Experteninterview:Oerlikons leitender Ingenieur für AM, Matthew Donovan, über 3D-Druck für die Luft- und Raumfahrt
Oerlikon, ein globaler Technologie- und Maschinenbaukonzern, bedient einige der sicherheitskritischsten Branchen, darunter Luft- und Raumfahrt und Verteidigung . Die additive Fertigung hat sich zunehmend zu einem wichtigen Bestandteil seines Angebots entwickelt, wobei das Unternehmen Anfang dieses Jahres in den USA ein Innovationszentrum und eine Produktionsstätte für fortschrittliche Komponenten im Wert von 55 Millionen US-Dollar errichtet hat.
Im Experteninterview dieser Woche sprechen wir mit Matthew Donovan, Principal Engineer for Additive Manufacturing bei Oerlikon, über die Weiterentwicklung einer End-to-End-AM-Produktionsanlage und spannende AM-Trends zu Achten Sie darauf, warum Standards für die Zukunft der Branche entscheidend sind.
Können Sie mir etwas über Oerlikon erzählen?
Oerlikon ist ein globales Unternehmen und führend in der Herstellung sowohl in den Segmenten Surface Solutions als auch Manmade Fibers. Als Teil des Segments Surface Solutions bietet Oerlikon AM Lösungen für die additive Fertigung, von Metallpulvern über Prototyping bis hin zur Serienproduktion.
Wie sind Sie zur additiven Fertigung gekommen?
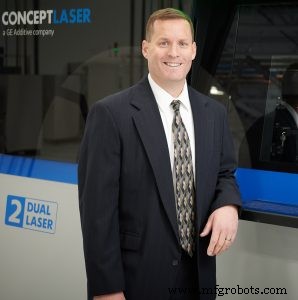
Mein Hintergrund liegt in der Luft- und Raumfahrt. Bevor ich zu Oerlikon kam, habe ich die letzten 20 Jahre hauptsächlich an Gasturbinentriebwerken, Komponenten für den heißen Abschnitt und Komponenten für den Verbrennungsabschnitt gearbeitet.
Ich habe einen Hintergrund in Brennstoffversorgungssystemen, hauptsächlich für Gasturbinentriebwerke in der Luft- und Raumfahrt, aber auch für industrielle Gasturbinen und Brennstoffzellenreformer. Ich habe auch an verschiedenen Forschungs- und Entwicklungsarbeiten mit der NASA und anderen Unternehmen gearbeitet. Ich habe also Erfahrung mit hochfesten Hochtemperaturmaterialien für sehr anspruchsvolle Umgebungen gesammelt.
Ich begann als Fertigungsingenieur, lernte die Besonderheiten der Herstellung und Konstruktion von Teilen und verbrachte damit Zeit als Qualitätsingenieur, der Felduntersuchungen für dieselben Komponenten durchführt.
Ich begann 2006 in der fortschrittlichen Fertigung zu arbeiten. Ich stieß auf herausfordernde Geometrien und Komponenten, die wir mit konventioneller Fertigung nicht wirklich herstellen konnten.
Zu diesem Zeitpunkt arbeitete ich mit Morris Technologies an 3D-gedruckten Metallkomponenten. Wir begannen mit der Entwicklung von Komponenten für Kraftstoffinjektoren mittels additiver Fertigung.
Im Laufe der Jahre habe ich einige Bauteile mittels additiver Fertigung entwickelt. Ich arbeitete für United Technologies und unterstützte das gesamte Unternehmen bei der Entwicklung und Implementierung von AM-Technologien, hauptsächlich mit dem Schwerpunkt auf Flugzertifizierungshardware.
Als wir an der Implementierung dieser Komponenten arbeiteten, stellte ich eine der größten Lücken fest, dass es an Standards für die Herstellung von Teilen und deren Zertifizierung mangelte.
Ein Großteil der mit der Luft- und Raumfahrt verbundenen Kosten sind nicht unbedingt die Komponenten selbst, sondern die Zertifizierung. Wir müssen für jede von uns hergestellte Komponente eine lückenlose Rückverfolgbarkeit gewährleisten. Die Entwicklung der Standards dafür, wie wir dies tun und dies für Additiv implementieren, war eine ziemliche Herausforderung.
