Spritzgießen für hochleistungsfähige, vereinheitlichte thermoplastische Strukturen
Verbundene Zahnrad-Antriebswelle aus Verbundwerkstoff. Herone verwendet geflochtene thermoplastische Verbundstoff-Prepreg-Bänder als Vorformlinge für einen Prozess, bei dem das Antriebswellenlaminat konsolidiert und Funktionselemente wie Zahnräder umspritzt werden, wodurch einheitliche Strukturen erzeugt werden, die Gewicht, Teileanzahl, Montagezeit und Kosten reduzieren. Quelle für alle Bilder | Reiher
Aktuelle Prognosen gehen von einer Verdoppelung der Verkehrsflugzeugflotte in den nächsten 20 Jahren aus. Um dem Rechnung zu tragen, schwanken die Produktionsraten 2019 für Composite-intensive Widebody-Jetliner von 10 bis 14 pro Monat pro OEM, während Narrowbodies bereits auf 60 pro Monat pro OEM angestiegen sind. Airbus arbeitet speziell mit Zulieferern zusammen, um traditionelle, aber zeitintensive Prepreg-Teile mit Handlaminierung auf der A320 auf Teile umzustellen, die in schnelleren 20-Minuten-Zykluszeitprozessen wie Hochdruck-Harzspritzpressen (HP-RTM) hergestellt werden Lieferanten einen weiteren Schub in Richtung 100 Flugzeuge pro Monat. Unterdessen prognostiziert der aufstrebende städtische Luftmobilitäts- und Verkehrsmarkt einen Bedarf an 3.000 elektrischen vertikalen Start- und Landeflugzeugen (EVTOL) pro Jahr (250 pro Monat).
„Die Industrie benötigt automatisierte Produktionstechnologien mit verkürzten Zykluszeiten, die auch die Integration von Funktionen ermöglichen, die thermoplastische Verbundwerkstoffe bieten“, sagt Daniel Barfuss, Mitgründer und geschäftsführender Gesellschafter von herone (Dresden), einem Verbundtechnologie- und Teilefertigungsunternehmen Unternehmen, das hochleistungsfähige thermoplastische Matrixmaterialien von Polyphenylensulfid (PPS) über Polyetheretherketon (PEEK), Polyetherketonketon (PEKK) und Polyaryletherketon (PAEK) verwendet. „Unser Hauptziel ist es, die hohe Leistungsfähigkeit von thermoplastischen Verbundwerkstoffen (TPCs) mit geringeren Kosten zu kombinieren, um maßgeschneiderte Teile für eine breitere Palette von Serienfertigungsanwendungen und neue Anwendungen zu ermöglichen“, fügt Dr. Christian Garthaus, zweiter Mitgründer und Geschäftsführer von herone, hinzu Partner.
