Greifdrehmoment:Die Antwort auf die falsche Frage
Greifmoment:Die Antwort auf die falsche Frage.
Teil 2 einer zweiteiligen Serie
(siehe Greifmoment:Ist dies der richtige Weg, um die Effektivität von Werkzeugen/Werkzeughaltern zu messen?).
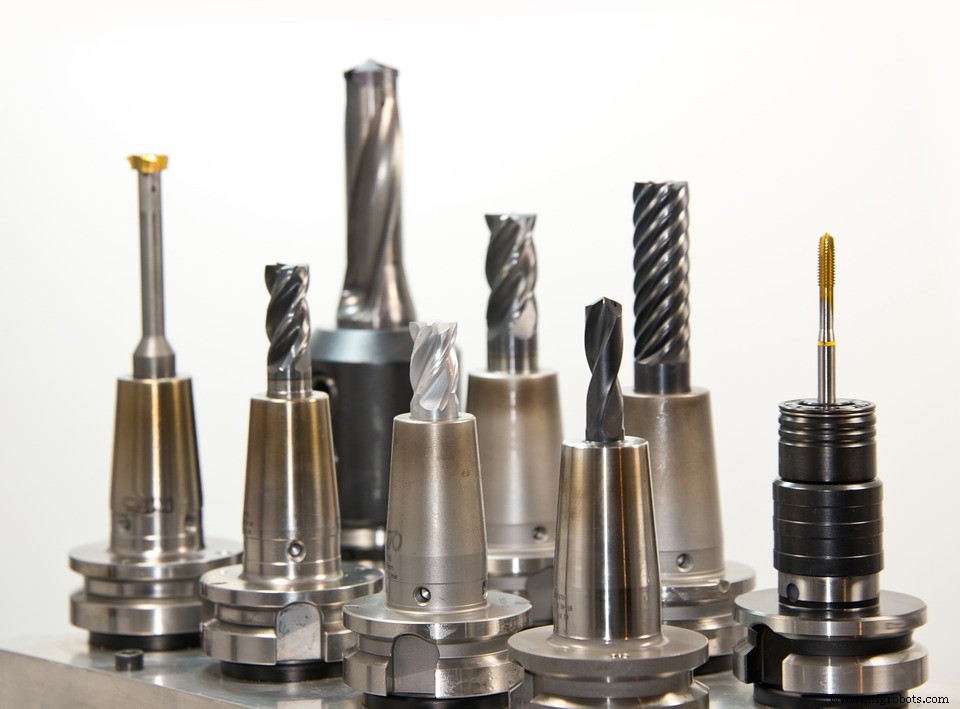
Mit der Weiterentwicklung der Maschinen für die Metallbearbeitung, die immer schneller wurden, hat sich auch die Suche nach dem, was wir „Werkzeugsicherheit“ nennen, fortgesetzt. Als neue Formen von Werkzeughaltern in Gebrauch kamen, war das Greifmoment weiterhin die bevorzugte Methode zur Beurteilung und zum Vergleich verschiedener Methoden, um Werkzeuge für die beste Produktivität an Ort und Stelle zu halten.
Sidelock-Schaftfräsfutter
Das Seitenschlossfutter war eine frühe (vor fast 100 Jahren) Lösung, um die Sicherheit des Werkzeugs zu gewährleisten. Diese Schnittstelle beinhaltet das Anziehen einer Schraube an der Seite des Halters in Verbindung mit einer geschliffenen Fläche an der Seite des Werkzeugs. Während die Werkzeugsicherheit gewährleistet ist, schafft die formschlüssige Lösung eine Vielzahl anderer Probleme, die es zu einem weniger als idealen System für moderne Bearbeitungsmethoden machen.
Erstens führt die Art der einseitigen Klemmung über eine Stellschraube zu einem offensichtlichen Rundlaufproblem. Wenn in der Nähe der Unterseite des Schafts eine Kraft ausgeübt wird, bewirkt dies, dass sich das Schneidende des Werkzeugs in die entgegengesetzte Richtung bewegt; daher tritt ein Rundlaufproblem auf, das die Werkzeuglebensdauer und Maßhaltigkeit verringert. Zweitens erzeugt die Schraube auf einer Seite des Halters in Verbindung mit einem Schneidwerkzeug, bei dem auf einer Seite ein Stück Material fehlt, ein offensichtliches Unwuchtproblem. Das Ergebnis ist eine erhöhte Vibration, die sich auf die Lebensdauer des Werkzeugs, die Oberflächengüte und die Lebensdauer der Spindellager auswirkt. Die gemeinsame Lösung zur Überwindung dieser beiden Nachteile sind langsamere Geschwindigkeiten und Vorschübe, um die Lebensdauer, die Oberflächengüte oder das Bearbeitungsgeräusch zu verbessern. Der letztendliche Nachteil, der oft nie erkannt wird, da viele Bearbeitungsprozesse vererbt werden, ist die verringerte Produktivität.
