Simulationssoftware breitet ihre Flügel aus
Wenn sie mit ärgerlichen Themen wie Produktkomplexität, Leichtbau, fortschrittlichen Materialien und neuen Herstellungsmethoden ringen, verwenden Fertigungsingenieure von heute zunehmend High-Fidelity-Simulationen, um Lösungen für diese Herausforderungen zu visualisieren. Die neueste Simulationssoftware kann Hinweise zur Verbesserung des Produktdesigns und der Leistung mit High-End-CAE-Paketen und NC-Simulationssoftware geben, die dabei helfen, nicht nur die besten Designs zu bestimmen, sondern auch die effizientesten Wege, sie zu erreichen.
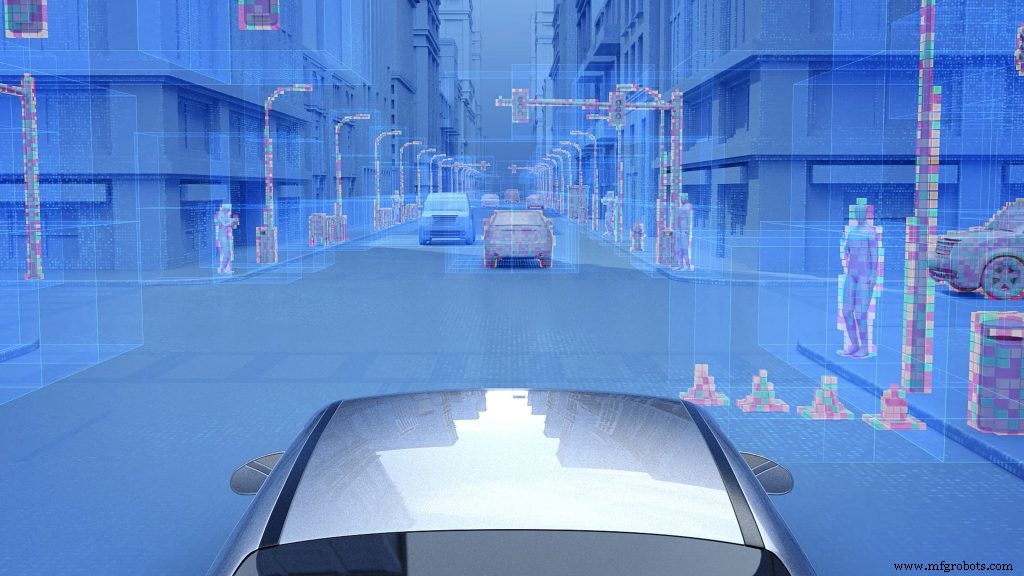
Neue Herstellungsverfahren wie die additive Fertigung (AM) stellen Hersteller vor andere Probleme, und die Simulation kann im Voraus bestimmen, welche Lösungen am besten funktionieren. Viele Simulationssoftwarepakete bieten jetzt additivspezifische Simulationen, die dabei helfen können, die Schichtprozesse zu veranschaulichen, mit denen additive Produkte hergestellt werden, und gleichzeitig zu visualisieren, wie traditionelle subtraktive Metallschneideprozesse effizienter gestaltet werden können.
Das Komplexitätsproblem lösen
In der diskreten Fertigung stehen Produktentwicklungsingenieure vor enormen Herausforderungen, da alles, von Autos über Flugzeuge bis hin zu riesigen Schiffen und schweren Maschinen, Millionen von Codezeilen enthält, die Systeme mit Elektronik programmieren, die auf das industrielle Internet der Dinge (IIoT) ausgerichtet sind.
„Die größeren Trends, die wir sehen, sind die zunehmende Komplexität von Produkten“, sagte Ravi Shankar, Director, Global Simulation Product Marketing, Siemens PLM Software (Plano, TX), während er auf den zunehmenden Anteil an Elektronik in mechanischen Komponenten hinwies. „Was das antreibt, ist der digitale Zwilling und modellbasiertes Engineering.“
Autonome Fahrzeuge und Drohnen sind das neueste Beispiel für komplexe Systeme, die Simulationssoftwaresysteme erfordern, sagte Shankar. „Wir haben auch den Fokus auf die Kraftstoffeffizienz und Emissionen von Fahrzeugen gesehen, mit der Zunahme des Gewichts und der Verwendung von generativem Design“, fügte er hinzu.
