Automatisiertes Fügen von hybriden Metall-Thermoplast-Verbundstrukturen
Ermöglichung von Hybridverbindungen im industriellen Maßstab
FlexHyJoin demonstriert einen Massenproduktionsprozess zur Herstellung einer thermoplastischen Verbunddachversteifung mit geschweißten Metallhalterungen für den Einbau in eine Metallkarosserie, wie im Anwendungsfall des Projekts, dem Fiat Panda Stadtauto. Quelle | IVW
Hybride Metall-Verbundstrukturen sind weiterhin für Automobil- und Luft- und Raumfahrtanwendungen interessant und bieten reduziertes Gewicht und verbesserte Leistung, indem sie „das richtige Material an der richtigen Stelle“ platzieren. Thermoplastische Verbundwerkstoffe (TPCs) sind für solche Multi-Material-Strukturen aufgrund ihrer schnellen Verarbeitung, einschließlich ihrer Schweiß- und Thermoformbarkeit, attraktiv. Das Verbinden von Verbundwerkstoffen mit Metallen beruhte jedoch bisher hauptsächlich auf mechanischen Befestigungselementen, die Bohrlöcher erfordern, die tragende Fasern beschädigen. Kleben wurde auch verwendet, aber eine Reihe von Thermoplasten sind auf diese Weise schwer zu kleben; außerdem erhöhen Klebstoffe Material und Gewicht. Zum Beispiel der BMW i3 , das ein kohlenstofffaserverstärktes Kunststoff (CFK)-Chassis und Kunststoff-Karosserieteile verwendet, verwendet 16 Kilogramm Klebstoff, was dem Gewichtseinsparungspotenzial von Verbundwerkstoffen teilweise entgegenwirkt.
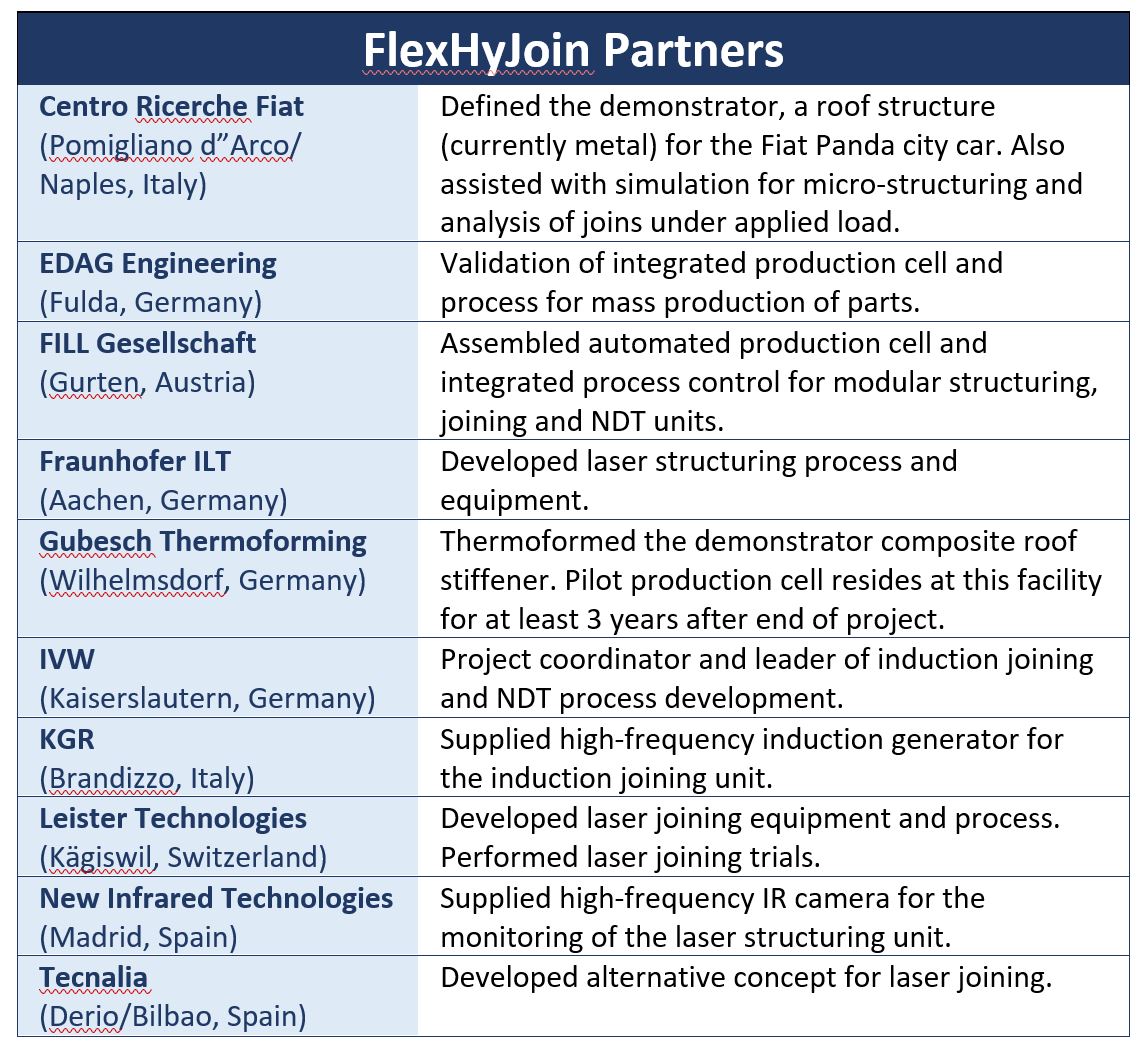
FlexHyJoin ist ein Projekt, das vom Forschungs- und Innovationsprogramm Horizon 2020 der Europäischen Union finanziert wurde und von Oktober 2015 bis Dezember 2018 durchgeführt wurde und sich den Herausforderungen beim Fügen von TPC- und Metallteilen widmete. Koordiniert vom Institut für Verbundwerkstoffe (IVW) – einer gemeinnützigen Forschungseinrichtung des Landes Rheinland-Pfalz und der Technischen Universität Kaiserslautern – brachte FlexHyJoin 10 Partner aus ganz Europa zusammen, um einen automatisierten Prozess zu entwickeln, der ein TPC-Automobildach ermöglicht Struktur zum Einbau in eine Metallkarosserie (BIW). Die Strategie bestand darin, eine gewichtsneutrale, hochfeste Verbindung – ohne Klebstoffe oder Befestigungsmittel – herzustellen, indem Metallkonsolen laservorbehandelt und diese per Induktion und Laserfügen an der Dachversteifung befestigt werden. Dies wurde in einer einzigen, automatisierten Produktionszelle mit integrierter Prozesskontrolle und zerstörungsfreier Inline-Prüfung (ZfP) erreicht.
Hybrid-Demonstrator in 140 Sekunden
Projektpartner Centro Ricerche Fiat (Pomigliano d’Arco/Neapel, Italien) lieferte Spezifikationen für das Demonstratorteil – eine Dachversteifung für den Fiat Panda Stadtauto, das derzeit aus Stahl gefertigt wird. Für FlexHyJoin wurde das Teil aus thermoplastischem Verbundmaterial (Abb. 1) von Gubesch Thermoforming (Wilhelmsdorf, Deutschland) unter Verwendung von 1,5 Millimeter dickem Tepex Dynalite 102 gewebtem Glasfaser/Polyamid 6 (PA6) Organoblech von Bond-Laminates (Brilon, Deuschland). Um diese TPC-Dachversteifung mit dem Panda zu verbinden 's Stahl BIW, ein Satz seitlicher Konsolen (links und rechts) aus 0,7 Millimeter dickem DC04-Stahl wurde an den Enden lasergeschweißt. Eine Mittelkonsole aus dem gleichen Material wurde mittels Induktionsfügen befestigt. FlexHyJoin hat gezeigt, dass beide Fügeverfahren für die industrielle Herstellung von Hybridstrukturen verwendet werden können.