Wie in unserem vorherigen Artikel erwähnt, werden Sidelock-Spannfutter auch heute noch verwendet, teilweise weil sie ein gewisses Maß an Werkzeugsicherheit bieten. Ihr inhärenter Mangel an Rundlaufgenauigkeit und Ausgewogenheit führte jedoch zur Entwicklung des ebenso beliebten Spannzangensystems. Aber was dieses System an Genauigkeit gewann, verschenkte es an Werkzeugsicherheit.
Spannzangenfutter
Spannzangenfutter haben sich aus der Notwendigkeit heraus entwickelt, eine höhere Genauigkeit als die des traditionellen Halters mit seitlicher Verriegelung zu erreichen. In dieser Hinsicht wurde die Genauigkeitsnote stark verbessert. Darüber hinaus war die Vielseitigkeit des Designs ein weiteres herausragendes Merkmal, das die zusätzlichen Kosten für einen komplett neuen Halter reduzierte, wenn ein anderer Werkzeugdurchmesser erforderlich war. Die verbesserte Vielseitigkeit und Genauigkeit machten dieses Spannfutter wohl zu einer der beliebtesten Werkzeughaltemethoden in der Branche. Was die Spannzange jedoch an Genauigkeit gewann, verlor sie an Spannmoment. Die mechanische Natur dieser Lösung machte das Herausziehen des Werkzeugs zu einem echten Problem für diejenigen, die damit jede Art von schweren Fräsoperationen versuchten. Viele Bediener würden versuchen, dies durch zu starkes Anziehen der Mutter zu kompensieren, aber leider führte dies nur zu einem Verlust an Rundlaufgenauigkeit und Werkzeugsicherheit, die immer noch unzureichend waren. Somit ging die Weiterentwicklung weiter.
Fräsfutter
Die nächste Evolution in der Werkzeugaufnahme kam in Form von Fräsfuttern. Hierbei handelt es sich um eine mechanische Lösung, die vor 50 Jahren entwickelt wurde, um ein größeres Spannmoment im Vergleich zu Spannzangen (mehr Sicherheit) mit ähnlicher Genauigkeit bereitzustellen, sodass Hersteller ein spannzangenartiges System haben konnten, das zum Schruppen geeignet ist. Fräsfutter galten als überlegen gegenüber der Seitenverriegelung, da sie eine verbesserte Genauigkeit mit erhöhtem Greifmoment für mehr Sicherheit boten … wenn sie richtig eingespannt waren. Die Erhöhung der Genauigkeit kam von der Spannzangenschnittstelle, die gleichmäßig 360° um den Schaft des Fräsers greift, während die Lagerlaufbahn für eine erhöhte Drehmomentübertragung beim Anziehen sorgt. Darüber hinaus können sie nach unten gesleevt werden, wodurch die Anzahl der verschiedenen Halter, die für jeden Werkzeugdurchmesser benötigt werden, begrenzt wird.
Fräsfutter haben jedoch viele separate Komponenten. Wie bereits erwähnt, wird das Werkzeug mit einem Rollenlagerkäfig gegriffen, der dann mit einer großen Außenmutter festgezogen wird, um das Spannfutter um das Werkzeug herum zusammenzudrücken. Während das Greifmoment gegenüber dem einer Spannzange deutlich erhöht ist, erfordert die schiere Größe des Rollenlagerkäfigs eine große Mutter, um sie aufzunehmen, daher ein Halterprofil, das sehr sperrig ist und eine schlechte Reichweite hat.
Auch wurde bereits erwähnt, dass die Wirksamkeit des Fräsfutters stark vom Bediener abhängt. Für eine ordnungsgemäße Klemmung muss die Mutter bis zum Anschlag angezogen und dann um eine ¼ Umdrehung zurückgedreht werden. Dies liegt daran, dass die Lager beim Anziehen etwas über sich selbst rollen, was zu Schlag führt. Indem Sie sich zurückziehen, entlasten Sie die Lager. Viele Bediener neigen jedoch aus Unkenntnis, Zeitmangel oder anderen Gründen dazu, die Mutter zu fest anzuziehen, ohne sich zurückzuziehen.
Ein weiterer Nachteil dieses Systems besteht darin, dass die Nadellager nach dem Anziehen nie an der gleichen Stelle sitzen und oft übereinander gerollt werden. Das Ergebnis ist die Unfähigkeit, ein wiederholbares Gleichgewicht zu erreichen. Bei niedrigeren Geschwindigkeiten sind die Nachteile der Unwucht nicht immer sofort sichtbar, aber bei höheren Geschwindigkeiten nehmen Rundlaufgenauigkeit und Standzeit schnell ab.