Siemens hat kürzlich eine Lösung für selbstfahrende Autos vorgestellt, die seine Simcenter-Simulationslösungen mit neuer Sensortechnologie kombiniert. Auf dem US Innovation Day von Siemens im März in Chicago stellte das Unternehmen das System vor, das virtuelle Sensorbilder von Tass PreScan mit der Mentor DRS360-Plattform verwendet, die die Entwicklung von Algorithmen für die Sensorfusion und -verarbeitung automatisiert.
„Der erste Trend ist, dass physikbasierte Weltmodelle und physikbasierte Sensormodelle erstellt werden können“, sagte Martijn Tideman, Produktdirektor bei Tass International (Steenovenweg, Niederlande), das letztes Jahr von Siemens übernommen wurde. „Diese Modelle erzeugen hochpräzise künstliche Sensorinformationen, die so generiert werden können, als kämen sie von echten Kameras, Radaren und LIDARs. Wenn Sie diese künstlichen Daten an Verarbeitungseinheiten im Auto, wie z. B. den DRS360, weitergeben, können Sie die Hardware/Software im Auto bewerten, ohne einen einzigen Kilometer zu fahren.“
Ein weiterer Schlüssel ist sicherzustellen, dass die automatisierte Fahrsimulationssoftware auf Hochleistungsclustern (HPCs) läuft, sagte Tideman.
„Diese Cluster können viele Simulationen parallel ausführen, was den virtuellen Bewertungs-/Validierungsprozess beschleunigt. Sie möchten am Wochenende eine Million virtuelle Meilen fahren können.
„Automatisierte Fahrsimulatoren müssen mit einer Vielzahl anderer Hardware- und Softwaremodule verbunden werden, z. B. Kartenimportprogrammen, um automatisch virtuelle Straßennetze oder Fahrdynamiksimulationstools zu generieren, um sicherzustellen, dass das Fahrzeug korrekt auf Steueraktionen reagiert“, erklärte er . „Schnittstellen zwischen Simulationswerkzeugen werden zunehmend standardisiert“, wie zum Beispiel mit FMI/FMU (Functional Mock-up Interface/Functional Mock-up Unit), fügte Tideman hinzu.
Disruptive Simulation
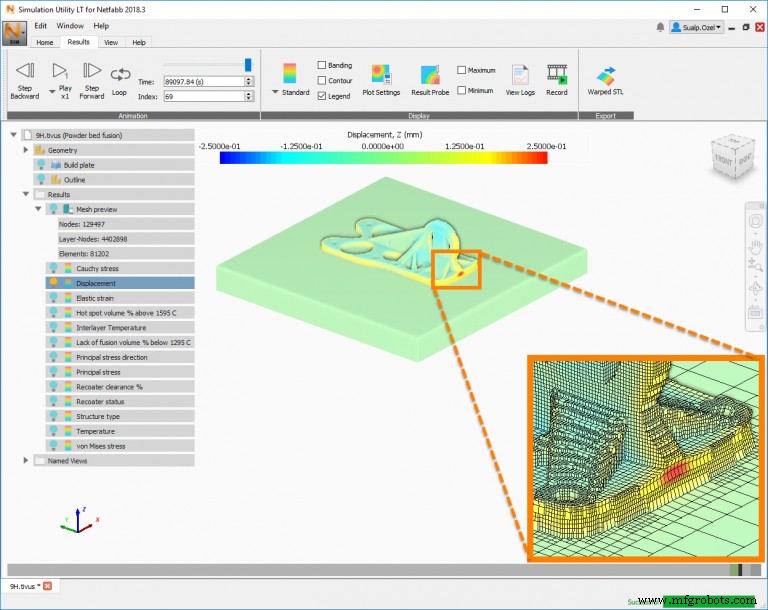
Mehrere Schlüsseltechnologien beeinflussen die Art und Weise, wie Simulation in der Fertigung angewendet wird. „Während es zahlreiche technische Entwicklungen gibt, die sich weiterentwickeln und verbessern, haben einige wenige das Potenzial, grundlegend zu verändern, wo, wie und von wem Simulationsfunktionen verwendet werden“, sagte Seth A. Hindman, Senior Manager, Produktstrategie und -management, Fertigung, Konstruktion und Produktion bei Autodesk Inc. (San Rafael, CA).
