FDM-3D-Druck:Wo stehen wir heute?
Fortschritte beim extrusionsbasierten 3D-Druck verändern die Entwicklung der Fused Filament Fabrication (FFF)-Technologie.
FFF oder FDM (Fused Deposition Modelling) ist eine der am häufigsten verwendeten 3D-Drucktechnologien. Mit zunehmender Akzeptanz in allen Industriesegmenten war FDM die umsatzstärkste 3D-Drucktechnologie im Jahr 2017 und soll die größte installierte Basis (SmarTech) haben.
Was hat also das Wachstum und die Reife der Technologie beflügelt? Und wie wird sich der 3D-Druck auf Extrusionsbasis in Zukunft entwickeln?
Um diese Fragen zu beantworten, wirft dieser Artikel einen Blick auf einige der wichtigsten Entwicklungen, die FDM prägen, und was als nächstes für diese aufregende Technologie ansteht.
Wichtige Meilensteine in der Entwicklung von FDM
- 1989 :Scott und Lisa Crump patentieren eine neue additive Fertigungsmethode, die unter dem Markenzeichen Fused Deposition Modeling (FDM) steht, und gründen das Hardwareunternehmen Stratasys.
- 1991 :Stratasys vermarktet zum ersten Mal den FDM-3D-Druck.
- 2005 :Markiert den Beginn des RepRap-Projekts, das dazu beiträgt, die Kosten des FDM-3D-Drucks zu senken.
- 2008 :Stratasys gibt bekannt, dass es Hochleistungs-ULTEM 9085 für seine FDM 900mc- und 400mc-Maschinen anbieten wird – ein großer Fortschritt für FDM-Materialien.
- 2009 :Die ersten FDM-Patente laufen ab und ermöglichen es Enthusiasten, ihre eigenen DIY-FDM-3D-Drucker zu entwickeln und zu vermarkten. Unternehmen wie MakerBot und Lulzbot werden mit ihren DIY-Drucker-Kits sehr erfolgreich.
- 2011 :Ultimaker, ein führender Hersteller von Desktop-FDM-3D-Druckern, wird gegründet.
- 2013 :Stratasys erwirbt MakerBot, einen Hersteller von Desktop-3D-Druckern.
- 2013 :Markforged, ein Hardwarehersteller, der FDM-3D-Drucktechnologie für Verbundwerkstoffe anbietet, wird gegründet.
- 2014 :Der große Hersteller von FDM-3D-Druckern BigRep wird gegründet.
- 2015 :Voodoo Manufacturing startet sein 3D-Druckgeschäft, das sich bis 2019 zu einer digitalen Fabrik mit über 200 FDM-Maschinen entwickeln wird.
- 2017 :Stratasys stellt seinen Continuous 3D Build Demonstrator vor – eine modulare 3D-Druckeinheit für Hochdurchsatzvorgänge.
- 2018 :Essentium vermarktet seine Hochgeschwindigkeits-Extrusionsplattform mit seiner FlashFuse-Technologie, die elektrische Heizung zum 3D-Drucken von Teilen verwendet.
Die Ursprünge von FDM
Die Entstehung des 3D-Drucks auf Extrusionsbasis geht auf die späten 1980er Jahre zurück, als der Ingenieur und Erfinder Scott Crump eine neuartige Rapid-Prototyping-Methode entwickelte.
1989 patentierte Crump die neue Technologie und nannte sie Fused Ablagerungsmodellierung. Im selben Jahr gründeten Scott und Lisa Crump gemeinsam Stratasys und lieferten zwei Jahre später ihre erste FDM-Maschine, den 3D Modeler.
Seitdem hat die FDM-Technologie enorm an Bedeutung gewonnen. die Lücke bei kostengünstigeren Rapid-Prototyping-Lösungen zu schließen.
Heute bleibt Stratasys eines der größten Hardwareunternehmen in der 3D-Druckindustrie und bietet 9 Modelle seiner FDM-Maschinen und mehrere Polyjet 3D-Drucker an.
