Digitalisierung steigert Zellproduktion von Autoteilen um 20 %
Zunehmende Größe und Menge seiner Bestellungen veranlassten den in Wisconsin ansässigen Autoteilehersteller Felss Rotaform LLC (New Berlin, WI), den Betrieb durch eine neue Maschinenbeschickungszelle mit zwei Robotern zu erweitern. Das Unternehmen ist Anbieter von Präzisionsteilen mit den Verfahren Rundkneten, Axialumformen und Rohrendenumformen. Um die Ziele der kontinuierlichen Prozessverbesserung des Unternehmens zu erreichen, musste die neue Zelle sicherer, schneller und flexibler sein als ihre vorherigen Fertigungszellen.
Um die komplexe Natur der Automatisierung zu bewältigen, wandte sich das Unternehmen aufgrund ihrer Erfolgsbilanz in Innovation und ihres Fachwissens in integrierter Robotik und Steuerungstechnologien an Siemens und den Systemintegrator IAS Inc. (New Berlin, WI). Sechs Monate später betrieb Felss Rotaform eine digitalisierte, integrierte Fertigungszelle, die die Produktivitäts- und Rentabilitätsrekorde des Unternehmens brach.
Bei der Überprüfung der Anforderungen für seine Roboterzelle der nächsten Generation hatte Felss Rotaform mehrere Ziele. Erstens wollte es die Produktivität steigern, indem es neue Hochgeschwindigkeits-SPS einsetzte, um kürzere Durchlaufzeiten für alle einzelnen Teile zu erreichen.
Zweitens wollte man eine fortschrittlichere Sicherheitslösung erforschen, die eine bessere Kontrolle darüber gewährleistet, wer die Zelle betritt. In den älteren Zellen konnte eine Maschine versehentlich eingeschaltet werden, wenn eine Wartungsperson in der Zelle anwesend war, wodurch diese Person einem Verletzungsrisiko ausgesetzt war. Um dies zu vermeiden, wollte Felss Rotaform einen automatisierten Prozess, der garantiert, dass die Zelle nach dem Neustart frei ist.
Drittens wünschte man sich mehr Flexibilität bei Zellwechseln, was es dem Unternehmen ermöglichen würde, eine breitere Produktpalette für seine Kunden zu testen und anzubieten. Bei den älteren Zellen musste jedes Mal die gesamte Zelle neu programmiert werden, wenn ein neuer Prozess durchgeführt wurde, was Tage dauern konnte, bis er ausgeführt wurde.
Das ursprüngliche Ziel von Felss Rotaform war eine Durchlaufzeit von 48 Sekunden für den gesamten Zyklus für jedes Teil in der neuen Zelle (weitaus schneller als bei allen älteren Zellen). Das Design und die Implementierung der Lösung beschleunigten den gesamten Teileproduktionsprozess um bis zu 38 Sekunden, was einer Effizienzsteigerung von 20 % entspricht. Nach der Implementierung der neuen Zelle verringerte sich die Ausfallzeit für komplexe Umstellungen von Tagen auf Stunden, und was früher acht Stunden dauerte, dauert jetzt nur noch 15 Minuten für typische geplante Umstellungen, so Chad Due, Elektrosteuerungsingenieur von Felss Rotaform. P>
„Diese neue Zelle kann in zwei Schichten produzieren, wofür vorher drei Schichten benötigt wurden. Dadurch können wir innerhalb von 24 Stunden 600 zusätzliche Teile produzieren. Darüber hinaus ist die Rentabilität der Zelle um 13 % gestiegen“, sagte Due.
Richard Parkhurst, Kundenbetreuer bei Siemens, wusste, dass IAS gut aufgestellt sein würde, um die Ziele von Felss Rotaform zu erreichen. „Einige Integratoren führen ausschließlich Softwareentwicklung durch, andere sind besser darin, die Hardware zu bauen und zusammenzubauen. IAS brachte eine Kombination aus allen erforderlichen Fähigkeiten und Fachkenntnissen mit, einschließlich Robotik- und Sicherheitstechnikfähigkeiten“, sagte er.
