Magnetischer 3D-Druck die nächste Generation maßgeschneiderter Verbundwerkstoffe
Fortify (Boston, MA, USA) wurde 2016 auf der Grundlage der Composite-3D-Druckforschung von Josh Martin (Fortifys CEO) und Randall Erb, Direktor des DAPS Lab an der Northeastern University in Boston, gegründet. (Erb ist auch Mitbegründer von Boston Materials und Fortify.) Ihr Ziel war es, eine schnelle Herstellung von Verbundwerkstoffen mit optimierten Mikrostrukturen zu ermöglichen. Die von ihnen entwickelte patentierte Fluxprint-Technologie verwendet Magnetfelder und digitale Lichtverarbeitung (DLP) – jedoch mit hochgefüllten Harzsystemen –, um kundenspezifische Mikrostrukturen in hochauflösenden 3D-gedruckten Verbundteilen herzustellen.
Fluxprint vs. DLP
Sowohl DLP als auch Stereolithographie (SLA) gelten derzeit als 3D-Drucktechnologien mit der höchsten Bauteilkomplexität und Präzision. Beide beruhen auf der Verwendung von Licht – typischerweise Ultraviolett (UV) – um ein lichtempfindliches Harz zu härten, das normalerweise Epoxid- oder Acryl- und Methacrylmonomere umfasst. Das Licht wird digital so gelenkt, dass es auf das Harz im Tank des Systems scheint, um die Formen oder Muster für jede Schicht zu erzeugen. Die Fertigungsplattform wird nach jeder Schicht bewegt, sodass die nächste Schicht gedruckt und zu einem fertigen, massiven Teil übergegangen werden kann.
DLP-Projektoren und SLA stammen aus den Anfängen des 3D-Drucks in den 1980er Jahren. DLP-Drucker sind in der Regel größer, da sie den eigentlichen Lichtprojektor beherbergen. Die meisten SLA- und DLP-Maschinen verwenden duroplastische Polymere, aber EnvisionTEC stellt einen Drucker her, der auch Thermoplaste verwenden kann. Beide haben traditionell reine Polymere ohne Verstärkung verwendet.
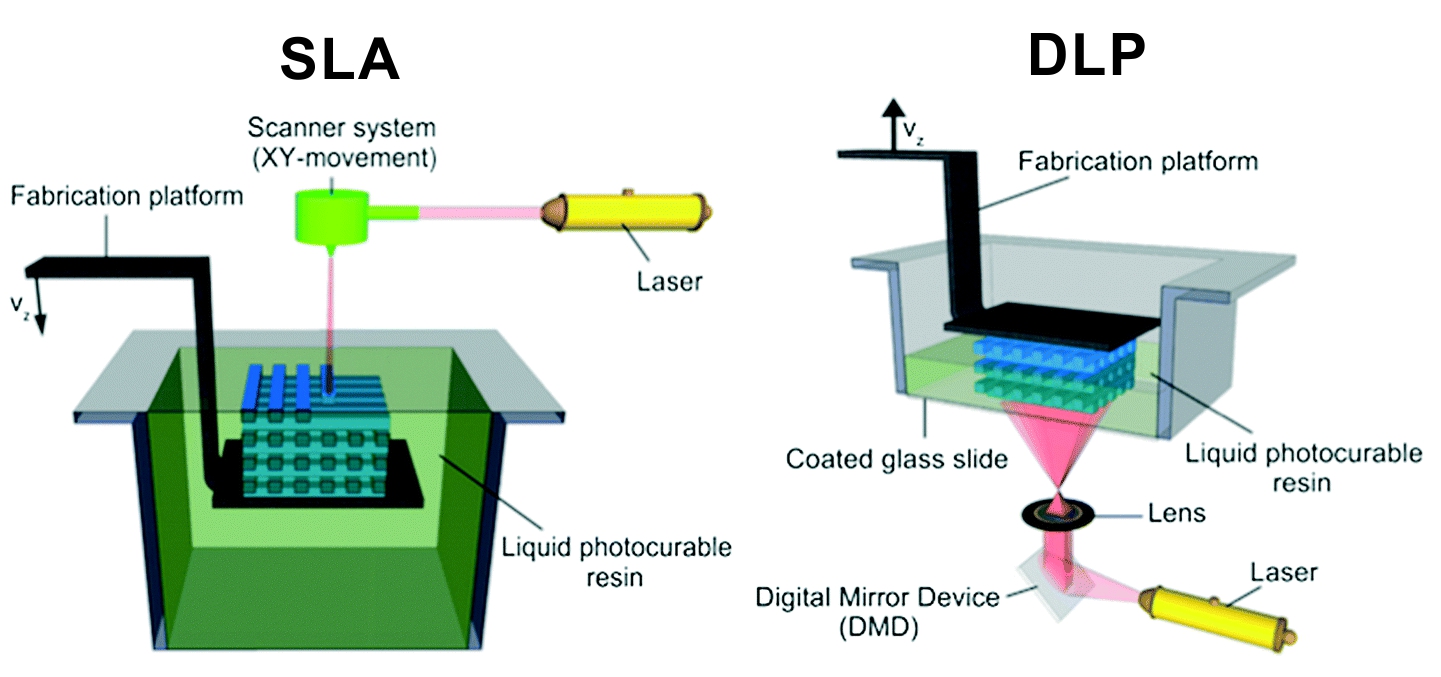
„DLP-Plattformen sind in der Lage, ausreichende Produktionsraten und Qualität zu erreichen“, sagt Fortify-CEO Josh Martin, „aber die mechanischen Eigenschaften waren schon immer eine Herausforderung. Unsere Kernthese lautet, dass ein Leistungssprung nicht allein durch die Polymerchemie erreicht werden kann. Die Nutzung der einzigartigen Eigenschaften von Verbundwerkstoffen in der hochauflösenden Additivindustrie wird jedoch das Spiel verändern.“
Er erklärt, dass Fortify sich auf die UV-Härtung hochgefüllter technischer Harze unter Verwendung einzigartiger Additive und der Kontrolle der Ausrichtung dieser eigenschaftsverbessernden Additive im Druck spezialisiert hat. Füllstoffe umfassen Glas-, Kohle- und Keramikfasern sowie Partikel. Zu den technischen Harzen gehören Acrylat- und Methacrylat-basierte (PMMA) oder Epoxy-basierte, kationische Harze – die laut Martin eher in der Lackindustrie üblich sind. Weltweit führende Harzhersteller (BASF, DSM, Dupont und andere) investieren massiv, um die Eigenschaften ihrer Additivmaterialien zu verbessern. Fortify ist in der Lage, die besten dieser Fortschritte auszuwählen, um ihre Verstärkungstechnologie hinzuzufügen.