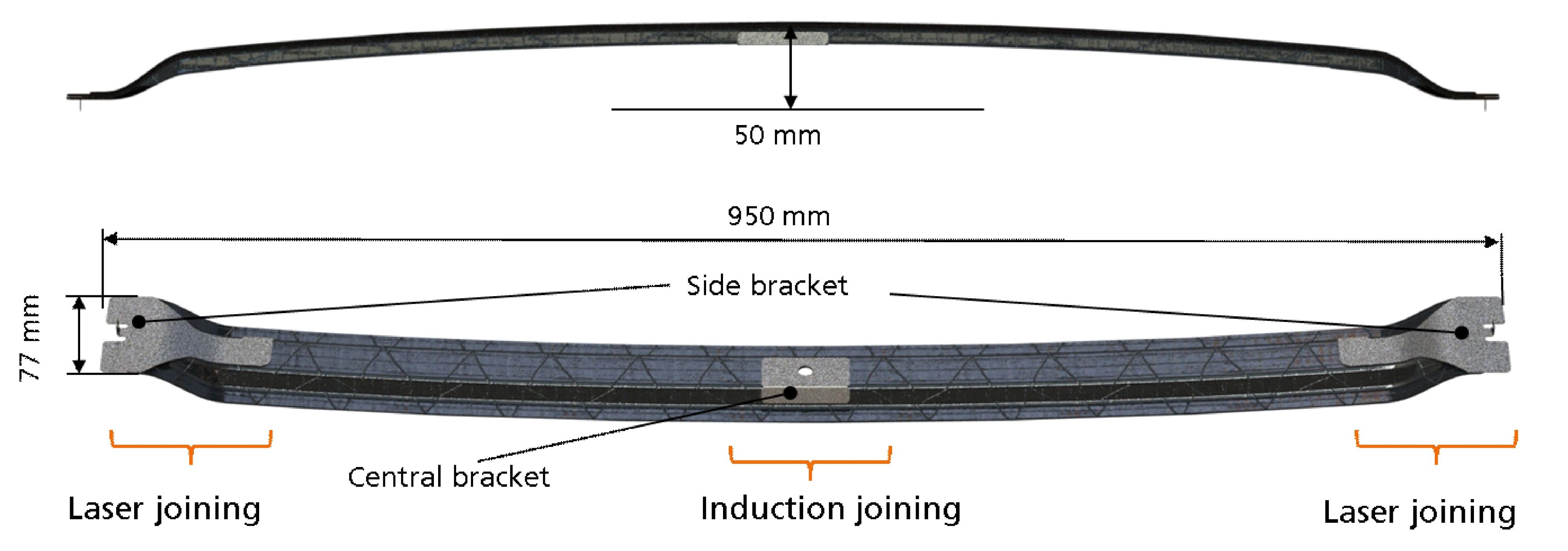
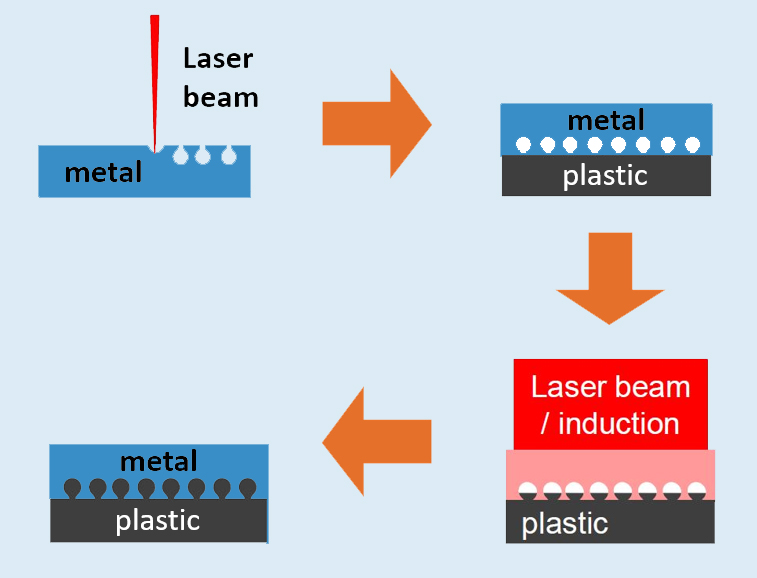
Abb. 1 Oberflächenstrukturierung für das Hybridfügen
FlexHyJoin demonstriert das Laser- und Induktionsfügen von Stahlhalterungen an eine gestanzte GF/PA6-Dachversteifung (oben ). Diese Hybridverbindungen basieren auf einer Oberflächenbehandlung der Metallbrackets, um Hinterschneidungen zu erzeugen, die während der Fügeprozessschritte mit geschmolzenem Kunststoff gefüllt werden (unten ).
Quelle | IVW
Ein einfaches Aufschmelzen der PA6-Matrix auf die Stahlhalterungen würde keine Verbindung mit ausreichender Festigkeit erzeugen, um die strukturellen Anforderungen zu erfüllen. Daher war vor dem Fügen eine Laseroberflächenbehandlung erforderlich. „Die Oberfläche der Brackets wurde per Laser strukturiert, um Hinterschneidungen zu erzeugen“, erklärt Johannes Voithofer, Projektleiter bei der Fill Gesellschaft (Gurten, Österreich), die mit dem Aufbau und der Integration der automatisierten Fertigungszelle beauftragt war. „Die behandelten Brackets werden auf das Kompositteil aufgesetzt. Beim Fügen werden dann Wärme und Druck aufgebracht, wodurch die PA6-Matrix aus dem Verbund in die laserinduzierten Hinterschneidungen fließt [siehe Abb. 1].“ Das Strukturierungsverfahren wurde von einem weiteren Partner, dem Fraunhofer-Institut für Lasertechnik (ILT, Aachen, Deutschland) entwickelt und führt zu einer Metall-Verbund-Verbindung, die sowohl Materialhaftung als auch mechanische Sicherung kombiniert.
Fügeteile werden dann an eine ZfP-Station übergeben, wo sie mittels einer Art Thermografie auf Fehler gescannt werden. „Halogenstrahler werden zur modulierten Erwärmung der Verbundoberfläche verwendet“, erklärt Vitalij Popow, IVW-Wissenschaftlicher Mitarbeiter und Leiter der Entwicklung des FlexHyJoin-ZfP und der Prozesskontrolle. „Dies führt zu einem oszillierenden Temperaturfeld innerhalb der Verbundstruktur. Wir analysieren die thermische Reaktion der Oberfläche über die Zeit und identifizieren Defekte in den Fugen.“ Die vollautomatische Prüfung erfolgt innerhalb der Fertigungszelle für jedes gefertigte Bauteil. Die Validierung des Prozesses wurde an etwa 400 Verbindungen durchgeführt.
Die automatisierte Fertigungszelle FlexHyJoin, wie derzeit konfiguriert, führt parallel Laserstrukturieren, Fügen und NDT mit Zykluszeiten von 81 Sekunden, 98-108 Sekunden bzw. 100 Sekunden aus, ohne Zeit für den Robotertransfer von Teilen zwischen den Stationen. Laut Voithofer beträgt die Zykluszeit pro fertigem Hybridteil rund 140 Sekunden.
Abb. 2 Hybridverbindung im industriellen Maßstab ermöglichen
Die Pilotfertigungszelle FlexHyJoin verfügt über drei modulare Stationen zum Oberflächenstrukturieren, Fügen und ZfP. Der einzelne Handling-Roboter der Zelle übergibt die Bauteile aus der Ladeschublade an jede dieser Stationen und legt fertige Hybridteile in eine angrenzende Schublade. Quelle | IVW und Füllung
Laserstrukturierung
Das Laserstrukturierungsverfahren erzeugt auf der Fügefläche der Metallbrackets Linien mit hinterschnittenen Geometrien. Bei FlexHyJoin waren die Hinterschneidungen 75 Mikrometer breit und 215 Mikrometer tief. Diese Abmessungen sowie die Anzahl der Linien und das Gesamtmuster der Linien können alle individuell angepasst werden und sind idealerweise auf die Anforderungen an Teil- und Zykluszeit abgestimmt.
