10 spannende 3D-Drucktechnologien, die in den letzten 12 Monaten entstanden sind
Die 3D-Druckindustrie entwickelt sich mit erstaunlicher Geschwindigkeit. In den letzten 12 Monaten haben eine Reihe von Unternehmen neue Technologien angekündigt und neue Maschinen auf den Markt gebracht, was auf eine aufregende Zukunft für die Branche hindeutet.
Damit Sie immer auf dem neuesten Stand im Bereich 3D-Druck bleiben, finden Sie hier unsere Liste der 10 aufregendsten Technologien, die kürzlich angekündigt wurden.
Metall-3D-Druck
1. Multilevel Concurrent Printing von Aurora Labs
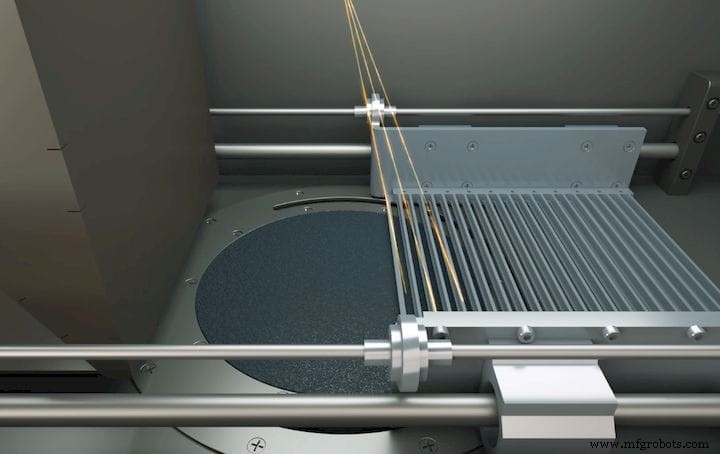
Während die Aussicht auf den 3D-Druck von Metallteilen mit einer Geschwindigkeit von 1 Tonne Metall pro Tag zu schön klingt, um wahr zu sein, scheint der australische Hersteller von 3D-Metalldruckern Aurora Labs genau das zu erreichen.
Seit 2014 entwickelt Aurora Labs eine neue Metall-3D-Drucktechnologie, um den Metall-3D-Druck mit viel höheren Geschwindigkeiten zu ermöglichen. Das auf der formnext 2018 erstmals vorgestellte Multilevel Concurrent Printing (MCP™) basiert auf einer bekannten Pulverbett-Fusionstechnologie – aber mit einer Wendung.
Im Gegensatz zu herkömmlichen Pulverbetttechnologien, die eine Schicht nach der anderen drucken, druckt MCP mehrere Schichten gleichzeitig in einem einzigen Durchgang. Auf der formnext 2018 gab das Unternehmen bekannt, rund 30 Schichten gleichzeitig drucken zu können, mit dem Ziel, dies in den nächsten 12 Monaten auf 100 Schichten zu erhöhen.
Wie funktioniert es?
Die MCP-Technologie hat zwei Schlüsselelemente:einen gitterartigen Recoater-Mechanismus und mehrere Laserstrahlen. Wenn der Druck beginnt, gleitet der Recoater-Mechanismus mit mehreren Trichtern über das Druckbett, wobei jeder Trichter in einem einzigen Durchgang verschiedene Pulverschichten aufträgt.
Wenn eine Schicht aufgetragen wird, wird sie durch ein Laser, der das Pulver durch die speziellen Lücken im Beschichter erreicht. Während desselben Durchlaufs werden nacheinander folgende Schichten abgeschieden und durch Laser sukzessive verschmolzen.
Im Wesentlichen bedeutet dies, dass mehrere Schichten in einem Durchgang gedruckt werden können, was die Druckzeit erheblich verkürzt.
Im Februar dieses Jahres gab das Unternehmen bekannt, dass es eine Druckgeschwindigkeit von 113 . erreicht hat Kilogramm pro Tag. Um den Meilenstein zu veranschaulichen, druckte Aurora Labs 3D eine Reihe von 10 mm hohen Titan-Sechskantteilen, was nur 20 Minuten dauerte.
Aurora Labs bereitet derzeit die kommerzielle Einführung seines Rapid-Manufacturing-Systems Ende des Jahres vor. Wird es bis dahin in der Lage sein, eine Tonne Metall pro Tag zu drucken? Nur die Zeit kann es verraten.
2. Die MELD-Technologie von MELD Manufacturing
Die MELD Manufacturing Corporation hat eine neue Methode entwickelt, um Metalle in 3D zu drucken, ohne sie zu schmelzen.
Die Technologie, die seit über einem Jahrzehnt in der Entwicklung ist, wurde letztes Jahr mit der Einführung von MELDs großformatigen B8-Maschine.
Wie funktioniert es?
Der größte Unterschied zwischen MELD und anderen Metall-AM-Techniken besteht darin, dass es sich um einen Festkörperprozess handelt. Bei MELD werden Metallpulver oder -drähte durch ein hohles rotierendes Werkzeug geleitet, wo Druck und Reibung das Metall verformen und in das darunterliegende Material einrühren.
Dieses Verfahren bietet viele einzigartige Vorteile. Erstens erzeugt die MELD-Technologie Teile, die vollständig verdichtet sind, d. h. sie benötigen keine nachträgliche Wärmebehandlung.