Um 2009 begann ich mit der Arbeit an AM-Standards mit ASTM F42. Ich habe an einigen Standards mitgearbeitet und war anschließend in einigen Ausschüssen tätig. Ich habe gemeinsam mit ISO/TC 261 und ASTM F42 den Konstruktionsleitfaden für das Schmelzen von Metallpulverbetten durch Laser, ISO ASTM 52911, verfasst.
Durch die Zusammenarbeit mit United Technologies, die Zusammenarbeit mit vielen hochtalentierten Leuten und den Zugang zu einer Reihe großartiger Ressourcen konnten wir verschiedene Innovationen entwickeln und einige wirklich führende Produkte für AM . entwickeln Metallpulverbett.
Was beinhaltet Ihre Rolle bei Oerlikon?
Ich habe 2017 bei Oerlikon angefangen und bin jetzt Principal Engineer für AM. Meine Rolle konzentrierte sich stark auf die Implementierung und Entwicklung von serienreifen AM-Metalltechnologien.
Wir begannen als Start-up-Division der Surface Solutions Group. Wir haben eine neue Anlage in Huntersville, North Carolina, gebaut, die wir vor etwas weniger als einem Jahr bezogen haben.
Es ist eine 120.000 Quadratmeter große Anlage, die derzeit 18 Metallpulverbettanlagen betreibt. Vor Ort verfügen wir über HIP- (heißes isostatisches Pressen) und Vakuumöfen sowie Möglichkeiten zur Nachbearbeitung, Pulverhandhabung und Inspektion.
Das Ziel war es, diese Einrichtung als echten End-to-End-AM-Produktionsworkflow mit Kontrolle über jeden Aspekt der Lieferkette zu etablieren, damit wir unseren Kunden Rückverfolgbarkeit bieten können.
Meine Rolle dabei war hauptsächlich die Maschinenzertifizierung. Ich arbeite eng mit den Maschinen-OEMs an der Installation und Qualifizierung unserer Maschinen zusammen und lasse sie dann für ihre Fähigkeit und die Cross-Fähigkeit von Komponenten über verschiedene Maschinen hinweg zertifizieren.
Wir sind dann in der Lage, die Maschinenfähigkeiten, die Toleranzen und die Präzision einer einzelnen Maschine zu verstehen, um die geometrische Toleranz einer AM-Komponente und die Unterschiede zwischen unseren Maschinen zu erzeugen und sie dann abzustimmen, damit wir liefern können dasselbe Produkt auf mehreren Maschinen.
Standardisierung ist ein wirklich großes Gesprächsthema, insbesondere für Branchen wie die Luft- und Raumfahrt. Wie haben sich die Dinge im Laufe Ihrer Tätigkeit in der Branche entwickelt und wie ist der aktuelle Stand der AM-Standardisierung?
Es gab einige sehr gute Entwicklungen.
Wir brauchen Standards, insbesondere in der Luft- und Raumfahrt, aber auch in anderen sicherheitskritischen Bereichen wie Medizin, Nuklear und Energie. Das Wichtigste an Standards ist, dass sie es jedem ermöglichen, dieselbe Sprache zu sprechen und zu verstehen, wozu ein Produkt fähig ist.
In Ermangelung von Standards baute jeder effektiv Teile und verrichtete seine Arbeit oft auf sehr ähnliche Weise, aber nicht auf die gleiche Weise. Sie sprachen nicht dieselbe Sprache. Es ist sehr üblich, dass sich Leute auf verschiedene Begriffe beziehen, die denselben Prozess bedeuten, oder sich auf denselben Begriff beziehen und radikal unterschiedliche Prozesse bedeuten.
Die Entwicklung von Standards ermöglicht es Ihnen, überall in derselben Sprache zu sprechen und zu verstehen, was Sie meinen, wenn Sie sich beispielsweise auf einen Qualifikationsaufbau, ein Ausgangsmaterial oder eine Maschinenqualifikationsstufe beziehen.
Wenn Sie in der Luft- und Raumfahrt keinen Standard haben, nach dem Sie ein Teil zertifizieren können, oder in der Regel mehrere Standards, um das von Ihnen hergestellte Teil, seine mechanischen Eigenschaften, Leistung und Toleranzen zu identifizieren und zu in der Lage sein, es bis zum ursprünglichen Los, aus dem es stammt, bis hin zur chemischen Zusammensetzung der darin enthaltenen Elemente zurückzuverfolgen, dann kann man es nicht auf eine Luft- und Raumfahrtplattform stellen.