Um dies zu erreichen, hat das Unternehmen einen neuen Ansatz entwickelt, beginnend mit vollimprägnierten Endlosfaserbändern, diese Bänder zu einem hohlen Preform „organoTube“ zu verflechten und die organoTubes zu Profilen mit variablen Querschnitten und Formen zu konsolidieren. In einem nachfolgenden Prozessschritt nutzt es die Schweißbarkeit und Thermoformbarkeit von TPCs, um Funktionselemente wie Verbundzahnräder auf Antriebswellen, Endfittings auf Rohre oder Kraftübertragungselemente in Zug-Druck-Streben zu integrieren. Barfuss fügt hinzu, dass es die Option gibt, ein Hybrid-Formverfahren zu verwenden, das von dem Ketonmatrix-Lieferanten Victrex (Cleveleys, Lancashire, UK) und dem Teilelieferanten Tri-Mack (Bristol, RI, USA) entwickelt wurde – bei dem PAEK-Band mit niedrigerer Schmelztemperatur für die Profile verwendet wird und PEEK für das Overmolding, wodurch ein verschmolzenes, einzelnes Material über die Verbindung hinweg ermöglicht wird (siehe „Overmolding erweitert PEEKs Angebot an Verbundwerkstoffen“). „Unsere Anpassung ermöglicht auch einen geometrischen Formschluss“, fügt er hinzu, „dadurch entstehen integrierte Strukturen, die noch höheren Belastungen standhalten.“
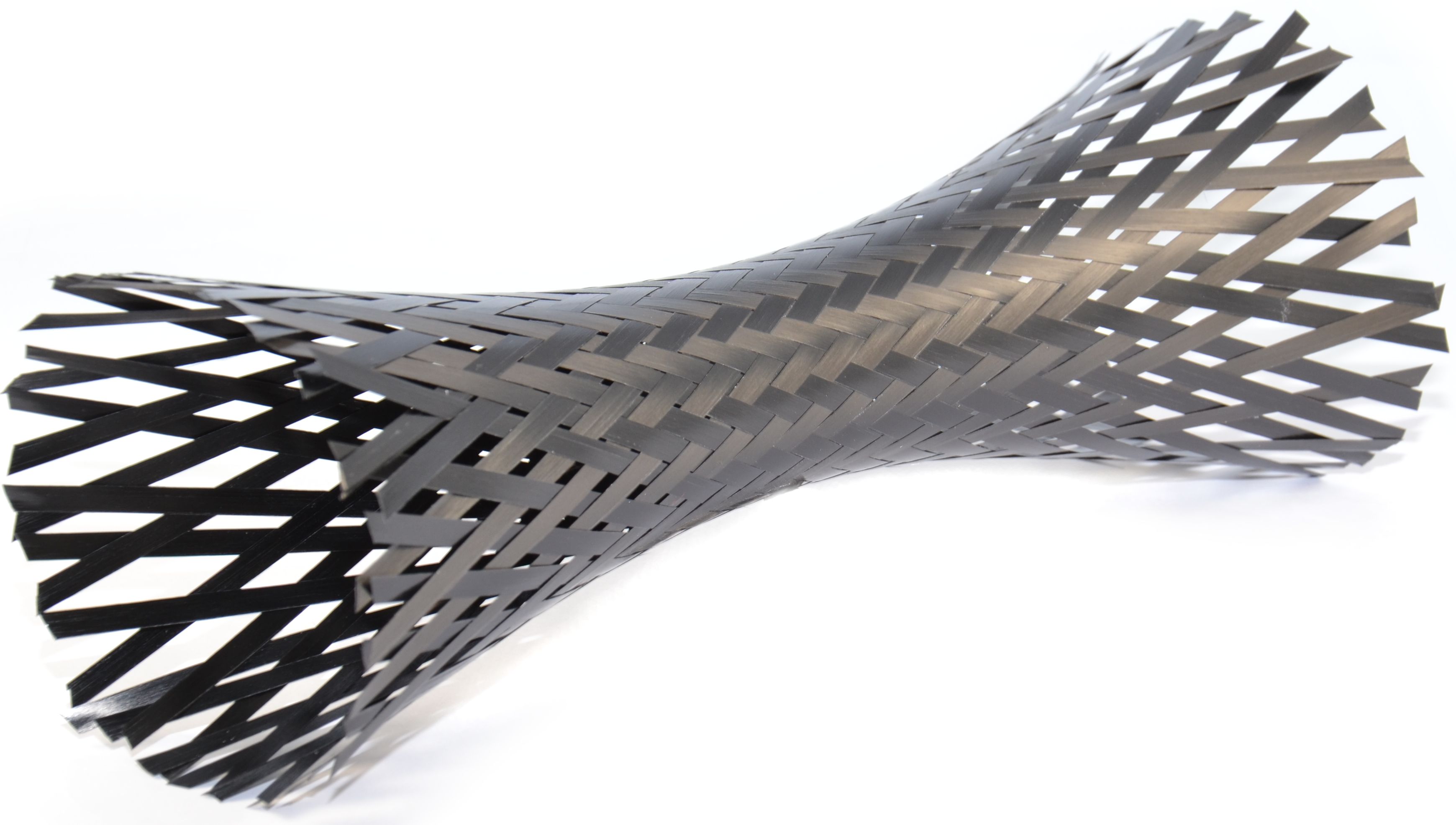
Geflochtener OrganoTube-basierter Formprozess