Zweitens kann das Verfahren nicht nur zur Herstellung von Teilen verwendet werden, sondern auch zur Reparatur und Beschichtung vorhandener Komponenten oder zur Herstellung kundenspezifischer Metalllegierungen. Nanci Hardwick, CEO von MELD Manufacturing, betont:
„Wir sind die einzige Technologie, die in der Lage ist, sehr große Teile zu skalieren und zu bauen oder zu reparieren. Eine weitere einzigartige Möglichkeit besteht darin, dass Sie ein vorhandenes Teil nehmen, in die Maschine legen und zusätzliches Material hinzufügen können, unabhängig davon, ob Sie eine verschleißfeste Beschichtung auf einem sehr leichten Material wünschen oder das Material zur Reparatur einer abgenutzten Oberfläche hinzufügen möchten. ”
Der 3D-Drucker von MELD benötigt kein Gehäuse und der Prozess findet in einer offenen Umgebung statt. Dies bedeutet, dass es viel Freiheit für die Erstellung größerer Teile gibt.
Die Technologie hat jedoch einige Einschränkungen. Eine ist die Herausforderung beim Drucken von Überhängen. Die Technologie erfordert auch erhebliche Investitionen, wobei die B8-Maschine 800.000 US-Dollar kostet. Aber bevor sie sich für die Investition entscheiden, können Kunden die Technologie über den Druckservice, den MELD Manufacturing anbietet, testen.
3. VELO 3D 's Intelligent Fusion
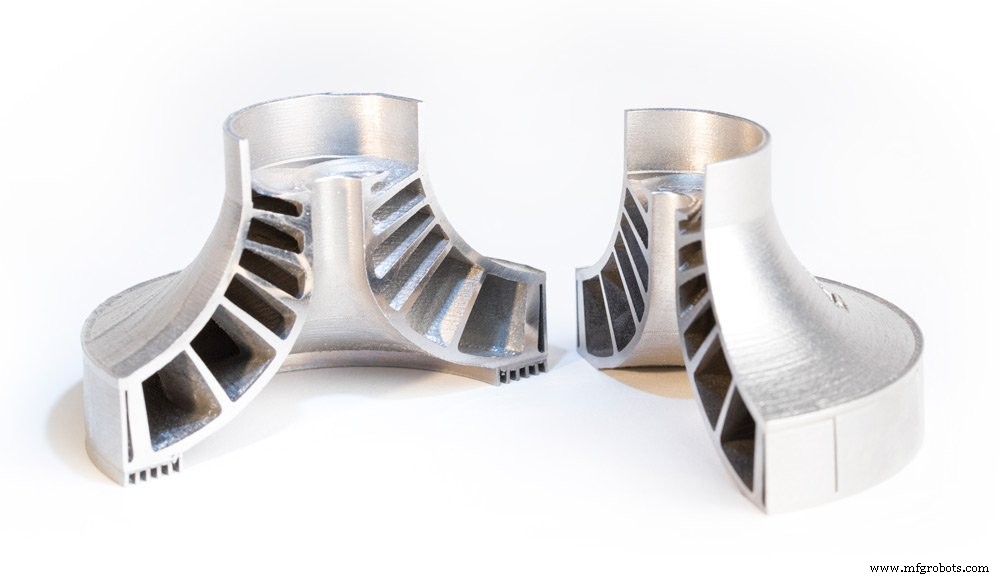
Der Mangel an Wiederholbarkeit und die Notwendigkeit, Stützstrukturen zu drucken, sind zwei der größten Herausforderungen beim Metall-3D-Druck. VELO
3D
aus Kalifornien hat sich zum Ziel gesetzt, diese Herausforderungen mit seiner Intelligent Fusion-Technologie zu lösen.
Während VELO
3D
wurde 2014 gegründet, das Unternehmen tauchte im vergangenen Herbst erstmals auf dem Radar auf, als es seinen laserbasierten 3D-Drucker Sapphire vorstellte. Intelligent Fusion™ bildet das Rückgrat sowohl des 3D-Druckers als auch des VELO
3D
's Druckvorbereitungssoftware Flow™. Einfach ausgedrückt ermöglicht Intelligent Fusion™ die enge Integration zwischen Hardware, Software und dem Prozess.
Wie funktioniert es?
Das System und die Software wurden gemeinsam entwickelt, um einen eng integrierten Prozess zu erreichen, der einige interessante Funktionen bereithält.
Der Sapphire 3D-Drucker basiert auf einem Pulverbett-Fusionsprozess, bei dem ein Laserstrahl Metallpulver aufschmilzt und Schicht für Schicht zu einem Teil verschmilzt. Das System ist umfangreich mit Sensoren ausgestattet, die eine geschlossene Schmelzbadregelung ermöglichen und dadurch die Teilekonstanz verbessern.
Softwareseitig bietet VELO
3D
hat seine Flow-Software entwickelt, um CAD-Dateien anstelle von STL-Dateien zu verwenden. Diese Entscheidung hat zwei Implikationen. Da das STL-Format die Oberfläche eines CAD-Modells mit Dreiecken annähert, führt die Verwendung von CAD von Anfang an zu einer höheren Genauigkeit.