Aktuelle FDM-3D-Drucker verwenden den gleichen Prozess des schichtweisen Schmelzens und Extrudierens von thermoplastischen Materialien wie die erste FDM-Maschine vor dreißig Jahren.
Es wäre jedoch falsch anzunehmen, dass sich die Technologie nicht weiterentwickelt hat. Zahlreiche Entwicklungen haben den FDM-3D-Druck geprägt und ihn zu einer der am weitesten verbreiteten additiven Technologien gemacht.
Der Aufstieg des RepRap-Projekts und des kostengünstigen FDM
Der Erfolg der FDM-Technologie lässt sich teilweise mit dem Aufstieg des RepRap-Projekts und dem Auslaufen mehrerer FDM-Patente Ende der 2000er Jahre erklären.
Das RepRap-Projekt förderte das Konzept von quelloffenen, sich selbst replizierenden 3D-Druckern. Das Konzept wurde zuerst von der DIY-Community übernommen. Aber nach dem Ablauf der wichtigsten FDM-Patente von Stratasys Ende der 2000er Jahre tauchten viele Unternehmen auf, um RepRep-basierte FDM-3D-Drucker zu kommerzialisieren.
Dies hat zu einer Reihe von FDM-Desktop-3D-Druckern zu deutlich geringeren Kosten geführt – was die Technologie zu einem großartigen Einstiegspunkt für Unternehmen macht, die mit der Technologie neu sind.
Die 2010er:Eine neue Generation von FDM
Der Aufstieg der RepRap-Bewegung und das Auslaufen der wichtigsten FDM-Patente haben die Entwicklung der Technologie im letzten Jahrzehnt erheblich beschleunigt. Eine Reihe vielversprechender Unternehmen ist entstanden, die den FDM-3D-Druck weiter vorantreiben wollen.
Pionierender kontinuierlicher 3D-Druck von Kohlefasern
Im Jahr 2014 machte ein kleines Startup, Markforged, mit seiner Continuous Filament Fabrication (CFF) 3D-Drucktechnologie Furore. Das Unternehmen ist angeblich das erste Unternehmen, das den Endlosfaser-3D-Druck ermöglicht und neue industrielle Möglichkeiten für die FDM-Technologie eröffnet.
Die kompakten und Desktop-3D-Drucker von Markforged werden von CFF angetrieben und verwenden zwei Druckköpfe:einen zum Extrudieren von Filamenten auf Nylonbasis und den anderen zum Verlegen von Endlossträngen hochfester Fasern, einschließlich Kohlefaser, Kevlar und Glasfaser .
Die Verstärkungsfasern bilden das „Rückgrat“ des gedruckten Teils und ergeben steife, starke und haltbare Teile.
Zum Beispiel soll die industrietaugliche X7-Maschine von Markforged, der neueste von sechs Polymer-3D-Druckern von Markforged, Teile stärker und 40 % leichter drucken als 6061 Aluminium.
Der X7 kostet 70.000 US-Dollar und bietet ein Bauvolumen von 330 x 270 x 200 mm und eine Schichthöhe von 50 Mikrometern. Für eine vergleichsweise preisgünstige Maschine sind diese Spezifikationen recht ordentlich, ganz zu schweigen von der Fähigkeit des X7, langlebige Werkzeuge sowie funktionale Ersatz- und Endverbrauchsteile zu drucken.
Indem Markforged die Möglichkeit bietet, mit verstärkten Materialien zu drucken, hat sich Markforged einen sehr profitablen Markt erschlossen. Allein im Jahr 2018 hat das Unternehmen Berichten zufolge über 2.500 industrielle 3D-Drucker ausgeliefert. Mit diesem rasanten Wachstum hat Markforged sich auf den Weg gemacht, eines der größten AM-Unternehmen der Branche zu werden.
Der neue Maßstab für den großformatigen FDM-Druck?
