Wie ausgereift sind 3D-Metalldrucktechnologien?
[Bildnachweis:CCDC Army Research Laboratory]
Metall-3D-Druck umfasst eine breite Palette von Technologien, jede mit ihren eigenen Vorteilen und Anwendungen – sowie ihrem eigenen Reifegrad.
Wenn Sie eine bestimmte Metall-3D-Drucktechnologie für die Produktion einsetzen möchten, ist es wichtig zu verstehen, wo ihre Fähigkeiten und Grenzen derzeit liegen. Beim 3D-Metalldruck stehen Unternehmen jedoch vor der Herausforderung, die Realität vom Hype zu trennen.
Um Unternehmen dabei zu helfen, den Reifegrad der wichtigsten 3D-Metalldrucktechnologien einfacher einzuschätzen, werden wir heute auf der Grundlage eines Technology Readiness Level (TRL)-Systems, das zuerst von der NASA entwickelt wurde.
Was genau ist der Technology Readiness Level (TRL)?
Der „Technology Readiness Level“ wurde Anfang der 1970er Jahre von der NASA entwickelt und ist ein Ansatz, mit dem beurteilt wird, ob eine aufkommende Technologie für die Weltraumforschung geeignet ist. In den 1990er Jahren wurden TRLs von vielen US-Regierungsbehörden angewendet und werden heute in vielen Branchen verwendet.
Das TRL-System misst den Reifegrad einer Technologie von Stufe 1 (Konzeptbewertung) bis Stufe 9 (Erfolgreiche Bereitstellung) . Jede der neun Ebenen zeigt einen Meilenstein in der Entwicklung der Technologie.
Wie kann die TRL verwendet werden, um den Reifegrad von Metall-3D-Drucktechnologien zu bewerten?
Wir haben diesen Ansatz angewendet, um den Reifegrad der verschiedenen 3D-Drucktechnologien zu bewerten. Um eine TRL für jede Metall-3D-Drucktechnologie zu ermitteln, haben wir ihre Entwicklung, die Branchen, die sie übernehmen, wie sie heute verwendet wird und die Entwicklungen, die ihre Zukunft gestalten, analysiert.
Bemerkenswerterweise kann die TRL in einigen Fällen anwendungsspezifisch sein. Die Direct Energy Deposition-Technologie liegt beispielsweise bei einer TRL von 8 für Produktionsanwendungen, während ihre Anwendungen für Reparaturen Level 9 erreicht haben.
Basierend auf unseren Untersuchungen glauben wir, dass die Mehrheit der Metall-3D Drucktechnologien haben die TRL 7 überschritten, die sich auf das Testen in einer Betriebsumgebung zur Lösung von Leistungsproblemen und auf Anwendungen im funktionalen Prototyping und Werkzeugbau bezieht.
Einige haben sich auch unter normalen Betriebsbedingungen als erfolgreich erwiesen (TRL 8) und sind auf dem Weg zur Integration in das breitere Fertigungsökosystem (TRL 9).
Laser-Pulverbett-Fusion

Technologiereifegrad:8
Laser Powder Bed Fusion (PBF) ist eine der etabliertesten 3D-Metalldrucktechnologien. Beim Metall-PBF-Verfahren wird ein leistungsstarker, fein abgestimmter Laser selektiv auf eine Metallpulverschicht aufgebracht. Auf diese Weise werden Metallpartikel Schicht für Schicht zu einem Bauteil verschmolzen.
Die Ursprünge des metallischen PBF lassen sich bis ins Jahr 1995 zurückverfolgen, als das Fraunhofer-Institut in Aachen das erste Patent zum Laserschmelzen von Metallen anmeldete. Seitdem sind viele Unternehmen, darunter etablierte Player wie EOS, Concept Laser (übernommen von GE) und SLM Solutions, mit ihrer Sicht auf die Technologie in den PBF-Markt eingestiegen.
In den letzten zehn Jahren haben die Hersteller von Metall-PBF-3D-Druckern hart daran gearbeitet, die Technologie für die Produktion zu optimieren. Zu diesem Zweck haben wir wichtige Marktteilnehmer gesehen, die Lösungen für die automatisierte und integrierte Produktion auf den Markt gebracht haben.
Die meisten dieser Lösungen haben ähnliche Eigenschaften:Sie sind modular, konfigurierbar und bieten einen hohen Automatisierungsgrad, um die Effizienz zu maximieren und den manuellen Arbeitsaufwand zu reduzieren.
