Anwendungs-Spotlight:3D-gedruckte Klammern
Halterungen sind, obwohl sie relativ einfache Teile sind, eine beliebte Wahl für den 3D-Druck. Zum einen ermöglicht der 3D-Druck die Optimierung der Halterung und hilft, die Leistung eines Teils sowie einer Struktur, in der eine Halterung verwendet wird, zu verbessern.
Im heutigen Application Spotlight untersuchen wir die wichtigsten Vorteile des 3D-Drucks für Brackets und tauchen in einige spannende Anwendungen in der Luft- und Raumfahrt- und Automobilindustrie ein.
Schauen Sie sich die anderen Anwendungen an, die in dieser Serie behandelt werden:
3D-Druck für Wärmetauscher
3D-Druck für Lager
3D-Druck für die Fahrradherstellung
3D-Druck für die digitale Zahnheilkunde und die Herstellung von Clear Alignern
3D-Druck für medizinische Implantate
3D-gedruckte Raketen und die Zukunft der Herstellung von Raumfahrzeugen
3D-Druck für die Schuhherstellung
3D-Druck für elektronische Komponenten
3D-Druck in der Bahnindustrie
3D-gedruckte Brillen
3D-Druck für die Endfertigung
3D-Druck für Turbinenteile
Wie 3D-Druck leistungsfähigere Hydraulikkomponenten ermöglicht
Wie 3D-Druck Innovationen in der Kernkraftindustrie unterstützt
Was ist eine Klammer?
Eine Halterung ist ein Befestigungselement, das dazu dient, zwei senkrechte Teile in einer Baugruppe zusammenzuhalten und den Winkel zu verstärken.
Klammern halten die Strukturen um uns herum zusammen (denken Sie an Gebäude, Flugzeuge und Autos) und bestimmen weitgehend die Stärke, Widerstandsfähigkeit und Integrität dieser Strukturen.
Warum 3D-Druck für Brackets verwenden?
Brackets sind relativ einfache Komponenten, die mit traditionellen Methoden hergestellt werden. Mit dem Aufkommen des 3D-Drucks können Ingenieure jedoch jetzt neue Wege zur Optimierung von Bracket-Designs erkunden.
Dies ist weitgehend möglich, dank der Fähigkeit des 3D-Drucks, komplexe geometrische Formen zu erzeugen, die mit herkömmlichen Fertigungsmitteln entweder unmöglich oder kosten- und zeitaufwendig wären.
Die wichtigsten Vorteile von 3D-gedruckten Brackets sind:
Schnellere Produktion
Die Herstellung komplexer Metallhalterungen erfordert normalerweise mehrere Maschineneinstellungen und kann viele Stunden dauern. Der 3D-Druck hingegen kann eine schnellere Lösung bieten. Ein Grund dafür ist, dass es möglich ist, mehrere Teile in einem 3D-Drucker zu verschachteln, was die gleichzeitige Herstellung mehrerer Brackets in derselben Maschine ermöglicht.
Für eine Halterung, die zuvor spritzgegossen wurde, ist die Zeitersparnis noch größer, da der 3D-Druck die Vorlaufzeit für die Herstellung eines Formwerkzeugs eliminiert.
Beseitigung der Montage
Einige Halterungen bestehen aus mehreren Teilen, was die Montagezeit der Halterung verlängern kann. Der 3D-Druck ermöglicht es, eine Halterung als ein konsolidiertes Teil zu entwerfen und zu produzieren, wodurch weniger Arbeit und Zeit zum Zusammensetzen der Halterung erforderlich ist. Der 3D-Druck einer Halterung als einzelnes Teil wird wahrscheinlich auch die Gesamtfestigkeit eines Teils erhöhen.
In einem Beispiel hat Philips mithilfe des 3D-Drucks eine neu gestaltete Halterung hergestellt, die Lampen an der Produktionslinie hält. Das Teil brach häufig aus, wobei jede Woche ein oder zwei ausfielen, hauptsächlich aufgrund wiederholter hoher Temperaturen, gepaart mit einer Struktur mit Bindenähten aus einer vierteiligen Halterung.