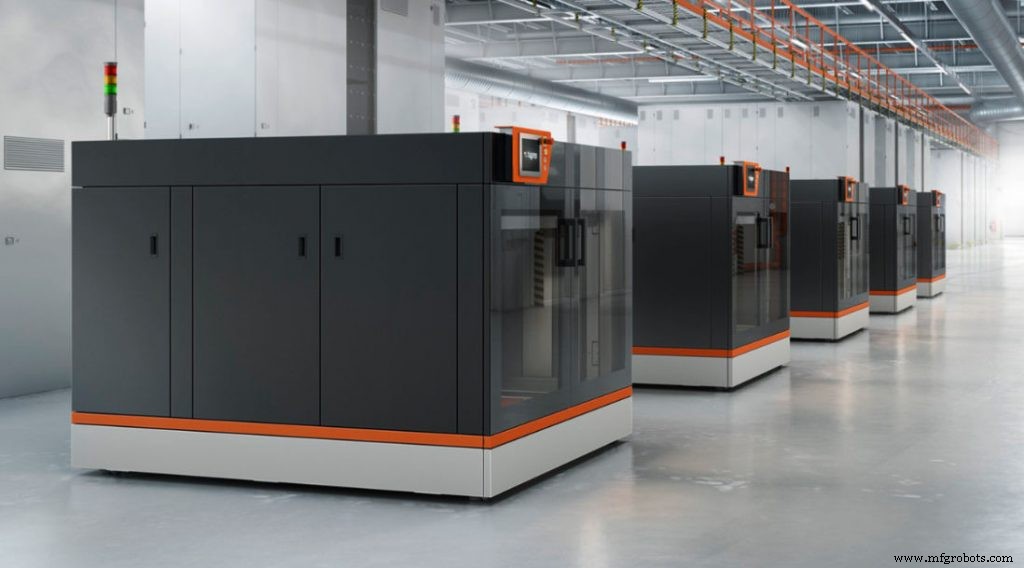
Großformatiger 3D-Druck hat das Potenzial, viele Herausforderungen zu lösen, denen sich Hersteller beim Prototyping und der Produktion größerer Teile gegenübersehen.
Solche Teile haben normalerweise längere Vorlaufzeiten, da eine Montage erforderlich ist. Außerdem müssen größere Werkzeuge hergestellt werden, was oft zu erheblichen Kosten führt.
Ein Unternehmen, das bei der Bewältigung dieser Herausforderungen hilft, ist BigRep. BigRep wurde 2014 gegründet und positioniert sich als Hersteller der größten Extrusions-3D-Drucker auf dem Markt mit einem Druckvolumen seiner Maschinen von über 1m³.
Der 3D-Druck großer Objekte hat zwar seine Vorteile, aber es gibt auch eine wichtige Einschränkung:die Geschwindigkeit. Das Drucken größerer Teile kann Tage oder sogar Wochen dauern, mit einem erhöhten Risiko von Druckfehlern.
BigRep möchte dieses Problem auf verschiedene Weise angehen.
In der Vergangenheit führte BigRep größere Düsen ein, um größere Mengen Kunststoff schneller extrudieren zu können, und führte auch entsprechend große Filamentspulen ein.
2017 , begann das Unternehmen mit der Produktion seines „Hochgeschwindigkeits“-Filaments, mit dem sich die Druckzeiten um bis zu 50 % verkürzen lassen.
Aber eine der aufregendsten Fortschritte ist die Metering Extrusion Technology (MXT .) von BigRep ).
Auf der formnext 2018 stellte BigRep zwei neue MXT-gesteuerte 3D-Drucker vor:BigRep PRO und BigRep EDGE. Das in Zusammenarbeit mit Bosch Rexroth entwickelte MXT-Extrudersystem zeichnet sich durch mehrere wichtige Merkmale aus, die es von Standardextrudern unterscheiden.
Es verfügt über ein spezielles Reservoir, in dem das geschmolzene Material gehalten wird. Ein von einem Schrittmotor angetriebenes Zahnrad nimmt eine bestimmte Menge des Materials aus diesem Vorratsbehälter und schiebt es in die Düse.
