Experteninterview:John Barnes, Gründer von The Barnes Group Advisors, über die Zukunft der additiven Fertigung
Der Bedarf an speziellen Fähigkeiten und Fachkenntnissen in der additiven Fertigung ist für die Einführung der Technologie von entscheidender Bedeutung. Die Beherrschung der additiven Prinzipien ist jedoch keine leichte Aufgabe, da sie mit einer steilen Lernkurve und einem erheblichen Zeitaufwand verbunden ist. Ein Unternehmen, das dieses Problem beheben möchte, ist The Barnes Group Advisors, ein in den USA ansässiges Beratungsunternehmen für additive Fertigung.
The Barnes Group Advisors (TBGA) wurde 2017 in Pittsburgh gegründet und konzentriert sich darauf, Unternehmen bei der Strategiefindung und Lösung von Problemen im Zusammenhang mit der Industrialisierung der additiven Fertigung zu unterstützen. Dafür bietet das Unternehmen nicht nur Beratungsleistungen an, sondern bietet auch ein Schulungsprogramm an.
Im Experteninterview dieser Woche erfahren wir von John Barnes, dem Gründer und Geschäftsführer des Unternehmens, warum die Personalentwicklung der Schlüssel zum Wachstum der Branche ist und was erforderlich ist, um das Beste daraus zu machen der additiven Fertigung.
Können Sie mir etwas über The Barnes Group Advisors und die von Ihnen angebotenen Dienstleistungen erzählen?
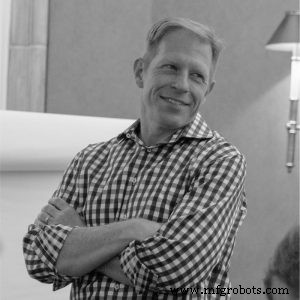
Wir haben das Unternehmen vor zwei Jahren gegründet, weil wir den Wandel und das Wachstum in der additiven Fertigung gesehen haben und die Technologie immer mehr industrialisiert wurde.
Bei TBGA haben wir alle einen technischen Hintergrund und waren daher in der Qualifizierung und Zertifizierung von Ansätzen verschiedener Branchen zur additiven Fertigung aktiv. In den meisten Fällen haben wir die Einführung der Technologie erleichtert. Als ich bei Arconic war, haben wir zum Beispiel die ersten Serienteile aus Titan für den Airbus A350 qualifiziert.
Wir sind derzeit ein Team von 13 Mitarbeitern, von denen viele Führungspositionen innehatten, darunter ich selbst – ich war zuvor Vice President bei Arconic. Unsere Leiterin der ADDvisor® Services ist Laura Ely, die frühere Technologiechefin von GKN Aerospace.
Mit dieser Expertise sind wir in der Lage, technische Anforderungen in einen strategischen Ansatz zu übersetzen. Wir füllen die Nische zwischen der Erklärung der additiven Fertigung für einen CEO oder einen Vice President of Engineering usw., damit sie an Dingen arbeiten, die für ihre Strategie relevant sind.
Basierend auf dem, was ein Kunde tut, schauen wir uns an, wo er in die Lieferkette passt, und versuchen dann, Ratschläge zu geben, wie er entweder an der additiven Fertigung teilnehmen oder die additive Fertigung nutzen kann.
Wir haben auch ein Schulungsprogramm entwickelt. Dies beruhte teilweise auf Anfragen, über die wir mehr über Additiv sprechen mussten. Gleichzeitig hatten wir einen Kunden, der fragte, ob wir ein Trainingsprogramm zusammenstellen könnten. Sie hatten beschlossen, ein großes AM-Unternehmen zu gründen und viele Ingenieure einzustellen.
Aber die Ingenieure wussten nicht, wie sie für den Prozess entwerfen sollten, und ohne dieses Wissen würde das Unternehmen seine Anforderungen niemals erfüllen finanzielle Ziele. Also haben wir das Trainingsprogramm erstellt.