Die Steuerung der Faserorientierung wird durch die Verwendung eines Magnetfelds erreicht. Wenn Fortify 3D ein Teil mit seiner Fluxprint-Technologie druckt, werden die Fasern Voxel für Voxel magnetisch ausgerichtet, um die Lastanforderungen des Teils zu erfüllen. (Sehen Sie den Prozess in Aktion im obigen Video.) Für nichtmagnetische Verstärkungsmaterialien wie Keramik- und Glaspartikel und -fasern werden proprietäre magnetische Markierungstechniken verwendet, um die Füllstoffe so zu beschichten, dass sie magnetisch reagieren und kompatibel sind mit das Harz.
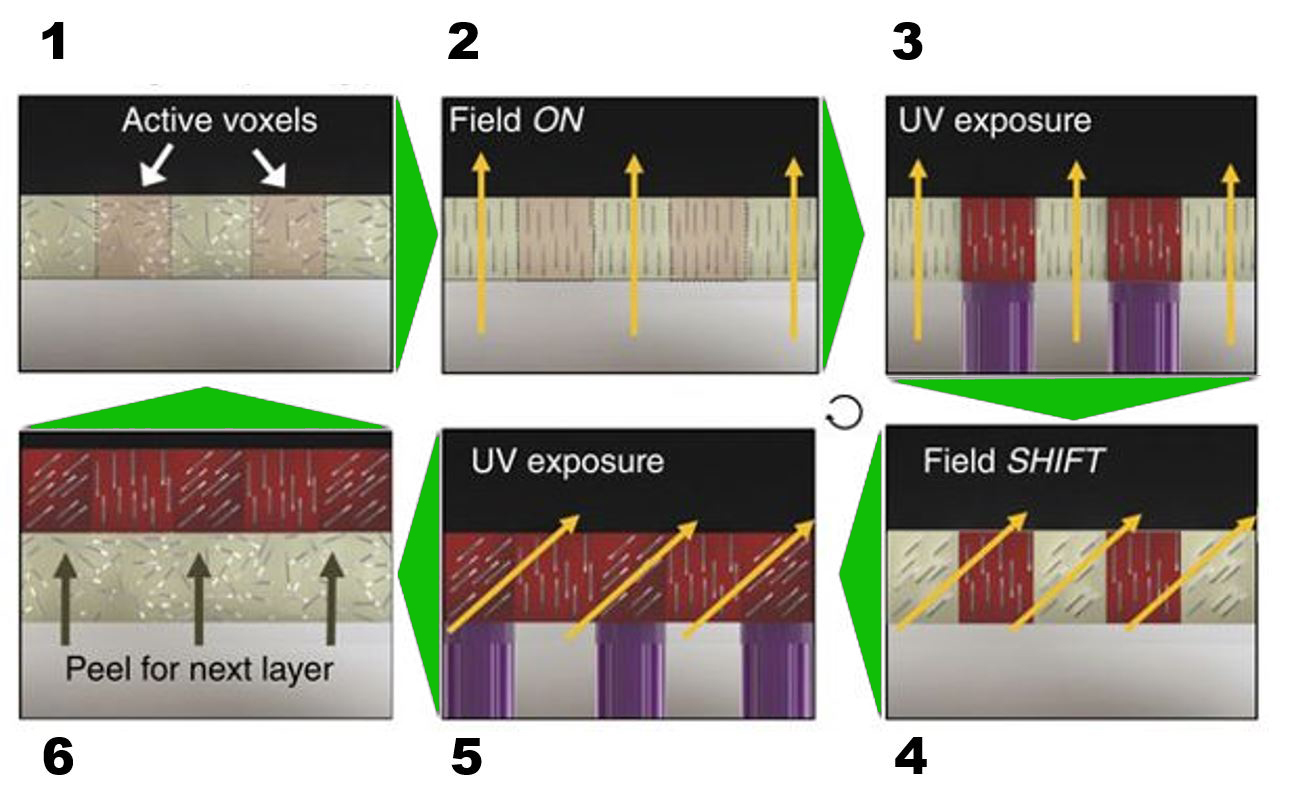
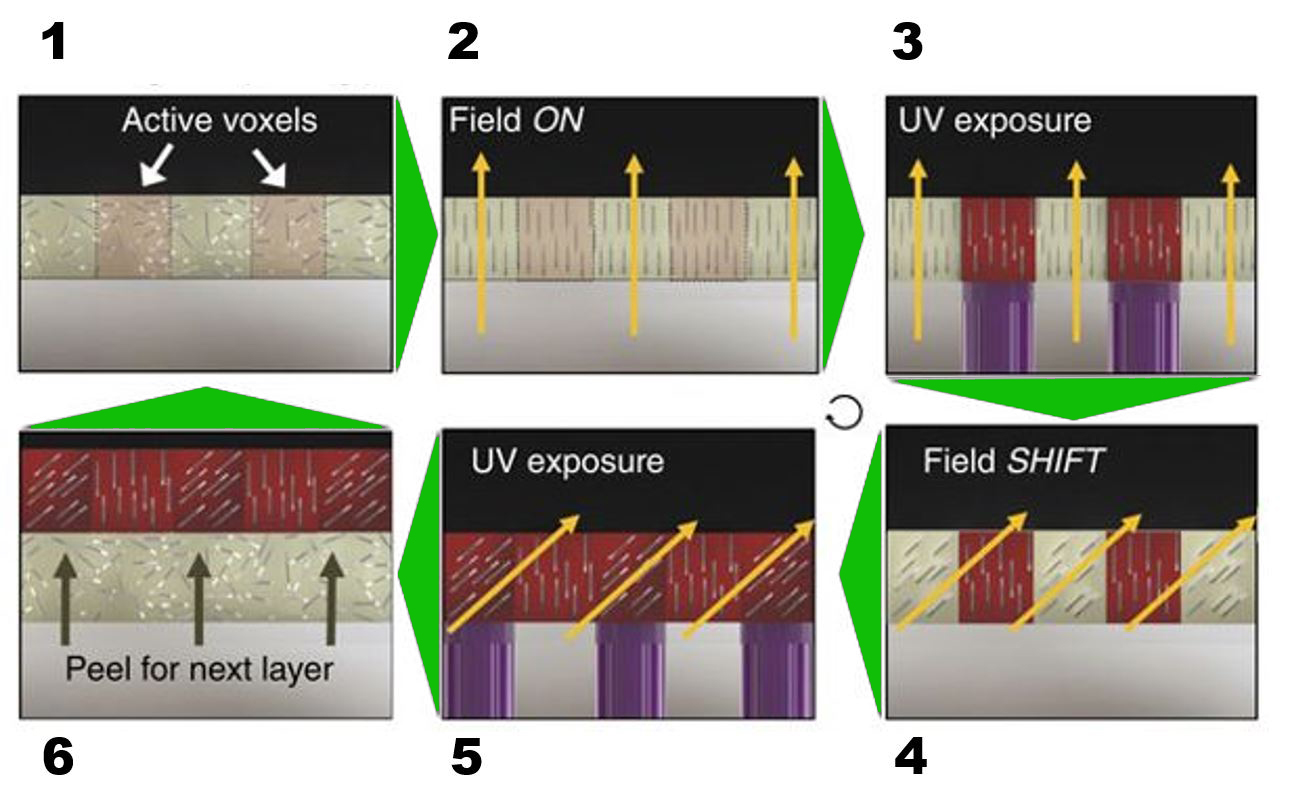
Der Fluxprint-Prozess ist im obigen Bild dargestellt und wie folgt beschrieben:
- Eine Schicht Beschickungsmaterial wird dem Baubereich mit zufällig ausgerichteten Verstärkungen zugeführt.
