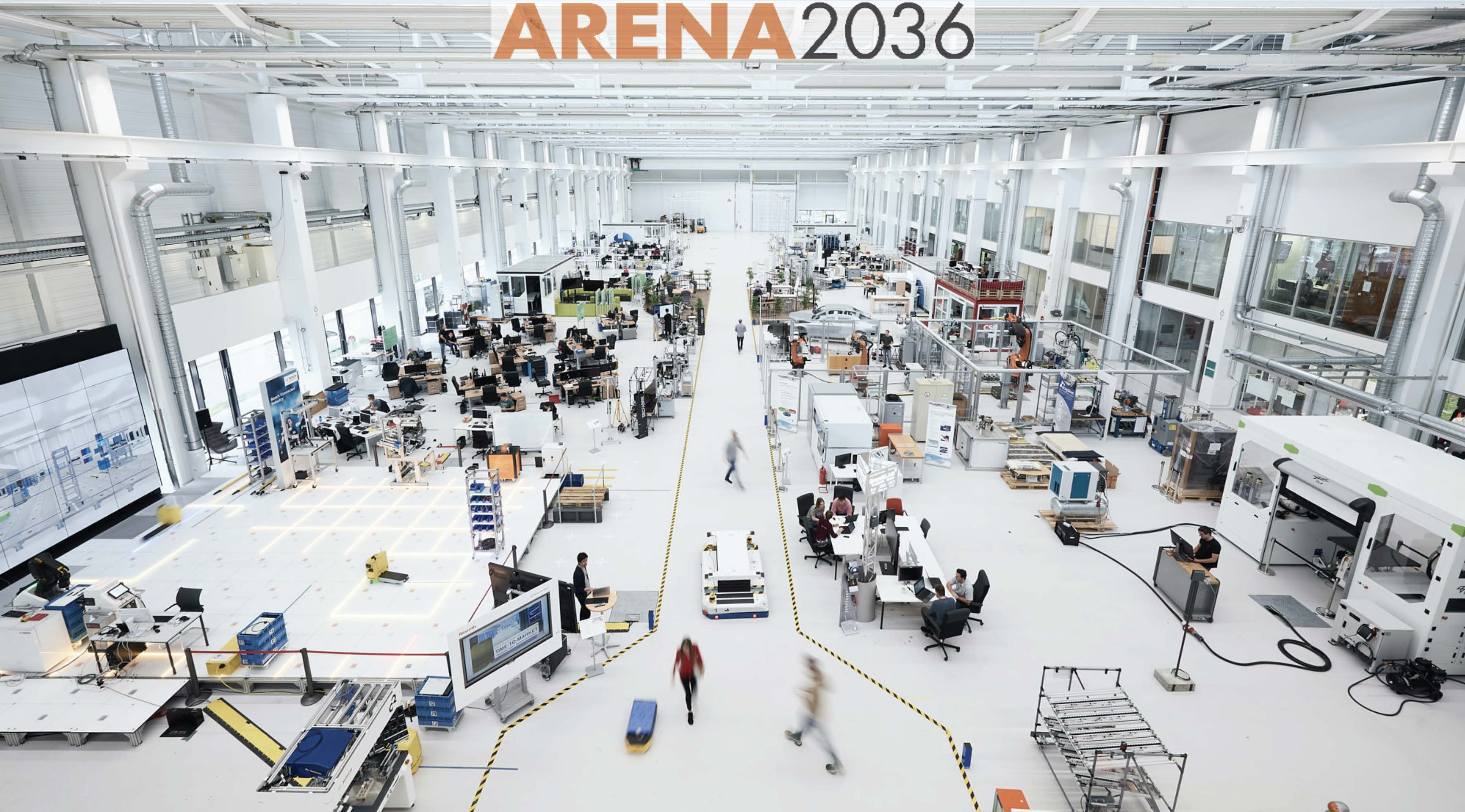
Das Composites 4.0 Testlab von Swinburne und ARENA2036 kooperieren über ein 3,6-Millionen-Dollar-Programm, das vom Global Innovation Linkage (GIL)-Programm der australischen Regierung zur Industrie 4.0-Fertigung von Leichtbau-Verbundwerkstoffen in großen Stückzahlen unterstützt wird, mit Schwerpunkt auf einer spezifischen Produktionstechnologie, die durch flexible Werkzeugsysteme und digitale Zwillingstechnologie. Es enthält:
- F&E und Kommerzialisierung, um gemeinsame Start-ups zu erleichtern.
- Gemeinsame Rekrutierung, Co-Betreuung und Austausch von Doktoranden
- Gemeinsame Forschungsworkshops und Symposien.