Wir können unglaublich komplexe Geometrien herstellen und mit AM Teile herstellen, die auf andere Weise physikalisch nicht möglich sind. Wir können viel Gewicht, Zeit, Material und Kosten sparen, indem wir Teile durch AM herstellen.
Die Gestaltungs- und Fertigungsfreiheit, die uns AM bietet, ist klar. Aber der Nachteil ist, dass es großartig ist, wenn Sie das Teil herstellen können, aber wenn Sie nicht beweisen können, dass es ein gutes Teil ist, nützt es niemandem.
Standards sind es, die uns dazu bringen, Teile herzustellen, zu verkaufen und in der Produktion für die Luft- und Raumfahrt zu verwenden.
Luft- und Raumfahrtnormen sind daher eines der Schlüsselstücke des Puzzles, bevor Sie Teile herstellen können.
Es gibt seit langem verschiedene Entwicklungsorganisationen, die in diesem Bereich sehr hart arbeiten. Ich arbeite seit ungefähr 10 Jahren als Freiwilliger an den ASTM-Standards und habe die Vorteile unserer Arbeit gesehen.
Wie ich bereits erwähnt habe, habe ich zum ursprünglichen Titanstandard für die Pulverbettfusion beigetragen. Für diesen ersten habe ich (und mehrere andere Leute) etwas mehr als zwei Jahre gebraucht, um den ersten validiert zu bekommen. Anschließend konnten wir in etwa der Hälfte der Zeit weitere umdrehen.
Die Dinge nehmen jetzt wirklich Fahrt auf. ASTM hat kürzlich in Zusammenarbeit mit der Auburn University sein Center of Excellence mit Sitz in Auburn, Alabama, ins Leben gerufen.
Die Absicht dahinter war, gezielte Forschungs- und Entwicklungsförderung und Anstrengungen durch Kooperationspartner einzusetzen, um schnell mehr Standards zu erreichen. Es gab viel Zusammenarbeit zwischen Industrie und Regierungsbehörden, um die Lücken und Standards zu identifizieren, die wir in der Branche wahrnehmen, und das ist es, was wir brauchen, um voranzukommen.
Vielleicht haben Sie schon von der ANSI-Roadmap gehört. Es ist ein sehr gutes Dokument, zu dem einige von uns in der Branche beigetragen haben, um unsere wichtigsten Lücken zu identifizieren, die wir schließen müssen, um eine echte Produktion für die additive Fertigung zu erreichen.
In der neuesten Version dieser Roadmap wurden meiner Meinung nach 91 Lücken identifiziert, hauptsächlich in Standardbereichen, und einige davon haben sehr hohe Priorität. Das ASTM Center of Excellence ist ein Vehikel, das verwendet wird, um F&E anzuwenden, um diese Lücken in den Standards zu schließen.
In einem anderen Bereich hat SAE International seine Aerospace Materials Specification (AMS). Die ersten für die additive Pulverbettschmelze waren AMS 7000, 7001, 7002 und 7003 für die kürzlich veröffentlichte Nickellegierung 625.
Das sind ausgezeichnete Arbeiten, die viele Ergebnisse bringen werden. Viele von uns verwenden diese Standards bereits zur Entwicklung von Serienteilen.
Was waren mit Ihrer Erfahrung bei der Einführung von AM einige der Herausforderungen bei der internen Integration der Technologie und wie haben Sie diesen Prozess bewältigt?
Oerlikon AM hat sich zum Ziel gesetzt, AM-Lösungen anzubieten, die den Anforderungen der anspruchsvollsten Branchen wie Luft- und Raumfahrt und Medizin usw. gerecht werden.
In unseren verschiedenen Einrichtungen verfügen wir über die richtigen Qualitätssysteme wie AS9100 für Luft- und Raumfahrt und ISO 13485 für Medizin. Aber die Integration aller dafür erforderlichen Systeme war eine Herausforderung, obwohl es einige Lösungen gibt, die Teile des Puzzles liefern.
Ich würde sagen, dass es nicht die eine Lösung gibt, die jeden einzelnen Aspekt unserer Bedürfnisse durchgängig abdeckt. Aber es gibt viele gute Tools, die Teile dieser gesamten End-to-End-Lieferkette abdecken.