- Magnetfeld wird angelegt, um die Bewehrung auszurichten.
- Aktive Voxel werden UV-Licht ausgesetzt, wodurch die Verstärkungsorientierung in diesen Voxeln fixiert wird (jetzt rot dargestellt).
- Das Magnetfeld wird verschoben, um eine neue Ausrichtung der Verstärkung festzulegen.
- Wiederholen Sie den UV-Belichtungsschritt, um die Ausrichtung für den nächsten Satz von Voxeln zu fixieren (nach Bedarf wiederholen).
- Bauplatte passt sich an, um ungehärtete Zufuhrmaterialmatrix für die nächste Druckschicht einzubringen.
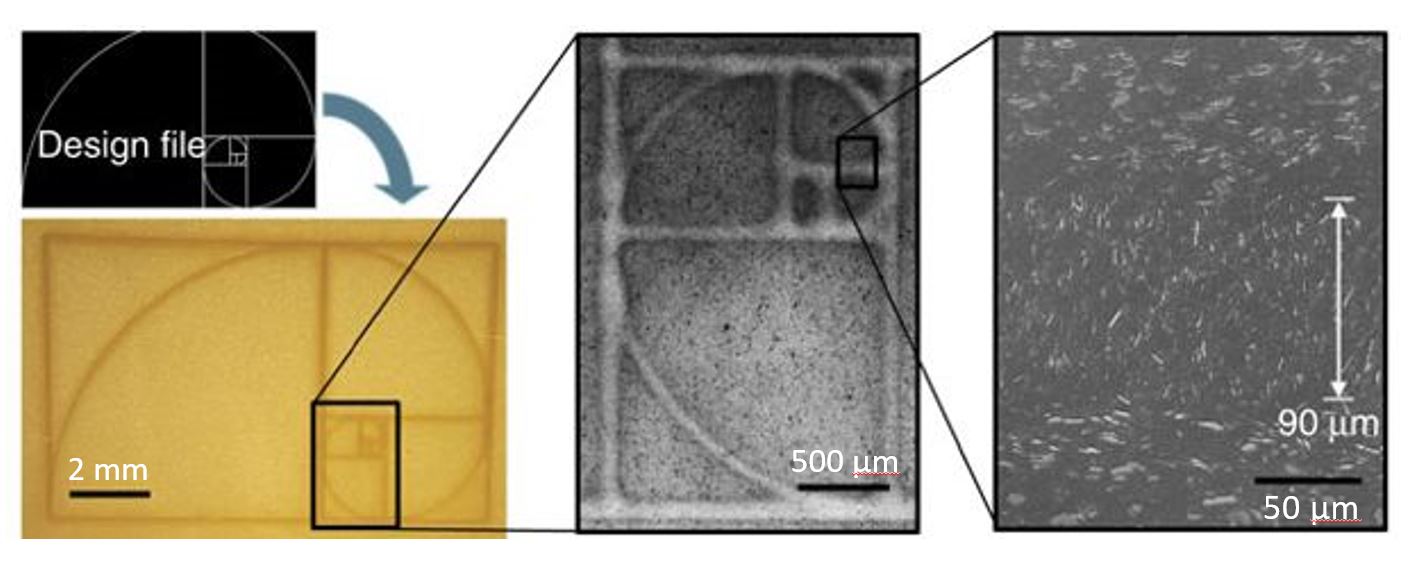
Die Fluxprint-Technologie ermöglicht die Kontrolle der Faserorientierung auf Voxelebene während des Druckprozesses. Quelle | „Entwurf bioinspirierter Verbundverstärkungsarchitekturen mittels 3D-Magnetdruck“ von Joshua J. Martin, Brad E. Fiore und Randall M. Erb, Nature Communications Band6, Artikelnummer:8641 (2015).
Warum Voxel-für-Voxel?
„Jede Geometrie hat einzigartige Dehnungs- und Spannungszustände“, erklärt Martin. „Die meisten Verbundwerkstoffe werden von Hand hergestellt, um dies zu berücksichtigen. Wir digitalisieren den Prozess. Wenn Sie beispielsweise einen UAV-Rahmen richtig verstärken können, können Sie weniger Material verwenden. Davon profitiert grundsätzlich jede Anwendung, die gegen die Schwerkraft arbeitet.“
Voxel-für-Voxel-Druck ist auch von Natur aus eine hohe Auflösung. „Dies ist der bisher höchstauflösende Herstellungsprozess für Verbundwerkstoffe“, sagt Martin und stellt fest, dass das Fused Deposition Modeling (FDM) – bei dem unverstärktes oder gemahlenes faserverstärktes Kunststofffilament