Zweitens können STL-Dateien sehr groß sein, was die Verarbeitung von Dateien umständlich macht. Die Umstellung auf CAD als initiales Dateiformat macht somit den Workflow der Druckvorbereitung einfacher und schneller.
Außerdem wurde die Flow Software sehr prozessbewusst entwickelt. Das bedeutet zum Beispiel, dass es vor dem Druckstart eine Simulation durchführen kann sowie Fehler vorhersagen und verhindern kann, bevor sie auftreten.
Kombinieren Sie dies mit den Closed-Loop-Steuerungsfunktionen von Sapphire, und Sie erhalten einen sehr intelligenten Prozess, der extreme Zuverlässigkeit bieten sollte.
Intelligent Fusion soll in der Lage sein, Erstdruck-Erfolgsraten von bis zu 90 % zu erreichen und gleichzeitig die Anzahl der Stützstrukturen um das Drei- bis Fünffache zu reduzieren.
Während VELO3D weitergeht um seine Technologie zu verbessern und neue Kunden zu gewinnen, freuen wir uns auf weitere Fallstudien, die die einzigartigen Fähigkeiten von VELO
3D
hervorheben 's Intelligent Fusion.
4. HPs Metal Jet
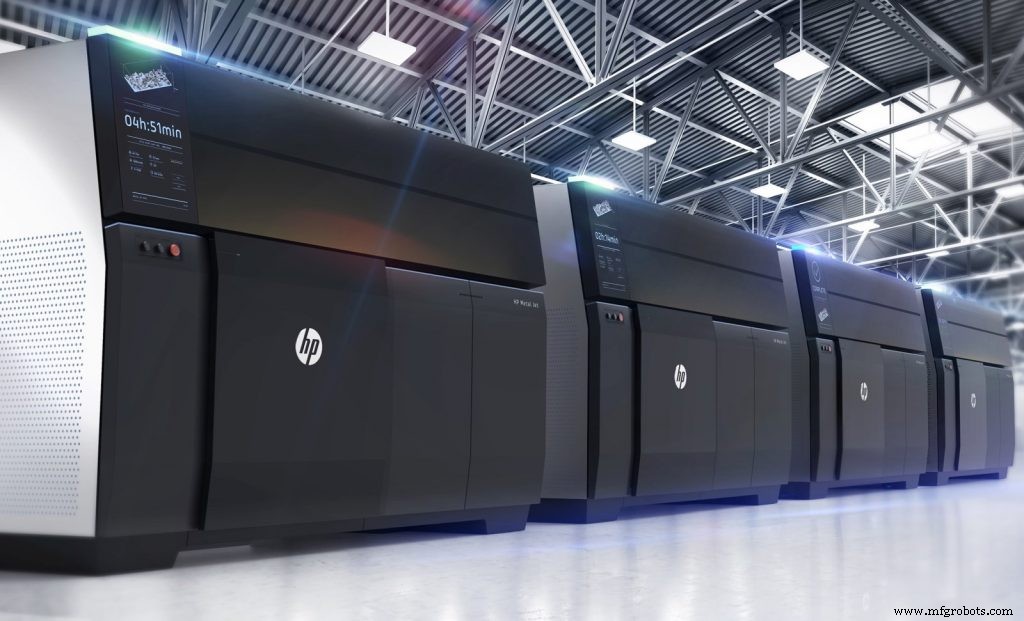
In der Welt des 2D-Drucks stehen die Drucker von HP für hohe Präzision und Geschwindigkeit. Im Jahr 2016 stellte das Unternehmen mit der Einführung seines Polymer-3D-Druckers Multi Jet Fusion öffentlich seinen Einstieg in den 3D-Druck vor.
Nachdem sich HP auf der Polymerseite des 3D-Drucks etabliert hat, ist HP nun in die Metallarena vorgedrungen und hat letztes Jahr seinen Metal Jet 3D-Drucker angekündigt. Das System wurde entwickelt, um mit anderen Produktionsverfahren wettbewerbsfähig zu sein.
Die Technologie, die dies ermöglicht, ist Binder Jetting.
Wie funktioniert es?
Beim Binder Jetting wird eine dünne Metallpulverschicht auf das Druckbett aufgebracht. Eine Reihe von Druckköpfen bewegt sich über dem Druckbett und spritzt winzige Tropfen eines Bindemittels – im Wesentlichen Klebstoff – dort, wo festes Metall benötigt wird. Wenn eine Schicht fertig ist, wird eine neue Pulverschicht aufgetragen, gefolgt von einem weiteren Durchgang des Bindemittels.
Nach dem Drucken verbleibt das fertige Teil in einem „grünen“ Zustand und muss einem Erwärmungsvorgang (genannt Sintern) unterzogen werden, um das Bindemittel auszubrennen und ein dichtes Teil zu erzeugen.
Dieses Verfahren hat mehrere Vorteile. Erstens ist es schnell. Mit doppelt so vielen Druckköpfen im Vergleich zu bestehenden Systemen behauptet HP, dass seine Metal Jet-Drucker bis zu 50-mal produktiver sind als vergleichbare Binde- und Lasersintermaschinen auf dem heutigen Markt.
Zweitens verbraucht der Prozess weniger Bindemittel, was den Sinterprozess schneller und kostengünstiger macht.