Eine unserer Herausforderungen besteht also darin, die Lösungen zu finden, die verschiedene Aspekte unserer Lieferkette abdecken Integrieren Sie diejenigen, die die von uns benötigten Aspekte abdecken, und integrieren Sie sie.
Beispielsweise handhaben einige Lösungen Finanzen und Inventar sehr gut, aber sie eignen sich nicht sehr gut für Fertigungsabläufe. Andere handhaben Fertigungsworkflows und Produktionsplanung gut, aber nicht beispielsweise mit der Bauzeitschätzung, Materialprüfungsproblemen oder geometrischen Komponentenproblemen wie Blaupausen und 3D-Modellen.
Es gibt also viele verschiedener Aspekte, und unsere Herausforderung besteht darin, all diese verschiedenen Teile zu integrieren, um eine nahtlose End-to-End-Lösung zu erhalten. Derzeit ist dies ein ziemlich manueller Prozess, aber wir arbeiten daran, ihn in Zukunft viel automatisierter zu gestalten.
Können Sie Erfolgsgeschichten darüber teilen, wie Sie AM in der Produktion eingesetzt haben?
Obwohl ich diese Kunden ohne ihre Genehmigung nicht speziell nennen kann, haben wir mehrere Komponenten, die aktiv in Produktion sind. Einige, die mir spontan einfallen, sind Komponenten für die Luft- und Raumfahrt und die Verteidigung.
Eine ist also eine Flugkomponente, die Teil eines Missionssystems auf einem Militärhubschrauber ist. Wir produzieren seit zwei Jahren für dieses Bauteil und haben bis heute über 200 Einheiten erfolgreich ausgeliefert.
Wir stellen auch eine weitere Komponente her, die für einen Bodensensor verwendet wird, bei dem Sie ein integriertes System aus 80 verschiedenen Einzelkomponenten in einem monolithischen Teil haben. Auch dieser ist seit fast zwei Jahren in Produktion.
Wir haben eine Reihe anderer Produktionskomponenten, die wir herstellen — für Öl- und Gas- und Unterwasserexplorationsgebiete, die in aktiver Produktion für Unterwasserrobotik sind — für einen anderen unserer Kunden, den wir Teile herstellen für, die sowohl in Öl und Gas, Bohren und Exploration als auch in der Unterwasserrobotik aktiv eingesetzt werden.
Wie sehen Sie die Entwicklung der additiven Fertigung in den nächsten fünf Jahren, sowohl hinsichtlich der Technologie als auch der Branche insgesamt?
In den nächsten fünf Jahren sehe ich eine technologische Weiterentwicklung mit mehr Multilasersystemen, die eine schnellere Produktion von Teilen ermöglichen und dadurch die Kosten der Komponenten senken werden. Dies wird die Implementierung von AM-Teilen weiter vorantreiben.
Die Teilekosten sind ein Schlüsselfaktor, und die Laserzeit ist Ihr Hauptgrund für die Kosten einer AM-Komponente. Wenn Sie also mehr Laser in ein Teil quetschen und die Komponenten mit diesen Multi-Laser-Systemen zertifizieren können, können Sie das gleiche Teil schneller und damit billiger bauen.
Die andere Entwicklung besteht darin, dass wir bessere In-Prozess-Überwachungssysteme haben werden. Es gibt derzeit einige verschiedene von verschiedenen Herstellern, aber ich habe den Eindruck, dass viele von ihnen zwar gute Systeme sind, aber noch nicht das Leistungsniveau haben, das Benutzer wie ich benötigen würden, um sie zu implementieren bei einer echten Produktionsrate.
Meine Hoffnung ist, dass wir bald wahr in-Prozess-Kontrolle haben werden, so dass wir überwachen können, was während des Prozesses in der Maschine passiert und in der Lage sein, Probleme mit einer Komponente zu identifizieren, bevor sie die Blätter Maschine.
Das ideale Szenario wäre eine intelligente Software, die Probleme erkennen und potenzielle Korrekturen mit technischer Unterstützung im Handumdrehen vornehmen kann. Noch besser wäre es natürlich, wirklich robuste Maschinen zu haben, die keine Probleme haben und rund um die Uhr laufen.
Gibt es Trends, auf die Sie sich freuen?
Ich bin gespannt auf verschiedene Entwicklungen, darunter In-Process-Monitoring-Systeme, wie ich bereits erwähnt habe.