Wir gehen grundsätzlich bedarfsorientiert vor. Zunächst besprechen wir mit unserem Kunden die Anforderungen an seine Produkte.
Sehr oft handelt es sich um ausgereifte Produkte und die Leute, die sie ursprünglich entworfen haben, gibt es nicht mehr. Wir sind also nicht dazu da, die additive Fertigung zu verkaufen, sondern sind da, um Ihnen zu helfen, ein besseres oder günstigeres Teil herzustellen. Und Additiv ist eine Lösung. Aber Sie müssen mit einem anforderungsbasierten Ansatz beginnen, der den Rest ein wenig einfacher macht.
Wie sind Sie zur additiven Fertigung gekommen?
Ich arbeitete zunächst für das heutige Honeywell Aircraft Engines, das ein Projekt mit Sandia National Labs und neun anderen Unternehmen unterzeichnet hatte.
Einige Wissenschaftler aus dem Labor nahmen eine unternehmerische Auszeit, um ein Unternehmen rund um eine Technologie zu gründen, die heute als gerichtete Energieabscheidungstechnologie bekannt ist, und nutzten Pulver als Ausgangsmaterial. Dieses Unternehmen heißt heute Optomec. So war es erfolgreich und es existiert noch heute.
Teil des Projekts zu sein war eine fantastische Gelegenheit, und so begann ich.
Ich wechselte dann zu Lockheed Martin und leitete das, was wir Manufacturing Exploration &Development für Skunk Works™ nennen. Zu diesem Zeitpunkt waren wir in jeder Form der additiven Fertigung sehr aktiv.
Für Verteidigung und Luft- und Raumfahrt hat Additive das Potenzial, viele Fragen zu beantworten. Also erforschten wir aktiv Polymersysteme, Blechlaminierungssysteme, gerichtete Energiesysteme, Pulverbettsysteme, und das ging einen Weg ein, Metallpulver in die Tiefe zu untersuchen.
Dann hatte ich das Glück, einen Auftrag bei der australischen National Science Agency, CSIRO, anzunehmen. Ich war Direktor ihres Hochleistungsmetallprogramms. An diesem Punkt kam das Additiv erneut zum Einsatz, da sie – wie viele nationale Labors wünschen – in der additiven Fertigung präsent sein wollten.
In Australien ist Additiv eine brillante Technologie, da sie viele Fertigungsprobleme löst. Das Land hat keine massive Fertigungsleistung und additive ist eine Möglichkeit, kleinere, effiziente Fertigungsmengen zu erreichen.
Wir haben das Labor 22 eingerichtet; Es ist eine Innovationseinrichtung mit verschiedenen Arten von Additivtechnologie. Mit diesem Lab richten wir einen Weg für Unternehmen ein, auf die Maschinen zuzugreifen und zu versuchen, ihr Produkt zu entwickeln.
Dafür haben wir viel recherchiert. Die kleine und mittlere Unternehmenslandschaft in Australien ist groß, und sie haben einfach nicht das Geld wie ein größeres Unternehmen, um einfach auf eine Maschine zu wetten und eine Million Dollar dafür auszugeben. Also gaben wir der Industrie Zugang zu dieser neuen Technologie.
Als ich 2015 in die USA zurückkehrte, arbeitete ich für ein Unternehmen namens RTI International Metals, das später von Alcoa gekauft wurde, und dann in Arconic verwandelt. Der CEO hatte erkannt, dass die Titanproduktion nicht in der von den Aktionären gewünschten Geschwindigkeit wachsen würde.
Also begann sie, in nachgelagerte Fertigungskapazitäten wie Umformung, Präzisionsbearbeitung und auch in Produktionsstätte für additive Fertigung in Texas. Meine Fähigkeiten, die Titanpulver und additive Fertigung umfassten, waren hier ziemlich wertvoll.
Also habe ich die F&E-Seite für das Advanced Manufacturing-Segment übernommen. Wie bereits erwähnt, haben wir das Projekt letztendlich von Airbus gewonnen und mussten dann Teile für den Airbus A350 qualifizieren.