„Das Mooresche Gesetz gilt viel länger, als die meisten es sich vorgestellt haben. Mit kontinuierlichen Fortschritten in der Rechenleistung ist unglaublich leistungsstarke Hardware zu einem sehr niedrigen Preis erhältlich. In Kombination mit der Entwicklung umfangreicher Glasfasernetze können Unternehmen mit externen Rechenressourcen verbunden werden, die die Geschwindigkeit ihrer eigenen Intranets überschreiten“, sagte Hindman. „Burst-Kapazität, elastische Datenverarbeitung und konfigurierbares HPC [Hochleistungsrechnen] ermöglichen es Unternehmen, die Art und Weise, wie sie ihre Produkte entwickeln und herstellen, grundlegend zu ändern, indem sie genügend Analysen durchführen, um wirklich zu verstehen, wie sich ihr Produkt in zahlreichen Anwendungen und Umgebungen verhalten wird.“
Hersteller entfernen sich auch von netzabhängigen Analysen, sagte Hindman.
„Die Allgegenwärtigkeit von 3D-Konstruktionsdaten hat die Nachfrage nach Simulationswerkzeugen, die nicht mehr netzabhängig sind und von der Assoziativität mit den nativen Konstruktionsdaten profitieren können, weiter vorangetrieben. Dies erhöht nicht nur die Produktivität im allgemeinen Arbeitsablauf, sondern erweitert auch das Publikum, das von Simulationsfunktionen profitieren kann. Der natürliche Druck besteht darin, Lösungen zu entwickeln, die robuster und intuitiver sind und sich von traditionellen CAE-Anforderungen lösen. Das langfristige Potenzial besteht darin, dass dies eine vereinfachte Interaktion mit Lösungen und die Automatisierung belastender Aufgaben ermöglicht.“
Die langjährige Perspektive innerhalb von CAE, die Simulation „nach vorne“ zu bringen, wird jetzt durch die Idee einer zielbasierten Analyse ersetzt, fügte Hindman hinzu. „Während die Vorabsimulation leistungsstark ist, ist sie immer noch auf eine traditionelle Konvention angewiesen, bei der das getestet wird, was Sie entworfen haben, anstatt die Erkundung von Designs voranzutreiben, die die von Ihnen definierten Ziele erfüllen“, sagte er. Autodesk führt derzeit das sogenannte generative Design in den Engineering-Markt ein, fügte Hindman hinzu, das seit Kurzem in Autodesk Fusion 360 Ultimate verfügbar ist.
„Unsere generative Designtechnologie ermöglicht die Erstellung von objektiv inspirierten Designs durch das System, was eine umfassende Erkundung des Designraums erleichtert und erkenntnisbasierte Kompromisse ermöglicht“, sagte Hindman. „In der Vergangenheit bestand die Hauptaufgabe von Ingenieuren darin, ein Design zu entwickeln, das funktioniert. Mit generativem Design erfüllt jedes Ergebnis erfolgreich diese Grundanforderung, was bedeutet, dass Entscheidungsfindung und Kompromisse auf die Ebene von Kerngeschäftsinitiativen gehoben werden.“
Additive Prozesse simulieren
Additive Entwicklungen begeistern die Fertigungsindustrie weiterhin, und viele Simulationsentwickler haben kürzlich entweder neue oder verbesserte additivspezifische Versionen ihrer Simulationssoftware herausgebracht.
Beispielsweise hat der Simulationsentwickler Ansys Inc. (Canonsburg, PA) am 19. April seine neuen Lösungen Additive Print und Additive Suite veröffentlicht, die Simulationen für Metall-AM-Prozesse ermöglichen. Die Lösungen sollen es Anwendern ermöglichen, leichte, komplexe Metallteile zu drucken und Mikrostruktureigenschaften und -verhalten zu analysieren. Laut Ansys wird dies dazu beitragen, die AM-Kosten zu senken, indem Designbeschränkungen begrenzt, Abfall reduziert und die Druckzeit verkürzt werden.