Der herone Prozess beginnt mit vollimprägnierten carbonfaserverstärkten thermoplastischen Tapes, die zu organoTubes geflochten und verfestigt werden. „Wir haben vor 10 Jahren begonnen, mit diesen organoTubes zu arbeiten und Verbund-Hydraulikrohre für die Luftfahrt zu entwickeln“, sagt Garthaus. Er erklärt, dass, da keine zwei Flugzeughydraulikrohre die gleiche Geometrie haben, für jede eine Form benötigt würde, wobei die vorhandene Technologie verwendet wird. „Wir brauchten ein Rohr, das nachbearbeitet werden konnte, um die individuelle Rohrgeometrie zu erreichen. Die Idee war also, durchgehende Verbundprofile herzustellen und diese dann CNC in die gewünschten Geometrien zu biegen.“
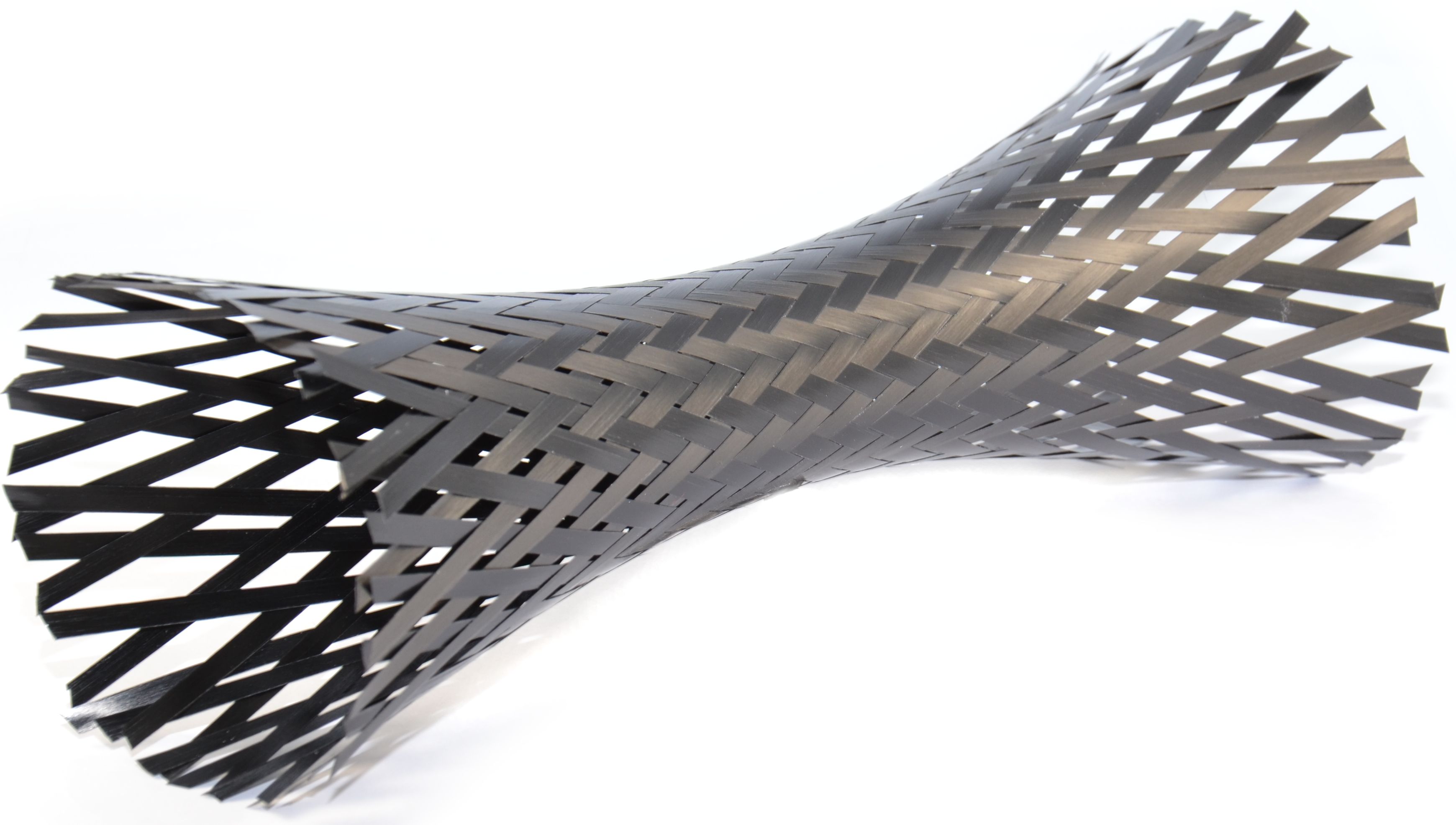
Abb. 2 Geflochtene Prepreg-Bänder bieten netzförmige Preforms, sogenannte organoTubes, für das Spritzgussverfahren von Heron und ermöglichen die Herstellung verschiedener Formen.
Dies klingt ähnlich wie das, was Sigma Precision Components (Hinckley, Großbritannien) mit seinem Kohlefaser-/PEEK-Triebwerks-Dressing macht (siehe „Redressing von Flugzeugtriebwerken mit Verbundrohren“). „Sie betrachten ähnliche Teile, verwenden aber eine andere Konsolidierungsmethode“, erklärt Garthaus. „Mit unserem Ansatz sehen wir Potenzial für eine Leistungssteigerung, beispielsweise eine Porosität von weniger als 2 % für Luft- und Raumfahrtstrukturen.“