Die Herstellung von Flugzeugteilen ist ein hartes Geschäft. Und es ist auch sehr schwierig, von einer Einrichtung, die in der Vergangenheit Prototypen erstellt hat, in eine Fertigungsumgebung überzugehen. Es ist eine Sache, wenn Sie ein Teil, eine Form, ein Mal herstellen. Wenn Sie produzieren, stellen Sie ein Teil, eine Form, aber 1.000 Mal her, also gibt es viel mehr Papierkram und viel mehr Qualifikation für spezielle Prozesse.
Sie haben das Potenzial von AM speziell für die Luft- und Raumfahrt und die Verteidigung angesprochen. Wie sehen Sie den aktuellen Stand der additiven Fertigung in diesen Branchen und was sind die wichtigsten Herausforderungen?
Die additive Fertigung ist eine disruptive Technologie und sowohl der Segen als auch Der Fluch disruptiver Technologien ist, dass sie nichts für die Sanftmütigen sind. Sie müssen sich verpflichten, sonst werden Sie den Wert nicht daraus ziehen.
Dazu gehört eine Komponente zur Personalentwicklung. Wenn Sie nicht wissen, wie Sie den Prozess gestalten sollen, werden Sie Ihren Business Case nie umsetzen. Design für Additiv ist für die meisten Ingenieure, die klassisch ausgebildet sind, um Metall von einem Block zu entfernen, nicht intuitiv. Sie müssen also die Dinge umdrehen.
Es ist sehr schwierig, eine risikoscheue Branche wie Luft- und Raumfahrt, Verteidigung oder Medizin dazu zu bringen, etwas disruptives zu übernehmen.
Die gute Nachricht ist jedoch, dass sie es tun. Die Medizin-, Luft- und Raumfahrtindustrie sowie die Verteidigungsindustrie haben Additive bereits früh eingesetzt. Diesen Fortschritt sehen wir weiterhin.
Wenn ich es auf eine andere Ebene reduziere, ist dieses Personalelement im Moment wirklich entscheidend. Es gibt nicht genügend Ingenieure, Manager und Führungskräfte, die die Technologie wirklich gut genug verstehen, um zu arbeiten und eine Strategie zu entwickeln, um das zu erreichen, was sie brauchen, um aus ihr herauszukommen.
Dies ist kein neues Phänomen. Dies gilt auch für traditionelle Technologien. Wenn Sie zum Beispiel umrüsten müssen, müssen Sie eine erhebliche Verpflichtung zur Umrüstung eingehen. Und das wirkt sich von unten nach oben auf das Unternehmen aus. Additiv ist nicht anders.
Warum ist es so wichtig zu wissen, wie man für die additive Fertigung konstruiert?
Wenn Sie nicht wissen, wie man Additiv entwickelt, werden Sie nicht den Kosten-Leistungs-Vorteil von Additiv erhalten.
Menschen neigen im Allgemeinen nur dazu, eine neue Technologie zu übernehmen, wenn Kostensenkungen oder Vorteile damit verbunden sind. Eine neue Technologie muss also alles tun, was die bestehende Technologie getan hat, aber sie muss es besser, schneller und billiger machen. Wenn der Business Case das nicht besteht, macht es keinen Sinn, das Projekt durchzuführen.
Wir machen die Analogie, dass Gewicht Geld ist. Und in der Welt der Additive ist Gewicht gleich Zeit und Zeit immer gleich Geld. Je mehr Material Sie haben, desto länger dauert der Druck und desto teurer wird es.
Das ist ein schwieriges Konzept.
Sie können den Preis der Maschine nicht kontrollieren und Sie können den Preis der Materialien nicht kontrollieren. Aber was Sie können Kontrolle ist Ihr Design. Ihr Design bestimmt, wie lange Ihre Maschinen laufen, sowie die gesamte Nachbearbeitung, die danach erfolgt. Und wenn Sie das nicht richtig machen, werden Sie die Kostenziele nie erreichen.