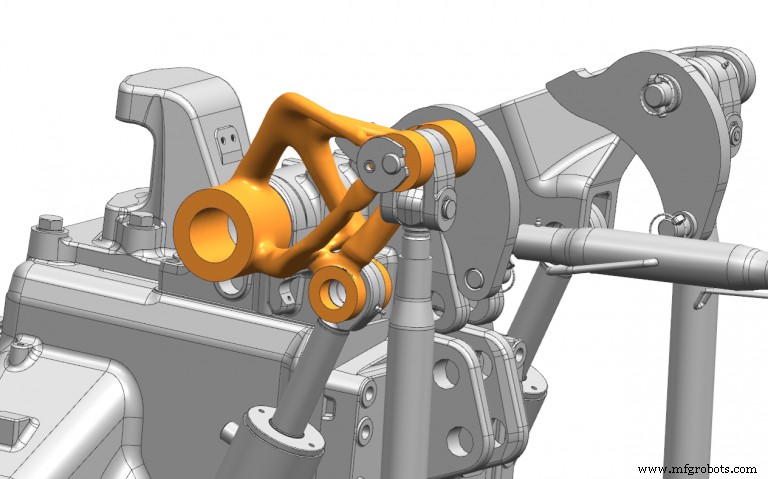
Der vollständige additive Simulationsworkflow von Ansys ermöglicht es Kunden, ihre Produktdesigns virtuell zu testen, bevor sie ein Teil drucken, so das Unternehmen. Die Software beinhaltet eine Simulation vor dem Druckprozess, die es Ingenieuren ermöglicht, die Leistung eines Teils in der Entwurfsphase zu entwerfen, zu testen und zu validieren, und die hohen Kosten für physische Versuche und Irrtümer erheblich reduziert.
AM ist ein Wendepunkt für die Fertigung, sagte Brent Stucker, Director of Additive Manufacturing bei Ansys. „Medizinprodukte können mit patientenindividuellen Geometrien hergestellt werden. Ersatzteilhaltungen für viele Komponenten gehören der Vergangenheit an, da Ersatzteile bei Bestellung produziert werden können“, so Stucker. „Produkte, die in extremen Umgebungen eingesetzt werden, beispielsweise in der Öl- und Gasindustrie, können mit neuen [haltbareren] Hybridmaterialzusammensetzungen hergestellt werden. Die geometrische Komplexität, die AM bietet, bedeutet, dass Dutzende von Komponenten in eine einzige Komponente integriert werden können, die leichter und leistungsfähiger ist.“
Stucker stellte fest, dass Designer und Maschinenbediener, die normalerweise keine technischen Simulationsanwender waren, jetzt einen komplexen Druckprozess verstehen müssen.
„Wir sehen, dass Maschinenbediener mehr wollen als nur fundierte Vermutungen, wenn es darum geht, vorherzusagen, ob ein Teil erfolgreich gebaut werden kann“, sagte er. „Sie müssen schnell verstehen, wie eine bestimmte Maschineneinstellung zu einer Verformung des Teils vor und nach dem Entfernen von Stützen führt und ob eine übermäßige Verformung dazu führen kann, dass der Pulververteilungsmechanismus auf das Teil trifft [was als Blattcrash bekannt ist]. Ähnlich verhält es sich mit Designern, die Design for AM [DfAM] machen. Sie möchten wissen, ob das von ihnen entworfene Teil erfolgreich gedruckt werden kann, und wenn ja, welche Eigenschaften diese Komponente haben wird.
„Simulation gibt Designern und Bedienern die Möglichkeit, den additiven Prozess zu verstehen“, fügte er hinzu. „Deshalb haben wir Ansys Additive Print als eigenständiges Tool zur Vorhersage des Druckprozesses entwickelt – damit ein Nicht-Ingenieur das Tool innerhalb weniger Tage verwenden kann.“
Während Simulationssoftware erfolgreich eingesetzt wurde, um sicherzustellen, dass eine entworfene Struktur den Betriebsbedingungen während des Feldbetriebs standhält, wird sie auch ständig durch komplexe Belastungen, Materialien und Physik herausgefordert, bemerkte Subham Sett, Direktor, Simulia Strategic Initiatives, Dassault Systèmes ( Paris). „Simulationssoftware tendiert jetzt dazu, Multiphysik- und Multiskalenlösungen bereitzustellen, die Vorhersagen für jeden Aspekt liefern, um das Branchenwachstum zu beschleunigen. Beispielsweise wird in der Automobilindustrie Simulationssoftware verwendet, um multiphysikalische Probleme von Mehrkörperdynamik, Geräuschen und Vibrationen, Crash-Tauglichkeit bis hin zu instationären Strömungen sowie Multiskalenprobleme aus dem Materialdesign, Multiskalen-Material-Up- und -Down-Skalierung und Substrukturen zu lösen. ”
Das Hinzufügen der Fähigkeit, die aus dem AM-Prozess resultierende Form vorherzusagen, zählt zu den aufregendsten neuen Entwicklungen in der Fertigungssimulation, sagte Sett. „Unter Berücksichtigung des Scanpfads, der Materialeigenschaften, der Maschinen- und Lasereigenschaften können wir die Verformung des Teils aufgrund von Hitze und Schwerkraft während des Druckvorgangs genau vorhersagen“, fügte er hinzu.