geschmolzen und auf einem Druckbett abgelegt wird – eine Auflösung von Hunderten hat von Mikrometern, während die von Fluxprint innerhalb von zehn Mikrometern liegt. „Das ist also eine Verbesserung um eine Größenordnung, die ein Gebiet betritt, das über das hinausgeht, was mit bloßem Auge wahrgenommen wird. Diese Art der Auflösung ist für eine Vielzahl von Endverwendungsteilen sehr wichtig.“
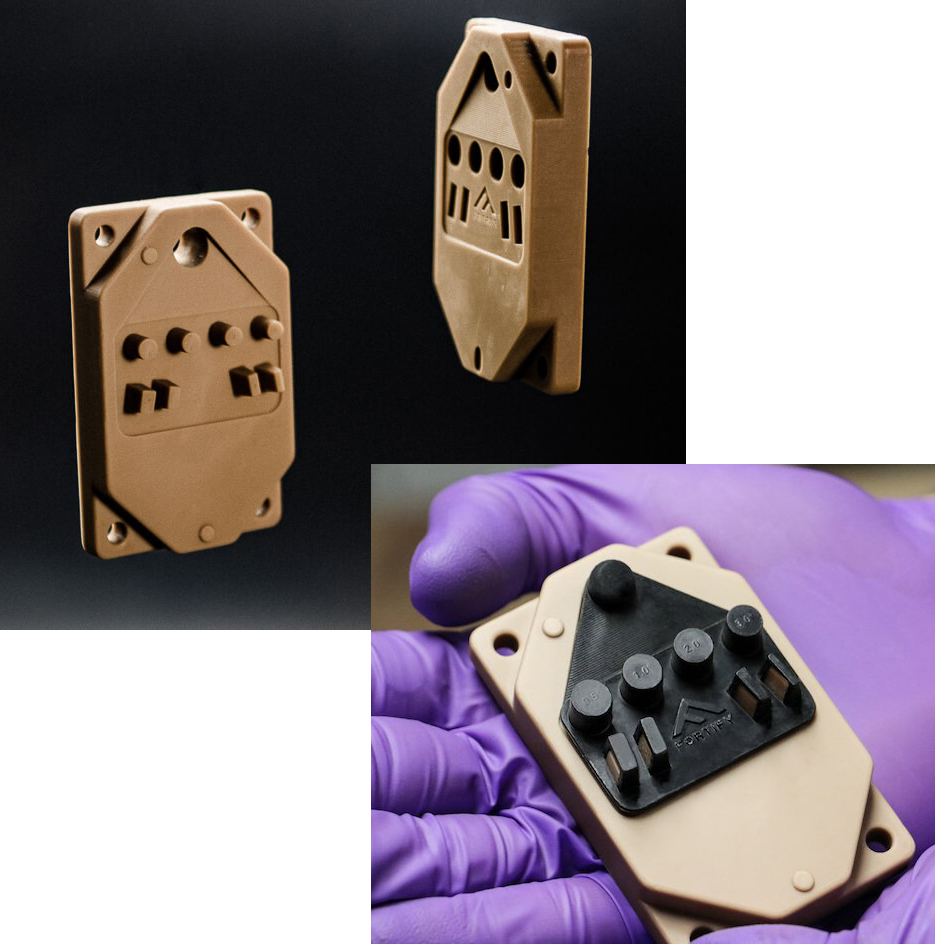
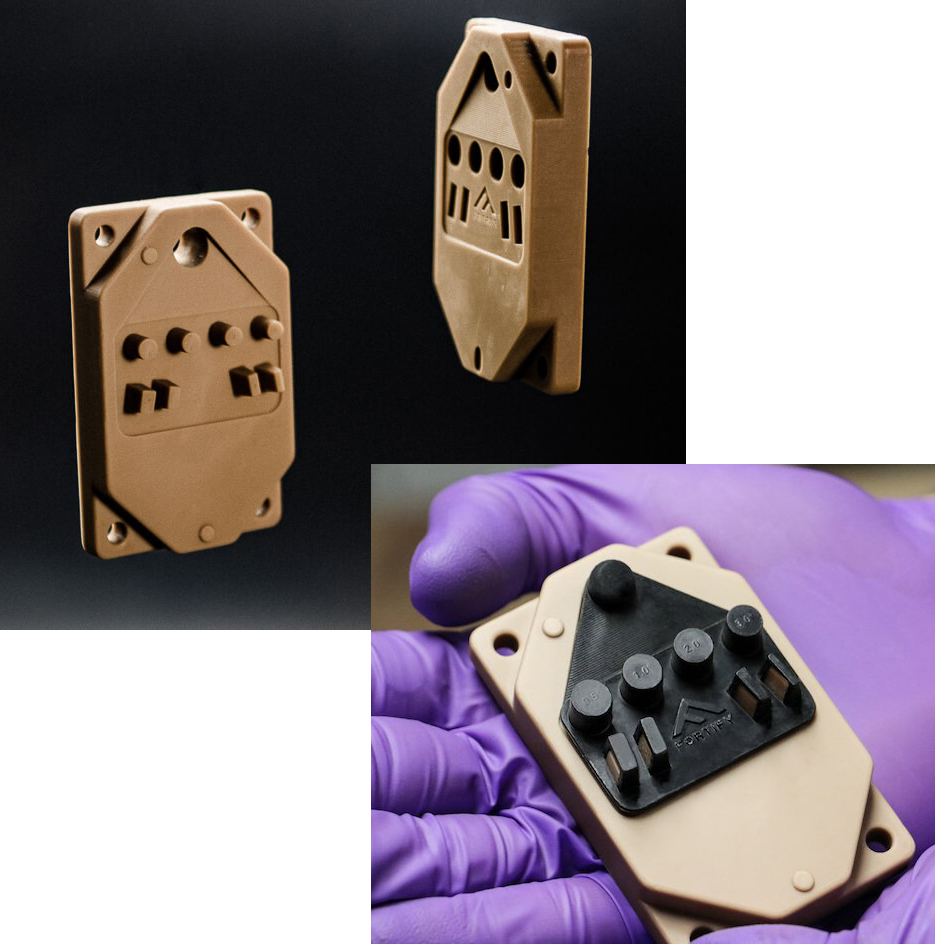
Die magnetische 3D-Drucktechnologie Fluxprint von Fortify kann Fasern so ausrichten, dass sie „Peg“-Vorsprünge an Spritzgusswerkzeugen verstärken. Quelle | Stärken.
„Wir bieten Spritzgusswerkzeuge, die deutlich günstiger sind als herkömmlich bearbeitetes Metall, in einem Bruchteil der Zeit geliefert werden können und Funktionen bieten, die mit herkömmlichen Bearbeitungstechniken nicht erreicht werden können“, so Martin weiter. „Ein Kunde würde jedes Jahr 12 verschiedene Designs durchlaufen, die aus Aluminium gefertigt wurden. Wir haben ihre Markteinführungszeit erheblich verkürzt und in mehreren Monaten mehr als ein Dutzend Designs produziert. Sie können jetzt innerhalb weniger Wochen vom Design zu den Teilen im Regal wechseln.“ Ein weiterer Vorteil ist die Möglichkeit, Vorsprünge zu verstärken, die als "Pegs" bezeichnet werden. Diese Extrusionen mit hohem Seitenverhältnis ziehen sich oft heraus. Die Verstärkung verhindert dies und hält gleichzeitig enge Toleranzen ein.
Lesen Sie mehr über die Vorteile von Fortify bei Spritzgusswerkzeugen in der Schwesterzeitschrift Additive Manufacturing von CW.