Gleichzeitig hat sich die Materialauswahl für PBF kontinuierlich erweitert. EOS hat beispielsweise im vergangenen Monat vier neue Metallpulver für seine Metall-3D-Drucker eingeführt. Darunter Edelstahl CX, Aluminium AlF357, Titan Ti64 Grade 5 und Titanium Ti64 Grade 23.
Dank dieser Entwicklungen hat Laser-PBF in vielen Branchen und Anwendungen Einzug gehalten. Eine Branche, die sich besonders für die Einführung von Metall-PBF interessiert, ist die Luft- und Raumfahrt.
Heute treiben 3D-gedruckte PBF-Metallteile wichtige Flugzeug- und Raumfahrzeugsysteme wie Motoren an. Hier glänzen die Schlüsselfähigkeiten der Technologie – die Herstellung komplexer Teile mit vereinfachter Montage und weniger Materialverschwendung – wirklich.
Ab sofort ist die Laser-PBF-Technologie in der Lage, Funktionsteile wiederholt zu liefern. Es sind jedoch noch einige Feinabstimmungen und Tests erforderlich, bevor sich die Hersteller auf die Serienproduktion festlegen können. Aus diesem Grund schlagen wir vor, dass es sich derzeit auf dem Technology Readiness Level 8 befindet.
In Zukunft werden die Benutzerfreundlichkeit und Zuverlässigkeit von Metall-PBF-Systemen zunehmen, was in vielerlei Hinsicht durch die Fortschritte in der Software und insgesamt getrieben wird Arbeitsablauf.
Ein Beispiel, das diesen Trend unterstützt, stammt vom kalifornischen Hersteller von Metall-3D-Druckern VELO3D.
Bei der Entwicklung seiner Laser-PBF-Technologie namens Intelligent Fusion hat das Unternehmen einen Schwerpunkt auf die Software- und Hardwareintegration gelegt. Das Ergebnis ist ein eng integriertes System, das Teile mit weniger Stützen, besserer Oberflächengüte und angeblich höherer Erfolgsquote drucken kann. Dies wiederum führt zu mehr Zuverlässigkeit, schnellerer Produktion und weniger Nachbearbeitung.
Laser PBF bleibt die treibende Kraft der Metall-3D-Druckindustrie. Metall-PBF-3D-Drucker haben die größte installierte Basis unter anderen Metall-3D-Drucktechnologien. Und die Hersteller von PBF 3D-Druckern haben im Vergleich zu Unternehmen, die andere Arten von Metall-3D-Druckern herstellen, die größten Anteile am 3D-Metalldruckmarkt.
Aus diesem Grund werden zunächst eine Reihe von Materialien für Metall-PBF-Technologien entwickelt. Dies bedeutet, dass sich die Entwicklung dieser Technologie fortsetzen wird, angetrieben durch die Nachfrage nach leistungsstarken, komplexen 3D-gedruckten Metallteilen.
Elektronenstrahlschmelzen
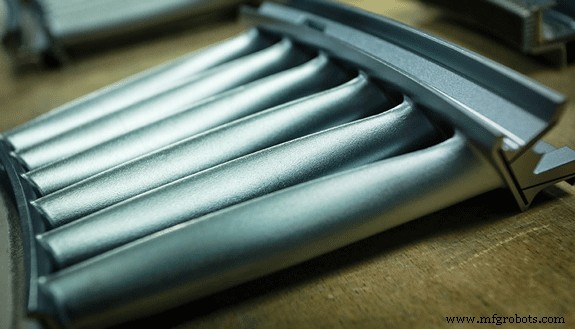
Technologiereifegrad:8
Electron Beam Melting gehört wie das Laser-PBF zur Familie der Pulverbett-Fusion von 3D-Drucktechnologien. EBM funktioniert ähnlich wie Laser-PBF, indem auch die Metallpulver geschmolzen werden, um ein vollständig dichtes Metallteil zu erzeugen.
Der entscheidende Unterschied zwischen den beiden Technologien ist die Energiequelle:EBM-Systeme verwenden anstelle eines Lasers einen Hochleistungselektronenstrahl als Wärmequelle, um Metallpulverschichten aufzuschmelzen.