Garthaus’ Ph.D. Diplomarbeit am ILK erforschte die Verwendung von kontinuierlicher thermoplastischer Verbundstoff (TPC)-Pultrusion zur Herstellung von geflochtenen Schläuchen, was zu einem patentierten kontinuierlichen Herstellungsverfahren für TPC-Rohre und -Profile führte. Vorerst hat sich herone jedoch dafür entschieden, mit Luftfahrtzulieferern und Kunden mit einem diskontinuierlichen Formgebungsverfahren. „Dies gibt uns die Freiheit, alle unterschiedlichen Formen herzustellen, einschließlich gebogener Profile und solcher mit unterschiedlichem Querschnitt, sowie lokale Patches und Lagenabfälle anzubringen“, erklärt er. „Wir arbeiten daran, den Prozess der Integration lokaler Patches zu automatisieren und sie dann mit dem zusammengesetzten Profil zusammen zu konsolidieren. Im Grunde ist alles, was man mit Flachlaminaten und Schalen machen kann, auch für Rohre und Profile möglich.“
Die Herstellung dieser TPC-Hohlprofile war eigentlich eine der schwierigsten Herausforderungen, sagt Garthaus. „Sie können mit einer Silikonblase nicht Stempelformen oder Blasformen verwenden; Also mussten wir einen neuen Prozess entwickeln.“ Aber dieses Verfahren ermöglicht sehr leistungsstarke und maßgeschneiderte Teile auf Rohr- und Wellenbasis, bemerkt er. Es ermöglichte auch die Verwendung des von Victrex entwickelten Hybridgusses, bei dem PAEK mit niedrigerer Schmelztemperatur mit PEEK umspritzt wird, wodurch das Organoblech und das Spritzgießen in einem einzigen Schritt konsolidiert werden.