Offene Materialien, neue Entwicklungen
Fortify verfolgt einen offenen Materialansatz. „Wir möchten die Möglichkeiten unserer Kunden für Wachstum und Exploration im Bereich Additive nicht einschränken“, erklärt Karlo Delos Reyes, VP of Applications von Fortify. „Wir garantieren unseren Kunden Flexibilität und die besten verfügbaren Materialien durch offene Innovation.“
„Wir arbeiten mit großen Polymerherstellern zusammen und passen die Oberflächenchemie von Additiven an“, sagt Martin. Er weist darauf hin, dass jeder Füllstoff seine eigenen Vor- und Nachteile in Bezug auf Verschleißfestigkeit, Temperaturverhalten usw. hat. „Bei Fasern reicht die Länge je nach Anwendung von wenigen µm bis zu einigen mm. Wo eine Oberflächenauflösung erforderlich ist, verwenden wir einen höheren Anteil an Additiven mit geringerer Länge. Wo wir uns eine rauere Oberfläche leisten können, aber beispielsweise die Zugfestigkeit optimieren wollen, verwenden wir längere Faseradditive.“
Eine der Strategien von Fortify besteht darin, mit Branchenführern und Lieferanten zusammenzuarbeiten, um Fachwissen zu nutzen und die gegenseitige Befruchtung von Ideen zu ermöglichen. Fortify gab vor kurzem eine Partnerschaft mit DSM Additive Manufacturing (Hoek van Holland, Niederlande und Elgin, Illinois, USA) bekannt, um Hochleistungs-Verbundwerkstoffe zu entwickeln, die in Fortifys Drucksystemen verwendet werden, um eine verbesserte mechanische und Temperaturleistung zu erreichen. „Sie werden unsere Harzpalette erweitern“, sagt Martin, „und wir freuen uns, mit ihnen zusammenzuarbeiten, um innovative Harze zu entwickeln.“
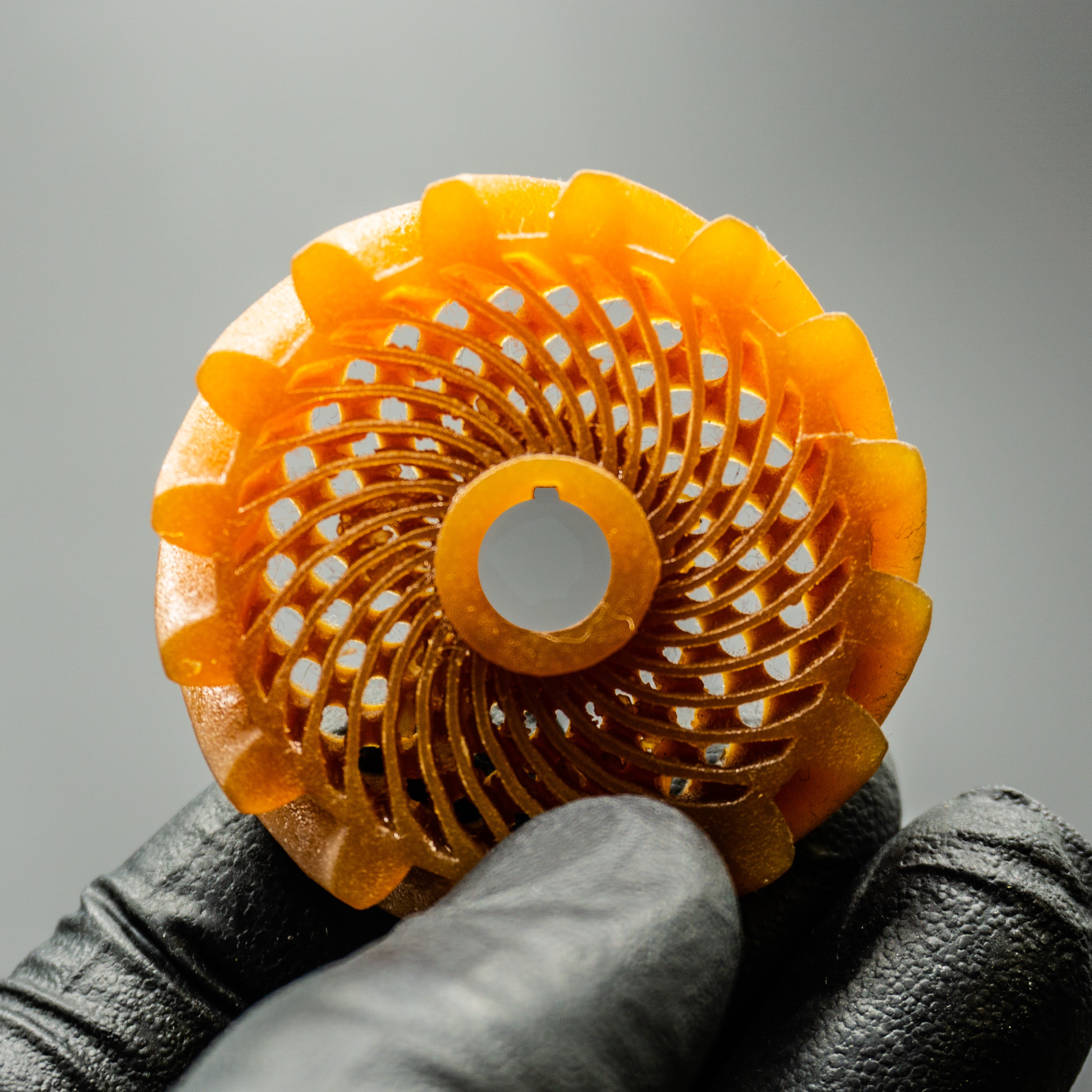
Glasfaserverstärktes Verbundteil hergestellt mit Fluxprint. QUELLE | Stärken.
Z-Richtungsverstärkung und Anwendungen
Fluxprint druckt immer noch nach Schichten. Ist es also möglich, eine Verstärkung in z-Richtung zu erreichen? „Wenn Sie 2 Millimeter lange Fasern drucken, können Sie diese nicht in z-Richtung legen“, sagt Martin. „Aber du könntest kürzer werden Fasern in z-Ausrichtung. Wir betrachten mehrere Längenskalen und wir sehen, dass sich das in Zukunft für eine optimierte Lastübertragung entwickelt.“
Fortify produziert bereits Teile für UAVs, einschließlich Propeller, und sieht viele weitere Anwendungen dieser Art in der Luft- und Raumfahrt. „Wir haben einen kleinen Baubereich, daher konzentrieren wir uns auf Anwendungen, bei denen wir problemlos kleinere Teilemengen erfüllen können“, sagt Martin. „Dies ist ein ausgereiftes Ökosystem, aber wir bieten ein neues Leistungsniveau bei den mechanischen Eigenschaften bei hohen Temperaturen und Toleranzen.“ Er zitiert die Möglichkeit, die Wärmeformbeständigkeit eines Teils zu verbessern und erklärt, dass es in der Automobilindustrie Dutzende von Teilen unter der Motorhaube gibt, die Festigkeit und Steifigkeit bieten müssen, während sie Temperaturen von 160°C ausgesetzt sind. „Solche Teile mit komplexen Geometrien eignen sich mit unserer Technologie gut für den 3D-Druck. Im Vergleich zu den aktuellen Verfahren zum Formen und Bearbeiten von Teilen aus PEI (Polyetherimid) bieten wir eine höhere Leistung, eine kürzere Vorlaufzeit und ein hohes Potenzial für niedrigere Kosten .”