Die Simulation des additiven Prozesses ermöglicht es Bauherren, den Prozess genauer vorherzusagen und zu steuern, wodurch verhindert wird, dass Fehler im Schicht-für-Schicht-Bauprozess für additive Teile auftreten.
Shankar von Siemens sagte, dass die Simulation in additiven Prozessen, die Siemens letztes Jahr mit seinem NX Additive-Modul hinzugefügt hat, es Herstellern ermöglicht, Fertigungsergebnisse vorherzusagen.
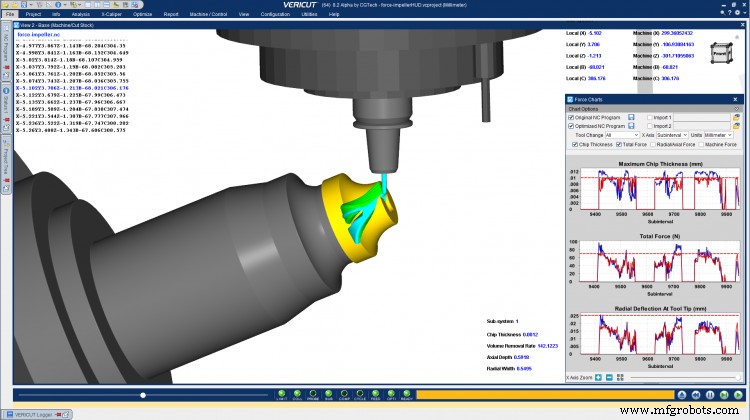
„Beim Erstellen der Schichten muss man viele Dinge wissen:Wie lange dauert es, bis es abgekühlt ist? Was sind die Hohlräume [die leeren Räume oder Taschen] in dem Teil? Die Simulation kann dabei helfen, die Hohlräume und auch die Eigenspannungen im Produkt anzugehen“, sagte er. Die Simulation hilft den Herstellern auch dabei, Prozesse zu standardisieren und zu verstehen, wie das Produkt funktionieren wird.
Siemens arbeitet derzeit an Themen wie additive Prozesse mit Phasenwechseln und Teilekühlung. In einigen Fällen wird aufgrund der rechenintensiven Natur dieser Simulationen HPC verwendet. „Berechnungen können oft lahmgelegt werden. Wenn Sie versuchen, große Modelle zu lösen, ist [HPC] attraktiv“, sagte Shankar.
In Bezug auf Additive baut Autodesk sein Lösungsportfolio weiter aus, sagte Hindman. „Die neueste Ergänzung des Netfabb-Portfolios ist die Aufnahme von generativen Designfunktionen von Autodesk. Wie ich bereits erwähnt habe, ermöglicht generatives Design die Erstellung von objektiv inspirierten Designs durch das System, um eine umfassende Erkundung des Designraums zu erleichtern. Ein Schlüsselfaktor dafür, wie das System als aktiver Teilnehmer funktionieren kann, ist, dass wir ihm beigebracht haben, den additiven Fertigungsprozess zu berücksichtigen, sodass es Ergebnisse generiert, die für den 3D-Druck optimiert sind.“
Mit der März-Version von Netfabb Ultimate führte Autodesk zusätzlich zum bestehenden eigenständigen Netfabb Local Simulation-Angebot integrierte Prozesssimulationsfunktionen ein. Hindman sagte, dass beide Netfabb-Versionen jetzt enthalten:verbesserte Vorhersagen von Effekten wie eingeschlossenem Pulver, Hot Spots/Scorching und fehlender Verschmelzung; zusätzliche Prozessemulation wie EDM-Teileentfernung und die Auswirkungen der Wärmebehandlung; verbesserte Leistung im optionalen Elastic-Computing-Service von Autodesk; Einführung von Prozessanalysefunktionen in Netfabb Ultimate; und optimierte Möglichkeit zum Austausch von simulationsgesteuerten kompensierten Teilvorformlingen gegen die ursprüngliche Geometrie.