„Beim Metallspritzguss müssen typischerweise mehr als 10 Gew.-% Bindemittel ausgebrannt werden. In unserem Fall haben wir weniger als 1%, was eine Größenordnung weniger ist, was das Sintern schneller, kostengünstiger und viel einfacher macht“, sagt Tim Weber, Global Head of Metals bei HP, in einem Interview mit AMFG .
Interessanterweise ähnelt Metal Jet ein wenig der Technologie und dem Wertversprechen hinter dem Produktionssystem von Desktop Metal. Beide Maschinen auf Binder-Jetting-Basis versuchen, die traditionelle Fertigung zu revolutionieren, indem sie eine höhere Geschwindigkeit und Skalierbarkeit ermöglichen. Desktop Metal behauptet beispielsweise, dass sein System mehr als viermal schneller ist als andere Binder-Jetting-Maschinen.
Während das Produktionssystem von Desktop Metal Anfang dieses Jahres veröffentlicht wurde, ist die Technologie von HP für eine Veröffentlichung im Jahr 2020 geplant und derzeit nur über den HP Metal Jet Production Service erhältlich.
Sobald Metal Jet veröffentlicht wird, wird es spannend sein zu sehen, wie sich die beiden Systeme auf dem Weg zur AM-Serienproduktion vergleichen werden.
Polymer-3D-Druck
5. LaserProFusion von EOS
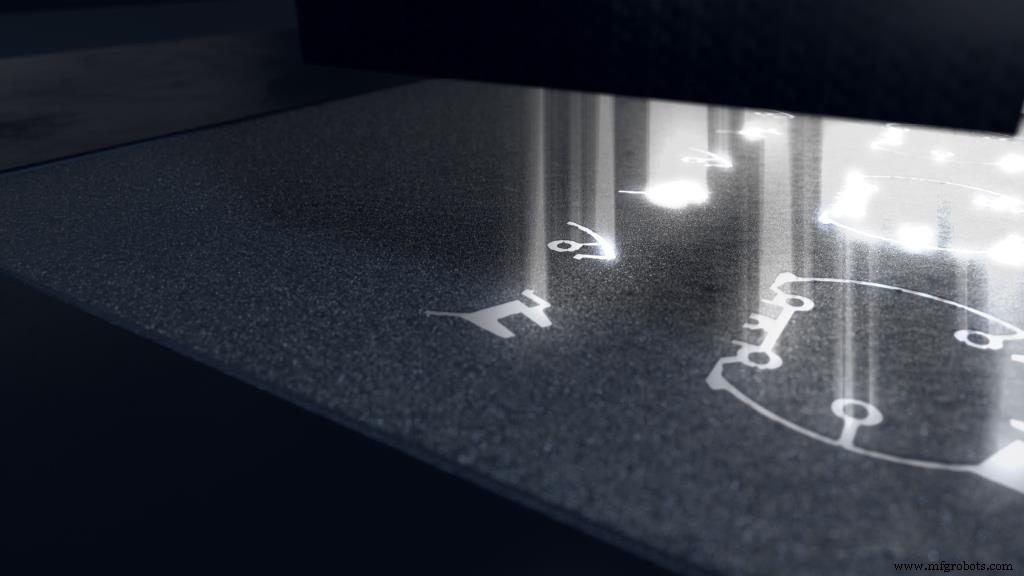
LaserProFusion ist vielleicht eine der am meisten erwarteten Polymer-3D-Drucktechnologien. LaserProFusion wurde auf der Formnext 2018 vorgestellt und ist ein kommendes Polymer-3D-Drucksystem von EOS, das verspricht, die Polymer-3D-Produktion dank der Einbeziehung von einer Million Diodenlasern zehnmal schneller zu machen.
EOS hat eine langjährige Geschichte in Polymer-3D-Druck, insbesondere mit Selective Laser Sintering (SLS). Bei SLS wird eine Pulverschicht, typischerweise Nylon, auf ein Druckbett aufgetragen und ein Laser konturiert dann den Querschnitt eines Teils, wobei Pulverpartikel miteinander verschmolzen werden.
Während aktuelle SLS-Maschinen mit einem oder wenigen CO₂-Lasern arbeiten, kann die LaserProFusion-Technologie bis zu Millionen Diodenlaser verwenden. Auf diese Weise kann das System Teile nicht nur mit hoher Auflösung, sondern auch mit einer viel höheren Druckgeschwindigkeit herstellen, die möglicherweise mit dem Spritzgießen konkurrieren kann.
Die angeblich seit 8 Jahren in der Entwicklung befindliche Technologie wird jedoch frühestens 2021 auf den Markt kommen. Es wird spannend zu sehen, welche Auswirkungen LaserProFusion haben wird, wenn sie ihren Weg findet in den Markt.