Der Werkzeugbau ist ebenfalls ein aktueller Markt, einschließlich Formen, Vorrichtungen und Vorrichtungen für das Spritzgießen. „Auch hier sind unsere Teile steifer, fester und haben eine höhere Temperaturbeständigkeit, wodurch die Maßgenauigkeit im Einsatz beibehalten wird“, sagt Martin. „Aber ihr wirklicher Wert liegt darin, nicht erfordern eine erhebliche Nachbearbeitung, wie sie beispielsweise beim Einsatz von EDM-Maschinen erforderlich ist, und entsprechen dennoch der Qualität von Vorrichtungen, die mit diesen traditionellen Methoden, einschließlich CNC-Fräsen, hergestellt werden.“
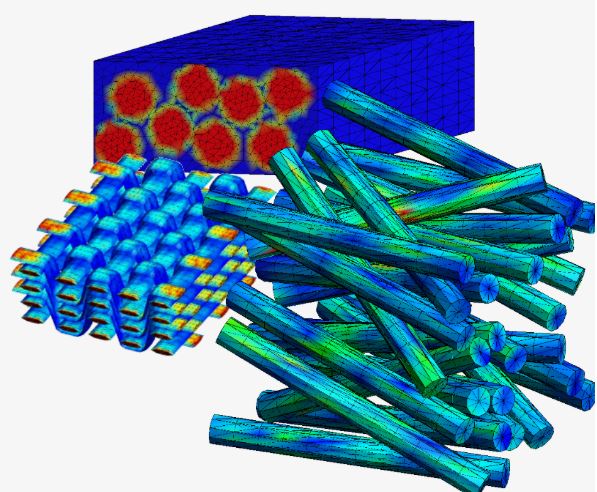
Quelle | MultiMechanik
Entwicklung der nächsten Generation multiskaliger, multifunktionaler Verbundwerkstoffe
Fortify ist eine Partnerschaft mit MultiMechanics (Omaha, Neb., USA) eingegangen, einem Entwickler von Multiskalenmodellierungs- und Simulationssoftware für fortschrittliche Materialien. Diese Partnerschaft ist aus mehreren Gründen interessant. Zunächst wird Fortify das Flaggschiffprodukt von MultiMechanics, MultiMech, verwenden, um die Leistung von Teilen vorherzusagen und optimieren deren Design und Faserorientierung, bevor sie gedruckt werden. Daher wird MultiMech agieren, um das Feedback für das geschlossene iterative Design bereitzustellen , die es Benutzern ermöglicht, Fluxprinted-Verbundteile schneller zuzuschneiden und zu optimieren. Fortify und MultiMechanics planen außerdem die Integration von MultiMech in Fortifys INFORM Software für generatives Design und Druckkontrolle. Somit werden vom Design über das virtuelle Testen bis zum Drucken alle Funktionen in einem einzigen, digitalen Stream gesteuert.
Für den zweiten Punkt ist es wichtig zu verstehen, was MultiMechanics über seine MultiMech-Software bietet:
- Multiskalige Finite-Elemente-Analyse , inklusive Modellierung einer praktisch unbegrenzten Anzahl von Skalen (z. B. Nano, Mikro, Ply, Laminat, Part).
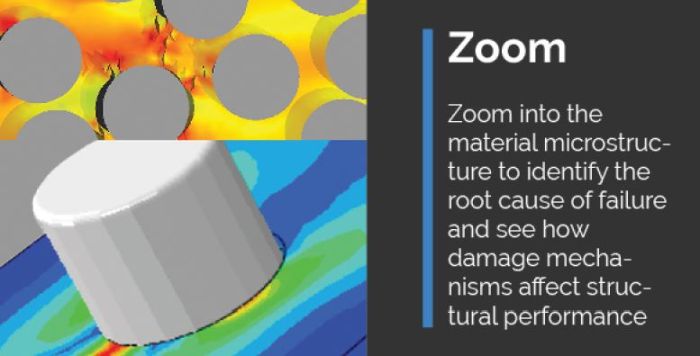
- Automatische Generierung komplexer 3D-Finite-Elemente-Mikrostrukturen und Modellierung fast jeder Materialmikrostruktur, einschließlich Endlos- und Schnittfasern, Partikeln, Hohlräumen, Schäumen, Geweben usw.
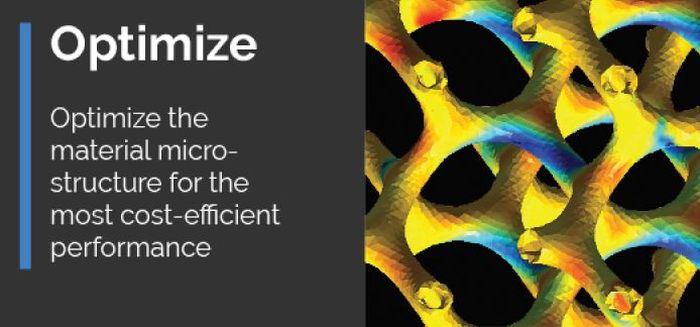
- Modelleffekte mikroskaliger Bestandteile, einschließlich Interaktionen , Volumenanteile, Verteilung und Orientierung, plus Import p prozessbedingte Variation aus Programmen (z. B. Moldex3D, Moldflow).
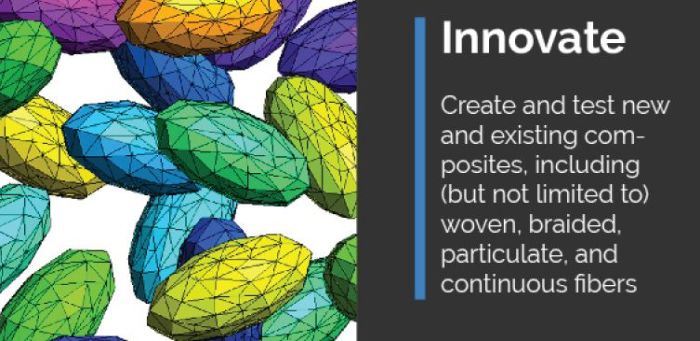
- Analysieren Sie, wie sich Fertigungsabweichungen auf die Teileleistung auswirken und führe da aus Magiermodellierung einschließlich Multiskalenübergang von Mikrorissen in Makrorisse.
Dies geht darauf zurück, warum Martin und Erb Fortify in erster Linie gründeten. In ihrem Artikel aus dem Jahr 2015 „Designing bioinspired Composite Verstärkungsarchitekturen über 3D-Magnetdruck“ heißt es:
Martin und Erb diskutieren natürliche Verbundwerkstoffe, die diskontinuierliche Fasern und Verstärkungspartikel verwenden, die in komplexen Architekturen mit mehreren Maßstäben organisiert sind überlegene Eigenschaften gegenüber ihren Bestandteilen zu erzielen. Ein Beispiel von Qunfeng Cheng in einem 2017 Materials Today Artikel ist Perlmutt in Abalone-Muscheln. Bestehend aus 95 Vol.% anorganischem Aragonit und 5 Vol.% organischer Proteinmatrix, ist die Bruchzähigkeit von Perlmutt 3.000 mal höher als die von Aragonit. Cheng merkt an, dass dies einen "Verstärkungseffekt" bei den mechanischen Eigenschaften zeigt, der weit über die Regel von Mischungen in traditionellen Verbundwerkstoffen hinausgeht .