„Die Position sowie die Anzahl der Mikrostrukturen auf der Fügefläche können an die Belastung im Bauteil angepasst werden“, erklärt Stefan Weidmann, IVW-Wissenschaftlicher Mitarbeiter und Leiter des Entwicklungsteams für die Induktionsfügeanlage FlexHyJoin. „Der Abstand zwischen Mikrostrukturen kann in hochbelasteten Bereichen der Fügefläche verringert und in weniger belasteten Bereichen vergrößert werden, um einen effizienten Mikrostrukturierungsprozess zu ermöglichen.“
Die Strukturierung erfolgt durch Abtragen der Metallbracketoberfläche mit einem Hochleistungs-Singlemode-Faserlaser von IPG Photonics (Burbach, Deutschland). Dieser YLR-1000-WC-Laser hat eine maximale Leistung von 1.000 Watt bei einer Emissionswellenlänge von 1.070 Nanometern. „Für den Mikrostrukturierungsprozess haben wir den Singlemode-Faserlaser wegen seiner hohen Fokussierbarkeit bei einer Spotgröße von etwa 40 Mikrometern eingesetzt“, erklärt Christoph Engelmann, Teamleiter Polymerbearbeitung am Fraunhofer ILT.
Der Laser befindet sich in einem optischen Kopf, der an einem ABB 1200-Roboterarm montiert ist. „Im Inneren des Optikkopfes haben wir zwei galvanometrische Spiegel, um den Strahl in ein 240 mal 240 Millimeter großes Arbeitsfeld umzulenken“, erklärt Engelmann. „Außerdem gibt es eine bewegliche Linse zum Nachführen der Z-Höhe (Z-Shifter). Mit dem Roboter haben wir lediglich den Scankopf über den Metallbauteilen positioniert, dann wird der Strahl durch die Spiegel umgelenkt und die Z-Position für jede einzelne Zeile der Mikrostruktur durch den Z-Shifter angepasst. Somit gibt es während der Bearbeitung keine Bewegung des Kopfes. Auf diese Weise können wir 2,5D-Teile behandeln, wobei wir für jede einzelne Linie in derselben Z-Position bleiben, uns aber zwischen den Linien anpassen können.“
„Aus Sicherheitsgründen sind sowohl die Strukturierungs- als auch die Fügeeinheit gekapselt“, erklärt Voithofer die schwarzen Schränke in der Pilotfertigungszelle (Bild 2). Somit bleibt ein automatisches Tor/Tür während des Laserbetriebs abgesenkt, öffnet sich zum Entnehmen von Fertigteilen und Einlegen neuer.
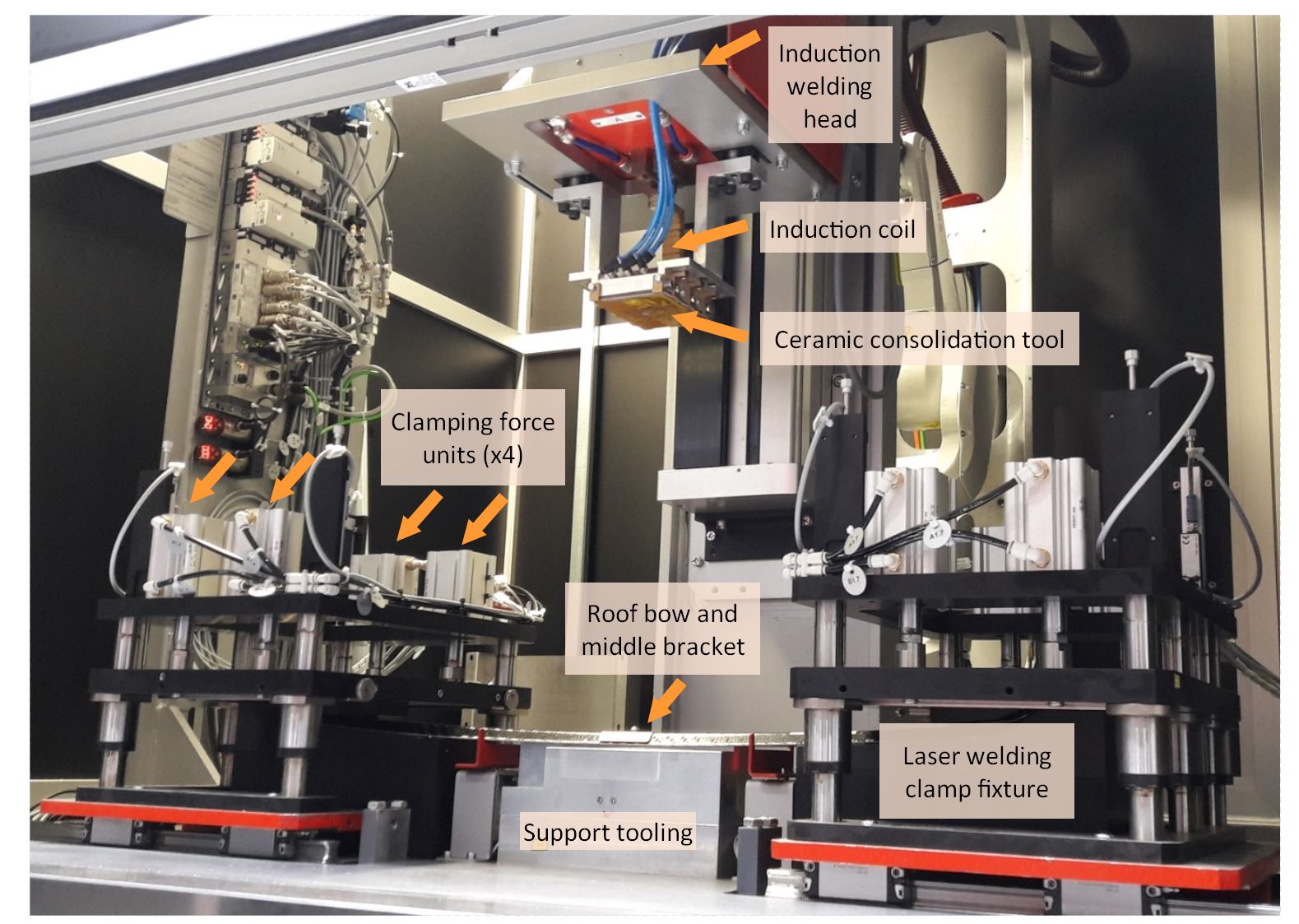
Abb. 3 Induktions- und Laserfügezelle
In der Fügezelle wird das Induktionsfügen verwendet, um die Mittelkonsole zu befestigen, während das Laserfügen verwendet wird, um die Seitenkonsolen an jedem Ende des Verbunddachspriegels zu verbinden. Quelle | IVW und Füllung
Induktions- und Laserfügen
Angrenzend an die Strukturierungszelle befindet sich die Fügezelle, die zwei unterschiedliche Arbeitsgänge umfasst:das Induktionsfügen des Mittelbügels und das Laserfügen des linken und rechten Seitenbügels. „Bei größeren Teilen mit mittlerer Komplexität wie dem Mittelhalter ist das Induktionsfügen das geeignetere Fügeverfahren“, sagt Weidmann. „Ein keramisches Konsolidierungswerkzeug mit Induktor übt Druck auf die Fügestelle aus und ist durchlässig für das elektromagnetische Feld, was zu einem effizienten Energieeintrag in die Metallhalterung zum Erwärmen führt. Dies ist praktisch für flache Formen, aber schwieriger für komplexe Formen, wie beispielsweise die Geometrie der Seitenhalterungen. Daher war es für diese effektiver, das Laserfügen zu verwenden.“ Weidmann fügt hinzu:„Das Induktionsfügen eignet sich am besten für große Teile und mittlerer Komplexität, während das Laserfügen besser für Teile mit hoher Komplexität geeignet ist.“
Ein gebohrtes Loch in der Dachversteifung aus Verbundwerkstoff richtet sie oben auf den Stützwerkzeugen aus, die so geformt ist, dass sie der Krümmung der thermogeformten Versteifung entspricht. Ein lasergeschnittenes Loch in der mittleren Halterung positioniert sie auf der Dachversteifung, während die seitlichen Halterungen nach ihrer Form ausgerichtet sind, die den Enden der Dachversteifung entspricht.
„Die mittlere Klammer wurde mit diskontinuierlichen verbunden Induktionsverbindung. „Das ist im Wesentlichen quasi-statisches Pressfügen“, sagt Weidmann, „was einfach bedeutet, dass es sich um einen statischen Prozess handelt, bei dem an einer Stelle eine flächige Verbindung erreicht wird, aber es gibt eine Bewegung in z-Richtung, weil sich die Dicke des Verbundwerkstoffs leicht ändert auf den während des (Induktions-)Fügens ausgeübten Konsolidierungsdruck.“
Die Induktionsfügeeinheit enthält einen Hochfrequenzgenerator KGR (Brandizzo, Italien), um die Induktionsspule mit einem elektrischen Wechselfeld zu versorgen. Der Kopf wird über einen Elektromotor und eine Spindel bewegt (Abb. 3), so dass das Keramikkonsolidierungswerkzeug nach unten auf das Metallbracket drückt. Die Induktionsspule im Konsolidierungswerkzeug bewirkt eine Erwärmung des Metalls, wodurch die Verbundmatrix schmilzt und die Verbindung entsteht. „Während des Heizens und Kühlens wird Druck ausgeübt“, bemerkt Weidmann.