Dieser Ansatz ermöglicht die volle Kontrolle über die Geschwindigkeit und Menge des aufgetragenen Materials. Laut BigRep macht das MXT-System seine neuen Drucker fünfmal schneller als aktuelle Extrusionsmaschinen und trägt zu einer deutlich höheren Präzision bei.
Das aktuelle MXT-System ist nur die erste Iteration des MXT-Konzepts, aber mit all seinen Vorteilen wird es spannend sein zu sehen, wie sich diese Technologie in Zukunft entwickelt.
Infundiert mit isotroper Stärke
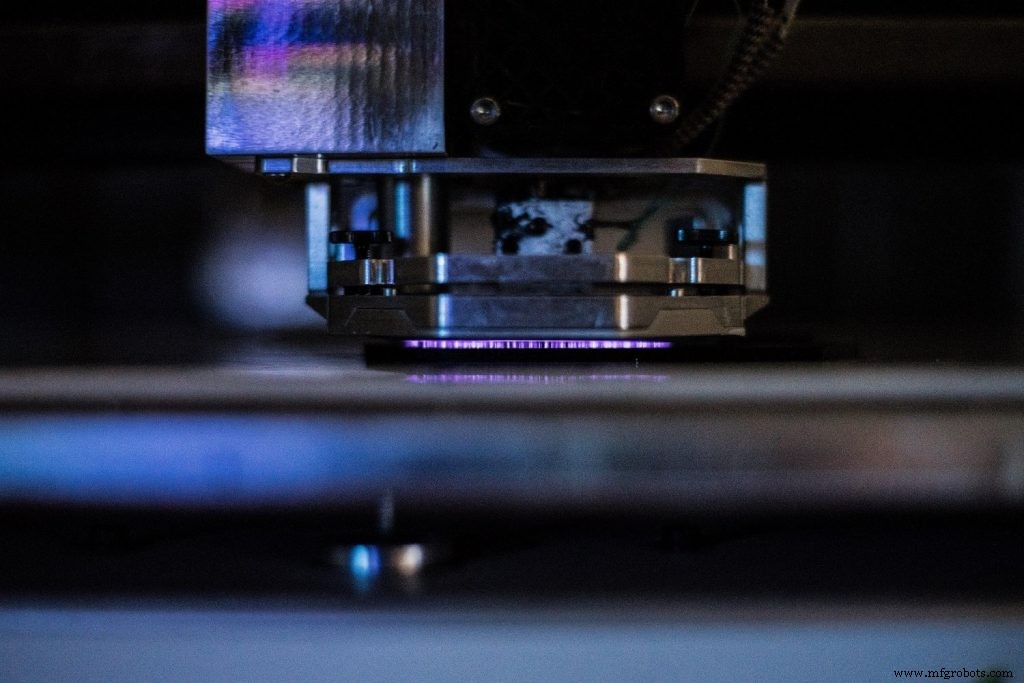
Neben Geschwindigkeitsbeschränkungen sind anisotrope Teile aufgrund der schichtweisen Natur des Druckprozesses ein weiteres häufiges Problem beim FDM-3D-Druck.
Das schichtweise Abscheiden von Material führt zu einer Schwäche des Teils in der Z-Achse (der Richtung, in der die Schichten abgeschieden werden). Während also ein Spritzgussteil zu fast 100 % isotrop (in alle Richtungen gleich stark) sein kann, verlieren FDM-Teile typischerweise in der Z-Achse an Festigkeit.
Einige Industriemaschinen lösen dieses Problem, indem sie ein Gehäuse verwenden, um den gesamten Gebäudebereich zu beheizen. Obwohl diese Lösung dazu beiträgt, die Verbindung zwischen den Schichten zu verbessern, ist sie tendenziell zu energieaufwendig.
Das 3D-Druckunternehmen Essentium hat eine neue, vielversprechende FDM-Technologie entwickelt, um die mechanische Festigkeit von 3D-gedruckten Teilen zu verbessern.
Die als FlashFuse bekannte Technologie beinhaltet die Abscheidung eines auf Energie ansprechenden Filaments und das Anlegen von elektrischem Strom. Dieser Strom heizt das Teil auf und formt die Schichten effektiv zusammen.