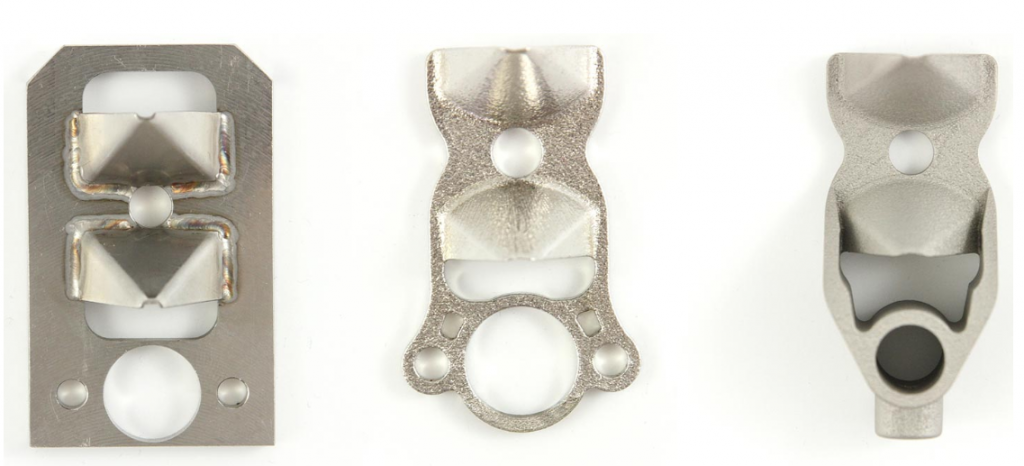
Philips konnte ein Metallteil als einteilige Halterung umgestalten, wodurch die zeitaufwändige Teilemontage reduziert und die Druckstellen der Bindenähte vollständig entfernt wurden. Während der ersten drei Monate des Gebrauchs ist die neu erfundene Halterung kein einziges Mal gebrochen.
Reduzierter Materialabfall
Der Prozess des 3D-Druckens einer Halterung als eine Komponente verwendet oft weniger Material, wodurch eine leichtere Halterung entsteht.
Diese Gewichtseinsparung führt zu einem geringeren Materialverbrauch und kann in einigen Fällen die Leistung eines Systems verbessern, bei dem eine Halterung verwendet wird.
Nehmen Sie die GEnx-Engines von GE als Beispiel. Die Motoren verwendeten Halterungen, die mit traditionellen Methoden wie Fräsen hergestellt wurden. Das bedeutet, dass die Teile aus einem großen Metallblock gefräst wurden und mehr als die Hälfte davon im Abfall landet.
Das Team, das an den Halterungen arbeitete, erkannte, dass durch den 3D-Druck des Teils bis zu 90 Prozent des Abfalls reduziert werden können.
Das Team implementierte außerdem kleine Designverbesserungen, die das Gewicht der Halterung um 10 % reduzierten. Laut dem Team zählt „beim Fliegen jede Unze“. Dies bedeutet, dass sich die Gewichtsreduzierung der Komponente auf den Treibstoffverbrauch des Flugzeugs auswirken kann, ihn reduziert und somit zu einem effizienteren Flugzeug führt.
In einem anderen Beispiel haben Ford-Ingenieure kürzlich eine elektrische Feststellbremshalterung aus Kunststoff für den Ford Mustang Shelby GT500 in 3D gedruckt, die 60 Prozent leichter ist als eine zuvor gestanzte Stahlversion.
Die Möglichkeit, Metall durch Kunststoff oder Verbundwerkstoff zu ersetzen
Für einige Anwendungen kann der 3D-Druck verwendet werden, um Brackets aus Kunststoff statt aus Metall herzustellen. Kunststoffhalterungen eignen sich möglicherweise besser für Anwendungen wie Konsumgüter mit begrenzter Lebensdauer oder Produkte mit empfindlichen elektronischen Komponenten, bei denen Metallhalterungen nicht funktionieren.