IAS erkannte, dass Siemens-Produkte entscheidend dazu beitragen würden, Felss Rotaform dabei zu helfen, seine Ziele zu erreichen, indem sie die erforderliche Geschwindigkeit, Zuverlässigkeit, Flexibilität und Sicherheit bieten. So wurde beispielsweise ein Ethernet-basierter, digitalisierter Siemens PROFIsafe-Kommunikations-Backbone in die Zelle integriert, um die Maschinen- und Perimetersicherheit zu steuern. Zwischen den verschiedenen SPSen und Robotern ist eine sichere Kommunikation gewährleistet. PROFIsafe leitet Statusinformationen von den Geräten innerhalb der Zelle an die Haupt-SPS weiter und bietet
einen großen Vorteil gegenüber älterer Technologie, da sowohl die Standard- als auch die sichere Kommunikation über ein einziges Bussystem stattfinden.
Alle Sensoren und Aktoren innerhalb der PROFIsafe-Lösung sind innerhalb des dezentralen Sicherheitskonzepts frei programmierbar, unabhängig von ihrer E/A-Station. Diese Flexibilität ermöglicht es dem Bediener, Aktoren selektiv abzuschalten. Weitere Vorteile sind ausfallsichere Kommunikation, erweiterte Diagnose und Hot-Swapping-Funktionen, die dazu beitragen, Ausfallzeiten zu reduzieren.
Siemens Simatic S7-1500 SPS mit integrierter Profinet-Schnittstelle spielten ebenfalls eine wichtige Rolle bei der Erhöhung der Betriebsgeschwindigkeit. Der Highspeed-Rückwandbus bringt mit seiner hohen Baudrate und dem effizienten Übertragungsprotokoll einen entscheidenden Performance-Vorteil für die schnelle Signalverarbeitung.
Laut Simon Vancina, IAS-Anwendungsingenieur und Hauptroboter- und SPS-Programmierer, „war die S7-1513F-SPS aufgrund ihrer Geschwindigkeit, der Bandbreite an verfügbaren
I/O-Erweiterungskarten und der programmierbaren Sicherheitssteuerung eine hervorragende Wahl für dieses Projekt Funktionalität, relativ kompakter Formfaktor und geringe Kosten.“
Das TIA Portal von Siemens spielte eine entscheidende Rolle bei der Einsparung von Zeit und Engineering-Ressourcen bei der Programmierung aller SPSen und HMIs. Die Nutzung des TIA Portals verkürzt die Time-to-Market durch Simulationstools, Programmierer-Produktivitätstools und zusätzliche Diagnose.
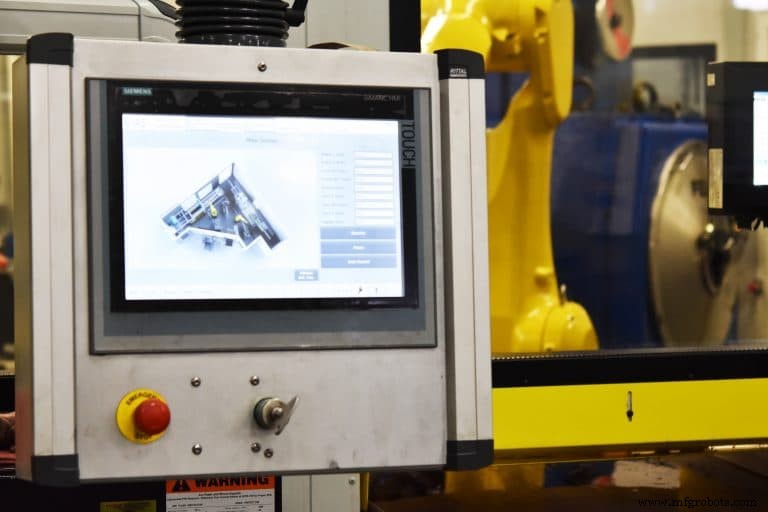
„Mit TIA Portal kann ich Code so schreiben, wie ich es möchte, und bei Bedarf von einer Programmiersprache zur anderen wechseln“, sagte Vancina. „Mit TIA Portal könnte ich beispielsweise Ladder Logic wählen, um einfache logische Abschnitte leichter lesbar zu machen, und dann in der nächsten Codezeile zu etwas wie strukturiertem Text wechseln, um komplexere Prozesssteuerungen oder Berechnungen zu implementieren. Nahezu alle SPSen ermöglichen die Verwendung der verschiedenen IEC 61131-3-Programmiersprachen, aber TIA Portal ermöglicht es Ihnen, sie auf einzigartige und effektive Weise zu kombinieren. Dies ist eine sehr praktische Funktion, die es uns ermöglicht, unsere Code-Entwicklungszeit zu verkürzen und dieses System viel schneller online zu bringen.“
Mit der Umsetzung des Projekts sah Felss Rotaform sofort Vorteile, die über seine Kernziele hinausgingen. Große Automobilhersteller sind immer bestrebt, neue Produkte zu testen. Sie verlassen sich darauf, dass ihre Lieferanten sie beim Testprozess unterstützen. Die reaktionsschnellsten Lieferanten in der Testphase werden oft mit Neugeschäft belohnt.