Autodesk hat außerdem in Partnerschaft mit den Portfolios Netfabb und PowerMill (PowerMill Ultimate) des Unternehmens Unterstützung für den Direct Energy Deposition (DED)-Prozess eingeführt, um das Know-how bei mehrachsigen Robotersteuerungen zu nutzen.
„Dies fügt eine weitere Möglichkeit hinzu, das Potenzial außergewöhnlich großer Verformungen und Ausfälle während der Hochgeschwindigkeitsabscheidungsfertigung vorherzusagen“, sagte Hindman. „Wenn Unternehmen sich der additiven Metallfertigung zuwenden, gibt es häufige Gefahren, denen sie sich stellen und die sie überwinden müssen.“ Er fügte hinzu, dass die häufigsten Herausforderungen beim Betrieb eines Metallpulverbett-Fusionsdruckers sind:Teileverformung, Verzug (das gedruckte Teil ist nicht akzeptabel und kann den Beschichter beschädigen); durch thermische Belastung verursachte Ausfälle/Brüche (Teile brechen während des Druckens und können den Beschichter beschädigen); Stützversagen (in dem Teil baut sich so viel Spannung auf, dass die Verbindung zwischen der Bauplatte und dem Teil bricht, wodurch das Teil unannehmbar wird und möglicherweise der Beschichter mit dem Teil kollidieren kann); und unterschiedliche Materialeigenschaften (Teile weisen sichtbare Mängel auf oder funktionieren nicht wie erwartet).
NC-Prozesse visualisieren
Für NC-Simulations- und Verifizierungsprozesse bleibt AM ein wichtiger Entwicklungsbereich mit Entwicklern von Systemen wie der NC-Simulationssoftware Vericut von CGTech (Irvine, CA), die kürzlich ein Vericut Additive-Modul hinzugefügt hat. „Die additive Fertigung ist nach wie vor einer der heißesten Trends in der Fertigung, daher bemüht sich Simulationssoftware, mitzuhalten“, sagte Gene Granata, Produktmanager bei CGTech Vericut.
„Die Verwendung von Simulationssoftware, die in der Lage ist, dieselben NC-Codes zu simulieren, die die Maschinen steuern, ist der beste Weg, um CNC-Geräte zu schützen und beim ersten Mal in der Werkstatt ein Qualitätsteil zu erstellen.“
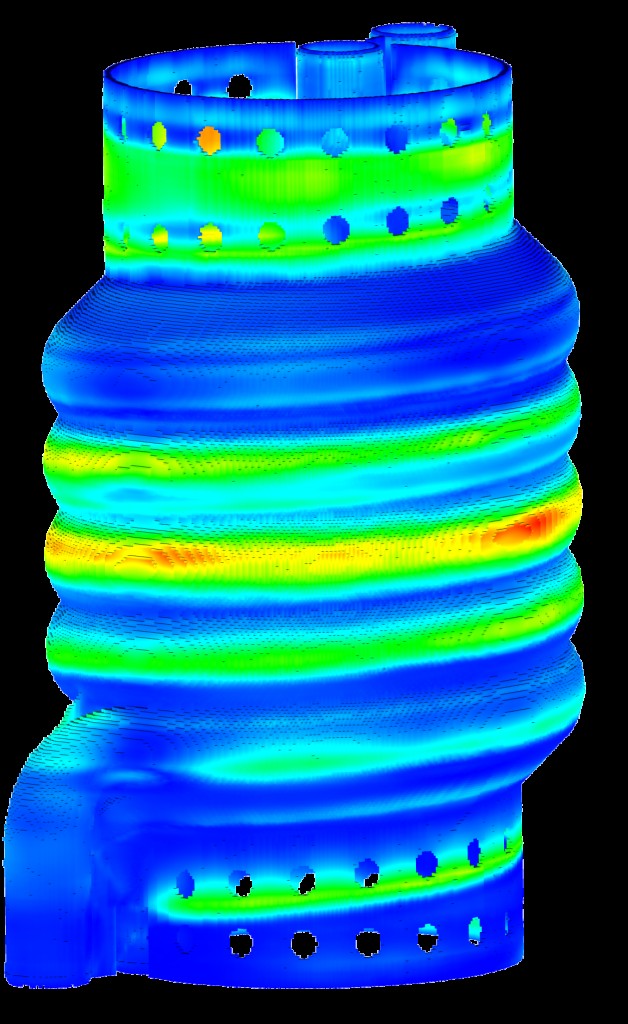
Bei Verbundwerkstoffen sind zwei der neuesten Trends, die auffallen, der Fokus auf die grafische Darstellung und die genaue Darstellung des Werkstücks, bemerkte Granata. „Obwohl die Verbesserung der Grafik wie eine kosmetische Verbesserung erscheinen mag, bietet die genaue Vorhersage und Visualisierung der Nettoform eines Verbundwerkstoffteils echte technische Vorteile. Hersteller verlassen sich immer stärker auf Software, um die endgültige Form und Qualität eines Teils vorherzusagen“, sagte er. „Mit einer hochauflösenden Anzeige des fertigen Werkstücks können Ingenieure damit beginnen, Merkmale, die sie am meisten betreffen, mit größerer Genauigkeit abzufragen.“