Es werden auch einige neue Materialien entwickelt und auf den Markt gebracht. Wir entwickeln verschiedene Materialien, die es einigen unserer Kunden ermöglichen, einige sehr revolutionäre Komponenten herzustellen.
Das andere, worüber ich mich freue, ist, dass die Hersteller auf der ganzen Welt viel stärker diversifiziert sind. Früher wurden die meisten AM-Maschinen in einer Handvoll Länder in Europa produziert. Jetzt gibt es neue Hersteller und verschiedene Länder, die unterschiedliche und neuartige Ansätze beim Bau von Maschinen anwenden.
Sie senken die Kosten der Maschinen und lernen aus ihrem Einsatz in der gesamten Branche, um sie für die Bediener intuitiver zu machen.
Meine Erfahrung in den ersten Jahren mit diesen Maschinen war, dass sie sehr pingelig sind und viel Aufmerksamkeit und „Babysitting“ erfordern. Und ehrlich gesagt war ein Großteil des Maschinendesigns nicht sehr fertigungsfreundlich.
Ich sehe, dass jetzt viel Benutzerfreundlichkeit in die Maschinen eingebaut ist, da Maschinenhersteller Feedback von ihren Benutzern bekommen.
Aber auch der zunehmende Wettbewerb durch verschiedene Hersteller auf der ganzen Welt trägt meiner Meinung nach dazu bei, Innovationen in den Systemen voranzutreiben, die Kosten zu senken und die Benutzerfreundlichkeit der Maschinensysteme zu erhöhen.
Was kommt als nächstes für Oerlikon, insbesondere für die Einrichtung, die Sie betreuen und betreiben?
Unser kurzfristiges Ziel für diese Einrichtung ist die Installation und Zertifizierung aller von uns gekauften Geräte. Wir haben also derzeit 18 Metallpulverbettsysteme online und betriebsbereit, und wir stellen auf vielen dieser Systeme Produktionshardware her.
Unser nächster Schritt für diese besteht darin, die Materialeigenschaften für alle unsere Materialsysteme für alle unsere Maschinen und die zugehörigen Datensätze zu vervollständigen. Aber das ist sehr zeitaufwendig und teuer.
Zum Glück haben wir hier viele sehr talentierte Leute mit viel Material-, Metallurgie- und Engineering-Erfahrung, und ich bin sehr stolz darauf, ein Mitglied dieses Teams zu sein.
Das andere Ziel besteht darin, die gesamte andere Ausrüstung aufrechtzuerhalten, um eine echte End-to-End-Produktionsanlage zu erreichen.
Wir haben vor kurzem unseren HIP-Ofen und unseren Vakuumofen online gestellt und arbeiten daran, diese zertifizieren zu lassen.
Wir haben auch einige CNC-Ausrüstung mitgebracht, und wir haben auch eine beträchtliche Anzahl zusätzlicher Öfen und CNC-Ausrüstung für die Nachbearbeitung. Das Ziel ist es also, all diese Geräte zu installieren, zu zertifizieren und betriebsbereit zu integrieren, um ein komplettes, zusammenhängendes Fertigungssystem zu schaffen.
Weitere Informationen über Oerlikon finden Sie unter: https://www.oerlikon.com/de/
3d Drucken
- Interview mit einem Experten:Professor Neil Hopkinson, Direktor für 3D-Druck bei Xaar
- Interview mit einem Experten:Philip Cotton, Gründer von 3Dfilemarket.com
- Interview mit einem Experten:Spencer Wright von pencerw.com und nTopology
- Interview mit einem Experten:Dr. Alvaro Goyanes von FabRx
- Experteninterview:Nanoe CEO Guillaume de Calan über die Zukunft des keramischen 3D-Drucks
- Experteninterview:Ultimaker-Präsident John Kawola über die Zukunft des 3D-Drucks
- Wie Ford Motor Company den 3D-Druck für die Automobilindustrie innoviert:Experteninterview mit Harold Sears
- Experteninterview:Nano Dimension-Mitbegründer Simon Fried über den Aufstieg des 3D-Drucks für die Elektronik
- Experteninterview:Brian Alexander von Solvay zur Entwicklung von Hochleistungspolymeren für den 3D-Druck
- Experteninterview:Ein Blick auf die ultraschnellen SLA-3D-Drucker in Industriequalität von Nexa3D