Das Laserfügen der Seitenkonsolen beginnt gleichzeitig mit dem Induktionsfügen. Zwei Spannvorrichtungen, die sich auf beiden Seiten des Stützwerkzeugs befinden, können eine Spannkraft von 4.000 Newton auf die seitlichen Halterungen aufbringen. „Die Klemmung ist notwendig, um den Spalt zwischen Verbund- und Metallbauteilen zu minimieren“, erklärt Voithofer. „Das verhindert Hohlräume in der Fuge.“ Nach Aufbringen der Klemmkraft fährt der Laserkopf in Position. Es ist mit einem LineBeam-Diodenlaser von Leister Technologies (Kägiswil, Schweiz) ausgestattet. Johannes Eckstaedt von Leister erklärt, dass dieser Laser eine maximale Ausgangsleistung von 600 Watt bei einer Emissionswellenlänge von 980 Nanometern hat. Der Strahl wird durch optische Linsen zu einer 27 Millimeter mal 1 Millimeter großen Linie geformt und auf die Metallhalterung fokussiert. Der Laserkopf ist an einem Roboterarm montiert, der es ihm ermöglicht, sich entlang der geformten Halterungsoberfläche zu bewegen. „Wir stellen für jeden Bereich der Klammern unterschiedliche Geschwindigkeiten ein, um eine homogene Fügetemperatur zu erreichen und die thermische Belastung für beste Fügeergebnisse zu reduzieren“, sagt Eckstaedt.