Simulationssoftware biete wichtige Tools zur Prozessbewertung und -optimierung, die die Produktivität der Werkstatt steigern, fügte er hinzu. „Es scheinen regelmäßig neue Möglichkeiten zum Erstellen ‚effizienter‘ Werkzeugwege auf dem Markt zu erscheinen, aber wie gut funktionieren sie wirklich? Simulationssoftware – angetrieben von nachbearbeiteten G-Code-Werkzeugwegen – enthüllt die „Wahrheit“ der Maschinenlaufzeiten“, sagte Granata. „Dies hilft NC-Programmierern und Fertigungsingenieuren, verschiedene Bearbeitungsmethoden zu beurteilen, damit sie letztendlich die effizientesten Methoden zur Herstellung ihrer Teile auswählen können.“
Automatisierung, Bearbeitungsoptimierung und Maschinenflexibilität sind Schlüsselbereiche, die Spring Technologies (Cambridge, MA), Entwickler von NCSimul- und Optitool-Software, bei der Entwicklung seiner Simulationssoftware vorantreibt, sagte Silvere Proisy, General Manager von Spring Technologies.
Da der Markt stärker automatisierte Prozesse verlangt, entwickelt NCSimul mehr Automatisierung, sagte er. „Die von der CAM-Software an NCSimul gesendeten Daten werden automatisch verifiziert und das Ergebnis der Simulation wird dem Programmierer als Abschlussbericht per E-Mail zugestellt. Die Benutzer müssen nicht mehr mit der Software interagieren; es kann alles auf einem entfernten Server laufen.“
Die CNC-Bearbeitungsoptimierung mit Optitool wurde verbessert, sagte er. „Es bietet jetzt zwei Optimierungsebenen:Eine ist die Reduzierung des Luftschneidens, bei der alle Annäherungs- und Rückzugsbewegungen optimiert werden, ohne die Vorschubgeschwindigkeiten im Material zu ändern; Die zweite Stufe ist die Lernmodusoptimierung, die die Materialschneidvorschübe basierend auf neun Schneidparametern wie Spandicke oder Spanfluss regelt, ohne die ursprünglichen Vorschübe und Geschwindigkeiten zu beeinträchtigen.“
Maschinenflexibilität ist der dritte Schwerpunkt der Entwicklung mit der Option NCSimul 4CAM. „Ein Fertigungsunternehmen in die Lage zu versetzen, einen Auftrag in wenigen Minuten von einer Maschine auf eine andere umzustellen, ohne das Teil in einer CAM-Software neu programmieren zu müssen, nennen wir eine Revolution“, sagte Proisy. „Es liest den anfänglichen G-Code und schreibt den neuen Code automatisch neu.“
Automatisierungssteuerung System
- 3D-CAD-Modellierung und ihre Beziehung zur Fertigung
- Kollmorgen aktualisiert seine Entwicklernetzwerk-Software
- Verwendung von vorbeugender Wartungssoftware für die Fertigung
- 7 beste ERP-Softwarelösungen für die Fertigung im Jahr 2022
- Smart Manufacturing:was es ist und seine Vorteile
- Honda gibt seine globale Umstrukturierung der Automobilherstellung bekannt
- Big Data ist die vierte industrielle Revolution
- Unternehmensprofil:Fertigungs- und Technologieexperte SourceDay
- Der Aufstieg digitaler Plattformen in der Fertigung
- Bright Machines bringt Microfactory-Hardware und -Software auf den Markt