Ein weiterer bemerkenswerter Aspekt bei der Verwendung von organoTube-Geflechtband-Preforms ist, dass sie sehr wenig Abfall produzieren. „Beim Flechten haben wir weniger als 2 % Abfall, und da es sich um TPC-Band handelt, können wir diesen geringen Abfall wieder im Overmolding verwenden, um die Materialausnutzungsrate auf 100 % zu erhöhen“, betont Garthaus.
Entwicklung eines Unternehmens und eines Demonstrators für Getriebewellen
Barfuss und Garthaus begannen ihre Entwicklungsarbeit als Forscher am Institut für Leichtbau und Kunststofftechnik (ILK) der TU Dresden. „Dies ist eines der größten europäischen Institute für Composites und hybriden Leichtbau“, sagt Barfuss. Dort arbeiteten er und Garthaus fast 10 Jahre lang an einer Reihe von Entwicklungen, darunter die kontinuierliche TPC-Pultrusion und verschiedene Fügearten. Diese Arbeit wurde schließlich in die heutige Heron-TPC-Prozesstechnologie destilliert.
„Wir haben uns dann beim deutschen EXIST-Programm beworben, das auf den Technologietransfer in die Industrie abzielt und jedes Jahr 40 bis 60 Projekte in den unterschiedlichsten Forschungsfeldern fördert“, sagt Barfuss. „Wir haben Fördermittel für Investitionsgüter, vier Mitarbeiter und Investitionen für den nächsten Schritt des Scale-up erhalten.“ Sie gründeten Heron im Mai 2018, nachdem sie auf der JEC World ausgestellt hatten.
Bis zur JEC World 2019 hatte herone eine Reihe von Demonstrationsteilen produziert, darunter eine leichte, drehmomentstarke, integrierte Zahnradantriebswelle oder Zahnradwelle. „Wir verwenden ein Carbonfaser/PAEK-Band organoTube, das in den für das Teil erforderlichen Winkeln geflochten ist und dieses zu einem Rohr zusammenführt“, erklärt Barfuss. „Wir heizen das Rohr dann auf 200 °C vor und umspritzen es mit einem Zahnrad, das durch Spritzen von kurzem kohlenstofffaserverstärktem PEEK bei 380 °C hergestellt wurde.“ Das Overmolding wurde mit Moldflow Insight von Autodesk (San Rafael, Kalifornien, USA) modelliert. Die Formfüllzeit wurde auf 40,5 Sekunden optimiert und mit einer Arburg (Loßburg, Deutschland) ALLROUNDER Spritzgießmaschine erreicht.
Dieses Umspritzen reduziert nicht nur Montagekosten, Fertigungsschritte und Logistik, sondern steigert auch die Leistung. Der Unterschied von 40 °C zwischen der Schmelztemperatur der PAEK-Welle und der des umspritzten PEEK-Zahnrads ermöglicht eine kohäsive Schmelzverbindung zwischen beiden auf molekularer Ebene. Eine zweite Art der Fügemechanik, der Formschluss, wird dadurch erreicht, dass der Schaft beim Umspritzen mit dem Spritzdruck gleichzeitig zu einer formschlüssigen Kontur tiefgezogen wird. Dies ist in Abb. 1 unten als „Spritzformen“ zu sehen. Es entsteht ein gewellter oder sinusförmiger Umfang, wo das Zahnrad verbunden ist, gegenüber einem glatten kreisförmigen Querschnitt, was zu einer geometrisch verriegelnden Form führt. Dadurch wird die Festigkeit der integrierten Getriebewelle weiter erhöht, wie im Test gezeigt (siehe Grafik unten rechts). Abb. 1. In Zusammenarbeit mit Victrex und ILK entwickelt, erzeugt herone beim Umspritzen durch Spritzdruck eine formschlüssige Kontur in der integrierten Getriebewelle (oben). Durch dieses Spritzgussverfahren kann die integrierte Getriebewelle mit Formschluss (grüne Kurve in der Grafik) ein höheres Drehmoment aufnehmen als eine umspritzte Getriebewelle ohne Formschluss (schwarze Kurve in der Grafik).