6. Farsoons Flugtechnologie
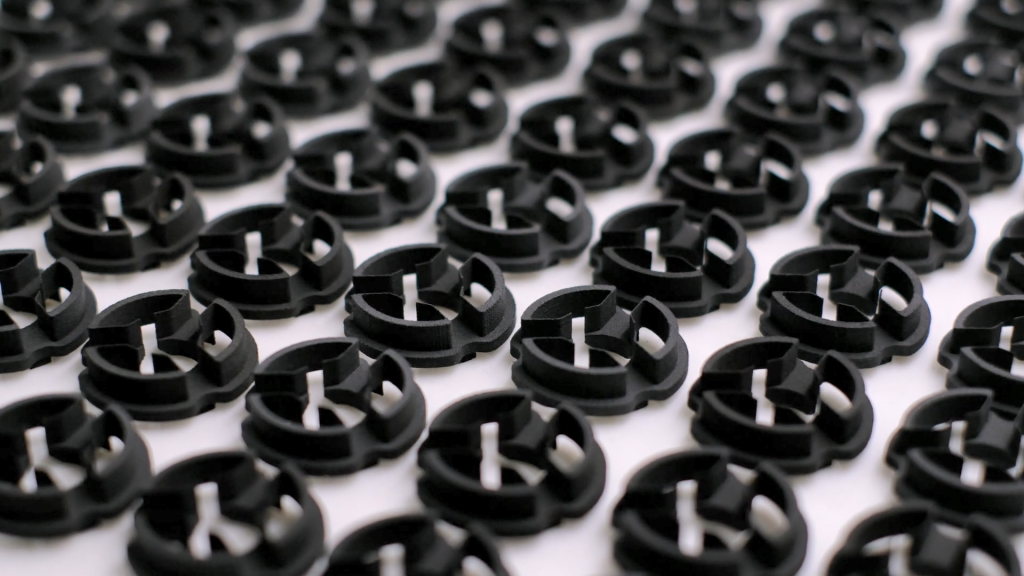
Ein weiteres Unternehmen, das die SLS-Technologie revolutionieren möchte, ist Farsoon. Um SLS noch schneller und genauer zu machen, nutzt Farsoon die Leistung eines Faserlasers in seiner neuen Flugtechnologie.
Wie funktioniert das?
Bei SLS wird eine Pulverschicht auf einer Bauplattform verteilt und dann zeichnet ein Laser die Konturen einer Schicht eines Teils nach und sintert das Pulver zusammen.
Um dieses Verfahren zu verbessern, hat der chinesische 3D-Druckerhersteller ein neues Scansystem entwickelt und vor allem den Standard-CO₂-Laser durch einen Faserlaser ersetzt.
Ein Faserlaser System ist in der Lage, dem Pulverbett mehr Leistung zuzuführen und die Energieverteilung auf das Material zu verbessern. Dies liegt daran, dass der Faserlaserstrahl eine kleinere Laserfleckgröße ermöglicht. Dies führt zu einer höheren Leistungsdichte, wodurch das Pulver in kürzerer Zeit gesintert werden kann.
In Kombination führen diese Vorteile zu einer Scangeschwindigkeit von über 20 m/s, was etwa dem Vierfachen vergleichbarer Technologien entspricht. Darüber hinaus macht die zusätzliche Leistung eines Lasers Feature-Details von nur 0,3 mm möglich.
Flight Technology wurde entwickelt, um die Einführung des 3D-Drucks für die Massenproduktion voranzutreiben und ist sicherlich ein Schritt in diese Richtung.
7. Die Hochgeschwindigkeits-Extrusion von Essentium
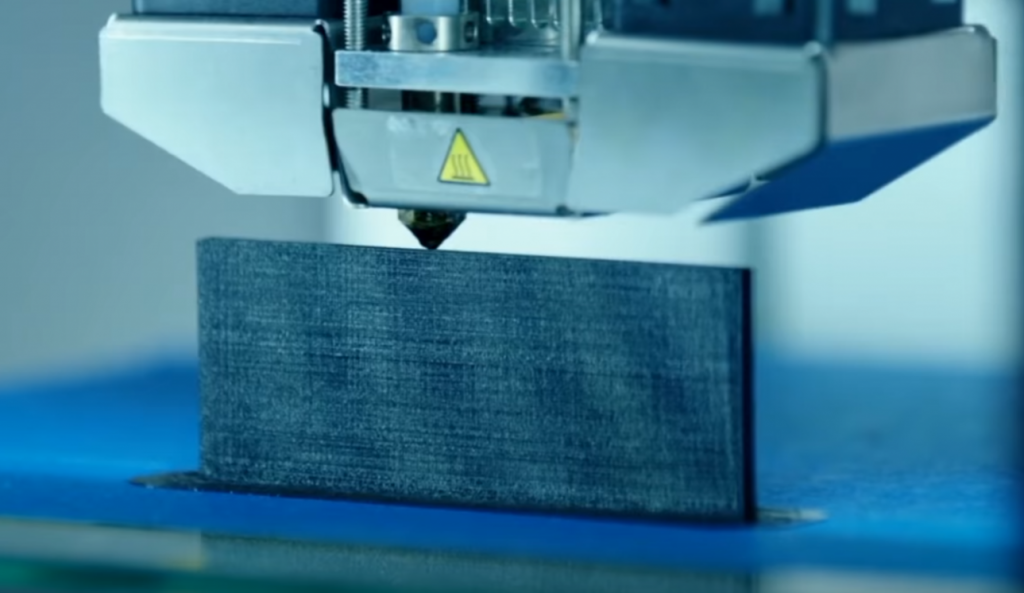
Der in den USA ansässige 3D-Druckerhersteller Essentium behauptet, den schnellsten 3D-Extrusionsdrucker entwickelt zu haben.
Wie funktioniert er?