Seit der Patentierung der Technologie im Jahr 2000 ist das schwedische Unternehmen Arcam der wichtigste Hersteller von EBM-3D-Druckern geblieben.
Nach der Übernahme des Unternehmens durch GE im Jahr 2016 hat sich die EBM-Technologie weiterentwickelt. Im Jahr 2018 brachte Arcam seine nächste Generation von EBM-Maschinen auf den Markt, die Spectra H.
Das "H" steht für "Hot Metal", was bedeutet, dass es hohe Hitze und rissanfällige Materialien wie Titanaluminid verarbeiten kann (TiAl) bei Temperaturen bis 1000°C.
Arcam EBM Spectra H verfügt über eine Reihe neuer Funktionen zur Steigerung der Produktivität und Reduzierung der Gesamtkosten.
Beispielsweise ist die EBM Spectra H mit einer 6kW HV-Leistung ausgestattet Einheit, die dazu beiträgt, die Vor- und Nachheizschritte im Vergleich zu anderen derzeit auf dem Markt befindlichen EBM-Maschinen um 50% zu reduzieren.
Außerdem wurde der Schichtungsprozess verbessert, um hohe Temperaturen zu reduzieren. Dadurch können Hersteller bis zu fünf Stunden bei einer Konstruktion in voller Höhe sparen und die Druckgeschwindigkeit im Vergleich zu anderen EBM-Maschinen um bis zu 50 % steigern.
Das GE Aviation-Geschäft, Avio Aero, verwendet Berichten zufolge 35 Arcam Maschinen:31 Arcam A2X-Maschinen und 4 Arcam EBM Spectra H-Maschinen. Bei Avio Aero werden die 3D-Drucker verwendet, um TiAl-Schaufeln für Niederdruckturbinen des neuen großen GE9X-Triebwerks herzustellen.
Neben der Luft- und Raumfahrt nutzt die Medizinindustrie die Technologie intensiv zur Herstellung medizinischer Implantate . Der früheste Einsatz von EBM für diese Anwendung geht auf das Jahr 2007 zurück.
Gestützt durch die Ressourcen und das Know-how von GE in der Metall-AM ist die EBM-Technologie auf dem Weg zur Industrialisierung. Die Technologie wird in Produktionsumgebungen in stark regulierten Branchen wie Luft- und Raumfahrt und Medizin eingesetzt. In Anbetracht dieser Anwendungen hat EBM die TRL 8 erreicht.
Direkte Energieablagerung
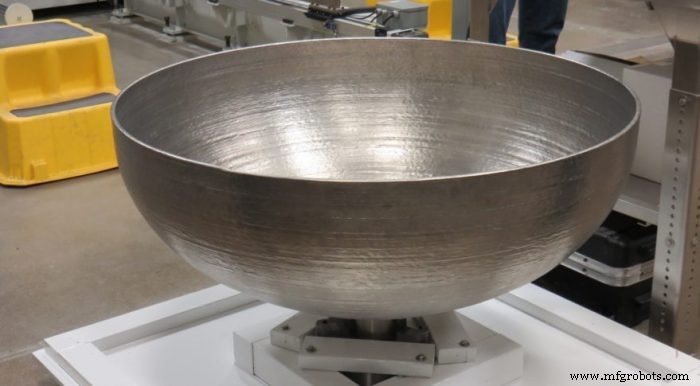
Technologiereifegrad:8
Die Direct Energy Deposition (DED) stammt aus Schweißprozessen und beinhaltet das Schmelzen von Metall mit einem Laser oder einem Elektronenstrahl, während das Material durch eine Düse auf eine Bauplattform geschoben wird.
DED-Systeme verwenden entweder Draht oder Pulver als Ausgangsmaterial. Die meisten Systeme verwenden handelsübliche Standardmaterialien, die für das Schweißen oder die Pulvermetallurgie entwickelt wurden. Die Verwendung von Standardmaterialien hat viele Vorteile, darunter eine breitere Materialauswahl, eine höhere Qualität und ein niedrigerer Preis.
Eine der ersten und erfolgreichsten Anwendungen von DED war die Reparatur beschädigter Komponenten. Die Technologie wird verwendet, um beschädigte Teile wie Turbinenschaufeln und Spritzgusseinsätze mit Material zu versehen. Durch die Reparatur verschlissener Teile trägt DED dazu bei, Ausfallzeiten und die Kosten für den Austausch eines Teils zu reduzieren und gleichzeitig die Lebensdauer des Teils zu verlängern.