Im Allgemeinen kann beim Laserfügen entweder ein Transmissions- oder ein Wärmeleitungsfügen verwendet werden. Beim Lasertransmissionsfügen muss der zu fügende Verbund für die gewählte Wellenlänge des Lasers transparent sein. Der Laser durchdringt dann den Verbund, trifft auf die Metalloberfläche des Brackets und erwärmt diese. Im FlexHyJoin-Demonstrator wurde diese Methode jedoch nicht angewendet, da das Organoblech-Laminat der Dachversteifung nicht lasertransparent war. Stattdessen wurde die alternative Methode des Wärmeleitungsfügens verwendet. Dabei wird der Laser einfach direkt auf die Metalloberfläche aufgebracht, die Wärme durch das Metallgrundmaterial auf den Verbundwerkstoff leitet, die PA6-Matrix bei 220-300 °C schmilzt und die Verbindung herstellt. „Aufgrund der hohen Wärmeleitfähigkeit der Stahlhalterungen verteilt sich die Laserwärme schnell und fügt die Seitenhalterungen effizient zusammen“, sagt Voithofer.
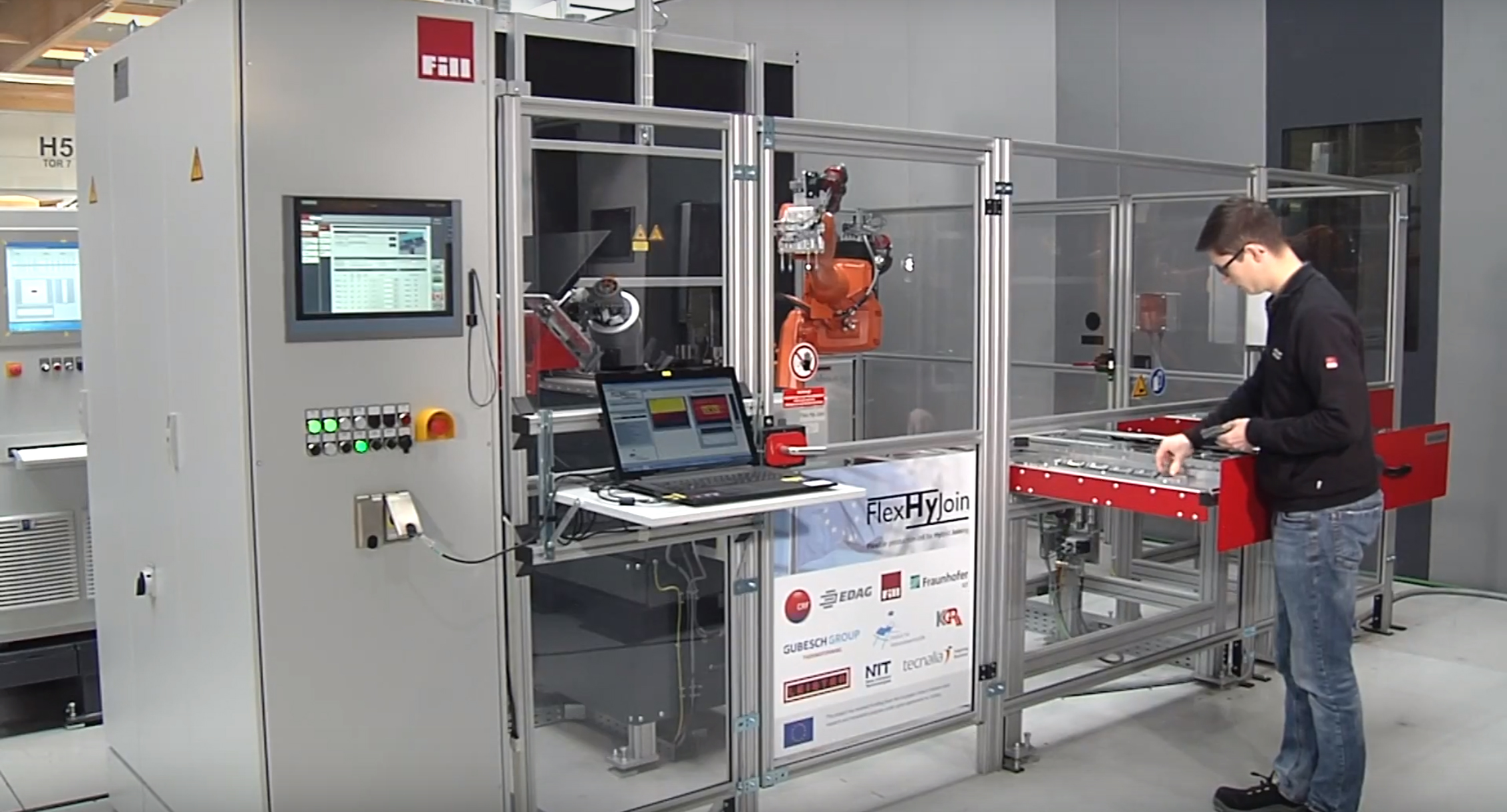
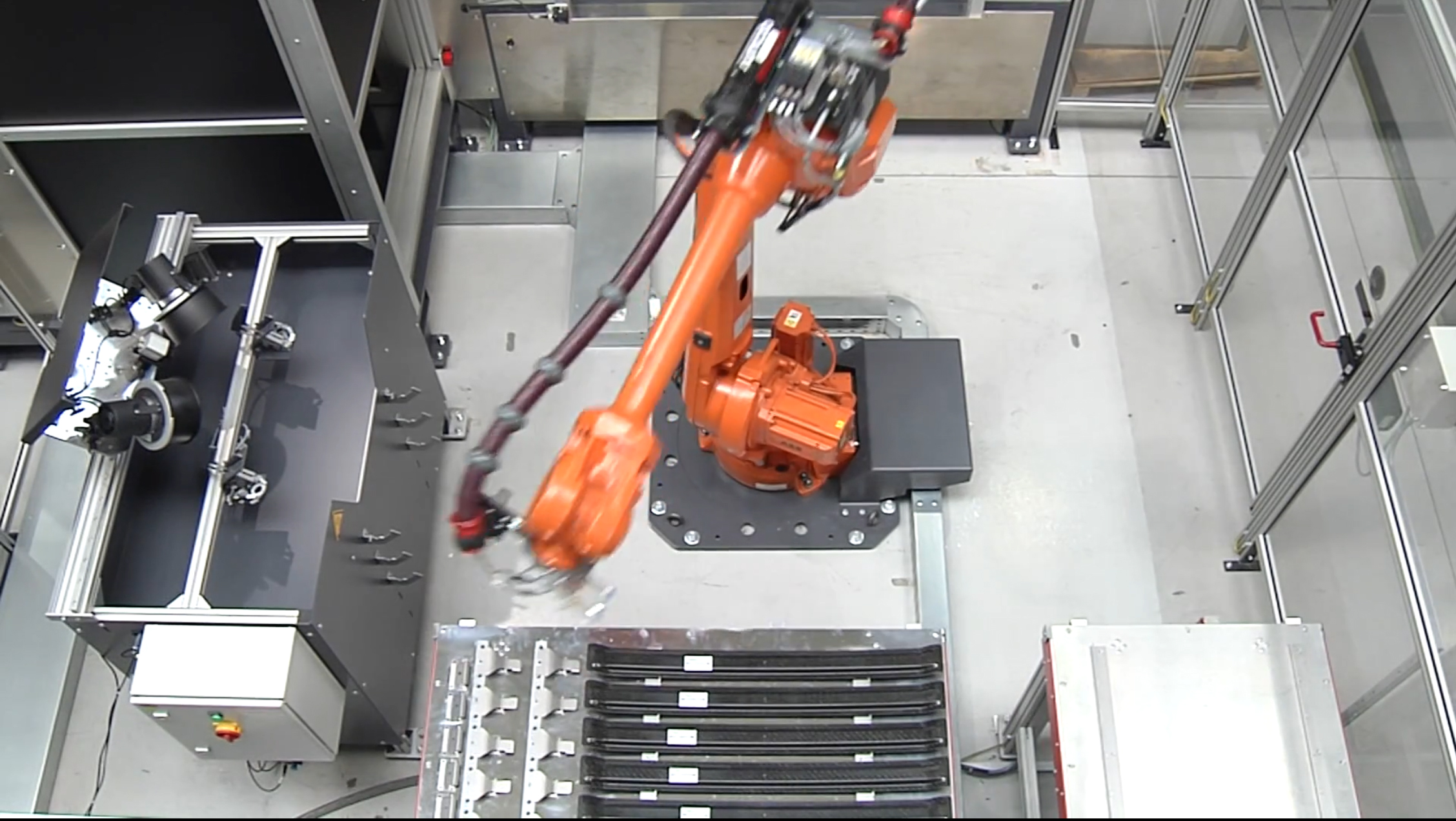
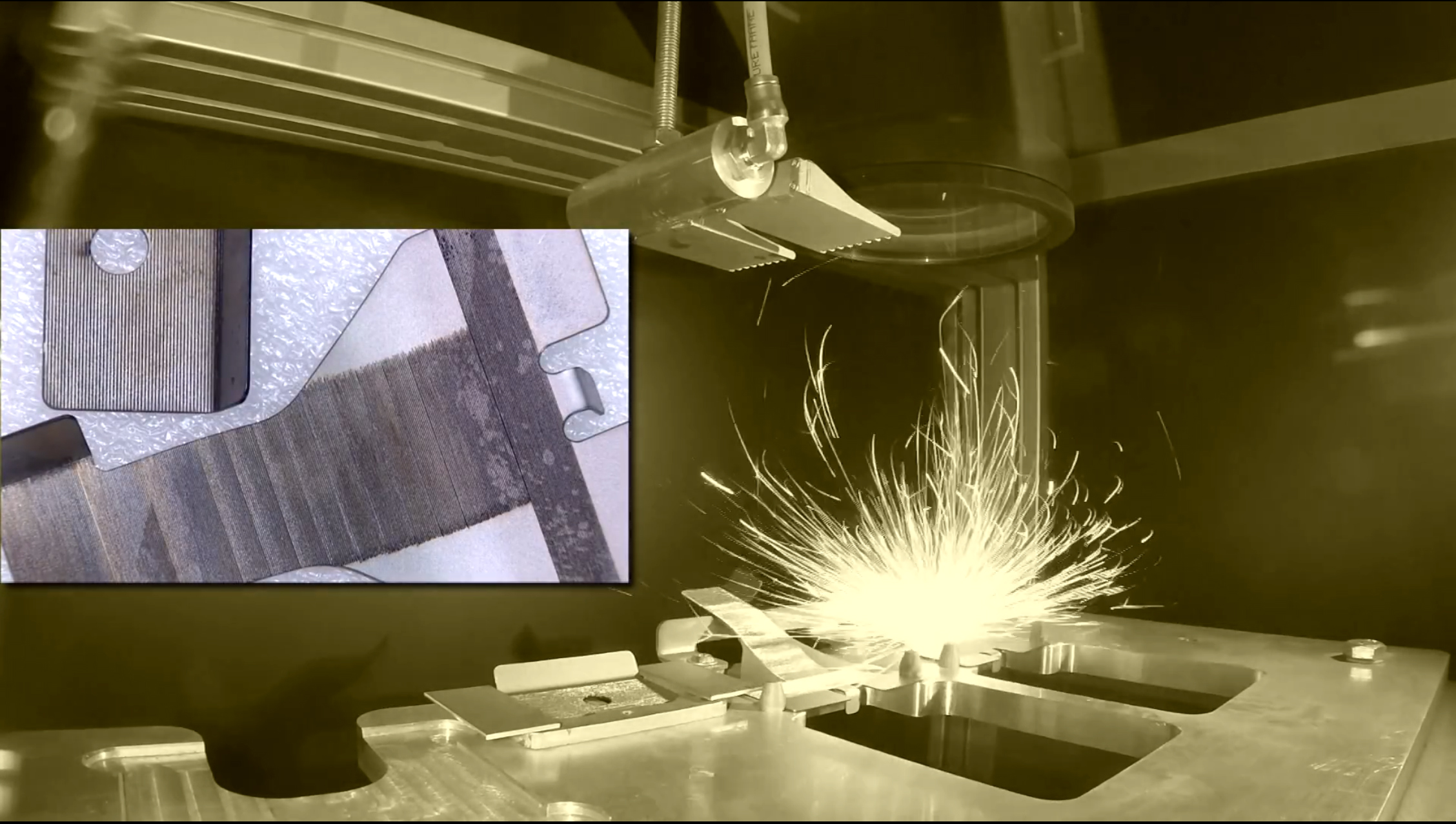
Schritt 3. Im Inneren der Strukturierungszelle erzeugt ein Hochleistungs-Faserlaser Hinterschneidungen in der Oberfläche der zu verbindenden Konsole in der Verbund-Dachaussteifung.
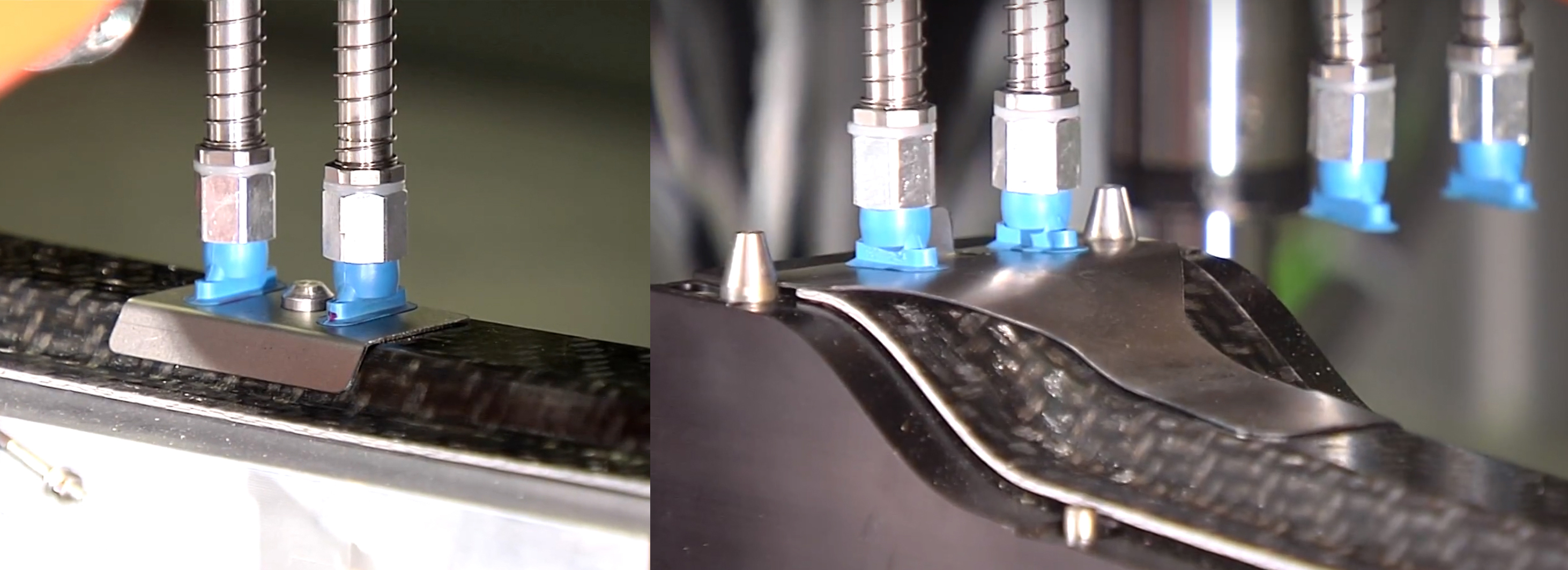
Schritt 5. Der Roboter fährt zurück in die Strukturierungszelle, nimmt die behandelten Konsolen auf und legt sie mit der strukturierten Seite nach unten auf den TPC-Dachspriegel.