Die neue Fertigungszelle bei Felss Rotaform wurde im Hinblick auf Produkttests konzipiert. Es kann sechs verschiedene neue Teilenummern in einer Woche ausführen, was einen ganzen Monat auf einer anderen Zelle dauert.
Auch bei der Erkennung defekter Teile ist die neue Zelle deutlich fortschrittlicher. Für Hersteller wie Felss Rotaform spielt die Rückverfolgbarkeit eine Schlüsselrolle bei der Senkung der Betriebskosten. Die Zelle kann dazu beitragen, den Versand defekter Teile zu verhindern, indem sie defekte Teile erkennt und in einen separaten Behälter legt, die Zelle sogar stoppt und den Bediener alarmiert, wenn Defekte zu häufig auftreten. Wenn ein defektes Teil geliefert und vom Kunden gefunden wird, kann dies die Rücksendung einer ganzen Lieferung bedeuten, was den Lieferanten Hunderttausende von Dollar kosten kann.
IAS und Siemens testen derzeit zwei ähnliche Roboterzellen, die 2018 implementiert werden und eine bessere Wartungsverfolgung für eine fortschrittlichere digitale Fertigung beinhalten. Das neue System verfolgt, wie lange eine Maschine läuft, und zeigt an, wenn wichtige kritische Teile sich ihren voraussichtlichen Zykluszeitschwellen nähern.
Eine Lösung, die untersucht wird, ist MindSphere, ein cloudbasiertes offenes Internet of Things (IoT)-Betriebssystem, das als verbundene Plattform mit Apps dient, die eine Reihe von Funktionen bieten, wie z. B. die Reduzierung von Sicherheitsrisiken und die Verbesserung der Verfügbarkeit von vernetzten Maschinen und Anlagen.
Darüber hinaus wird das neue System Predictive Analytics beinhalten, um eine Warnung über potenzielle Probleme an die Hauptsteuerung einer Zelle zu senden. „Das neue System sagt Ihnen, was ersetzt werden muss und welche Art von Teil das System benötigt. Sie scannen das Teil, bevor Sie es installieren, und es sagt Ihnen, ob es das richtige Teil für diese Maschine ist“, sagte Vancina.
Weitere Informationen von Siemens erhalten Sie unter www.siemens.com oder telefonisch unter 847-640-1595; von IAS gehen Sie zu www.iasworldwide.com oder rufen Sie 866-243-2402 an.
Automatisierungssteuerung System
- Gewinner des SPE Auto Innovation Award 2019
- Spritzgießen:Einfache Roboterzelle zum Anschnitt ohne Programmierung
- Einen besseren Puffer aufbauen:Fördertechnik im Kern der Lights-Out-Formzelle
- Renegade steigert Produktion von hitzebeständigen Kohlefaser-Prepregs
- Alltec expandiert auf dem nordamerikanischen Markt
- Digitalisierung von Produktionsanlagen
- Endbearbeitungsrevolver reduziert Zykluszeit
- Drehzelle automatisiert Produktion von Ölkupplungen
- Großserienfertigung von Teilen
- Portalportal geeignet für die Inline-Fertigung von Kleinteilen