Die auf der Formnext 2018 erstmals vorgestellte High Speed Extrusion (HSE)-Plattform von Essentium basiert auf der Fused Filament Fabrication (FFF)-Technologie. Beim FFF wird ein thermoplastisches Filament geschmolzen und durch eine Düse geschoben, um Teile Schicht für Schicht zu drucken. Eine lange Druckzeit, insbesondere bei größeren Objekten, war eine der Haupteinschränkungen von FFF.
Um diese Herausforderung zu meistern, enthält Essentiums HSE eine Reihe von Designmerkmalen, die es möglicherweise zu einem der am schnellsten verfügbar.
Der HSE verwendet beispielsweise alle Linearmotoren, was bedeutet, dass sich der Druckkopf mit einer viel höheren Geschwindigkeit (1 m/s) und mit größerer Genauigkeit bewegen kann. Angeblich ist das Bewegungssystem auf eine Position von bis zu 30 Mikrometer genau – bei solchen Geschwindigkeiten ziemlich unglaublich. Um der Geschwindigkeit des Bewegungssystems gerecht zu werden, hat Essentium auch leistungsstarke Servomotoren anstelle von Steppern eingebaut.
Ein weiteres Element, das dieses System einzigartig macht, ist die proprietäre Düse von Essentium, die HSE Hozzle™, die in 3 Sekunden von 20°C auf 500°C aufheizen kann.
Zusätzlich zur HSE-Technologie hat Essentium auch seine FlashFuse-Technologie entwickelt, um Teileschwäche in der Z-Achse (der Richtung, in der die Schichten aufgebracht werden) zu überwinden, ein häufiges Problem bei 3D-gedruckten Teilen .
Die Technologie beinhaltet die Abscheidung eines auf Energie ansprechenden Filaments und das Anlegen von elektrischem Strom. Dieser Strom heizt das Teil auf, formt die Schichten effektiv zusammen und erzeugt in alle Richtungen gleich starke Teile.
Für die Veröffentlichung im Laufe dieses Jahres geplant, wird Essentium seine FlashFuse- und HSE-Technologie in einer einzigen Plattform mit dem Namen HSE 180•S kombinieren.
Durch die Optimierung der Bewegungen, der Extrusion, der Temperatur und schließlich der Bauteilfestigkeit ist Essentium auf dem besten Weg, einen neuen Maßstab für den 3D-Extrusionsdruck zu setzen.
8. Den SCHRITT von Additive Solutions weiterentwickeln
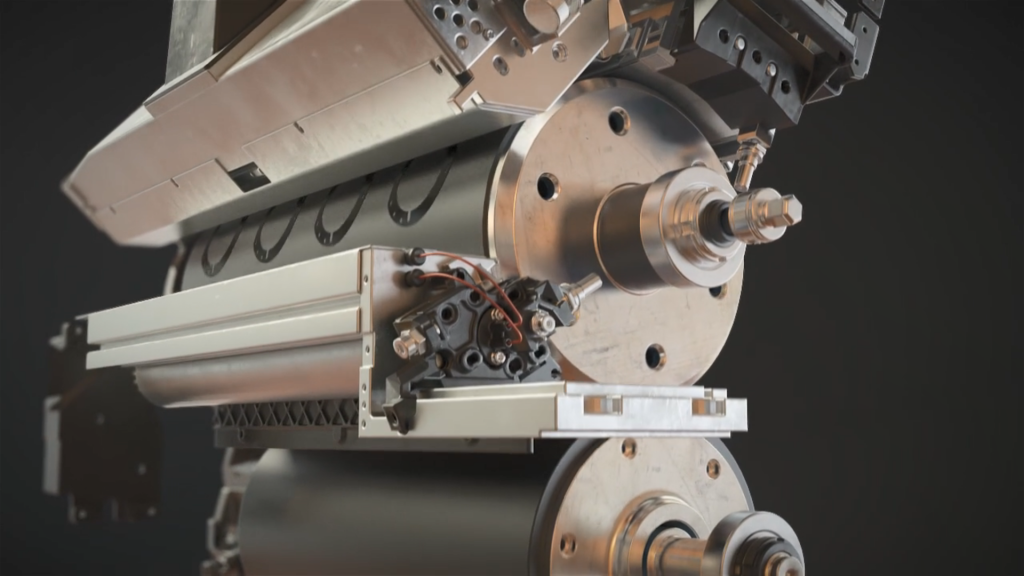
Die Verlagerung hin zur Produktion und die Fähigkeit, mit der traditionellen Fertigung zu konkurrieren, ist für viele Hersteller von 3D-Druckern ein gemeinsames Thema. Das Spin-off von Stratasys, Evolve Additive Solutions, ist keine Ausnahme.
Evolve ist im letzten Jahr mit seinem Selective Toner Electrophotographic Process (STEP) erstmals in der 3D-Druckszene aufgetreten – einer Technologie, für die das Unternehmen fast entwickelt hat zehn Jahre.
Wie funktioniert das?
STEP ist wie kein anderes bekanntes Polymer-3D-Druckverfahren, das heute auf dem Markt erhältlich ist, da es weder Laser verwendet noch Kunststofffilamente extrudiert. Stattdessen basiert es auf derselben elektrofotografischen Drucktechnologie, die in vielen Bürodruckern verwendet wird.