Diese Partnerschaft sieht auch gemeinsame F&E-Projekte mit dem Fraunhofer-Institut für Produktionstechnik und Automatisierung und dem Institut für Arbeitswirtschaft und Organisation (Fraunhofer IPA und IAO, Stuttgart) vor, darunter auch Doktorandenpraktika am Institut für Flugzeugbau (IFB) der Universität Stuttgart Industrie 4.0-Bereiche. „Das GIL-Projekt ist ein wichtiger Meilenstein für fortschrittliche Composite-Prozesse und auch für die Zusammenarbeit von SUT, Universität Stuttgart und ARENA2036“, sagt Professor Peter Middendorf, Direktor des IFB. „Wir sind stolz, Partner im Projekt selbst zu sein und zwei weitere von der Bundesregierung geförderte Verbundforschungsprojekte mit direktem Bezug zur GIL ankündigen zu können.“
„Wir werden eine neue Kohorte digital versierter gemeinsamer Doktoranden zwischen Swinburne und der Universität Stuttgart ausbilden“, sagt Fox. „Wir werden nicht nur Composite 4.0-Prozesse weiterentwickeln, sondern auch globale Partnerschaften festigen und neue Produkte schaffen, die aus Australien exportiert werden können, insbesondere in neue Mobilitätsmärkte. Durch diese internationalen Kooperationen wird das Industry 4.0 Testlab von Swinburne australische KMU aktiv in globale Wertschöpfungsketten einbinden. Wir haben dies bereits mit unserem Partner Imagine Intelligent Materials demonstriert und freuen uns darauf, dies auf weitere australische Innovatoren auszudehnen.“
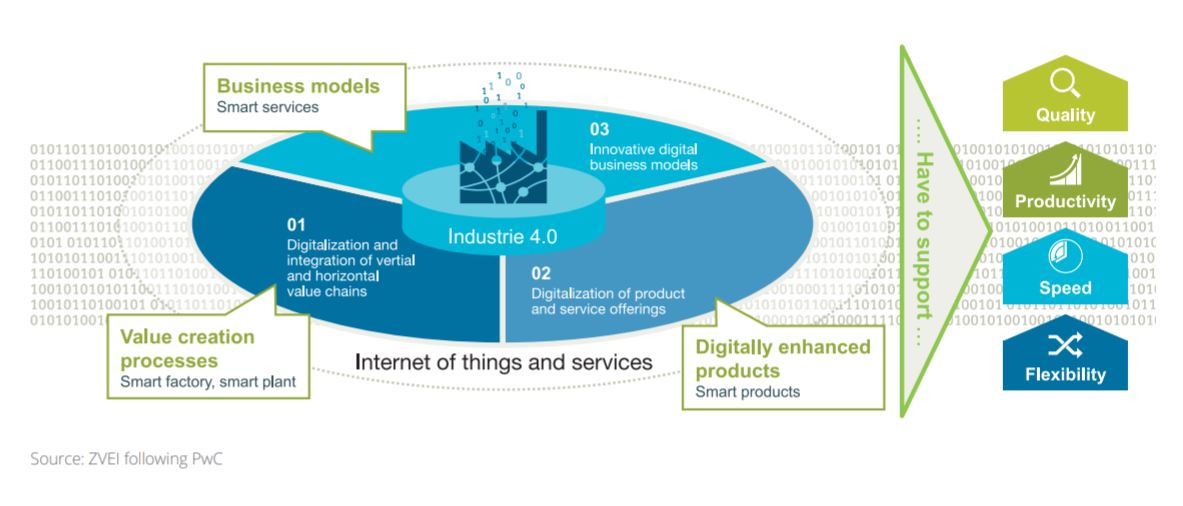
„In der schnelllebigen digitalen Fertigung der Zukunft wird der internationale Wettbewerb hart sein“, sagt Fox. „Deshalb ist unsere Entwicklung dieser Composites 4.0-Fähigkeiten und Mitarbeiter jetzt so wichtig.“
Das Industry 4.0 Testlab for Composite Additive Manufacturing an der Swinburne University wird im Dezember 2020 eröffnet. Bleiben Sie auf dem Laufenden bei CW für zukünftige Updates und lesen Sie unser Juli-2020-Feature „Composites 4.0:Digitale Transformation, adaptive Produktion, neue Paradigmen“ zusammen mit seinen fünf Online-Seitenleisten:
- Composites 4.0:Digitaler Zwilling vs. digitaler Thread
- Zaero-Projektupdate
- Composites 4.0:Wo soll ich anfangen?
- Kein Business Case für das Lehren von Robotern
- Composites 4.0-Architektur und Ontologie
Harz
- Der Wert der additiven Fertigung in der Automobilindustrie
- Einführung von AM Fridays und Additive Podcast
- Henkel bietet Werkstoffplattform für die additive Fertigung
- Essentium und Lehvoss kooperieren bei der Entwicklung von Materialien für die additive Fertigung
- High-Flow-POM für die Medizin- und Gesundheitsbranche
- Nachhaltige Thermoplaste und additive Fertigung bilden in Colorado eine Allianz
- Was ist additive Fertigung? - Typen und Arbeitsweise
- Der Fall für den 3D-Druck in der Fertigung
- Top 5 logistische Herausforderungen und Lösungen für die Fertigungsindustrie
- Umfrage von Protolabs und Censuswide deutet darauf hin, dass die Fertigung nicht bereit für Industrie 4.0 ist