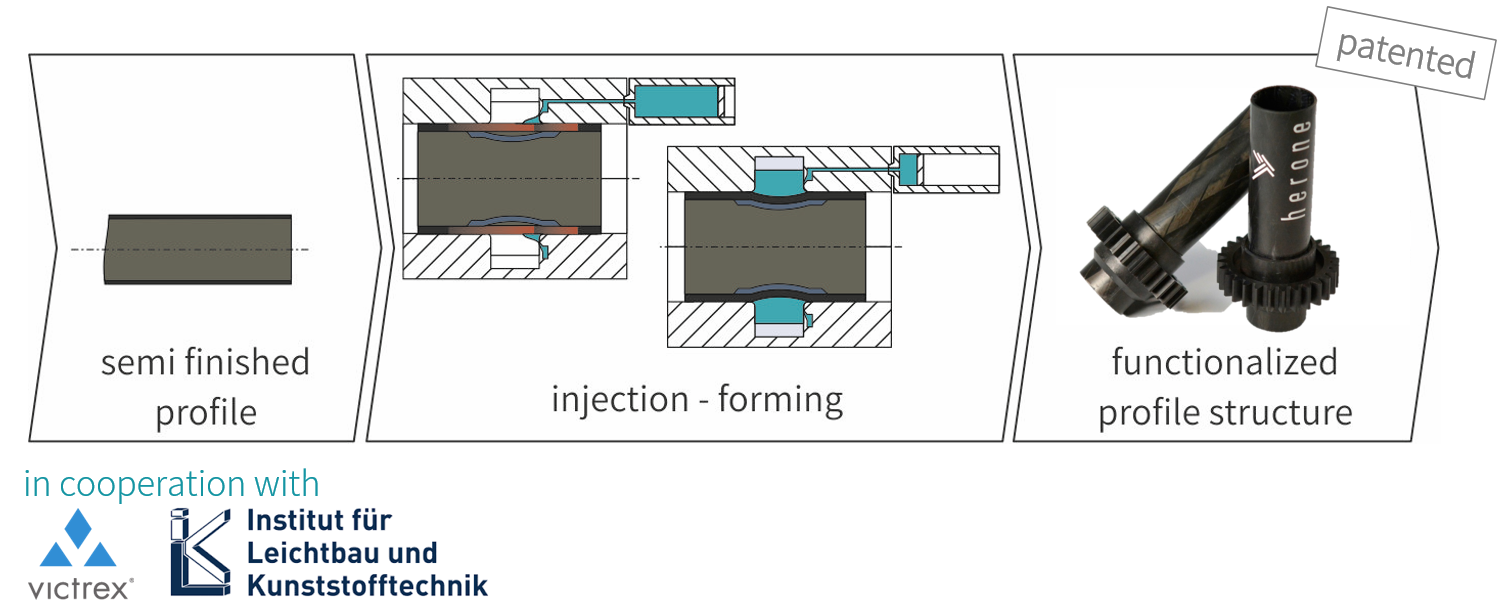
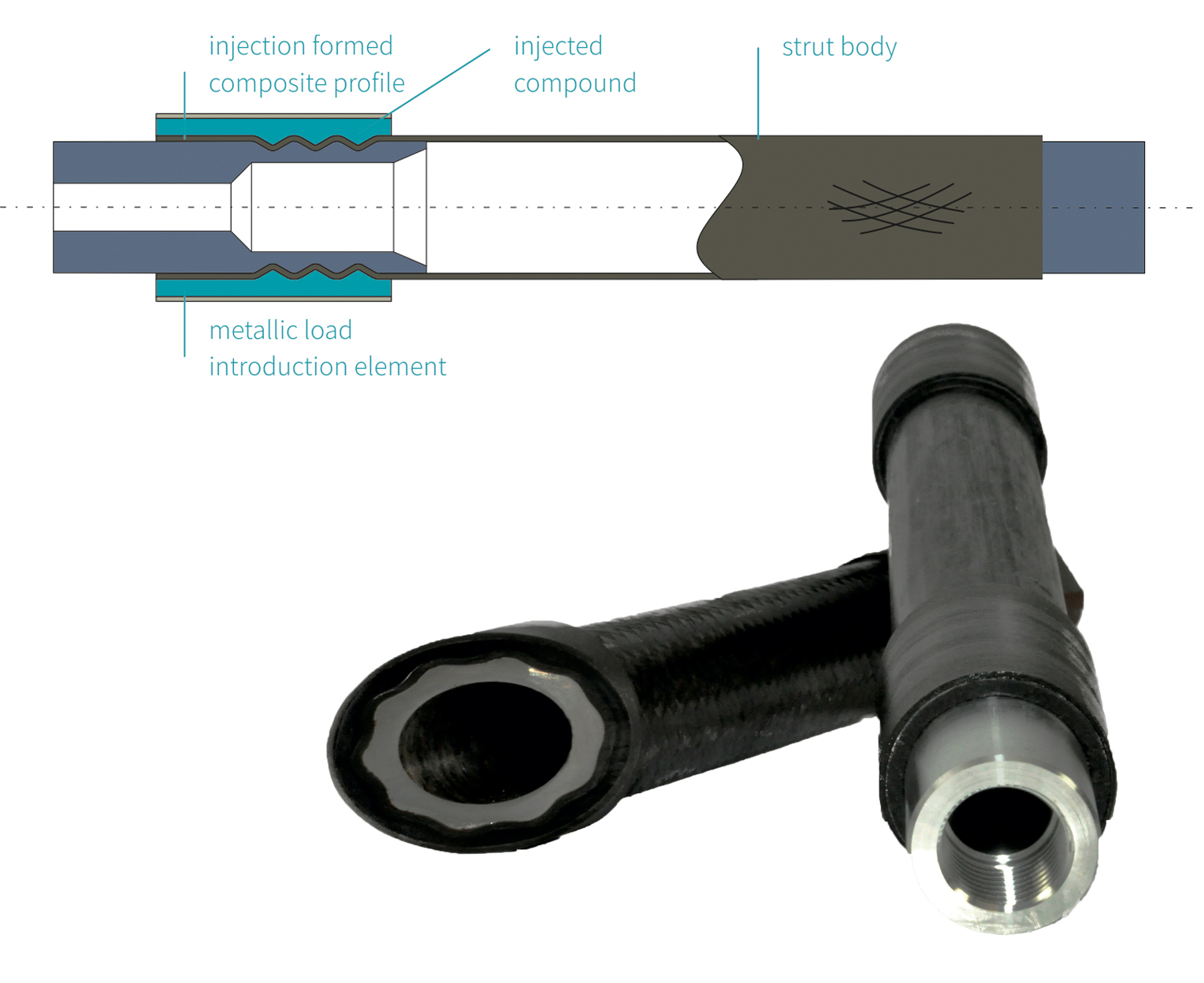
„Der Hauptvorteil, den wir bieten, besteht darin, die Anzahl der Teile zu verringern“, bemerkt er. „Dies vereinfacht die Ermüdung, die für Flugzeugstrebenanwendungen eine große Herausforderung darstellt. Formschluss wird bereits bei duroplastischen Verbundwerkstoffen mit Kunststoff- oder Metalleinlage verwendet, es gibt jedoch keinen stoffschlüssigen Verbund, sodass Sie eine leichte Bewegung zwischen den Teilen erzielen können. Unser Ansatz bietet jedoch eine einheitliche Struktur ohne solche Bewegungen.“
Als eine weitere Herausforderung für diese Teile nennt Garthaus Schadenstoleranz. „Man muss die Streben schlagen und dann Ermüdungstests durchführen“, erklärt er. „Da wir hochleistungsfähige thermoplastische Matrixmaterialien verwenden, können wir eine bis zu 40 % höhere Schadenstoleranz gegenüber Duroplasten erreichen, und auch Mikrorisse durch Stöße nehmen bei Ermüdungsbelastung weniger zu.“
Obwohl Demonstrationsstreben eine Metalleinlage aufweisen, entwickelt herone derzeit eine vollthermoplastische Lösung, die einen stoffschlüssigen Verbund zwischen dem Verbundstrebenkörper und dem Lasteinleitungselement ermöglicht. „Wenn es möglich ist, bleiben wir lieber aus Verbundwerkstoffen und passen die Eigenschaften an, indem wir die Art der Faserverstärkung