In unseren Schulungen gehen wir neben dem Thema Additiv auch auf die Kostentreiber in der additiven Fertigung ein, denn Ingenieure müssen wissen, wie sich mit einem additiven Bauteil Kosten aufbauen können.
Was kann oder wird getan, um diese Kompetenzlücke in AM zu schließen?
Die gute Nachricht ist, dass es jedes Jahr mehr Ressourcen gibt. Mittlerweile gibt es sogar Online-Ressourcen.
Mein Unternehmen hat beispielsweise über die Purdue University ein Online-Zertifikat für AM-Interessierte zusammengestellt. Es gibt sowohl einen Ingenieur-/Manager-Track als auch einen Executive-Track. Sie müssen nichts wissen, Sie brauchen kein Ingenieurstudium, um das Studium zu übertreffen. Und es ist online verfügbar.
MIT hat auch einen Online-Kurs gemacht und ich denke, wir sehen AM ähnlich, es schafft Wahlmöglichkeiten für den Studenten. Bei Purdue haben wir den Kurs mit Blick auf Menschen konzipiert, die berufstätig sind und nicht viel Zeit haben.
Es gibt also qualitativ hochwertige Online-Inhalte, die dazu beitragen, dass Menschen ohne jeglichen Hintergrund, sagen wir, auf ein mittleres Niveau kommen.
Die Natur des Lernens ist heute Ändern. Der Zugang zu hochwertigen Informationen und Bildung in sehr abgelegenen Gebieten ist jetzt über das Internet möglich. Was mir daran gefällt, ist, dass der Zugang zum Online jetzt nicht auf einen bestimmten sozioökonomischen Hintergrund oder Geschlecht ausgerichtet ist.
Eines der Dinge, die ich an der additiven Fertigung wirklich mag, ist, dass sie viele junge Leute in die Fertigung gebracht hat, weil sie additive Fertigung nicht als Fertigung betrachten. Es ist einfach cool.
Wir versuchen, dies zu fördern, denn je mehr Verstand Sie für eine Situation haben, desto besser wird sie.
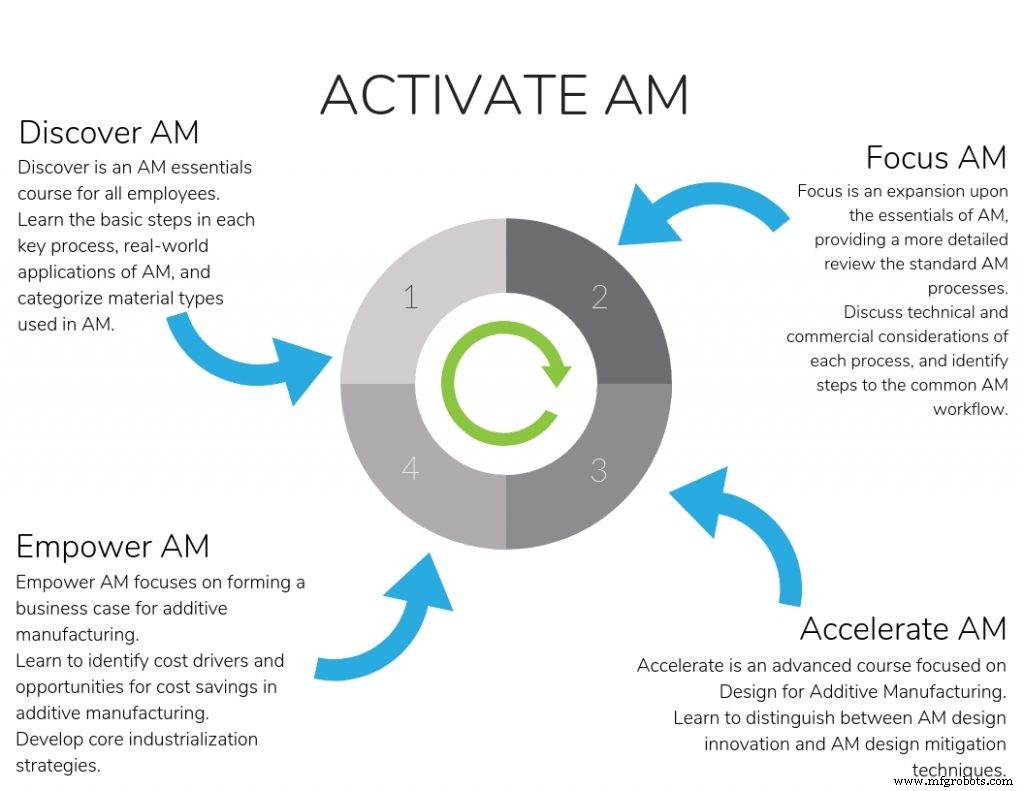
Die Branche verlagert sich stetig in Richtung Endteilfertigung. Was sind Ihre Gedanken dazu? Was müssen wir noch tun, um an diesen Punkt zu gelangen?