Dieser Ansatz hat zwei Vorteile.
Erstens erreichen 3D-gedruckte Teile mit der FlashFuse-Technologie eine Festigkeit, die mit der von Spritzgussteilen vergleichbar ist. Zweitens verhindert es die Verformung des Teils wie beispielsweise ein Verziehen, da die Temperatur während des Druckprozesses stabil bleibt.
Diese Technologie treibt jetzt den 3D-Drucker High Speed Extrusion (HSE) 180-S von Essentium an, der 75.000 US-Dollar kostet.
Die Überwindung einiger der wichtigsten Hindernisse beim FDM-3D-Druck hat dem Unternehmen geholfen, 22 Millionen US-Dollar in einer von BASF Venture Capital geführten Serie-A-Runde zu beschaffen. Mit der jüngsten Finanzierung möchte Essentium seine Technologie für Produktionsanwendungen vorantreiben und einen neuen Maßstab für den FDM-3D-Druck setzen.
Industrietaugliche FDM-Materialien
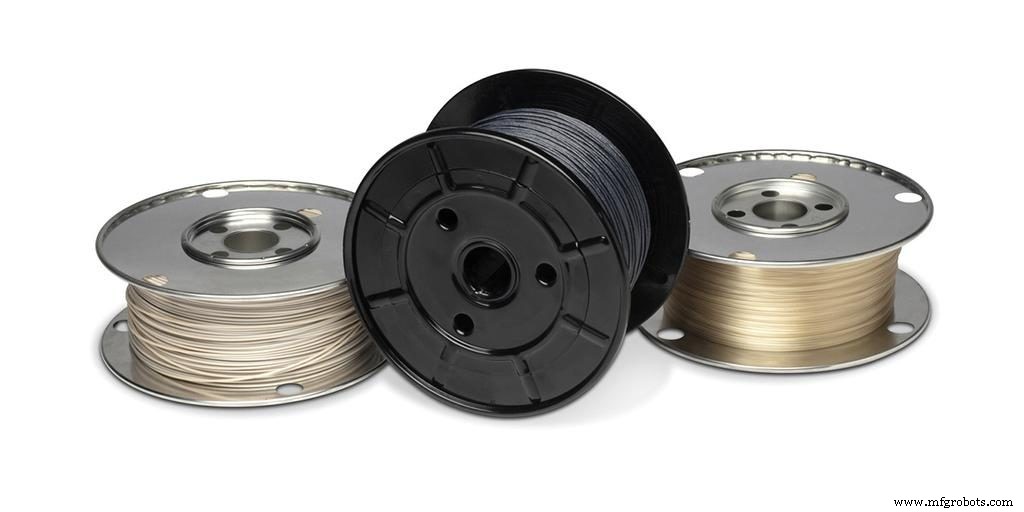
Obwohl der Markt für FDM-Materialien noch jung ist, hat er sich im Laufe der Jahre erheblich weiterentwickelt und die Materialwissenschaft über die Standard-PLA- und ABS-Filamente hinaus getrieben.
Heute können FDM-Anwender unter anderem Verbundwerkstoffe, Nylon, flexible, biokompatible und technische Materialien kaufen.
Besonders spannend ist die Möglichkeit, mit Hochleistungsmaterialien wie ULTEM und PEEK zu drucken.
Diese Thermoplaste sind aufgrund ihrer hohen Schmelztemperaturen besonders anspruchsvoll zu verarbeiten. Viele aktuelle FDM-Maschinen sind jedoch mit Hochtemperaturextrudern ausgestattet, was FDM zu einer der wenigen Additivtechnologien macht, die diese Hochleistungsthermoplaste verarbeiten können.
Viele der Fortschritte bei FDM-Materialien wurden durch die zunehmende Zahl von Chemieunternehmen ermöglicht, die der Industrie beitreten, um die industrielle Nutzung des 3D-Drucks voranzutreiben. Dazu gehören BASF, SABIC, Verbatim (Mitsubishi Chemical Group), Evonik und Solvay, um nur einige zu nennen.