ändern, einschließlich Kohlenstoff-, Glas-, Endlos- und Kurzfasern“, sagt Garthaus. „Auf diese Weise minimieren wir Komplexität und Schnittstellenprobleme. Wir haben zum Beispiel viel weniger Probleme als die Kombination von Duroplasten und Thermoplasten.“ Darüber hinaus wurde die Verbindung zwischen PAEK und PEEK von Tri-Mack getestet, mit Ergebnissen, die zeigen, dass sie 85 % der Festigkeit eines unidirektionalen CF/PAEK-Basislaminats aufweist und doppelt so stark ist wie Klebeverbindungen mit branchenüblichen Epoxidfolienklebern.
Neue Fabrik, neue Teile, neue Märkte
Laut Barfuss beschäftigt herone jetzt neun Mitarbeiter und wandelt sich vom Anbieter für Technologieentwicklung zu einem Anbieter von Luftfahrtteilen. Der nächste große Schritt ist der Aufbau einer neuen Fabrik in Dresden. „Bis Ende 2020 werden wir eine Pilotanlage zur Herstellung erster Serienteile haben“, sagt er. „Wir arbeiten bereits mit Luftfahrt-OEMs und wichtigen Tier-1-Zulieferern zusammen und demonstrieren Designs für viele verschiedene Arten von Anwendungen.“
Das Unternehmen arbeitet auch mit eVTOL-Lieferanten und einer Vielzahl von Kooperationspartnern in den USA zusammen. Während herone Luftfahrtanwendungen ausreift, sammelt es auch Herstellungserfahrung mit Sportartikelanwendungen wie Schläger und Fahrradkomponenten. „Unsere Technologie kann ein