In den 2018 Erweiterten Materialien Artikel „Additive Manufacturing as a Method to Design and Optimize Bioinspired Structures“, behaupten die Autoren Audrey Velasco-Hogan, Jun Xu und Marc A. Meyers, dass die hierarchische Struktur Materialien wie Perlmutt, Knochen, Bambus und Schalen von Krustentieren ermöglichen ihre beeindruckende Kombination von Festigkeit, Modul, Leichtgewicht, Zähigkeit und Ermüdungsbeständigkeit. Ihre Partikel/Filamente und ihre Matrix sind auf jeder Ebene unterschiedlich organisiert (z. B. Nano-, Mikro-, Meso-, Makro-), Variieren der Eigenschaften auf jeder Ebene (d. h. ein Multiskalen-Komposit). In Kombination mit effizienten Schnittstellen zwischen den Ebenen wirkt diese hierarchische Struktur synergistisch, um die Rißausbreitung zu verringern und die Zähigkeit zu erhöhen unter Beibehaltung der Härte – etwas, das in Keramik nach etwa einem Jahrhundert der Versuche noch nicht erreicht wurde.
Zukunft von Verbundwerkstoffen und INFORM
Das ist die Zukunft von Verbundwerkstoffen:Entwicklung von hierarchischen Verbundwerkstoffen mit einzigartigen Eigenschaften auf präzise Anwendungen zugeschnitten. Und es wird bereits zügig vorangetrieben. So ist beispielsweise das Deutsche Zentrum für Luft- und Raumfahrt (DLR) in Stuttgart auch eine Partnerschaft mit MultiMechanics eingegangen. um zu verstehen, wie sich Temperaturänderungen auf die Mikrostruktur und das Materialverhalten von Keramik-Matrix-Verbundwerkstoffen (CMCs) auswirken . Diese Analyse gilt als entscheidend für die zukünftige Produktion von CMC-Komponenten des DLR, darunter Düsen für Raketen und Wärmeschutzsysteme für Wiedereintrittsfahrzeuge. „Unsere Arbeit bei MultiMechanics war in den letzten zehn Jahren der genauen Verknüpfung des mikrostrukturellen Verhaltens gewidmet. von fortschrittlichen Materialien auf die Gesamtleistung des Teils und seine Herstellung “, sagt Dr. Flavio Souza, Präsident und CTO von MultiMechanics. „Mit MultiMech können wir Mikrostrukturrisse modellieren und bestimmen, wie sich diese auf das gesamte Verbundbauteil auswirken würden“, sagt Neraj Jain, Gruppenleiter in der Abteilung Keramische Verbundwerkstoffe und Strukturen am DLR. „Die effiziente Integration von MultiMech mit unseren anderen FEA-Tools wie Abaqus und ANSYS steigert unsere Produktivität und bringt uns unserem Ziel näher, CMC-Materialien virtuell zu optimieren .“
Sobald diese Verbundwerkstoffe virtuell optimiert wurden, werden sie gedruckt, wobei MultiMech in die INFORM-Software von Fortify eingebettet ist, die über ihr generatives Design-Backbone bereits auf organische, lastoptimierte Architekturen ausgerichtet ist . (Beachten Sie, dass auch der Geschäftsbereich Composite Materials von Solvay sowohl in MultiMechanics als auch in die 3D-Drucktechnologie investiert hat.)
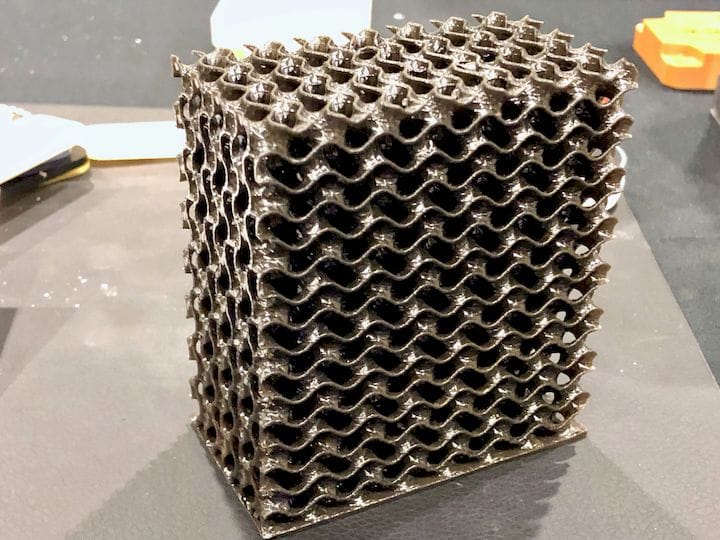
Faserverstärktes Gitter, Design bereitgestellt von nTopology. Quelle | Stärken.
„INFORM verwendet fortschrittliche Algorithmen zur Optimierung der Faserorientierung für jedes Teil“, erklärt Martin. „Während der 3D-Druck-Workflow traditionell mit STL beginnt, um das Design zu schneiden, beginnt unser mit FEA (ein Modell mit Spannung und Dehnung) und entscheidet dann, in welche Voxel dieses modellierte Design unterteilt und wie die Fasern ausgerichtet werden sollen. Wir durchlaufen Iterationen, richten die Fasern mit Spannungs-/Dehnungsfeldvektoren aus, simulieren dann das Verhalten dieses Drucks und verwenden diese Daten, um das Design zu verfeinern und zu optimieren, um ein mikrostrukturelles generatives Design zu erreichen .”
Nur der Anfang
Beachten Sie, dass diese zukünftigen Verbundwerkstoffe eine Reihe von Materialien umfassen. Das Naval Research Laboratory (NRL, Arlington, Virginia, USA) entwickelt CMCs unter Verwendung einer keramischen Matrix mit einer sekundären keramischen Verstärkung durch Nanopartikel und/oder Filamente. Diese CMCs können auch eine kontinuierliche Faserverstärkung verwenden. Mit anderen Worten, auf jeder Ebene können unterschiedliche Bestandteile und Architekturen verwendet werden, um die erforderliche Zähigkeit und die maßgeschneiderten elektrischen und thermischen Eigenschaften zu erzielen (zum Beispiel in Hyperschall, lesen Sie mehr in meinem Artikel über Nanokomposite vom Juli 2019).
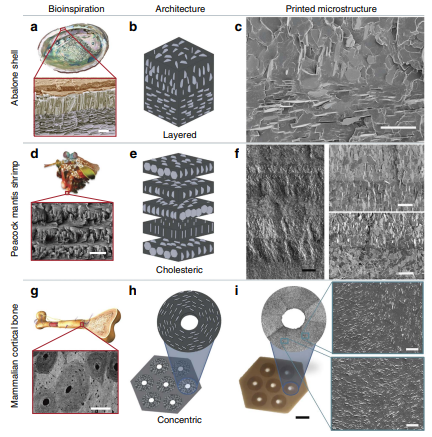
QUELLE | Abbildung 3, „Entwurf bioinspirierter Verbundverstärkungsarchitekturen über 3D-Magnetdruck“ von Joshua J. Martin, Brad E. Fiore und Randall M. Erb, Nature Communications Band 6 (2015).
Auch hierarchische Verbundwerkstoffe werden mit verstärkten Epoxidfarben und thermoplastischen Polymermatrizen gedruckt und getestet. Dies ist vielleicht der größte Vorteil für Fortify als Startup. Sie bereitet sich nicht nur auf die Verbundwerkstoffe der Zukunft vor, sondern entwirft und produziert sie bereits. Und auch wenn das bereits Erreichte beeindruckend ist – es ist erst der Anfang.