Solvay hat beispielsweise kürzlich PEEK- und PPSU-Filamente auf den Markt gebracht. Beide Materialien haben außergewöhnliche Eigenschaften:PEEK ist bekannt für sein ausgezeichnetes Festigkeits-Gewichts-Verhältnis, während PPSU eine hohe Hitze-, Chemikalien- und Schlagfestigkeit besitzt.
Die Verfügbarkeit solcher Thermoplaste in Produktionsqualität ermöglicht Schlüsselanwendungen wie Flugzeugteile, Automobillager, Öl- und Gaskomponenten und medizinische Geräte.
Es gibt noch viel mehr FDM-Thermoplaste noch zu entwickeln. Aber die wachsende Nachfrage wird dazu beitragen, ihre Entwicklung zu stimulieren und neue Anwendungen für den 3D-Druck zu ermöglichen.
3D-Druckfarmen:die Zukunft von FDM?
Es gab einige Herausforderungen, die den Einsatz des FDM-3D-Drucks in Produktionsanwendungen einschränkten, darunter schwache Teile und langsame Druckgeschwindigkeiten.
Die jüngsten Entwicklungen in der FDM-Technologie tragen jedoch dazu bei, die Grenzen der Geschwindigkeit und Stärke zu überwinden. Aber damit FDM als Produktionstechnologie wirklich durchstarten kann, muss es skalierbarer werden.
Eine der Lösungen könnte in sogenannten FDM-3D-Druckfarmen liegen. Solche Farmen umfassen ein Netzwerk von einem Dutzend oder mehr 3D-Druckern, um eine Produktion rund um die Uhr zu ermöglichen. Voodoo Manufacturing ist ein Beispiel für ein Unternehmen, das diesen Ansatz in die Praxis umsetzt.
Das Unternehmen beherbergt über 200 FDM-3D-Drucker und verwendet fortschrittliche Software, um 3D-Druckaufträge automatisch verfügbaren Maschinen zuzuweisen. Mit seiner 3D-Druckfarm ist Voodoo Manufacturing in der Lage, Hunderte und sogar Tausende von Bestellungen zu Spritzgusspreisen zu erfüllen.
Die Hersteller von 3D-Druckern haben ebenfalls begonnen, auf diesem Konzept aufzubauen. Im Jahr 2017 präsentierte Stratasys seinen Continuous Build 3D Demonstrator, eine modulare Einheit mit mehreren FDM-3D-Drucker-„Zellen“, die jeweils gleichzeitig arbeiten und von einer zentralen, cloudbasierten Architektur gesteuert werden.
Stratasys hat die kommerzielle Verfügbarkeit der Continuous Build-Plattform noch nicht bekannt gegeben. Das Unternehmen glaubt jedoch, dass dieser Ansatz den Traum vom 3D-Druck für die Produktion erfüllen könnte.
Angesichts der Entwicklung hin zu robusteren Materialien und neuen Fertigungsstrategien steht FDM für die nächste Einführungswelle. Stärkere und größere Teile und ein schnellerer und besser skalierbarer 3D-Druckprozess werden neue Märkte für Extrusionsmaschinen eröffnen und die FDM-Technologie als riesige Fertigungsmöglichkeit etablieren.
3d Drucken
- Stressfreie Reinigung für den FDM-Druck
- Entwicklung von Standards für den 3D-Druck:Wo stehen wir heute? (Update 2020)
- Metall-3D-Druck:Wo stehen wir heute?
- Stereolithographie und digitale Lichtverarbeitung:Wo stehen wir heute?
- Wie Desktop-3D-Drucker den 3D-Druck verändern
- Wie ausgereift sind 3D-Metalldrucktechnologien?
- Industrie 4.0-Faktencheck:Wo stehen wir heute?
- Neue Durchbrüche in FDM von Stratasys
- Vergleich von 3D-Technologien:SLA vs. FDM
- FDM-3D-Druck:Desktop vs. Industriell