Um den Einsatz von DED über Reparatur hinaus zu ermöglichen, entwickeln und optimieren Hersteller von DED-Systemen Lösungen für die Herstellung von funktionalen Metallteilen.
Beispielsweise hat Sciaky, einer der Pioniere der DED-Technologie, eine Regelung mit geschlossenem Regelkreis in seine additiven Elektronenstrahl-Fertigungssysteme eingeführt. Das Prozessüberwachungssystem von Sciaky kombiniert optische Echtzeit-Bildgebung mit maschinellem Sehen, um die Größe, Form und Temperatur des Schmelzbades zu messen.
Auf der Grundlage der aus dem Bild gewonnenen Daten wird dann ein geschlossenes Regelsystem gibt der Software Einstellbefehle zur Steuerung der Strahlleistung, der Drahtvorschubgeschwindigkeit und der Bewegung der Maschine. Dadurch kann die Prozesswiederholbarkeit wesentlich verbessert werden.
DED-Technologie wurde bereits in mehreren Luft- und Raumfahrt- und Verteidigungsanwendungen eingesetzt. Beispiele sind Titan-Kraftstofftankkuppeln für Satelliten, Titanstrukturteile für die Boeing 787 Dreamliner und Ersatzteile für Militärfahrzeuge.
Die Technologie hat sich als leicht verfügbare Wartungslösung etabliert. Bei dieser Anwendung steht DED bei TRL 9.
Wenn es um Produktionsanwendungen geht, kann DED auch als Fertigungswerkzeug verwendet werden. Es sind jedoch weitere Entwicklungen erforderlich, um die Inprozesssteuerung voranzutreiben und die Druckauflösung zu verbessern.
Die Technologie produziert ab sofort endkonturnahe Formen, die eine erhebliche Bearbeitung erfordern, um die Teilespezifikation und eine gute Oberflächengüte zu erreichen. Durch die Verbesserung der Druckauflösung können Hersteller den Zeit- und Kostenaufwand für die Sekundärbearbeitung reduzieren.
Metallbinder Jetting
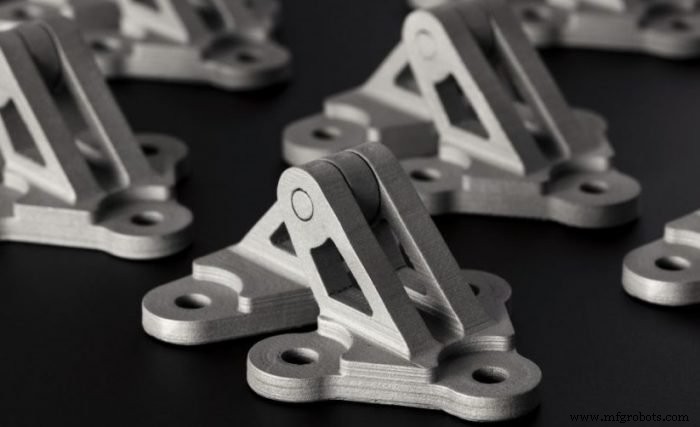
Technologiebereitschaftsgrad:Variiert
Metal Binder Jetting entwickelt sich schnell zu einer vielversprechenden Fertigungstechnologie. Der Technologiereifegrad variiert jedoch stark zwischen den heute auf dem Markt befindlichen Metallbinder-Jetting-Technologien.
Metal Binder Jetting wurde erstmals 1993 am MIT entwickelt. Der Druckprozess beginnt mit dem Auftragen einer dünnen Pulverschicht, wobei die Druckköpfe gezielt Bindemitteltröpfchen in das Pulverbett einbringen. Der Prozess wiederholt sich Schicht für Schicht, bis das Teil fertig ist, wobei ungenutztes Pulver (ca. 95 %) recycelt wird.
ExOne, das die Technologie seit 1996 vom MIT lizenziert, blieb das einzige Unternehmen, das Metall anbot Binder Jetting Services und Systeme bis Anfang der 2010er Jahre. Die Metallbinder-Jetting-Systeme von ExOne wurden hauptsächlich zur Herstellung von Metallprototypen und Werkzeugen verwendet.