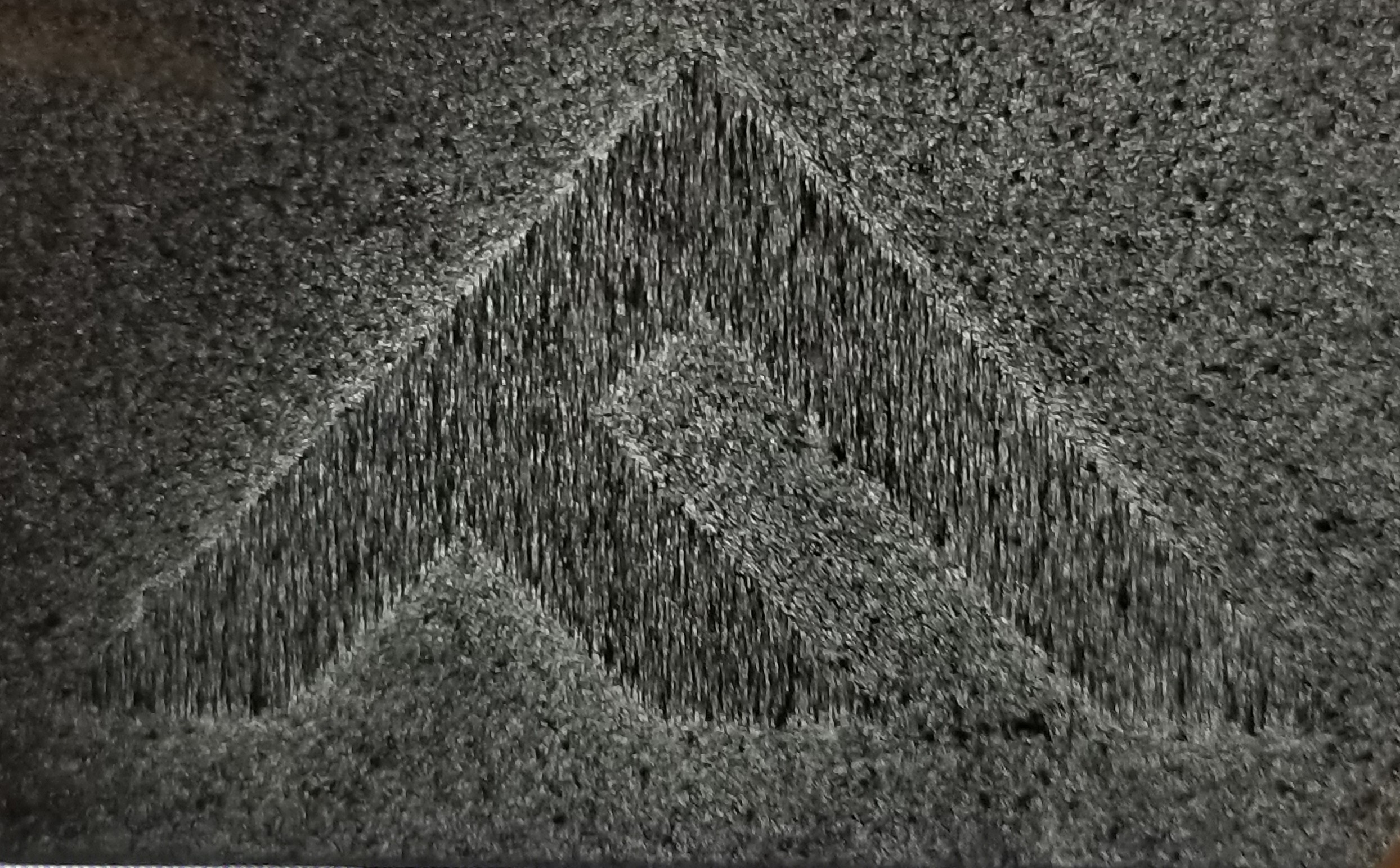
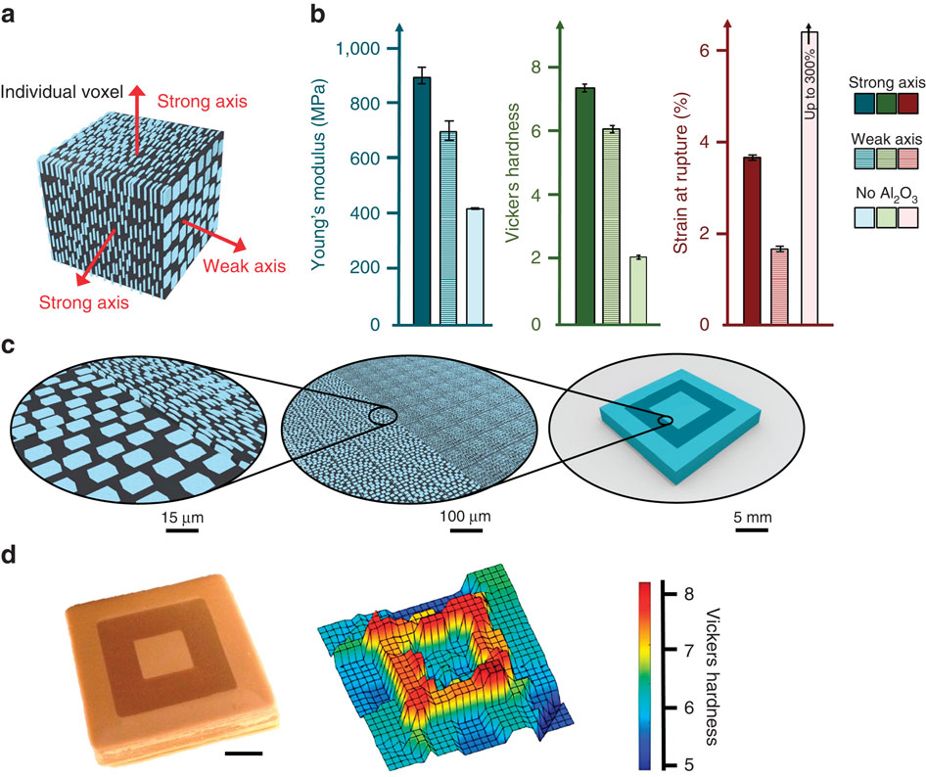
Harz
- Die 3 grundlegenden Schritte des 3D-Drucks
- Könnte Multi-Material-3D-Druck der nächste Schritt für AM sein?
- Das ABC des 3D-Drucks
- Die Evolution des 3D-Drucks
- Community Colleges:Ausbildung der nächsten Generation von Herstellern
- Tag der Fertigung 2017:Bildung der nächsten Generation von Arbeitnehmern
- 3D-Druckverbundwerkstoffe mit Endlosfasern
- Material für die nächste Generation intelligenter Sensoren
- Ultradünne Terahertz-Quelle ebnet den Weg zur nächsten Generation der Kommunikationstechnologie
- COVID-19:Nachfrage nach Smart Factory der nächsten Generation