breites Spektrum komplexer Teile mit Leistungs-, Zykluszeit- und Kostenvorteilen herstellen“, sagt Garthaus. „Unsere Zykluszeit mit PEEK beträgt 20 Minuten, gegenüber 240 Minuten mit autoklavgehärtetem Prepreg. Wir sehen ein breites Feld an Möglichkeiten, aber im Moment liegt unser Fokus darauf, unsere ersten Anwendungen in die Produktion zu bringen und den Wert solcher Teile für den Markt zu demonstrieren.“
Herone wird auch auf der Carbon Fiber 2019 präsentieren. Erfahren Sie mehr über die Veranstaltung unter carbonfiberevent.com.
Harz
- Thermoplastisches Biomaterial „Feinabgestimmt“ für medizinische Anwendungen
- Fraunhofer nimmt automatisierte Engel-Produktionszellen für F&E thermoplastischer Verbundwerkstoffe in Betrieb
- Composites Evolution präsentiert Hochleistungs-Prepregs, neuartige thermoplastische UD-Bänder
- Thermoplastische Bänder zeigen weiterhin Potenzial für Verbund-Flugzeugstrukturen
- Konsortium sucht Lösungen für thermoplastische Kohlefaser-Verbundstrukturen
- Karl Mayer startet Produktionslinie für thermoplastische UD-Bänder
- INEOS Styrolution baut Produktionsstätte für thermoplastischen Verbundwerkstoff StyLight
- Herone-Produktionstechnologie gewinnt JEC Innovation Award
- AeroLas erforscht neue Spinntechnologie für thermoplastisches Hybridgarn
- Thermoplastische Tür eine Premiere für Automobilverbundwerkstoffe