Ich glaube, wir sind nah dran. Wir sehen weniger Schlagzeilen wie „Diese Gruppe hat den allerersten 3D-gedruckten Linkshänder-Schraubendrehergriff hergestellt“ und etwas mehr von „Dieses Unternehmen hat die additive Fertigung für dieses Auto oder diesen Zug eingeführt“.
Diese Verschiebung bedeutet viel harte Arbeit, über die es nicht so viel Spaß macht, darüber zu sprechen, wenn man sich mit Spezifikationen, Arbeitsanweisungen und insbesondere damit einhergehenden Lieferketteninitiativen beschäftigt.
Außerdem beteiligen sich jetzt viele Tier-1- und Tier-2-Lieferanten und sogar relativ kleine Zerspanungshäuser. Sie kommen zu uns und fragen:„Ist es jetzt an der Zeit, dass wir uns einmischen? Wo sind wir? Was sollen wir tun?“
Wir haben einen Standardprozess, den wir die „Vier Linsen“ nennen:Maschinen, Materialien, der digitale Raum, der Ihr Produkt und alle Daten umfasst, und schließlich Menschen.
Wir koppeln das mit dem TBGA AM Reifegradmodell. Wir versuchen, die Produktanforderungen und die Fähigkeiten, die für die Verwendung von AM erforderlich sind, in Einklang zu bringen. Wir haben eine fünfstufige Matrix, in der Sie sich die Produktanforderungen ansehen und diese dann mit Fähigkeiten und Fähigkeiten abgleichen müssen, während Sie diesen Weg hinaufgehen.
Auf Level null ist das die Prototyping-Welt. Sie müssen nicht viele Arbeitsanweisungen, Spezifikationen oder große Kenntnisse in der additiven Fertigung haben, um diese Produktanforderungen zu erfüllen.
Dann gehst du in die Werkzeug- und Werkstatthilfen und da musst du ein bisschen mehr wissen. Da Sie jedoch kein Teil an einen Kunden liefern, ist es etwas einfacher.
Und dann kommen Sie in den Teileaustausch und die Teilekonsolidierung. Oben können Sie dieses Teil nur mit Additiv herstellen. Wenn Sie auf dieser Skala aufsteigen, müssen Ihre Fähigkeiten, Ihr Verständnis und Ihr Training mit Additiv zunehmen. Andernfalls wird es ein sehr riskantes Unterfangen.
Wir sehen, dass die meisten Leute auf Level null und Level eins sehr kompetent werden. Sie bewegen sich jetzt in diese Substitution, wo sie versuchen, ein zusätzliches Teil gegen das vorhandene auszutauschen. Und das ist schwierig, denn die Teile sind für unterschiedliche Prozesse ausgelegt. Wenn es nicht für Additiv ausgelegt ist, ist es sehr schwierig, einen Business Case dafür zu machen.
Die Abkehr davon erfordert zusätzliche Risiken, da Sie jetzt Ihre Lieferkette in Ihrem Herstellungsprozess unterbrechen. Und da sehen wir, dass viele Leute gerade sind. Sie versuchen herauszufinden, wann sie den Übergang von einem Teil der Ebene 2 zu einem Teil der Ebene 3 schaffen können, wo die geschäftliche Seite einfacher wird.