Als jedoch die Patente für das Metallbindemittel-Strahlen ablaufen, verschärfte sich der Wettbewerb und ermutigte das Unternehmen, mit der Entwicklung von Lösungen auf Produktionsebene zu beginnen. Der neueste 3D-Drucker X1 25PRO wurde vor einigen Monaten auf den Markt gebracht.
Ein weiterer großer Player im Metal Binder Jetting-Markt ist Digital Metal. Seine erstmals 2017 eingeführten 3D-Drucker DM P2500 haben Berichten zufolge über 300.000 Komponenten in verschiedenen Branchen hergestellt, darunter Luft- und Raumfahrt, Luxusgüter, zahnärztliche Werkzeuge und Industrieausrüstung.
Es gibt auch ein paar Neulinge in der Metal Binder Jetting Arena, darunter HP und Desktop Metal.
Nach der Vorstellung der Multi Jet Fusion-Technologie für Polymerteile im Jahr 2016 stellte HP 2018 die nächste Erweiterung seines Additivangebots vor:ein Metal Jet 3D-Drucksystem. Mit einem neuen System möchte HP die Technologie in eine hochvolumige Produktionsumgebung einführen.
Um dies zu erreichen, hat das Unternehmen sein System mit mehr Düsen ausgestattet und innovative Bindemittel eingeführt. Zusammengenommen sollen diese Fortschritte den Druckprozess schneller und einfacher machen.
Die Technologie hinter dem 3D-Drucker von Desktop Metal nennt das Unternehmen Single Pass Jetting (SPJ), eine schnellere Version des typischen Binder-Jetting-Verfahrens. Das Unternehmen behauptet, dass sein System mit bis zu 12.000 cm3/h drucken kann, was über 60 kg Metallteilen pro Stunde entspricht.
Interessanterweise teilen HPs Metal Jet und das Produktionssystem von Desktop Metal einen ähnlichen Wert Vorschlag. Beide Maschinen auf Binder-Jetting-Basis versuchen, die traditionelle Fertigung zu revolutionieren, indem sie eine höhere Geschwindigkeit und Skalierbarkeit ermöglichen.
Während das Produktionssystem von Desktop Metal Anfang dieses Jahres veröffentlicht wurde, ist die HP-Technologie für 2020 geplant und derzeit nur über den HP Metal Jet Production Service erhältlich.
Zugegeben, viele der Metal Binder Jetting-Technologien sind erst vor kurzem erschienen. Das bedeutet, dass sie einige Zeit brauchen werden, um ihre Serientauglichkeit durch weitere Tests intern oder beim Kunden nachzuweisen.
Mit einer Erfolgsgeschichte in Produktionsanwendungen liegen die älteren Technologien, wie die von Digital Metal und ExOne, zwischen den Technologiereifegraden 7 und 8. Wir erwarten, dass neuere Metallbindemittel-Jetting-Technologien die TRL erreichen und übertreffen werden 8 in den nächsten Jahren.
Metallbindemittel-Strahlsysteme werden sich weiterentwickeln, um die Märkte zu adressieren, die für andere Metall-3D-Drucktechnologien eine Herausforderung darstellen, einschließlich der Produktion von Automobil- und Industriegütern mit höheren Stückzahlen. Daraus ergeben sich viele spannende Wachstumschancen für diese Technologie in der Zukunft.
Bound Metal Deposition
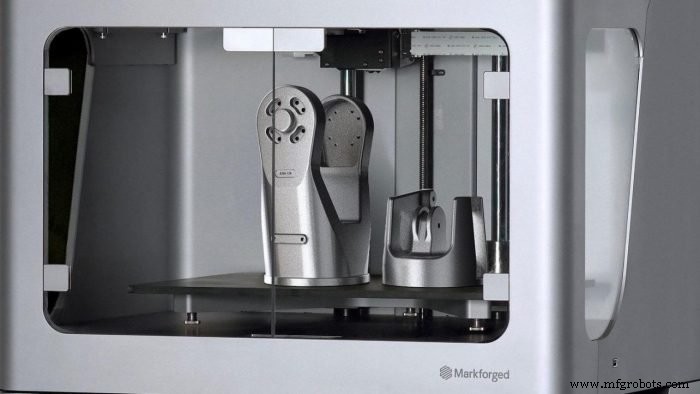
Technologiereifegrad:7
Bound Metal Deposition ist ein aufregender Neuling im Bereich der additiven Metallfertigung. Die Technologie funktioniert ähnlich wie die Fused Filament Fabrication (FFF), bei der ein Filament erhitzt und durch eine Düse extrudiert wird, wodurch ein Teil Schicht für Schicht entsteht. Im Gegensatz zu den bei FDM verwendeten Kunststofffilamenten verwendet die Metallextrusion jedoch Filamente aus Metallpulvern oder -pellets, die in Kunststoffbindemittel eingeschlossen sind.