Schließlich ist das Fräsfutter eine teure Haltelösung. Abgesehen von den Anschaffungskosten sind die Wartungskosten zu berücksichtigen, da die meisten alle 6 Monate zerlegt und geschmiert werden müssen. Da dies Zeit und Geld kostet, überspringen Bediener diesen wichtigen Schritt oft. Dadurch sinkt das Greifmoment und die Rundlaufgenauigkeit wird beeinträchtigt.
Andere Optionen
Welche anderen Alternativen zu Schaftfräserfuttern oder Fräserfuttern haben Bediener verwendet, um Werkzeugsicherheit zu erreichen?
Die Schrumpfpassung bringt die Reibpassungsmethode auf eine andere Ebene. Es nutzt die Eigenschaften der Wärmeausdehnung, um ein hohes Greifmoment mit zusätzlicher Genauigkeit und Reproduzierbarkeit des Gleichgewichts aufzunehmen. Es kann auch mit dem Safe-Lock™-System verwendet werden. Dieses System hat nicht nur ein hohes Spannmoment, Genauigkeit und Ausgewogenheit; Es ist auch eines der am einfachsten zu erlernenden Systeme für Bediener.
Das Einpresssystem verwendet eine mechanische Presse, um eine Spannzange/Hülse vorübergehend zu verformen, um ein Rundschaftwerkzeug einzusetzen. Der Halter hat einen leichten Winkel, der dem der Spannhülse entspricht. Eine hydraulische Presse, die sich durch eine gerade Bohrung in der Mitte bewegt, presst Spannzange und Werkzeug zusammen. Das Greifmoment ist hoch und die Rundlaufgenauigkeit ist gut, aber dem Körper des Halters fehlt physische Masse, was ihn für schwere Seitenlasten weniger als ideal macht und daher nicht für schweres Schruppen geeignet ist. Auch fehlt es an Flexibilität, da Werkzeuge eine bestimmte Schaftgröße haben müssen oder die Spannzange brechen kann. Und da das System proprietär ist, sind Sie in Bezug auf Preis, Lagerverfügbarkeit und Angebotsvielfalt sehr stark auf nur einen Hersteller angewiesen.
Hydrodehnspannfutter eignen sich gut für gerade vertikale Arbeiten (Bohren/Reiben), aber nicht zum Fräsen. Sie verwenden Flüssigkeit unter Druck, um eine innere Blase auszudehnen, die schließlich mit dem Werkzeug in Eingriff kommt. Es ist für die Hochgeschwindigkeitsbearbeitung mit geringen Schnitttiefen und Schnittkräften geeignet, aber es ist nicht ideal für schweres Schruppen oder alle Szenarien, in denen größere Radialkräfte oder Hitze auftreten. Wieso den? Die Flüssigkeit im Futter ist zu flexibel, um eine ausreichende Übertragung des Spannmoments zu gewährleisten. Darüber hinaus kann das Hochleistungsfräsen in einigen Fällen Temperaturen erzeugen, die tatsächlich dazu führen, dass das interne Öl verdunstet und somit einen Ausfall verursacht. Ähnlich wie beim Mühlenfutter ist auch hier von Zeit zu Zeit eine Wartung erforderlich, um sicherzustellen, dass die inneren Blasen nicht zu stark verschleißen und undicht werden.
Wie dieser Artikel zeigt, wurde die Suche nach dem maximalen Greifmoment jahrzehntelang ohne wirkliche Befriedigung fortgesetzt, da der Bedarf nicht richtig definiert wurde. Greifmoment war die Antwort auf die falsche Frage.
Zuvor auf Haimer-USA.com vorgestellt.
Industrietechnik
- Farben:Das beste Malwerkzeug!
- Die Frage zur Vertragspflege – Teil 2
- Die Frage zur Vertragspflege – Teil I
- Digitale Finanzierung ist die Antwort auf langsame ESG-Fortschritte
- Energieeffizienz als Dienstleistung ist das neueste Instrument zur Bekämpfung des Klimawandels
- Unwucht:Das versteckte Problem, das Maschinenwerkstätten lösen müssen
- Optimierung der Werkzeuglebensdauer:Die Auswirkung von Führungswinkeln auf Drehoperationen
- MEP bringt Vorteile bei der Teilefertigung für die Luft- und Raumfahrt
- Die Herausforderungen des Hartdrehens meistern
- Oberflächeninspektion in die Hände des Werkzeugmaschinenbedieners legen