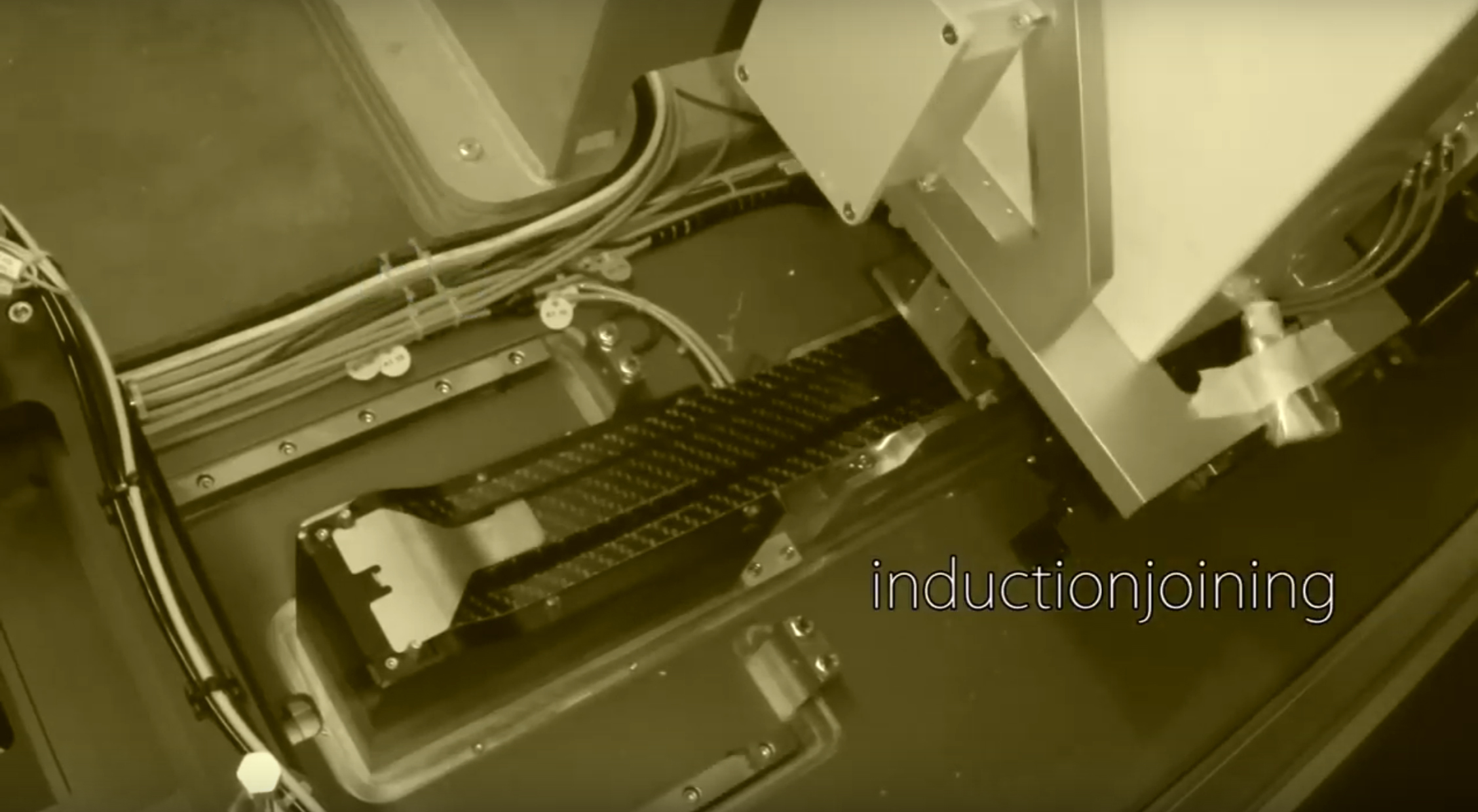
Schritt 6. Anschließend setzt der Roboter Spanneinheiten auf die drei Halterungen. Die Induktionsfügeeinheit senkt sich auf die Mittelkonsole ab. Die Induktionsspule bewirkt, dass sich die Metallhalterung erwärmt und die PA6-Matrix des darunter liegenden Verbundwerkstoffs schmilzt.
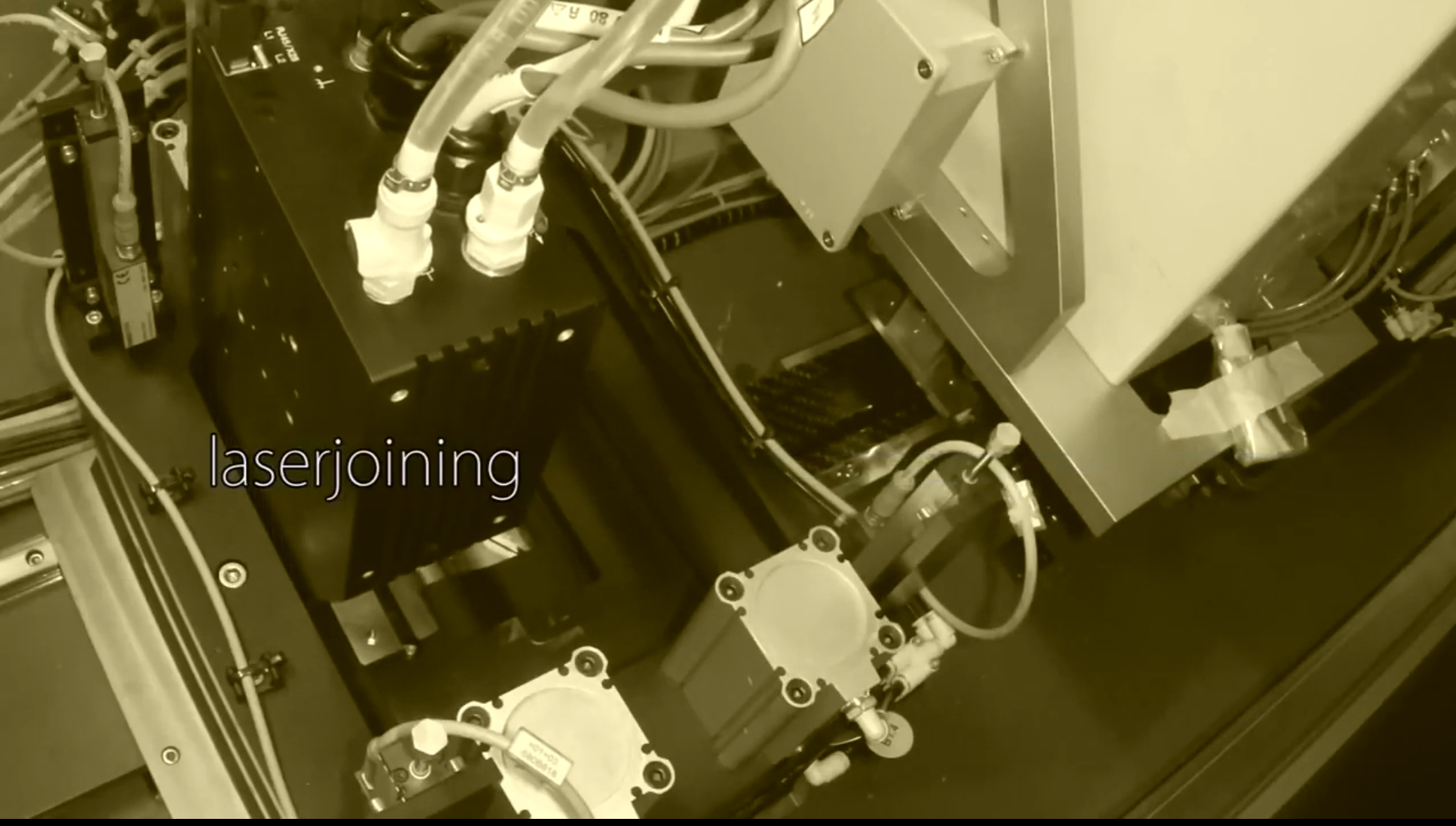
Schritt 7. Während das Induktionsfügen abgeschlossen ist, wird die Laserfügeeinheit abgesenkt, um die linken und dann rechten Halterungen zu verbinden. Der Laser erhitzt das Metall, wodurch die darunterliegende PA6-Matrix mit den Hinterschneidungen verschmilzt und eine hochfeste Verbindung entsteht.