Ein Beispiel stammt von einem Hersteller von Kommunikationsgeräten, Boyce Technologien. Das Unternehmen nutzte den 3D-Druck, um Kunststoffteile für die NYC Transit-Totems zu bauen. Jedes dieser Systeme verfügt auf der Oberseite über eine grüne Acrylkappe, die einen LED-Streifen zur Beleuchtung sowie ein empfindliches Antenneninstrument beherbergt.
Um eine Unterbrechung des Antennensignals zu vermeiden, sollte es keine geben metallisches Material davor. Das bedeutet, dass das Unternehmen die Halterungen für den LED-Streifen und das Gehäuse für die Antenne aus Kunststoff fertigen musste. Das Boyce-Team hatte nur einen kurzen Zeitraum für Design, Engineering und Produktion, sodass der 3D-Druck eine geeignete Lösung darstellte.
Mit dem BigRep Studio-System war Boyce in der Lage, gebogene Montagehalterungen für die LED-Leuchten zur Beleuchtung der Kappe zu prototypieren und dann direkt mit der Herstellung dieser Teile auf derselben Plattform fortzufahren.
Der 3D-Druck dieser Halterungen ermöglichte eine schnellere und kostengünstigere Herstellung als Spritzguss oder maschinelle Bearbeitung und erfüllte gleichzeitig die Anforderungen an die Nichtmetallisierung über der Antenne.
Weitere Beispiele für 3D-gedruckte Klammern
Luft- und Raumfahrt
3D-gedruckte Titanhalterungen für Boeing 787
3D-gedruckte Halterungen für die Luft- und Raumfahrt aus Titanlegierungen werden im Flugzeugbau immer häufiger verwendet. Ein Beispiel ist eine Halterung für einen Zugangstürverschluss für die Boeing 787, installiert von Spirit AeroSystems.
Der zuvor maschinell bearbeitete Türschlossbeschlag wird jetzt von Norsk Titanium mit seiner proprietären Rapid Plasma Deposition (RPD)-Technologie 3D-gedruckt. Der Name beschreibt das Verfahren:Ein Plasmalichtbogen ermöglicht die kontrollierte Abscheidung von Titan mit schnellen Aufbaugeschwindigkeiten. Die Technologie ist Berichten zufolge 50-100-mal schneller als pulverbasierte Systeme und verbraucht 25-50 Prozent weniger Titan als Schmiedeverfahren.
Der Hauptgrund für den Wechsel zum Titan-3D-Druck ist die Möglichkeit, die Herstellung zu reduzieren Kosten. Titan ist teuer, und bei der Bearbeitung eines Teils aus einem Titanblock wird viel von diesem teuren Material verschwendet. Das zweite Problem sind die hohen Maschinenzeit- und Schneidwerkzeugkosten, die in die Zerspanung des Metalls fließen und die Produktionskosten in die Höhe treiben.
Durch den 3D-Druck einer Halterung kann Spirit diese Kosten erheblich senken und gleichzeitig die Markteinführungszeit für neue Teile um mindestens 60 Prozent verkürzen.
Liebherr-Aerospace 3D druckt Halterungen für Airbus
In einem weiteren Beispiel in der Luft- und Raumfahrtindustrie hat Liebherr-Aerospace mit dem 3D-Druck von Bugfahrwerkshalterungen für den Airbus A350 XWB begonnen.
Diese Halterungen werden die ersten qualifizierten überhaupt sein 3D-gedruckte Titanteile in das Airbus-System eingeführt.
Im Gegensatz zu Spirit AeroSystems konnte Liebherr ein Teil neu konstruieren, um eine Gewichtsreduzierung von 29 Prozent zu erreichen. Durch den Einsatz von 3D-Druck konnte zudem die Steifigkeit des Bauteils um 100 Prozent gesteigert werden.
Liebherr-Aerospace hat 2019 einen wichtigen Meilenstein erreicht:Das Luftfahrtbundesamt hat dem Unternehmen grünes Licht für die Fertigung von Komponenten mit AM gegeben. Liebherr druckt seither Titan-Serienteile inklusive Brackets in 3D.