Gibt es irgendwelche Entwicklungen im Bereich Additiv, auf die Sie sich freuen?
Im Allgemeinen sehen wir, dass eine Menge Wissenschaft diese Welt jetzt einholt. Wir verstehen jetzt besser, welche Prozesse funktionieren, und die Maschinen werden viel schneller. Also alles sehr positiv.
Als Werkstoffingenieur sehe ich in diesem Bereich das enorme Potenzial für Materialien, sowohl in Polymeren als auch in Metallen. Das Potenzial ist groß, denn jetzt müssen Sie nicht mehr riesige Mengen an Material haben, um etwas herzustellen. Ich denke, die Leute, die davon am meisten profitieren werden, sind Design- und Materialingenieure – ich denke, es ist an der Zeit, zu glänzen.
Die additive Fertigung verbessert sich wirklich in allen Aspekten und es sieht so aus, als würden mehr Lösungen entwickelt, um einige der Lücken zu schließen. Das alles ist Teil des Industrialisierungspfads. Alles verbessert sich mit Additiv, und das ist für mich aufregend.
Die Leute bewegen sich in die Nachbearbeitungsseite und entwickeln Modifikationen an bestehenden Geräten, die sie für andere Branchen verwendet haben.
Auch die Softwareseite kommt mit neuen Konstruktionswerkzeugen und MES-/Workflow-Softwaresystemen sehr stark an.
Eine weitere spannende Sache ist die zweite Generation der Photopolymerisationstechnologien. Wir haben mit einer ganzen Reihe von Startups zu tun und jeder hat eine neue Idee, eine neue Wendung, eine neue Denkweise über den Prozess.
Sie haben kurz MES oder Workflow-Softwaresysteme erwähnt. Wie schätzen Sie die Bedeutung von MES- und Workflow-Software ein und wie kann diese zur Industrialisierung von AM beitragen?
Alles, was uns bei der Verwaltung des AM-Prozesses, des Risikos und der Verbesserung des Arbeitsinventars helfen kann, hilft auf der geschäftlichen Seite.
Luft- und Raumfahrt und Medizin haben sehr gute Qualitäts- und Sicherheitsnachweise. Das will man für eine neue Technologie nicht aufs Spiel setzen und ich denke, da kommen die Systeme ins Spiel.
Bei MES-Systemen sehe ich auch große Chancen darin, Intellektuelle besser schützen zu können Eigentum sowie die Möglichkeit, verschiedene Prozesse zu monetarisieren.
Ich denke, mit einigen der neuen Tools gibt es jetzt bessere Möglichkeiten, um zu verfolgen, wohin 3D-Druckdateien gehen, und sicherzustellen, dass sie die richtigen sind. Häufige Probleme der Qualitätssicherung werden mit solchen Management-Softwaretools besser.
Weitere Informationen zu The Barnes Group Advisors finden Sie unter: https://www.thebarnes.group/
3d Drucken
- Experteninterview:Pat Warner, Spezialist für additive Fertigung des Renault Formel-1-Teams
- Additive Fertigungstechnologien:Das Unternehmen der Nachbearbeitung, das die Zukunft der Fertigung gestaltet
- Ist die Hybridfertigungstechnologie die Zukunft der additiven Fertigung?
- Experteninterview:Nanoe CEO Guillaume de Calan über die Zukunft des keramischen 3D-Drucks
- Experteninterview:Ultimaker-Präsident John Kawola über die Zukunft des 3D-Drucks
- Experteninterview:CEO von PostProcess Technologies zur Lösung des Post-Processing-Engpasses für die additive Fertigung
- Expertenkommentar:Die Zukunft des Abfalls in einer digitalen Welt
- Die wichtigsten Arten der additiven Fertigung
- Die Zukunft des 3D-Drucks in der Fertigung
- Ist 3D-Druck die Zukunft der Fertigung?