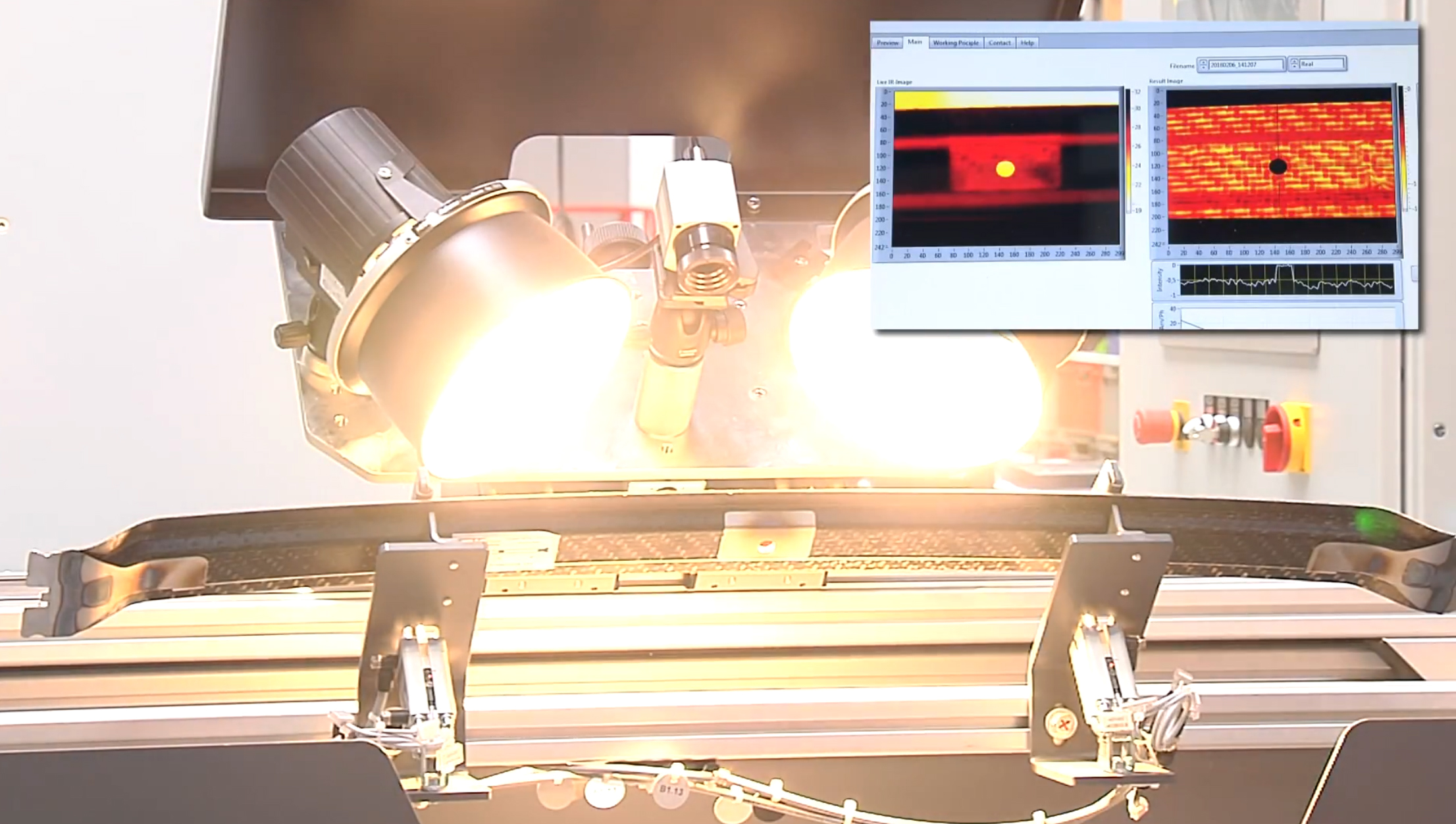
Beitreten zur Prozesskontrolle
Die grundlegende Methode zur Steuerung beider Fügeprozesse besteht darin, die Temperatur und die Zeit gegen einen Satz optimierter Parameter zu messen, die durch Tests definiert wurden. „Daher haben wir Fügeprüfmuster mit unterschiedlichen Parametern hergestellt und mit speziellen Prüfaufbauten für jeden Parametersatz mechanische Prüfungen durchgeführt. Für die Seitenkonsole wurde eine Kombination aus Scher- und Schälversuch entwickelt, für die Mittelkonsole eine Druckbelastungsprüfung, vergleichbar mit einem Zugscherversuch, jedoch wird geschoben statt gezogen, um eine Scherbelastung zu erhalten im Fügebereich“, sagt Popow. Der Aufbau dieser Sonderprüfungen wurde gemeinsam mit der EDAG Engineering GmbH (EDAG, Fulda, Deutschland) konzipiert, die auch die Auswertung der Prüfergebnisse durchführte. Nach diesem Vorgehen wurde der beste Parametersatz für die Fügeprozesse identifiziert und anschließend in der Pilotfertigungszelle eingesetzt.
„Das induktive Fügeverfahren wurde vorab kalibriert“, sagt Weidmann. „Wir wissen, dass wir die Fügetemperatur nach ca. 30 Sekunden erreichen, messen die Temperatur aber aus Sicherheitsgründen auch vor Ort, um eine Überhitzung zu vermeiden.“ Ein Pyrometer, das die Strahlung einer Oberfläche aus der Ferne misst, wurde verwendet, um einen bekannten Hot Spot im Induktionsfügebereich zu messen. „Aufgrund des hohen eingestrahlten Lichts und der hohen Wärme in-situ kann es jedoch keine genauen Messungen der Laserverbindung liefern“, erklärt er. Auf der Verbundseite der Laserfügebereiche könnten jedoch Kontaktsensoren verwendet werden, die jedoch für den Induktionsfügeprozess nicht geeignet waren, da sie typischerweise aus Metall bestehen und sich durch Induktion erwärmen und die Messung verfälschen würden.
„Auch die beheizten Bereiche aller Fügestellen werden vom Presswerkzeug und den Spannvorrichtungen abgedeckt“, so Weidmann. „Damit haben wir die Dickenänderung des Bauteils durch Druck und Hitze vor und nach dem Fügen als Qualitätssicherungsmethode validiert.“ Diese Dickenänderung wird von einem im Positionierwerkzeug für die Dachaussteifung integrierten Abstandssensor gemessen (ebenfalls in Abb. 3 dargestellt). „Beim Zusammenpressen der Teile wird der Abstandssensor bewegt“, erklärt er. „Bei Hitze und Fügedruck fließt das geschmolzene Matrixpolymer in die Kavitäten der Laserstrukturierung und wird leicht aus der Fügezone herausgedrückt, bis die Fügestelle abkühlt. Dies führt zu einer Dickenänderung, die vom Distanzsensor protokolliert wird.“ Weidmann und das IVW-Team haben diese Distanz zur Teilequalität korreliert. „Eine Dickenänderung – also eine Verdichtung – von mehr als 0,1 Millimeter bedeutet eine gute Fugenqualität“, so Weidmann.