Der STEP-Prozess beginnt mit der elektrostatischen Aufladung einer Walze, die dann über das pulverförmige Material, das als Toner bezeichnet wird, fährt. Die eine Tonerschicht haftet an der Walze und wird dann auf ein Förderband übertragen.
Auf dem Förderband durchläuft der wachsende Teil eine Heizeinheit, in der eine neue Schicht mit der vorherigen verschmolzen wird, bevor die nächste Materialschicht abgelegt wird.
Diese Technologie kann potenziell sehr hohe Durchsatzraten ermöglichen, was sie für den 3D-Druck in der Massenproduktion kostengünstig macht.
Außerdem sind die mit dem STEP-Prozess 3D-gedruckten Teile isotrop, was bedeutet, dass sie in allen dreien Festigkeiten aufweisen Richtungen. Dies liegt zum Teil daran, dass die Evolve-Maschine nicht nur das Teil, sondern auch die nächste Schicht vorwärmt, was zu einer hervorragenden Verbindung zwischen den Schichten führt.
Die Technologie von Evolve wird voraussichtlich erst kommerziell verfügbar sein 2020. Aber wenn dies der Fall ist, könnte es einen völlig neuen Weg zum 3D-Druck von Polymerteilen bieten.
9. Fluxprint-Technologie von Fortify
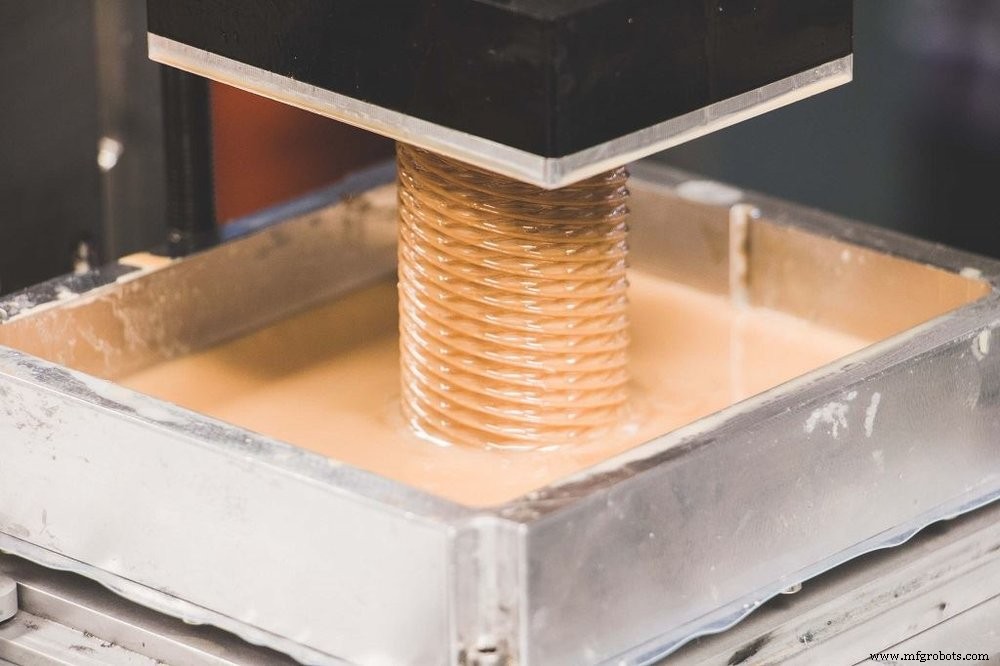
Das in Boston ansässige Startup Fortify ist kürzlich mit seiner einzigartigen Methode zum 3D-Druck von extrem starken fasergefüllten Teilen auf den Markt gekommen. Diese neue Methode wird durch die Fluxprint-Technologie von Fortify ermöglicht, die Magnetfelder verwendet, um die Ausrichtung der Fasern innerhalb eines Teils zu steuern.
Wie funktioniert es?
Der Fortify 3D-Drucker basiert auf der Digital Light Processing-Technik, bei der ein digitaler Lichtprojektor verwendet wird, um lichtempfindliche Polymere zu verfestigen. Beim Fluxprint-Verfahren werden die Polymere mit Schnittfasern vermischt, die mit einer Metallic-Beschichtung versehen werden.
Ein Magnetfeld wird dann an die Fasern angelegt, wodurch sie sich entsprechend der magnetischen Kräfte ausrichten.
Im nächsten Schritt wendet der Drucker Licht an, um eine Schicht eines Teils auszuhärten. Der Vorgang wird Schicht für Schicht wiederholt, um den Druck abzuschließen.
Durch die Kontrolle der Faserorientierung auf jeder Schicht kann Fluxprint sehr steife und starke Teile herstellen. Diese Technologie könnte insbesondere für die Herstellung von Spritzgussformen und Automobilwerkzeugen nützlich sein.
Fortify beabsichtigt, in den nächsten 8 bis 12 Monaten seinen ersten kommerziellen 3D-Drucker auf den Markt zu bringen. Wir freuen uns, dass diese Technologie Gestalt annimmt und wir werden in Zukunft sicherlich noch viel von Fortify hören.