Die beiden bekanntesten Unternehmen in diesem Bereich sind Markforged und Desktop Metal. Beide Unternehmen stellten 2017 erstmals ihre Metall-3D-Drucksysteme (Markforgeds Metal X und Desktop Metals Studio System) vor.
Derzeit wird die Technologie hauptsächlich verwendet, um Metallprototypen und -werkzeuge schneller und kostengünstiger herzustellen.
Ein Beispiel ist die Dixon Valve &Coupling Company, ein Hersteller und Lieferant von Zubehör für die Flüssigkeitstransferindustrie. Das Unternehmen hat Metal X von Markforged zum 3D-Drucken von Greiferbacken verwendet. Bei diesen Werkzeugen handelt es sich im Wesentlichen um Klemmen, die an einem Roboterarm montiert sind, der den Stahlkupplungen Dichtringe hinzufügt.
Die Herstellung solcher Werkzeuge dauert 14 Tage und kostet 355 US-Dollar. Zum Vergleich:Der 3D-Druck eines Metallgreifers kostet 7 US-Dollar und die Fertigstellung dauert 1,25 Tage – eine Reduzierung der Kosten und der Vorlaufzeit um mehr als 90 %. effektives Prototyping und die Beschleunigung der Markteinführungszeit, sein Einsatz auf der Produktionsseite bleibt begrenzt. Zum einen sind solche Systeme als kompakte Metall-3D-Drucker positioniert, die schwer zu skalieren sind.
Jedoch werden immer mehr Unternehmen die Technologie übernehmen, insbesondere für abgelegene Standorte wie Ölplattformen, und wir sehen möglicherweise mehr Beispiele von Ersatz- und Gebrauchsteilen, die in den kommenden Jahren durch gebundene Metallabscheidung hergestellt werden.
Innovation mit Metall-3D-Druck
Die meisten Metall-3D-Drucktechnologien haben einen recht hohen Technologiereifegrad erreicht, was bedeutet, dass sie für Produktionsanwendungen geeignet sind.
Natürlich bleibt noch viel zu tun, insbesondere bei der Verbesserung der Wirtschaftlichkeit und Geschwindigkeit von 3D-Metalldrucktechnologien. Derzeit sind Pulverbettverfahren, DED und Metal Binder Jetting deutlich teurer als herkömmliche Fertigungssysteme.
Kostengünstigere Pulverbeschichtungssysteme bieten einen gewissen Zugang zum Metall-3D-Druck und könnten einen guten Einstiegspunkt für kleinere Unternehmen bieten.
Letztendlich ist die Weiterentwicklung der Technologie nur ein Teil des Puzzles. Ebenso entscheidend ist die Weiterentwicklung des Ökosystems rund um den Metall-3D-Druck. Dies kann die Entwicklung einer besser integrierten und benutzerfreundlicheren Softwarelösung, die Automatisierung von Nachbearbeitungsvorgängen und die Schaffung optimierter Arbeitsabläufe beinhalten.
Nur wenn alle Teile zusammengefügt werden, können beim 3D-Metalldruck signifikante Prozess- und Produktinnovationen erzielt werden.
3d Drucken
- Wie Objektmodelle für den 3D-Druck entworfen werden
- Wie Brücken im 3D-Druck verwendet werden
- Wie kann der 3D-Druck beim Metallguss von Vorteil sein? Hier sind 3 Möglichkeiten
- Metall-3D-Druck:Wo stehen wir heute?
- Wie ausgereift ist Ihre Branche bei der Einführung des 3D-Drucks? [Infografik]
- 10 spannende 3D-Drucktechnologien, die in den letzten 12 Monaten entstanden sind
- Wie Desktop-3D-Drucker den 3D-Druck verändern
- AM auf der ganzen Welt:Wie ausgereift ist der 3D-Druck im asiatisch-pazifischen Raum?
- Wie sich der Markt für 3D-Druckhardware im Jahr 2020 entwickelt
- Wie nachhaltig ist der industrielle 3D-Druck?