Inline-ZfP
IVW hat eine weitere Methode zur Qualitätssicherung entwickelt – die Inline-Thermografieprüfung. „Für die Qualitätssicherung ging es vor allem darum, die Eigenschaften im Fügebereich zu sehen“, erklärt Popow. „Aber das war sehr schwierig, also haben wir nach Fertigstellung des Teils eine Thermografie auf der Verbundseite der Verbindungen durchgeführt.“
IVW hat sich für eine aktive Thermografie-Technik namens Lock-In-Thermografie entschieden, weil sie ein besseres Signal-Rausch-Verhältnis bietet als andere aktive Methoden (z. B. Pulsphasen-Thermografie) und auch auf tiefere Defekte untersuchen kann. „Die Grundidee besteht darin, dem Verbund Wärme zuzuführen, die dann in den Fügebereich und wieder zurück an die Oberfläche leitet“, sagt Popow. „Bei der Lock-in-Thermografie wird das Bauteil mit einer definierten Frequenz über mehrere angeregt Perioden. Diese Reaktion analysieren wir dann im Laufe der Zeit. Wenn sich zwischen der Verbundoberfläche und dem Verbindungsbereich Bereiche befinden, die aufgrund einer Fehlstelle oder eines Defekts nicht homogen sind, zeigt sich dies in der thermischen Reaktion.“
Die thermische Reaktion wird als Bild erfasst. Die Punkte, aus denen diese Bilder bestehen, sind Pixel, kurz für Bildelemente. Jedes Pixel ist auch ein Messpunkt. Somit wird das Temperatursignal für jedes Pixel über den gesamten Untersuchungsbereich analysiert. „Als Ergebnis erhält man Amplituden- und Phaseninformationen für jeden Pixel, und die Software rekonstruiert diese dann wieder zu einem Bild, das visuell untersucht werden kann“, fügt er hinzu. Es lieferte aber auch umfangreiche Messreihen für die 126 getesteten Teile. „Wir haben diese NDT-Ergebnisse mit den Ergebnissen der mechanischen Tests von EDAG korreliert“, sagt Popow. Sein Team testete auch den Verbindungsbereich nach dem Entfernen der Klammern – also zerstörende Prüfung. „Damit haben wir drei Testergebnisse korreliert und können jetzt aus der visuellen Analyse der Thermografie-Ergebnisse Verbindungsbereiche mit geringer Festigkeit gegenüber hochfesten Bereichen identifizieren“, sagt er.
Integrierte Zelle für die Massenproduktion
Eine der größten Errungenschaften von FlexHyJoin ist laut Weidmann die Integration aller Technologieeinheiten, die jeweils von einem anderen Projektpartner entwickelt wurden, in eine automatisierte, optimierte Produktionslinie. Voithofer, derjenige, der die Geräte bei Fill integriert, erklärt, dass „jede Ausrüstung, die an uns geliefert wurde, eine andere Steuerung verwendet. Ich musste eine Master-SPS entwickeln, um all die verschiedenen Prozesseinheiten zu steuern.“ Dazu gehörten die Lasergehäuse und der Handhabungsroboter der Zelle, die von Fill geliefert wurden. „Es war auch sehr schwierig, all diese Prozessschritte zusammenzuarbeiten, da sie unterschiedlich lange dauern“, fügt er hinzu.
Voithofer begann mit der Entwicklung einer Architektur für jede Prozesseinheit und jeden Roboter und überlegte, wie diese für den besten Durchfluss positioniert werden können. „Unser Konzept bestand darin, die drei Stationen – Strukturieren, Fügen und NDT – modular in drei separaten Gehäusen zu halten“, sagt er. „So konnten wir einzelne Einheiten extrahieren und auf Messen oder anderen Demonstrationsprojekten einsetzen und dann wieder zurückgeben. Die Arbeitszelle ist also modular und dennoch integriert.“
Die jahrzehntelange Erfahrung von Fill in dieser Art der Systemintegration für die Serienfertigung von Verbundwerkstoffen hat dazu beigetragen, das zu erreichen, was Popow als die größte Leistung von FlexHyJoin ansieht:den Übergang vom Labormaßstab in den industriellen Maßstab. „Wir sind das erste Konsortium, das ein solches Verfahren realisiert hat, das für die Massenproduktion von metallverbundenen Verbundwerkstoffen geeignet ist“, sagt er. „Dieses Verfahren lässt sich für viele Automobilteile wie Stabilisatoren, Stoßfänger und Türen anwenden“, sagt Voithofer. „In einem leichten BIW gibt es viele Verbundteile, die mit Metallteilen verbunden werden.“
Anpassung an mehrere Branchen
Bis zur Serienreife der Zelle sind jedoch noch einige Änderungen erforderlich. „Wir würden das Laserstrukturieren und Fügen nicht mehr in getrennten Gehäusen halten, sondern zu einem zusammenfassen“, sagt Voithofer. „Dies würde das Öffnen und Schließen von Schaltschranktüren zwischen diesen Prozessen überflüssig machen und die Zykluszeit reduzieren.“ Außerdem würde er alle Stationen auf einem Förderband linear verbinden. Die Linie würde somit kontinuierlich laufen, wobei die Teile für jede Station aufgenommen und wieder auf das Förderband gelegt werden, bevor sie die Zelle verlassen, um sie in eine BIW zu montieren. Dies würde die Zykluszeit weiter verkürzen. Außerdem könnten erweiterte Schubladen, die Hunderte von Teilen zuführen können, es der Linie ermöglichen, ganze Schichten zu durchlaufen, ohne dass Nachschub erforderlich ist.
Obwohl diese Pilotproduktionszelle für die Automobilindustrie bestimmt war, kann sie leicht an Luft- und Raumfahrt, Sport-/Konsumgüter und industrielle Anwendungen angepasst werden. „Das war eigentlich eine der Hauptrichtlinien“, sagt Weidmann, „dass es unterschiedliche Geometrien und Teile fügen können muss. Die einzigen Änderungen sollten das Induktionsfüge-Verdichtungswerkzeug, die Spannvorrichtungen für das Laserfügen und die Stützwerkzeuge sein. Die Hauptteile der Zelle sollten gleich bleiben.“ Er merkt an, dass IVW auch die Hybridverbindung von Titan und Stahl mit gewebten Kohlenstoffaser/Polyphenylensulfid (PPS) Organoblech-Verbundwerkstoffen demonstriert hat und jetzt Demonstrationen von Polyetheretherketon (PEEK) und Polyetherketonketon (PEKK) entwickelt. „Dazu müssen lediglich die Fügeprozesse für höhere Temperaturen angepasst und optimale Prozessparameter neu definiert werden“, sagt Weidmann. „Die Zelle ist offen für eine Vielzahl von Materialien, darunter Aluminium und Kupfer sowie andere thermoplastische Verbundmatrixsysteme wie Polypropylen und Polyethylen.“
„Die Projektpartner haben gut zusammengearbeitet und freuen sich, die Entwicklung weiter voranzutreiben“, bemerkt er. „Wir denken, dass diese Art der Produktion sehr vielversprechend ist, und die Reaktionen, die wir bisher aus der Industrie erhalten haben, zeigen, dass es eine Vielzahl von Unternehmen gibt, die dieses Versprechen ebenfalls sehen.“
Harz
- Solvay erweitert die Kapazität von thermoplastischen Verbundwerkstoffen
- Synthese und Untersuchung optischer Eigenschaften von Ti0.91O2/CdS-Hybridkugelstrukturen
- Oberflächenimpedanz von Metaoberflächen/Graphen-Hybridstrukturen
- Fraunhofer nimmt automatisierte Engel-Produktionszellen für F&E thermoplastischer Verbundwerkstoffe in Betrieb
- Die Bedeutung der Harzauswahl
- DLR-Institut für Konstruktion und Konstruktion steigert Reifegrad von thermoplastischen Rumpfstrukturen aus Verbundwerkstoff
- Einfach zu verwendende Kits ermöglichen die Reparatur von Verbundstrukturen im Feld
- Konsortium sucht Lösungen für thermoplastische Kohlefaser-Verbundstrukturen
- Verbundwerkstoff für Architekturverkleidungen enthüllt
- Verbundwerkstoff + Metall:Hybridtechnologie mit Hohlprofil