10. Programmierbare Photopolymerisation von Origin
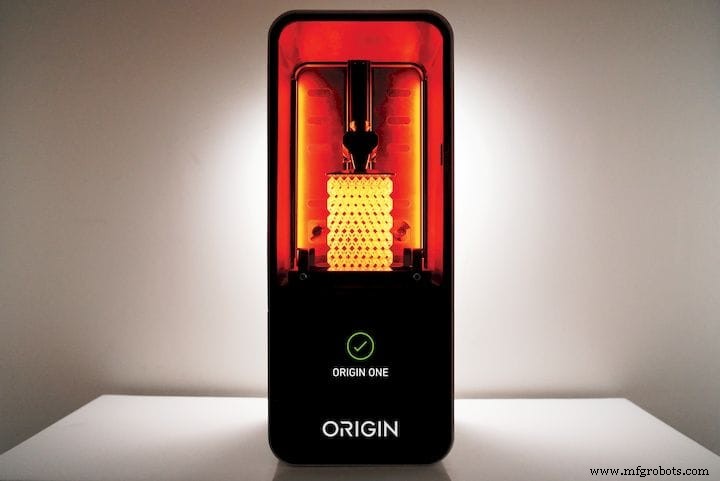
Das in den USA ansässige Startup Origin hat sich auf der formnext 2018 aus dem Stealth gestürzt, um die Massenproduktion mit 3D-Druck zu ermöglichen. Auf der RAPID-Messe im letzten Monat hat Origin einen Schritt in Richtung seines Versprechens gemacht und den Origin One 3D-Drucker vorgestellt.
Auf den ersten Blick könnte man meinen, dass Origin One einfach noch nicht ist ein weiterer 3D-Drucker aus Harz. Das Geheimnis des Origin One liegt jedoch im Inneren der Maschine. Das Unternehmen hat eine programmierbare Photopolymerisation (P3)-Technologie entwickelt, die einen hohen Durchsatz, eine reduzierte Nachbearbeitung und eine viel größere Auswahl an zu bedruckenden Materialien ermöglicht.
Wie funktioniert es?
Im Gegensatz zu aktuellen 3D-Harzdruckern ist P3 sauerstofffrei. Der 3D-Drucker von Origin verwendet ein Inertgas, wodurch sich das Druckbett mit extrem geringem Kraftaufwand wegziehen lässt, um die nächste Schicht aufzubauen. Durch die Reduzierung der Kraft kann die Maschine einen höheren Durchsatz erreichen.
Außerdem konnte Origin die erforderliche Nachbearbeitungszeit durch die Integration des Aushärtungsprozesses in seinen 3D-Drucker erheblich reduzieren. Bei anderen Resin-3D-Druckern erfolgt die Aushärtung normalerweise in einer spezialisierten Einheit, die manchmal bis zu mehreren Stunden dauert.
Mit P3 erreichen Teile beim Drucken 99 % ihrer endgültigen Eigenschaften. Anschließend werden sie nur gereinigt und schnell durch ein abschließendes UV-Härtungsfördersystem geleitet, das eine leistungsstarke Mikrowellen-Fusionslampe verwendet. Der Vorgang soll nicht länger als fünf Minuten dauern, was durchaus bemerkenswert ist.
Derzeit verfügt Origin über rund 50 validierte Materialien, die für seinen P3-Prozess optimiert sind. Dies wurde dank des offenen Materialansatzes von Origin erreicht, der sich auf Chemieexperten verlässt, um die Auswahl an Materialien zu erweitern, die den Benutzern zur Verfügung stehen.
Obwohl das Unternehmen gerade erst seinen Weg zur Transformation der Fertigung begonnen hat, hat Origins jüngste Welle von Partnerschaften mit großen Materialunternehmen und dem Schuhhersteller ECCO lassen auf eine vielversprechende Zukunft schließen.
Das Potenzial des 3D-Drucks freisetzen
Obwohl sie so unterschiedlich sind, haben alle Technologien auf unserer Liste ein gemeinsames Ziel:den 3D-Druck von seinen Ursprüngen im Prototyping bis zur vollständigen industriellen Produktion weiter voranzutreiben. Um dies zu erreichen, werden die Technologien schneller, genauer und zuverlässiger entwickelt.
Es wird offensichtlich einige Zeit dauern, bis diese Versprechen erfüllt werden. Die aufkommenden Technologien legen jedoch die Grundlage dafür, den 3D-Druck über seine derzeitigen Grenzen hinaus in die rosige Zukunft zu bringen.
3d Drucken
- Scalmalloy:Das neueste Hochleistungsmaterial für den 3D-Metalldruck
- 3D-Druck im Jahr 2018:7 Trends, die die Branche geprägt haben
- 10 spannende Einsatzmöglichkeiten des 3D-Drucks in der Konsumgüterindustrie
- Experteninterview:VP of Technology Partnerships von VELO3D zur Erweiterung der Fähigkeiten des 3D-Metalldrucks
- 10 spannende Beispiele für den 3D-Druck in der Automobilindustrie im Jahr 2021
- Wie ausgereift sind 3D-Metalldrucktechnologien?
- Wie sich der Markt für 3D-Druckhardware im Jahr 2020 entwickelt
- 9 Fortune-500-Unternehmen, die Vorreiter beim Einsatz des industriellen 3D-Drucks sind
- Die Entwicklung der 3D-Drucktechnologie von HP:Von Polymer zu Metall AM
- 4 Faktoren, die die Kosten der Metallherstellung beeinflussen