Automobil
Eine Dachhalterung, optimiert und 3D-gedruckt von BMW
Im Jahr 2018 hat BMW seinen ikonischen i8 Roadster mit einer preisgekrönten 3D-gedruckten Metalldachhalterung auf den Markt gebracht.
Die Dachhalterung, ein kleines Bauteil, das beim Falten hilft und das Verdeck des Autos aufklappen, erforderte ein neues Design, um die Leistung des Dachfaltmechanismus zu maximieren. Um dieses Ziel zu erreichen, kombinierten die Ingenieure von BMW 3D-Druck mit Software zur Topologieoptimierung.
Mit der Software konnten die Ingenieure Parameter wie das Gewicht, die Größe des Bauteils und die Belastung eingeben. Die Software generierte dann ein Design, das die Materialverteilung des Teils optimierte.
Der Entwurf des Ingenieurteams war unmöglich zu gießen. Das Team stellte fest, dass der einzige Weg, dieses Design zu ermöglichen, der Metall-3D-Druck war.
Dank der Selective Laser Melting (SLM)-Technologie haben die Ingenieure eine Metalldachhalterung entwickelt, die zehnmal steifer und 44 Prozent leichter ist als die herkömmliche Alternative.
Bugattis leichte Halterungen
Bugattis Fahrzeuge sind auch mit einer Reihe von 3D-gedruckten Halterungen ausgestattet. Eine davon ist eine in Zusammenarbeit mit dem Fraunhofer IAPT hergestellte Spoilerhalterung aus Titan. Dieser Spoiler soll das aerodynamische Design von Bugatti-Fahrzeugen verbessern.
Ein weiterer Partner im Projekt Spoilerhalterung war Siemens, das half, die Halterung für die Produktion zu optimieren. Am Ende zeigte das fertige Teil eine Zugfestigkeit von 1.250 MPa, eine Materialdichte von über 99,7 Prozent und eine Gewichtsreduzierung von 53 Prozent.
3D-Druck wurde auch verwendet, um eine kleine Motorhalterung mit integrierter Wasserkühlung für den Supersportwagen Bugatti Chiron. Das Teil dient als aktiver Hitzeschild, wodurch die vom Motor übertragene Wärme deutlich reduziert wird. Das innovative Bauteil, gedruckt in AlSi10Mg auf einem SLM280 Twin 3D-Drucker von SLM Solutions, ist seit der Veröffentlichung des ersten Bugatti Chiron in allen Serienfahrzeugen verbaut.
3D-gedruckte Halterungen:Kleine Bauteile mit großen Chancen
Halterungen sind kleine und eher banale Teile, die in der Vergangenheit schwer zu optimieren waren, als Ingenieure durch traditionelle Herstellungsmethoden eingeschränkt waren. Heute können Ingenieure optimierte Brackets entwerfen und diese Designs mithilfe des 3D-Drucks zum Leben erwecken.
Dank der Technologie können Brackets leichter, aber dennoch steifer und haltbarer gemacht werden. Die obigen Beispiele zeigen auch, dass durch den Einsatz des 3D-Drucks die Lebensdauer und die Gesamtleistung der Komponente verbessert werden können.
Natürlich sind wir noch weit von massengedruckten 3D-Brackets entfernt. Spezialanwendungen wie Flugzeughalterungen und Halterungen, die in kleinen Stückzahlen hergestellt werden, werden jedoch auch in Zukunft eine gute Nische für die Technologie bleiben.
3d Drucken
- Schweißen und Kleben von 3D-gedruckten Kunststoffteilen
- Erkunden des Polyjet-3D-Drucks
- Was ist Bioprinting?
- Anwendungs-Spotlight:3D-Druck für medizinische Implantate
- Anwendungs-Spotlight:3D-Druck für die digitale Zahnheilkunde und die Herstellung von Clear Alignern
- Anwendungs-Spotlight:3D-Druck für die Fahrradherstellung
- Anwendungs-Spotlight:3D-Druck für Lager
- Anwendungs-Spotlight:3D-Druck für Wärmetauscher
- COVID-19 hat 3D-Druck ins Rampenlicht gerückt
- Anwendung des 3D-Drucks in der Automobilindustrie